5 causas de fallas en el equipo (y lo que puede hacer para evitarlas)
Esta publicación fue escrita originalmente como un blog invitado por Nicole Pontius de Camcode. Editado y actualizado por el equipo de Fiix en junio de 2019.
- 5 causas comunes de fallas en el equipo
- Causa n. ° 1:funcionamiento incorrecto
- Causa n. ° 2:No realizar el mantenimiento preventivo
- Causa n. ° 3:demasiado mantenimiento preventivo
- Causa n. ° 4:no monitorear continuamente el equipo
- Causa n. ° 5:cultura de confiabilidad mala (¡o no!)
- El resultado final
Ocurre una falla en el equipo. El impacto puede abarcar una amplia gama, desde arreglos fáciles con pérdidas mínimas hasta catastróficos, según factores como los costos de reparación, el tiempo de inactividad total, las implicaciones para la salud y la seguridad y el impacto en la producción y la prestación de servicios.
Hay varias razones comunes por las que el equipo puede averiarse, y comprender por qué su equipo puede estar fallando es su primera línea de defensa contra las graves consecuencias de un tiempo de inactividad no planificado.
Utilice estos siete secretos para reducir el tiempo de inactividad y ganar contra las fallas
Supere la falla del equipo
5 causas comunes de falla del equipo
Causa n. ° 1:funcionamiento incorrecto
Hay un montón de personas que pueden estar dentro y alrededor del equipo a diario y que podrían tener un impacto significativo en su condición operativa general.
Los operadores de equipos son uno de esos grupos. Por lo general, reciben capacitación en profundidad sobre los procedimientos operativos adecuados, la resolución de problemas básicos y las mejores prácticas para el uso seguro de equipos relevantes para las máquinas con las que trabajarán. Sin embargo, podría llegar el día en que un operador termine trabajando en una máquina para la que no ha sido capacitado adecuadamente. A veces, esta situación surge como resultado de la escasez de personal o ausencias inesperadas. Otras veces surgen emergencias que requieren una reparación rápida con personal disponible que no necesariamente tiene el nivel de experiencia que tienen sus operadores más experimentados.
Una solución a estos problemas es asegurarse de tener suficientes operadores capacitados para permitir cierta flexibilidad y un plan de contingencia para emergencias por escasez de personal. Si es posible, todos sus operadores deben tener alguna capacitación sobre cada equipo, incluso sobre los activos con los que no suelen trabajar.
Lo más importante es que nunca permita que un operador utilice equipos para los que no esté calificado. Esto no solo ayudará a reducir los errores operativos, sino que, en algunas industrias, es imperativo para el cumplimiento normativo. La Administración de Salud y Seguridad Ocupacional (OSHA) establece regulaciones para los requisitos de capacitación del operador para ciertos tipos de equipos y para la seguridad ocupacional general. Sin embargo, depende de usted conocer las regulaciones aplicables a su industria y asegurarse de tener implementados los procedimientos de cumplimiento adecuados.
Causa # 2:No realizar el mantenimiento preventivo
La mayoría de los equipos requieren un mantenimiento regular para un rendimiento óptimo, pero con demasiada frecuencia, el mantenimiento preventivo es la primera tarea que debe realizar cuando tiene poco personal y está abrumado. Es fácil ignorar el mantenimiento regular cuando todo parece ir bien y muchas empresas trabajan bajo el supuesto de que los trabajadores experimentados identificarán los problemas inminentes antes de que el equipo falle por completo.
Dicho esto, muchos de los signos sutiles de una disminución del rendimiento o las primeras etapas de falla no son fácilmente detectables y, a menudo, pasan desapercibidos. En otros casos, las empresas simplemente carecen de métodos de planificación eficientes para garantizar que se realice el mantenimiento continuo. El seguimiento de equipos y maquinaria con etiquetas de activos puede ayudar a mantener los programas de mantenimiento en marcha y los equipos funcionando con la máxima eficiencia operativa.
