Características importantes del laminado de alambrón
Características importantes del laminado de alambrón
Los alambrones normalmente se laminan en un tren de laminación de alta velocidad, donde la temperatura del acero es superior a 1000 °C, la velocidad máxima de laminación supera los 120 metros por segundo (m/s) y las bobinas de alambrón producidas pueden tener una longitud de hasta 10 kilómetros (km). . Durante la laminación de alambrón, generalmente se toman de 25 a 30 pasadas en un laminador continuo.
El alambrón es un material que tiene una aplicación muy amplia. Desde componentes para la industria automotriz, cuerdas para neumáticos, electrodos, elementos de conexión como tuercas y tornillos, resortes, alambres y productos de alambre, refuerzos de acero, etc., todo se basa en alambrón. Es por eso que el molino de alambrón normalmente se diseña teniendo en cuenta la versatilidad. Siendo el molino un molino intensivo en energía, se hace necesario que las soluciones óptimas se incorporen en el diseño del molino sin comprometer la flexibilidad. Todos los rangos de tamaño, materiales y aleaciones deben producirse de manera eficiente y con alta productividad en el laminador de alambrón.
Se requieren alambrones para cumplir con los requisitos de los usuarios de alambrón en cuanto a calidad superficial e interna, así como propiedades físicas, químicas, mecánicas y metalúrgicas. Los alambrones se someten a un procesamiento posterior, como estirado, forjado o mecanizado en las formas deseadas y tratamiento térmico para permitir que el producto alcance la resistencia deseada. Por lo tanto, se requiere que el alambrón sea capaz de garantizar un buen rendimiento de las piezas producidas donde sea que se utilice y, al mismo tiempo, que tenga una buena trabajabilidad en las diferentes etapas del procesamiento posterior.
El usuario de alambrón tiene tres requisitos básicos, a saber (i) eliminar o simplificar uno o más de los procesamientos secundarios o terciarios para mejorar la productividad y reducir los costos de procesamiento, (ii) mejorar la funcionalidad, es decir, extender la vida útil, para reducir el peso, o aportar otras ventajas al producto final para el que se utiliza el alambrón, y (iii) eliminar el uso de sustancias nocivas para el medio ambiente durante los procesos posteriores al procesamiento.
Para cumplir con los requisitos cada vez más rigurosos del consumidor, el laminador de alambrón debe tener las capacidades generales de los alambrones de laminación desde varios puntos de vista, a saber (i) mejorar la precisión dimensional, (ii) implementar laminación sin tamaño (es decir, laminación productos de diferentes tamaños sin cambiar los rollos), (iii) mejorar la productividad al acelerar el trabajo de cambio de rollos (reduciendo el tiempo de cambio de rollos) y (iv) mejorar la calidad de la superficie del producto al evitar la aparición de defectos superficiales durante el transporte en el proceso de laminado.
Se supone que el molino de alambrón no solo suministra los materiales, sino que debe suministrar alambrón para cumplir con los requisitos del largo procesamiento posterior al que se someten en los procesos secundario y terciario hasta que se producen los productos finales. Además, dado que los productos finales se utilizan en muchos casos como piezas vitales en varios campos industriales, existen requisitos para la racionalización de procesos en colaboraciones integradas con los clientes. Por lo tanto, el molino debe ser capaz no solo de cumplir con los requisitos de calidad de los usuarios, sino también de cumplir con sus requisitos de productividad, rendimiento, flexibilidad y costos de producción durante el procesamiento posterior. Un alto rendimiento del molino junto con la adecuada calidad del producto es de suma importancia para el control del costo de producción.
La capacidad de producción de un laminador de alambrón depende del volumen de producción de unos pocos productos estándar o de una combinación de productos diversificada que consta de alambrón con una gran cantidad de calidades de acero y calidades de productos especializados.
Un laminador de alambrón necesita básicamente (i) instalaciones de calentamiento para calentar el material inicial (palanquilla) a temperaturas de laminación, (ii) instalaciones de laminación que consisten en cajas de laminación con rodillos, calzos, guías y protecciones, (iii) tendido, tratamiento térmico y equipo de bobinado, y (iv) equipo de transporte y manejo. Todos los equipos deben trabajar en estrecha coordinación con un control de las temperaturas de laminación, la pérdida de tiempo de separación, la pérdida de velocidad, los adoquines, el producto no conforme y las desviaciones de calidad que conducen a la desviación o incluso al rechazo.
