Síntesis de grafeno de una sola capa de gran superficie utilizando aceite de palma de cocción refinado sobre sustrato de cobre mediante CVD asistido por pulverizador
Resumen
Presentamos una síntesis de grafeno de una sola capa de gran superficie sobre un sustrato de cobre utilizando un aceite de palma de cocción refinado, una única fuente de carbono natural, mediante un sistema de deposición de vapor químico asistido por un inyector en aerosol hecho en casa. Se estudian los efectos de la distancia entre la boquilla de aspersión y el sustrato y la temperatura de crecimiento. A partir del análisis de mapeo Raman, una distancia más corta de 1 cm y una temperatura de alrededor de 950 ° C conducen al crecimiento de grafeno de una sola capa de área grande con una cobertura de hasta el 97% del tamaño del área medida de 6400 μm 2 . La cristalinidad del grafeno de capa única crecido es relativamente buena debido al alto porcentaje de distribución de los valores de FWHM de la banda 2D que está por debajo de 30 cm −1 . Sin embargo, la concentración de defectos es relativamente alta y sugiere que es necesario introducir una técnica de enfriamiento rápido.
Introducción
El grafeno, un nanomaterial bidimensional, posee una sp 2 -uniones de átomos de carbono hibridados con un solo átomo de espesor [1]. Sus extraordinarias propiedades, como transporte electrónico superior, conductividad térmica, durabilidad mecánica, etc., han atraído enormes estudios para diversas aplicaciones potenciales en nanoelectrónica [2], optoelectrónica [3], supercondensadores y almacenamiento de energía electroquímica [4], células solares [ 5] y sensores [6]. De hecho, muchas aplicaciones, como los detectores portátiles, la piel electrónica y los sensores de presión, requieren estructuras de grafeno flexibles de gran superficie [7]. Por lo tanto, para llevar el grafeno a aplicaciones prácticas, se requiere absolutamente una tecnología para realizar grafeno de gran superficie con un espesor uniforme y sin defectos. Dado que la exfoliación micromecánica parece tener una limitación para obtener grafeno de gran superficie con un espesor uniforme, aunque puede producir grafeno de alta cristalización con menos defectos [8, 9], la deposición química en fase de vapor (CVD) se ha considerado una técnica prometedora para superar tales limitación [10, 11]. En principio, la calidad del grafeno cultivado por CVD está controlada por varios parámetros de crecimiento principales, como la fuente de carbono, la temperatura, el sustrato y la presión [12]. Generalmente, se requiere una temperatura elevada (superior a 800 ° C) para producir grafeno de alta calidad mediante CVD. Sin embargo, se informó que un proceso de CVD modificado, específicamente el método de CVD encerrado en carbono (CE-CVD), podía hacer crecer grafeno sobre láminas de Cu a una temperatura baja de casi 500 ° C [13]. En la técnica de CVD, por lo general, el grafeno se cultiva en un sustrato metálico utilizando gases de hidrocarburos tóxicos y explosivos como metano [14], acetileno [15] y propileno [16] a través de CVD de baja presión [17] o presión atmosférica [18]. , que llevan al uso de los sistemas de crecimiento con alto grado de seguridad y precauciones de manipulación.
