10 métricas increíblemente útiles para mejorar su análisis de mantenimiento
El análisis de mantenimiento ha cambiado mucho durante la última década. Las nuevas herramientas y tecnología han aumentado nuestra capacidad para recopilar e interpretar datos. Nos ha permitido tomar decisiones informadas que no hubieran sido posibles hace diez años.
Pero si nuestra comprensión del análisis de mantenimiento ha cambiado, ¿por qué seguimos confiando en el mismo puñado de métricas que usamos hace 40 o 50 años?
Las métricas como la efectividad general del equipo (OEE) y el tiempo medio de reparación (MTTR) dominan casi todas las listas de mediciones de la industria. Pero los expertos están de acuerdo en que tienen fallas. Estas métricas tradicionales no solo son propensas a sesgos e inexactitudes, sino que a menudo no tienen un propósito. Y cuando los datos no tienen un propósito, no puede usarlos para tomar decisiones clave, como contratar a un técnico adicional o aumentar la frecuencia de una tarea.
Es por eso que hemos reunido 10 métricas útiles que no verá en ninguna otra lista y algunos consejos sobre cómo usarlas para mejorar su programa de mantenimiento.
10 métricas de mantenimiento para un mejor análisis de mantenimiento
N.º 1:tiempo dedicado a respaldar la producción
¿Qué es ?:El tiempo total que el equipo de mantenimiento dedica a actividades centradas en la producción. Por lo general, se mide semanalmente, mensualmente o trimestralmente.
¿Cómo puedes usarlo ?:Todos tienen que colaborar para completar un pedido grande de vez en cuando. Pero cuando de vez en cuando se convierte en todos los días, el mantenimiento se ve afectado. Esta métrica lo ayuda a detectar una acumulación de trabajo insalubre antes de que suceda y a reasignar recursos para evitarla. También lo ayuda a abogar por un mayor número de empleados en su equipo o un mayor presupuesto de capacitación para ayudar al personal de producción a aprender las tareas de mantenimiento menores.
