Alcoa persigue la excelencia en confiabilidad
Si no puede soportar el calor, es mejor que no busque empleo en las instalaciones de Alcoa Primary Metals en el sur de Indiana.
Los recipientes que escupen fuego y los crisoles llenos de metal fundido pueden hacer que la temperatura ambiente del piso de producción se acerque a los tres dígitos. El calor irradia visiblemente de la maquinaria. Riachuelos de sudor corren por las mejillas y la espalda de los trabajadores. Los descansos frecuentes para tomar agua y Gatorade son una necesidad.
Es un entorno físicamente exigente, pero el calor real al que se hace referencia en el primer párrafo se relaciona más con la posición de esta planta en particular en la industria de la fundición de aluminio. Este sitio, que forma parte de las masivas operaciones Warrick de Alcoa, se construyó a fines de la década de 1950 y comenzó a producir aluminio en bruto para la industria de láminas de lata a principios de la década de 1960.
Es una planta antigua en una industria sensible a la edad y la tecnología. En 1980 había 33 plantas de fundición estadounidenses en funcionamiento. En la actualidad, hay 13. Sólo el 6 por ciento de la capacidad mundial de aluminio se producirá este año en fundiciones de más de 50 años. El tiempo corre.
A este estado, agregue eso:
-
El 25 por ciento de la fuerza laboral de la planta es actualmente elegible para jubilarse por edad o años de servicio;
-
los salarios pagados por la planta se encuentran entre los más altos de la industria; y,
-
Hace unos años, los costos de mantenimiento de esta fundición por tonelada métrica de aluminio producida eran los segundos más altos del sistema mundial de Alcoa.
¿Puedes sentir el calor? Todos los empleados de esta planta lo hacen. Pero en lugar de esperar una desaparición que parecía inminente, el personal de mantenimiento y operaciones dio un paso al frente y tomó medidas.
“Tenemos que engancharlo si queremos mantener este nivel de vida y mantener viva esta planta”, dice Mark Keneipp, gerente de la fundición Alcoa Business System. "Esta es la nueva realidad. Solo tienes que lidiar con eso ".
Comienza con una mirada en el espejo.
“Nuestro desafío era y es ser competitivo en costos a pesar de nuestra vejez”, dice Keneipp. “Ya no estamos al frente de la curva de edad. Debemos tener un horizonte de 15 a 20 años para atraer capital dentro de Alcoa. Si son de 25 a 30 años, sería genial. Para hacer eso, tenemos que demostrar continuamente que somos una planta eficiente, estable, rentable y eficiente ”.
Este no es un entorno para los débiles. Pero a través del trabajo duro y la perseverancia, hay muchas recompensas.
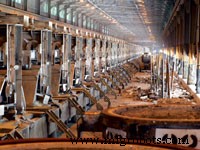
Tiempo de espera de llamada
Los esfuerzos para mantener la presencia de Alcoa Primary Metals en la comunidad manufacturera del sur de Indiana comenzaron a nivel corporativo.
En 1997, el director ejecutivo de Alcoa, Alain Belda, comenzó a llevar los principios del sistema de producción de Toyota (TPS) a las 250 ubicaciones globales de su empresa.
Director de producción de la planta de aluminio Rodney Cunningham (izquierda), coordinador de procesos Larry York y senior Brian Audie, ingeniero de procesos de personal, se encuentra dentro de un tanque de alúmina vacío en los terrenos de las operaciones Warrick de Alcoa. El sitio usó tradicionalmente cuatro tanques de este tipo como recipientes para contener alúmina, un ingrediente clave en el proceso de fundición del aluminio. Las iniciativas de manufactura esbelta y el pensamiento crítico llevaron a la planta a reducir su tamaño a dos tanques, lo que le permitió a la empresa ahorrar una gran suma de dinero.
TPS es una filosofía de fabricación ajustada basada en la producción "justo a tiempo", la eliminación de residuos y la resolución rápida de problemas. Sin embargo, la fundición de Indiana hizo un descubrimiento importante al implementar el sistema.
"TPS, flow y lean no funcionan si tiene un equipo inestable e impredecible", dice Keneipp.
