Insensibilidad efectiva de la resina de melamina urea-formaldehído mediante polimerización interfacial en explosivos de nitramina
Resumen
Para mejorar la seguridad de los explosivos de nitrato de amonio, se seleccionó la resina de melamina urea-formaldehído (resina MUF) para la preparación de tres explosivos de nitramina típicos (ciclotetrametilentetranitramina, HMX; criclotrimetilentrinitramina, RDX; y polímero verde a base de hexanitrohexaazaisowurtzitane, CL-20). explosivos adheridos (GPBX) mediante polimerización interfacial. Mientras tanto, se estudiaron y compararon las correspondientes partículas compuestas preparadas mediante métodos de mezclado físico y baño de secado. La morfología de las partículas, la estructura cristalina, la estabilidad térmica y el rendimiento de seguridad de las partículas compuestas resultantes se caracterizaron mediante microscopía electrónica de barrido (SEM), difracción de rayos X en polvo (XRD), espectros de infrarrojos por transformada de Fourier (FT-IR), calorímetro de barrido diferencial (DSC) y prueba de sensibilidad al impacto, respectivamente. Los resultados de SEM mostraron que MUF se recubrió con éxito en la superficie de los tres explosivos, y diferentes partículas compuestas preparadas por el mismo método tienen sus propias características únicas. Este efecto se atribuye a la capacidad de la resina para aislar y amortiguar los estímulos externos. Es obvio que la polimerización interfacial es una técnica de desensibilización eficaz para preparar partículas compuestas núcleo-capa para explosivos.
Antecedentes
A medida que la tecnología y los sistemas de armas continúan evolucionando, se requiere munición no solo para tener alta precisión, alta potencia y largo alcance para el sistema de potencia de fuego de armas, sino también para mantener una seguridad relativamente alta en otros entornos. Sin embargo, explosivos convencionales como hexahidro-1,3,5-trinitro-1,3,5-trizina (RDX), 1,3,5,7-teranitro-1,3,5,7-tetrazocano (HMX) y 2,4,6,8,10,12-hexanitro-2,4,6,8,10,12-hexaazaiso-wurtzitane (CL-20) son difíciles de cumplir con estos requisitos (estructuras moleculares que se muestran en la Fig.1), y el desarrollo de explosivos de alta potencia insensibles (IHE) se considera una forma deseable de satisfacer la aplicación de sistemas de armas [1, 2, 3]. Muchos estudiosos nacionales y extranjeros están interesados en la desensibilización de explosivos de nitramina, por lo general utilizando técnicas de refinamiento [4, 5], recubrimiento [6, 7] y eutécticas [8, 9] para lograr el propósito de reducir la sensibilidad. La tecnología de recubrimiento para materiales energéticos es un método para envolver el modificador en la superficie del polvo mediante un determinado proceso para lograr el propósito de insensibilidad, que incluye principalmente recubrimiento físico y recubrimiento químico. El recubrimiento físico se refiere principalmente a la formación de una determinada capa de recubrimiento en la superficie de partículas sólidas explosivas por adsorción o fuerza externa. Y los métodos de recubrimiento físico comunes incluyen el método de suspensión en agua [10], el método de recubrimiento por cristalización [11], el método de secado por atomización [12], el método supercrítico [13] y el método de separación de fases [14]. El método de revestimiento químico se refiere a formar una capa de revestimiento sobre la superficie de partículas sólidas mediante metátesis, reacción de polimerización, tratamiento de alta energía o similar en un medio determinado. Es bien sabido que los indicadores clave para la evaluación de un material núcleo-caparazón son el grado de cobertura, la resistencia mecánica y la inhibición de la autonucleación de la capa de recubrimiento [15]. Por lo tanto, explorar nuevas técnicas de recubrimiento y encontrar nuevos materiales de recubrimiento son formas efectivas de garantizar que los explosivos posean una buena estructura núcleo-carcasa y cumplan con los requisitos de seguridad. Nuestra investigación se basa en los dos métodos de recubrimiento descritos anteriormente.