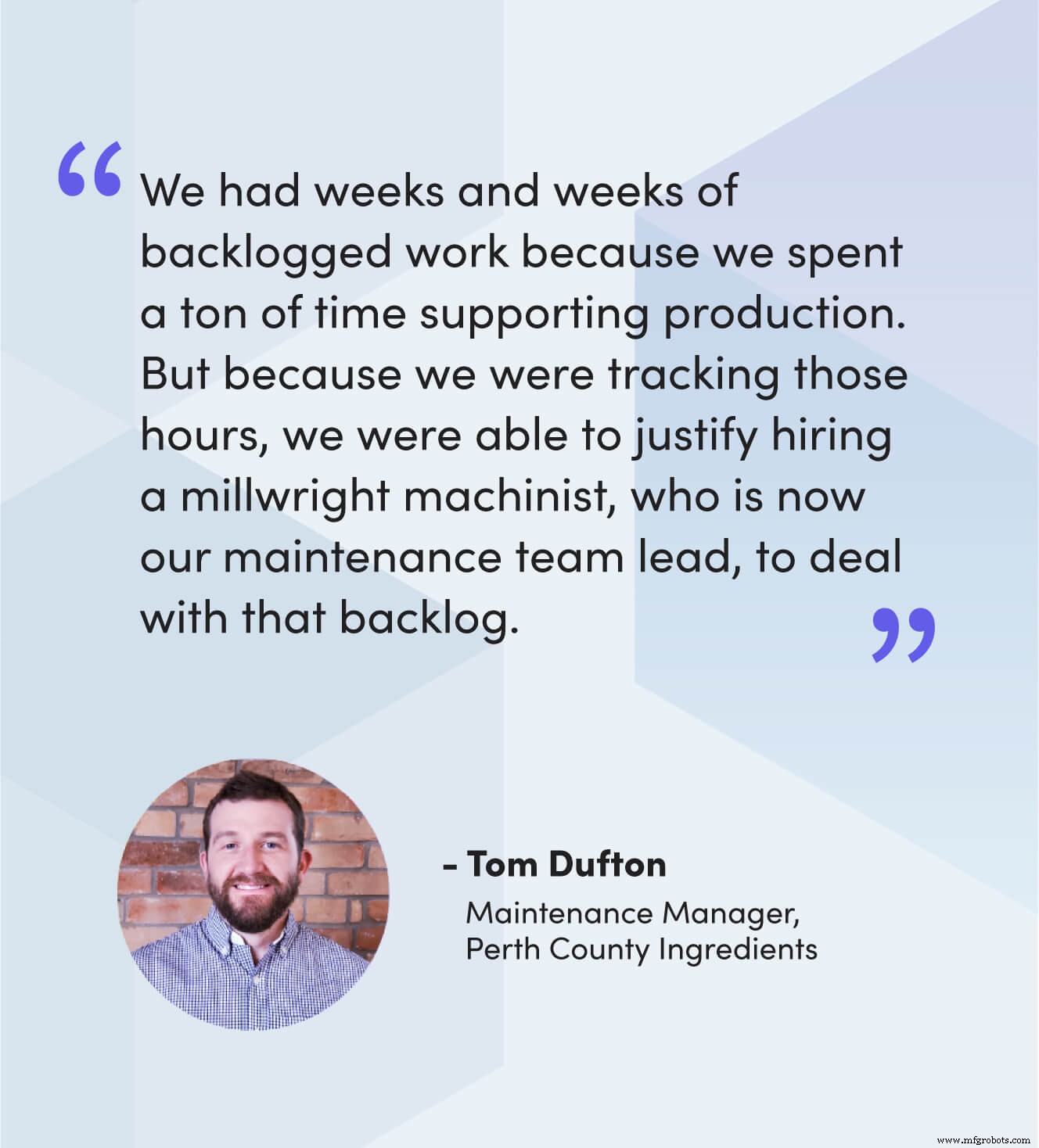
N.º 2:trabajo de seguimiento creado después de las inspecciones
¿Qué es ?:La cantidad de órdenes de trabajo correctivas creadas a partir de inspecciones de rutina. Por lo general, se mide mensualmente, trimestralmente o anualmente.
¿Cómo se puede utilizar ?:Hay muchas formas diferentes de utilizar esta métrica para el análisis de mantenimiento. Puede ordenarlo por máquina, turno o sitio para obtener información sobre el rendimiento de sus activos o equipo. Pero lo más útil es por tarea.
Es una buena señal cuando el mantenimiento preventivo regular incluye reparaciones de seguimiento. Significa que su horario es preciso y que está previniendo problemas mayores. Le permite marcar reparaciones comunes y crear procesos para hacerlas más eficientes. Por ejemplo, puede crear juegos de piezas para un acceso más rápido.
Si el porcentaje de inspección fallida es bajo, puede aumentar los intervalos de mantenimiento preventivo. Esto reducirá la cantidad de tiempo y dinero invertidos en tareas sin aumentar el riesgo.
N.º 3:costo del mantenimiento de seguimiento frente al costo esperado de la falla total
¿Qué es ?:Una comparación entre el costo del mantenimiento correctivo (es decir, mano de obra y piezas) y el costo de la falla de los activos si no se realiza el mantenimiento (es decir, pérdida de producción, mano de obra y piezas).
¿Cómo se puede utilizar ?:Utilice este tipo de análisis de mantenimiento para planificar su estrategia de mantenimiento. Por ejemplo, si las inspecciones regulares le cuestan más que las fallas, es probable que pueda optar por un enfoque de ejecución hasta la falla para un activo en lugar de uno preventivo.
También puede utilizar esta métrica para priorizar las tareas y la acumulación, y averiguar cómo asignar su presupuesto.