El mantenimiento de la planta eficiente, racionalizado y rentable y la confiabilidad de la maquinaria deben ser lo primero.
Para ilustrar este punto, Keneipp ofrece un diagrama llamado "el iceberg de mantenimiento". Por encima del agua se encuentran los costos de mantenimiento directos vinculados a los materiales, la mano de obra, las horas extraordinarias, los servicios por contrato y los gastos generales y los beneficios. Debajo de la superficie se esconden costos indirectos vinculados al tiempo de inactividad, configuración y puesta en marcha, horarios perdidos, exceso de inventario, gestión de crisis, compras de emergencia y un efecto dominó general en la producción.
“Los componentes indirectos son rehenes de los procesos y equipos inestables de una planta”, dice.
Todo este desperdicio engulle el sistema y aumenta los costos de operación y mantenimiento.
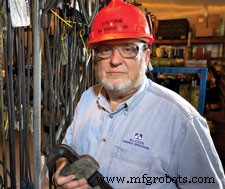
En 2002, esta planta de fundición tuvo costos totales de mantenimiento de más de $ 35 millones. Su relación "dolorosamente alta" de más de $ 137 en costos de mantenimiento por cada tonelada métrica de aluminio producida (ver "Solo los hechos" para el tonelaje anual) la colocó en el segundo lugar entre las plantas de fundición de Alcoa en todo el mundo. El promedio mundial en 2002 fue de $ 90 por tonelada métrica.
Esta planta de Alcoa y sus líderes tenían dos opciones.
“El gerente de la planta, Royce Haws, dijo que íbamos a reducir nuestros costos. No era una opción quedarse donde estábamos. Iba a suceder ”, dice Keneipp. “Podríamos hacerlo de la manera inteligente o de la manera miope. Cuando te vuelves miope, esos son días de miedo. Es difícil atraer capital a la planta para hacer las cosas que deben hacerse cuando simplemente pospone el mantenimiento. Nadie se siente bien con ese enfoque. Esa es la motivación para que la gente busque algo mejor ".
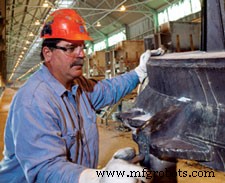
Atrapando las olas
Si aún no lo ha adivinado, la planta de Alcoa eligió el enfoque inteligente para reducir los costos de mantenimiento. Los líderes de mantenimiento se asociaron con consultores de Life Cycle Engineering (LCE) y Ron Moore Group a principios de 2003 para crear un enfoque llamado Proceso de excelencia en confiabilidad, que se implementó en tres "oleadas". El proceso se basa en la creencia de que una asociación formalizada y bien definida es imperativa entre el mantenimiento y las operaciones. En esta asociación, las operaciones son propietarias del equipo y tienen un interés principal en la confiabilidad. El mantenimiento es un socio igualitario dedicado a proporcionar métodos, habilidades, experiencia y apoyo oportunos y efectivos.
"Eso es un gran cambio", dice el superintendente de ingeniería de confiabilidad Joseph Motz. "Solía ser un entorno de silo con muchos señalamientos".
El metal fundido se vierte de un crisol
en el Departamento de Lingotes de la planta de Alcoa.
Algunos ejemplos:
Un operador notó un problema potencial. No se programó ni se hizo ninguna corrección. La máquina se averió. ¿Quién tuvo la culpa?
O bien, el mantenimiento se presentó para un trabajo de mantenimiento preventivo de dos horas. Mientras estaba en la máquina, encontró problemas adicionales y terminó el trabajo de mantenimiento preventivo ocho horas después, lo que afectó la producción. ¿Quién tuvo la culpa?
La respuesta en estos casos fue tanto el mantenimiento como las operaciones.
"Tuvimos que darnos cuenta de que todos estamos en el mismo equipo", dice Motz. “Todos estamos aquí para fabricar aluminio. Si vamos en direcciones diferentes y no trabajamos juntos, el proceso no funciona ".
La primera ola del enfoque de tres olas comenzó en junio de 2003.
