Una guía del administrador de mantenimiento para crear y usar AMFE
Un feroz ataque de ransomware afectó a la ciudad de Atlanta en marzo de 2018. Terminó siendo una de las infracciones más costosas de la última década. Los servicios públicos se interrumpieron. Los departamentos se vieron obligados a hacer el papeleo esencial a mano. Y le costó al gobierno de la ciudad $ 17 millones.
Cuando el polvo se asentó, una cosa quedó clara:la ciudad no estaba preparada para este desastre. Una auditoría realizada dos meses antes de la infracción encontró 2000 vulnerabilidades en el sistema de TI de la ciudad. Fue un buen paso, pero fue muy poco, demasiado tarde.
Lo que sucedió en Atlanta es una advertencia con una gran lección:el riesgo nunca se puede eliminar, pero se puede manejar. Esto es especialmente cierto en el mantenimiento. La falla del equipo es inevitable. Pero saber cómo reducir la probabilidad de fallas y cómo reaccionar cuando sucede, es fundamental para el éxito.
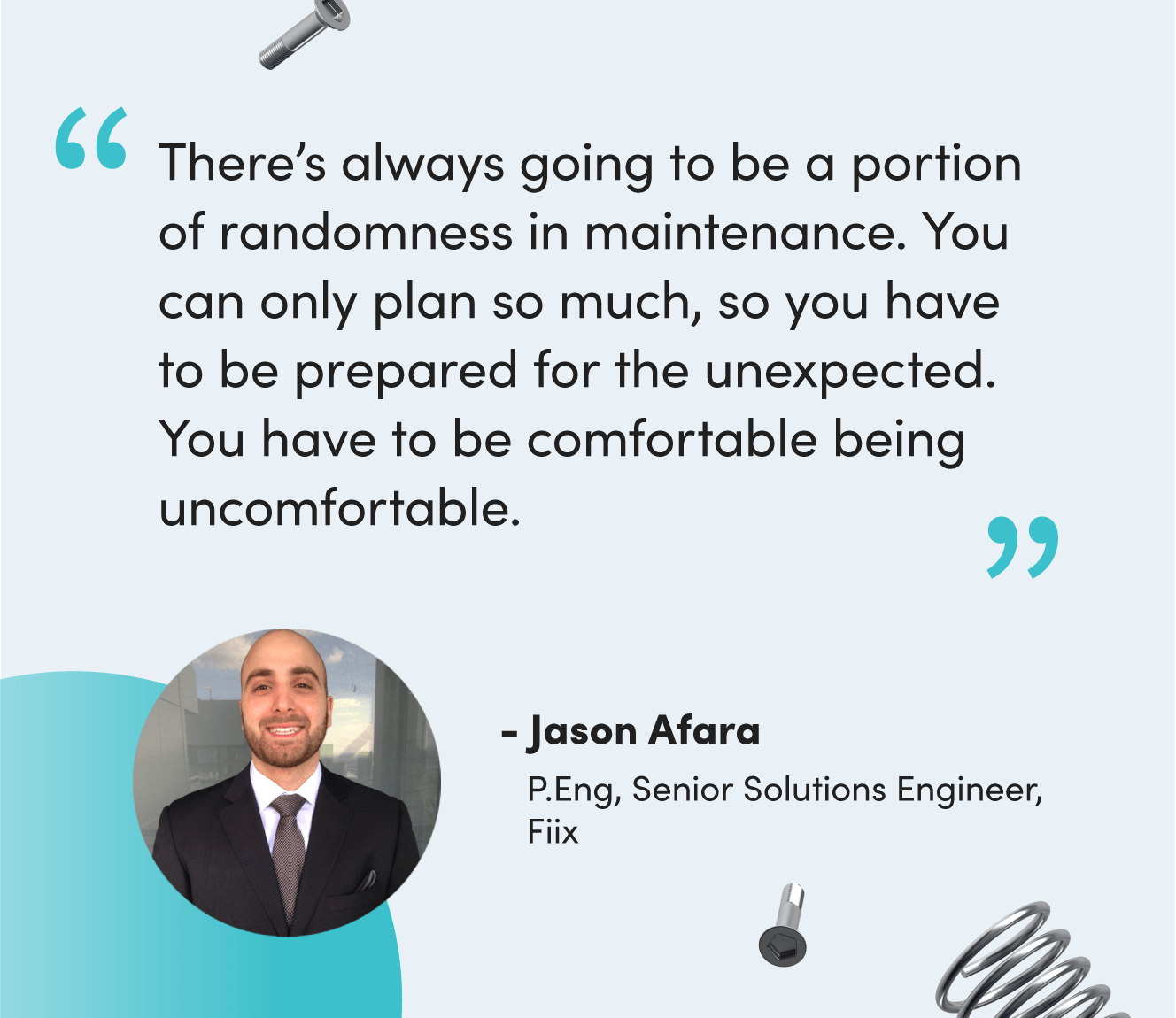
Un análisis de modos y efectos de falla (FMEA) es una herramienta para comprender y anticipar fallas para que pueda limitar su impacto. En este artículo, aprenderá:
- Qué es un FMEA
- Los diferentes tipos de AMFE
- Cómo crear un FMEA
- Y cómo los equipos de mantenimiento pueden utilizar un FMEA
¿Qué es un FMEA?