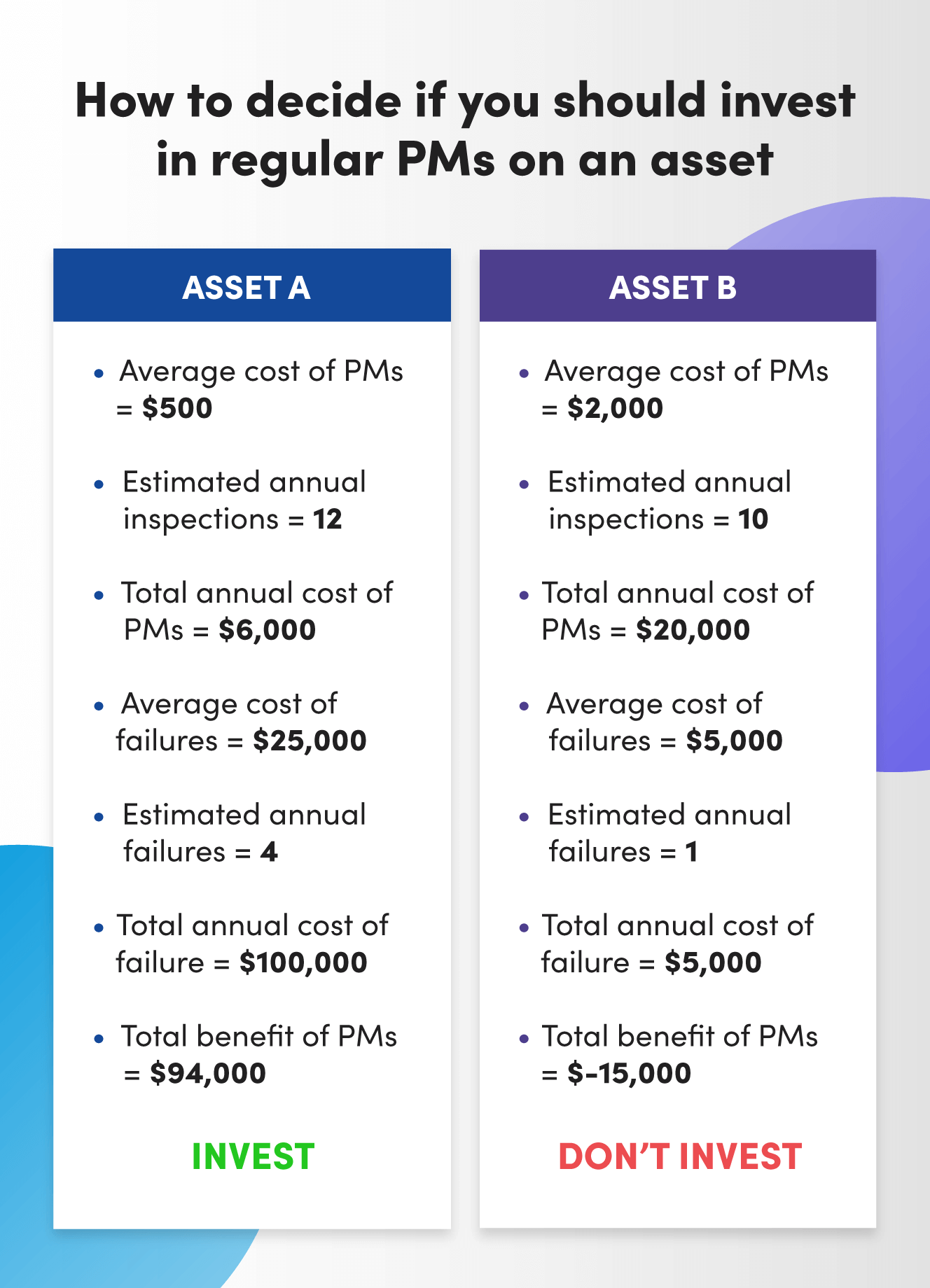
N.º 4:costo por tipo de mantenimiento
¿Qué es ?:El costo total de mantenimiento (es decir, mano de obra y piezas) por tipo de mantenimiento (es decir, preventivo, de emergencia, seguimiento). Por lo general, se mide mensualmente, trimestralmente y / o anualmente.
