Proceso de alto horno de reciclaje de gas superior
Proceso de alto horno de reciclaje de gas superior
En el área de producción de metal caliente (HM) por alto horno (BF), la tecnología más prometedora para reducir significativamente las emisiones de CO2 (dióxido de carbono) es el reciclaje de CO (monóxido de carbono) y H2 (hidrógeno) de la gas saliendo de la parte superior BF. El contenido de CO y H2 del gas BF superior tiene el potencial de actuar como elementos de gas reductores y, por lo tanto, su recirculación al BF se considera una alternativa eficaz para mejorar el rendimiento del BF, mejorar la utilización de C (carbono) y H2, y reducir la emisión de CO2. Esta tecnología de 'reciclado de gas superior' (TGR) se basa principalmente en la reducción del uso de C fósil (coque y carbón) con la reutilización de los agentes reductores (CO y H2), después de la eliminación del CO2 del BF superior. gas. Esto conduce a reducir los requerimientos de energía. Debido a las ventajas de alta productividad, alta tasa de PCI (inyección de carbón pulverizado), baja tasa de combustible y baja emisión de CO2, etc.. , el proceso TGR-BF se considera uno de los procesos de fabricación de hierro prometedores en el futuro.
En TGR-BF, se inyecta oxígeno (O2) en el BF en lugar de aire caliente para eliminar el nitrógeno (N2) en el gas BF superior. Parte del gas BF superior que contiene CO y H2 se utiliza nuevamente como agente reductor en el BF. El CO2 del gas superior BF se captura y luego se almacena. Se han sugerido, evaluado o aplicado en la práctica varios procesos de reciclaje para diferentes objetivos. Estos procesos se distinguen por (i) con o sin eliminación de CO2, (ii) con o sin precalentamiento y (iii) la posición de inyección.
El concepto del TGR-BF (Fig. 1) implica muchas tecnologías que incluyen (i) la inyección de CO y H2 de los componentes de gas BF superiores reductores en las toberas del eje y del hogar, (ii) la reducción del consumo de entrada de C fósil debido a la reducción del coque (iii) uso de gas O2 puro en lugar de aire caliente en la tobera del hogar (eliminación de N2 del proceso), y (iv) recuperación de CO2 puro del gas BF superior para almacenamiento subterráneo.
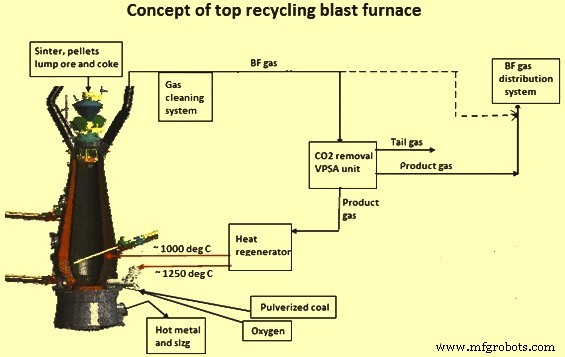
Fig. 1 Concepto de TG- BF
El concepto de reciclaje de gas superior se probó experimentalmente en el BF experimental (EBF) de LKAB en Lulea, Suecia. Se modificó el EBF y se construyó una planta de separación de gases basada en la tecnología VPSA (adsorción por cambio de presión al vacío) cerca del EBF.
Historia del reciclaje de gas superior de BF
Para reducir la tasa del reductor y aumentar la productividad del BF, se han introducido varios conceptos nuevos basados en el proceso BF convencional durante el siglo XX.
Ya en la década de 1920, se desarrolló un concepto para la inyección del gas reductor caliente en el BF. Era necesario compensar el menor volumen de gas de las toberas del horno mediante la inyección de gas reductor precalentado a 1000 °C con un 27 % de CO, un 33 % de H2 y un 26 % de N2 en la zona del eje inferior. Como resultado, se encontró que solo el 30 % del coque (en ese momento 345 kg/tHM) era necesario para el proceso BF. A mediados de la década de 1960, esta idea se retomó en Bélgica y, a principios de la década de 1970, se llevaron a cabo las primeras pruebas en un hogar BF de 4,6 m de diámetro en Cockerill-Seraing, Bélgica. Se inyectó una cantidad específica de 400 N cum/tHM de gas reformado que se precalentó hasta 1000 grados C en el eje inferior del BF. Se observó una relación de sustitución de 0,22 kg a 0,26 kg de coque por N cum de gas reductor.
