Una guía ridículamente simple para administrar el tiempo de inactividad planificado | Tiempo de inactividad programado
El mantenimiento preventivo es la estrategia de mantenimiento más popular porque brinda muchos beneficios y, al mismo tiempo, no es increíblemente difícil ni costoso de implementar.
Dicho esto, el mantenimiento preventivo tiene sus desventajas.
Una de las objeciones más citadas es que implementarlo significa que estará haciendo un mantenimiento excesivo. En otras palabras, sus técnicos perderán tiempo en inspecciones y activos innecesarios que quizás (todavía) no requieran ese nivel de atención.
Si profundizamos un poco más, veremos que esto conduce a un problema más significativo. Cuando realiza un trabajo preventivo en un activo, en muchos casos, ese activo debe cerrarse primero. En la traducción, debe programar el tiempo de inactividad planificado.
Como nadie quiere apagar un activo durante las horas pico de producción o para trabajos de mantenimiento que aún no deben realizarse, veamos cómo puede desarrollar un programa de mantenimiento que tenga en cuenta esos desafíos y minimice los tiempos de inactividad programados.
¿Qué es el tiempo de inactividad planificado? tiempo de inactividad programado?
En pocas palabras, el tiempo de inactividad planificado es un período de tiempo que reserva para el mantenimiento programado y las actualizaciones durante el cual sus activos deben cerrarse.
Dado que el mantenimiento proactivo a menudo se realiza en activos críticos que son importantes para la producción, no tiene otra solución que pausar las operaciones normales de producción hasta que se realicen las reparaciones / inspecciones / actualizaciones.
Las organizaciones buscan evitar estos problemas programando el mantenimiento durante los turnos de noche (u otros momentos en los que las máquinas no están en uso). Sin embargo, si su departamento de mantenimiento no tiene turnos de noche o si tiene un ciclo de producción de 24 horas al día, 7 días a la semana, encontrar el momento adecuado para programar el tiempo de inactividad planificado puede resultar realmente complicado, muy rápido.
Nota rápida:para el resto del artículo, usaremos los términos "tiempo de inactividad planificado" y "tiempo de inactividad programado" indistintamente, ya que se refieren a lo mismo en la práctica.
Tiempo de inactividad planificado y no planificado
La diferencia entre tiempo de inactividad planificado y no planificado se explica por sí mismo:USTED decide cuándo desea tener un tiempo de inactividad planificado, las MÁQUINAS deciden cuándo quieren tomar un descanso y no se molestan en preguntar si eso se ajusta a su horario.
Dejando a un lado las bromas, las fallas inesperadas del equipo que provocan un tiempo de inactividad no planificado pueden ser muy costosas , que es una de las razones clave por las que muchas empresas están cambiando del mantenimiento reactivo al preventivo .
Saber cuánto tiempo dedica al mantenimiento planificado frente al no planificado es fundamental, por lo que es una de las muchas cosas que Limble realiza un seguimiento.
A continuación, se muestra un ejemplo de cómo puede utilizar Limble para realizar un seguimiento de cuánto tiempo dedica a las tareas de mantenimiento planificadas frente a cuánto tiempo dedica a reaccionar ante problemas inesperados:
Veamos cómo programar los tiempos de inactividad planificados para que pueda realizar un mantenimiento adecuado con un impacto mínimo en la velocidad y el volumen de producción.
Cómo administrar el tiempo de inactividad planificado
# 1) Comprenda su producción
A lo largo del año, es muy probable que tenga un reflujo y un flujo en la producción diaria. Conozca cada máquina que utiliza y discierna cómo las diferentes estaciones afectan los ciclos de producción y, a su vez, el uso diario de las máquinas.
Durante el pico de producción, planifique encontrar el mejor momento que afecte menos el resultado final. Encontrar tiempo para prepararse puede significar fuera de horario. Si tiene una tienda abierta las 24 horas, los 7 días de la semana, podría significar la hora más lenta del día.
La clave es saber cuándo se ralentiza la producción y cuándo se acelera según lo previsto.
# 2) Reduzca el mantenimiento excesivo con un CMMS
Una de las principales formas de ejecutar un plan de mantenimiento exitoso es poder organizar, administrar y rastrear grandes cantidades de información a través de varias fuentes.