Requisitos de un laminador de alambrón moderno
Hay varios parámetros importantes (Fig. 1) para el laminado de alambrón en un laminador de alambrón. Un laminador de alambrón moderno generalmente está diseñado para trabajar con la filosofía de "efectividad general del equipo" (OEE). El valor OEE del molino es el valor obtenido al multiplicar la utilización del molino, la eficiencia del molino y el tiempo de rendimiento del molino. La utilización del molino es el tiempo operativo disponible dividido por el tiempo de producción planificado y expresado en porcentaje. La eficiencia del molino es el tiempo de funcionamiento dividido por el tiempo de funcionamiento disponible del molino y expresado en porcentaje. El tiempo de rendimiento del molino es el tiempo para producir el producto principal relacionado con el tiempo de ejecución. El rendimiento del producto se expresa como el peso de la bobina aceptada dividido por el peso de los tochos y expresado en porcentaje.
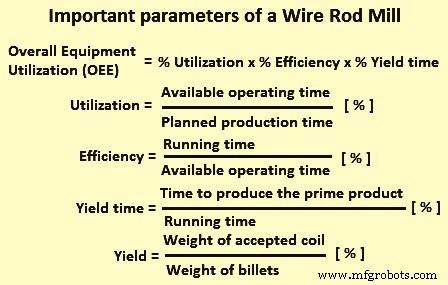
Fig. 1 Parámetros importantes de un molino de alambrón
Los laminadores de alambrón normalmente tienen un OEE más bajo que otros tipos de laminadores debido al mayor tiempo de inactividad para el cambio de rodillos y el cambio de soporte y los ajustes de ranura y guía durante el cambio de productos. El OEE del molino se puede mejorar si se puede reducir este tiempo de inactividad.
La capacidad de producción teórica de un molino es la capacidad que se puede obtener sin pérdidas, es decir, con un 100 % de utilización, un 100 % de eficiencia y un 100 % de rendimiento. Sin embargo, la capacidad real depende del nivel de OEE de la planta. Si el nivel de OEE de la planta es del 60 %, entonces la capacidad de producción de la planta es del 60 % de la capacidad teórica. El nivel de OEE en un laminador de alambrón de última generación con un laminador optimizado bien definido normalmente es del 80 %.
El costo de la mala calidad en la planta de alambrón generalmente se determina como la suma total del costo de inspección y los rechazos/desvíos de alambrón debido a defectos internos y externos. Para un molino de alto rendimiento, puede rondar el 10 %. Puede aumentar hasta un 30 % en un laminador de alambrón con una mezcla de productos diversificada que consta de alambrón con una gran cantidad de grados y calidades de producto especializadas.
En una planta moderna de alambrón, el enfoque principal está en la productividad y la calidad. La alta utilización, la eficiencia y el rendimiento dan una alta productividad. Pero la alta productividad en sí misma no es lo único para el éxito de una planta de alambrón. Tiene que producir productos que aporten valor a los clientes y estos obtengan alambrón de calidad digno de los pagos que están haciendo por el alambrón.
La productividad y la utilización del molino dependen del tiempo de inactividad en el molino causado por varias razones, incluido el diseño del molino y la combinación de productos. En la planta, el rendimiento desde la palanquilla hasta el producto final se registra en todos los pasos y el seguimiento del material en la planta hace un seguimiento de las pérdidas que se producen en la planta. Las categorías principales de las pérdidas que tienen lugar en el molino son (i) pérdidas de tiempo entre intervalos, (ii) pérdidas de velocidad, (iii) pérdidas debidas al canto rodado, (iv) pérdidas debidas a desviación de calidad, (v) pérdidas debidas al molino. tiempo de inactividad, (vi) pérdidas debidas al desvío/rechazo de alambrón durante la inspección en el lado de acabado de la planta, y pérdidas de tiempo debidas a operaciones de mejora del valor en el caso de la producción de productos de alambrón especializados.