Un análisis de modos y efectos de falla, o FMEA, identifica y documenta todas las formas en que un equipo puede fallar y el impacto potencial de estas fallas. Describe:
- Modos de falla para componentes individuales
- Las consecuencias de las fallas en la productividad y la seguridad
- Un plan para prevenir o reaccionar ante estos problemas
La construcción de AMFE es un componente clave del mantenimiento centrado en la confiabilidad (RCM).
Hay tres objetivos principales de un FMEA:
- Prevenga futuras averías reduciendo la probabilidad de fallas comunes y críticas mediante el mantenimiento planificado y los procedimientos operativos estándar
- Reducir los tiempos de respuesta, disminuir el tiempo de inactividad y mejorar la salud y la seguridad cuando ocurre una falla en los activos
- Priorizar el mantenimiento preventivo y correctivo en situaciones que no sean de emergencia
¿Cuáles son los diferentes tipos de AMFE?
Los AMFE se pueden clasificar en subtipos según el tipo de riesgo que están evaluando y el impacto que tienen. Aquí hay un resumen rápido de cada tipo de AMFE:
- FFMEA (modo de falla funcional y análisis de efectos) :Un FFMEA analiza los riesgos que afectan la forma en que funciona un sistema. El objetivo de un FFMEA (a veces llamado modo de falla del sistema y análisis de efectos) es prevenir estas fallas antes de que sucedan.
- DFMEA (modo de falla de diseño y análisis de efectos) :Una DFMEA evalúa los riesgos de un activo en la etapa de diseño. El propósito de este análisis es encontrar y corregir problemas potenciales con un activo antes de que se implemente para aumentar su confiabilidad, reducir la cantidad de mantenimiento necesario y extender el ciclo de vida del activo.