Estructura molecular de RDX, HMX, CL-20 y MUF Binder. R-CH2OH es MF
Durante décadas, los aglutinantes de "trialdehído" convencionales han sido el foco de investigación de los académicos nacionales y extranjeros. Con la mejora continua del rendimiento integral, han comenzado a aparecer informes relevantes sobre sus aplicaciones en el campo de los materiales energéticos. En 2015, Yang et al. [16] utilizó un 3% de monómero de resina de melamina-formaldehído (MF) para recubrir CL-20, HMX y RDX. Las partículas preparadas tenían una capa de revestimiento de resina MF compacta y uniforme, y su estabilidad térmica y propiedades de seguridad se mejoran en gran medida. Este artículo tiene similitudes con ese informe porque también hemos descubierto que la resina de melamina-urea-formaldehído es más adecuada como material aglutinante explosivo, en comparación con la resina de melamina-formaldehído. La resina MF tiene un rendimiento excelente; sin embargo, es frágil y costoso. Lo más importante es que el producto de resina MF no se puede almacenar durante mucho tiempo. Si se utiliza como material de revestimiento para fabricar partículas compuestas energéticas con una estructura de núcleo-carcasa, es probable que se deterioren las propiedades de las partículas. Li et al [17] prepararon ciclotetrametilentetranitramina en microesferas energéticas de elastómero termoplástico de poliéster-éter (HMX @ TPEE) con una distribución del tamaño de partícula de 50 a 200 μm mediante un método de evaporación del solvente en emulsión (ESV), y las partículas resultantes tenían menor sensibilidad y mayor estabilidad térmica. En este artículo, se propuso un método de baño de secado mejorado y se prepararon los explosivos ligados con polímeros (PBX) con excelente rendimiento integral utilizando resina de melamina urea-formaldehído (resina MUF) como material de la carcasa y tres explosivos diferentes como material del núcleo. . Wang y col. [18] obtuvo nanocompuestos de ciclotetrametilentetranitramina / nitrocelulosa (HMX / NC) de 30 nm con una buena propiedad integral mediante un método supercrítico de sol-gel mejorado. Puede verse que la elección del aglutinante tiene una gran influencia en la morfología, el tamaño de partícula y el rendimiento de las PBX resultantes.
Como todos sabemos, la asistencia ultrasónica se ha aplicado ampliamente a la síntesis química y la modificación de materiales funcionales [19, 20]. En nuestro estudio, se preparó un aglutinante MUF verde con un rendimiento general superior mediante un método de síntesis de dos pasos. A continuación, se utilizó el aglutinante MUF preparado como material de cubierta, y HMX, RDX y CL-20 como materiales de núcleo, respectivamente. En primer lugar, utilizando un método de mezcla física simple, se fabricaron tres explosivos / partículas MUF diferentes (con un contenido de MUF del 5%) mediante asistencia ultrasónica. Posteriormente, en las mismas condiciones, las otras seis partículas energéticas compuestas se prepararon utilizando un método de baño de secado mejorado y un método de polimerización interfacial optimizado, respectivamente. En resumen, por primera vez, se fabricaron nueve partículas energéticas compuestas diferentes con la misma proporción de MUF mediante asistencia ultrasónica mediante los tres métodos diferentes. Curiosamente, a través de diferentes métodos, obtuvimos PBX con diferentes morfologías, como formas aparentes expuestas a partículas (mezcla física), poligonales irregulares (método de baño de secado) y núcleo-capa densa (polimerización interfacial). Sorprendentemente, a medida que aumentó la apariencia estética de la morfología de las partículas, mejoraron su estabilidad térmica y su rendimiento de seguridad. A través de la investigación y el análisis, las partículas energéticas compuestas preparadas por polimerización interfacial son óptimas en morfología, estabilidad térmica y rendimiento de seguridad. Por lo tanto, para obtener partículas energéticas compuestas con el mejor rendimiento integral, se prefiere considerar el método de polimerización interfacial para preparar GPBX después de determinar el aglutinante utilizado.
