Tipos de mantenimiento:una comparación
Tipos de mantenimiento
Es bien sabido que cada año se pierden miles de millones de dólares debido al tiempo de inactividad no programado y la mala calidad de los activos. En una batalla interminable para combatir esta estadística, las organizaciones implementan uno de una variedad de tipos de mantenimiento, a menudo combinando dos o más. Las definiciones de los tipos de mantenimiento varían en la industria, lo que puede hacer que sea bastante confuso diferenciar cosas como el mantenimiento preventivo y predictivo, entre otros.
La mayoría de los tipos de mantenimiento se dividen en dos categorías principales:preventivo y correctivo. Mantenimiento preventivo es cuando usted inicia de manera proactiva las tareas y los planes de mantenimiento para evitar que ocurran fallas. Además de prevenir fallas, el mantenimiento preventivo puede tener el objetivo de minimizar las consecuencias de la falla o determinar el riesgo de que ocurra la falla.
Mantenimiento correctivo ocurre después de que se ha producido la falla. Básicamente, su equipo está recuperando el estado de funcionamiento del activo en este punto. Para aclarar, el mantenimiento correctivo se puede deliberar en la forma de una estrategia de mantenimiento de ejecución hasta fallas, que se discutirá a continuación.
Examinemos los tipos de mantenimiento más comunes que se utilizan en las industrias de fabricación y procesos.
- Mantenimiento preventivo. El mantenimiento preventivo es una rutina establecida de inspección periódica del equipo, detectando pequeños problemas y solucionándolos antes de que se conviertan en problemas mayores. El objetivo principal del mantenimiento preventivo es cero tiempo de inactividad. Este objetivo se busca después de utilizar tres objetivos:mejorar la vida productiva de los equipos, reducir las averías críticas de los equipos y minimizar la pérdida de producción debido a fallas en los equipos.
Hay un par de tipos de mantenimiento que se incluyen en la categoría de mantenimiento preventivo. Estos incluyen:
- Mantenimiento basado en el uso, que utiliza activadores basados en el uso real de cada activo. El seguimiento del uso de activos con monitores de equipos permite a los gerentes de mantenimiento establecer un programa de mantenimiento preventivo de acuerdo con parámetros preestablecidos.
- Mantenimiento prescriptivo se parece mucho al mantenimiento preventivo, pero aprovecha el software de aprendizaje automático como la inteligencia artificial (IA) y el Internet de las cosas (IoT) para ayudar a programar las tareas de mantenimiento preventivo.
Para ver en profundidad los tipos de mantenimiento preventivo, cómo diseñar un programa de mantenimiento preventivo, herramientas de mantenimiento preventivo y más, consulte el enlace al principio de esta sección.
- Mantenimiento predictivo. El mantenimiento predictivo es el mantenimiento que monitorea el desempeño y la condición del equipo durante las condiciones normales de operación para reducir la probabilidad de fallas. Similar al mantenimiento preventivo (algunas personas incluso lo categorizan como un tipo de mantenimiento preventivo) y está estrechamente relacionado con el mantenimiento basado en condiciones (CBM) , el objetivo del mantenimiento predictivo radica en el nombre:predecir primero cuándo podrían ocurrir fallas y luego prevenir la falla a través del mantenimiento correctivo programado.
Aunque muchas organizaciones emplean mantenimiento predictivo y preventivo (el 76 por ciento usa preventivo, mientras que el 65 por ciento usa predictivo, según una encuesta reciente de Reliable Plant), existen algunas diferencias clave. Más notablemente, el mantenimiento preventivo no requiere el aspecto de monitoreo de condición que requiere el mantenimiento predictivo. Esto significa que el mantenimiento predictivo utiliza tecnologías basadas en condiciones como termografía infrarroja, monitoreo acústico, análisis de vibraciones y análisis de aceite. Otra diferencia clave es que el mantenimiento preventivo implica inspeccionar y realizar el mantenimiento de los activos independientemente de si el equipo necesita mantenimiento (el programa de mantenimiento se basa en un disparador). El mantenimiento predictivo no lo hace.
A continuación, se muestra un cuadro que muestra cómo el mantenimiento basado en condiciones se relaciona con el mantenimiento predictivo y proactivo. Aquí, el mantenimiento predictivo es uno de los dos lados que se derivan de CBM:un lado proactivo que se enfoca en encontrar la causa raíz de una falla y un lado predictivo que se concentra en los síntomas y fallas de fallas.
