Endurecimiento por delaminación sinérgica de laminados de fibra de vidrio y aluminio mediante tratamiento de superficie e intercalado de óxido de grafeno
Resumen
Se estudiaron los efectos sinérgicos del tratamiento superficial y el intercalado sobre las propiedades mecánicas interlaminares de los laminados de fibra de vidrio y aluminio. Las láminas de aluminio se trataron con grabado alcalino. Mientras tanto, se introdujo una intercalación de óxido de grafeno (GO) entre la hoja de aluminio y el compuesto epoxi reforzado con fibra de vidrio. Se emplearon ensayos de flexión con doble viga en voladizo y muescas en los extremos para evaluar la tenacidad a la fractura interlaminar de los laminados de fibra de vidrio y aluminio. Los resultados obtenidos muestran que la eficiencia de endurecimiento del intercalado depende de las características de la superficie del aluminio, así como de la carga de GO. Una comparación adicional revela que las tenaces a la fractura de modo I y modo II más altas se obtienen en las muestras con tratamiento de grabado alcalino y adición de intercalado de GO con un 0,5% en peso de carga de GO, que son 510% y 381% más altos en comparación con el plano. muestra. Se observaron superficies de fractura para descubrir aún más los mecanismos de refuerzo.
Introducción
Los laminados de fibra metálica (FML) son un tipo novedoso de compuestos híbridos ligeros, que se componen de sustratos metálicos y plásticos reforzados con fibra (FRP) [1]. Debido a la estructura híbrida, los FML brindan excelentes propiedades mecánicas que incluyen alta resistencia y rigidez específicas, buena resistencia a la fatiga y excelente tolerancia al daño [2, 3]. Sin embargo, una unión interfacial débil de los FML puede causar delaminación y fallas en el despegado debido a las diferencias de propiedades físicas entre la hoja de metal y la capa compuesta [4]. Por tanto, es fundamental mejorar las propiedades mecánicas interlaminares de los FML.
Para mejorar las propiedades mecánicas interlaminares de los FML, una serie de métodos de tratamiento de superficies, tales como grabado ácido o alcalino [5,6,7], anodizado [8], ablación láser [9, 10], tratamiento con agente de acoplamiento de silano [11, 12], y plasma a presión atmosférica [13], se han propuesto para modificar la morfología superficial de las chapas metálicas. Entre estos métodos, el grabado con álcali se considera un método simple y eficiente, que puede eliminar la capa débil de óxido nativo en la superficie del metal, así como crear una superficie rugosa y una capa de óxido estable para fortalecer la unión interfacial. Hoy en día, el desarrollo de la nanotecnología ha ampliado significativamente el dominio de aplicación de los nanomateriales en varios campos, incluidos el aeroespacial [14], los dispositivos electrónicos [15], la energía [16] y el medio ambiente [17]. La incorporación de nanomateriales en la capa interlaminar es otra forma eficaz de mejorar las propiedades interlaminares de los compuestos laminados modificando la región rica en resina. Los nanomateriales intercalados comunes, como la nanoarcilla [18], la fibra de carbono de crecimiento en vapor [19] y el nanotubo de carbono [20], se han utilizado ampliamente en los FML.
El grafeno, que consta de una sola capa de átomos de carbono, exhibe propiedades mecánicas [21], eléctricas [22] y térmicas [23] ultra altas, que lo convierten en un candidato prometedor para modificar la matriz polimérica. Rafiee y col. [24] fabricó los compuestos a granel a base de resina epoxi reforzados con grafeno mediante mezcla de solución. Los resultados demuestran un aumento del 40% y 53% en la resistencia a la tracción y la tenacidad a la fractura de los nanocompuestos, respectivamente. Kostagiannakopoulou y col. [25] adoptó el grafeno como agentes endurecedores en la matriz para preparar polímeros reforzados con fibra de carbono y observó un aumento del 50% en la tenacidad a la fractura interlaminar. Sin embargo, la eficacia de endurecimiento del grafeno depende del estado de dispersión del grafeno en la matriz polimérica. Las propiedades químicas de la superficie del grafeno afectan su compatibilidad interfacial con la matriz polimérica y luego conducen a una mala dispersión del grafeno [26]. Como derivado del grafeno, el óxido de grafeno (GO) contiene varios grupos que contienen oxígeno (hidroxilos, epóxido, carbonilo y carboxílico) en su superficie, lo que le confiere una mejor dispersión y compatibilidad en la matriz polimérica en comparación con el grafeno. Debido a sus ventajas potenciales, GO se ha convertido en un refuerzo eficaz en compuestos poliméricos [27, 28, 29]. Se ha informado de un aumento significativo de la tenacidad a la fractura interlaminar modo I del 170,8% para los laminados de fibra de carbono modificados con intercalación de óxido de grafeno [30]. Pathak y col. reportaron una mejora integral en el módulo de flexión, la resistencia a la flexión y la resistencia al corte interlaminar de los compuestos de fibra de carbono mediante la incorporación de 0,3% en peso de GO [31]. Sin embargo, hasta donde sabemos, las propiedades mecánicas interlaminares de los FML endurecidos por GO interleaf no se han estudiado hasta la fecha. Además, los efectos sinérgicos del tratamiento de la superficie de la placa de metal y la intercalación GO no se han entendido bien.
Los FML estudiados en este trabajo se basan en laminados de fibra de vidrio y aluminio (laminados GFRP / Al) que han sido ampliamente utilizados en diversos campos, como la industria aeroespacial y automotriz. Combinando el tratamiento de grabado con álcali y el intercalado epoxi reforzado con GO, se investigaron sistemáticamente las tenacidad a la fractura interlaminar de modo I y modo II de los laminados de GFRP / Al. Además, se llevaron a cabo varias caracterizaciones para descubrir el mecanismo de endurecimiento sinérgico.
Métodos / Experimental
Materiales
Se utilizaron escamas de grafito natural (XF051, malla 100) compradas a Nanjing XFNANO Materials Tech Co., Ltd., para preparar óxido de grafeno mediante el método modificado de Hummers [32]. El adhesivo epoxi utilizado en este estudio fue diglicidiléter de bisfenol F. EPON862. Se eligió poliamida (Epikure3140A) como agente de curado. Se seleccionaron placas de aleación de Al (7075) con un espesor de 2,5 mm como parte metálica de los FML. Los preimpregnados de fibra de vidrio unidireccionales (preimpregnados de GFRP) fueron proporcionados por Weihai Guangwei Composite Material Co., Ltd, China. Todos los demás materiales, como hidróxido de sodio (NaOH), N , N -dimetilformamida (DMF), acetona, ácido clorhídrico (37% en peso) y trióxido de cromo, fueron suministrados por Chengdu Kelong Chemical Reagent Co., Ltd. (China).
