Deposición de vapor químico de acetileno mejorada con plasma en catalizadores bimetálicos codepositados que aumenta la continuidad de la hoja de grafeno en condiciones de crecimiento a baja temperatura
Resumen
Aquí, presentamos un método novedoso para la síntesis a baja temperatura de grafeno monocapa a 450 ° C en un catalizador bimetálico policristalino de Ni-Au. En este estudio, la síntesis de deposición de vapor químico a baja temperatura de grafeno se realizó a 450 ° C en Ni-Au codepositado que muestra una formación exitosa de grafeno monocapa sin un proceso de recocido adicional. Los resultados experimentales sugieren que la codeposición por haz de electrones del catalizador bimetálico es el procedimiento clave que permite la eliminación del recocido a alta temperatura previo al crecimiento del catalizador antes de la síntesis de grafeno, un proceso indispensable, utilizado en informes anteriores. La formación se mejoró aún más mediante el crecimiento asistido por plasma en el que el plasma acoplado inductivamente ioniza los precursores de carbono que interactúan con el catalizador de Ni-Au codepositado de 50 nm de espesor a 450 ° C. Estas condiciones de crecimiento combinadas aumentan drásticamente la uniformidad de la hoja de grafeno y la conectividad del área del 11,6% al 99%. Estos parámetros de fabricación permiten la formación de grafeno que cambia de un modelo de crecimiento basado en difusión masiva hacia una reacción basada en la superficie. La técnica informada aquí abre la oportunidad para el crecimiento de grafeno a baja temperatura para su uso potencial en futuras aplicaciones CMOS.
Introducción
Han pasado más de 10 años desde el aislamiento del grafeno [1], una sola capa de átomos de carbono en una red hexagonal; sin embargo, este material 2D único aún no se ha incorporado industrialmente a un nivel en el que esté beneficiando a los bienes de consumo. El grafeno es un material especialmente prometedor para la industria de los semiconductores debido a sus notables propiedades electrónicas [2, 3]. Como barrera de difusión atómicamente delgada [4], el grafeno es un activo poderoso en la carrera por crear espaciamientos de transistores cada vez más pequeños y continuar el reinado de la Ley de Moore. Sin embargo, sus aplicaciones en la industria de los semiconductores se han visto seriamente obstaculizadas por las altas temperaturas que generalmente se requieren para sintetizar el grafeno, en el rango de 800 ° C ~ 1000 ° C [5], y el hecho de que el proceso de transferencia de grafeno se limita a geometrías planas. . El crecimiento directo del grafeno en circuitos integrados evitaría el proceso de transferencia del grafeno, otro proceso destructivo, de un catalizador de crecimiento al dispositivo. Actualmente, es posible crecer sobre catalizadores de Cu y Ni (metales comunes en circuitos integrados), pero estos requieren altas temperaturas de crecimiento [5], lo que podría dañar las estructuras ya existentes de un circuito integrado. Mucha investigación se ha centrado en reducir las temperaturas de síntesis de grafeno y ha habido un éxito reciente. Weatherup et al. [3] han demostrado que es posible cultivar grafeno a 450 ° C agregando una capa de Au de 5 nm evaporada térmicamente sobre un catalizador de Ni policristalino de 550 nm de espesor depositado por pulverización catódica, pero un recocido previo de 600 ° C de las capas de Au y Ni son necesarias para producir una aleación de Ni-Au. Un mecanismo propuesto es que la adición de Au al catalizador de Ni ayuda a limitar la absorción de carbono durante la exposición al precursor de carbono y reduce la nucleación del grafeno y los sitios de difusión externa como los bordes de los escalones y los límites de los granos [3]. Si bien se ha avanzado para reducir la temperatura de síntesis al rango de 400–600 ° C [3, 6, 7], también deben superarse los impactos dañinos de la transferencia de láminas de grafeno. Crecimiento directo sobre Si o SiO 2 es otro objetivo deseado para las láminas de grafeno, pero esto no se ha informado en la región de 400 ° C ~ 500 ° C necesaria para los procesos de semiconductores back-end-of-line (BEOL). Mientras que el crecimiento directo de grafeno sobre Si o SiO 2 aún no se ha logrado, la síntesis de grafeno en catalizadores más delgados representa un paso sustancial hacia este objetivo. En un catalizador más delgado, la capa de grafeno resultante está cada vez más cerca del sustrato objetivo. Esto crea la posibilidad de desarrollar un proceso de transferencia que sea menos dañino para el grafeno al minimizar