Se han realizado muchos intentos alternativos benignos para reemplazar estos precursores típicos con hidrocarburos peligrosos moderados suministrados a partir de fuentes de carbono líquido o sólido. Por ejemplo, Weiss et al. investigó el crecimiento de grafeno sobre sustrato de cobre (Cu) utilizando etanol [19]. Choi y col. informaron del crecimiento en un ambiente oxidado mediante el uso de una combinación de etanol y metanol como fuente de carbono [20]. También se han estudiado otras fuentes de carbono líquido similares, como el benceno [21] y el tolueno [22]. También se ha informado de un resultado motivado sobre el crecimiento del grafeno a partir de fuentes naturales de carbono como el alcanfor [23, 24]. Recientemente, hemos informado del crecimiento de grafeno mixto simple y bicapa libre de defectos sobre sustrato de níquel (Ni) utilizando un aceite de palma refinado para cocinar [25, 26] mediante CVD térmico. Aquí, el aceite de palma de cocción refinado evaporado se entregó al sustrato de Ni mediante un flujo constante de argón / hidrógeno (Ar / H 2 ) gas portador. El crecimiento se realizó a una temperatura de 900 ° C durante 15 s, antes de que se enfriara rápidamente mediante la técnica de enfriamiento rápido. Sin embargo, la cobertura del grafeno cultivado es relativamente baja, alrededor del 60%. En este artículo, demostramos una ruta alternativa para sintetizar grafeno de una sola capa de área grande con una cobertura de hasta 97% utilizando un sistema CVD asistido por inyector en aerosol casero sin introducir H 2 durante el crecimiento por primera vez. Este inyector de pulverización permite la atomización del precursor en gotitas del tamaño de una micra. Las gotas atomizadas permiten una mejor cinética de descomposición debido al aumento de la superficie en comparación con los métodos convencionales de CVD. Un privilegio más es que la tasa de flujo de inyección de precursor permite el control del flujo de gotas que controla la tasa de transferencia de masa durante la deposición de vapor [27].
Métodos
Se utiliza una lámina de Cu comercial (Nilaco, 99,9% de pureza, 30 μm de espesor) como catalizador metálico. En primer lugar, se enjuaga una lámina de Cu cortada en 1 cm × 1 cm con agua destilada (DI), seguido de un tratamiento con ácido acético 1 M / H 2 O (1:10) a 60 ° C durante 30 min. Luego, esta muestra de Cu se enjuaga con alcohol isopropílico y acetona durante 10 min en un baño ultrasónico (35% de potencia, UP400S, Hielscher, Alemania) para eliminar cualquier contaminación y óxido nativo de la superficie. Luego, la muestra de Cu se seca usando un soplado de nitrógeno. Las figuras 1a yb muestran el esquema de una configuración de CVD asistida por inyector de pulverización casera y el gráfico de tiempo de crecimiento, respectivamente. Una cantidad específica de aceite de palma de cocción refinado líquido se suministra a la cámara mediante un sistema de inyección de fluido de alta precisión (Sono-Tek, EE. UU.) Con una capacidad de inyección de 0,01 ml / s. A continuación, se carga un sustrato de Cu tratado en la cámara de reacción facilitada con un calentador de sustrato como se muestra en la Fig. 1a. Después de cargar el sustrato de Cu, la cámara de reacción es evacuada por una bomba rotatoria hasta 6 Pa antes de ser purgada con Ar. Estas evacuaciones y procesos de purga de Ar se repiten tres veces para minimizar el aire atrapado en la cámara de reacción.
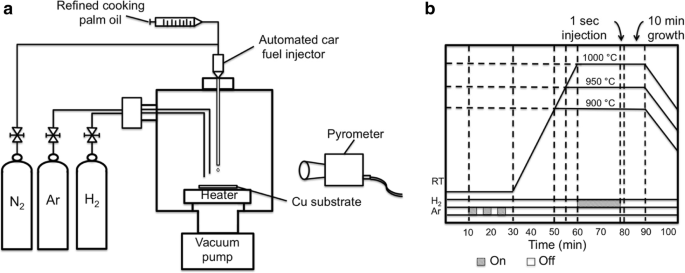
un Esquema de una configuración de CVD asistida por inyector en aerosol hecha en casa y b tabla de tiempo de crecimiento