Preparación de la muestra
La fabricación de laminados de GFRP / Al se muestra esquemáticamente en la Fig. 1. Primero, los tratamientos superficiales de las placas de aluminio se llevaron a cabo en los siguientes pasos:(a) las placas de Al se enjuagaron con acetona para desengrasar y luego se secaron en un horno para eliminar la humedad, (b) las placas de Al se sumergieron en una solución de NaOH 0,1 M y se sometieron a ultrasonidos durante 30 min a temperatura ambiente para modificar la morfología de la superficie de las placas de Al, (c) las placas de Al tratadas se sacaron y se sometieron a ultrasonidos en destilado agua hasta que se terminó la reacción de aluminio con NaOH, y (d) las placas de Al lavadas se secaron a 60ºC durante 1 h. Se pueden encontrar más detalles sobre el tratamiento de la superficie mediante grabado alcalino en la Ref. [5].
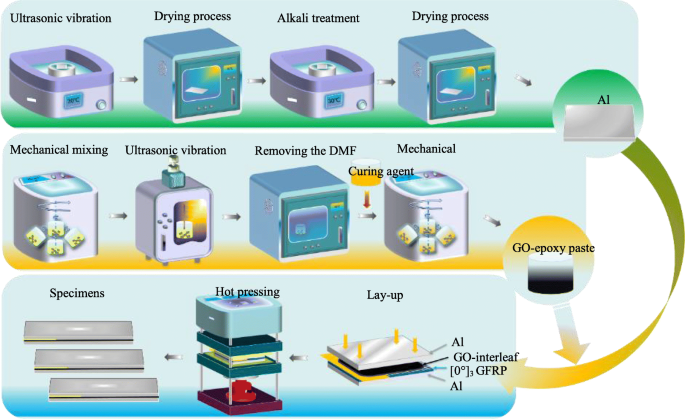
Ilustración esquemática de la fabricación de muestras y el proceso de prensado en caliente
Luego, se fabricó pasta epoxi reforzada con GO como la capa intermedia de endurecimiento. El proceso de preparación detallado de la intercalación de GO es similar al de nuestro trabajo anterior [30]. Los pasos principales incluyen (a) preparar la suspensión de GO / DMF mediante mezcla mecánica y vibración ultrasónica, (b) verter resina epoxi en la suspensión de GO / DMF y mezclarlos mediante una cuerda planetaria y ultrasonidos, (c) calentar la mezcla anterior para eliminar el DMF y (d) agregar el agente de curado con agitación constante.
Finalmente, los FML se prepararon utilizando el método de prensado en caliente como se muestra en la Fig. 1. Los pasos principales incluyen lo siguiente:(a) Se apilaron tres pilas de preimpregnados de GFRP unidireccionales entre dos piezas de placas de aluminio mediante un proceso de laminado. Durante el proceso de fabricación, la pasta GO-epoxi obtenida se untó cuidadosamente en la interfaz de las placas de aluminio y los preimpregnados de GFRP utilizando una cuchilla roma, donde la densidad de área del epoxi se estableció en un valor constante de aproximadamente 167 g / m ^ {2}. . (b) Se insertó una película de liberación para hacer una grieta inicial. (c) Los FML se empaquetaron con una película de poliimida y se curaron a una temperatura de 130 ° C y una presión de 0,12 MPa.
Para explorar los efectos del tratamiento superficial y el intercalado GO-epoxi sobre la tenacidad a la fractura de los FML, se prepararon cinco tipos de muestras, es decir, la llana, GO0.5%, SH-GO0%, SH-GO0.5%, y SH-GO1%, donde "SH" indica el tratamiento de grabado con álcali de las placas de Al, "GO" representa la intercalación de GO-epoxi y el porcentaje después de "GO" indica la fracción en peso de GO en el epoxi.
Pruebas experimentales y caracterización
Se llevaron a cabo ensayos de doble viga en voladizo (DCB) y flexión con muescas en los extremos (ENF) para medir la tenacidad a la fractura interlaminar modo I y modo II de los laminados de GFRP / Al de acuerdo con la Norma Industrial Japonesa (JIS) K7086 [33]. Las configuraciones de las muestras DCB y ENF se muestran en la Fig. 2. Los procedimientos de prueba detallados y los métodos de cálculo de la tenacidad a la fractura son similares a los de la Ref. [33].
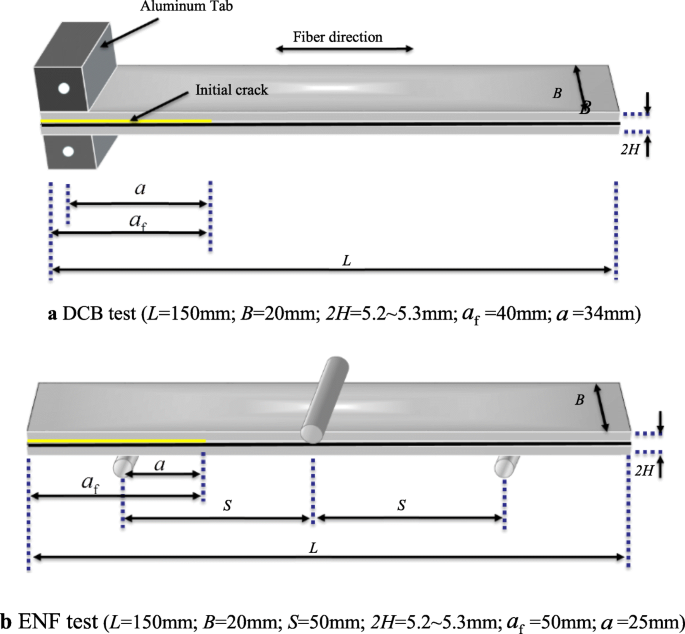
Ilustración esquemática de la muestra para a DCB y b Prueba ENF
Las morfologías de la superficie de las escamas de grafito, GO, la hoja de aluminio y las superficies de fractura de las muestras ensayadas se caracterizaron mediante microscopía electrónica de barrido (SEM). Mientras tanto, las nanoestructuras de las láminas GO se observaron mediante microscopía electrónica de transmisión (TEM) y microscopía de fuerza atómica (AFM). La estructura química de los sustratos de aluminio y GO se caracterizó en un sistema ESCALAB 250Xi XPS (Thermo Electron Corporation, EE. UU.). Además, se estudiaron la rugosidad de la superficie y el rendimiento de humectabilidad de la hoja de aluminio utilizando un perfilador interferométrico óptico y un goniómetro de ángulo de contacto, respectivamente.