No se llevaron a cabo más investigaciones por razones económicas debido al alto costo del gas natural. A fines de la década de 1970, se inició en Alemania el trabajo de desarrollo de un nuevo proceso en el que la inyección de O2 puro frío, combustible y gas reciclado se realizaba en dos niveles de tobera. Basado en esta idea, se desarrolló un proceso en Canadá en 1984 para un BF convencional sin una segunda fila de toberas. La característica principal de este concepto era la inyección de carbón para sustituir el coque. Ambos conceptos nunca se realizaron y terminaron solo como un estudio.
Casi al mismo tiempo, NKK utilizó esta idea en Japón, donde se instaló una segunda fila de toberas en el medio del eje. En estas toberas se inyectó gas reductor precalentado, consistente en gas superior reciclado sin eliminación de CO2. El gas se calentó por combustión parcial con oxígeno. En las toberas del hogar se inyectaron O2 frío, carbón y gas superior reciclado en frío. NKK probó el proceso en un BF experimental con 3 toberas, un volumen interno de 3,9 cum y un diámetro de solera de 0,95 m. La tasa de inyección de carbón podría incrementarse a 320 kg/tHM, mientras que la tasa de coque podría reducirse a 350 kg/tHM. La escasez de gas combustible en la planta siderúrgica integrada debido al reciclaje del gas BF superior detuvo el desarrollo de este proceso, ya que el precio de la energía eléctrica y el gas natural era alto en Japón.
La primera operación comercial de un BF con reciclaje de gas superior se realizó a finales de la década de 1980 en 12 campañas por parte de RPA Toulachermet en Rusia en el BF número 2 con un volumen útil de 1033 cum. En este concepto de proceso BF totalmente de coque, se insufló gas superior caliente y casi libre de CO2 en las toberas del hogar, junto con O2 puro. El gas superior descarbonatado se calentó en estufas calientes hasta 1200 ºC. Con este nuevo proceso se produjeron casi 250 000 toneladas de metal caliente (HM). La tasa de coque más baja alcanzada fue de 367 kg/tHM, frente a la referencia de 606 kg/tHM lo que supuso una reducción de la tasa de coque de 239 kg (39 %). Durante estas campañas, se observaron serios desgastes de la tobera, lo que llevó a cambios en el diseño de la tobera. Las dificultades con el sistema de limpieza con CO2 finalmente detuvieron el proceso. Teniendo en cuenta estas investigaciones previas, en 2004 se desarrolló el concepto de ULCOS (fabricación de acero con dióxido de carbono ultrabajo) TGR-BF.
Desarrollo de ULCOS TGR-BF
El trabajo de desarrollo se ha llevado a cabo en dos fases. En la primera fase de desarrollo, que se desarrolló entre 2004 y 2009, el proceso se denominó "proceso de alto horno nuevo de ULCOS". Durante esta fase se han desarrollado y probado tres nuevos conceptos de proceso. En la segunda fase, que comenzó en 2009 y que se denominó "proceso de alto horno de reciclaje de gas superior de ULCOS", se llevaron a cabo dos campañas adicionales de ULCOS TGR-BF.
Durante el desarrollo se utilizaron modelos de balance de masa y calor y un modelo simétrico del eje 3-D del BF para el cálculo de los datos principales y el estado interno del proceso para la selección de los mejores parámetros operativos. Se definieron y examinaron cuatro alternativas para el posible ahorro de C alcanzable y la factibilidad de operar el BF bajo estos nuevos conceptos. La conclusión fue que las alternativas 1, 3 y 4 deberían poder lograr un ahorro de C fósil del 21 % o más con un alto nivel de inyección de carbón pulverizado. La alternativa 2 fue rechazada debido al bajo ahorro de C esperado y la necesidad de una tecnología desafiante para calentar el gas reciclado en dos pasos, primero en un recuperador y luego calentándolo por oxidación parcial. Todas las alternativas incluían la eliminación de CO2 y la inyección de gas producto rico en CO en las toberas del hogar, el uso de O2 puro y la inyección de carbón junto con el gas reductor. En todas las alternativas, el uso de biomasa, mineral parcialmente reducido y gas rico en hidrógeno se había considerado como una posibilidad en el futuro.