"Wave 1 fue Ron Moore", dice Keneipp. “Lo trajimos para hablar con los líderes clave de la planta. Desafió los paradigmas ancestrales. "Es necesario adoptar más una filosofía de propietario de activos". "Estás desperdiciando dinero". Sacude las cosas y abre los ojos ".
Wave 2 llegó en agosto con una evaluación completa de excelencia en confiabilidad realizada por LCE. Durante un período de dos semanas, la empresa llevó a cabo largas entrevistas con 90 empleados de operaciones y mantenimiento (por hora y salario), así como con el controlador de la planta.
La información condujo a:
-
un análisis financiero que detalla el valor estimado para cerrar las brechas de excelencia en confiabilidad en comparación con el costo de implementación (presentado como un cálculo de retorno de la inversión);
- un plan maestro preliminar que describía los procesos y metodologías necesarios para cerrar las brechas.
“Queríamos observar nuestra condición actual e identificar una condición objetivo”, dice Keneipp. “La brecha entre esos dos es tu dolor o tu ganancia. ¿Vale la pena el esfuerzo de salvar la brecha? Teníamos que demostrarle ese valor a la alta dirección. Tuvimos que demostrar que había mérito en poner dinero en la vieja planta.
“Ante todos los hechos, era prudente obtener la aprobación del dinero lo antes posible para proceder”.
Wave 3 comenzó en septiembre. Líderes de operaciones y mantenimiento:
-
implementó el plan maestro
-
educó a todos los empleados sobre sus nuevas funciones y responsabilidades relacionadas con el aumento de la confiabilidad del equipo
-
realizó talleres sobre técnicas adecuadas de mejora de la confiabilidad
-
establecido procesos definidos y medidas efectivas de progreso
“Esto no es fácil. Nada de esto lo es ”, dice Rodney Cunningham, gerente de producción de la sala de marihuana. “Pero si tiene un compromiso de gestión y una asociación entre el mantenimiento y las operaciones, sus posibilidades de éxito aumentan. Sin esas cosas, no lo logrará ".
Elevando el listón
El establecimiento de definiciones en una variedad de áreas ha ayudado a impulsar mejoras. Un enfoque principal fue definir "¿qué es posible?" y "¿qué es el progreso?"
La respuesta llegó al aceptar la efectividad general del equipo (OEE) como una métrica clave para toda la planta. OEE rastrea las fuentes de pérdida operativa, incluida la disponibilidad, el rendimiento y la calidad del equipo, y se expresa como un porcentaje del rendimiento óptimo.
"Básicamente se define por un mejor desempeño pasado", dijo el gerente de producción de electrodos, Tom Svoboda. “Lo viste pasar. No era ficticio ni hipotético. Ya sea que el equipo estuviera funcionando extraordinariamente ese mes o que usted estuviera realmente al tanto del proceso, sucedió. La pregunta es, si lo hizo durante ese período de tiempo, ¿por qué no puede hacerlo todo el tiempo? "
Usando una analogía deportiva para ilustrar la importancia del 100 por ciento de OEE, si un saltador alto normalmente salta 6 pies y 6 pulgadas pero establece una mejor marca personal de 7 pies, lo que condujo específicamente a este pico de rendimiento del 100 por ciento. ¿Entrenó de manera diferente? ¿Cambió su dieta antes del encuentro? ¿Llevaba zapatos diferentes? Literalmente subió el listón. ¿Qué se puede aprender y qué se puede hacer para lograr esa marca una y otra vez?
El mantenimiento y las operaciones trabajaron juntos para definir el rendimiento máximo de las funciones de la planta (por ejemplo, ensamblaje de ánodo), procesos (descarga de mineral), resultados (chatarra) y piezas individuales de equipo (horno de anillo). Al recopilar esta información, se determinó que era posible ahorrar $ 8,3 millones en costos anuales como resultado del logro de los objetivos de la OEE.
Con la información de fondo, se definieron los estados actuales y se establecieron las condiciones objetivo. Se llevaron a cabo actividades:proyectos de trabajo que utilizan herramientas de manufactura esbelta como kaizen y mejora continua. Se midió y analizó el progreso. Y se calcularon los beneficios tangibles.
