Una mejor planificación del mantenimiento es la bala de plata de MillerCoors
Tim Davison, planificador de MillerCoors Asset CARE
Planificar no es sexy. Tom Clancy no escribirá un thriller de espionaje titulado "El planificador de mantenimiento".
No pondrá a sus amigos al borde de los taburetes de la barra contando el momento en que tomó todos los pasos apropiados y se aseguró de que el proyecto de revisión se desarrollara sin problemas. ("Amigo, ¿qué pasó entonces?")
No hay ostentación ni destello ni atractivo visual.
“Cuando un departamento de mantenimiento busca mejoras, generalmente hay un gran enfoque en mostrar los triunfos y tomar fotografías de antes y después, cosas que sorprenden”, dice Dan Roberts, director de confiabilidad de Asset CARE para Miller Coors en Golden, Colorado.
“El mantenimiento predictivo es atractivo. Con la termografía infrarroja, toma una instantánea y dice:'Mire lo que encontré'. Con el análisis de vibración, lo conecta, imprime sus lecturas y dice:'Sí, encontré un rumbo malo'. Eso es muy importante y necesario, pero hay un buen trabajo en el núcleo. Simplemente no es sexy. ¿Cómo muestra los resultados de una planificación y programación efectivas? No puedes hacerlo con fotos de antes y después ".
De manera silenciosa y encubierta, la organización de mantenimiento y confiabilidad de MillerCoors utiliza la planificación y la programación como una herramienta de mejora. Proporciona equilibrio en un entorno donde el desequilibrio tiene consecuencias importantes.
Mantenimiento de la cadena
MillerCoors, la tercera cervecera más grande de Estados Unidos, se ha enfocado en mejoras de mantenimiento durante más de una década, y por una buena razón. La cervecería Golden funciona las 24 horas del día, los siete días de la semana, para elaborar 217 millones de onzas de cerveza cada día.
"Quizás hay dos días al año en los que no estamos produciendo", dice Tim Davison, un planificador de Asset CARE en la parte de la cervecería del gran complejo de múltiples plantas en Golden.
El proceso de elaboración de cerveza, desde las materias primas hasta los productos envasados y enviados, se ejecuta en una cadena estrechamente vinculada, y muchos componentes del proceso cuentan con piezas de maquinaria no redundantes. Si se produce una avería mecánica, es posible que cambiar el trabajo a un equipo similar no sea una opción. En estos casos, el proceso se detiene.
"Cuando hay una avería, suele ser un gran problema", dice Ron Kerr, gerente de Asset CARE para servicios públicos. "Afecta a casi todo el mundo aguas arriba y aguas abajo".
El operador de prensa Craig Doebele maneja los controles a lo largo de la
línea de producción en Rocky Mountain Metal Container, la empresa conjunta MillerCoors / Ball.
El objetivo es que la maquinaria funcione sin parar durante meses seguidos, especialmente durante la temporada alta de verano, hasta que se pueda programar un breve período de mantenimiento.
La estructura única de las unidades de negocio de Golden añade estrés a la cadena. Si bien MillerCoors es propietaria de la cervecería, es un socio conjunto en las unidades de fabricación de latas (con Ball Corporation) y de botellas (Owens-Illinois). Es necesario lograr que todos vayan en la misma dirección, pero requiere paciencia.
El ingrediente que falta
El ritmo de mejora del mantenimiento, lento y constante durante años, se aceleró a fines de la década de 1990 después de que Anheuser Busch anunciara recortes de precios. Para mantenerse competitivo, MillerCoors buscó reinvertir en la parte delantera del negocio.
“El costo de nuestros productos tuvo que reducirse por un gran margen”, dice Roberts. “Necesitábamos ir tras una serie de elementos, siendo las operaciones uno de ellos. La oportunidad y el objetivo eran convertirnos en la operación más confiable posible ”.
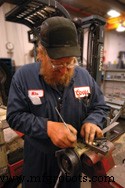
Asset CARE (acrónimo de Capability, Availability, Reliability and Enhancement) se convirtió en el grito de guerra. Se emplearon herramientas de mantenimiento centrado en la confiabilidad (RCM), análisis de causa raíz de fallas (RCFA) y mantenimiento predictivo (PdM). Incluso con estos avances positivos, algo faltaba.