Los efectos de la distancia entre la boquilla y el sustrato, d , se estudian. Aquí, d se fija en 1, 3 y 6 cm. El sustrato se calienta a las temperaturas de crecimiento establecidas, T , es decir, 900, 950 y 1000 ° C mientras se mantiene la cámara de reacción en un entorno de Ar. Después de alcanzar la temperatura establecida, el hidrógeno (H 2 ) de 40 sccm se introduce durante 20 min. Este tratamiento de recocido en H 2 se realiza con el propósito de eliminar aún más la contaminación restante y reducir la rugosidad de la superficie de Cu. Después de eso, el flujo de H 2 se detiene y se inyecta un aceite de palma de cocción refinado durante 1 s (~ 0,05 ml) en la cámara de reacción utilizando un inyector de combustible computarizado (inyector de combustible de automóvil). Luego, el crecimiento (o calentamiento) se mantiene a la temperatura establecida durante 10 min. Después del crecimiento, el calentador se apaga y la muestra se enfría a temperatura ambiente en ambiente de vacío con evacuación continua. Dado que en este trabajo se utiliza un inyector de pulverización automático para controlar la cantidad o concentración de carbono (C), se espera que el elemento C pueda alcanzar y extenderse uniformemente sobre el sustrato calentado después de la descomposición térmica efectiva del aceite de palma refinado para cocinar. . La descomposición se puede expresar mediante la siguiente reacción:
$$ {\ mathrm {CH}} _ 3 {\ left ({\ mathrm {CH}} _ 2 \ right)} _ {14} \ mathrm {COOH} \ a 16 \ mathrm {C} +16 {\ mathrm {H }} _ 2 \ uparrow + {\ mathrm {O}} _ 2 \ uparrow $$ (1)Se supone que el mecanismo de crecimiento sigue el mecanismo bien aceptado descrito en [22, 23]. Aquí, el elemento C descompuesto se absorbe en el sustrato de Cu durante la etapa de calentamiento y luego se desorbe de nuevo a la superficie del sustrato de Cu para formar una capa de grafeno durante la etapa de enfriamiento. Dado que el enfriamiento se realiza mediante la evacuación continua, se especula que el sustrato se enfría a una velocidad relativamente más rápida.
La microscopía óptica se utiliza para observar la morfología y homogeneidad de las películas de grafeno en crecimiento sobre sustrato de Cu. Las características estructurales, como el número de capas de grafeno, la homogeneidad y los defectos, se examinan mediante espectroscopía micro-Raman (WiTec Alpha 300) a una longitud de onda del láser de excitación de 514 nm. Aquí, se utiliza una lente de aumento de × 100, lo que da un tamaño de punto de láser de aproximadamente 400 nm. El tiempo de integración es de 0,5 s, y la potencia del láser se mantiene por debajo de 1 mW para evitar cualquier daño o calentamiento de la muestra, lo que puede inducir la desorción de los adatomos del grafeno. El espectrómetro está equipado con una etapa piezoeléctrica que permite el mapeo Raman de un área de hasta 200 μm × 200 μm. Para investigar la falta de homogeneidad de la película de grafeno, el mapeo Raman se utiliza para recopilar una gran cantidad de espectros con diferente grado de desorden. Aquí, el número analizado de espectros es 1024 para el tamaño de 80 × 80 μm. Las mediciones Raman se realizan sin transferir la película de grafeno a un nuevo sustrato plano. Por tanto, se puede decir que la presentación de datos del grafeno se encuentra en su estado original. Vale la pena señalar que la fuerte señal de fondo del sustrato de Cu se ha eliminado de cada espectro mediante sustracción manual.
Resultados y discusión
Las Figuras 2a-c muestran la distribución de calor simulada (vista transversal) en la cámara de reacción junto con la ubicación de la boquilla a una distancia de 1, 3 y 6 cm del sustrato. La extensión de la ley de Fourier a una cantidad vectorial bidimensional da como resultado el flujo de calor por unidad de área como en la Ec. 2, donde la conductividad térmica relaciona el flujo de calor y el gradiente de temperatura linealmente. q xy es el flujo de calor en el x y y direcciones (W / m 2 ), k es la constante de conductividad térmica (W / m K) y T es la temperatura (K).
$$ {\ overrightarrow {q}} _ {xy} =- k \ izquierda (i \ frac {\ parcial T} {\ parcial x} + j \ frac {\ parcial T} {\ parcial y} \ derecha) $ (2)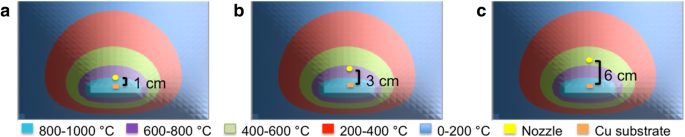
Distribución de calor (vista transversal) en la cámara de reacción y la ubicación de la boquilla del sustrato con una distancia de a 1 cm, b 2 cm y c 6 cm
Se utilizó un método de diferencias finitas para resolver la ecuación. Por lo tanto, por el bien de los elementos de control diferencial, solo la factorización de la conducción en estado estable de conservación de energía tiene lugar como en la Ec. 3.