Resultados y discusión
Caracterizaciones del GO
Las morfologías de la superficie de las escamas de grafito y GO se caracterizaron por SEM y TEM como se muestra en la Fig. 3. Se puede observar una estructura multicapa de escamas de grafito en la Fig. 3a, mientras que las imágenes SEM y TEM de GO en las Figs. 3b yc exhiben una estructura de capa fina. Esto indica que la estructura multicapa del grafito está estratificada y el óxido de grafeno se ha sintetizado con éxito. La Figura 3d presenta la imagen AFM de la nanoplaca GO. El grosor del GO preparado es de aproximadamente 0,968 nm, lo que indica que se ha logrado una sola capa de nanoestructura de óxido de grafeno después de una exfoliación completa del grafito. Además, el estado de dispersión de GO juega un papel crucial en el endurecimiento de los polímeros. Una dispersión deficiente de GO puede provocar efectos desfavorables en la transición del estrés de la resina a las nanohojas de GO. Por lo tanto, es necesario caracterizar y evaluar el GO disperso. Las Figuras 3e yf muestran las microestructuras de las láminas GO después de la dispersión en resina epoxi. La incorporación de GO a una concentración de 0.5% en peso exhibe una buena dispersión en la resina, mientras que se puede observar una ligera agregación de GO a una concentración más alta (1.0% en peso), lo que puede resultar en concentración de tensión y por lo tanto debilitar la resistencia y tenacidad de el epoxi.
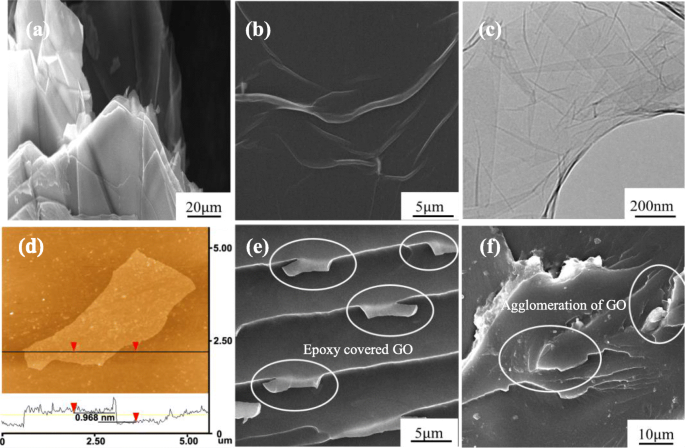
Imágenes SEM de a escamas de grafito. b VAYA sábanas. c Imagen TEM de GO. d Imagen AFM de GO. e GO hojas en resina epoxi (0,5% en peso). f GO hojas en resina epoxi (1,0% en peso)
La estructura química en la superficie de GO es otro factor importante que afecta la eficiencia de endurecimiento de GO en los polímeros, que es responsable de la interacción interfacial entre GO y la matriz de resina [30, 31, 34]. Se empleó espectroscopía de fotoelectrones de rayos X (XPS) para identificar la propiedad química de la superficie del GO preparado. Como se muestra en la Fig. 4, el espectro C 1s de GO se divide en cuatro picos que se asignan a cuatro tipos de enlaces de carbono:(1) C – C / C =C (284.5 eV), (2) C – O ( 286,9 eV), (3) C =O (288,2 eV) y (4) O – C =O (289 eV) [35]. La presencia de grupos funcionales oxigenados es beneficiosa para la dispersión de GO y la fuerza de unión entre GO y la matriz polimérica [30, 31, 34]
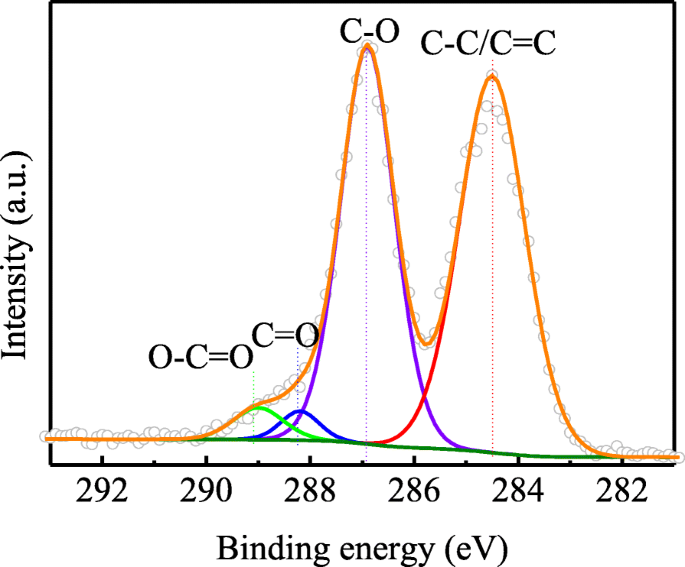
Espectro de XPS C1s de las hojas GO
Propiedades físicas y químicas de la superficie de la aleación de aluminio
En general, la separación interfacial entre el compuesto de FRP y el metal implica fallas tanto interfaciales como cohesivas, que comúnmente se ven afectadas por las características de la superficie de la hoja de metal. Por lo tanto, las propiedades fisicoquímicas, incluida la microestructura de la superficie, la rugosidad, la composición química y la humectabilidad de la superficie de la aleación de aluminio, se caracterizaron mediante varios instrumentos de medición.
La Figura 5 muestra la morfología de la superficie y la microestructura de las placas de aleación de Al antes y después del grabado con álcali. Como puede verse, la superficie de la aleación de Al tratada mediante grabado con álcali se vuelve más rugosa que la de la superficie de la aleación de Al desengrasante. Se pueden observar muchos orificios y valles a microescala en la superficie de la aleación de Al tratada por grabado alcalino, que son favorables para el relleno de resina epoxi y GO para formar un enclavamiento mecánico y mejorar la fuerza de unión de la interfaz compuesto / metal [ 7, 19, 36]. Además, los perfiles superficiales de las placas de aleación de Al antes y después del ataque con álcali también se midieron utilizando el perfilador óptico interferométrico. Los correspondientes valores de rugosidad de la superficie ( R a , R q y R z ) se resumen en la Tabla 1, donde R a representa la desviación media aritmética del perfil, R q es la rugosidad cuadrática media de la raíz y R z representa la altura de diez puntos de las irregularidades. En la Tabla 1 se puede observar una diferencia significativa en los valores medidos antes y después del grabado con álcali, lo cual es consistente con los resultados de observación de SEM en la Fig. 5. La alta rugosidad de la superficie de grabado con álcali implica un aumento en el área de superficie específica que es beneficiosa para el enclavamiento mecánico entre la hoja de aleación de Al y la matriz de polímero.
