Fabricación y caracterización de un nuevo catalizador anódico compuesto de nanofibras de carbono Tio2 para celdas de combustible de metanol directo mediante el método de electrohilado
Resumen
El platino (Pt) es el catalizador común que se usa en una celda de combustible de metanol directo (DMFC). Sin embargo, el Pt puede conducir al envenenamiento del catalizador por especies carbonáceas, por lo que reduce el rendimiento de DMFC. Por lo tanto, este estudio se centra en la fabricación de un nuevo compuesto TiO 2 Soporte de catalizador anódico de nanofibras de carbono para pilas de combustible de metanol directo (DMFC) mediante técnica de electrohilado. La distancia entre la punta y el colector (DTC) y el caudal se examinaron como parámetros que influyen en la técnica de electrohilado. Para garantizar que se fabrique el mejor material catalítico, la nanofibra se sometió a varias caracterizaciones y pruebas electroquímicas, incluidas FTIR, XRD, FESEM, TEM y voltamperometría cíclica. Los resultados muestran que D18, fabricado con un caudal de 0,1 mLhr −1 y DTC de 18 cm, es una nanofibra ultrafina con el diámetro medio más pequeño, 136,73 ± 39,56 nm. Presentó la actividad catalizadora más alta y el valor de área superficial activa electroquímica con 274,72 mAmg −1 y 226,75 millones 2 g −1 PtRu , respectivamente, en comparación con las otras muestras.
Antecedentes
La pila de combustible de metanol directo (DMFC) es uno de los futuros sistemas de generación de energía renovable y muy respetuoso con el medio ambiente. El sistema genera energía eléctrica utilizando un combustible líquido (metanol) directamente sin ningún dispositivo adicional o procesos de combustión. Las ventajas de los DMFC son su simplicidad, alta energía específica, baja temperatura de funcionamiento y fácil arranque con repostaje instantáneo [1]. Sin embargo, los sistemas DMFC todavía adolecen de varias limitaciones, como el envenenamiento del catalizador y la cinética de reacción lenta, que hacen que el sistema tenga un rendimiento y una potencia de salida bajos [2]. Ambas limitaciones se deben al catalizador y al material utilizado en este sistema.
El platino (Pt) es el catalizador común utilizado en DMFC. Sin embargo, el Pt puede conducir al envenenamiento del catalizador por especies carbonáceas, por lo que reduce el rendimiento de DMFC. Más tarde, se introduce platino-rutenio (PtRu) para aumentar la velocidad de reacción, pero el parámetro cinético del catalizador sigue siendo uno de los principales problemas en DMFC. Por tanto, la alteración hacia este catalizador bimetálico comienza a situarse en el campo del catalizador DMFC. Uno de los enfoques más atractivos entre los investigadores es la introducción del óxido metálico y los nanomateriales como componente catalizador lateral. Dióxido de titanio (TiO 2 ) es un óxido metálico que está ganando mucha atención por parte de los desarrolladores de investigación. TiO 2 tiene varias propiedades beneficiosas, que es no tóxico, no inflamable y altamente resistente a la corrosión [1], puede aumentar la estabilidad electroquímica y térmica [3] y afectar las propiedades electrónicas y el mecanismo bifuncional de los catalizadores compuestos [4]. Ito y col. [5] desarrolló PtRu / TiO 2 -nanofibras de carbono incrustadas (CNF) (PtRu / TECNF), y Ercelik et al. [6] presentó el PtRu / C-TiO 2 como electrocatalizador en la aplicación DMFC, y el resultado muestra que el rendimiento de este nuevo electrocatalizador compuesto es superior al catalizador PtRu.
El nanomaterial es una de las nanotecnologías que fascina en una amplia gama de aplicaciones, incluida la conversión de energía. Existen numerosos tipos de nanomateriales en el campo de la conversión de energía, que son nanofibras, nanotubos, nanocables, nanovarillas y otros. Este material se convierte en la principal atracción en la investigación de materiales energéticos debido a la reducción dimensional a la escala nanométrica que puede afectar muchos pasos elementales, incluida la transferencia de carga y el reordenamiento molecular, así como las propiedades de la superficie para proporcionar fracciones de alto volumen interfacial y velocidades de reacción mejoradas [ 7]. Este estudio se centra en las estructuras de nanofibras para ambos materiales, TiO 2 óxido de metal y carbono. Esto se debe a las propiedades especiales de las nanofibras que pueden proporcionar relaciones de aspecto / superficie / volumen elevadas [7], alta conductividad eléctrica, buena resistencia mecánica y dispersión uniforme del catalizador, lo que puede aumentar la actividad electrocatalítica [8].
Las nanofibras se pueden producir mediante varios procesos, incluido el soplado en fusión, la polimerización interfacial, el electrohilado y la precipitación de polímeros inducida por antidisolventes [9]. Recientemente, el electrohilado es la principal elección entre los investigadores debido al gran beneficio de producir estructuras de nanofibras ultrafinas. El electrohilado es un proceso único para la formación de fibras con diámetros de escala submicrónica (en el rango de nanómetros a micrómetros) utilizando soluciones a base de polímeros o fundidos mediante fuerzas electrostáticas [10]. Hay tres componentes principales para el electrohilado:una fuente de alimentación de alto voltaje (varias decenas de kV), la hilera (jeringa con una aguja) y un colector conectado a tierra (p. Ej., Placa o colector giratorio) [11, 12]. La Figura 1 ilustra el proceso general y la configuración para el proceso de electrohilado. Por lo tanto, el electrohilado es popular debido a su procedimiento simple, versátil, de alto rendimiento, eficaz y con un proceso más económico [7, 13].