la cantidad de manipulación manual del grafeno debido a su proximidad al sustrato objetivo. Si bien el grafeno se sintetiza comúnmente mediante técnicas de deposición química de vapor (CVD), la adición de un plasma remoto puede ayudar a reducir las temperaturas de síntesis. El crecimiento del plasma energiza los gases precursores a través de la ionización, superando la energía térmica que se pierde al crecer en el rango de 400 ° C ~ 500 ° C en comparación con el rango de 800 ° C ~ 1000 ° C. Las ventajas de un plasma acoplado inductivamente remoto son dobles:el plasma se crea lejos del catalizador de crecimiento, lo que reduce el daño del bombardeo iónico en la superficie de síntesis, y el plasma se produce a través de bobinas de inducción que están fuera de la cámara de crecimiento de grafeno donde se encuentra el catalizador. se encuentra el sustrato. En un sistema de plasma capacitivo típico, la etapa de síntesis se encuentra entre dos placas de metal dentro de la cámara de vacío con un potencial eléctrico entre ellas que expone la superficie de crecimiento a cualquier material extraño de la fuente de plasma. Usando una bobina de inducción exterior envuelta alrededor del tubo de flujo de gas, ionizamos los gases precursores creando un campo electromagnético alterno dentro del tubo. Esto elimina completamente la fuente de plasma de la cámara, lo que no permite que material extraño de la fuente de plasma contamine potencialmente el catalizador de crecimiento. Aquí informamos sobre la síntesis de grafeno monocapa (MLG) a 450 ° C mediante la deposición de vapor químico de plasma acoplado inductivamente (ICPCVD) en un catalizador de Ni-Au delgado (50 nm) codepositado mediante la técnica de evaporación por haz de electrones.
Métodos experimentales
Preparación del catalizador
Se utilizaron dos métodos de preparación del catalizador para este estudio para comparar los efectos del Ni-Au frente al Ni puro, y todas las deposiciones de catalizador se realizaron en una herramienta separada de Deposición física de vapor (PVD) de Kurt J. Lesker. Para los experimentos de crecimiento de grafeno de Ni puro, el catalizador de Ni se preparó mediante pulverización catódica con magnetrón sobre SiO 2 / Obleas de Si hasta el espesor deseado (50 nm). Para la preparación del catalizador de Ni-Au, los gránulos de Au y Ni se mezclaron primero mediante calentamiento por haz de electrones, donde el sistema de haz de electrones dirige un haz de electrones a un crisol que contiene gránulos de metal tanto de Au como de Ni. Aquí se prefirió la deposición por haz de electrones debido al hecho de que permite un control preciso del porcentaje en peso de Au en la mezcla. El haz de electrones calienta y mezcla los gránulos, y la mezcla resultante luego se codeposita mediante evaporación en SiO 2 / Obleas de Si como se ilustra esquemáticamente en la Fig. 1. Este proceso de aleación remota produce un catalizador que expone Ni al precursor de hidrocarburo mientras se implanta Au en la masa de Ni y en la superficie del catalizador. La preparación de catalizador que se utilizó en la bibliografía publicada [3] deposita metales mediante un método de estratificación en el que se depositan varios metales uno encima del otro. A continuación, las capas deben recocerse a 600 ° C para formar una aleación o mezcla. La técnica de codeposición aplicada en este estudio tenía como objetivo eliminar el proceso de recocido del catalizador y lograr la formación de grafeno a baja temperatura mediante el uso de un catalizador de aleación de Ni-Au que se prefabricaba antes de la deposición. La naturaleza del estado premezclado del catalizador codificado evita la necesidad de un recocido previo de mezcla para formar un catalizador válido. Por motivos de simplicidad en este informe, llamamos a este proceso de deposición de catalizador "codeposición" porque el Ni y el Au se codepositan sobre el sustrato. Para nuestros experimentos, optamos por depositar una aleación de Au al 1% en peso que ha demostrado ser más eficaz en la síntesis de grafeno a baja temperatura [3]. Tanto el catalizador de Ni puro como el de Ni-Au se depositaron hasta un espesor de 50 nm debido a nuestro interés en el crecimiento del catalizador más delgado. Encontramos que este espesor se encuentra dentro de los rangos informados anteriormente para el crecimiento a base de níquel [8, 9], aunque a temperaturas mucho más altas que 450 ° C, sin embargo, nuestro catalizador de Au-Ni de 50 nm es un orden de magnitud más delgado que el reportado Crecimiento de grafeno multicapa (MLG) a 450 ° C [3].