Flexibilidad del molino
En un laminador de alambrón, el acero (palanquilla) se calienta por encima de su temperatura de recristalización y se pasa a través de varias ranuras de los cilindros en el laminador. Los diseños de paso de laminación comunes que se utilizan en las plantas de alambrón son diamante-cuadrado, diamante-diamante, paso de caja, cuadrado-óvalo, falso óvalo redondo y óvalo redondo. En los laminadores de alambrón, normalmente se realiza laminación sin tamaño, lo que significa que se pueden laminar alambrón de cualquier tamaño sin las limitaciones de los tamaños de paso de los rodillos que se encuentran en el laminador. Esto también se conoce como flexibilidad de la serie. Además, la simplificación del programa de paso de un tren de laminación anterior permite reducir sustancialmente la frecuencia del cambio de rodillos. Cuanto más amplio sea el rango del tamaño del producto que se puede enrollar con los mismos rollos (rango libre de tamaño), mayor será el efecto de la frecuencia reducida de cambio de rollo. El laminado libre de tamaño no se limita al tren de acabado. También se puede aplicar al molino de preacabado.
Para mejorar la productividad, hay un enfoque en minimizar el tiempo de inactividad del tren de alambrón. La efectividad de dicho enfoque generalmente se mejora al reducir el tiempo y la necesidad de cambiar los rodillos cuando se van a fabricar nuevas dimensiones finales y nuevos grados y formas de acero. Esto se consigue mejorando el rango de trabajo, también denominado flexibilidad de la serie. Se alcanza una flexibilidad mejorada cuando se lamina una gran cantidad de diferentes grados de acero, con diferentes formas y dimensiones con un cambio mínimo del programa de laminado. Cada grado de acero se caracteriza por su forma específica de flujo de material, como una distribución diferente, al pasar por el espacio entre rodillos. También es necesario reducir el tiempo de puesta en marcha y el tiempo de espera para la temperatura de laminación correcta, según el grado de acero real. Sin embargo, los diferentes ciclos de calentamiento todavía provocan tiempos de inactividad demasiado altos, cuando se debe laminar una amplia gama de grados. Para satisfacer las demandas del mercado actual, que incluyen lotes más pequeños y numerosos tipos de aceros, se ha convertido en una necesidad que las plantas modernas de alambrón muestren un alto grado de flexibilidad.
Un aspecto especial en un laminador de alambrón es el uso de un diseño de paso de rodillo flexible o ranuras flexibles con un rango de trabajo alto. Con el uso de secuencias flexibles de pases de rodillos, el laminado se puede realizar en las mismas ranuras para una amplia gama de productos acabados, simplemente cambiando la distancia de los rodillos. Por lo tanto, el cambio de ranura puede reemplazarse por un simple cambio de la separación entre cilindros y esto reduce el tiempo de inactividad para cambiar de un producto a otro. Existe una fuerte interdependencia entre la flexibilidad del diseño de paso de rodillos, la utilización del molino y el rendimiento.
Al adoptar un diseño de paso de rodillo flexible, se puede reducir una parte importante de las pérdidas en el molino. Un diseño de paso de rodillo flexible minimiza el riesgo de sobrellenado de ranuras y la creación de cantos rodados durante el cambio de grado de acero. Un diseño de paso de rollo flexible también tiene ventajas para el desarrollo de productos cuando existe la necesidad de introducir nuevos tamaños o grados de acero. Además, se puede lograr una mejora importante del tiempo de funcionamiento que aumenta el valor con un diseño de paso de rollo flexible.
Productividad del molino
El laminador de alambrón se puede combinar con un laminador de barras al tener una salida de lecho de enfriamiento antes del bloque de acabado. Esto normalmente se hace para utilizar la capacidad del laminador aguas arriba. Cuando se cambian los rodillos en el bloque de alambrón, el laminador anterior produce barras para reducir el tiempo de inactividad total del laminador.
Los laminadores de alambrón modernos son generalmente laminadores de un solo hilo. En el caso de un laminador de múltiples torones, se introduce un segundo laminador intermedio en cada uno de los torones para reducir la influencia del cambio en el número de laminados simultáneos en los torones. El segundo laminador intermedio puede tener la forma de un bloque de preacabado. También puede ser en forma de bloque de laminación de tres rodillos. La principal característica del laminador de tres rodillos es su capacidad para suprimir las variaciones de dimensión entre los tres rodillos ranurados que laminan toda la circunferencia de un material laminado y, por lo tanto, reducen la dispersión en comparación con un laminador convencional de dos alturas. Este molino intermedio se conoce como molino de encolado donde el conformado se realiza por medio de baja reducción. Esto ayuda a tener una filosofía de laminación familiar aguas arriba en el molino, lo que reduce el tiempo de reinicio.