En la alternativa 1 (Fig. 2), el gas producto descarbonatado se inyecta frío con O2 puro y carbón en las toberas del hogar y caliente en las toberas del eje. Un punto crítico en esta alternativa fue la pequeña tasa de flujo de gas frío al nivel de la tobera del hogar, lo que llevó a tamaños de canal de rodadura más pequeños y temperaturas de llama más altas en comparación con el proceso BF normal. Además, fue necesario un nuevo diseño de tobera debido a las pequeñas tasas de flujo de gas.
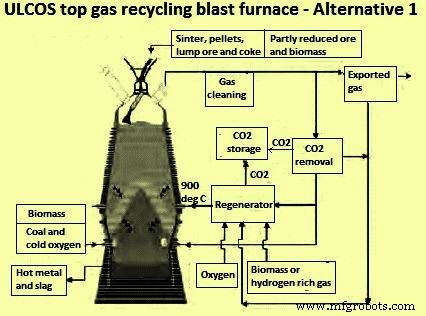
Fig. 2 Alto horno de reciclaje de gas superior ULCOS - Alternativa 1
En la alternativa 3 (Fig. 3), el gas producto descarbonatado se inyectó caliente en las toberas normales del hogar junto con O2 y carbón. Para alcanzar un alto ahorro de carbono era necesario operar con baja RAFT (temperatura de llama adiabática de la pista de rodadura) y al mismo tiempo con una alta tasa de inyección de carbón.
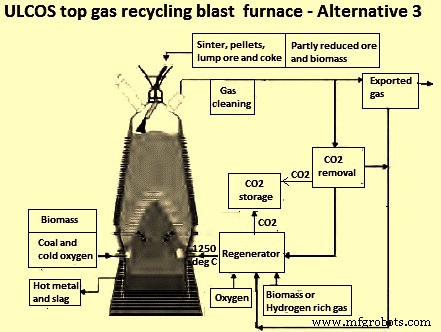
Fig. 3 Alto horno de reciclaje de gas superior ULCOS - Alternativa 3
En la alternativa 4 (Fig. 4), el gas producto descarbonatado se inyectó caliente en las toberas del hogar y caliente en el eje inferior. La temperatura del gas reciclado varió desde la temperatura ambiente hasta los 1250 °C.
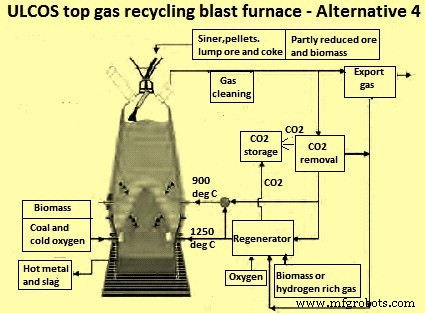
Fig. 4 Alto horno de reciclaje de gas superior ULCOS - Alternativa 4
En las alternativas 1 y 4, el gas producto también se inyecta a través de las toberas del eje. Las diferencias son la temperatura de inyección de gas y la posición de los puntos de inyección. En todos los casos, al menos una parte del gas se calentó en un sistema regenerativo. El ahorro esperado de carbono fósil para la alternativa 1 fue del 21 % a una tasa de carbón de 170 kg/tHM, la alternativa 3 fue del 24 % a una tasa de carbón de 180 kg/tHM y la alternativa 4 fue del 25 % a una tasa de carbón de 150 kg/tHM .
Luego se realizó el modelado matemático de las condiciones de la pista de rodadura y las pruebas de gasificación y se realizaron investigaciones a escala piloto y de laboratorio para el diseño y la ingeniería de las toberas bajo las restricciones de inyección simultánea de gas reciclado, O2 puro y carbón pulverizado. La geometría de la tobera se ha mejorado en base a los resultados de los cálculos para evitar puntos calientes y fallas durante la operación y para mantener un impulso suficiente de la corriente de gas para formar una canalización con una profundidad suficiente.
Campañas de proceso TGR-BF en el BF experimental
El objetivo de los ensayos fue demostrar el funcionamiento del EBF en modo TGR completo con O2 puro y PCI en las toberas del hogar. Esto se llevó a cabo bajo las tres alternativas definidas. La carga ferrosa estuvo compuesta por un 30 % de pellets y un 70 % de sinterizado. La tasa de producción de HM se mantuvo a un nivel constante de 1,5 toneladas por hora y la tasa de PCI se varió entre 130 kg/tHM a 170 kg/tHM. Durante los diferentes períodos de prueba, se maximizó el volumen del gas superior reciclado para obtener el máximo ahorro de C fósil. Los resultados obtenidos durante las pruebas en LME luego se compararon con los cálculos del modelo.