$$ \ frac {\ parcial} {\ parcial x} \ izquierda (k \ frac {\ parcial T} {\ parcial x} \ derecha) + \ frac {\ parcial} {\ parcial y} \ izquierda (k \ frac {\ parcial T} {\ parcial y} \ derecha) + \ punto {q} =0 $$ (3)Respectivamente, cuando la temperatura del sustrato se establece en el rango de 800–1000 ° C. Estas ubicaciones se han seleccionado en este estudio de modo que el aceite de palma se inyecte desde tres regiones diferentes de temperaturas, es decir, 800–1000 ° C (1 cm), 600–800 ° C (3 cm) y 400–600 ° C (6 cm). Las figuras 3a-c muestran la imagen óptica del grafeno recién crecido en Cu en d =1, 3 y 6 cm, respectivamente, cultivados a una temperatura de 1000 ° C. Está bien informado que una temperatura más alta es mejor para la descomposición completa de la fuente, así como para la absorción uniforme del elemento C en el sustrato de Cu. Como puede verse en la Fig. 3a, el color de la superficie de Cu es casi similar al color original del sustrato de Cu no calentado, lo que indica muy pocas capas de grafeno. El color se vuelve ligeramente más oscuro para la muestra con d =3 cm. Sin embargo, se observan muchos puntos negros en las muestras cultivadas en d =6 cm, lo que indica la formación de carbono amorfo en las cavidades (orificios) y raspaduras del sustrato de Cu [26]. Vale la pena señalar que el tratamiento del sustrato metálico por H 2 el recocido puede reducir la rugosidad de la superficie [26]. Sin embargo, tales cavidades y arañazos que se forman generalmente durante la producción de la hoja de Cu no pueden eliminarse si la profundidad es demasiado grande. Se ha informado que el carbono amorfo es fácil de formar en tales cavidades y rayones debido a la acumulación del elemento C. A partir de estos resultados, se puede suponer que d =1 cm es la mejor distancia para producir unas pocas capas de grafeno uniformes con una excelente supresión de las estructuras de carbono amorfo.

Las imágenes ópticas del grafeno sobre sustrato de Cu cultivado a una temperatura de 1000 ° C con la distancia entre una boquilla y un sustrato de a 1 cm, b 3 cm y c Crecimiento de 6 cm
Las figuras 4a-c muestran los espectros Raman del grafeno cultivado en d =1, 3 y 6 cm, respectivamente. Tres picos intensos a ~ 1350 cm −1 , ~ 1560 cm −1 y ~ 2691 cm −1 correspondientes a las bandas G, D y 2D, respectivamente, se pueden observar claramente en todas las muestras. Un pico correspondió a la banda D + D '(~ 3250 cm −1 ) solo se observa en la muestra cultivada en d =6 cm indica la existencia de carbono amorfo en la estructura, como se muestra en la Fig. 4c. Las figuras 5a-c muestran el mapeo Raman de la relación de intensidad de las bandas 2D y G ( I 2D / Yo G ), Fig. 5d – f el mapeo Raman de la relación de intensidad de las bandas D y G ( I D / Yo G ) y la Fig. 5g – i los valores de la mitad del máximo de ancho completo (FWHM) de la banda 2D para cada distancia, es decir, 1, 3 y 6 cm. Con base en estos mapeos Raman, los histogramas para indicar los porcentajes de distribución de I 2D / Yo G , yo D / Yo G , y FWHM se presentan en la Fig. 5j – 1, respectivamente. Como se muestra en la Fig. 5j, la muestra cultivada en d =1 cm tiende a estar dominado por el grafeno de una sola capa, mientras que las muestras cultivadas en d =3 y 6 cm están dominados por grafeno bicapa y multicapa. Cabe señalar que la determinación de espesores de capa se realiza en base a los siguientes valores:capa única, I 2D / Yo G ≥ 2; bicapa, 1 ≤ I 2D / Yo G <2; y multicapa, I 2D / Yo G <1 [28, 29]. La muestra cultivada en d =1 cm parece generar menos concentración de defectos en comparación con la muestra cultivada en d =6 cm como se puede entender en la Fig. 5k. Los valores de FWHM de la banda 2D para todas las muestras están principalmente por debajo de 10 cm −1 lo que indica una cristalinidad relativamente alta del grafeno desarrollado como se muestra en la Fig. 5l. Se puede concluir que la distancia entre la boquilla y el sustrato debe ser pequeña para que las gotas se puedan descomponer de manera efectiva antes de que alcancen la superficie de Cu y se absorban uniformemente en la superficie de Cu.