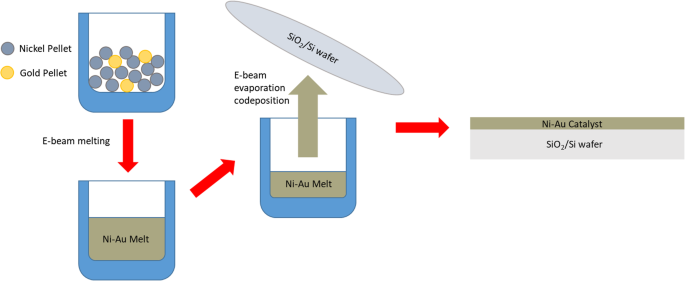
Diagrama esquemático de la técnica de codificación por haz de electrones en la que vemos que los gránulos de Ni y Au se mezclan remotamente en un crisol antes de evaporarse sobre el sustrato. Este proceso sirve para eliminar por completo la necesidad de recocido previo al crecimiento utilizado en la literatura anterior y permite una síntesis completa de grafeno monocapa a 450 ° C
Crecimiento de grafeno
Nuestros regímenes de crecimiento de grafeno se realizaron en una cámara ICPCVD de pared fría construida a medida. Las temperaturas se midieron mediante un medidor de termopar fijado a la superficie de la muestra para detectar temperaturas de superficie precisas in situ. Los gases se introdujeron en la cámara a través de un cabezal de ducha. Las muestras se colocaron en una plataforma calentada radiantemente aproximadamente 25 cm por debajo del cabezal de ducha de gas. Los catalizadores preparados se introdujeron en la cámara ICPCVD y se bombearon a una presión base de 1 × 10 −6 Torr después de lo cual H 2 se introdujo a 15 sccm mientras la muestra se calentaba a la temperatura de proceso de 450 ° C. Una vez que las muestras alcanzaron la temperatura de proceso, el H 2 se detuvo el flujo y la cámara se purgó con Ar. Una vez que se restableció la presión base, se detuvo Ar y C 2 H 2 se voló a 0,1 sccm llevando la presión de la cámara a 6 × 10 −6 Torr. Para un crecimiento mejorado con plasma, se introdujo una potencia de RF que variaba de 0 a 10 W para diferentes muestras de crecimiento. Diez vatios eran la potencia de RF más alta que se podía suministrar mientras se mantenía un plasma de acoplamiento inductivo (ICP) remoto y estable, ya que a una C 2 tan baja H 2 presión, la resistencia del gas es muy alta y la corriente inducida comienza a fluir en otra parte a potencias de plasma más altas. Una vez que se alcanzó la duración de crecimiento deseada (7 min para los crecimientos de CVD y 30 s para los de ICPCVD), C 2 H 2 se detuvo el flujo, seguido de otra purga de Ar para eliminar los gases de proceso restantes fuera de la cámara. A continuación, se apagó el calentador de muestras, lo que permitió que la muestra se enfriara a temperatura ambiente.
