El mantenimiento preventivo (PM) es fundamental para la rentabilidad y el rendimiento en industrias con uso intensivo de activos.
Cada tarea de PM debe proporcionar una línea de visión clara de los objetivos de gestión de activos y los objetivos de la organización. Debe saber por qué aprieta cada perno, por qué alinea cada motor y por qué lava cada transportador con tanta frecuencia.
Cada tarea de PM debe agregar valor y desempeñar su papel para lograr una alta disponibilidad de activos y preservar la confiabilidad inherente de los activos. Cada tarea de PM debe proporcionar un retorno de la inversión durante todo el ciclo de vida del activo.
Antes de entrar en detalles, demos un paso atrás.
En pocas palabras, el mantenimiento preventivo es una estrategia que consiste en todas las tareas realizadas por nuestros departamentos de operaciones y mantenimiento para evitar fallas en los equipos y preservar sus funciones principales.
Pero eso es lo que es. Las tareas de mantenimiento que previenen la falla de nuestro equipo y preservan su función operativa para entregar nuestros bienes o servicios vendibles. Defiende a nuestras organizaciones contra esos archienemigos:el tiempo de inactividad no programado y las pérdidas de producción.
Pero hablaremos de eso más adelante.
Estas son algunas de las tendencias industriales y empresas dominantes en las últimas décadas:
Década |
Tendencias dominantes |
10s |
Industria 4.0
IoT.
Mantenimiento 4.0.
Economía circular y producción sostenible,
Google. Facebook. Gorjeo. Snapchat. |
00s |
Producción sostenible.
“Glocalización” (global + adaptar a local).
Robots industriales.
GE. Microsoft. Intel. |
años 90 |
Globalización.
Manufactura esbelta, Six Sigma, RCM.
Toyota, General Motors |
años 80 |
Automatización, informática, electrónica.
ExxonMobil, IBM |
años 70 |
Internacionalización.
|
años 60 |
Producción en masa.
Comercio internacional.
El efecto Deming en la Calidad. |
50 |
Crecimiento de la posguerra, aumento del consumismo. |
40s |
Exigencias de la Segunda Guerra Mundial. |
El equipo estaba sobrediseñado y era sencillo en el tiempo previo a la década de 1940. Esto significaba que, en general, era confiable y fácil de mantener, y el mantenimiento reactivo era la estrategia principal. Pero durante la década de 1940, algo cambió drásticamente. A medida que la Segunda Guerra Mundial se extendía por toda Europa, el aumento de la demanda industrial significó que los eventos de tiempo de inactividad se magnificaron. El equipo naturalmente se volvió más complejo y tomó más tiempo repararlo. Por lo tanto, el mantenimiento preventivo pasó a primer plano en forma de revisiones programadas.
La década de 1950 vio un aumento del consumismo de la generación que sobrevivió a los años de guerra y se hizo más demanda en la industria y el mantenimiento preventivo.
En la década de 1960, la producción en masa estaba en pleno efecto y el comercio internacional estaba creciendo sustancialmente, lo que imponía exigencias aún mayores a los equipos. Las ideas y la influencia de Edward Deming estaban teniendo un profundo efecto en la calidad del producto, pero las revisiones programadas y el mantenimiento reactivo seguían siendo dominantes.
A partir de la década de 1970 surgió la necesidad de una mayor calidad y disponibilidad, menos tiempo de inactividad y ciclos de vida más prolongados de los equipos. Las organizaciones se habían internacionalizado y necesitaban ser competitivas a nivel mundial. El mantenimiento preventivo tenía que agregar valor, y tenía que valer la pena hacerlo. Me di cuenta de que las revisiones programadas no siempre agregaban valor y no siempre prevenían fallas.
El mantenimiento preventivo tuvo que seguir adelante.
Las nuevas tecnologías, como el monitoreo de condiciones, estaban ahora en su infancia. Los PM se centraron más en la limpieza, la lubricación y la inspección.
La década de 1980 vio el auge de la automatización industrial, las computadoras y la electrónica para impulsar la eficiencia operativa. Junto con esto, surgió la necesidad de nuevas habilidades de mantenimiento, múltiples habilidades y nuevas rutinas de PM.