- PFMEA (modo de falla del proceso y análisis de efectos) :Un PFMEA busca posibles fallas dentro de un proceso. La diferencia entre un PFMEA y otros tipos de AMFE es que se centra en lo que puede salir mal durante la operación y el mantenimiento de un sistema.
- FMECA (modo de falla, efectos y análisis de criticidad) :Un FMECA (o análisis de criticidad) analiza tanto los modos de falla como el nivel de riesgo asociado con esos modos de falla.
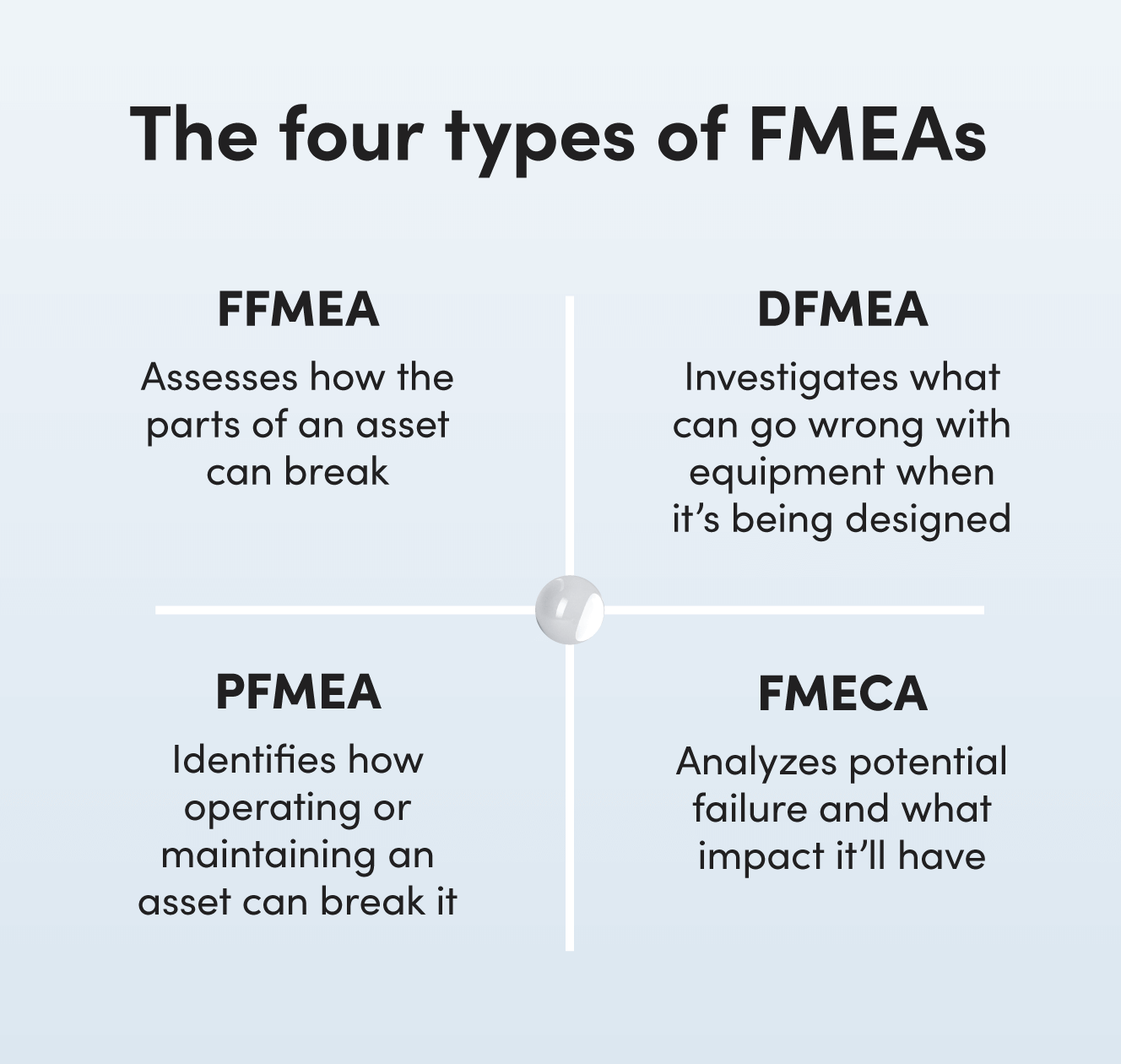
¿Cuál es la diferencia entre un modo de falla y un código de falla?
Un modo de falla es un error o defecto que causa el mal funcionamiento de un sistema. Un ejemplo de un modo de falla en un transportador de transferencia de velocidad variable podría ser el agarrotamiento del rodamiento. Un cojinete roto hará que el transportador se ralentice o deje de funcionar.
Un código de falla es un modo de falla representado por una etiqueta alfanumérica. Los códigos de falla se utilizan a menudo en el software CMMS como una forma de transmitir información rápidamente y clasificar o informar sobre fallas. Los códigos de falla suelen estar respaldados por tres piezas de información contextual. Un ejemplo de un código de falla se ve así:
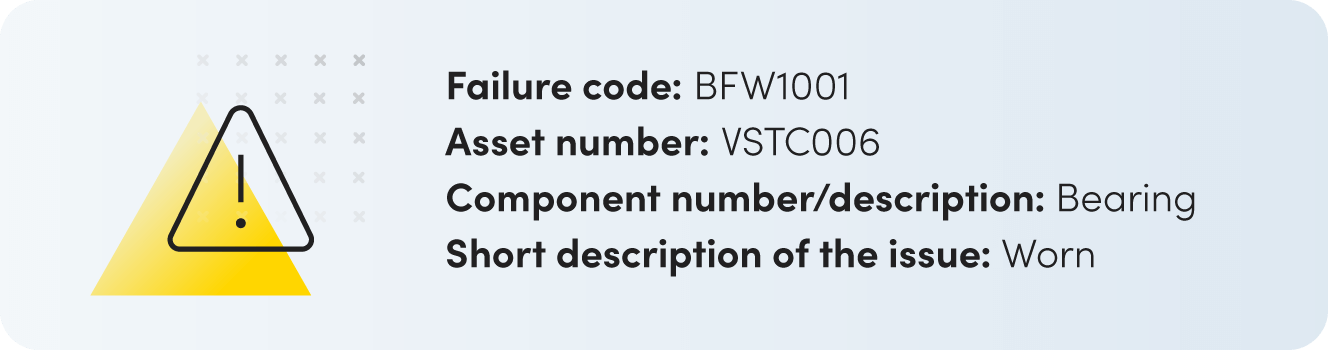
¿Cuál es la diferencia entre FMEA y FRACAS?
Un análisis de modos y efectos de falla describe la posible falla, sus causas y su impacto. Es un proceso que enumera posibles incidentes futuros y sus posibles causas raíz. Es una medida proactiva.