Métodos
Materiales
HMX, RDX y CL-20 fueron proporcionados por Gansu Yinguang Chemical Industry Group Co. En nuestro estudio, las materias primas se seleccionaron en un proceso de baño de secado. Al preparar compuestos explosivos / MUF mediante métodos de mezcla física y polimerización interfacial, las materias primas se recristalizaron de acuerdo con la referencia [21]. El dimetilsulfóxido se obtuvo de Tianjin Fuchen Chemical Reagent Factory. Tween 80 y Span 80 se mezclaron como emulsionante compuesto para explosivos con M Tween 80 :M Span80 de 0,57:0,43. La trietanolamina (TEOA, utilizada para ajustar el valor de pH durante la reacción) era de Tianjin Sailboat Chemical Reagent Technology Co., Ltd. Urea, formaldehído, ácido clorhídrico (se usó ácido clorhídrico diluido al 5% para ajustar el valor de pH en el presente estudio) , y resorcinol (R-80) fueron proporcionados por Tianjin Tianli Chemical Reagent Co., Ltd. El cloruro de amonio se compró a Tianjin Guangfu Technology Development Co., Ltd. El alcohol polivinílico 2488 (PVA) fue suministrado por Qingdao Yousuo Chemical Technology Co., Ltd. El agua pura se obtuvo del suministro de agua pura de Taiyuan Iron and Steel Co., Ltd.
Síntesis de dos pasos de resina MUF
El aglutinante MUF con excelentes propiedades integrales se preparó mediante un proceso de dos pasos. En primer lugar, preparación del prepolímero de resina de urea-formaldehído. Se mezclaron 0,62 g de urea y 1,87 g de solución de formaldehído (la concentración es del 37%) y luego la urea se disolvió suficientemente con un agitador magnético. El valor de pH de la mezcla se ajustó a 8,5 ~ 9,5 con trietanolamina. La solución se colocó en un baño de agua a 65ºC y se agitó durante 1 h hasta que se obtuvo un prepolímero de resina de urea-formaldehído transparente y viscoso. Después de enfriar, se añadió gota a gota HCl hasta que el valor de pH de la solución se ajustó a aproximadamente 3,5 y se dejó a un lado. En segundo lugar, preparación de MUF. Se añadieron 1,87 g de prepolímero a 35 ml de agua desionizada para formar una emulsión con agitación uniforme. Posteriormente, se añadieron sucesivamente PVA al 8%, 0,01 g de melamina, 0,125 g de resorcinol y 0,06 g de cloruro de amonio y se ajustó el valor de pH a aproximadamente 3,5 con ácido clorhídrico diluido. Luego, el matraz de tres bocas se colocó en el baño de agua a 65 ° C y se hizo reaccionar durante 3 ~ 4 h, seguido de un enfriamiento natural en reposo y una filtración al vacío. La solución se lavó con agua desionizada, proporcionando finalmente resina MUF de alta calidad. Después del secado, se pesaron aproximadamente 0,3 g de MUF.
Preparación de partículas compuestas explosivas / MUF por polimerización interfacial y métodos de baño de secado
La preparación de partículas compuestas explosivas / MUF mediante métodos de baño de secado y polimerización interfacial es completamente consistente con la preparación del prepolímero de resina de urea-formaldehído en la síntesis de dos pasos del aglutinante MUF. Sin embargo, el segundo paso es obviamente diferente.
En la fabricación de partículas de material compuesto explosivo / MUF mediante polimerización interfacial, se añadieron 6 g de explosivos a 35 ml de agua desionizada y se añadieron gota a gota 0,01 g de span-80 como emulsionante. Posteriormente, el sistema se emulsionó y se cortó a una velocidad de 7000 rad / min durante 30 min hasta que se formó una emulsión explosiva estable. La emulsión explosiva reemplazó el agua desionizada en la síntesis de dos pasos de resina MUF. El diagrama de síntesis se muestra en B en la Fig. 2 a continuación.