¿Cómo se puede usar ?:Los costos más altos suelen ser el resultado de procesos defectuosos. Esta vista le permite averiguar qué procesos necesitan trabajar para que pueda aumentar la eficiencia.
Por ejemplo, ¿las órdenes de trabajo no son claras y generan mayores tiempos de reparación y costos laborales? Intente aclarar las instrucciones.
¿Va a traer contratistas externos para que realicen reparaciones de emergencia? Podría invertir en más capacitación para su equipo o contratar a un especialista.
N.º 5 - Arranques limpios después del mantenimiento
¿Qué es ?:La cantidad de veces que una línea de producción comienza sin paradas o desperdicios después de completar el mantenimiento. Esto se mide mensualmente, trimestralmente y anualmente.
¿Cómo puede usarlo ?:Incluya esta métrica en su análisis de mantenimiento para trazar una línea directa entre el trabajo de su equipo y un mayor rendimiento.
Si las puestas en marcha limpias son bajas, le da otra oportunidad de detectar problemas en sus procesos. Por ejemplo, es posible que las especificaciones de una línea de producción estén desactualizadas. Esto hará que los técnicos reconstruyan los componentes incorrectamente y que la línea se detenga. Actualizar las especificaciones es un simple ajuste que podría conducir a un mayor rendimiento.
N.º 6:tamaño de la acumulación
¿Qué es ?:El número total de horas de tareas de mantenimiento vencidas y programadas. Realice un seguimiento de esta métrica semanal y mensualmente.
¿Cómo puedes usarlo?:Esta métrica puede ser una bendición cuando se trata de brindarle a tu equipo el alivio que tanto necesita. Cuantifique la brecha entre las horas laborales disponibles y el total de horas pendientes. Es posible que descubra que la cantidad de trabajo pendiente supera con creces lo que puede hacer su equipo. Úselo para justificar un mayor presupuesto para gastar en horas extra adicionales, contratar a otro técnico o traer más contratistas.
N.º 7:Los 10 activos principales por tiempo de inactividad
¿Qué es ?:Ésta es su lista de grandes bateadores:el equipo que se descompone con más frecuencia o que tarda más en repararse. Controle estos activos semanalmente, mensualmente y trimestralmente.
¿Cómo puedes usarlo ?:Esta métrica mantiene visibles tus mayores problemas. Es posible que levante una ceja ante eso, pero los problemas muy visibles se resuelven más rápido. Este tipo de análisis de mantenimiento puede ayudarlo a priorizar sus esfuerzos de resolución de problemas, tomar decisiones rápidamente y medir su impacto.
Por ejemplo, si sabe que el activo A está en la parte superior de su lista de tiempo de inactividad, puede comenzar por aislar el motivo. ¿Es porque las reparaciones demoran más en ese activo? ¿Se retrasa el trabajo? ¿Ese equipo se estropea una y otra vez?
La respuesta a estas preguntas le dará una idea de cómo prevenir fallas en el futuro. Puede deshacerse de las piezas obsoletas que se siguen rompiendo. O ponga a un técnico adicional a trabajar. O aclare cuánta lubricación debe usarse en un rodamiento. Si todo lo demás falla, realizar este tipo de análisis de mantenimiento ayuda a justificar un gasto de capital en equipos nuevos.
N.º 8:porcentaje de mantenimiento planificado (últimos 90 días)
¿Qué es ?:La relación entre el mantenimiento planificado y todos los demás tipos de mantenimiento durante los últimos 90 días.
¿Cómo se puede utilizar ?:Esta es una medida de progreso. Pasar del mantenimiento reactivo al planificado no ocurre de la noche a la mañana. El marco de tiempo le permite establecer una conexión clara entre la acción y los resultados. Puede trazar una línea entre lo que sucedió y su impacto en sus objetivos finales.