El mantenimiento preventivo es una función continua que nunca debe dejarse en el camino. El cuidado de su equipo con ajustes regulares prolongará la vida útil de su equipo y, en última instancia, le dará más por cada dólar. Además, el mantenimiento preventivo puede identificar pequeños problemas con soluciones económicas antes de que se conviertan en averías importantes y costosas. Cuando utiliza estrategias efectivas de control de inventario para asegurarse de tener las piezas de repuesto adecuadas en el suministro para las tareas de mantenimiento más comunes y las fallas de funcionamiento, el tiempo de inactividad para el mantenimiento de rutina y las reparaciones es mínimo. De hecho, el Departamento de Energía de EE. UU. Estima que el mantenimiento preventivo da como resultado:
- Hasta un 30% de reducción en los costos de energía y mantenimiento
- 35% a 45% menos de averías
- Reducciones en el tiempo de inactividad hasta en un 75%
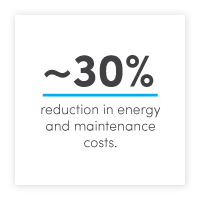
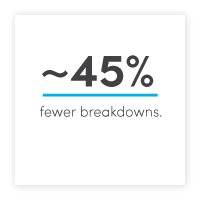
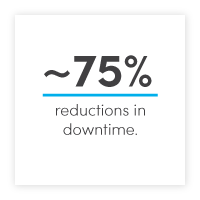
Deje de combatir incendios todo el día con esta plantilla de programa de mantenimiento preventivo gratuita
Causa n. ° 3:demasiado mantenimiento preventivo
"Seguramente esto es un error", estás pensando. "Me acaba de decir que NO hacer mantenimiento preventivo hará que las cosas se rompan". Es cierto, hay una pequeña situación de Ricitos de Oro en lo que respecta al mantenimiento preventivo. No lo suficiente puede ser problemático por las razones que describimos anteriormente, pero demasiado también es un motivo importante de preocupación.
Ya hemos escrito sobre esto en profundidad antes, así que consulte este blog si desea profundizar en el concepto de averías posteriores al mantenimiento. Pero aquí están las notas de Coles:cada vez que ingresa a una máquina para mantenerla, abre esa pieza de equipo a un conjunto completo de riesgos y, con el tiempo, esos riesgos pueden agravarse y provocar fallas.
No hay suficientes MP
Se pasan por alto los signos de falla temprana
Los programas de mantenimiento sufren
Reducción de la eficiencia del equipo
La vida útil de los activos se reduce
Aumentan las averías y el tiempo de inactividad
Los costos se disparan
Solo suficientes MP
Los costos están controlados
Se logra la entrega justo a tiempo
Se reduce el tiempo de inactividad
Se aumenta la eficiencia del técnico
La seguridad mejora
Se optimiza la productividad de los activos críticos
Demasiados MP
Aumento del gasto excesivo
El desgaste de los activos se dispara
Se pierde el tiempo del técnico
Se utiliza inventario innecesario
Se recopila información inexacta
Asegúrese de no realizar demasiados PM con esta plantilla de registro de mantenimiento
Piénselo en términos de cirugía:un bypass triple es una operación que salva vidas. Pero no desea someterse a una cirugía a corazón abierto de forma regular simplemente porque han pasado algunos años o porque su corazón ha latido varios millones de veces. Pero muy a menudo, así es exactamente como abordamos el mantenimiento preventivo. Se realiza en un cronograma predefinido (generalmente basado en el tiempo o el uso) sin tener en cuenta la condición operativa real del activo.
Lo que nos lleva a ...
Causa n. ° 4:falla al monitorear continuamente el equipo
Entonces, ¿cómo se encuentra el equilibrio adecuado de mantenimiento preventivo? La cura aquí es simple en concepto pero un poco más compleja en ejecución:mantenimiento basado en condiciones. Se trata de un mantenimiento que se realiza en función de las condiciones de funcionamiento de una pieza de equipo, en lugar de simplemente un programa de "configúrelo y olvídese". Tiene en cuenta muchas cosas, desde el historial del equipo de información del fabricante hasta datos en tiempo real como el análisis de vibraciones.
El monitoreo continuo se basa en los datos de los sensores para establecer una línea de base de cómo se ve el buen estado del equipo a fin de detectar cambios sutiles, que se pueden usar para predecir averías y fallas. Esto permite más tiempo para la planificación de contingencias y la programación del tiempo de inactividad para minimizar las interrupciones de producción. Este tipo de monitoreo y los datos que se recopilan en el proceso pueden ayudar a las empresas a identificar las causas del mayor estrés en la maquinaria y ajustar las cargas de trabajo y los horarios para disminuir la carga en los equipos que muestran indicadores tempranos de fallas inminentes.
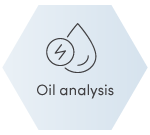
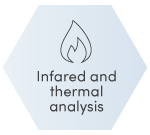
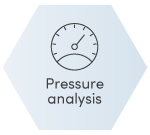
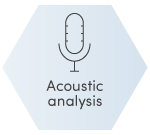
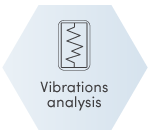
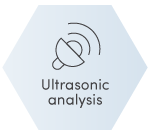
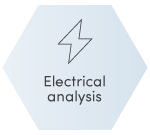
Prepárese para cada falla en sus activos críticos con esta plantilla FMEA
El problema aquí es que esto es realmente difícil de hacer si administra el mantenimiento con lápiz y papel o Excel. Si aquí es donde desea que vayan sus operaciones de mantenimiento, podría ser el momento de considerar la posibilidad de cambiar a una solución de mantenimiento digital.