La década de 1990 vio la globalización masiva y la popularidad de la fabricación ajustada y los enfoques Six Sigma para reducir el desperdicio y los defectos. El mantenimiento centrado en la confiabilidad (RCM) aumentó la comprensión de la estrategia de mantenimiento. Y los años 90 vieron un impulso hacia el mantenimiento impulsado por el operador donde se esperaba que los operadores realizaran el 1
st
mantenimiento de línea y tareas de PM.
El enfoque cambió en la década de 2000 a la sostenibilidad debido al cambio climático y nació el término 'Glocalización'. Por ahora, las tecnologías de monitoreo de condición habían avanzado significativamente en el mantenimiento preventivo. Los robots industriales también se destacaron y trajeron consigo nuevos requisitos de PM.
El panorama industrial había cambiado significativamente en la década de 2010. El mantenimiento preventivo se encontró en un 4
th
revolución industrial (industria 4.0) donde los sensores y sistemas interconectados proporcionaron información en tiempo real sobre el estado del equipo, aunque el enfoque se mantuvo en la sostenibilidad y la economía circular. Los gigantes de la tecnología dominaron el panorama donde sus principales activos y equipos eran los centros de datos.
Hoy en día, en industrias dinámicas y con uso intensivo de activos, tenemos una mejor comprensión del mantenimiento preventivo y la forma en que agrega valor para lograr nuestros objetivos organizacionales.
Entendemos que permitir que los activos fallen, y luego repararlos, es un negocio costoso. Y que hay mejores formas de realizar el mantenimiento preventivo.
El mantenimiento preventivo se compone de diferentes tipos de tareas
Algunos creen que PM consiste solo en reemplazos basados en el tiempo o el uso. Esto no es estrictamente cierto. Es solo la mitad de la imagen. El mantenimiento preventivo se puede dividir en dos áreas principales:mantenimiento basado en tiempo/uso y mantenimiento basado en condición.

Mantenimiento basado en tiempo/uso
Esto es probablemente lo que le viene a la mente cuando piensa en PM:piezas y componentes que se reemplazan o renuevan según el tiempo (calendario) o según el uso. Se puede programar el cambio de un filtro de proceso cada 12 meses o se puede programar el reemplazo de una cuchilla cortadora de papel después de 2500 horas de servicio. En ambos casos, se sabe que los artículos se desgastan poco después de alcanzar esos límites. Y, por lo tanto, el fabricante está previniendo fracaso.
Las tareas basadas en calendario son mucho más fáciles de programar, pero corren el riesgo de mantener el activo por encima o por debajo porque no hay garantía de que el filtro de proceso se haya utilizado todos los días de esos 12 meses. Por otro lado, las tareas basadas en el uso, aunque más difíciles de rastrear y administrar, son más efectivas y económicas ya que se basan en la utilización real del activo.
Otras tareas típicas de PM, como la limpieza y la lubricación de los activos, pueden considerarse actividades basadas en el tiempo/uso. Estas tareas simples, pero críticas, a menudo se realizan de forma programada en semanas o meses de actividad de fabricación y sirven para preservar el funcionamiento y la confiabilidad del equipo.
Mantenimiento basado en la condición (CBM)
Este tipo de mantenimiento significa que realizamos una tarea de reparación o reemplazo basada únicamente en la condición medida de un activo.
Usamos una técnica llamada monitoreo de condición que nos permite llevar a cabo un mantenimiento basado en la condición.
Primero, medimos un parámetro específico de la salud de un activo, como vibración, temperatura, decibelios, partículas de desgaste o contaminación. Luego trazamos la tendencia del valor del parámetro a lo largo del tiempo. Cuando creemos que ha llegado a un punto crítico de que el activo avanza hacia una falla funcional (ya no puede realizar sus funciones), programamos una intervención de mantenimiento basada en la condición.
Estos son algunos ejemplos de intervenciones de CBM:
- Reemplazo de cojinetes desgastados
- Equilibrar los impulsores del ventilador
- Renovación de contactores eléctricos
- Juegos de bombas de alineación
- Reposición de aceites lubricantes
- Apretar cables eléctricos sueltos
CBM es la forma más rentable y económica de mantener activos basados en mecanismos de deterioro reales y reales.