Por ejemplo, si su porcentaje ha bajado, puede ver qué sucedió en los últimos 90 días para provocar esa caída. Eso podría ser un colapso masivo e inesperado. O un aumento en el apoyo a la producción durante la temporada alta. Si desea aumentar el porcentaje, intente crear un mejor proceso de solicitud de trabajo para descubrir problemas antes. O acorte los intervalos de inspección en los activos con las instancias más altas de tiempo de inactividad inesperado.
Obtenga más información sobre el porcentaje de mantenimiento planificado y cómo mejorarlo
N.º 9:Hora de la llave inglesa (últimos 90 días)
¿Qué es ?:La cantidad de tiempo que los técnicos dedican a trabajar en un equipo como parte del tiempo total que lleva completar un trabajo. Por lo general, esto se mide por trabajo o como promedio semanal, mensual y trimestral.
¿Cómo se puede usar ?:El tiempo de la llave es una herramienta común para el análisis de mantenimiento, pero a menudo se usa de manera incorrecta. Los técnicos suelen (e injustamente) son los culpables del poco tiempo de uso. Conduce a una inflación de tiempo desgarrador a medida que los técnicos modifican los números para evitar problemas.
El bajo tiempo de uso de la llave usualmente tiene sus raíces en procesos defectuosos, no en la habilidad del técnico. Eso conduce a mayores atrasos, un mantenimiento más reactivo y costos laborales evitables.
Para utilizar el tiempo de la llave en su análisis de mantenimiento, comience con los trabajos que tengan las puntuaciones más bajas. Revise estos trabajos paso a paso con los técnicos. Trabajen juntos para descubrir dónde los procesos poco claros o incompletos causan retrasos. Detectará los cuellos de botella más fácilmente si divide la tarea en partes más pequeñas. El resultado es más valor por el tiempo y el dinero de su equipo.
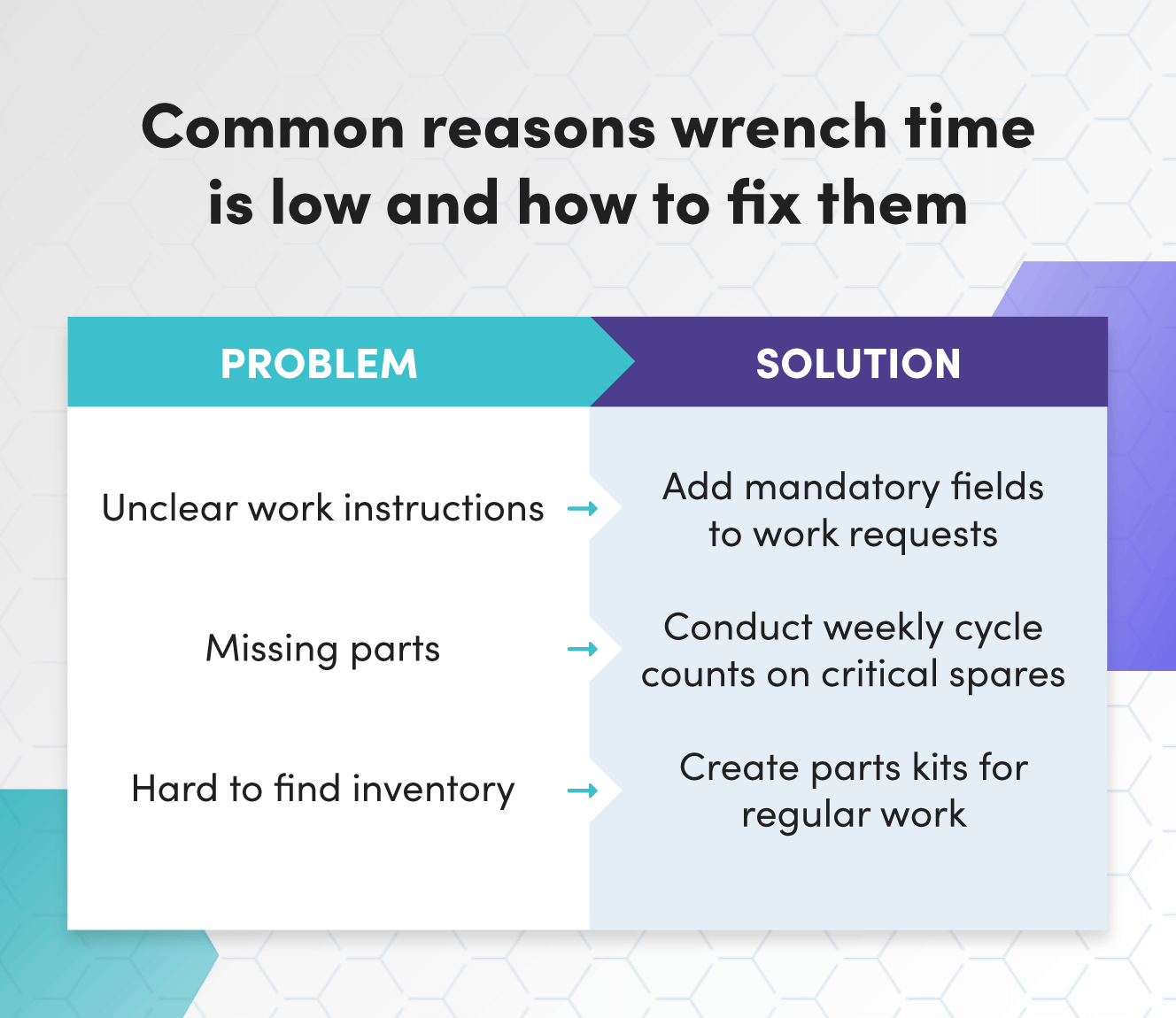
N.º 10 - Órdenes de trabajo de salud y seguridad completadas
¿Qué es ?:La cantidad de órdenes de trabajo completadas por motivos de salud y seguridad o cumplimiento. Por lo general, se realiza un seguimiento mensual, trimestral y anual.