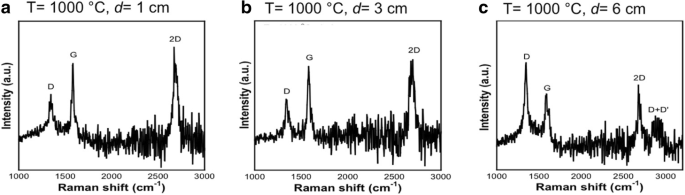
Espectro Raman único de grafeno sobre sustrato de Cu cultivado a una temperatura de 1000 ° C con una distancia entre una boquilla y un sustrato de a 1 cm, b 3 cm y c 6 cm
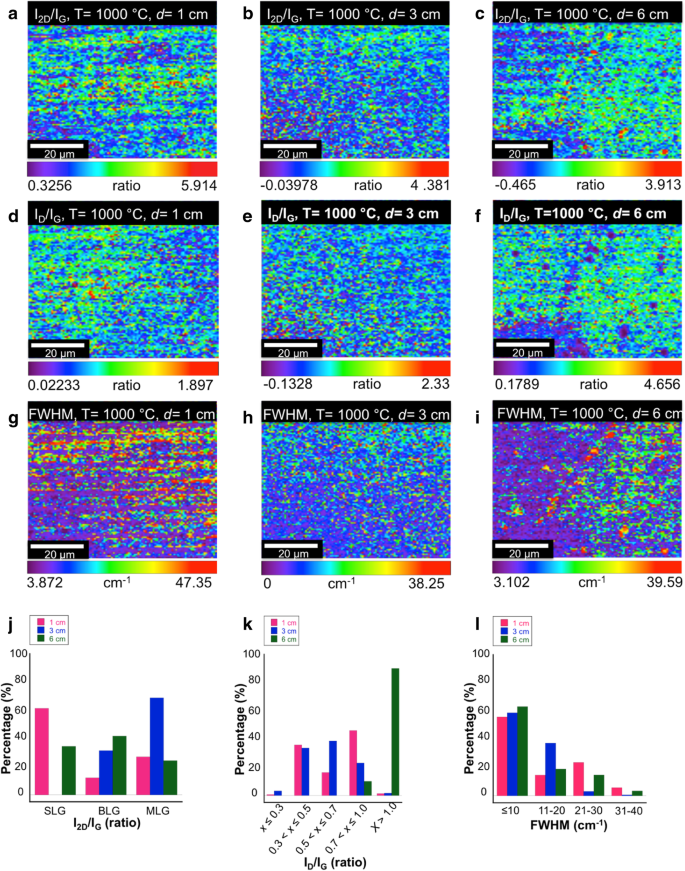
Imágenes de mapeo Raman de grafeno en sustrato de Cu para a - c yo 2D / Yo G , d - f yo D / Yo G y g - yo Valor FWHM de la banda 2D, para 1 cm, 3 cm y 6 cm. Además, los histogramas para indicar el porcentaje de distribución de la relación de intensidad, j yo 2D / Yo G , k yo D / Yo G y l Valor FWHM de la banda 2D. Temperatura de crecimiento 1000 ° C
Las Figuras 6a yb muestran los espectros Raman de las muestras cultivadas a temperaturas más bajas de 900 y 950 ° C, respectivamente. Aquí, la distancia entre la boquilla y el sustrato se fija en d =1 cm ya que esta distancia resulta ser una distancia adecuada para obtener la mejor calidad de grafeno. Como se muestra en la Fig. 6a, se puede decir que la película desarrollada a 900 ° C está dominada por una película de carbono amorfo y casi no se observa crecimiento de grafeno. Mientras tanto, la muestra cultivada a 950 ° C confirma el crecimiento de la capa de grafeno. La figura 6c-e muestra el mapeo Raman de I 2D / Yo G , yo D / Yo G y FWHM de la banda 2D para la muestra cultivada a 950 ° C, respectivamente. Muestra claramente que la película desarrollada posee una excelente uniformidad de capa refiriéndose a la distribución uniforme del color. Los histogramas generados a partir de estos mapeos Raman se utilizan para indicar los porcentajes de distribución de I 2D / Yo G , yo D / Yo G , y FWHM como se presenta en la Fig. 6f – h, respectivamente. Como se muestra en la Fig. 6f, las muestras cultivadas a tal temperatura parecen estar dominadas por grafeno de una sola capa