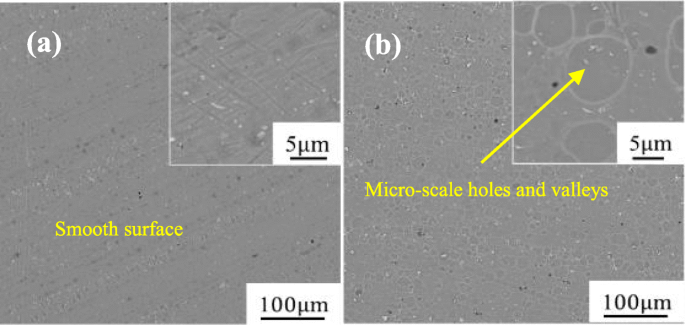
Imágenes SEM de la superficie de Al después de a desengrasante y b grabado alcalino
Se realizó XPS para analizar la modificación química de la superficie de la aleación de Al con diferentes tratamientos superficiales. La Figura 6 presenta el espectro de barrido estrecho de Al 2p y O 1s para las superficies de aleación de Al sin grabar y grabadas. La Figura 6a muestra los espectros de ionización de Al 2p sin convolucionar de superficies no grabadas, que solo tiene un pico con una energía de enlace de 74,4 eV correspondiente a γ-óxidos de aluminio (γ-Al 2 O 3 ) [37]. El espectro de O 1s de la superficie sin grabar se divide en 2 picos, que se asignan a Al 2 O 3 (531,3 eV) e hidróxido de aluminio (533,1 eV), respectivamente [13].
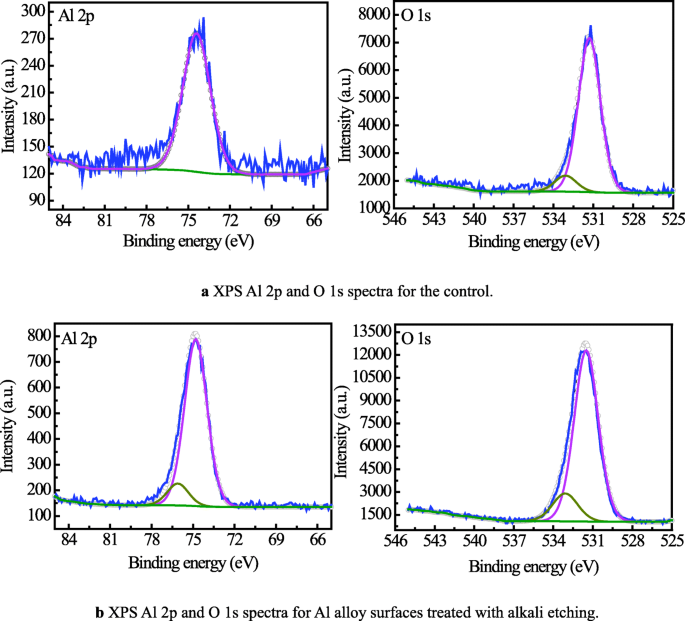
Escaneo estrecho de espectros XPS de superficie de aleación de Al
La Figura 6b muestra los espectros de ionización de Al 2p desenrollados de la superficie grabada, donde el primer pico ubicado a 74,8 eV está asociado a Al 2 O 3 , y el pico a 76,1 eV corresponde al hidróxido de aluminio [38]. Los espectros de O 1s de las superficies grabadas muestran dos picos, uno para Al 2 O 3 (531,5 eV) y el otro para hidróxido de aluminio (533,1 eV) [13]. Comparando los resultados de la superficie de la aleación de Al no grabada y grabada, un cambio en la energía de unión del Al 2p implica que la propiedad química de la superficie de la aleación de Al ha sido modificada por el tratamiento de la superficie [6]. Mientras tanto, las relaciones de intensidad de hidróxido a óxido del pico de O 1s de las superficies grabadas son más altas que las de las superficies no grabadas, lo que podría mejorar la adhesión interfacial debido a la formación de más enlaces de hidrógeno entre los grupos hidroxilo en hidróxido de aluminio y epoxi. moléculas [13].
Para investigar el efecto del tratamiento superficial sobre la humectabilidad de la superficie de la aleación de Al, se dejaron caer gotas estándar sobre la superficie de las muestras probadas para medir los ángulos de contacto. La Figura 7 presenta la imagen de los ángulos de contacto estáticos para la superficie de la aleación de Al antes y después del grabado con álcali. Se puede encontrar que la superficie de la placa de Al tratada con álcali tiene un ángulo de contacto más pequeño, lo que implica una mejor humectabilidad de la superficie de la aleación de Al con el tratamiento de grabado con álcali. La mayor humectabilidad también puede contribuir a mejorar la fuerza de unión interfacial [6].
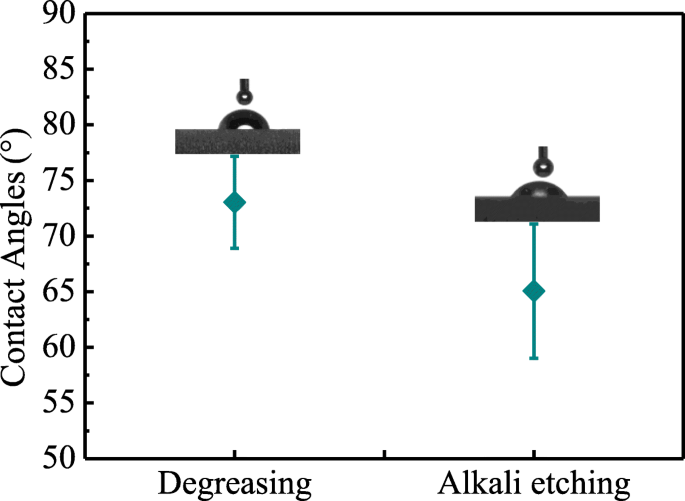
Ángulo de contacto de la gota de agua en la superficie de la aleación de Al con diferentes tratamientos superficiales
Resistencia a la fractura interlaminar en Modo I
Las pruebas de DCB se realizaron en diferentes tipos de laminados de GFRP / Al. La Figura 8 muestra la relación entre la carga P y desplazamiento de apertura de fisuras (COD). Se puede encontrar la tendencia general en la carga y el desplazamiento de apertura de la fisura ( P -COD) la respuesta de las muestras de FML es casi similar, es decir, la carga aplicada primero aumenta linealmente y luego aumenta ligeramente en un patrón no lineal hasta que la carga alcanza el máximo, seguido de una disminución gradual en la etapa final. Debido a la incertidumbre del inicio del crecimiento de la grieta, la carga crítica ( P C ) se define como la intersección de la P -Curva COD con una línea correspondiente a un cumplimiento 5% superior al inicial [33].