Tener una CMMS moderna puede ayudarlo enormemente a rastrear y dar sentido a todos esos datos.
Reducir el mantenimiento reactivo en un 73,2%
Ver los resultados que disfruta Red Hawk con Limble
Lea nuestroCaso de estudio
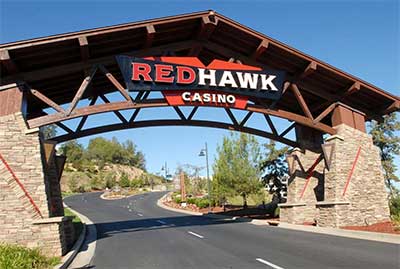
Estas son solo algunas de las cosas que puede hacer con un CMMS:
- registrar el rendimiento de la máquina y el historial de activos
- rastrear el progreso de todas las tareas (leer órdenes de trabajo)
- realizar un seguimiento del uso de todo el inventario y las piezas de repuesto
- realizar un seguimiento del rendimiento del técnico
- programar y supervisar su programa completo de mantenimiento preventivo
Al tener todos estos datos a su disposición, puede reducir el mantenimiento excesivo :
- espaciar la frecuencia del trabajo de mantenimiento en los activos que pueden manejarlo
- reducir la duración del evento de tiempo de inactividad acelerando el diagnóstico y la comunicación del equipo
- asegurarse de que todas las piezas de repuesto estén disponibles cuando las necesite
- tener un departamento de mantenimiento bien organizado en general
Para obtener una visión en profundidad de CMMS, consulte nuestra guía ¿Qué es un sistema CMMS y cómo funciona?
# 3) Limite el enfoque de su plan de mantenimiento
Una excelente manera de saber dónde comenzar su programación de mantenimiento es enumerar todos sus activos y asignarles un rango. Puede parecer obvio, pero saber qué máquinas tienen la máxima prioridad en su fábrica le dará un norte.
Una vez que haya enumerado sus máquinas importantes, enumere los activos menores que podrían ser tan secundarios que no necesitan incluirse en el mantenimiento de rutina.
Las máquinas individuales, por ejemplo, requieren menos esfuerzo con el uso. Es posible que no necesite aceite o lubricación; otro podría estar menos involucrado que otros dispositivos, con muchas menos partes móviles.
De cualquier manera, las máquinas específicas necesitan menos mantenimiento general. Y debe quedar claro qué máquinas se incluyen en esta categoría. Después de todo, a menudo no vale la pena tener todas sus máquinas en un plan de mantenimiento preventivo.
Además de todo lo mencionado, comprender cuánto debe durar cada tarea de mantenimiento y cuando la máquina se usa menos será crucial para crear un plan de mantenimiento preventivo eficaz para que pueda programar el tiempo de inactividad planificado en el momento más oportuno.
# 4) Tenga un POE claramente definido
Tener procedimientos operativos estándar claramente definidos. para cada operación que deba repetirse con frecuencia es una excelente manera de optimizar sus operaciones de mantenimiento.
Dado que el tiempo de inactividad planificado es algo que deberá programar con una regularidad razonable, tener pautas claras ayudará a los técnicos a realizar su trabajo más rápido, lo que significa que sus activos necesitarán menos tiempo para volver al trabajo.
Tenga en cuenta que la velocidad y la calidad de los trabajos de mantenimiento realizados son igualmente importantes . Si bien es bueno mantener el tiempo de inactividad programado al mínimo, el trabajo de mantenimiento mal realizado seguramente dará lugar a un aumento en el tiempo de inactividad no planificado.
Y creo que todos podemos estar de acuerdo en que dos horas adicionales de tiempo de inactividad programado son mucho más aceptables que un día entero de un apagado o una interrupción no planificados.
N.º 5) Comprenda sus cuellos de botella
Los retrasos frecuentes en las entregas dificultan el mantenimiento de existencias de las piezas de repuesto necesarias. Algunos técnicos superiores de mantenimiento se jubilaron o dejaron la empresa, por lo que está trabajando con un equipo más joven que carece de experiencia y capacitación. ¿Trabaja con activos más antiguos que necesitan mucha atención y les gusta averiarse inesperadamente?