con una cobertura de hasta el 97%. Sin embargo, la muestra cultivada también parece generar una concentración de defectos ligeramente mayor en comparación con la muestra cultivada a 1000 ° C, como puede entenderse comparando la Fig. 6g y la Fig. 5k. Se especula que este defecto se genera debido a una velocidad de enfriamiento considerablemente lenta. En este sentido, se informó que un enfriamiento rápido es una solución capaz de obtener una capa de grafeno libre de defectos. Se ha informado que el crecimiento de grafeno mediante la técnica de CVD utilizando Cu como catalizador metálico exhibe un mecanismo mediado por la superficie debido a sus propiedades de baja solubilidad en carbono. Utilizando CVD a presión atmosférica (APCVD), se puede cultivar grafeno monocapa de gran superficie. Desafortunadamente, bajo una alta concentración de carbono, los elementos C descompuestos en la fase gaseosa seguirán depositándose para formar un apilamiento de grafeno hasta que la superficie esté cubierta por BLG y MLG. Aquí, la formación de grafeno sigue a una segregación y precipitación del mecanismo de crecimiento. En tales condiciones, se necesita un enfriamiento rápido para suprimir la deposición de grafeno. Además, el grafeno uniforme se puede cultivar bajo un sistema CVD de condiciones de vacío ultra alto o baja presión. El enfriamiento rápido da como resultado la reducción del tamaño de los granos de Cu equiaxiales, lo que reducirá los sitios de los límites de los granos. Esto eventualmente forzará la redistribución de átomos de C de una manera homogénea y uniforme. [25, 26]. Los valores de FWHM de la banda 2D se encuentran principalmente en el rango de 21 a 30 cm −1 lo que indica una cristalinidad relativamente alta del grafeno desarrollado como se muestra en la Fig. 6h.