Roberts cita el ejemplo de un fan que experimentó tres fallas dinámicas durante un período de tiempo de 18 meses. Después de la primera falla, RCFA identificó la lubricación como la causa principal. Se instaló un sistema de lubricación automática. Después de la segunda falla, los lubricadores automáticos se consideraron problemáticos. Después de la tercera falla, los líderes de mantenimiento dieron un paso atrás.
“Ahora participamos en ejercicios de mapeo de causas que nos llevan a explorar múltiples causas fundamentales”, dice Roberts. "RCFA no dice que haya una causa raíz, pero lleva a las personas en esa dirección".
Al profundizar, la planificación y la programación surgieron como un factor que contribuyó al problema.
Un mes antes de la tercera falla, el análisis de vibraciones había identificado anomalías. Sin embargo, no se tomaron los pasos adecuados para programar el mantenimiento y convertirlo en una prioridad antes de que ocurriera la falla. La lección:es poco probable que se obtengan ganancias sustanciales si no se cuenta con una planificación y programación básicas.
“Antes de nuestros esfuerzos concentrados, no estábamos planificando ni programando, per se”, dice Roberts. “Los planificadores examinaron las órdenes de trabajo en el sistema informático, las imprimieron, se las entregaron a un supervisor y esperaron a que el supervisor se las entregara a la cuadrilla. Se puso poco esfuerzo en sentarse semanalmente con las operaciones y revisar lo que se avecinaba, determinar las prioridades e identificar los recursos ”.
Las plantas funcionaron en modo de mantenimiento reactivo. Los planificadores dedicaron un tiempo considerable a buscar, almacenar y distribuir las piezas de repuesto.
“Si nuestra organización tiene visión de futuro, estamos encontrando las cosas que necesitan ser corregidas, escribiendo la orden de trabajo, planificando la orden de trabajo y haciendo el trabajo. Si es reaccionario, compramos asientos de primera clase en aviones para enviar un motor ”, dice Bobby McCall, gerente de mantenimiento para operaciones de empaque.
El trabajo reactivo tuvo sus recompensas:palmaditas en la espalda y obsequios de agradecimiento de la producción. Cada año se entregaba un trofeo de viaje al planificador responsable del mayor número de entregas nocturnas.
Luego, MillerCoors ideó una mejor manera al identificar los componentes esenciales de una planificación de mantenimiento eficaz. Estos maximizan los recursos, minimizan los costos y aumentan la confiabilidad general del equipo. Las secciones que siguen describen varios de estos componentes.
Dan Roberts es el director de fiabilidad de
Asset CARE de MillerCoors Brewing Compañía en
Golden, Colorado. Si bien las plantas de la compañía
han logrado avances significativos,
él admite que "todavía no hemos llegado".
Verdaderamente Dedicado
Como en cualquier esfuerzo, la dedicación es la clave del éxito. En MillerCoors, el mantenimiento con visión de futuro comienza con planificadores y recursos dedicados.
Una organización de planificación necesita el número adecuado de planificadores. Cada planificador debe tener un área de responsabilidad que sea:
• razonable en tamaño geográfico;
• razonable en número de personal artesano representado; o,
• razonable en número de piezas de equipo.
Sin esos límites, ¿cómo puede el planificador dedicar el tiempo y los recursos adecuados para mantener eficazmente esa área?
Davison dice que con un área demasiado grande, un planificador no puede concentrarse en todo el alcance, solo en los malos actores y las situaciones de emergencia que surgen. Cuando un planificador se centra en los malos actores y las fallas, no permite la planificación predictiva y proactiva necesaria.
"Dos personas no pueden planificar 4.000 equipos", dice Davison. "Todo lo que tendrán tiempo es para pedir piezas".
El mecánico de montacargas Jerry Mitchell quita una rueda
para exponer un cojinete para trabajos de mantenimiento preventivo.