La alternativa 3 y la alternativa 4 se probaron en 2007, durante la primera campaña tras una puesta en marcha convencional. La alternativa 3 se probó para la optimización durante el otoño de 2009 en la segunda campaña, seguida de una prueba de la alternativa 1. En la tercera y última campaña durante 2010, el enfoque estuvo en la alternativa 4 a 900 °C. La alternativa 4 se consideró como una alternativa preferida para el seguimiento del proyecto de demostración ULCOS BF a escala industrial. El límite de 900 ºC para la temperatura del gas reinyectado se fijó para evitar problemas de reducción de sílice por H2 de los materiales refractarios.
Durante cada campaña, se tomaron medidas in situ de la temperatura y la composición del gas, así como muestras del material de carga del EBF con las dos sondas de carga. Para investigar el comportamiento del material de carga bajo las nuevas condiciones de operación, se cargaron cestas con diferentes materiales sinterizados y granulados en el EBF justo antes de la parada de la campaña. Estas cestas se recuperaron del EBF durante la disección del horno después del enfriamiento rápido con nitrógeno. Esto se había hecho durante las campañas de 2007 y 2010. En la segunda campaña de 2009, solo se pudo realizar el apagado debido a un final de campaña no preparado debido a un problema en el sistema de carga de EBF y, por lo tanto, no se cargaron canastas.
Durante las campañas, se recuperaron muestras de la zona cohesiva y se midió el tamaño y la forma de la pista para una mayor investigación. Las campañas se iniciaron con una semana de operación normal BF convencional (chorro de aire caliente) con sinter, primero para calentamiento y estabilización térmica y luego para establecer una referencia para la operación BF convencional. Luego de la referencia, se realizó una parada para desconectar el soplador y conectar el gas producto a los calentadores de cantos rodados (regeneradores). La puesta en marcha en la modalidad TGR-BF se realizó mediante soplo artificial consistente en O2 frío de las lanzas y N2 caliente de los calentadores de guijarros. En pasos progresivos, el N2 de los calentadores de guijarros fue reemplazado por gas superior descarbonatado (gas producto).
Resultados de las campañas de ULCOS TGR-BF
La primera conclusión que surgió de las campañas es que es posible operar el proceso ULCOS TGR-BF. No se produjo ningún problema relacionado con la seguridad durante las campañas con el nuevo proceso. La operación de la unidad VPSA, que es la segunda instalación en importancia, fue fluida y sin mayores fallas. El EBF junto con la unidad VPSA funcionó muy bien durante las campañas.
Sin embargo, debe señalarse que la operación de la unidad VPSA estuvo influenciada por los cambios en la composición del gas superior y el volumen del gas del EBF. Por lo tanto, ambas unidades debían funcionar en una relación muy estrecha. La proporción máxima de gas de punta reciclado que se logró durante las campañas estuvo en torno al 90 %.
Durante las campañas del proceso TGR-BF se experimentó un funcionamiento estable del BF con un suave descenso de la carga y fue fácil mantener la estabilidad térmica. La eficiencia del gas en el pozo BF se mantuvo estable durante las diferentes alternativas y hubo una buena distribución de gas como lo muestran las mediciones de las sondas del pozo en carga. Sin embargo, hubo algunas fallas en los equipos durante las campañas por lo que el EBF tuvo que detenerse durante la operación en las nuevas condiciones del proceso. Algunas paradas prolongadas requerían volver al paso de operación de la "operación convencional" con chorro caliente artificial de O2 frío y operación de N2 caliente. Las pequeñas paradas solo requerían detener la inyección de gas y agregar algo de coque y/o carbón extra.
Después de la puesta en marcha con N2, cuando no hay gas BF superior disponible, el gas producto podría reciclarse de nuevo en aproximadamente 1 hora. Todos los problemas se solucionaron según lo previsto y la estabilidad térmica del BF nunca estuvo seriamente en peligro. A lo largo de la campaña, la experiencia adquirida y el aumento de la confianza permitieron progresivamente que la recuperación de EBF fuera más rápida (a nivel de producción). Cada vez que durante el cambio de alternativas (3 a 4, 3 a 1), el BF se detuvo durante unas 8 horas para realizar las conexiones de gas necesarias a las toberas del eje y el cambio de las toberas del hogar.