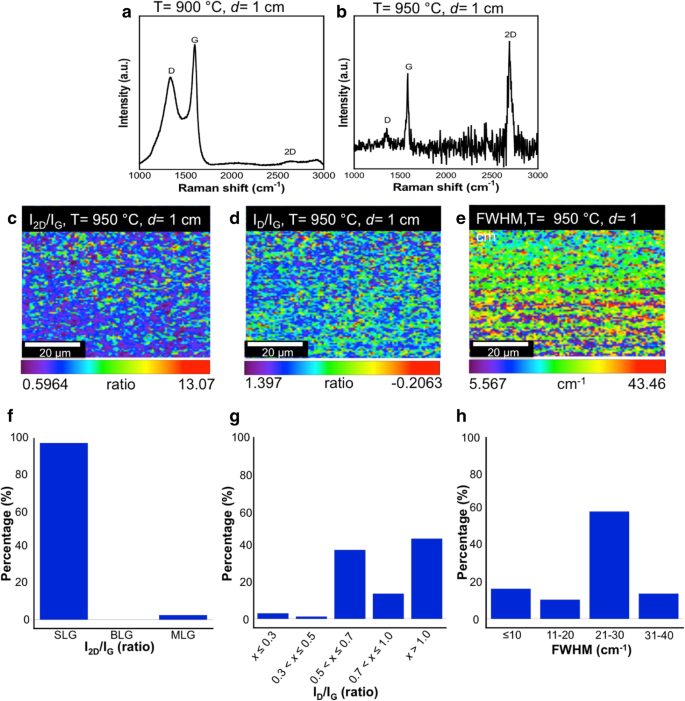
Espectro Raman único para la muestra cultivada a temperaturas de a 900 ° C y b 950 ° C. Imágenes de mapeo Raman de muestra cultivada en sustrato de Cu a una temperatura de 950 ° C para c yo 2D / Yo G , d yo D / Yo G y e Valor FWHM de la banda 2D. Además, los histogramas para indicar el porcentaje de distribución de la relación de intensidad, f yo 2D / Yo G , g yo D / Yo G y h Valor FWHM de la banda 2D. La distancia entre la boquilla y el sustrato es de 1 cm
Conclusiones
Se realizó un crecimiento de grafeno de una sola capa de gran área sobre sustrato de Cu utilizando un aceite de palma de cocción refinado, una única fuente de carbono natural, mediante un sistema de deposición de vapor químico asistido por un inyector en aerosol hecho en casa. Se estudian los efectos de la distancia entre la boquilla de aspersión y el sustrato y la temperatura de crecimiento. El crecimiento de grafeno de una sola capa de gran superficie con una cobertura de hasta el 97% del tamaño del área medida de 6400 μm 2 se obtuvo en condiciones óptimas de proceso (temperatura de crecimiento de 950 ° C y distancia entre la boquilla y el sustrato de 1 cm). La cristalinidad del grafeno de una sola capa crecido es relativamente buena con un alto porcentaje de distribución de los valores de FWHM de la banda 2D que está por debajo de 30 cm −1 . Sin embargo, la concentración de defectos es relativamente alta y sugiere la necesidad de un tratamiento de enfriamiento rápido. Más estudios sobre las propiedades como la estructura atómica, la transmisión y la resistencia justificarán aún más el rendimiento del grafeno actual en comparación con el otro grafeno cultivado.
Abreviaturas
- Ar:
-
Argón
- C:
-
Carbono
- Cu:
-
Cobre
- CVD:
-
Deposición de vapor químico
- FWHM:
-
Medio máximo de ancho completo
- H 2 :
-
Hidrógeno
Nanomateriales
- Aceite de cocina
- Optimización de los intervalos de drenaje de aceite utilizando BN frente a AN
- Eliminación por adsorción de iones de cobre (II) de una solución acuosa utilizando un nano-adsorbente de magnetita de residuos de cascarilla de molino:síntesis, caracterización, adsorción y mode…
- Síntesis biogénica, caracterización y evaluación del potencial antibacteriano de nanopartículas de óxido de cobre contra Escherichia coli
- Nanopartículas de sílice para la administración intracelular de proteínas:un nuevo enfoque de síntesis que utiliza proteína verde fluorescente
- Síntesis en un solo recipiente del soporte jerárquico de la aleación de Pd-Cu similar a una flor en el grafeno hacia la oxidación del etanol
- Evaluación de estructuras de grafeno / WO3 y grafeno / ceO x como electrodos para aplicaciones de supercondensadores
- Síntesis fácil y respetuosa con el medio ambiente de nanocables de Co3O4 y su prometedora aplicación con grafeno en baterías de iones de litio
- Síntesis sonoquímica de un solo paso y propiedades fotocatalíticas fáciles de compuestos de puntos cuánticos de grafeno / Ag3PO4
- Síntesis rápida de nanocristales de Pt y materiales de Pt / La2O3 microporosos mediante levitación acústica
- Crecimiento directo de un diodo emisor de luz amarillo a base de nanocables de nitruro III en cuarzo amorfo utilizando una capa intermedia fina de Ti