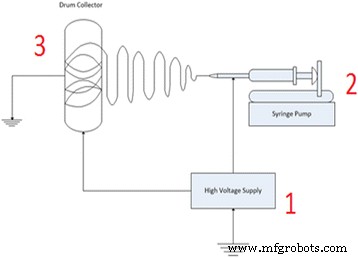
Configuración de electrohilado para todos los componentes principales
Este proceso tiene varios parámetros que se pueden ajustar para obtener las estructuras óptimas de nanofibras, ya sea por diámetro o morfología superficial, y los parámetros de influencia son diferentes para cada material. Los parámetros se pueden dividir en tres categorías principales:solución, ambiente y parámetros de proceso. Este estudio se centra en los parámetros del proceso, y el caudal de la solución y la distancia entre la punta de la aguja y el colector (DTC) fueron elegidos como los principales parámetros de influencia para obtener el diámetro más pequeño. Esto se debe a la escasa investigación centrada en estos parámetros [14], aunque se han considerado como las principales variables para la obtención de nanofibras ultrafinas [15,16,17,18].
Así, este estudio presenta el compuesto TiO 2 nanofibra de carbono como soporte del catalizador en el electrodo del ánodo. Se espera que esta combinación del material compuesto aumente la actividad electrocatalítica y reduzca el envenenamiento del catalizador con el fin de impulsar el rendimiento general de DMFC. Los principales objetivos de este estudio son fabricar el diámetro de nanofibras más pequeño posible para aumentar el área de superficie y proporcionar un punto más activo para la reacción catalítica y mejorar el rendimiento de DMFC. La fabricación de nanofibras implica varios pasos, incluidos los procesos de sol-gel, electrohilado, estabilización y carbonización. Para obtener las nanofibras de menor diámetro, los parámetros de electrohilado de caudal y DTC se toman como las principales variables en este estudio. Las nanofibras preparadas se caracterizan por espectroscopía infrarroja por transformada de Fourier (FTIR), difracción de rayos X (XRD) y microscopía electrónica de barrido (FESEM). Todos los soportes de catalizador con diferente parámetro de electrohilado se depositan en PtRu (PtRu / TiO 2 -CNF) y evaluados mediante análisis electroquímico de superficie activa (ECSA) y voltamperometría cíclica (CV) para evaluar el rendimiento y determinar su potencial como soportes catalíticos en DMFC. Los resultados experimentales muestran el efecto de los parámetros de electrohilado sobre el diámetro de la nanofibra, así como su potencial en aplicaciones DMFC.
Métodos / Experimental
Materiales
Se obtuvieron poli (acetato de vinilo) (PVAc, Mw =500.000), dimetilformamida (DMF, 99,8%), isopropóxido de titanio (TiPP, 97% de contenido), ácido acético (99,7%) y precursor de Ru (45-55% de contenido). de Sigma-Aldrich Co., Ltd., mientras que el precursor de Pt (40% de contenido) y el etanol (99,8%) se recibieron de Merck, Alemania y R&M Chemical Reagents, respectivamente. Todos los productos químicos se utilizaron sin más purificación. El aparato principal, la máquina de electrohilado, tiene la marca Nfiber N1000, Progene Link Sdn. Bhd., Y la trituradora de celdas ultrasónica INS-650Y es de INS Equipments Trading Co., Ltd., China.
Preparación de TiO 2 -Nanofibras CNF
El método sol-gel comienza con la preparación de una solución de polímero, en la que se disolvió PVAc (11,5% en peso), como fuente de carbono, en el disolvente, DMF. La solución de polímero se agitó a 60ºC durante 1 hora y luego se agitó durante la noche a temperatura ambiente. El TiO 2 el precursor, el TiPP y la solución de polímero se mezclaron en una proporción de 1:1 y se añadió una pequeña cantidad de ácido acético y etanol a la solución de polímero. La mezcla se homogeneizó mediante una trituradora de células ultrasónica durante 60 s. Luego, la solución se transfirió a una jeringa para inyección en una unidad de electrohilado de nanofibras. El voltaje aplicado fue de 16 kV, mientras que el caudal y el DTC se manipularon en el rango de 0,1 a 0,9 mLh −1 y 14-18 cm. El caudal se estableció en 0,1, 0,5 , y 0,9 mLh −1 , denotados F0.1, F0.5 y F0.9, respectivamente. Las muestras con valores de DTC de 14, 16 y 18 cm se denominan D14, D16 y D18, respectivamente. La nanofibra fabricada se dejó reposar durante 5 ha temperatura ambiente antes de estabilizarse durante 8 ha 130 ° C. La nanofibra estabilizada se carbonizó a 600 ° C durante 2 h bajo una atmósfera de nitrógeno usando un horno de tubo y luego se trituró con mortero y maja durante 5 min antes de su uso posterior en este estudio. La carga de masa para todas las muestras es la misma, que es de 6,67 mg −1 .