Los experimentos realizados a nivel de laboratorio habían demostrado que el material de carga convencional no sería un problema para el nuevo proceso. Esto se confirmó durante las campañas. No se relacionaron problemas de proceso particulares con las propiedades de los materiales de carga. Los resultados de los sondeos y las muestras de excavación mostraron el perfil de reducción de un horno de trabajo central que es un nivel de reducción bajo en la pared y un nivel de reducción más alto en el centro del horno para muestras de sinterización y gránulos. Las pruebas de volteo en las muestras de excavación mostraron un comportamiento de desintegración similar al de un proceso BF convencional que correspondía a las pruebas de laboratorio. A partir del trabajo de prueba de carga, se pudo concluir que las propiedades de carga que se utilizan en el BF convencional actual parecen no tener ningún problema para el proceso ULCOS TGR-BF.
Los resultados alcanzados durante las campañas ULCOS TGR-BF fueron muy alentadores en cuanto al ahorro del C (carbón y coque). Las pruebas de las tres campañas habían mostrado una disminución sustancial en la tasa del reductor que se logró mediante la inyección del gas BF superior descarbonatado. Durante las tres campañas el aporte de carbón y coque se redujo de unos 530 kg/tHM a 400 kg/tHM, lo que representa un ahorro considerable de la C. El aporte de carbón se redujo de 470 kg/tHM a unos 350 kg/tHM, lo que se tradujo en un ahorro de C de alrededor del 25 %.
Aunque la alternativa 1 no pudo explorarse por completo debido a la parada temprana de la segunda campaña, la reducción máxima en la entrada de C a través del coque fue del 21 % en comparación con el período de referencia bajo la operación BF convencional. Para esta alternativa se desarrolló una nueva tecnología de toberas. El diseño de la tobera constaba de tubos coaxiales con el tubo interior utilizado para la inyección del carbón pulverizado y el tubo exterior para la inyección de O2. Las tres toberas instaladas funcionaron muy bien y tras desmontar no se observaron daños ni desgaste. El VPSA pudo reciclar hasta el 88 % del gas superior BF.
En cuanto a la alternativa 3, el consumo de C podría reducirse hasta un 15 % en la primera campaña con un índice máximo de reciclaje de gas en torno al 72 %. Los resultados de esta alternativa fueron más bajos (alrededor del 15 %) de lo esperado a partir de los cálculos del balance de masa y calor (24 %), ya que esta era la primera experiencia con el modo de reciclaje de gas superior y el proceso no estaba optimizado. En la segunda campaña los resultados de esta alternativa fueron mucho mejores, al conseguirse la máxima reducción de aporte de C en torno al 25 % con un ratio de reciclado de gas superior al 90 %.
En el caso de la alternativa 4, se logró un ahorro de C del 24 % con una tasa máxima de reciclaje de gas del 90 %. En cuanto al consumo de coque y carbón, se produjo un ahorro de hasta 123 kg/tHM en el nuevo proceso (alternativa 4) respecto al periodo de operación de referencia. A partir de estos resultados se pudo determinar una buena correlación entre la cantidad de gas inyectado (CO+H2) y la reducción de la tasa de reductor. La entrada de C a través del coque y el carbón podría reducirse en 17 kg en promedio por cada 100 N cum de gas (CO+H2) inyectado.
Las campañas de EBF han demostrado que es posible ejecutar un proceso de BF a un nivel de consumo de C fósil mucho más bajo en comparación con el nivel de consumo de BF actual. Se demostró un ahorro de C de hasta un 25 % mediante la inyección del gas superior descarbonatado reductor. Esta es una caída significativa en comparación con el proceso BF mejor operado en la actualidad. De hecho, se espera que la aplicación de la tecnología BF-TGR en BF moderno conduzca a reducir el consumo de C de un nivel actual de alrededor de 405 kg C/tHM a un nivel de alrededor de 295 kg C/tHM.