¿Cómo se puede utilizar ?:Algunas métricas son cuantitativas. Otros son cualitativos. Éste es el último. Y es esencial para medir el desempeño de su equipo de mantenimiento y el impacto que tiene en su negocio. Un lugar de trabajo seguro mantiene bajos los accidentes y eleva la productividad y la moral. Pasar las auditorías y seguir cumpliendo es fundamental para la seguridad del personal y evitar multas.
Tres grandes objetivos que puede lograr al combinar estas métricas
Todas las métricas mencionadas anteriormente son poderosas por derecho propio. Pero cuando se combinan, potencian su análisis de mantenimiento y lo ayudan a lograr tres objetivos comunes:
Obtenga un presupuesto mayor y más tiempo para el mantenimiento
Métricas para combinar:
- Costo por tipo de mantenimiento
- Limpiar las puestas en marcha después del mantenimiento
- Los 10 activos principales por tiempo de inactividad
Obtener más dinero y tiempo para el mantenimiento significa ganarse a quien reparte el presupuesto ya quien dirige la producción. La forma más rápida de incorporarlos es alinear su plan con sus objetivos. Las tres métricas anteriores lo ayudarán a lograrlo.
Primero, resalte el costo-beneficio del mantenimiento preventivo. El mantenimiento preventivo regular puede parecer caro. Pero una sola instancia de mantenimiento de emergencia puede costar hasta 250.000 dólares. Si realiza un seguimiento de los costos por tipo de mantenimiento, puede resaltar cuánto está perdiendo la empresa con el mantenimiento reactivo y cuánto puede ahorrarle invirtiendo en mantenimiento preventivo.
A continuación, es hora de influir en el equipo de producción. Utilice puestas en marcha limpias después del mantenimiento para demostrar a la producción que tiene en mente sus mejores intereses. Enfatiza lo que es bueno para el mantenimiento y a menudo es bueno para la producción.
Nadie te va a dar más recursos sin un plan. Su lista de malos actores es un modelo de cómo va a aprovechar al máximo su tiempo y dinero extra. Cuantifica el problema y deja muy claro dónde enfocará sus esfuerzos.