Caracterización del grafeno
Después de la síntesis, las muestras de grafeno se revistieron por rotación con PMMA. Luego, las obleas se colocaron en FeCl 3 para grabar el Ni, seguido de yodo / yoduro de potasio (40 mL H 2 O / 4 g KI / 1 g I 2 ) solución para grabar el Au restante. La película resultante se transfirió luego a SiO 2 limpio / Obleas de Si, y el PMMA se grabó con acetona. El análisis espectroscópico de grafeno se realizó utilizando un espectrómetro Raman UV Horiba Jobin Yvon HR800 con un láser de 532 nm para identificar los picos espectrales clave esperados para películas delgadas de grafeno. Las relaciones de intensidad máxima D:G y D:D '( I D:G , yo D:D ’ ) proporcionan información sobre la densidad del defecto y el tipo de defecto en el grafeno, respectivamente. La intensidad máxima de 2D:G ( I 2D:G ), así como el ancho completo del pico 2D a la mitad del máximo (FWHM) proporcionan información sobre el número total de capas de grafeno. Pantallas de grafeno monocapa sin defectos I D:G de aproximadamente 0, sin embargo, cuando los defectos están presentes un I 2D:G > 1.0 y FWHM 2D <100 cm −1 son indicativos de grafeno monocapa [10]. Las imágenes de la superficie se llevaron a cabo utilizando un Zeiss Sigma VP FEG SEM configurado con un detector de electrones secundarios In-Lens, que permite ver los tamaños de grano y las morfologías del catalizador después de la formación de grafeno. Se utilizó ImageJ para realizar el cálculo de porcentajes de hojas superiores a I 2D:G =1, lo que sugiere el porcentaje de grafeno monocapa producido, y los picos Raman se ajustaron y analizaron utilizando un programa escrito en R para identificar las proporciones de picos y FWHM.
Resultados y discusión
Aquí, se muestra que el uso de codeposición de Ni-Au como técnica de preparación de catalizador erradica el proceso previamente requerido de pre-recocido a 600 ° C para alear el catalizador de Ni-Au comparándolo con un catalizador de control de Ni solo de línea base y con el anterior. informes [3]. Para comparar los efectos del Ni-Au con el Ni puro, la Figura 2 muestra un espectro Raman promedio de grafeno transferido cultivado mediante CVD térmico a 450 ° C con un C 2 de 7 min. H 2 exposición sobre (a) Ni puro y (b) el catalizador de Ni-Au codificado sin recocido en contraste con la literatura anterior [3]. El modelo de crecimiento del catalizador de Ni puro CVD aceptado para el grafeno [11] sugiere que los precursores de hidrocarburos se absorben en la masa de Ni y se deshidrogena, ya que el C muestra una alta difusión en Ni. Durante el enfriamiento, los átomos de C individuales se difunden fuera de la masa de Ni a la superficie y forman grafeno [12]. La Figura 2a muestra una película delgada de carbono amorfo y el espectro correspondiente (inserto) que es típico del crecimiento catalizado por Ni puro a baja temperatura. El catalizador de Ni policristalino contiene muchos bordes escalonados y límites de grano en la superficie como resultado de la deposición por pulverización catódica que actúan como sitios que tienen una alta probabilidad de difusión de C y, por lo tanto, como sitios de nucleación de grafeno durante el enfriamiento, lo que permite que los átomos de C se difundan de la masa. en demasiadas ubicaciones, lo que provoca superposición. Sin embargo, con la adición de 1% en peso de Au, en la Fig. 2b se observa una mejora drástica en el espectro Raman. El espectro muestra picos D, G y 2D bien definidos con I 2D:G =1.2 y FWHM 2D =48,5 cm −1 lo que sugiere la formación de grafeno monocapa con defectos. Hay una I relativamente grande D:G =0.68 y un I correspondiente D:D ’ =5.0, lo que sugiere que existen tipos de defectos de vacancia y desajuste de celosía [13], sin embargo, tenga en cuenta que en ambas Fig. 2a, b, se produjeron películas delgadas enteras. Según la literatura, el carbono no se difunde fácilmente en Au [14], y esto sugiere que el Au podría reducir el número de sitios de nucleación de grafeno al bloquear los bordes de paso y los límites de grano [3] si se encuentra en estas regiones produciendo un menor número de capas por limitando tanto la absorción de C como la difusión externa. Para ilustrar el mecanismo de crecimiento de esta formación, la figura 3 muestra un conjunto de diagramas esquemáticos que comparan los modelos de crecimiento de Ni puro vs Ni-Au para los crecimientos térmicos de CVD, donde la síntesis típica de grafeno de Ni desarrolla grafeno multicapa debido a la incapacidad de regular la absorción de C y difusión externa (Fig. 3a), sin embargo, la adición de Au ayuda a controlar la absorción y difusión de C en el Ni (Fig. 3b). Estos resultados muestran que la adición de Au es eficaz para producir grafeno a bajas temperaturas, lo que es consistente con los resultados reportados por Weatherup et al. [3]. Sin embargo, lo más importante es que nuestros resultados demuestran que el uso de codeposición elimina completamente el recocido a 600 ° C requerido para producir una aleación de Ni-Au, lo que hace que esta sea una síntesis verdaderamente de 450 ° C mediante la aleación remota del catalizador de Ni y Au antes de la deposición en lugar de durante el proceso. receta de crecimiento.