Un sistema de notificación, análisis y acción correctiva de fallas (FRACAS) es un sistema de notificación de ciclo cerrado que analiza fallas que ya han ocurrido. Examina las fallas pasadas para averiguar por qué sucedieron y qué impacto tuvieron para poder prevenirlas en el futuro. Es una medida reactiva.
La creación de AMFE para el mantenimiento es una parte clave de la construcción de un FRACAS. De hecho, es el primer paso del proceso. Un FMEA es una línea de base para fallas, así como para el desempeño del equipo y del equipo. Puede basar decisiones, como qué informes crear o qué fallas apuntar, en función de esta información.
Cómo se pueden utilizar los AMFE para el mantenimiento
Hay tres formas principales en que los equipos de mantenimiento pueden usar un modo de falla y análisis de efectos:
- Para crear un programa de mantenimiento preventivo que reduzca la probabilidad de fallas en los activos y optimice los recursos
- Para prepararse para el mantenimiento de emergencia, de modo que los activos se puedan reparar rápidamente y el tiempo de inactividad se pueda minimizar
- Para priorizar el mantenimiento correctivo y la acumulación de mantenimiento
Uso de AMFE para crear un programa de mantenimiento preventivo
Hay tres formas en las que puede utilizar los AMFE para ejecutar un programa de mantenimiento preventivo de clase mundial:
- Cree nuevas tareas de mantenimiento preventivo
- Priorizar el mantenimiento preventivo
- Optimice el mantenimiento preventivo
Descargue esta plantilla para crear un programa de mantenimiento preventivo
El primer paso para crear un programa de mantenimiento preventivo es comprender qué fallas pueden ocurrir y con qué frecuencia ocurren. Un FMEA describe esta información. Por ejemplo, si se está diseñando un nuevo activo, un FMEA le permite determinar qué PM son necesarios para prevenir posibles modos de falla y con qué frecuencia deben realizarse. Eso le permitirá mapear las entradas que se utilizan para crear nuevos PM, incluido quién se asignará al trabajo, qué activará el trabajo, cuánto costará y cuánto tiempo llevará.
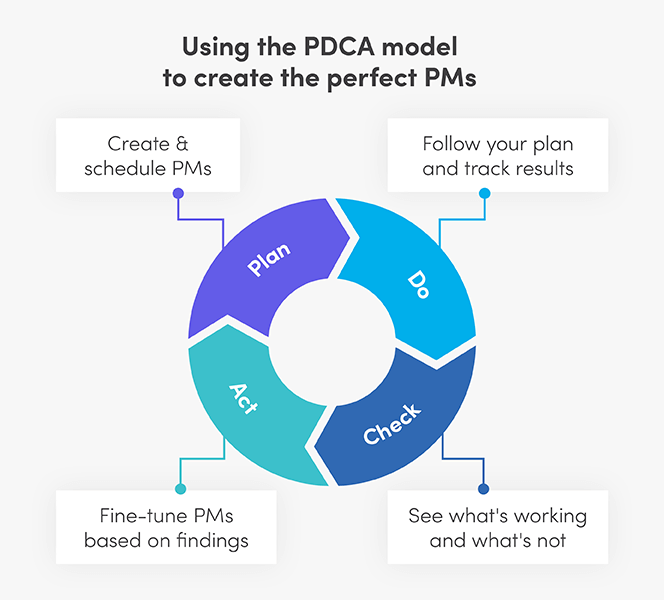
El éxito de su programa de mantenimiento preventivo depende tanto de la cantidad de fallas que encuentre y detenga como del impacto de esas fallas. Si evita 100 pequeñas averías, pero no detecta las cinco o seis averías que le cuestan a su empresa millones de dólares, su programa es defectuoso. Un FMEA tiene toda la información que necesita para priorizar los MP y apuntar a las averías más probables y disruptivas.
Si bien los AMFE le brindan una base para crear un programa de mantenimiento preventivo, sus planes no durarán para siempre. Su operación está cambiando todo el tiempo. Su horario de PM debe cambiar con él. El uso de los historiales de órdenes de trabajo y reparaciones para actualizar los AMFE le ayuda a optimizar su cronograma y mantenerse al día con otros cambios. Por ejemplo, es posible que un modo de falla no ocurra con tanta frecuencia como lo pronosticó. Estos datos pueden llevarlo a reducir la frecuencia del PM destinado a prevenir este modo de falla. Luego, puede destinar esos recursos a otra tarea de mantenimiento.