Obtenga una plantilla para presentar su próximo gran (y costoso) proyecto de mantenimiento
Haga que su equipo de mantenimiento compre el cambio
Métricas para combinar:
- Porcentaje de mantenimiento planificado (90 días)
- Hora de la llave inglesa (últimos 90 días)
- Trabajo de seguimiento creado después de las inspecciones
El cambio apesta. Y eso dificulta que su equipo se incorpore a un nuevo sistema o proceso. La mejor manera de cambiar la opinión de los detractores es mostrarles cómo su plan está eliminando sus mayores dolores. El seguimiento de las métricas anteriores es una forma de hacerlo.
Estos puntos de datos le brindan la oportunidad de comparar cómo operaba antes de un cambio (es decir, mucho mantenimiento reactivo y frustración por las conjeturas) y lo que ha logrado desde que implementó un nuevo sistema o proceso. Ver la recompensa de primera mano hace que sea más fácil convertir a los críticos y expandir su proyecto, ya sea configurando un CMMS o permitiendo que los operadores de la máquina realicen el mantenimiento de rutina.
Cree un programa de mantenimiento preventivo que pondría celosos a la mayoría de las otras empresas
Métricas para combinar:
- Costo por tipo de mantenimiento
- Trabajo de seguimiento creado después de las inspecciones
- Costo del mantenimiento de seguimiento frente al costo esperado de la falla total
Los mejores programas de mantenimiento preventivo no tienen la mayor cantidad de PM. En cambio, tienen los PM más eficientes. Eso significa hacer el trabajo correcto en el momento correcto. Estas métricas lo ayudarán a lograr este equilibrio.
Medir el costo por tipo de mantenimiento lo ayuda a asignar recursos a tareas preventivas y medir la eficiencia de sus MP. Puede hacer un seguimiento de si las estrategias de reducción de costos están funcionando y asegurarse de que no generen costos reactivos en el futuro.