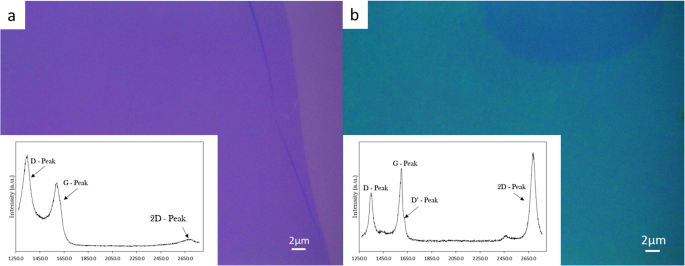
Imágenes ópticas y espectros Raman (inserciones) de a carbono amorfo como resultado de un intento de síntesis de grafeno durante 7 min C 2 H 2 exposición en catalizador de Ni puro de 50 nm a 450 ° C y b síntesis exitosa de grafeno siguiendo los mismos parámetros que a en el catalizador Ni-Au codificado, tenga en cuenta la mancha oscura en la parte superior de la imagen b es un área de grafeno multicapa y se capturó para agregar contraste y ayudar a identificar el área de monocapa circundante. Hay una mejora obvia creada por la adición de 1% en peso de Au, ya que esta es la única variable modificada para permitir el cambio drástico del carbono amorfo al grafeno. Etiquetado en a son los picos clave utilizados para la caracterización del grafeno. Para b , calculamos I 2D:G =1.2, FWHM 2D =48,5, I D:G =0,68 y I D:D ’ =5.0
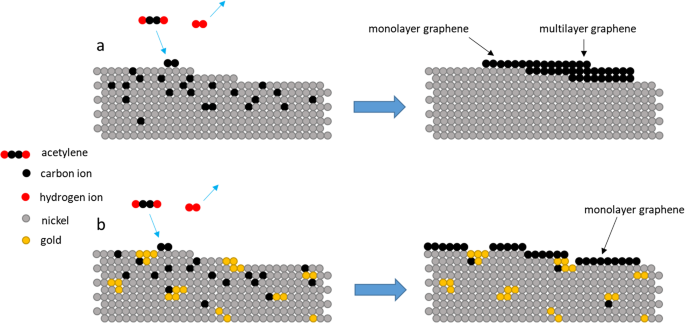
Diagrama esquemático del crecimiento del grafeno en a catalizador de Ni puro en el que se produce grafeno de pocas capas (FLG) debido a la absorción y difusión incontrolada de C en sitios de alta energía, como los bordes de los escalones, en comparación con b Síntesis de Ni-Au codepositada mediante la cual el Au actúa como un limitador de la absorción de C, además de reducir los altos niveles de producción de grafeno al bloquear las miras de nucleación como los bordes escalonados
Si bien el Ni-Au codificado produce películas de grafeno, es crucial poder producir grandes áreas de grafeno continuo y uniforme para aplicaciones prácticas. Para abordar este problema, se realizaron tres crecimientos en Ni-Au codepositado para comparar los efectos de incorporar un plasma remoto con tres poderes de plasma diferentes en el crecimiento. La Figura 4a-c muestra un Raman I 2D:G mapa de grafeno cultivado con Ni-Au codepositado a través de ICPCVD (0 W, 5 W y 10 W respectivamente) con un C 2 de 30 s H 2 tiempo de exposición. La Figura 4a es un mapa Raman de síntesis realizado sin la adición de potencia de plasma de RF que muestra un patrón de tablero de ajedrez que es el resultado de pequeñas áreas de espesor de capa de grafeno alterno. La adición de potencia de plasma de RF de 5 W en la Fig. 4b y 10 W en la Fig. 4c muestra porciones más grandes de capas conectadas y más uniformes mostradas por un aumento en el área de