En 2004, $ 2.4 millones en mejoras se vincularon a ganancias de OEE.
Profundizar y tomar medidas también condujo a una disminución de los gastos de mantenimiento en la planta de fundición. En el primer año después de comenzar la iniciativa de confiabilidad, los gastos cayeron $ 1.9 millones, de una cifra de referencia de $ 32 millones a $ 30.1 millones. En 2004, la cifra descendió otros 700.000 dólares. La proporción de gastos de mantenimiento por tonelada métrica producida también se redujo a 109 dólares en 2004.
El plan "Planificado"
También se hizo un gran esfuerzo para definir mejor los elementos de mantenimiento. Específicamente, en este sistema de confiabilidad dirigido por el operador, "¿cómo se planifica el trabajo?" y "¿cómo se hace el trabajo?"
“Mirando hacia atrás, nos engañábamos pensando que estábamos saludables”, dice el gerente de mantenimiento Danny Reyes. “Muchas de nuestras antiguas métricas estaban fuera de contacto. Pensamos que nuestro 'porcentaje de trabajo planificado y programado' estaba en el 85 por ciento y nuestro 'porcentaje de finalización de PM' estaba en el 90 por ciento ".
LCE informó a la planta que estaba usando definiciones incorrectas.
“El 'porcentaje de trabajo planificado y programado' en realidad era solo el 'porcentaje programado'. La planificación era muy limitada”, dice Reyes. “Fue el cumplimiento del cronograma. Probablemente el 10 por ciento de esos trabajos fueron planeados ".
Una proporción de 35 a 1 de personal artesanal (140) a planificadores (cuatro) era el meollo del problema.
“No funcionó muy bien”, dice el planificador de mantenimiento Larry McCubbins. “Hubo muy poco tiempo para planificar. Te convertiste en un programador, y no muy bueno en eso ".
Un entorno reactivo prospera en este entorno. “Estábamos aplicando el 'enfoque de mantenimiento del hogar'”, dice Keneipp. “Así es como tú y yo abordamos los proyectos un sábado por la mañana. Es realmente ineficaz y no está planificado ".
Desde entonces, la planta ha agregado tres planificadores para un total de siete, lo que proporciona una proporción más manejable de 20 a 1.
"Eso hace posible que estos muchachos instalen, organicen el trabajo, lo planifiquen, lo programen con los centros de producción, se aseguren de que todas las piezas estén allí, se aseguren de que el equipo no funcione y el tiempo esté asignado", dice el superintendente de mantenimiento de fundición. Scott Deon.
Otras claves para una mejor planificación:
-
Un documento formal ahora describe los componentes de un trabajo planificado (consulte la barra lateral en la página 14). "Los pobres cuatro planificadores que teníamos tratando de hacer todo no hacían las cosas de la misma manera", dice Deon. "Este nuevo formato ahora estandariza cómo realizar el trabajo".
-
Los planificadores utilizan ahora un área formal y segura para preparar el trabajo. En el pasado, las piezas y los materiales necesarios se enviaban por partes a un lugar de trabajo. La pila puede permanecer durante semanas hasta que lleguen todos los artículos. Durante el tiempo de espera, no era raro que las piezas o herramientas se movieran, se perdieran o se usaran para otro trabajo.
“Mientras el planificador planifica el trabajo, pide todos los materiales y los entrega aquí. ”, Dice McCubbins. “Cuando todo para el trabajo está aquí, lo juntamos en una paleta o dos. Luego, los artesanos vienen y lo llevan al lugar de trabajo y realizan el trabajo ". -
Comunicación eficaz.
“Solía pensar que sabía lo que la gente quería. Este proceso me enseñó que no lo hice ”, dice McCubbins. “No sabía lo que querían ni lo que era adecuado para ellos. En el pasado, planeé el trabajo y no hice preguntas ".
Agrega Deon:" Con la responsabilidad compartida con la producción, ahora sabemos qué trabajo es lo primero. La persona propietaria del equipo debe saber qué es lo más crítico. Antes, no creo que lo estuviéramos adivinando. ¿Pero estábamos al 100 por ciento? Probablemente no ". -
Reuniones semanales enfocadas y efectivas.