Para obtener más detalles sobre el mantenimiento predictivo, la tecnología de mantenimiento predictivo y más, haga clic en el enlace al comienzo de esta sección.
- Mantenimiento centrado en la confiabilidad (RCM). El mantenimiento centrado en la confiabilidad es el proceso de identificar problemas potenciales con su equipo y determinar qué debe hacer para asegurarse de que esos activos continúen produciendo a su máxima capacidad. En otras palabras, analiza las averías para descubrir los métodos de mantenimiento adecuados y los programas de mantenimiento personalizados para cada activo individual.
El mantenimiento centrado en la confiabilidad a veces se confunde con el mantenimiento preventivo, pero hay una diferencia clave:el mantenimiento preventivo no es selectivo como RCM, lo que lo hace menos eficiente. Dado que RCM analiza cada activo de forma individual, la ineficiencia se reduce asignando tareas de mantenimiento adaptadas a cada equipo.
El mantenimiento centrado en la confiabilidad utiliza un flujo de trabajo general de cuatro pasos:elija el activo, evalúe el activo, determine el tipo de mantenimiento y repita el proceso. Los criterios de evaluación para implementar un programa RCM plantean siete preguntas:
- ¿Qué tan bien debería funcionar este equipo?
- ¿De qué formas puede fallar este equipo?
- ¿Qué causa cada falla?
- ¿Qué sucede cuando ocurre una falla?
- ¿Por qué es importante cada falla?
- ¿Qué tareas (proactivas) se deben realizar para evitar que ocurran estas fallas?
- ¿Qué se debe hacer si no se puede encontrar una tarea preventiva adecuada?
Haga clic en el enlace al comienzo de esta sección para leer más sobre el mantenimiento centrado en la confiabilidad, incluido cómo implementar RCM, estudios de casos del mundo real de organizaciones que han implementado un programa RCM y más.
- Mantenimiento productivo total (TPM). El mantenimiento productivo total es el proceso de utilizar máquinas, equipos, empleados y procesos de apoyo para mantener y mejorar la integridad de la producción y la calidad del sistema. El objetivo de un programa TPM es mejorar la efectividad general del equipo (OEE) mediante la formación de equipos pequeños y multidisciplinarios para abordar áreas centrales como el mantenimiento preventivo y autónomo, la capacitación de operadores de maquinaria y la estandarización de los procesos de trabajo. El mantenimiento productivo total se centra en todos los departamentos de una organización, asegurando un uso eficiente y eficaz de los medios de producción.
El mantenimiento productivo total se considera más un proceso que un programa, así como un proceso de mejora de las operaciones en lugar de un programa de mantenimiento completo. Tampoco es una solución rápida, ya que se necesitan años para lograr el máximo beneficio de un proceso TPM de alta calidad; sin embargo, puede ver los resultados de inmediato.
El mantenimiento productivo total incorpora las técnicas de lean manufacturing y el Sistema 5-S de su benchmark aceptado internacionalmente compuesto por ocho pilares:mantenimiento autónomo, mejora focalizada, mantenimiento planificado, mantenimiento de calidad, gestión temprana de equipos, formación y educación, seguridad, salud y medio ambiente, y TPM en administración.
La implementación de TPM implica cinco fases:
- Identifique un área piloto
- Restaurar el equipo a las condiciones óptimas de funcionamiento
- Medir OEE
- Abordar / reducir pérdidas importantes
- Implementar el mantenimiento planificado
Haga clic en el enlace al comienzo de esta sección para leer más sobre TPM, incluidos los ocho pilares de TPM, cómo implementarlo, cómo mantener un proceso de TPM y más.
- Mantenimiento autónomo. El mantenimiento autónomo es una estrategia de mantenimiento que consiste en capacitar a los operadores para que monitoreen continuamente sus equipos, realicen ajustes y realicen tareas menores de mantenimiento para aumentar la eficiencia. Esto se hace en lugar de dedicar técnicos de mantenimiento a realizar el mantenimiento programado regularmente, dejándolos libres para tareas de mantenimiento más importantes y urgentes.
El mantenimiento autónomo tiene dos principios básicos:prevenir el deterioro del equipo mediante un funcionamiento adecuado y llevarlo y mantenerlo en condiciones "como nuevo" mediante la restauración y la gestión adecuada. Esto requiere que los operadores dominen habilidades como la detección de anomalías al comprender los componentes de la máquina, realizar mejoras, identificar problemas de calidad y averiguar qué causó los problemas de calidad.