Con respecto a la cobertura del planificador a la artesanía, Roberts dice que su objetivo actual es un planificador por cada 15 a 18 artesanos. La regla general es que a medida que avanza hacia la clase mundial, puede tener más personas de artesanos por planificador. Si está en los peldaños más bajos de la escalera, un porcentaje mayor de planificadores es apropiado.
El objetivo del cervecero es limitar específicamente a sus planificadores a tareas que pertenecen a la confiabilidad y mantenimiento del área definida de responsabilidad. De lo contrario, es fácil que los planificadores se desvíen de un trabajo que queda fuera de su rol y función.
"La producción puede ver al planificador como un 'go-fer' o un Wal-Mart, que está allí para atender todas sus necesidades y deseos", dice Brad Simpkins, gerente de Asset CARE a cargo de equipos móviles.
La gestión de la planta y del departamento también puede obstaculizar a los planificadores con las tareas administrativas, de generación de informes y de entrada de datos.
"Sin la capacidad de tener un enfoque real, la planificación se vuelve reactiva", agrega Simpkins.
Igual de importante, estos planificadores también requieren recursos dedicados (tiempo y mano de obra) para completar el trabajo planificado y programado. Esto puede ser un trago amargo para algunos trabajadores de producción y mantenimiento.
"Algunos de los mecánicos que trabajan por horas dijeron:'Nos gusta lo que estamos haciendo ahora'. Les gusta entrar en el caballo blanco y salvar el día", dice Jay Johnson, gerente de mantenimiento de operaciones de proceso. “Pero vieron que la gerencia estaba detrás de esto al 100 por ciento. Esto no iba a desaparecer ".
Los gerentes y operadores de producción también estaban recelosos de poner al caballo blanco a pastar.
En la organización de empaque de MillerCoors, el equipo de mantenimiento se dividió a partes iguales en tres turnos. "Su propósito era reparar las máquinas y hacerlas funcionar", dice Kerr.
Luego, llegaron los primeros cambios de programación. Un porcentaje considerable de artesanos que trabajaban de noche y los fines de semana se cambió para realizar el trabajo planificado en el turno de día.
“La producción nos dijo:'¡No estás apoyando nuestras averías!'”, Dice Kerr. "Estás bien. No voy a apoyar sus averías. Voy a apoyar el trabajo proactivo. Lograr que aceptaran eso requirió un acto de fe ".
Entre los departamentos funcionales de MillerCoors, el embalaje es actualmente el pionero en impulsar recursos dedicados al trabajo planificado y proactivo.
“Vamos a planificar el 100 por ciento de las horas disponibles para el trabajo de mantenimiento planificado”, dice McCall. “Todavía escuchamos, 'No puedes hacer eso; tienes que planificar las averías ". No, no vamos a planificar las averías. Planearemos hacer el trabajo planeado. Nos ocuparemos de las averías si ocurren ”.
En todos los niveles, la organización debe darse cuenta de que los operadores y el personal artesanal existen en una instalación de fabricación porque hay un proceso que operar y mantener. Los planificadores existen para maximizar la efectividad de los operadores y mantenedores. Cuando todos los niveles de la operación comiencen a trabajar juntos como un equipo, para un objetivo común de mejorar la confiabilidad y el rendimiento operativos, ya no habrá un enfoque en las "victorias del caballo blanco", sino en las ganancias sostenibles a largo plazo.
Gestión del tiempo
Otra clave para el éxito de la planificación de MillerCoors es aprovechar al máximo el tiempo.
Como se señaló en la sección anterior, la producción fue un poco escéptica. Si el mantenimiento iba a aliviar los dolores de la producción, estos "pensadores avanzados" tendrían que demostrar su valía. Recuerde, una máquina fuera de línea puede tener enormes implicaciones.
Un desafío fue lograr que la producción se diera cuenta de que detener una máquina durante 40 minutos para el mantenimiento preventivo durante un día y una hora predeterminados era mejor que una interrupción de tres horas después de una avería en un día y una hora desconocidos. El desafío adicional fue lograr que la producción creyera que su valioso tiempo no se desperdiciaría.