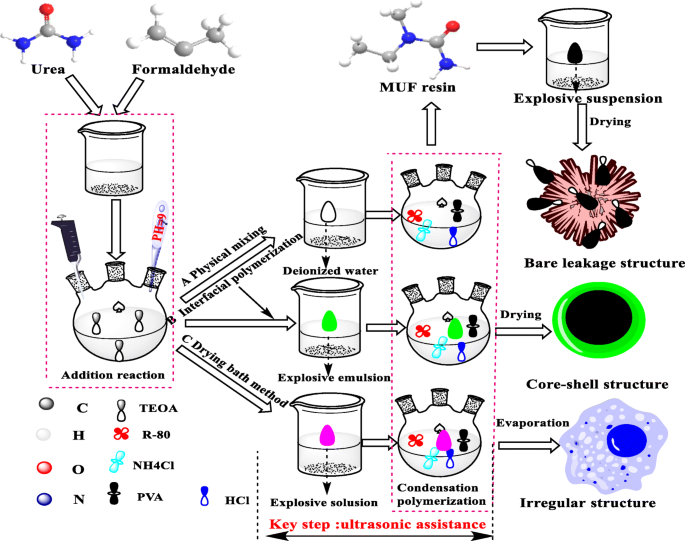
Diagrama esquemático de diferentes métodos para preparar HMX / MUF, RDX / MUF y CL-20 / MUF
En la preparación de partículas de material compuesto explosivo / MUF mediante el método del baño de secado, se disolvieron 6 g de explosivo en 35 ml de DMSO a 65 ° C para formar una solución explosiva. La solución explosiva reemplazó el agua desionizada en la síntesis de dos pasos de resina MUF. Después de 3 a 4 h de reacción, se formó una mezcla lechosa estable explosivo / MUF. Luego, la emulsión se colocó en un horno y se secó a 70 ° C durante 48 h, obteniendo finalmente partículas compuestas explosivas / MUF. El diagrama de síntesis se muestra en C en la Fig. 2 a continuación (baño de secado). Cabe señalar que después de la adición de la emulsión explosiva, se debe realizar una asistencia ultrasónica para evitar la aglomeración del aglomerante y el explosivo.
Preparación de partículas compuestas explosivas / MUF mediante mezcla física
Para comparar con las partículas explosivas / MUF preparadas por los dos primeros métodos, también preparamos partículas explosivas / MUF utilizando un método de mezcla físico simple. El aglutinante MUF, preparado mediante la síntesis de dos pasos, se mezcló con 6 g de explosivo en 35 ml de agua desionizada, y luego, la solución mixta se agitó en el baño de agua a 65 ° C durante 2 h. Después de eso, la mezcla se dejó reposar, seguido de filtración y secado; Se obtuvieron partículas compuestas explosivas / MUF. El esquema de preparación se muestra en A en la Fig. 2 (Mezcla física).
Etiquetamos las muestras preparadas mediante el método de polimerización interfacial, el método del baño de secado y el método de mezcla física, como muestra 1, muestra 2 y muestra 3, respectivamente.
Caracterización
Se tomaron imágenes de microscopía electrónica de barrido por emisión de campo (FESEM) en un MIRA3 LMH SEM (Tescan) a 10 k; Los patrones de difracción de rayos X (XRD) se obtuvieron utilizando un difractómetro de rayos X DX-2700 (Dandong Haoyuan Corporation, Liao ning, China) con radiación de Cu-Kα (40 kV, 30 mA) a λ =1,5418 Å. Todas las muestras se escanearon de 5 ° a 50 ° con pasos de 0,03 y tiempo de recuento de 6 s; Los espectros de infrarrojos de transformada de Fourier (FT-IR) se caracterizaron por un Nicolet FT-IR 8700 Thermo (Waltham, MA, EE. UU.) Con una resolución de número de onda de 4 cm −1 y un solo promedio de 32 exploraciones a temperatura numérica; El análisis térmico se realizó en un calorímetro de barrido diferencial (DSC-131, France Setaram Corporation, Shanghai, China) a una velocidad de calentamiento de 10 ° C / min. El aparato de martillo de caída; la altura especial ( H 50 ) representa la altura a partir de la cual 2.500 ± 0.002 kg de martillo de caída dará lugar a un evento explosivo en el 50% de las pruebas. En cada determinación, se realizaron 25 pruebas de caída para calcular la H 50 . Y la masa de la muestra es de 30 mg. La sensibilidad a la fricción de las muestras se probó con un instrumento de fricción WM-1. En cada determinación, se analizaron 25 muestras y una probabilidad de explosión ( P , %) fue obtenido. Y la masa de la muestra es de 20 mg. El tamaño de partícula probado por el analizador dinámico de partículas QICPIC (SYMPATEC Co., Ltd., Alemania) y su entorno de trabajo es de 5 ~ 35 ° C; la humedad relativa es inferior al 85%; el tipo de fuente de luz es láser He-Ne; la potencia es de 2,0 mW; y la longitud de onda es de 0,6328 μm.