La implementación del mantenimiento autónomo implica siete pasos:aumentar el conocimiento del operador, limpieza e inspección inicial de la máquina, eliminar la causa de la contaminación y mejorar el acceso, desarrollar estándares para lubricación e inspección, inspección y monitoreo, estandarizar el mantenimiento visual y mejora continua.
Para obtener una visión más detallada del mantenimiento autónomo, cómo implementarlo y cómo mantenerlo, haga clic en el enlace al principio de esta sección.
- Mantenimiento de ejecución hasta fallas (RTF). El mantenimiento de funcionamiento hasta la falla es un tipo de mantenimiento reactivo no planificado que suele ser una estrategia deliberada diseñada para minimizar los costos. Las organizaciones pueden optar por adoptar un plan RTF para cosas como activos desechables (máquinas con piezas desechables destinadas a intercambiarse en lugar de repararse), activos no críticos como herramientas, activos duraderos o activos que no están sujetos a desgaste o es poco probable que lo hagan. fallan en condiciones normales de funcionamiento, o activos que muestran patrones de fallas aleatorios que no se pueden predecir.
La advertencia para el mantenimiento de RTF es que requiere buen juicio. Saber cuándo etiquetar algo como una falla total en lugar de repararlo es parte del conjunto de habilidades que viene con el mantenimiento de RTF. Puede presentar algún riesgo ya que los activos no están siendo monitoreados, lo que hace que la organización se quede mirando el barril del tiempo de inactividad no planificado cuando algo se rompe.
Sin embargo, cuando se implementa en los activos correctos con una planificación inteligente para lidiar con fallas inevitables, RTF puede ahorrar tiempo y dinero al no reemplazar equipos intactos.
Mantenimiento de máquinas y el cuerpo humano en paralelo
Cuando se trata de tipos, técnicas y costos de mantenimiento, los tipos principales de mantenimiento se pueden comparar con el cuerpo humano para obtener una instantánea de la tarea equivalente de "mantenimiento corporal". La siguiente tabla usa un ejemplo de activo de generación de energía y lo compara con el corazón humano.
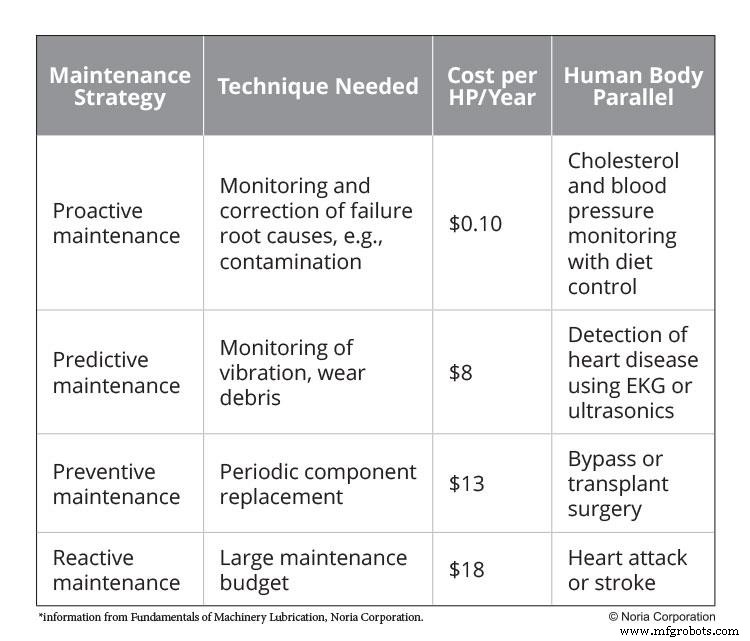
Tipos de activadores de mantenimiento
Los activadores de mantenimiento se pueden configurar y utilizar con varios tipos de mantenimiento. Los activadores de averías se utilizan con planes de mantenimiento reactivos o de ejecución hasta el fallo. El mantenimiento predictivo utiliza elementos como disparadores basados en el tiempo en forma de alertas para tratar de evitar que ocurra una falla. Otros desencadenantes que se discutirán incluyen desencadenantes basados en eventos, uso y condición.