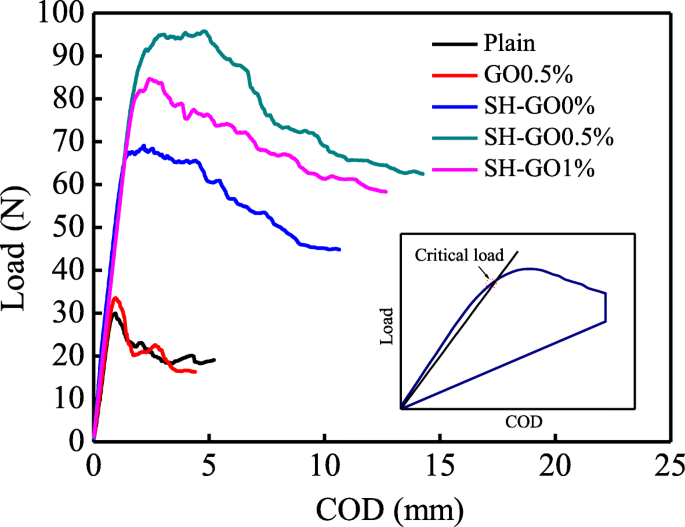
Carga representativa y desplazamiento de apertura de fisuras ( P -COD) para diferentes muestras durante las pruebas DCB
La Figura 9 presenta la carga crítica P C de las probetas ensayadas. Podemos ver que la P C para el espécimen GO0.5% es similar al simple, que es mucho menor que los de los otros tipos de especímenes. Después de pretratar la aleación de aluminio mediante grabado alcalino, el P C de la muestra de SH-GO0% aumenta significativamente, lo que indica un papel importante desempeñado por el tratamiento de la superficie en la adhesión interfacial. Vale la pena señalar que la carga crítica P C para la muestra SH-GO 0,5% se incrementa aún más cuando se combina el grabado con álcali y la adición de 0,5% en peso de GO, y el P más alto obtenido C es aproximadamente un 160% más alto que los de la muestra simple y GO 0,5%, lo que indica un posible efecto de endurecimiento sinérgico entre el tratamiento de superficie y la intercalación GO. Sin embargo, la P C disminuye con un aumento adicional del contenido de GO (SH-GO1%), que podría atribuirse a la aglomeración de GO en una concentración más alta.
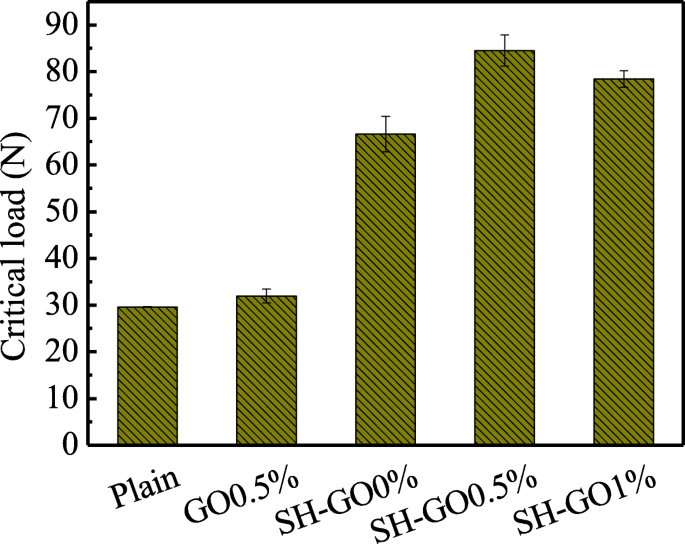
Carga crítica P C para varias muestras durante las pruebas DCB
La Figura 10 representa la tenacidad a la fractura en modo I como una función del incremento de crecimiento de la grieta ∆ a ( R -curva) para las muestras analizadas. Como puede verse, para la muestra simple y GO0.5%, la tenacidad a la fractura en modo I es independiente del incremento de crecimiento de la grieta ∆ a , que también indica la unión interfacial débil entre la aleación de aluminio desengrasada y los laminados de fibra de vidrio. Sin embargo, para los otros tipos de muestras, se puede observar un comportamiento de fractura típico, donde la tenacidad a la fractura en modo I aumenta primero con el crecimiento de la grieta y luego se vuelve estable debido al efecto de puenteo de la fibra de vidrio.