Controlar el trabajo de seguimiento es una forma de optimizar las frecuencias de MP. Si una inspección no conduce a un trabajo correctivo, puede aumentar los intervalos de inspección. Eso significa que puede utilizar menos horas de mano de obra y piezas, y gastar ese dinero y tiempo en otra parte. De manera similar, comparar los costos del mantenimiento correctivo y la falla total asegura que no gastará dinero en tareas proactivas que no valen la pena.
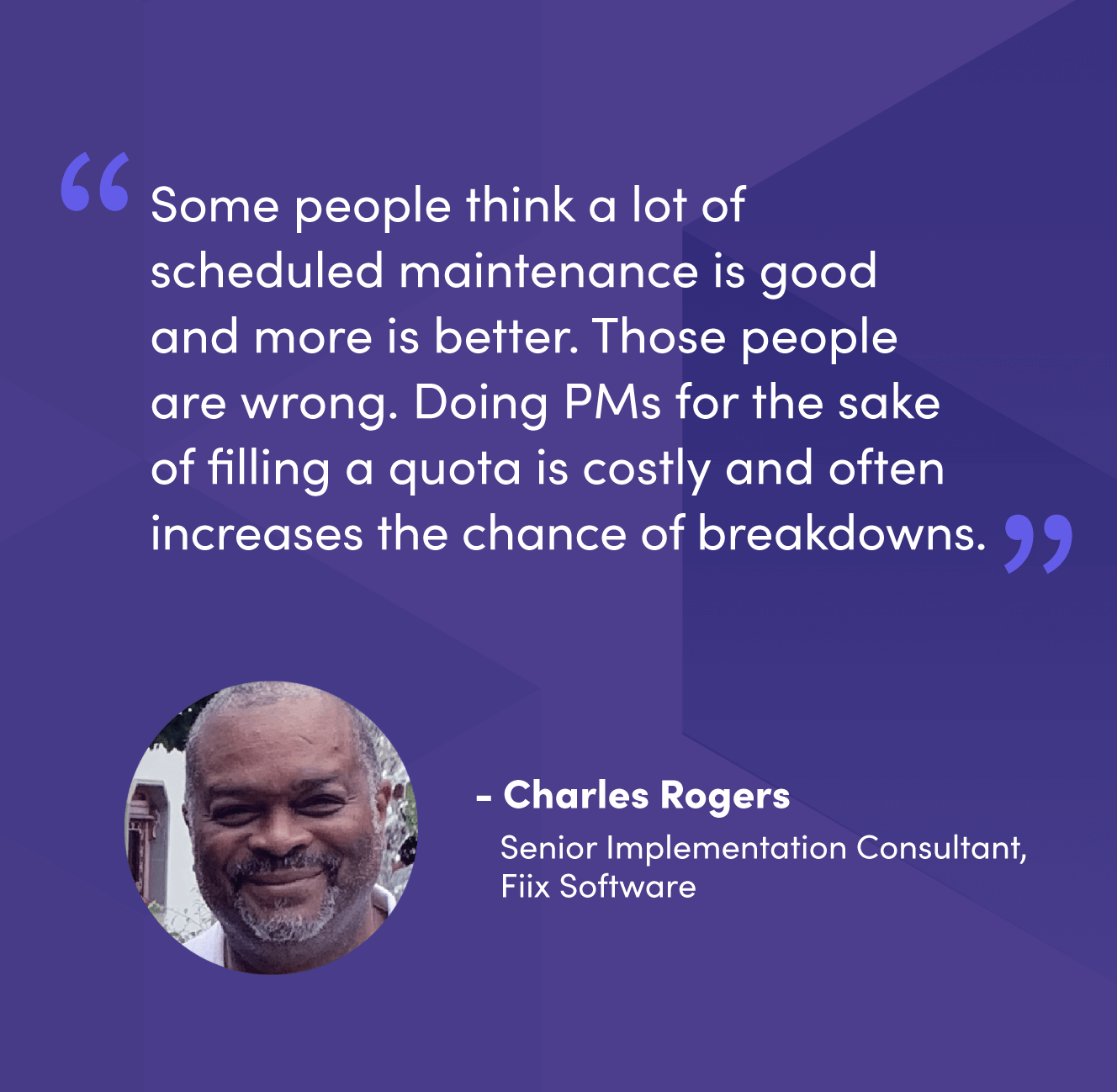
El mejor análisis de mantenimiento está en constante evolución
Las mejores métricas de mantenimiento tienen un propósito. Se recopilan y utilizan de forma coherente. Guían las decisiones y le informan sobre cómo ejecutar su programa de mantenimiento a diario. Esta es la columna vertebral de un análisis de mantenimiento exitoso.
Por otro lado, todo el análisis de mantenimiento es un trabajo en progreso. Revise sus métricas con regularidad para asegurarse de que sigan siendo relevantes para sus objetivos y la forma en que trabaja su equipo de mantenimiento. Algunas de las métricas enumeradas anteriormente pueden funcionar para usted ahora, pero es posible que otras sean más efectivas en seis meses. O quizás cinco años.
Por último, el mejor análisis de mantenimiento incorpora datos que otros departamentos encuentran útiles. Si puede conectar las métricas anteriores para resolver los desafíos de otras unidades comerciales, estará bien encaminado para crear un programa de mantenimiento de clase mundial.
Mantenimiento y reparación de equipos
- MTTF vs. MTBF:explicación de las métricas de fallas
- Ahorro de costes de mantenimiento predictivo
- Cómo mejorar la gestión del inventario de mantenimiento
- ¿Debería el mantenimiento reactivo ser parte de su estrategia de mantenimiento?
- Cómo optimizar su programa de MP
- Residuos invisibles en organizaciones de mantenimiento
- Costo y valor de reemplazo estimado
- Maximice su programa de análisis de lubricación
- 3 consejos para mejorar su plan de mantenimiento de equipos
- Determinación de los beneficios de CMMS con un análisis simple de costo-beneficio
- Reducción del desgaste del tren de rodaje