“Los propietarios de activos presiden las reuniones y los planificadores / programadores de mantenimiento del área son los facilitadores”, dice Keneipp. “Si es una reunión de planificación, discutimos cómo vamos a hacer esto. Si se trata de una reunión de programación, establecemos el horario ".
También con respecto a cómo se realiza el trabajo, la planta tomó medidas para documentar el historial del equipo y estandarizar las instrucciones de las tareas de mantenimiento.
“Al principio, se podían obtener registros, pero luego la documentación se detenía”, dice Dan Decastra, ingeniero de energía de la estación rectificadora. “Entonces, creamos una ubicación en el servidor y comenzamos a documentar. Para esta estación, creamos una lista de "chicos malos". Escogimos los grandes problemas y empezamos por ahí. Ahora, puede volver al 2001 y ver un historial de los interruptores de aire, contactos, transformadores y patines ".
Jonathan Fulton, ingeniero de confiabilidad, agrega:“Quizás un tercio de nuestra fuerza laboral de mantenimiento podría jubilarse mañana si quisiera. Esa es una gran responsabilidad potencial para nosotros. Y es difícil conseguir un artesano de calidad del exterior. Para abordar esto, estamos estandarizando los procesos de trabajo y desarrollando el historial del equipo. Al hacer esto, podemos hacer que las personas con experiencia técnica se pongan al día rápidamente ”.
Notas sobre la cuna
Un ejemplo de mejora final es cómo la planta definió mejor quién compra productos de mantenimiento y cómo se gasta el dinero en herramientas y materiales de tipo consumible.
En el pasado, el personal de mantenimiento variado de la planta de fundición compraba herramientas manuales, herramientas eléctricas, productos de seguridad, limpiadores, productos para el manejo de materiales y otros cien artículos necesarios. Los productos comprados se guardaron en cunas de herramientas descentralizadas alrededor de la instalación y en una serie de lugares de espera no oficiales (casilleros, cofres y cubículos).
“A medida que la planta siguió expandiéndose, se agregaron áreas. Tenían un pequeño grupo y alguien hacía los pedidos y ellos compartían sus suministros aquí y allá ”, dice el mecánico general Dick Day. “Estábamos gastando una gran cantidad de dinero tratando de alimentar estas cunas satélite. No fueron administrados. La gente compraba cosas, pero no era realmente accesible ".
Si un mecánico necesitaba una herramienta en particular, la buscaba. Estaba por alguna parte. Si no podía encontrarlo, pediría uno. Esa herramienta comprada podría desaparecer antes de que le llegara. Condujo a gastos innecesarios y superfluos.
Para abordar esto, se construyó una cuna centralizada y todos los elementos de la cuna satélite y el cubículo se llevaron a esta área cerrada y segura.
Llegaron los inútiles.
"Nos dimos cuenta de que teníamos muchas cosas obsoletas, algo para un equipo que quizás hayamos sacado hace 10 años", dice Keneipp.
Y entró lo valioso.
“Fue increíble todo lo que salió de la carpintería. Alguien trajo un gabinete con más de $ 38,000 en bombas y gatos ", dice Day, quien se convirtió en el asistente principal de la cuna central. “Empezamos a usar lo que teníamos. Para algunos materiales, no tuvimos que pedir nada durante un año ".
Hoy, Day es responsable de comprar estos productos relacionados con el mantenimiento. Recibe las compras, almacena los artículos y los dispensa según sea necesario.
"Sabemos lo que tenemos y dónde está ubicado", dice.
Day también ha creado un sistema mínimo / máximo para una variedad de productos y se embarcó en esfuerzos para estandarizar las marcas de herramientas eléctricas y suministros de soldadura.
“Con las herramientas eléctricas, nos hemos estandarizado principalmente en DeWalt, y nos estamos involucrando mucho en sus herramientas inalámbricas”, dice. "Para los suministros de soldadura, hemos estandarizado nuestras pistolas de alimentación de alambre y las piezas de repuesto para esas pistolas".