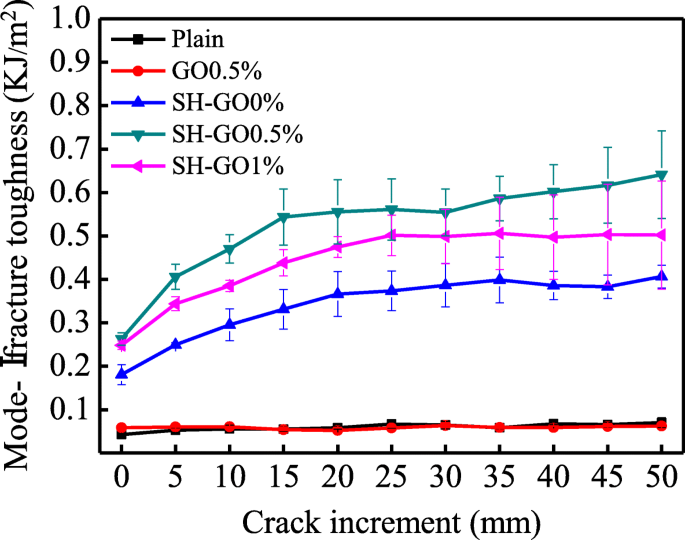
Comparación de la R -curvas para varias muestras durante las pruebas DCB
Para comprender mejor los efectos del tratamiento superficial y el intercalado GO sobre las propiedades mecánicas interlaminares de los laminados de GFRP / Al, la tenacidad a la fractura de modo I G IC y resistencia a la fractura G IR se resumen en la Fig. 11, donde G IC es el valor de inicio en la R -curva y G IR es el valor medio de cinco puntos dentro del rango de extensión de la grieta ∆ a de 20 a 40 mm. Como puede verse en la Fig. 11, no hay una diferencia significativa en G IC y G IR entre el espécimen simple y GO0.5%. Sin embargo, aumentos sustanciales de 225% y 600% en G IC y G IR para la muestra de SH-GO0% se puede observar cuando las placas de aleación de Al se trataron con el grabado químico alcalino. Esta mejora se debe al hecho de que la morfología y la química de la superficie, así como la humectabilidad de las placas de aleación de Al, se mejoran mediante el tratamiento de grabado alcalino como se describe en la sección “Tenacidad a la fractura interlaminar Modo I”. Para las muestras de endurecimiento sinérgico (SH-GO0.5% y SH-GO1%), tanto el G IC y G IR son mucho más altos que los de las muestras endurecidas con tratamiento de superficie solo (SH-GO0%) o solo con intercalación de GO (GO0,5%), lo que puede atribuirse a los efectos sinérgicos del tratamiento de superficie (adhesión interfacial mejorada) y el GO interleaf (matriz epoxi endurecida). El máximo de G IC y G IR observados en muestras SH-GO 0,5% son 263 J / m 2 y 590 J / m 2 , respectivamente, que son aproximadamente un 510% y un 820% más altos que los de la llanura, respectivamente.
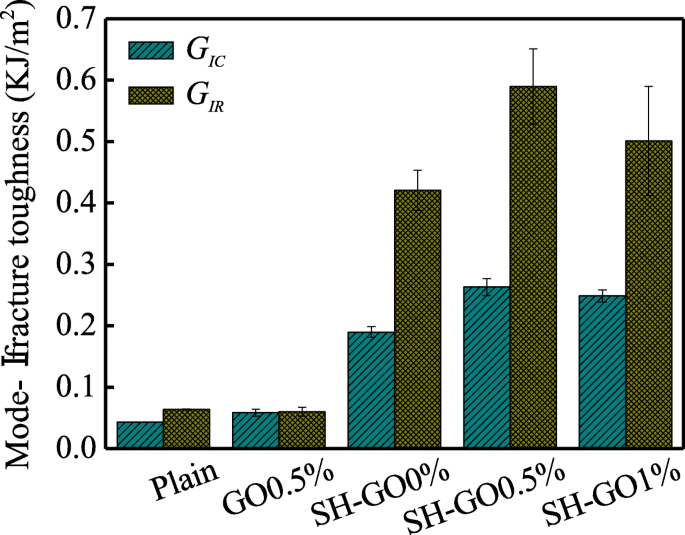
Comparación de la tenacidad y resistencia a la fractura en modo I para varias muestras
Resistencia a la fractura interlaminar en Modo II
Las curvas de carga-deflexión de Modo II de las muestras ENF se muestran en la Fig. 12. Normalmente, las curvas de carga-deflexión muestran una respuesta lineal en la etapa inicial, y luego una respuesta no lineal hasta la carga máxima, seguida de una caída abrupta en la etapa final. La Figura 13 muestra la carga crítica P C y tenacidad a la fractura interlaminar de modo II G IIC de las probetas ensayadas calculadas a partir de los perfiles de carga-deflexión. Cabe señalar que el criterio para definir la carga crítica P C para las muestras ENF es similar a la de las muestras DCB. Podemos ver que tanto G IIC y P C de las muestras ENF tienen la misma tendencia que las de las muestras DCB. Los valores máximos de la tenacidad a la fractura modo II y la carga crítica se observan en la muestra de SH-GO0.5%, que son 381% y 99% más altos que los de la muestra simple, respectivamente.
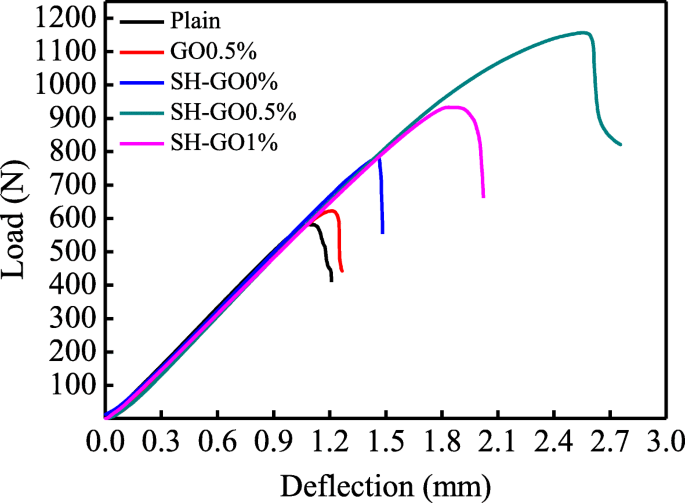
Curvas representativas de carga-deflexión para diferentes muestras durante las pruebas ENF
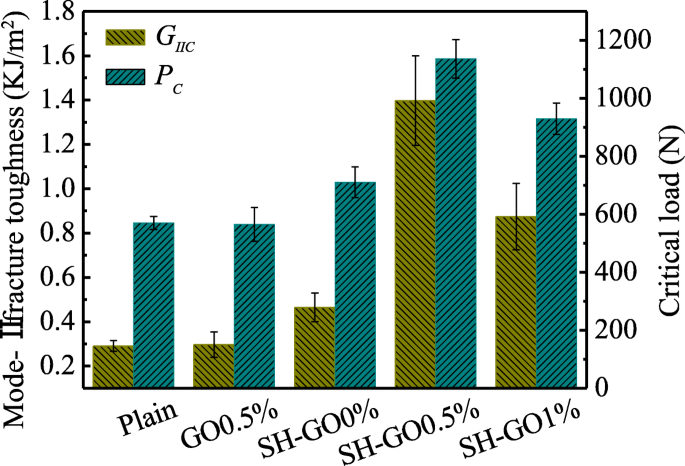
Comparación de la tenacidad a la fractura en modo II G IIC y carga crítica P C para varias muestras durante las pruebas ENF
Observación de la morfología de la fractura
Para revelar aún más los mecanismos de endurecimiento, se observaron mediante SEM las morfologías de fractura de los laminados de GFRP / Al probados.