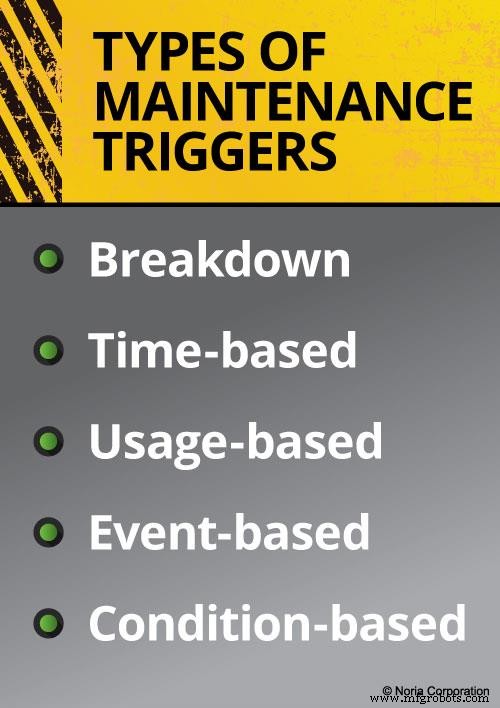
- Desglose activadores. Como se mencionó anteriormente, los activadores de averías se utilizan con programas de mantenimiento reactivo o de ejecución hasta la falla. Cuando un activo deja de funcionar, se activa una alerta que programa una orden de trabajo de mantenimiento para reparar el activo y restaurarlo a su condición operativa normal.
Los activadores de averías generalmente solo son útiles cuando una organización está ejecutando un grupo de equipos de bajo costo y fáciles de reemplazar y tiene piezas de repuesto y unidades en stock que se pueden intercambiar fácil y rápidamente, minimizando el tiempo de inactividad tanto como sea posible. El uso de activadores de avería es similar a un juego del gato y el ratón; no tener que planificar el mantenimiento permite un presupuesto de mantenimiento menos costoso, pero también significa que debe tener repuestos y equipos disponibles en todo momento, así como personal para solucionar problemas. Mantener acciones como esta va en contra de principios lean como Just in Time (JIT), que están diseñados para reducir las existencias retenidas.
- Activadores basados en el tiempo. Quizás los desencadenantes de mantenimiento más utilizados se basan en el tiempo. Estos están vinculados a un software de planificación de mantenimiento como un sistema de gestión de mantenimiento computarizado (CMMS) y alerta basada en un intervalo de tiempo preestablecido. Los activadores basados en el tiempo se utilizan en programas de mantenimiento predictivo y preventivo para tareas simples como lubricar engranajes o programar una inspección. Por ejemplo, cuando un activo alcanza un tiempo de ejecución de 14 días, se activa una alerta para que sea reparado. Fuera de un entorno de fabricación, un activador basado en el tiempo sería cambiar los filtros de aire de su unidad de calefacción, ventilación y aire acondicionado (HVAC) cada tres meses.
- Activadores basados en el uso. Al igual que los activadores basados en el tiempo, los activadores basados en el uso se basan en una métrica predeterminada basada en el uso del activo en cuestión, independientemente del período de tiempo. A diferencia de los activadores basados en el tiempo, que se llevan a cabo de forma reglamentaria independientemente de la condición de la máquina, los activadores basados en el uso significan que un activo solo recibe mantenimiento una vez que ha completado una cantidad específica de servicio.
Al igual que su automóvil recibe un cambio de aceite cada 5,000 millas, cualquier máquina que realice operaciones con restricciones de tiempo o cantidad se puede configurar con un disparador basado en el uso. Las lecturas del medidor se pueden agregar a un CMMS y usarse para configurar alertas cuando se alcanza una cantidad o valor deseado. Los activadores basados en el uso son una excelente manera de mantener el equipo sujeto a horarios irregulares y se usan con mayor frecuencia con programas de mantenimiento predictivo o preventivo.
- Activadores basados en eventos. Los desencadenantes de eventos se pueden utilizar para responder y evaluar equipos o instalaciones después de que se haya producido un evento, como un incendio o una inundación. Por ejemplo, la necesidad de programar y realizar verificaciones del sistema eléctrico y la infraestructura después de una inundación puede ser impulsada por un CMMS, y el sistema alerta al equipo de mantenimiento de tales tareas. Aunque los desencadenantes basados en eventos ocurren después de que ha tenido lugar un evento, es posible que no todos estén conectados directamente con el evento en sí. La mayoría de los desencadenantes basados en eventos actúan como controles de seguimiento de un evento.