I uniforme 2D:G , representada por grandes áreas de color uniforme, con potencia de RF creciente. Esto muestra que la adición de plasma ayuda a crear una hoja de grafeno más grande y uniforme que está respaldada por el gráfico de datos de la Fig. 4d. La tendencia es que a medida que el plasma de RF aumenta a 10 W, hay un aumento en I 2D:G , una disminución en I D:G y una disminución en FWHM 2D todos los cuales son significativos de grafeno monocapa. Para explorar visualmente la continuidad de la película delgada de grafeno, la figura 5a muestra una imagen SEM de grafeno pretransferido cultivado a través de ICPCVD de 10 W donde vemos una hoja de 15 μm de ancho de grafeno monocapa continuo (MLG) con pocas islas de grafeno de pocas capas (FLG). ). Hay un moteado visible en la superficie en la Fig.5a, pero esto se atribuye a la estructura de grano subyacente del catalizador, ya que esta es una imagen del grafeno recién crecido y nuestro catalizador policristalino aún no se ha eliminado, que se detalla en la Fig. .5b así como la correlación de los espectros Raman para el grafeno multicapa (MLG) y el grafeno de pocas capas (FLG) en la Fig. 5c. Nuestros hallazgos sugieren, como se representa en la Fig. 6, que los iones de C deshidrogenado producidos por el plasma de RF alcanzan la superficie del catalizador y actúan como sitios de nucleación de alta energía para el crecimiento hasta la semilla. Si bien hay absorción en el Ni, estos iones C tienen una alta probabilidad de unirse con iones C adicionales en la superficie produciendo dímeros y moléculas más grandes que es mucho menos probable que se absorban en el catalizador de Ni. Dado que vemos una mayor uniformidad al aplicar plasma al crecimiento y una falta de uniformidad en el crecimiento térmico de CVD, como se muestra en la Figura 4, esto sugiere que durante la síntesis de ICPCVD, el catalizador no absorbe demasiado para producir grafeno multicapa. En cambio, el crecimiento se trasladó a un mecanismo dominado por la superficie. Este movimiento hacia un crecimiento dominado por la superficie también respalda nuestro enfoque de utilizar un catalizador delgado que se saturaría incluso más rápido que los catalizadores más espesos.
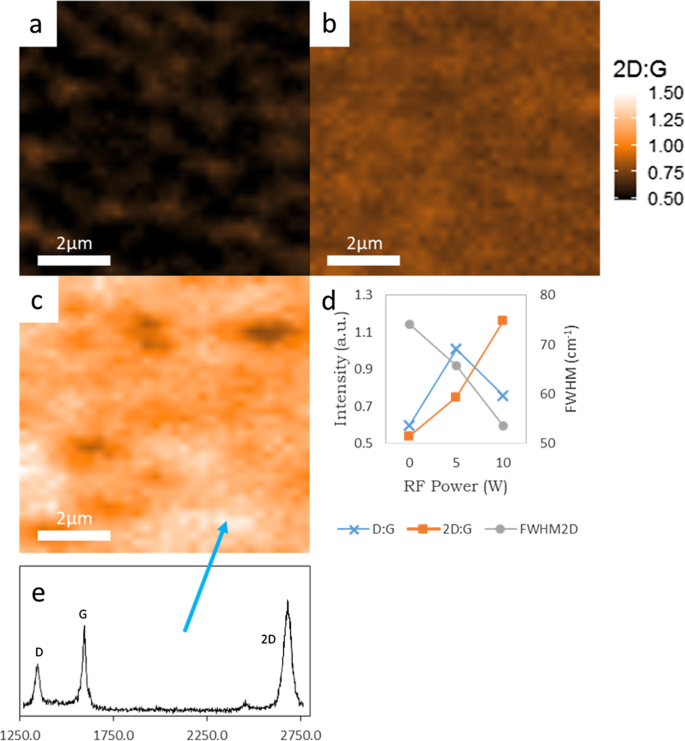