Para aumentar la velocidad del molino y, por lo tanto, la productividad del molino, se instala un molino reductor/dimensionador (RSM) después de un bloque de acabado convencional. La integración de un RSM después del bloque de acabado convencional mejora sustancialmente la productividad del molino en tamaños pequeños (hasta en un 60 %). Su extrema precisión ha sido probada en muchas instalaciones. Además, en combinación con el laminado a muy baja temperatura, esto da como resultado una microestructura más refinada que puede eliminar procesos secundarios adicionales. El RSM proporciona mejoras tanto en la productividad como en la calidad del producto terminado, al mismo tiempo que reduce los costos operativos y aumenta la calidad del producto de alambrón. Admite un diseño de pasada de un solo rollo desde la caja 1 en el grupo de desbaste hasta la última caja del bloque de acabado. Dado que facilita un mismo diseño de paso unifamiliar, se puede mantener una alta eficiencia del molino sin tener en cuenta el tamaño del producto final.
Normalmente, las tensiones entre cajas se evitan en la medida de lo posible en el laminado del alambrón, ya que, de lo contrario, los extremos de cabeza y cola quedan fuera de tolerancia porque los extremos libres no pueden laminarse bajo tensión. Este hecho puede resultar en surcos sobrellenados y defectos en los extremos como aletas. Sin embargo, en el bloque sin giro de alta velocidad con transmisión fija, las tensiones entre soportes se utilizan para lograr condiciones de rodadura estables. Cuando se aplican tensiones entre soportes a la barra laminada, las ranuras se ajustan para dar la tolerancia requerida.
Calidad del alambrón
Los alambrones se están utilizando en varias aplicaciones. En muchas de las aplicaciones, los requisitos de calidad de los alambrones son muy estrictos. La calidad inferior de los alambrones aumenta los defectos/desviaciones de los productos finales y afecta negativamente los rendimientos por parte de los clientes, lo que genera insatisfacción en los clientes.
Dado que la laminación del alambrón es una laminación intensiva en energía, siempre es necesario que la laminación de bobinas de alambrón defectuosas se reduzca al mínimo. A veces, cuando el defecto en la palanquilla es bastante grande, puede incluso causar cantos rodados en el molino. Dado que la longitud del alambrón de una palanquilla es muy larga, el aseguramiento de la calidad en toda la longitud del alambrón después del laminado requiere tiempo y esfuerzo. Por esta razón, el control de calidad de los lingotes (el material de partida antes de la laminación) es de gran importancia. Los lingotes defectuosos deben identificarse, separarse y eliminarse mediante inspección de lingotes. Las palanquillas deben inspeccionarse tanto por los defectos superficiales como por los defectos internos. Los defectos menores de la superficie se pueden eliminar moliendo (acondicionando) la palanquilla.
Las características importantes exigidas en los alambrones (especialmente en los alambrones delgados) son la alta productividad en el trabajo secundario y la alta resistencia después del trefilado final. La alta productividad significa minimizar la rotura del alambre durante el trefilado y el agrupamiento o, idealmente, sin rotura, mayor trefilado directo y buena trefilado en condiciones severas de trefilado, como una alta velocidad de trefilado. Estos requisitos cada vez más sofisticados de los clientes aplican estándares estrictos a elementos de control de calidad como inclusiones no metálicas, segregación, descarburación, propiedades mecánicas y microestructura.
Normalmente, hay tres requisitos principales para las varillas de alambre para muchas aplicaciones. Estos son (i) mayor resistencia, (ii) eliminación o simplificación del procesamiento posterior y (iii) menor uso de sustancias nocivas para el medio ambiente. Se requiere una mayor resistencia del acero debido a la reducción de costos por parte del usuario y muchas otras razones. Dado que, en el extremo del usuario, los alambrones se someten a diferentes tipos de trabajo secundario, como forjado, trefilado y mecanizado, así como a tratamientos térmicos para recocido, templado, revenido,
etc., por lo tanto, los requisitos desde el punto de vista de la reducción de costos, el ahorro de energía y la conservación del medio ambiente instan encarecidamente a eliminar o simplificar el tratamiento térmico y el mecanizado (como el conformado casi neto o sin virutas).