Cuándo usar el monitoreo basado en condiciones
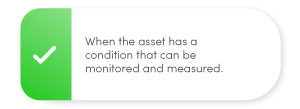
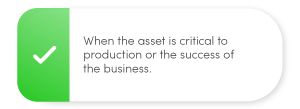
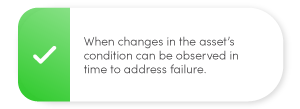
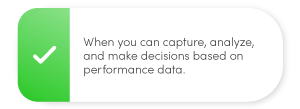
Causa n. ° 5:cultura de confiabilidad mala (¡o no!)
Todo el mundo ha estado ahí; una gran presión desde arriba significa que no hay un segundo que perder si tiene alguna esperanza de alcanzar sus objetivos de producción. En estas circunstancias, puede ser tan tentador (y tan fácil) para un operador o un trabajador de mantenimiento notar que algo no funciona al 100%, colocarle una tirita y decir:"Lo resolveré cuando las cosas se calmen abajo". El problema es que, de manera realista, las cosas nunca se calman hasta el punto en que tendrás tiempo para volver a visitar ese trabajo. Lo que significa que la solución de curita se convierte en una solución semipermanente hasta que deja de funcionar y se convierte en una falla total.
Un buen ejemplo de esto es Boeing. Probablemente esté familiarizado con los dos accidentes mortales que involucraron al avión 737 Max de la compañía, lo que generó dudas sobre si la prisa de Boeing por llevar el avión a producción llevó a la compañía a asumir riesgos de seguridad que finalmente resultaron en los accidentes.
Pero la historia más tranquila se refiere a un modelo de avión diferente:el 787 Dreamliner. Varios denunciantes se han presentado para dar la alarma sobre los Dreamliners, que se fabricaron en 2009 en una planta entonces nueva cerca de Charleston, Carolina del Sur. Desde el principio, la producción descuidada fue un problema que fue constantemente barrido bajo la alfombra a favor de programas de producción agresivos.
Si desea conocer la historia completa, consulte el artículo completo del New York Times aquí (o el podcast relacionado del Daily si le gusta más el audio). Pero en pocas palabras, los problemas en Boeing son un muy buen ejemplo de presión competitiva en los niveles más altos de una empresa que tiene un efecto dominó en toda la cadena de mando, hasta la fábrica. La mala cultura en la parte superior crea una mentalidad de "hágalo rápidamente" que puede resultar en descuidos devastadores, soluciones de curitas y errores.
Entonces, ¿qué pasa si la mala cultura está en la raíz de la falla de su equipo? ¿Qué puedes hacer? Cubrimos el tema de cómo comenzar a establecer una cultura que se centre en la confiabilidad, así que continúe y revise una (¡o todas!) De estas piezas para tener una base firme en la confiabilidad.
En resumen:operadores capacitados, un programa de mantenimiento preventivo sólido y un enfoque en la cultura de la confiabilidad son sus boletos para un futuro sin fallas (o al menos menos fallas)
El equipo puede ser impredecible y ocurren fallas. La gente comete errores, las piezas se vuelven viejas y, a veces, el mantenimiento preventivo es solo una cosa de más en un día ya ajetreado. Pero si garantiza una formación adecuada de los operadores, realiza un mantenimiento preventivo o basado en la condición en el momento adecuado y trabaja para lograr una mejor cultura general, tendrá una mejor oportunidad de mantener su equipo funcionando en óptimas condiciones.
Mantenimiento y reparación de equipos
- Mantenimiento autónomo:qué es y por qué es importante
- ¿Qué es la confiabilidad y la gestión de activos?
- ¿Qué constituye un mantenimiento y una fiabilidad de primer nivel?
- La muerte del departamento de mantenimiento y lo que podemos hacer al respecto
- ¿Pueden coexistir el mantenimiento y las operaciones?
- ¿Qué puede hacer para mejorar el mantenimiento y la confiabilidad?
- Principales causas de fallas en las máquinas y cómo prevenirlas
- ¿Qué es una caída de presión y cómo se previene?
- 4 consejos de mantenimiento para extender la vida útil del equipo y el retorno de la inversión
- ¿Qué es ejecutar hasta fallar y RTF siempre es malo?
- Instalaciones y mantenimiento industrial