Mapas Raman de grafeno cultivado en Ni-Au codificado de 50 nm con 30 s C 2 H 2 tiempo de exposición a través de a CVD, b ICPCVD con plasma de 5 W y c ICPCVD con plasma de 10 W. El yo 2D:G , yo D:G y FWHM 2D para cada potencia de plasma se muestran en d donde es evidente que 10 W sirve como el mejor debido a su mayor I 2D:G , inferior I D:G y FWHM 2D más pequeño en comparación con los demás, y un espectro representativo tomado de la región más brillante de c se muestra en e
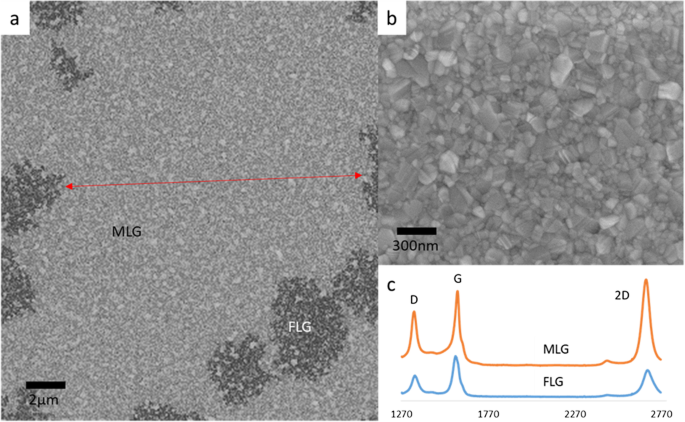
Imágenes de microscopio electrónico de barrido de grafeno recién crecido en catalizador de Ni-Au codepositado cultivado a 450 ° C mediante ICPCVD de 10 W que muestran a una sección de 15 μm de ancho de grafeno monocapa continuo (MLG) (flecha roja) con islas de grafeno de pocas capas (FLG) (oscuras) (espectros Raman promediados correspondientes en c ) y b gran aumento del área de grafeno monocapa donde se forma el grafeno en la parte superior de los granos de catalizador
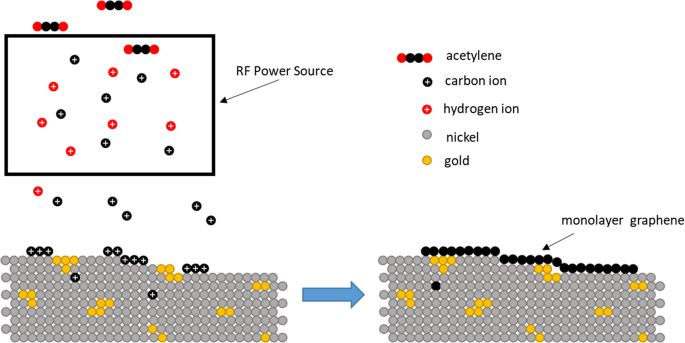
Diagrama esquemático del crecimiento de ICPCVD en el que vemos un cambio hacia un mecanismo dominado por la superficie. Este cambio es causado por la ionización de los átomos de C que actúan como sitios de nucleación de grafeno de alta energía una vez que alcanzan la superficie del catalizador y permite el uso de un catalizador más delgado ya que hay menos absorción, lo que conduce a la sobreproducción de grafeno durante el enfriamiento
Los beneficios de ICPCVD sobre CVD también se pueden ver al comparar la cobertura multicapa (MLG). Se comparó un conjunto de muestras de síntesis de ICPCVD y CVD y los resultados se muestran en la Fig.7, que muestra mapas Raman de (a) crecimiento de CVD de 7 min versus (b) crecimiento de ICPCVD de 30 s con 10 W de potencia de RF en Ni- Au. Según nuestro cálculo del mapa Raman, hemos estimado que el crecimiento de ECV en 7 minutos muestra una cobertura del 11,6% de I 2D:G > 1.0, mientras que el crecimiento de ICPCVD en los 30, por otro lado, muestra una cobertura del 99% de I 2D:G > 1.0. Esto sugiere que el plasma juega un papel importante en la conectividad y uniformidad del grafeno en un catalizador delgado y previene la absorción de grandes cantidades de C en el catalizador en oposición al crecimiento de CVD en el que la absorción excesiva de C conduce a la sobreproducción de grafeno y, por lo tanto, a una menor uniformidad. .