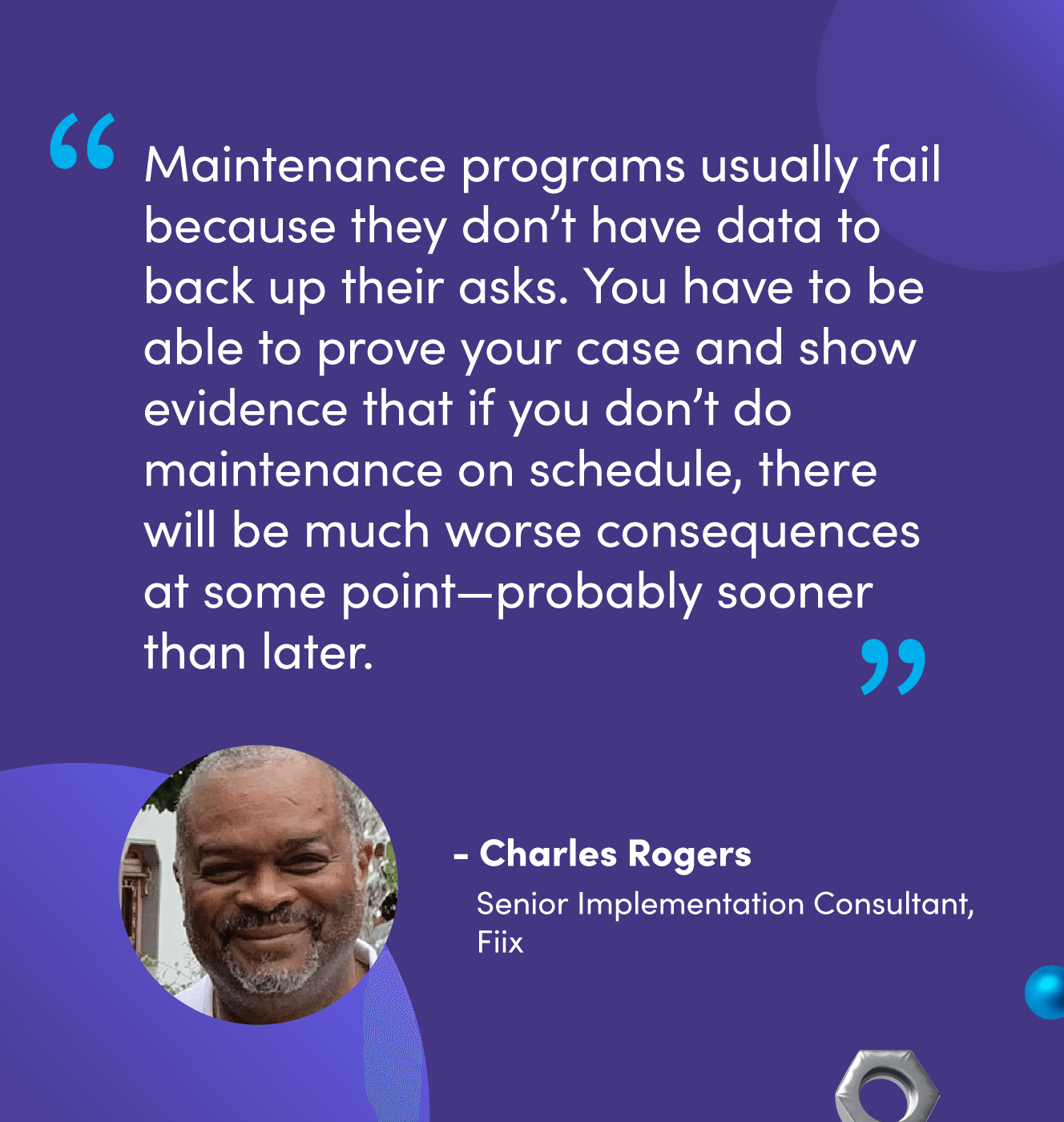
Uso de AMFE para prepararse para el mantenimiento de emergencia
Ninguna cantidad de mantenimiento eliminará totalmente la falla. Lo mejor que puede hacer es planificar averías de alto impacto y alto riesgo para que su equipo pueda solucionarlas en una hora en lugar de dos. Un FMEA es una herramienta valiosa para implementar estas medidas de emergencia.
Empiece por observar las fallas que tienen el mayor impacto y ocurren con mayor frecuencia. De esta lista, elija los modos de falla que son difíciles de detectar. Terminará con modos de falla que son difíciles de detectar y causan el mayor desorden. Desarrolle un plan de respuesta de emergencia para estas averías.