Deposición de catalizador
El TiO 2 Se añadieron nanofibras de CNF a una mezcla de alcohol isopropílico (IPA) y agua desionizada (agua desionizada) y se sometieron a ultrasonidos en un baño ultrasónico durante 20 min. El precursor del catalizador de platino y rutenio (20% en peso con una relación 1:1) se mezcló con la solución y se agitó durante 20 min. Luego, se ajustó el pH de la solución mezclada con solución de NaOH hasta alcanzar pH 8. Se elevó la temperatura a 80 ° C, y 25 ml de NaBH 4 0,2 M se añadió gota a gota a la solución mixta. La solución se agitó durante otra hora más. Después, la mezcla se enfrió, se filtró y se lavó repetidamente. El catalizador en polvo se secó a 120 ° C durante 3 hy finalmente se trituró con un mortero y maja para obtener un catalizador en polvo fino que estaba listo para usar en las pruebas de rendimiento.
Caracterización del catalizador
El compuesto químico en el soporte del catalizador se identificó mediante espectroscopia infrarroja por transformada de Fourier (FTIR, PerkinElmer) y se utilizó difracción de rayos X (XRD, D8 Advance / Bruker AXS, Alemania) para analizar el patrón y la estructura cristalina de las muestras. La morfología y la distribución del tamaño de las muestras se analizaron mediante microscopía electrónica de barrido por emisión de campo (FESEM, SUPRA 55VP). Se utilizó microscopía electrónica de transmisión (TEM, Tecnai G2 F20 X-Twin) para observar la estructura detallada y la distribución elemental de las nanofibras.
Evaluación de la medición electroquímica
El rendimiento se midió para todos los catalizadores fabricados con diferentes parámetros. El catalizador de PtRu se depositó en el TiO 2 -Soporte de catalizador CNF para evaluación mediante medidas electroquímicas. Estas medidas se obtuvieron usando un sistema de celda de tres electrodos, que usa voltamperometría cíclica (CV) para examinar la actividad del catalizador en la reacción de oxidación de metanol (MOR) usando una estación de trabajo electroquímica Autolab. El sistema de celda de tres electrodos se hizo funcionar a temperatura ambiente e incluyó un electrodo de Pt, plata / cloruro de plata (Ag / AgCl) y carbono vítreo (GCE, 3 mm de diámetro) como electrodo contador, de referencia y de trabajo. Antes de comenzar la medición, el GCE se limpió con alúmina y papel de pulir, trazando un patrón redondeado que se asemeja al número "ocho", varias veces. Luego, el GCE se enjuagó con agua desionizada y se sonicó durante 30 s antes de su uso. La tinta de catalizador para el GCE se preparó dispersando 15 mg de catalizador en una mezcla de 400 µl de agua DI, 400 µl de IPA y 125 µl de solución de Nafion (5% en peso) durante 30 min. Luego, se aplicaron 2,5 µl de tinta de catalizador sobre el GCE usando una micropipeta y se secó durante 1 ha temperatura ambiente antes de calentarlo a 80 ° C durante otros 30 min. El electrolito era una solución de 0,5 M H 2 SO 4 en metanol 2 M y se burbujeó durante 20 min con gas nitrógeno para eliminar cualquier oxígeno. La medición de CV se realizó en un rango de potencial de - 0,1 a 1,1 V frente a Ag / AgCl a una frecuencia de exploración de 50 mVs −1 .
Resultados y discusión
Caracterización estructural
Efecto de la tasa de flujo
La espectroscopía FTIR se realizó en el TiO 2 -Muestras de CNF para identificar los compuestos químicos presentes. Los espectros de IR de las muestras producidas a diferentes velocidades de flujo se muestran en la Fig. 2. Los espectros revelaron señales de enlace químico representativas de TiO 2 y carbono. Los picos medianos y anchos a 3200–3600 cm
−1
representan grupos funcionales O-H, mientras que la banda de absorción C =O nítida y fuerte estaba ubicada en la región de 1550-1850 cm
−1
[19]. Los picos de los alcanos (grupos C-H) son débiles y anchos y están ubicados en las regiones de 1300 a 1450 cm
−1
. Sin embargo, los grupos C-C supuestamente aparecen en números de onda muy bajos, por debajo de 500 cm
−1
[19] y no existen en los espectros debido al pequeño rango de número de onda (4000 cm
−1
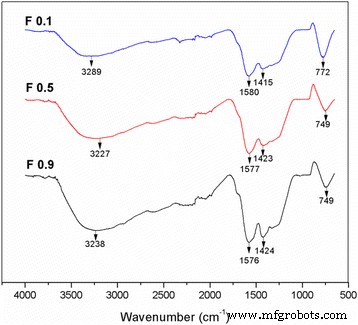
Los espectros de infrarrojos para el TiO 2 -Muestra CNF con diferente parámetro de caudal en el rango de 650 a 4000 cm −1 número de onda
El TiO 2 -Muestras de CNF fabricadas a velocidades de flujo de 0,1, 0,5 , y 0,9 mLh −1 se denotan F0.1, F0.5 y F0.9, respectivamente. La Figura 3 muestra los patrones XRD del TiO 2 -Soportes de catalizador CNF fabricados con diferentes caudales. La Figura 3a es una muestra individual para el soporte del catalizador, que es la muestra F0.1, para observar el patrón XRD de cerca con todo el material de pico en TiO 2 -CNF, mientras que la Fig. 3b es toda la muestra de caudal involucrada. La existencia de TiO 2 y se incluye carbono en la muestra. El TiO 2 consta de dos estructuras, anatasa y rutilo, porque la temperatura de carbonización convierte una pequeña cantidad de anatasa TiO 2 en rutilo TiO 2 . Los picos de difracción para anatasa TiO 2 son 25 ° (101), 38 ° (112), 48 ° (200), 53,9 ° (105), 62 ° (213) y 68 ° (116), mientras que los de rutilo, TiO 2 son 27 ° (110), 36 ° (101), 41 ° (111) y 54 ° (211). La fuente de carbono está indicada por varios picos de difracción, incluidos los de 30 ° (110) y 55 ° (211). La anatasa y el rutilo TiO 2 formó una estructura tetragonal, mientras que el carbono estaba en la estructura cristalográfica cúbica centrada en las caras.