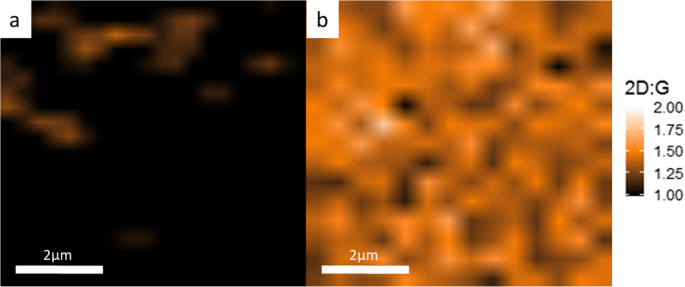
Mapas raman que muestran I 2D:G > 1.0 para a Síntesis de CVD con un tiempo de exposición de 7 min frente a b Síntesis ICPCVD de 10 W con un tiempo de exposición de 30 s. Ambos crecimientos son 450 ° C en catalizador de Ni-Au codepositado. La adición de plasma aumenta la uniformidad de la capa desde un 11,6% ( a ) al 99% ( b )
Conclusiones
Hemos demostrado la validez de la codeposición como una técnica de preparación de catalizador única que elimina de manera efectiva la necesidad de recocido para los catalizadores de Ni-Au mediante la pre-aleación remota del catalizador durante la evaporación del haz de electrones y produciendo un catalizador con capacidad inmediata para el crecimiento de grafeno a 450 ° C. La adición de usar un plasma acoplado inductivamente durante el crecimiento sirve para aumentar el área de la película delgada de grafeno y la uniformidad de la capa al cambiar el proceso de síntesis a un mecanismo dominado por la superficie que es beneficioso cuando se usan catalizadores delgados para el crecimiento. El estudio presentado aquí demostró el progreso significativo del uso de CVD mejorada con plasma y catalizador delgado de Ni-Au codepositado para cultivar grafeno con una calidad mejorada a baja temperatura. Sin embargo, los parámetros de crecimiento deben adaptarse y optimizarse con respecto a las aplicaciones específicas. Por ejemplo, el diseño y la optimización del catalizador para aumentar aún más el tamaño de grano de grafeno en condiciones de crecimiento a baja temperatura y el crecimiento directo de grafeno en los sustratos deseados. Estos son los problemas que se abordarán en las investigaciones en curso.
Disponibilidad de datos y materiales
Todos los datos están disponibles de los autores a través de una solicitud razonable.
Abreviaturas
- 2D:
-
Dos dimensiones
- BEOL:
-
Final de línea
- CVD:
-
Deposición de vapor químico
- FLG:
-
Grafeno de pocas capas
- FWHM:
-
Medio máximo de ancho completo
- ICPCVD:
-
Deposición de vapor químico por plasma acoplado inductivamente
- MLG:
-
Grafeno monocapa
- PVD:
-
Deposición física de vapor
Nanomateriales
- ¿Qué es la deposición de vapor químico?
- Tecnologías avanzadas de deposición de capas atómicas para micro-LED y VCSEL
- Investigaciones de estructuras de vacantes relacionadas con su crecimiento en la hoja h-BN
- Crecimiento autocatalizado de nanocables verticales de GaSb en vástagos de InAs mediante deposición de vapor químico metalorgánico
- Las nanofibras jerárquicas de poliamida 6-ZnO antibacteriana fabricadas por deposición de capas atómicas y crecimiento hidrotermal
- Propiedades fotocatalíticas de los polvos de TiO2 recubiertos con Co3O4 preparados por deposición de capa atómica mejorada con plasma
- Película WS2 de gran superficie con grandes dominios individuales producidos por deposición de vapor químico
- Evaluación de estructuras de grafeno / WO3 y grafeno / ceO x como electrodos para aplicaciones de supercondensadores
- Reducción de óxido de grafeno a baja temperatura:Conductancia eléctrica y microscopía de fuerza de sonda Kelvin de barrido
- Espectroscopia Raman de grafeno multicapa cultivado epitaxialmente en 4H-SiC por descomposición térmica de Joule
- Mecanismos de formación de nanocables de InGaAs producidos por una deposición de vapor químico de dos pasos de fuente sólida