En el contexto de minimizar el tiempo de inactividad planificado para el mantenimiento preventivo, piezas de repuesto , técnicos sin experiencia / no calificados y activos obsoletos son los 3 cuellos de botella más comunes que debe programar.
La buena noticia es que estos cuellos de botella se pueden evitar con un poco de solución y previsión.
Si sus repuestos no le llegan rápidamente, considere ordenarlos antes o cambiar a un nuevo proveedor cuando sea posible.
Cuando sepa que tiene técnicos sin experiencia, puede:
- emparejarlos con colegas más experimentados
- tener un POE claramente definido del que acabamos de hablar
- bríndeles la capacitación necesaria
- tener un proceso de contratación más riguroso
Y, por último, debe encontrar una manera de contabilizar los activos obsoletos. En la mayoría de los casos, esto significará que deberá prestar especial atención a esos activos, ya que pueden ser muy problemáticos y ser la causa de muchos tiempos de inactividad no programados. Algunas formas de hacerlo son:
- rastrear cuidadosamente el historial de activos para extrapolar patrones de desglose comunes para que pueda tratar de abordarlos durante los tiempos de inactividad planificados
- programar inspecciones adicionales que se pueden realizar mientras el activo está en funcionamiento
- instalar sensores para realizar supervisión basada en condiciones
N.º 6) Reduzca la duración de los tiempos de inactividad programados mediante una colaboración eficaz
Los departamentos que interactúan con el personal de mantenimiento deben estar en sintonía y coordinar los ajustes y reparaciones de rutina. Siempre que todos comprendan dónde estará el equipo de mantenimiento para cada parada planificada, los operadores de máquinas, el personal de limpieza y otros trabajadores pueden comenzar a preparar el entorno para concentrarse solo en lo que necesitan hacer y garantizar un tiempo de inactividad mínimo.
Cuando ocurre lo contrario y existe una mala comunicación entre los departamentos, no es difícil imaginar diferentes errores y accidentes que pueden ocurrir y prolongar el tiempo que sus activos pasan en espera.
No permita que una mala organización y comunicación sea la razón por la que sus paradas planificadas causaron retrasos en la producción.
¿Cuándo programar el tiempo de inactividad planificado?
Como gerente de mantenimiento de instalaciones, está claro que solo usted puede encontrar el momento adecuado para programar el tiempo de inactividad planificado en sus instalaciones.
Dicho esto, tenemos algunos consejos que podrían ayudar:
- Programe el trabajo de mantenimiento planificado después del horario comercial
- Inmediatamente antes de las principales festividades
- Antes de un clima severo muy esperado
- Uno cada dos años simula un apagón y prueba todos los equipos críticos a la vez
Para obtener explicaciones más detalladas, puede consultar mi publicación de invitado que trata sobre cuándo programar el mantenimiento planificado . .
Se trata de planificar el futuro
Como puede ver, con suficiente planificación y organización, puede minimizar en gran medida la cantidad de tiempo de inactividad durante el mantenimiento planificado.
Ya sea durante una temporada alta de producción o la temporada más lenta del año, estar organizado y tener un programa de mantenimiento exacto garantizará que su producción funcione al más alto nivel y que sus máquinas estén en condiciones óptimas de funcionamiento.
Si está interesado en explorar completamente cómo Limble puede ayudarlo a mantener al mínimo la cantidad de tiempo dedicado a los tiempos de inactividad planificados, deje un comentario a continuación o envíenos un mensaje .
Mantenimiento y reparación de equipos
- Programado vs. Mantenimiento no programado en instalaciones de fabricación
- Una guía para implementar el mantenimiento productivo total
- Guía de indicadores clave de rendimiento de fabricación
- El futuro del mantenimiento:una guía práctica para la Industria 4.0
- Una guía sencilla para crear un programa de mantenimiento predictivo
- Mantenimiento basado en condiciones:una guía completa
- Estrategias simples para administrar su proceso de MRO
- La programación de mantenimiento necesita una acumulación planificada
- Una guía sencilla para la evaluación comparativa de mantenimiento
- ¿Qué es el mantenimiento programado?
- Guía básica para el mantenimiento de minicargadoras