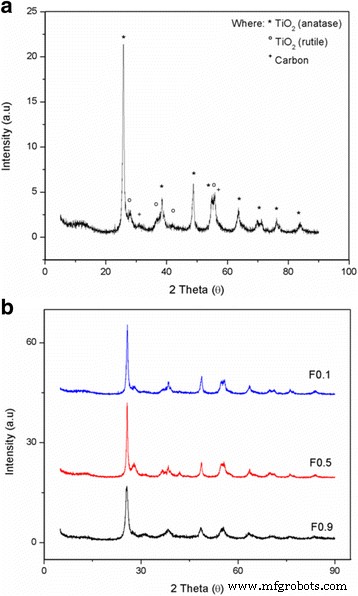
Patrones de difracción de rayos X de a TiO 2 individual -CNF muestra y b muestra de caudal diferente
Se encontró que la velocidad de flujo en la técnica de electrohilado afecta el diámetro de la nanofibra, que se calculó mediante análisis FESEM. La imagen FESEM se presenta en la Fig. 4, mientras que los resultados de la distribución de tamaño y el diámetro se muestran en la Fig. 5 y la Tabla 1. La imagen confirma que la estructura de nanofibras se formó en todos los caudales estudiados. Las nanofibras F0.1 mostraron una morfología suave debido a la velocidad de flujo más lenta, lo que da tiempo suficiente para que el solvente se evapore, ayudando a producir la estructura suave. El diámetro medio de nanofibras de 100 mediciones es 161,18 ± 26,08 nm, que es el diámetro más pequeño entre las muestras producidas a diferentes velocidades de flujo. Sin embargo, la imagen de FESEM de F0.5 muestra la formación de cintas planas en las nanofibras debido a la falta de evaporación del núcleo, es decir, el solvente está atrapado en el núcleo y se difunde a la atmósfera ambiental para causar la estructura de la cinta plana [ 21]. F0.9 muestra nanofibras más rugosas con diámetros no uniformes y varias perlas formadas en la morfología de las nanofibras. Esto ocurre cuando el caudal es muy superior al valor óptimo, lo que reduce el tiempo de secado antes de que la fibra llegue al colector. Los diámetros medios de nanofibras de F0.5 y F0.9 fueron mayores que los de F0.1, que fueron 220.28 ± 38.01 y 286.33 ± 50.83 nm, respectivamente. La imagen de FESEM revela que el diámetro de las nanofibras aumenta a medida que aumenta la velocidad de flujo durante el electrohilado. F0.1, que tiene un caudal de 0.1 mLhr −1 , se utilizó para un análisis más detallado del efecto del DTC en el diámetro de la nanofibra.
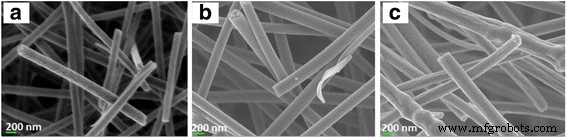
Imagen de FESEM de a TiO 2 -CNF (F0.1), b TiO 2 -CNF (F0.5) y c TiO 2 -CNF (F0.9) a × 30.000 aumentos
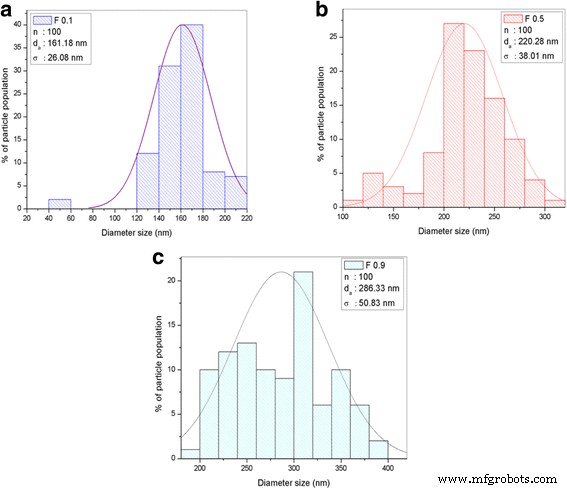
Datos de histograma de distribución de tamaño de diámetro con el parámetro de n, d a y σ. un TiO 2 -CNF (F0.1). b TiO 2 -CNF (F0,5). c TiO 2 -CNF (F0.9)
Efecto de la distancia entre la punta y el colector
El TiO 2 sintetizado -Los soportes de catalizador CNF fueron analizados por FTIR para evaluar el enlace químico en las muestras, y los espectros IR de las muestras se ilustran en la Fig. 6. Los espectros IR muestran tres muestras con diferentes parámetros DTC después del proceso de carbonización. Todas las muestras sintetizadas muestran la existencia de enlaces iónicos de O-Ti-O y carbonato, donde los picos y números de onda en los espectros estaban en el mismo rango que los de las muestras F0.1, F0.5 y F0.9 en el sección previa. Los números de onda estaban lo suficientemente cerca como para indicar la similitud de las muestras, incluidas las muestras producidas a diferentes velocidades de flujo en la Fig. 2. Sin embargo, la muestra D14 muestra la existencia de un nuevo pico alrededor de 2300–2400 cm -1 , que indican las vibraciones de estiramiento N-H. Este pico se puede clasificar como pico de sales de amina terciaria, donde el enlace N-H es débil y sin valor práctico que pueda despreciarse [19]. La presencia de este enlace puede deberse a la eliminación incompleta del compuesto disolvente durante el proceso de carbonización. Esta observación muestra que los parámetros de electrohilado del caudal y el DTC no influyen en la unión química de las muestras.