“Tuvimos un historial deficiente con la planificación y la programación. Teníamos que demostrar que si nos da el tiempo, lograremos el trabajo proactivo planificado ”, dice Davison. “Ellos derribaron la línea. Están perdiendo dinero. Tienes que aprovechar al máximo esa ventana ”.
La maximización del tiempo se produce mediante una planificación y programación eficaces.
Primero, una ventana de mantenimiento debe estar claramente definida (hora programada, fecha, alcance y duración) y acordada por los planificadores de mantenimiento y los líderes de producción. A partir de ahí, el planificador solicita las piezas y los materiales necesarios y se asegura de que se disponga de la cantidad correcta de recursos para realizar el trabajo. El planificador supervisa que no se produzcan sorpresas o, peor aún, cancelaciones cuando se abre la ventana. La mano de obra de mantenimiento varada o no productiva tiene un impacto directo en los costos de la empresa.
La participación no termina ahí. Durante la ventana, el planificador observa, ayuda y evalúa el trabajo para obtener un conocimiento completo del trabajo. Ese conocimiento se aplica para planificar y programar mejor tareas similares en el futuro. Él o ella también se gana una medida de respeto y aprecio por parte de los artesanos que trabajan en el trabajo. Esto es vital cuando surgen preguntas y consejos técnicos en un momento posterior.
Si bien este es el método convencional de planificar a medida que surge el trabajo en MillerCoors, también existen métodos especializados de planificación y programación.
La planta de fabricación de latas, que debe funcionar constantemente para satisfacer las necesidades de la cervecería (12 millones de latas por día), utiliza un plan de tiempo de inactividad de 12 meses que es desarrollado mutuamente por los líderes de operaciones, mantenimiento, ingeniería, control de procesos, calidad, almacén y programación.
El plan de 2005 enumera las fechas, ubicaciones, actividades de mantenimiento y detalles del proyecto para 1,655 horas de tiempo de inactividad programado. El plan de 2006 se elaboró en septiembre.
“Colocamos a 20 personas en una habitación y lo resolvemos como un equipo”, dice David Miller, director de servicios técnicos de Rocky Mountain Metal Container (la empresa conjunta MillerCoors / Ball). “Pusimos todo en el cronograma y exploramos, ¿qué más podemos hacer durante esa interrupción? ¿Cómo podemos maximizar ese tiempo? No podemos tener sorpresas durante el año. Tenemos que estar por delante del juego. Por lo tanto, el plan de tiempo de inactividad es nuestro documento guía para garantizar la confiabilidad del equipo y la entrega de latas de aluminio para cumplir con los requisitos de la cervecería ".
La planta de fabricación de botellas, que produce 3 millones de botellas por día, utiliza la visión de futuro para cierres programados de una sola máquina y de toda la planta.
“Solíamos estar funcionando todo el año y luego cerrábamos en Navidad para trabajos de mantenimiento preventivo (PM)”, dice Tim Hood, gerente de servicios de ingeniería de Rocky Mountain Bottle Company (la empresa conjunta MillerCoors / Owens-Illinois). "Durante el resto del año, lidiarías con las fallas a medida que sucedieran porque no programamos ningún otro tiempo de inactividad".
En la actualidad, los planificadores y los líderes de mantenimiento y producción de esta planta programan sesiones de tiempo de inactividad denominadas "paradas máximas en boxes". De manera similar al plan de tiempo de inactividad de la planta de latas, estas paradas para mantenimiento preventivo y revisiones se establecen con mucha anticipación.
"Programamos diferentes máquinas en diferentes momentos", dice Hood. "De esa manera, no tendrás todo tu equipo abajo a la vez. Movemos los recursos para compensar el tiempo de inactividad ”.
En septiembre se produce un cierre anual de la planta, dirigido por un solo planificador.
"Él está involucrado en todo el plan, tratando de averiguar qué trabajo se debe hacer durante la interrupción", dice Hood. “Hacemos limpieza a vapor en las máquinas y PM todo el equipo de distribución eléctrica durante este tiempo. Es una empresa enorme. Cuando terminamos un cierre, el planificador ya está preparando el plan para el siguiente ”.
El proceso de elaboración comienza con el malteado de la cebada.