Un subconjunto de las técnicas de monitoreo de condición son las inspecciones sensoriales y detalladas. Juegan un grande papel en el mantenimiento preventivo y la detección activa del deterioro de los activos. Aunque a menudo son cualitativos, siempre debemos esforzarnos por hacerlos lo más cuantitativos posible. Las inspecciones sensoriales pueden incluir lo siguiente:
- Escuchar ruidos inusuales.
- Buscando daño.
- Olor en busca de signos de quemadura.
Se pueden utilizar inspecciones detalladas (y listas de verificación) en todos los tipos y categorías de activos, desde una pequeña bomba dosificadora de 1kW en una cervecería hasta una turbina de vapor de 250 MW en una acería. Las inspecciones pueden incluir lo siguiente:
- Asegúrese de que el descentramiento del eje sea de 0,004" o menos.
- Inspeccione el prensaestopas del cable del motor en busca de signos de deterioro.
- Asegúrese de que la tensión de la correa de transmisión esté entre 88 y 90 libras.
- Inspeccione el sello mecánico de la bomba en busca de fugas.
Ahora que todos sabemos qué significa el mantenimiento preventivo y en qué consiste, es hora de hacernos la siguiente pregunta.
¿Qué hace bueno PM parece?
En primer lugar, hay que aclarar que el mantenimiento preventivo no se aplica a todos los activos. En la mayoría de los casos, se aplicará a los activos de criticidad media y alta de su organización. Los activos de baja criticidad a menudo se ejecutan hasta fallar porque las consecuencias de su fracaso no justifican el tiempo y los recursos de PM.
En segundo lugar, una discusión sobre el mantenimiento preventivo no puede estar completa sin afirmar que las mejores organizaciones de su clase utilizan el análisis de modos y efectos de falla (FMEA) para desarrollar sus enfoques y estrategias de mantenimiento, de los cuales PM es siempre un elemento clave.
En tercer lugar, administre sus PM en un sistema EAM o CMMS. El mantenimiento preventivo tiene su propio proceso de flujo de trabajo como parte de la gestión del trabajo tradicional. Si conoce sus PM programados, puede pronosticar la planificación de recursos y mantener el control de los costos.
Estas son algunas de las mejores prácticas y sugerencias que lo ayudarán a llevar a cabo adecuadamente mantenimiento preventivo:
PM basado en el tiempo o el uso:guarde estas tareas para artículos o componentes que realmente se desgastan con el tiempo. Si está reemplazando o reacondicionando elementos que no muestran características de desgaste genuino, entonces está tirando dinero por el desagüe. Recuerde, este tipo de PM debe reservarse para elementos que estén en contacto con el producto o donde se produzca fricción.
CBM:sus mediciones de monitoreo de condición deben tomarse en los intervalos correctos para la detección de fallas y deben basarse en modos de falla detectables. Con esto queremos decir que está midiendo la vibración para resaltar cojinetes dañados, desalineación, desequilibrio o cavitación. No puede decirte todo. Y no le dirá que tiene producto contaminado pasando por su bomba. Las mediciones también deben ser repetibles y recolectadas desde el mismo lugar cada vez.
Inspecciones:su programa de inspecciones será altamente exitosa si se basa en modos de falla conocidos, es cuantitativa y repetible. Mira la diferencia aquí:
1a. |
Compruebe el juego axial del rodamiento. |
1b. |
Asegúrese de que todos los pernos de la cabeza de la tapa estén apretados. |
1a. |
Con un DTI, asegúrese de que el juego axial del cojinete esté entre 0,001" y 0,0015" a temperatura ambiente (18 a 30 ºC). |
1b. |
Con una llave dinamométrica calibrada en forma cruzada, asegúrese de que los cuatro (4) pernos de cabeza de casquete estén apretados a 250 pulgadas-libras. |
¿Puedes ver cómo el segundo conjunto de inspecciones es valor añadido? ?