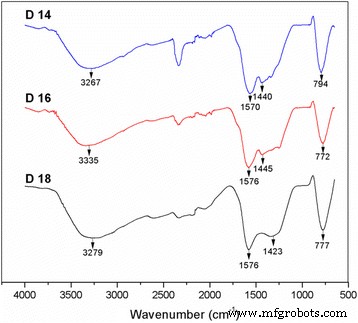
El espectro de infrarrojos para el TiO 2 -Muestra CNF con diferente parámetro DTC en el rango de 650 a 4000 cm −1 número de onda
La cristalinidad del TiO 2 -Se analizaron los soportes de catalizador CNF. Los patrones de XRD se muestran en la Fig. 7a para muestras individuales y en la Fig. 7b para DTC. La muestra individual en la Fig. 7a indica el patrón XRD de cerca para el DTC 18 para ver el pico de existencia de todo el material involucrado. Los materiales involucrados en el soporte del catalizador, TiO 2 y carbono, se muestra que existen en cada muestra. Los picos de difracción se examinaron en un intervalo de 2θ de 5 ° a 90 °, y los picos a 31 ° (110) y 55 ° (211) indican que el carbono con una estructura cristalográfica de FCC está presente en el soporte del catalizador. El pico de difracción agudo a 25 ° (101) se atribuyó a TiO 2 en forma de anatasa, y hay varios otros picos para anatasa TiO 2 , incluidos los de 38 ° (004), 48 ° (200), 53 ° (105), 55 ° (211), 63 ° (204) y 69 ° (116). Los otros cuatro picos de difracción a 27 ° (110), 36 ° (101), 41 ° (111) y 54 ° (211) pertenecen al rutilo TiO 2 . Tanto anatasa como rutilo TiO 2 tienen una estructura cristalográfica tetragonal.
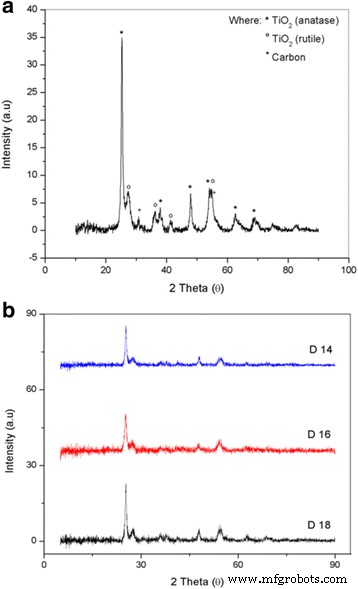
Patrones de difracción de rayos X de a TiO 2 individual -CNF muestra y b muestra de DTC diferente
TiO 2 -Las nanofibras de CNF se fabricaron mediante electrohilado con diferentes valores de DTC, denominados D14, D16 y D18. El DTC se varió a 14, 16 y 18 cm. El diámetro de la nanofibra se calculó mediante análisis FESEM. La Figura 8 muestra las imágenes FESEM de las muestras con diferentes valores de DTC con un aumento de × 30.000. El efecto de la variación en DTC sobre el diámetro de las nanofibras se estimó utilizando la distribución del tamaño de partícula (diámetro), como se ilustra en la Fig.9, y los valores se tabulan en la Tabla 2. La distribución de diámetro incluye varios parámetros, n (nanopartículas población), d a (tamaño de partícula medio aritmético) y σ (desviación estándar) [22].
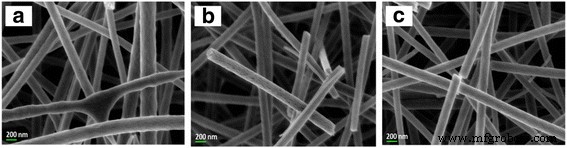
Imagen de FESEM de a TiO 2 -CNF (D14), b TiO 2 -CNF (D16) y c TiO 2 -CNF (D18) a × 30.000 aumentos
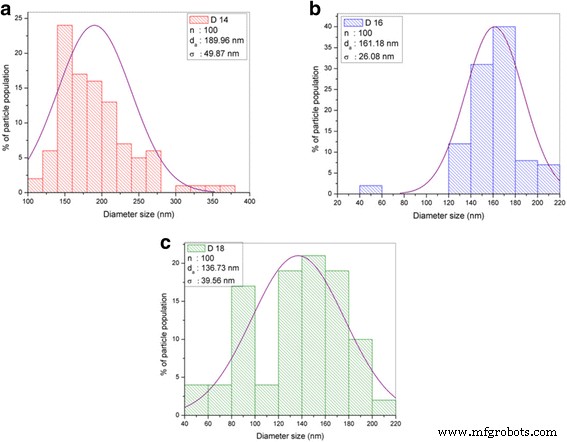
Datos de histograma de distribución de tamaño de diámetro con el parámetro de n, d a y σ. un TiO 2 -CNF (D14). b TiO 2 -CNF (D16). c TiO 2 -CNF (D18)
El diámetro medio más pequeño fue 136,73 ± 39,56 nm (90-170 nm), perteneciente a D18, seguido de D16 y D14 con diámetros de 161,18 ± 26,08 y 189,96 ± 49,87 nm, respectivamente. Cuanto más largas sean las distancias entre la punta y el colector, menor será el diámetro de las nanofibras. Este comportamiento se debe al tiempo de deposición y al intervalo de inestabilidad del batido durante el proceso de electrohilado. La distancia más larga proporciona un tiempo de deposición más largo y, durante ese período, se produce el fenómeno de inestabilidad del batido, también conocido como mecanismo de adelgazamiento y división. Este fenómeno se produce debido a las interacciones entre los iones cargados y el campo eléctrico [17]. Cuando la fuerza eléctrica aplicada a la punta de la boquilla alcanza un valor crítico, la densidad altamente cargada y la fuerza viscoelástica dividen los chorros en chorros más pequeños, creando una trayectoria de flexión, enrollamiento y espiral hacia el colector. Cuando el DTC es más largo, se produce repetidamente la división del chorro, lo que da como resultado fibras ultrafinas y de menor diámetro. Por lo tanto, el diámetro más pequeño pertenece a la muestra D18 con un caudal de 0,1 mLh −1 y DTC de 18.