La cebada es remojado en agua y estimulado a germinar.
Después de cuatro a cinco días, la "malta" se calienta para detener
mayor crecimiento. Luego, la malta se agrieta con rodillos de acero para
exponer su contenido.
Información útil
El éxito de la planificación de MillerCoors también está ligado a aprovechar al máximo la información. Comienza con algo tan básico como proporcionar información precisa sobre los recursos disponibles para un turno determinado.
"¿Quién está aquí? ¿Cuánto tiempo están aquí? ¿Con cuántos recursos tienen los planificadores para planificar? Antes, como en cualquier organización reactiva, era nebuloso ”, dice McCall. “En SAP, lo concretamos. Los planificadores ven que "tengo una ventana de ocho horas y diez hombres. Puedo planificar 80 horas de trabajo. Aquí hay 80 horas de trabajo para poner en ese plan ".
Otra antigua área gris fueron las órdenes de trabajo. Como en la mayoría de las plantas, se crea una orden de trabajo cuando se identifica el trabajo. Pero, ¿qué información se incluye en esa orden de trabajo?
Aprendiendo del pasado, los líderes de mantenimiento de MillerCoors ahora dicen que una orden de trabajo debe ser capaz de capturar el código de carga del equipo adecuado, todo el historial del equipo, el costo de mano de obra y materiales, y los requisitos de servicio del contrato. Para rastrear con precisión las fallas del equipo, se ingresa una descripción detallada del trabajo cuando se crea la orden y se ingresa una descripción precisa de lo que se hizo para corregir la falla al completar la orden de trabajo. Si no se hace esto, el historial de un equipo en particular se distorsiona y es posible que no represente con precisión las averías o fallas. Además, el número de equipo adecuado se ingresa en la orden de trabajo. Sin esto, las medidas vitales de seguimiento del historial, como el material utilizado y las horas de mano de obra cobradas, están vinculadas a la pieza incorrecta del equipo o faltan por completo.
"En el pasado, se tomaban malas decisiones porque no teníamos información precisa sobre las órdenes de trabajo", dice Davison.
Cuando se crea una orden de trabajo en MillerCoors, se toman notas para ayudar a identificar:
• cualquier pieza, habilidad o recursos externos necesarios para completar el trabajo;
• cualquier herramienta, equipo o recurso especializado potencialmente necesario; y,
• cualquier problema potencial de seguridad o medioambiental.
Con esta información inicial, el planificador obtiene las piezas y los materiales necesarios, reúne los recursos necesarios y planifica y programa el trabajo con precisión. Esto aumenta el tiempo de uso de la llave inglesa.
Cuando el trabajo está terminado, un artesano ingresa información detallada para cerrar correctamente la orden de trabajo. En el sistema de órdenes de trabajo SAP de la empresa, ingresa con precisión un código de causa, un código de falla y una parte del objeto en la parte del historial final de la notificación. Se documenta una descripción detallada de texto extenso del trabajo realizado junto con cualquier problema o discrepancia.
Pero todos esos pasos son inútiles si no usa la información.
El trabajo de mantenimiento es repetitivo. Lo que se aprende hoy sobre una máquina resulta útil cuando la misma máquina o una similar requiere mantenimiento en el futuro. Las historias identifican tendencias y ayudan a construir estrategias de confiabilidad efectivas.
"Si los datos no son precisos para ese equipo, no obtendrá la imagen completa y cometerá errores en el mantenimiento de ese equipo", dice Davison. "Si no está registrado en el sistema, no tiene ningún dato para analizar. Los planificadores lo necesitan para decidir cómo planificarlo la próxima vez, hacerlo mejor y utilizarlo para fines de raíz ”.
Con la información de la orden de trabajo ingresada correctamente, el personal de MillerCoors puede acceder a la orden de trabajo y al historial de costos de una pieza individual de equipo, departamento, centro de costos o instalación completa. Con estos datos, los planificadores determinan los porcentajes de finalización de MP, el tiempo de respuesta de la orden de trabajo, el tiempo medio de reparación y el tiempo medio entre fallas. También acceden a la combinación porcentual de órdenes de trabajo de PM, correctivas, de averías y de proyectos para un período de tiempo determinado. Estos informes les brindan las herramientas para ajustar las frecuencias de MP de acuerdo con las órdenes generadas y el MTBF.