Resultados y discusión
Morfología de las muestras
La morfología y estructura de RDX, HMX y CL-20 sin procesar; el aglutinante MUF sintetizado (Archivo adicional 1:Sección S1); y se midieron las partículas compuestas explosivas / MUF preparadas por los tres métodos, respectivamente. La imagen SEM muestra que los explosivos de nitramina en bruto exhiben una forma poligonal y una distribución de tamaño desigual. La apariencia del aglutinante MUF original es esférica; sin embargo, se puede ver claramente que las partículas no están llenas porque su interior puede estar vacío o parcialmente agua.
En comparación con los explosivos sin revestimiento (Figs. 3a, 4a y 5a), la morfología de las partículas compuestas de explosivo / MUF preparadas por diferentes métodos es bastante diferente, mientras que la morfología de las diferentes partículas compuestas de explosivo / MUF preparadas por el mismo método tiene características similares . Las partículas compuestas preparadas por el método de mezcla física tienen un fenómeno de exposición de partículas obvio, mostrando un efecto de recubrimiento pobre (Fig. 3d, 4d y 5d). Esto se debe a que es difícil distribuir el aglutinante uniformemente sobre la superficie del explosivo solo por acción mecánica. El proceso de dispersión de la agitación mecánica solo es reversible. Después de la colisión, las gotas se agregarán nuevamente, logrando finalmente un equilibrio dinámico que mantiene una cierta granularidad. La unión mutua incontrolable ocurre durante la colisión de gotas, que está fuera de control.
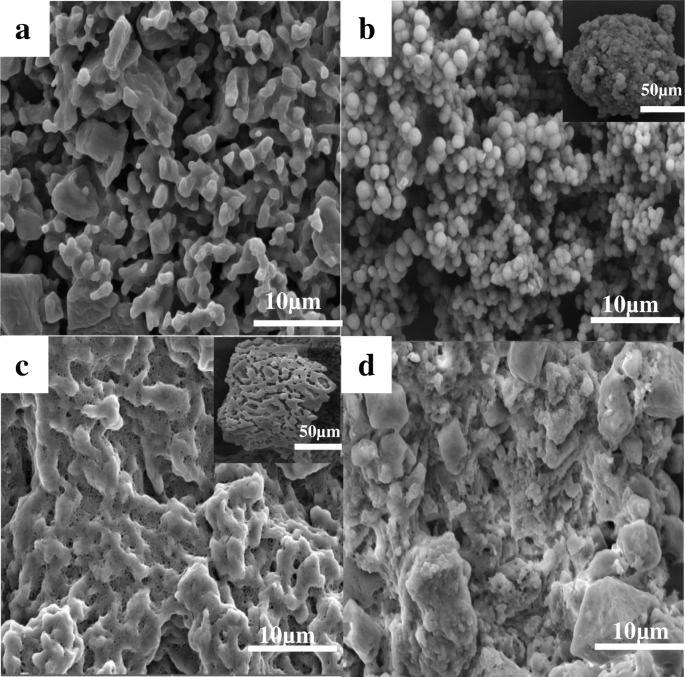
Imágenes SEM del HMX sin recubrimiento ( a ), HMX / MUF-1 ( b ), HMX / MUF-2 ( c ) y HMX / MUF-3 ( d ); se insertan las imágenes correspondientes con poca ampliación
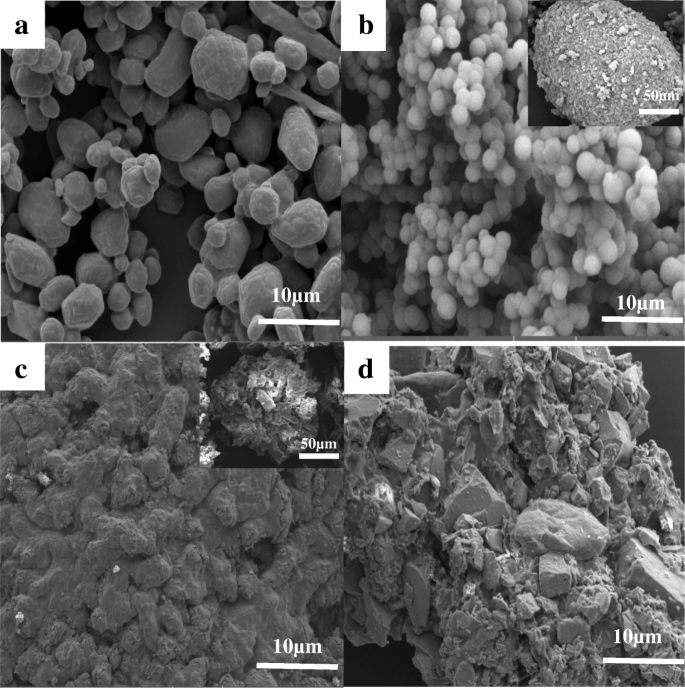
Imágenes SEM del RDX sin recubrimiento ( a ), RDX / MUF-1 ( b ), RDX / MUF-2 ( c ) y RDX / MUF-3 ( d ); se insertan las imágenes correspondientes con poca ampliación
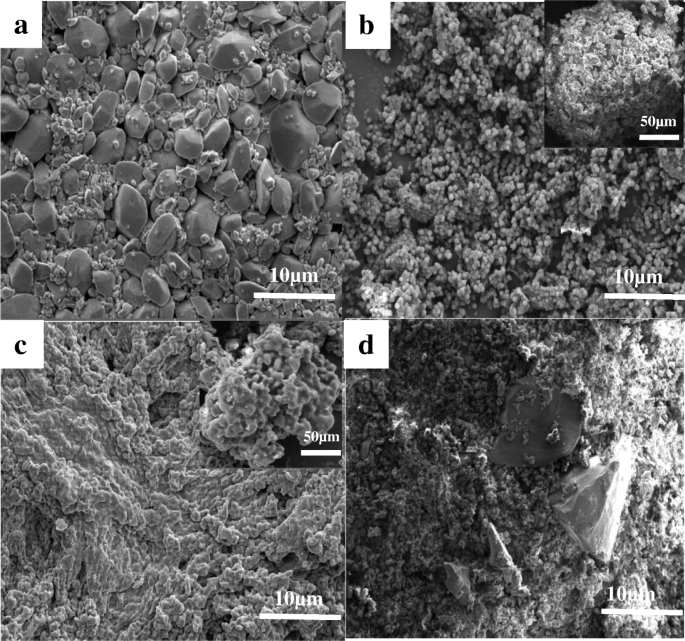
Imágenes SEM del CL-20 sin recubrimiento ( a ), CL-20 / MUF-1 ( b ), CL-20 / MUF-2 ( c ) y CL-20 / MUF-3 ( d ); se insertan las imágenes correspondientes con poca ampliación