La Figura 14 muestra las superficies de fractura de las muestras GO0.5%, SH-GO0%, SH-GO0.5% y SH-GO1% después de las pruebas DCB. Con respecto a la muestra de GO0.5% (ver Fig. 14a yb), la superficie de la fractura tiene un aspecto suave, sin fibra de vidrio o resina epoxi visible adherida a la superficie de las placas de aleación de Al. El tipo de falla de la muestra GO0.5% es la falla del adhesivo. En cuanto a la muestra de SH-GO0% (ver Fig.14c yd), se pueden observar algunas fibras rotas y resina epoxi adheridas a la superficie o incrustadas en los micro-huecos, lo que indica que el grabado con álcali podría promover el enclavamiento mecánico entre el Al placa de aleación y matriz de polímero y luego mejorar la unión interfacial entre ellos. El tipo de falla de la muestra SH-GO0% es una combinación de cohesivo y adhesivo. La falla cohesiva causada por el desprendimiento de moléculas de resina puede consumir más energía en comparación con la falla interfacial [19], lo que indica que la muestra de SH-GO0% tiene una mayor tenacidad a la fractura en modo I en comparación con la muestra de GO.5%. Con respecto a las muestras SH-GO0.5% y SH-GO1% (ver Fig. 14e-h), se puede observar una morfología de fractura más irregular y rugosa, que creará un área de fractura más grande y requerirá una fuerza impulsora mayor y energía. El tipo de falla de las muestras SH-GO0.5% y SH-GO1% es una falla casi cohesiva, lo que indica que la adición de la intercalación GO puede mejorar aún más la tenacidad a la fractura interlaminar de los laminados de GFRP / Al con el tratamiento de superficie. Las posibles razones son las siguientes:Debido a sus excelentes propiedades mecánicas, GO puede mejorar efectivamente la tenacidad de la resina epoxi al inducir la desviación de la fisura y el efecto de puenteo de la fisura [30], que comúnmente requiere una mayor fuerza impulsora y una mayor energía de fractura. Mientras tanto, los grupos funcionales en la superficie de las láminas GO contribuirán a la fuerte unión interfacial entre GO y la resina epoxi, que puede consumir más energía durante el proceso de extracción de GO de la matriz epoxi. Además, la adición de GO aumenta los grupos funcionales reactivos de la matriz de resina [39, 40]. Por lo tanto, la tenacidad a la fractura en modo I para las muestras SH-GO0.5% y SH-GO1% aumenta aún más en comparación con la muestra SH-GO0%.
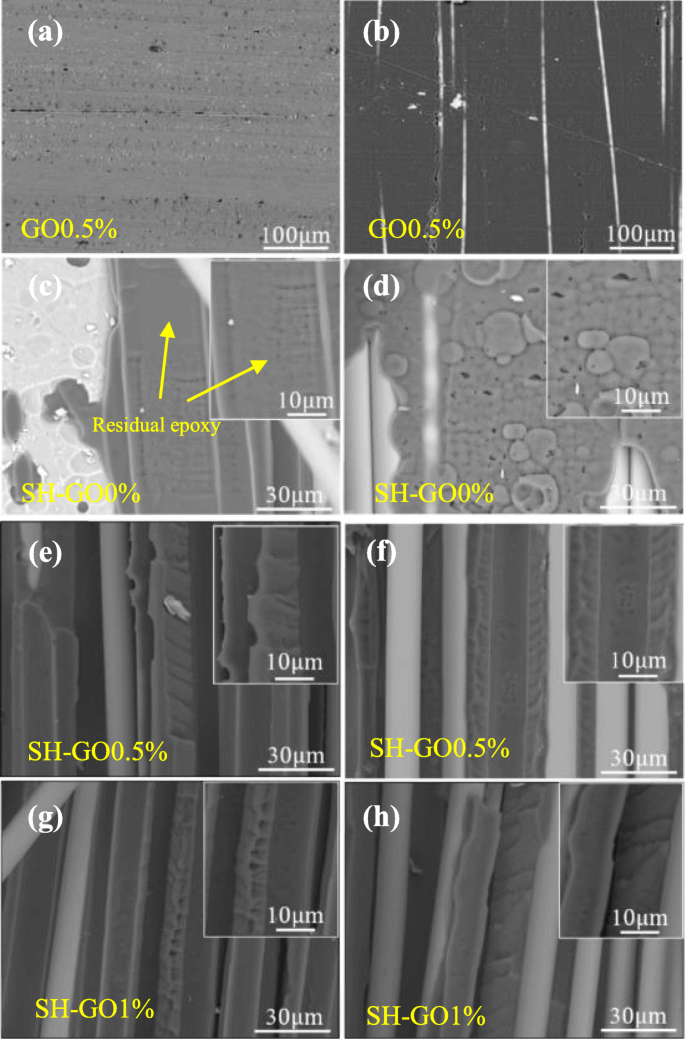
Superficies de fractura de laminados de GFRP / Al modo I. a, b GO0.5%. c , d SH-GO0%. e , f SH-GO 0,5%. g , h SH-GO1% (izquierda, lado Al; derecha, lado compuesto)
Sobre la base del análisis anterior, se ha demostrado el efecto sinérgico del tratamiento de superficie y el intercalado de GO-epoxi en la mejora de la tenacidad a la fractura interlaminar de modo I de los laminados de Al / GFRP. Sin embargo, una GO excesiva puede tener un efecto negativo en la tenacidad de la fractura. Debido a que la agregación de GO puede causar concentración de tensión y reducir la tenacidad del epoxi (ver Fig.3), la tenacidad a la fractura de modo I de SH-GO1% es menor que la de la muestra de SH-GO0.5%.
También se empleó SEM para investigar las superficies de fractura ENF de las muestras probadas. Para la muestra de GO0.5% (Fig. 15a yb), las superficies de fractura en la placa de Al y el lado de GFRP son relativamente lisas, que es similar a la morfología de fractura DCB de la muestra de GO0.5%. Se pueden observar fibras rotas y epoxi residual adherido en las superficies de la placa de Al para las muestras de SH-GO0% (Fig.15c), SH-GO0.5% (Fig.15e) y SH-GO1% (Fig.15g). ), lo que implica la aparición de fallas cohesivas y una mayor tenacidad a la fractura en comparación con la muestra de GO0.5%. Además, hay muchos labios de cizallamiento típicos en las superficies de las placas de Al y los lados de material compuesto para las muestras SH-GO0.5% y SH-GO1%, lo que indica un aumento de la zona de daño y una mayor deformación plástica, que puede conducir a una tenacidad a la fractura en modo II superior a la del SH-GO0%. Además, la agregación de GO también puede ser la razón principal de la menor tenacidad a la fractura en modo II de la muestra SH-GO1% en comparación con la muestra SH-GO0.5%.