El diámetro de las nanofibras fabricadas, TiO 2 -CNF, se compara con el estudio anterior de diámetro de nanofibras para TiO 2 nanofibras basadas en nanofibras, y esta comparación se muestra en la Tabla 3. Los resultados muestran que el TiO 2 -CNF tiene el diámetro de nanofibras más pequeño con 136,73 ± 39,56 nm. Esto se debe al parámetro óptimo utilizado durante el método de electrohilado; que es bajo en caudal y alto valor de DTC. Por lo tanto, con menor caudal y mayor valor de DTC, se produce el diámetro más pequeño de una nanofibra. Esto muestra que los parámetros de electrohilado dan el mayor efecto al diámetro de la nanofibra. Aunque es preferible un DTC más largo y un caudal menor, existen valores óptimos para estos parámetros, ya que estos parámetros pueden conducir a una pérdida de peso. Esto ocurre debido a la sobre-evaporación, en la que la nanofibra se forma antes de llegar al colector, lo que permite que la nanofibra viaje libremente a regiones no deseadas.
La muestra D18 con un caudal de 0,1 mLh −1 y se seleccionó DTC de 18 para el análisis TEM para examinar la morfología y obtener el tamaño del diámetro. La imagen TEM y el mapeo elemental del TiO 2 -El soporte del catalizador CNF se muestra en la Fig. 10. La imagen TEM muestra que TiO 2 -CNF da como resultado una nanofibra suave y sedosa con un diámetro de 135,38 nm. El diámetro está en el mismo rango (90-170 nm) que el obtenido del análisis FESEM. El mapeo se emplea para examinar la distribución de TiO 2 y carbono sobre nanofibras. Los resultados reflejan que TiO 2 y carbono formado uniformemente en la estructura de nanofibras, debido a la distribución homogénea de la solución de polímero y el TiO 2 precursor durante el método sol-gel. Este mapeo también muestra la ubicación de los materiales, en los que TiO 2 y el carbono se encuentran a lo largo de toda la superficie de las nanofibras, lo que beneficia la creación de áreas de reacción activas durante la catálisis. Se espera que las otras muestras de nanofibras tengan la misma distribución uniforme de TiO 2 y carbono. El tamaño de partícula de TiO 2 y carbono en las muestras de nanofibras y su efecto hacia MOR se discute en la siguiente sección.
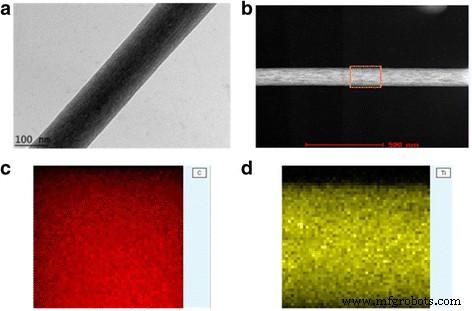
TiO 2 -Soporte de catalizador CNF a Imagen TEM (escala 100 nm), b Imagen TEM para TiO 2 y mapeo de nanofibras C, c mapeo para nanofibras C y d mapeo para TiO 2 nanofibra
Caracterización electroquímica de la reacción de oxidación del metanol
La caracterización electroquímica implica tres pasos principales, que son la caracterización de la actividad electroquímica, el rendimiento electrocatalítico y la estabilidad y durabilidad a largo plazo. La actividad electroquímica y el rendimiento electrocatalítico se analizaron mediante CV utilizando un sistema de tres electrodos para adquirir información cualitativa y cuantitativa sobre la reacción implicada [23]. La Figura 11a, b muestra la imagen TEM del catalizador PtRu depositado en la superficie del F0.1 y D18 TiO 2 -CNF soporta, respectivamente. El catalizador PtRu se distribuyó uniformemente sobre la superficie de las nanofibras tanto en F0.1 como en D18. La Figura 11c muestra el patrón XRD de D18 PtRu / TiO 2 -CNF, mientras que la Tabla 4 da los datos para el diámetro de nanofibras, obtenido de FESEM, y tamaño de cristalito de las partículas en las muestras, obtenido de XRD. La Tabla 4 muestra que las muestras de la serie F (F0.1, F0.5 y F0.9) con catalizador agregado tienen un TiO 2 (anatasa) tamaño de cristalito de aproximadamente 20 a 22 nm. El cambio en el diámetro de la