Las partículas de material compuesto preparadas mediante el método del baño de secado tienen capas de revestimiento claramente densas. Sorprendentemente, después de que MUF encapsula completamente las partículas explosivas, es difícil formar una esfera completa, la mayoría de las cuales aparecen como partículas densas pero irregulares (como se muestra en las figuras 3c, 4c y 5c). Y este fenómeno puede explicarse mediante la teoría básica de la química de la interfaz [22]. Durante el proceso de eliminación del solvente, la viscosidad del explosivo / MUF aumenta gradualmente a medida que el solvente se evapora y las partículas dispersas tienden a reagruparse. Por otro lado, dado que la solubilidad del dispersante PVA en DMSO es pequeña, cuando los aglutinantes MUF chocan entre sí, no existe una buena fuerza de dispersión, lo que hace que se peguen entre sí, eventualmente formando una forma irregular. Además, la teoría del crecimiento de cristales [23] también puede servir como un poderoso apoyo para explicar esta morfología irregular. El método del baño de secado hace que el explosivo experimente un proceso de crecimiento y desarrollo del “cristal embrión-núcleo-cristal”. Dado que el sistema MUF está en una fase fluida metaestable y el sistema contiene una variedad de superficies externas, las partículas explosivas disueltas se nuclean en estas superficies, lo que puede reducir la barrera de nucleación causada por el aumento de la energía superficial de MUF y disminuir efectivamente la energía superficial. barrera durante la nucleación de explosivos. La nucleación explosiva se forma preferentemente en esta irregularidad, es decir, la nucleación no uniforme también es una causa de morfología irregular de partículas. En la ilustración de la Fig. 3d, podemos ver que la morfología general de las partículas de HMX / MUF es "panal", que está relacionada con la menor energía de enlace entre MUF y HMX (Archivo adicional 1:Sección S2). A medida que avanza la evaporación, el aglutinante MUF se encogerá gradualmente. Una energía de unión demasiado baja entre ellos hace que MUF sea incapaz de encapsular completamente HMX, y genera una fuerte tensión interna, que eventualmente forma la forma de "panal" [24].