Su plan de respuesta a emergencias debe incluir cualquier información que reduzca los tiempos de respuesta y reparación. También debe tener en cuenta la salud y la seguridad. Esto podría incluir lo siguiente:
- Kit de piezas para reducir el tiempo dedicado a recuperar repuestos críticos y equipo de protección personal (descargue una plantilla de kit de piezas)
- Creación de una lista de tareas detallada o sugerencias para la resolución de problemas
- Adjuntar diagramas, manuales, fotos y otras ayudas visuales a las órdenes de trabajo
- Describir una lista de técnicos o contratistas que pueden completar la reparación
- Establecer una forma de comunicarse con los técnicos rápidamente, como el software CMMS
Uso de AMFE para priorizar el mantenimiento correctivo y la acumulación de mantenimiento
La detección temprana de fallas es útil, pero no significa nada si no tiene un proceso para corregir esa falla de manera rápida y efectiva. Un FMEA le ayuda a construir este proceso.
El primer paso es identificar los modos de falla con una puntuación de gravedad alta (es decir, los activos que le costarán más a su empresa si caen). Se deben realizar acciones correctivas en este equipo lo antes posible. Esta lista le permitirá crear materiales de capacitación y planes de respuesta para que todos sepan cómo reaccionar ante una falla.
Puede emplear un enfoque similar al priorizar la acumulación de mantenimiento, excepto por un paso adicional. Después de clasificar el trabajo diferido por gravedad, observe el trabajo sobrante por frecuencia de fallas. Compare esto con lo tarde que está el trabajo. Si un modo de falla tiene una tasa de frecuencia que excede el número de inspecciones perdidas, este trabajo debe tener prioridad ya que la probabilidad de falla es mayor.
Esta plantilla gratuita lo ayudará a priorizar su trabajo pendiente de mantenimiento
Cómo crear un FMEA
La plantilla AMEF a continuación lo ayudará a detectar el riesgo en su operación y tomar medidas para prevenirlo.
Descargue su propia plantilla de AMFE aquí
Pero primero, aquí se explica cómo obtener datos para su FMEA
Los buenos AMFE dependen de buenos datos. Sin datos, desarrollará su programa de mantenimiento sobre la base de conjeturas y suposiciones. Pero, ¿cómo encuentra la información requerida para un FMEA? Las tres fuentes siguientes le brindan una base excelente:
- Directrices de OEM:este es su punto de partida. Estas pautas le brindan una línea de base para completar un AMEF si no tiene otros datos.
- Entrevistas con operadores y técnicos:aproveche la experiencia de quienes trabajan con equipos todos los días. Le brindarán información que no puede encontrar en ningún otro lugar, como si un componente necesita el doble de lubricación de lo sugerido o si la frecuencia de una falla ha aumentado debido a que las especificaciones de la máquina han cambiado.
- Datos de órdenes de trabajo:sus órdenes de trabajo revelan cómo se está desempeñando el equipo y son una gran fuente de información para ajustar y mejorar sus AMFE. Busque fallas comunes, qué acciones se tomaron para encontrar y corregir la causa raíz, qué retrasó una reparación y qué tan fácil fue detectar una falla.
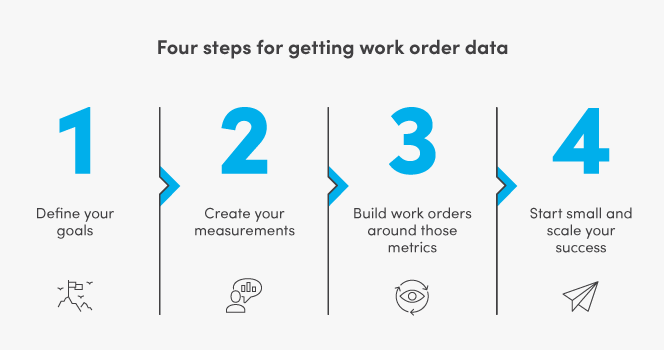
Ninguna de estas fuentes funciona sola. Combínelos para obtener una imagen completa de cómo funciona su equipo, cómo puede fallar, el impacto de la falla y qué se debe hacer al respecto.
Una plantilla de AMFE
1. Identificar componentes de activos
Documente cada componente del activo que pueda romperse o degradarse. Por ejemplo, los componentes de una línea de embotellado pueden incluir cajas de cambios, motores, ruedas dentadas, cojinetes y boquillas.
Comience con su equipo más crítico y continúe desde allí. Este es un buen momento para crear convenciones de nomenclatura claras y una jerarquía de activos si aún no las tiene.
2. Identificar posibles modos de falla
Es hora de identificar cómo pueden fallar esos componentes. Si un solo componente tiene múltiples modos de falla, enumere cada modo de falla en consecuencia. Por ejemplo, los modos de falla de un rodamiento pueden incluir desalineación, corrosión o contaminación.