Por el contrario, el primer conjunto de inspecciones es ambiguo y puede generar pérdida de tiempo, malas interpretaciones, argumentos y errores.
¡Nadie quiere eso!
¿Vale la pena el mantenimiento preventivo el esfuerzo?
Mencionamos antes que PM tiene que valer la pena. Y con eso queremos decir financieramente Vale la pena el esfuerzo. Los costos de prevenir la falla deben ser menores que los costos de la falla misma; de lo contrario, no lo es.
Mira este diagrama:
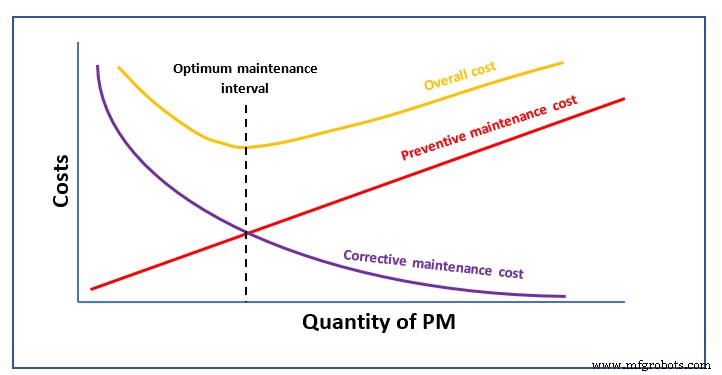
Muestra un concepto muy simple.
Si realiza muy poco PM, sus costos de mantenimiento correctivo serán altos, es decir, tendrá muchas fallas que corregir. Por el contrario, si realiza un mantenimiento preventivo excesivo, sus costos de mantenimiento correctivo serán muy bajos, pero los costos de mantenimiento preventivo se dispararán hacia arriba.
Al comprender sus activos, sus modos de falla y las necesidades de mantenimiento, puede encontrar el punto óptimo:el intervalo de mantenimiento óptimo . Este es el intervalo de mantenimiento preventivo que brindará a su organización los costos de mantenimiento más bajos durante el ciclo de vida del activo para una tarea de mantenimiento preventivo específica.
Un concepto similar con respecto a los costos se puede ver aquí:
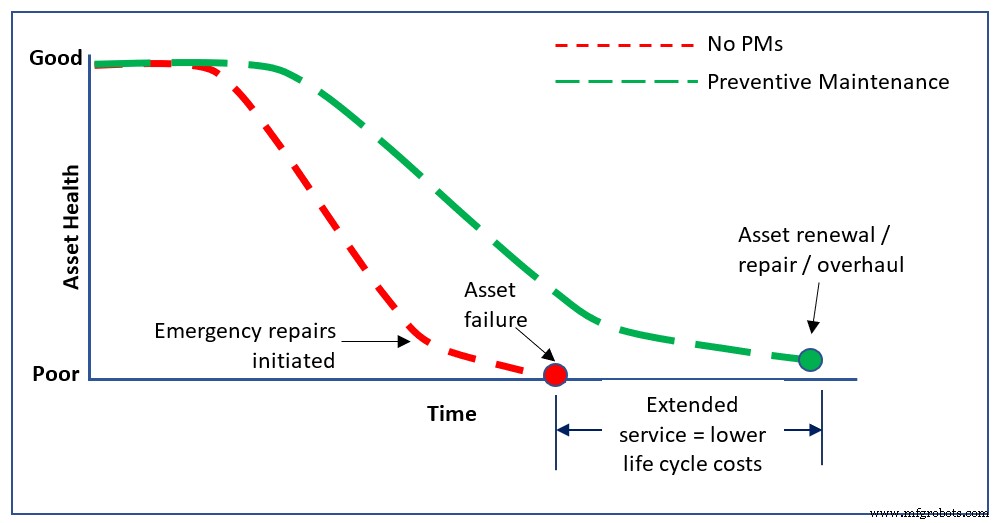
Muestra que al extender los ciclos de vida de los equipos a través del mantenimiento preventivo regular, podemos ahorrar costos significativos del ciclo de vida en términos de gastos operativos y de mantenimiento.