La unidad VPSA ha operado de manera estable. Se había notado que la unidad VPSA podía tratar el 97 % del gas superior del BF. La fracción volumétrica media de CO2 en el gas inyectado se situó en torno al 2,67 % y la tasa de recuperación de CO fue del 88 %, cumpliendo los requisitos de cantidad y calidad. En combinación con las unidades VPSA y CCS, las emisiones de CO2 reducidas por el proceso TGR-BF podrían llegar a 1270 kg/tHM, lo que representa el 76 % de las emisiones totales de CO2 en el proceso de fabricación de hierro. El 24 % del CO2 reducido fue por reciclaje de gas y el otro 52 % fue transportado y almacenado bajo tierra por CCS.
Desde el punto de vista del proceso, se puede afirmar que la operación ULCOS es más estable que la operación BF convencional, en cuanto a temperatura y calidad del HM se refiere. Esto parece deberse esencialmente a la menor influencia de la reacción de pérdida de solución relacionada con los niveles mucho más bajos de la tasa de reducción directa (DRR). El valor más bajo observado de esta RRD es del 5 %. No hubo indicación en los resultados operativos de que este fuera realmente el valor mínimo que podría alcanzarse en ULCOS TGR-BF. La calidad de HM se vio afectada en gran medida por la operación de ULCOS TGR-BF. Especialmente, se observó una disminución sustancial del contenido de silicio (superior al 1 % absoluto) y un aumento correlativo del contenido de C. Sin embargo, debe señalarse que el contenido de silicio en el funcionamiento BF convencional es mucho menor (alrededor del 0,5 % en el BF convencional frente al 2,0 % en el EBF) y, por lo tanto, no debe esperarse un cambio tan grande durante la aplicación de ULCOS. Proceso BF-TGR a escala industrial.
Las campañas de prueba de ULCOS TGR-BF han demostrado que el nuevo proceso TGR-BF es factible y fácil de operar. Se puede operar con buena seguridad, alta eficiencia y gran estabilidad. Las campañas de prueba han demostrado que es posible cambiar la operación EBF entre 4 modos de operación (convencional, alternativas 1, 3 y 4). También demostró que es posible operar el proceso BF y la planta de separación de gases VPSA en un circuito cerrado. Los ahorros de C obtenidos fueron consistentes con las predicciones de los cálculos del diagrama de flujo. Las pruebas también indicaron que los materiales de carga convencionales sinterizados, gránulos y coque son adecuados para el proceso ULCOS TGR-BF.
Según la experiencia de las campañas de EBF, los elementos que requieren atención para la aplicación industrial segura y sostenible del proceso ULCOS TGR-BF son (i) el riesgo de fuga de gas a nivel de la tobera puede exigir que el nivel de la tobera esté físicamente separado de la casa de fundición para protección contra incendios, (ii) riesgo de fuga debido a la flexión de las bridas a altas temperaturas, (iii) alargamiento de la chimenea de estufas/calentadores calientes para evitar gases venenosos en el entorno, (iv) para evitar fallas en la fase de arranque , el personal operativo debe recibir capacitación con gas artificial durante la prueba de funcionamiento, (v) los parámetros de inyección óptimos son importantes para evitar la acumulación/obstrucción en la punta de la tobera, (vi) la importancia del control de flujo de explosión individual en las toberas para evitar la acumulación de exceso de O2 y carbón pulverizado en la tobera en caso de obstrucción, (vii) se debe modificar la selección del refractario y la fabricación de los elementos refractarios y se debe evitar, en la medida de lo posible, el uso de anclajes de acero C, alternativamente Se deben utilizar otros materiales que no sean acero C o acero revestido con alúmina, y (viii) es importante evitar la formación de polvo de metal mediante una selección cuidadosa de las piezas metálicas.
Los resultados de la prueba han demostrado que la alternativa 4 tuvo el mejor efecto de reducción de emisiones y fue seleccionada como la primera opción para la prueba en el BF a escala industrial durante la siguiente etapa.
Proceso de manufactura
- Sistema de control, medición y automatización de procesos de alto horno
- Generación y uso de gas de alto horno
- Uso de coque de nuez en un alto horno
- Inyección de carbón pulverizado en un alto horno
- Irregularidades del alto horno durante la operación
- Sistema de enfriamiento de alto horno
- Sistemas de carga superior de alto horno
- Química del Proceso de Fabricación de Hierro por Alto Horno
- Revestimiento refractario de alto horno
- Inyección de gas de horno de coque en un alto horno
- Comprender el proceso de soldadura por gas