3. Enumere los efectos potenciales de la falla
Describa el resultado de una falla y cómo afecta la producción y la seguridad del personal. Por ejemplo, un rodamiento desalineado cerrará una línea hasta que pueda ser reemplazada (aproximadamente tres horas), con una pérdida potencial de 1.800 unidades.
4. Puntuación de gravedad
Esta es una medida del impacto de una falla en la producción y la seguridad. Se puntúa en una escala del 1 al 10, siendo 1 un evento de bajo impacto y 10 un evento de alto impacto. Tenga en cuenta el estado del activo al puntuar. Por ejemplo, un automóvil en el que la llanta explota a baja velocidad experimentará problemas menores en la dirección, pero una explosión a alta velocidad es mucho más peligrosa.
Comience a calcular la puntuación de gravedad de un activo con esta plantilla de análisis de criticidad
5. Enumere las posibles causas
Enumere todas las posibles razones por las que puede haber ocurrido una falla. Vaya más allá de una causa directa. Por ejemplo, un cojinete corroído puede suceder porque los suministros estaban mal etiquetados o las instrucciones no eran claras, lo que da lugar a una lubricación inadecuada.
Llegue al fondo de la falla con este útil (¡y gratuito!) modelo de análisis de causa raíz
6. Puntuación de frecuencia esperada
Ésta es una medida de cuán común es un modo de falla. Se puntúa en una escala del 1 al 10, donde 1 representa un evento que ocurre raramente y 10 representa un evento que ocurre con mucha frecuencia.
7. Enumere los controles de proceso actuales
Documente todas las medidas implementadas para prevenir o detectar una falla. Los controles de proceso pueden incluir inspecciones semanales de mantenimiento preventivo, reemplazos mensuales de piezas y el uso de sensores para detectar niveles peligrosamente altos de vibración.
8. Puntuación de detección
Este número determina qué tan fácil es detectar un problema antes de que cause una falla total. Se puntúa en una escala del 1 al 10. Se otorga una puntuación de 1 a un evento que nunca se puede detectar. Se otorga una puntuación de 10 a un evento que se puede detectar casi siempre. Por ejemplo, un neumático pinchado a veces puede detectarse en sus primeras etapas, por lo que obtendría un puntaje de 5. Un parabrisas astillado a menudo es causado por eventos impredecibles, lo que significa que es difícil de detectar y obtendría un puntaje de 9.
9. Número de prioridad de riesgo
El número de prioridad de riesgo calcula los modos de falla que tienen el mayor impacto y son los más evitables. Para encontrar el RPN, multiplique las puntuaciones de gravedad, frecuencia y detección. Por ejemplo, si un modo de falla tiene una puntuación de gravedad de 8, una puntuación de frecuencia de 5 y una puntuación de detección de 10, el RPN sería 400. Cuanto mayor sea el número, más recursos se deben invertir para prevenir esa falla.
10. Determine la acción recomendada
Establezca un plan para reducir la probabilidad de fallas o aumentar las posibilidades de detección temprana. Esto puede incluir aumentar la frecuencia de MP en un componente o invertir en equipos de monitoreo de condición.
Cómo gestionar los AMFE
Los AMFE son documentos vivos que deben revisarse y actualizarse periódicamente. A continuación, se muestran algunos eventos que podrían desencadenar una revisión de un AMEF:
- Se diseña o instala un nuevo activo en sus instalaciones
- Un nuevo técnico u operador se une al equipo
- Se realiza un cambio en el modo de funcionamiento de una máquina (es decir, se ejecuta con más frecuencia o cambian las especificaciones)
- Un modo de falla ocurre con más frecuencia
- Se implementa nueva tecnología que lo ayuda a detectar o prevenir fallas más fácilmente
- Encuentra un nuevo modo de falla o el motivo de una falla existente
- El impacto de la falla cambia (es decir, se está produciendo un nuevo producto con material más costoso)
Tanto el personal de mantenimiento como el de operaciones deben participar en la modificación y adición de un modo de falla y análisis de efectos. La diversidad de perspectivas y experiencias con los equipos ayuda a evitar lagunas en sus AMFE.