“En algunos equipos, encontramos que nuestras frecuencias de PM eran demasiado altas”, dice McCall. “Nuestros planificadores analizan los PM de forma regular. Se aseguran de que esté en su lugar el PM correcto, con la frecuencia correcta. La idea es que el trabajo que planeamos es el trabajo que se debe realizar. Queremos utilizar mejor nuestro tiempo y dinero e ir tras lo correcto ".
Los gerentes de activos de CARE, Bobby McCall (izquierda) y Ron Kerr
discuten motores y cajas de cambios en la línea de envasado de la cervecería.
Golden Results
Las mejoras en la planificación y la destreza en la planificación han tenido un impacto en MillerCoors.
“Siempre hemos tenido grandes personas con el deseo de hacer las cosas correctas”, dice el ingeniero de planta Mike Fognani. "La planificación y la programación nos permiten combinar a esas excelentes personas con las herramientas, los materiales y el tiempo necesarios para tener éxito".
El trabajo planificado y programado en muchas áreas del sitio constituye ahora más del 60 por ciento de la carga de trabajo de mantenimiento; en el pasado reciente, esa cifra era menos del 30 por ciento.
El trabajo de PM completado ha aumentado dramáticamente. En el área de montacargas, por ejemplo, Simpkins dice que la tasa de finalización pasó del 31 por ciento al 82 por ciento en menos de 18 meses.
La disponibilidad, la productividad y el tiempo de actividad de los equipos han aumentado. Todo esto ha llevado a reducir los costos de mantenimiento.
“Solía ser 'el mantenimiento no puede mantenerlo en funcionamiento', 'no eres confiable' y 'estás gastando demasiado dinero'”, dice McCall. "Desde que nos estabilizamos y nos volvimos más proactivos, nuestros costos de mantenimiento se han reducido".
Todavía existen muchas oportunidades.
“En muchas áreas, estamos haciendo lo que tenemos que hacer y obteniendo los resultados que buscamos”, dice Roberts. “Estamos en el camino correcto, pero todavía no lo hemos logrado. Todavía tenemos focos de oportunidades con la planificación y la programación, y nos estamos enfocando en formas de hacer cambios importantes, incluso a raíz del gran trabajo que ya está en juego ”.
Costos reducidos. Mayor confiabilidad. Mejores decisiones. Mayor estabilidad.
MillerCoors puede haber encontrado una manera de hacer que la planificación sea sexy.
Solo el sitio de hechos :Plantas de MillerCoors en Golden, Colorado (incluye la cervecería y las áreas de apoyo a la producción relacionadas), y Rocky Mountain Metal Container y Rocky Mountain Bottle Company (dos plantas de empresas conjuntas).Empleo :Casi 2000 empleados en las plantas de fabricación de Golden.
Tamaño del sitio :Ubicado principalmente en un valle de cinco millas de largo en Golden.
Productos :Casi una docena de marcas de cerveza, incluidas Coors, Coors Light, Irish Red Lager de George Killian, Aspen Edge y Keystone. Además, bebidas de malta de la marca Zima.
Volumen de producción :Más de 20 millones de barriles de cerveza elaborados en Golden anualmente.
Mantenimiento y reparación de equipos
- Realice más trabajos de mantenimiento con una planificación adecuada
- Cómo lograr una planificación de mantenimiento eficaz
- Reuniones matutinas:planificación y programación de mantenimiento
- En mantenimiento, dos más dos pueden equivaler a ocho
- Planificación de mantenimiento:¿Qué beneficios ofrece?
- Trabajo en equipo, planificación y programación
- Tramos de control para planificadores de mantenimiento y otros
- Boeing acuerda mejorar los procesos de planificación de mantenimiento
- ¿Es mejor el mantenimiento preventivo o el predictivo?
- Por qué el mantenimiento proactivo es mejor que el mantenimiento preventivo
- Planificación de mantenimiento