nanofibra tiene poco efecto sobre el tamaño de cristalita de TiO 2 , mientras que el tamaño del cristalito del carbono cambia a medida que aumenta el diámetro de la nanofibra de 15,9 nm en F0,1 a 25,8 nm en F0,9. El tamaño de cristalito de Pt también tiende a aumentar con el tamaño de cristalito de carbono. El tamaño de cristalito de Pt soportado en F0.1, F0.5 y F0.9 es 5.67, 8.04 y 9.75 nm, respectivamente. Los cambios en el tamaño de los cristalitos de Pt se deben a las propiedades superficiales de la nanofibra. La Tabla 4 también muestra el tamaño de cristalito de PtRu soportado en muestras de la serie D. El diámetro de la nanofibra disminuye de valor de D14 a D16 a D18. A diferencia de las muestras de la serie F, el tamaño de cristalito de TiO 2 (anatasa) en las muestras de la serie D disminuye a medida que disminuye el diámetro de la nanofibra. El TiO 2 El tamaño de cristalito es 23,40, 21,50 y 18,60 nm para D14, D16 y D18, respectivamente. El tamaño de cristalito de carbono y Pt también disminuye con una disminución en el diámetro de las nanofibras. El tamaño de cristalito de carbono disminuye de 17,3 nm en D14 a 14,4 nm en D18, mientras que el tamaño de cristalito de Pt soportado en D14, D16 y D18 es de 5,44, 5,67 y 4,64 nm, respectivamente. A partir de estos datos, los cambios en los tamaños de cristalitos de TiO 2 y el carbono de la nanofibra provocan cambios en las propiedades superficiales de la nanofibra, lo que provoca cambios en el tamaño de los cristalitos de las partículas de Pt depositadas en la superficie de la nanofibra.
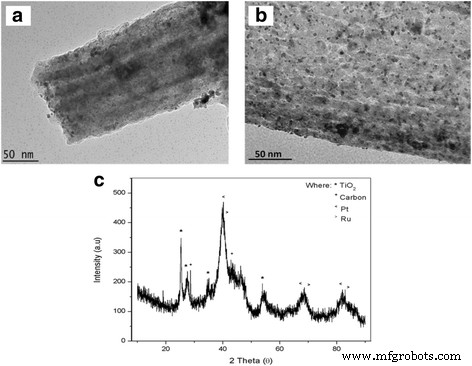
Imagen de PtRu depositada en TiO 2 -CNF a Imagen TEM de PtRu / TiO 2 -CNF en F0.1, b Imagen TEM de PtRu / TiO 2 -CNF en D18 y c Patrón XRD de PtRu / TiO 2 -CNF de D18
La Figura 12 muestra los perfiles CV del PtRu / TiO 2 -CNF electrocatalysts with different catalyst supports in 0.5 M H2 SO4 solución. The CV curve for F0.1, F0.5, and F0.9 are shown in Fig. 12a, while D14, D16, and D18 are shown in Fig. 12b. Hydrogen adsorption-desorption by Pt occurs around − 0.2 to 0.1 V vs. Ag/AgCl. The mass loading for all the electrocatalyst in this profile is the same that as 0.57 mgcm −2 . The PtRu/TiO2 -CNF supported on D18 exhibits a steep current peak for hydrogen adsorption in comparison in the other D series samples, while F0.1 has a steep peak in comparison with the F series samples. The peak indicates that the active surface area on the PtRu/TiO2 -CNF electrocatalyst and the ECSA can be calculated from the equation:ECSA = Q /(Γ .W Pt ). Where, Q is the integral of the hydrogen adsorption area, Γ is the constant for the charge required to reduce the proton monolayer on the Pt (2.1 CmPt −2 ), and W Pt is the mass loading of Pt. Table 5 shows the ECSA of all the catalyst samples in units of m 2 g −1 with mass loadings according to the mass of PtRu. From Table 5, the ECSA for PtRu supported on F0.1, F0.5, and F0.9 is 131.29, 65.05, and 25.03 m 2 g −1 , respectively. The ECSA value decreases with increasing Pt crystallite size in the catalyst samples. The catalyst supported on D14, D16, and D18 has an ECSA value of 21.48, 131.29, and 226.75 m 2 g −1 , respectively. As shown previously, the value of the Pt crystallite size in the D series samples decreases from D14 to D18, and thus, the ECSA increases according to Pt crystallite size. Smaller size particles lead to an increase in the active surface area of the catalyst. Overall, the electrospinning parameters clearly show big influence towards the diameter and surface properties (surface morphology) of nanofibers.