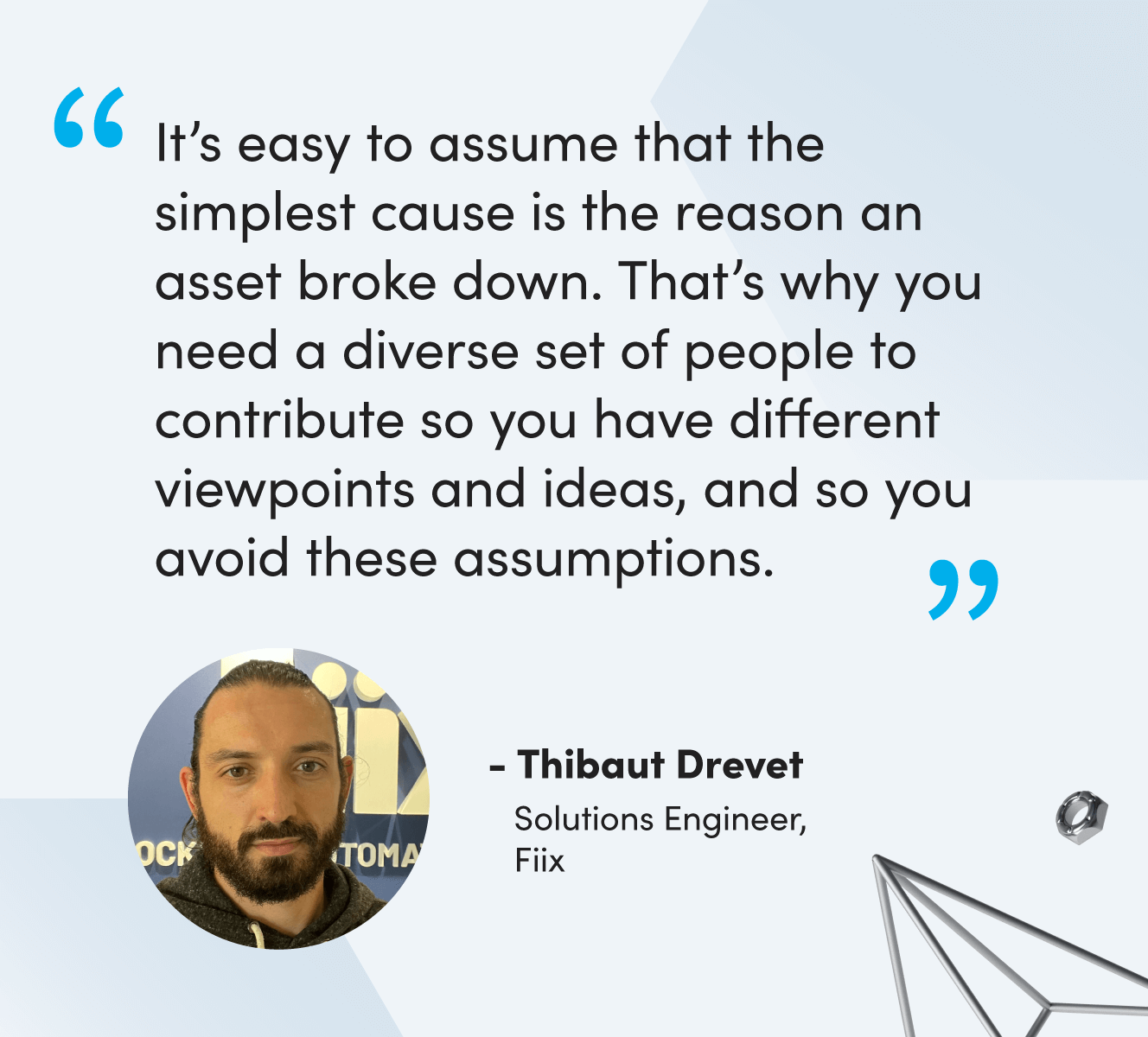
Los AMFE son una inversión a largo plazo para el éxito
Un modo de falla y análisis de efectos no es una solución de curita o una herramienta de resolución de problemas. Es una actividad continua con el objetivo de prevenir fallas donde sea posible y mitigar sus efectos cuando no lo es. Es un recurso de planificación y una protección contra pérdidas financieras y riesgos de seguridad.
Si bien la creación de AMFE implica una inversión de tiempo considerable, le devolverá la inversión a largo plazo al ayudarlo a planificar con anticipación, evitar el mantenimiento reactivo y realizar un seguimiento del éxito del equipo.
Mantenimiento y reparación de equipos
- Cómo mantener el mantenimiento en modo proactivo
- Guía rápida para el desarrollo y la ejecución de PM
- Los mejores en mantenimiento y confiabilidad
- Los detalles importan en el mantenimiento y la confiabilidad
- Simplifique el mantenimiento:utilice los sentidos y la sensibilidad
- 5 causas de fallas en el equipo (y lo que puede hacer para evitarlas)
- El tiempo es dinero:consejos para usar software de mantenimiento para ahorrar tiempo y gastar más eficientemente
- Simplificar el informe de fallas en el mantenimiento
- Una guía para el mantenimiento y las piezas de los remontes
- Su guía para la operación y el mantenimiento de grúas
- 4 consejos de mantenimiento para extender la vida útil del equipo y el retorno de la inversión