El control de las inclusiones no metálicas, los precipitados, la transformación y la estructura metalográfica es una medida metalúrgica clave para mejorar las propiedades de los alambrones. El control de las inclusiones no metálicas es una de las principales técnicas iniciales para el aumento de la resistencia de los aceros para muelles, la prolongación de la vida útil de los aceros para cojinetes, la eliminación del plomo de los aceros de fácil mecanización, etc. Control de la estructura y forma de los óxidos y sulfuros es eficaz para lograr las propiedades deseadas de estos aceros.
En un laminador de alambrón, no hay concesiones cuando se trata de cumplir con las propiedades específicas del material de bobina con precisión. Aquí es donde el sistema de transportador de enfriamiento controlado (CCC) juega un papel clave. Es necesario controlar la alta calidad constante en toda la bobina de alambrón.
En este sentido, el sistema CCC juega un papel importante para el procesamiento de productos de alambrón de calidad, logrando la uniformidad deseada y las propiedades metalúrgicas y mecánicas. Controla estrictamente las variaciones de resistencia a la tracción alrededor del anillo en productos enfriados rápidamente a una desviación estándar dentro del 1 % de la resistencia a la tracción promedio.
El sistema CCC, mediante una selección adecuada del régimen de enfriamiento, se adapta a la producción de todos los grados convencionales de acero, así como a grados de productos especiales con modos de enfriamiento alternativos. También optimiza el procesamiento de grados de acero aleado y al carbono cuando se usa junto con el RSM para laminación a baja temperatura y enfriamiento controlado, lo que produce una muy buena combinación de propiedades y control dimensional.
El sistema CCC facilita el procesamiento en una amplia gama de condiciones, incluidos los modos de enfriamiento rápido y lento dentro de un solo sistema. Esta capacidad permite que el laminador de alambrón produzca una amplia gama de aceros al carbono y aleados simples, así como aceros inoxidables y otros grados especiales. El sistema CCC da como resultado mejores propiedades de alambrón laminado, lo que permite la producción de más grados en una condición utilizable directamente, y reduce o elimina los procesos posteriores, como el recocido esferoidizado.
La laminación termomecánica (TMR) en el tren de alambrón refina el tamaño de grano final como resultado de la recristalización dinámica. Combinado con el enfriamiento final por agua en línea y el enfriamiento superior controlado en el sistema CCC, TMR juega un papel importante en la determinación de las propiedades del producto final. Esto es particularmente beneficioso para los productos de acero de baja y media aleación que posteriormente se esferoidizan durante el procesamiento posterior. La capacidad de controlar fuertemente el tamaño del grano también influye en la transformación posterior a productos duros como la bainita y la martensita al cambiar el tiempo y la temperatura de inicio de la transformación. Por lo tanto, TMR puede minimizar el trabajo en frío directo aguas abajo y reducir los tiempos de recocido.
La combinación del procesamiento en el sistema CCC y las bajas temperaturas de laminación proporciona la capacidad de reducir la templabilidad en algunos grados críticos de alambrón. En última instancia, esto promueve la formación de ferrita y retarda la evolución a bainita y martensita. El tamaño de grano refinado logrado a través de TMR mejora la difusión durante el tratamiento térmico y puede resultar en tiempos y temperaturas de tratamiento térmico reducidos. Para aquellas varillas que no son tratadas térmicamente, las estructuras refinadas y complejas aumentan la resistencia a la tracción durante la deformación en frío, produciendo varias ventajas tales como (i) menor resistencia a la tracción en estado laminado, (ii) mejor respuesta aguas abajo y (iii) mayor trabajo templabilidad. Las mejoras provienen del refinamiento del grano y el control microestructural. El buen control del proceso de enfriamiento en el sistema CCC combinado con la templabilidad reducida de los alambrones hace que el proceso sea muy estable y reduce la posibilidad de formar fases duras no deseadas.
Proceso de manufactura
- Rodillo
- Tiara
- Alambre de púas
- Robot de alarma rodante
- MOSMusic
- Dobladora de alambre 3D Arduino
- Principales características de un moderno tren de laminación de barras y perfiles ligeros
- Características principales de un molino de alambrón moderno
- Características principales de un moderno laminador de bandas en caliente
- Proceso de laminado para acero
- Laminación en frío de aceros