- Activadores basados en condiciones. Los desencadenantes basados en condiciones se emplean de acuerdo con una evaluación de un activo individual. La evaluación se utiliza para determinar si es aceptable que el activo continúe funcionando o si es necesario el mantenimiento. Esta es una opción más detallada porque requiere que el personal de mantenimiento tenga conocimientos prácticos del activo para tomar una decisión informada sobre su estado.
El estado del equipo también se puede evaluar de forma remota. Los sensores colocados en un activo para monitorear parámetros como la temperatura, la vibración y el ruido se pueden usar como alertas activadas por condiciones. Por ejemplo, si un sensor nota un aumento de temperatura que supera un rango predeterminado, se envía una alerta para programar una inspección.
Tecnología de mantenimiento moderna
Una de las claves más importantes para que los fabricantes se destaquen en el mantenimiento operativo es utilizar los datos proporcionados por la tecnología moderna. Para hacer esto, se requiere una nueva solución de mantenimiento para mantener los activos, empleados y procesos organizados y funcionando sin problemas.
Los avances tecnológicos son más frecuentes en el monitoreo basado en condiciones en forma de mantenimiento proactivo y predictivo. Bajo estos tipos de mantenimiento, tecnologías como el análisis de aceite, el análisis de vibraciones, la termografía y el análisis de la corriente del motor pueden ayudar a determinar las causas raíz y los síntomas de falla, buscar beneficios como la extensión de la vida útil de la máquina y la detección temprana de fallas, y reducir la cantidad y el impacto de las fallas.
La revolución tecnológica actual en la industria manufacturera ha dado lugar a menos errores y defectos, ha optimizado la producción y ha reducido los costes laborales. Los sensores automatizados que pueden monitorear continuamente la maquinaria se encuentran entre las mayores mejoras. No solo se pueden emplear en varios tipos de mantenimiento, sino que también pueden generar una gran cantidad de datos que se pueden analizar y utilizar para mejorar los procesos.
Las soluciones CMMS pueden ayudar a aprovechar todos estos datos e integrarlos con cuatro aspectos clave para una estrategia de tecnología de mantenimiento moderna:usar el mantenimiento predictivo, enfocarse en los datos y el IoT, administrar el inventario y mejorar los ciclos para un éxito continuo.
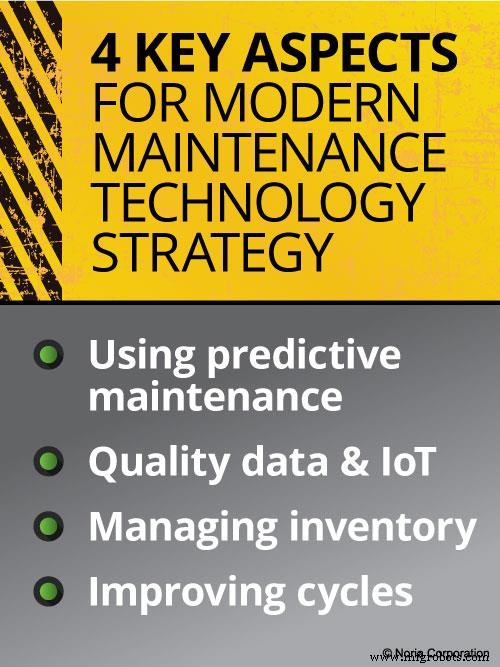
- Uso del mantenimiento predictivo: Si bien el mantenimiento preventivo es una buena manera de evitar que funcione hasta fallar y reducir el tiempo de inactividad, el siguiente paso es implementar el mantenimiento predictivo para recopilar y analizar de manera eficiente los datos que están generando sus máquinas.
- Datos de calidad e IoT: Es importante tener un CMMS que pueda manejar la enorme cantidad de datos que se producen en su planta. Querrá integrar datos desde sensores básicos autoinstalados a sensores integrados y todo lo demás. Por lo general, esto significa que debe buscar un CMMS con una estrategia de IoT para que no esté casado con un solo tipo de hardware.
El IoT se emplea para integrar de forma inalámbrica los datos recopilados de los activos en la planta a un CMMS utilizado en toda la organización. Esto requerirá configurar los activadores y alertas discutidos anteriormente para crear automáticamente órdenes de trabajo sin interacción humana.