La moraleja de la historia? Sea planificado y proactivo, no totalmente reactivo.
Aspectos a tener en cuenta
Después de todas esas cosas buenas, debemos moderar un poco la discusión con cosas para estar atentos o precavidos de!
Mantenimiento recomendado por OEM – si su activo aún se encuentra en el período de garantía, entonces sí, siga las instrucciones por todos los medios. Pero tenga en cuenta que después de que finalice el período de garantía, debe revisar su estrategia de mantenimiento preventivo. Esto se debe a que los PM recomendados por los OEM se basan en estimaciones conservadoras y en los peores escenarios. Pueden hacer que mantenga en exceso su activo. Esto se debe a que el OEM no sabe en qué industria se encuentra y no sabe cuál es el entorno operativo.
Y otro punto a considerar es que todos los OEM ganan dinero con las ventas de repuestos.
PM ambiguo y cualitativo – tenga en cuenta que las inspecciones de mantenimiento preventivo como "verificar la bomba" dejan a su organización abierta a la confusión, llamadas falsas, malas interpretaciones y un mayor riesgo. Como dijimos anteriormente, hágalo de valor agregado y cuantitativo siempre que sea posible.
Revisiones programadas – Si está realizando revisiones programadas y reemplazando piezas, asegúrese absolutamente de que las piezas que está reemplazando realmente se están desgastando por medios normales. Si reemplaza motores y cajas de engranajes cada seis meses, por si acaso fallan – entonces es probable que esté desperdiciando tiempo valioso, recursos calificados y dinero.
No reemplazas la caja de cambios de tu auto cada seis meses, ¿verdad?
Esa es una excelente descripción general del mantenimiento preventivo en términos de qué es, de dónde proviene, las mejores prácticas y qué debe tener en cuenta.
¿Adónde puedes ir ahora?
Aquellas organizaciones que luchan por la excelencia operativa entienden la necesidad de adoptar la Industria 4.0 y la digitalización del mantenimiento. El mantenimiento preventivo, sus procesos y sus flujos de trabajo encajan perfectamente en este nuevo concepto. Los trabajadores ahora pueden administrar sus PM en el piso de producción en tiempo real con soluciones móviles conectadas a Internet. Los datos dinámicos de mantenimiento preventivo vistos a través de la lente de la industria 4.0 abrirán nuevos caminos para la toma de decisiones ricas en datos en su EAM o CMMS.
Asegúrese de cubrir todos los pasos de la planificación de mantenimiento
Dynaway EAM para Business Central es una solución simple pero intuitiva que es fácil de usar y lo ayuda a cerrar todas las brechas en su planificación de mantenimiento.
¡Pase menos tiempo detrás de la computadora y más tiempo manteniendo sus activos!
-
¿Qué es el Mantenimiento Proactivo?
El mantenimiento proactivo es más que lo opuesto al mantenimiento reactivo bajo demanda. En cambio, es un primo cercano del mantenimiento preventivo, y eso significa que puede brindar muchos de los mismos beneficios, incluida la ayuda para evitar todos los costos y frustraciones del tiempo de inacti
-
¿Cuáles son las funciones importantes del mantenimiento preventivo?
Hubo un tiempo en que la gerencia de la organización y los gerentes solían tomar el mantenimiento muy a la ligera, ¡pero ahora ya no! Hoy en día, las organizaciones contratan gerentes especialmente para que se encarguen del mantenimiento. Los gerentes entienden el valor del mantenimiento adecuado. A
-
¿Qué es el mantenimiento de subestaciones?
El mantenimiento de la subestación es un proceso de inspección periódica y planificada y, si es necesario, reparación y reemplazo de todos los equipos de conmutación, edificios y equipos auxiliares en las instalaciones de la subestación. En términos simples, el mantenimiento de la subestación es un
-
¿Qué es el mantenimiento de planta?
El mantenimiento de la planta generalmente se refiere a los métodos, estrategias y prácticas utilizadas para mantener una fábrica industrial funcionando de manera eficiente. Esto puede incluir cualquier cosa, desde revisiones periódicas de los equipos para asegurarse de que funcionen correctamente,