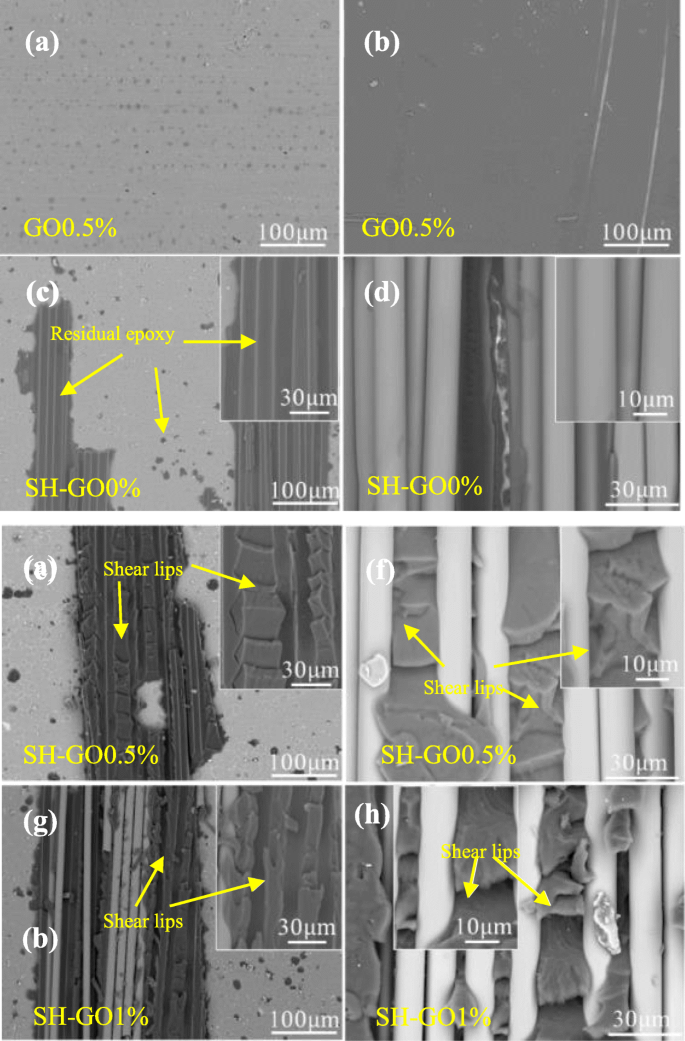
Superficies de fractura de los laminados de GFRP / Al modo II. un , b GO0.5%. c , d SH-GO0%. e , f SH-GO 0,5%. g , h SH-GO1% (izquierda, lado Al; derecha, lado compuesto)
Conclusiones
En este estudio, el tratamiento de la superficie, por ejemplo, el grabado con álcali y la intercalación de GO-epoxi se combinaron para mejorar sinérgicamente las propiedades mecánicas interlaminares de los laminados de Al / GFRP. Los resultados de DCB y ENF demuestran que las muestras con el tratamiento de grabado alcalino y la intercalación de epoxi GO0.5% poseen la más alta tenacidad a la fractura interlaminar de modo I y modo II, que son 510% y 381% más altas que las de la hoja plana. espécimen, respectivamente. In addition, different characterization technologies were employed to investigate the surface properties of the Al plates and the fracture surface of the tested laminates to uncover the synergistic toughening mechanisms.
Disponibilidad de datos y materiales
Los conjuntos de datos que respaldan las conclusiones de este artículo se incluyen dentro del artículo.
Abreviaturas
- Al:
-
Aluminio
- FRPs:
-
Fiber-reinforced plastics
- GFRP/Al laminates:
-
Glass fiber-aluminum laminates
- GFRP prepregs:
-
Glass fiber prepregs
- GO:
-
Óxido de grafeno
- DCB:
-
Double cantilever beam test
- ENF:
-
End-notched flexure test
- XPS:
-
Espectroscopia de fotoelectrones de rayos X
- SEM:
-
Microscopio electrónico de barrido
- TEM:
-
Microscopía electrónica de transmisión
- AFM:
-
Microscopía de fuerza atómica
- FMLs:
-
Fiber metal laminates
- NaOH:
-
Sodium hydroxide
- DMF:
-
N , N -dimetilformamida
- JIS:
-
Japanese Industrial Standards
- P -COD:
-
Load and crack opening displacement
- G IC :
-
Mode-I fracture toughness
- G IR :
-
Mode-I fracture resistance
- G IIC :
-
Mode-II fracture toughness
- P C :
-
Critical load
- γ-Al2 O 3 :
-
γ-Aluminum oxides
- SH:
-
Alkali etching treatment of Al plates
- R a :
-
The arithmetic average deviation of the profile
- R q :
-
The root mean square roughness
- R z :
-
The ten-point height of irregularities
Nanomateriales
- Grafeno en altavoces y auriculares
- Nanotubos de titanato Nanocompuestos de óxido de grafeno decorados:preparación, retardo de llama y fotodegradación
- Ajuste de la química superficial de la polieteretercetona mediante revestimiento de oro y tratamiento con plasma
- Bioseguridad y capacidad antibacteriana del grafeno y el óxido de grafeno in vitro e in vivo
- Evaluación de estructuras de grafeno / WO3 y grafeno / ceO x como electrodos para aplicaciones de supercondensadores
- Preparación de molienda de bolas en un solo paso de óxido de grafeno / CL-20 a nanoescala para una sensibilidad y un tamaño de partículas significativamente reducidos
- Preparación de polimerización in situ de nanocompuesto de polietileno / grafeno de peso molecular ultra alto mediante una estructura esférica y en sándwich Soporte de grafeno / Sio2
- Reducción de la conductividad de protones mejorada y la permeabilidad del metanol mediante biomembrana de óxido de grafeno sulfonado con electrolito de alginato de sodio
- Reducción de óxido de grafeno a baja temperatura:Conductancia eléctrica y microscopía de fuerza de sonda Kelvin de barrido
- Redistribución del campo electromagnético en nanopartículas metálicas sobre grafeno
- Una bomba de agua nanométrica inducida por el movimiento browniano y no browniano de una hoja de grafeno en una superficie de membrana