- Gestión de inventario: Una encuesta reciente de Plant Services descubrió que casi el 29 por ciento de los encuestados tenía una acumulación de tareas de mantenimiento de tres a cuatro semanas. Adoptar siempre un enfoque reactivo para el mantenimiento solo aumenta la acumulación de pedidos, lo que significa que sus activos no reciben el mantenimiento adecuado que necesitan. El seguimiento de las tareas atrasadas en un CMMS lo ayuda a identificar problemas, causas y soluciones, y lo lleva a adoptar una cultura más proactiva para reducir el atraso.
- Mejora de ciclos: Aprovechar los datos de una configuración de piso de planta modernizada e integrarlos a través de un CMMS lo coloca en el camino para mejorar su ciclo de mantenimiento, mantener los ahorros y aumentar la eficiencia.
Tendencias de la tecnología de mantenimiento moderno
- Internet industrial de las cosas: Como se mencionó anteriormente, la Internet de las cosas, y más específicamente la Internet industrial de las cosas (IIoT), es una forma moderna de recopilación de datos automatizada mediante el uso de una red de sensores inalámbricos. Hoy en día, los sensores multipropósito de bajo costo están más disponibles que nunca. Pueden configurarse en diferentes redes de sensores en múltiples activos industriales y usarse para recopilar automáticamente datos de mantenimiento. Esto elimina la necesidad de datos manuales costosos y que consumen mucho tiempo, que son propensos a errores humanos.
- Realidad aumentada (RA): El mantenimiento y la formación remotos están comenzando a beneficiarse de la RA gracias a la capacidad de ofrecer instrucciones remotas. Este enfoque personalizado permite personalizar las tareas de mantenimiento de acuerdo con la comprensión y el nivel de habilidad del empleado. La realidad aumentada puede facilitar la capacitación proporcionada por un proveedor de equipos o personal de mantenimiento de alto nivel a través de una presentación cibernética que muestra cómo realizar una tarea.
Si bien sigue siendo una tendencia emergente, el uso de RA para la formación está ganando popularidad debido a la creciente complejidad de los equipos industriales. La realidad aumentada puede aliviar la carga del personal de mantenimiento que intenta mantenerse al día con las variaciones en los nuevos equipos, incluidas las capacidades tecnológicamente avanzadas que acompañan a cada activo. Ya existen varios proveedores que ofrecen soluciones de RA a gran escala para tareas de mantenimiento y proveedores de IIoT que proporcionan RA como parte de un paquete integrado.
- Mantenimiento como servicio (MaaS): MaaS es un paradigma relativamente nuevo para el mundo del mantenimiento. Básicamente, implica la prestación de servicios de mantenimiento a pedido. Con MaaS, un proveedor puede cobrar al operador de la planta de acuerdo con los servicios de mantenimiento que realmente utiliza en lugar de una tarifa de servicio fija. Los proveedores hacen esto recopilando y procesando grandes cantidades de datos, almacenándolos a través de la nube y programando tareas basadas en estos datos. Los servicios incluyen:
- predecir la vida útil de un activo u ofrecer información sobre los intervalos de mantenimiento óptimos;
- proporcionar manuales de servicio, videos y soporte interactivo de realidad virtual (VR) y AR;
- configurar la tecnología de la información (TI) y otros sistemas dentro de una planta en función de los resultados analíticos; y
- proporcionando estadísticas e informes detallados sobre la maquinaria.
Los proveedores están empezando a poner a disposición las primeras etapas de los programas MaaS. Los elevadores ThyssenKrupp ahora vienen con un programa de mantenimiento proactivo que predice problemas antes de que ocurran y notifica a las personas apropiadas para realizar una inspección. BMW también planea llevar MaaS al consumidor en un futuro cercano, ofreciendo programas que permitirán a los propietarios de automóviles saber cuál es el mejor momento para realizar el mantenimiento de sus vehículos.
Mantenimiento y reparación de equipos
- Diferencia entre mantenimiento preventivo y mantenimiento predictivo
- Optimización del mantenimiento preventivo mediante un CMMS
- Mantenimiento preventivo vs mantenimiento predictivo:Vuelta a lo básico
- Mantenimiento preventivo:descripción general
- Mantenimiento preventivo
- Uso de software de mantenimiento preventivo para la fabricación
- Cómo hacer el mantenimiento preventivo planificado (PPM)
- Cómo programar órdenes de trabajo de mantenimiento preventivo
- Beneficios clave del software de mantenimiento preventivo
- ¿Qué es el Mantenimiento Preventivo?
- 5 tipos de mantenimiento que debes conocer