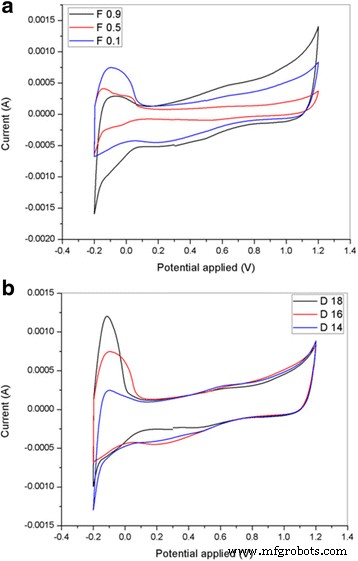
Cyclic voltammetry profiles of the PtRu/TiO2 -CNF with a different flow rate, F0.1, F0.5, F0.9, and b different DTC, D14, D16, and D18, in 0.5 M H2 SO4 solution at the scan rate of 50 mVs −1
The electrocatalytic performance of PtRu supported on the different F and D series nanofibers is tabulated and plotted in Table 5 and Fig. 13. The CV curve was measured in 2 M methanol and 0.5 M H2 SO4 solution saturated with N2 gas at room temperature. The mass loading for all the electrocatalyst is the same which is 0.57 mgcm −2 . Figure 13 shows multiple CV curves over a potential range of − 0.1 to 1.1 V vs. Ag/AgCl. Figure 13a shows the CV graphs for PtRu supported on the F series nanofiber samples. As the diameter of the nanofiber decreases from sample F0.9 to F0.1, the current density in MOR increases, and the oxidation peak and onset potential of MOR shift towards positive values. On the other hand, in the D series nanofiber samples, the oxidation peak potential of the catalyst supported on D14, D16, and D18 is 0.754, 0.771, and 0.732 V (vs. Ag/AgCl), respectively. There is no pattern in the oxidation peak potential in the D series samples, and the onset potential is almost the same for each sample, at 0.36 V vs. Ag/AgCl. However, the peak current density at the oxidation peak potential of MOR increases in accordance to the catalyst support on D14, D16, and D18. The peak current density for D14, D16, and D18 is 201.45, 249.58, and 274.72 mAmg −1 PtRu , respectively. It can be clearly seen that the increase in the current density matches the patterns in the diameter, from FESEM analysis, and ECSA value. This shows that a smaller diameter size produces high surface area and increases the number of active sites on the electrocatalyst surface. The higher peak current for the composite electrocatalyst may result from the supporting material (TiO2 -CNF), where changes in the structure and the combination of materials can be very effective in producing positive effects on the metal-support interaction [5, 24].
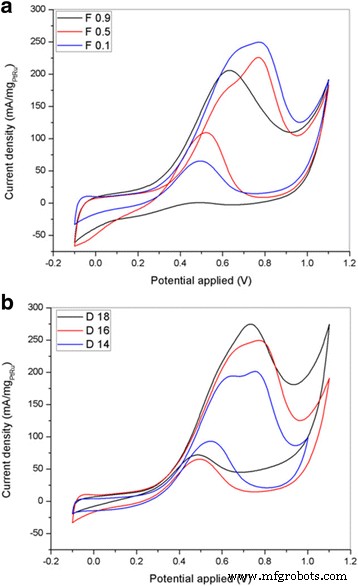
Cyclic voltammograms for PtRu/TiO2 -CNF with different a flow rate and b DTC of the catalyst support in 2 M methanol and 0.5 M H2 SO4 at the scan rate of 50 mVs −1
The reverse scan in the CV curve shows a small oxidation peak at a potential of approximately 0.49–0.55 V vs. Ag/AgCl. This second oxidation peak appeared due to the incomplete removal of oxidized carbonaceous species in the forward scan [25]. However, the ratio between the forward (If ) and reversed (Ib ) oxidation peak for PtRu/TiO2 -CNF (D18) exceeded 3.8, which means that the electrocatalyst has high tolerance towards carbonaceous species, reducing the potential for catalyst poisoning. This result shows that the combination of metal oxide and carbon nanofibers has a good potential for use in fuel cell applications.
Conclusion
TiO2 -CNF nanofibers can be fabricated via electrospinning, which is the main technique, and several other methods. The nanofibers are influenced by the flow rate and the DTC, which were examined as electrospinning process parameters, with three different samples for each parameter, denoted F0.1, F0.5, F0.9, D14, D16, and D18. The results showed that the TiO2 -CNF (D18) sample produced the smallest average diameter of 136.73 ± 39.56 nm. TiO2 -CNF was mixed with PtRu to form the composite catalyst, and its CV performance was examined. The current density of the PtRu/TiO2 -CNF (D18) sample is 1.4 times higher than that of PtRu/TiO2 -CNF (D14), while the ECSA of PtRu/TiO2 -CNF (D18) is 10 times higher than that of the other samples. Thus, the flow rate and DTC highly affect the diameter, morphology, and performance of the nanofibers. The nanofiber performance increased with decreasing nanofiber diameter, which shows the capability of the composite nanofiber catalyst to be an upcoming anode catalyst for DMFCs.
Nanomateriales
- El método de fabricación de moléculas artificiales gana el premio al mejor póster
- Compuestos de grafeno y polímeros para aplicaciones de supercapacitores:una revisión
- Diseño de materiales de nanotubos de carbono compuestos y limpios mediante caracterización porosimétrica
- Rendimiento mejorado de un nuevo catalizador anódico de PdAu / VGCNF para la electrooxidación en una pila de combustible de glicerol
- Fabricación, caracterización y citotoxicidad de nanopartículas de carbonato de calcio derivadas de concha de oro-berberecho conjugado de forma esférica para aplicaciones biomédicas
- Compuesto de aerogel / azufre de carbón activado recubierto de polianilina para batería de litio-azufre de alto rendimiento
- Fabricación y caracterización de nanoclips de ZnO mediante el proceso mediado por poliol
- Soporte de catalizador anódico novedoso para pila de combustible de metanol directo:caracterizaciones y rendimiento de una sola pila
- Un método sencillo para cargar nanopartículas de CeO2 en matrices de nanotubos de TiO2 anódico
- Catalizadores a base de platino en varios soportes de carbono y polímeros conductores para aplicaciones de celdas de combustible de metanol directo:una revisión
- Comportamiento del conjunto de electrocatalizador de membrana y electrocatalizador nanoestructurado en una celda de combustible de glicerol directo pasivo