Hace su tarea y encuentra formas innovadoras de reducir costos.
Algunos ejemplos son:
Guantes :“Solíamos comprar una marca de guantes que tenía una pequeña pestaña por $ 12 el par. Eso es lo que todo el mundo 'tenía que tener' ”, dice. “Podrías comprar los mismos guantes con un poco de elástico por $ 2.67 el par. A la gente le gustaban ".
Aceite hidráulico :“Lo compramos por galón a $ 8 cada uno. Al comprarlo a granel, ahora ahorramos $ 3 por galón. Vierto el aceite en jarras reutilizables que cuestan 57 centavos cada una ”.
Manguera de acetileno :“Solíamos comprarlo preempacado en un carrete. Ahora, lo compramos en un rollo de 500 pies y cortamos lo que la persona necesita. Ahorramos un 25 por ciento ”.
Day dice que todo es sentido común.
“Lo veo como mi dinero”, dice. "Si este es mi negocio, así es como lo manejaría".
Haciéndolos sudar
Gracias al trabajo arduo, la asociación, la propiedad y el pensamiento innovador, esta planta de fundición de Alcoa se ha vuelto más estable, eficiente, predecible, confiable y competitiva en costos.
Los beneficios de costos de la OEE son de $ 4,4 millones anualizados para 2005 hasta la fecha en comparación con la cifra de referencia de 2003.
Los gastos de mantenimiento hasta la fecha de 2005 son de $ 27,1 millones anualizados y reflejan una disminución de $ 4,9 millones con respecto a la cifra de referencia de 2003.
Los costos de mantenimiento para el segundo trimestre de 2005 fueron de $ 96 por tonelada métrica producida y se espera alcanzar los $ 87 en un futuro cercano.
Una evaluación de seguimiento de LCE colocó a la planta en la categoría de "condiciones proactivas" y se está trabajando para elevarla a la categoría de "excelencia".
Hay optimismo e impulso.
“Cuando me contrataron hace 15 años, dijimos:'Somos tecnología antigua. No podemos competir con algunas de las instalaciones más modernas ", dice Fulton. “Para mí, la recompensa es vernos competir y tener una mayor eficiencia. Estamos produciendo mejor con nuestra tecnología de 40 o 50 años que en los sitios construidos hace 10 o 20 años ”.
Si bien el calor nunca desaparecerá por completo para esta planta, está haciendo todo lo posible para hacer sudar a la competencia.
¿Cuáles son las características de un trabajo planificado?
-
Existe una estimación de tiempo precisa para el trabajo de modo que el supervisor tenga una expectativa razonable sobre cuándo podría asignar la tarea.
-
Existe una estimación precisa de los recursos necesarios en términos de personal artesanal, piezas de reparación / reemplazo, herramientas, equipo de apoyo, etc.
-
Se obtiene toda la información necesaria (planos, permisos, relacionada con la seguridad, etc.).
-
Se establecen la secuencia de pasos del trabajo, los procedimientos y las instrucciones para realizar el trabajo.
-
Todas las piezas y materiales necesarios están equipados.
-
Como un control integrado para asegurar un trabajo planificado de calidad, discuta periódicamente la naturaleza del trabajo con un supervisor y / o el artesano asignado para completar el trabajo. Asegúrese de que se comprenda plenamente el alcance del trabajo y de que el paquete de trabajo del kit esté completo.
Mantenimiento y reparación de equipos
- ¿Qué es la cultura de confiabilidad?
- ¿Cuál es la función del ingeniero de confiabilidad?
- Una revolución en la confiabilidad de Whirlpool
- Los mejores en mantenimiento y confiabilidad
- La clave n. ° 1 para el éxito de la confiabilidad
- ¿Ventas centradas en la confiabilidad?
- ¿Cómo acelera la excelencia en confiabilidad los beneficios de Lean?
- Fiabilidad orientada a la familia
- Gestión de la cadena de suministro:más allá de la excelencia en fiabilidad
- Por qué la excelencia en confiabilidad es imperativa para la seguridad
- La confiabilidad es una iniciativa ecológica