Lo más interesante es que las partículas de material compuesto explosivo / MUF preparadas por el método de polimerización interfacial poseen todas una estructura esferoidizada, y la superficie de las partículas resultantes es densa y lisa (como se muestra en las Figuras 3b, 4b y 5b). Probablemente esto se deba a que la adición del dispersante PVA disminuye la tensión superficial del agua y mejora la humectabilidad, aumentando así la afinidad entre las moléculas explosivas y la solución aglutinante. La constante de Hamaker disminuye simultáneamente y la energía de atracción entre partículas se reduce, formando un impedimento estérico eficaz. Más importante aún, la energía repulsiva entre las partículas compuestas aumenta, lo que mejora enormemente la dispersabilidad entre el explosivo / MUF [25]. Como se muestra en el inserto de las Figs. 4b y 5b, numerosas partículas compuestas RDX / MUF y CL-20 / MUF exhiben una morfología esférica súper sólida, con superficies densas y lisas. Sorprendentemente, la morfología de las partículas HMX / MUF mostradas en la Fig. 3b también es esférica, pero no tan completa como las partículas compuestas RDX / MUF y CL-20 / MUF, atribuyéndose a la energía de unión mínima entre HMX y MUF. Una energía de unión demasiado baja hace que el sistema mixto sea demasiado estable, lo que da como resultado una tendencia obvia a que la superficie MUF se contraiga automáticamente. Por lo tanto, aunque las partículas de HMX / MUF tienen tendencia a ser esferoidizadas, no están llenas.
Estructura cristalina de las muestras
Para investigar si ocurrió la transformación de fase de HMX y CL-20, se emplea el análisis XRD, y los resultados se muestran en la Fig. 6. A través del análisis, se puede ver si la estructura cristalina ha cambiado durante la preparación del explosivo / MUF partículas compuestas. Más importante aún, el análisis de difracción de rayos X confirmó desde el lado que MUF se cubrió con éxito en la superficie del explosivo. De la Fig. 6a, HMX / MUF-1, HMX / MUF-2 y HMX / MUF-3 contienen casi todos los picos de difracción del HMX sin procesar. Y fenómenos similares también aparecen en los patrones de difracción de las partículas compuestas RDX y CL-20, como se muestra en la Fig. 6c, e. Esto indica que la estructura cristalina del explosivo no cambia durante toda la preparación del MUF / explosivo mediante la mezcla física, el baño de secado y los métodos de polimerización interfacial. Además, hemos notado un fenómeno similar entre las tres partículas compuestas explosivas / MUF, es decir, los picos de difracción principales de las partículas compuestas explosivas / MUF se debilitan y ensanchan en comparación con las materias primas. Por ejemplo, en los patrones de difracción HMX / MUF, RDX / MUF y CL-20 / MUF, la difracción principal alcanza un pico de 2 θ =16,39 °, 12,58 ° y 13,29 ° muestran el fenómeno de debilitamiento y ensanchamiento más obvio. Esto puede atribuirse a las propiedades físicas "isotrópicas" de la MUF amorfa, lo que da como resultado una disposición irregular de las partículas explosivas / MUF resultantes en la distribución espacial. Esta disposición periódica debilita la intensidad de difracción del explosivo [26]. Más importante aún, el pico de difracción de MUF también está presente en el pico de difracción de las partículas compuestas explosivas / MUF. Por ejemplo, en los patrones de difracción HMX / MUF, RDX / MUF y CL-20 / MUF, los picos de difracción son 2 θ =26,71 °, 26,78 ° y 26,99 ° son mucho más altos que el pico de difracción en la misma posición de las materias primas. Obviamente, esto se debe a que el pico de difracción alrededor de 2 θ =27 ° es uno de los picos característicos de difracción más dominantes de MUF. Dado que el contenido de MUF representa solo el 5% del explosivo, los picos de difracción discretos presentes en la propia MUF son menos pronunciados en las partículas compuestas. Como se muestra en la vista ampliada del pico de difracción insertado en cada imagen, en comparación con los explosivos originales, aparecen nuevos picos de difracción en las tres partículas explosivas compuestas, como en 2 θ =41,30 ° en el patrón de difracción de muestra HMX, 2 θ =39,45 ° en el patrón de difracción de muestra RDX y 2 θ =35,93 ° en el patrón de difracción de la muestra CL-20, lo que confirma efectivamente la existencia de aglutinante MUF en las partículas compuestas explosivas / MUF.
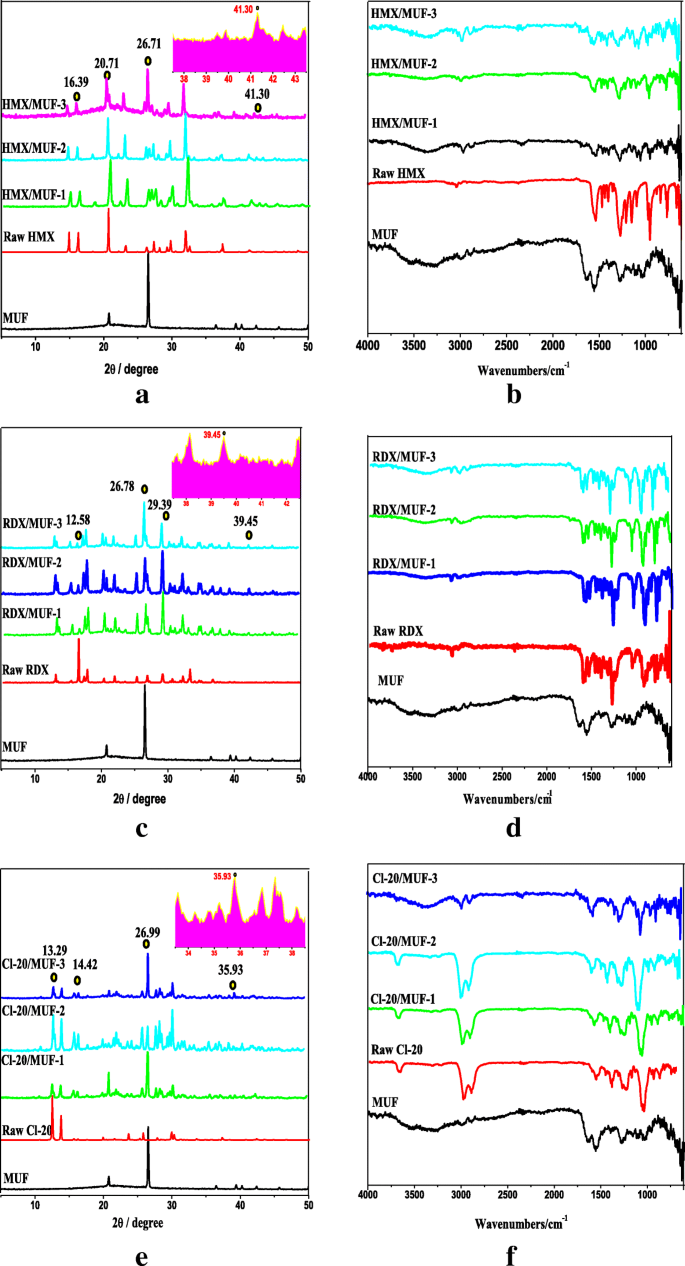
un - f Muestras de espectro XRD y FI-IR
Se realizó un análisis FI-IR para identificar la estructura molecular de las muestras. En general, las partículas compuestas preparadas mediante las tres técnicas diferentes contienen casi todos los picos de vibración de estiramiento del aglutinante y el explosivo. Los resultados de la medición confirmaron desde el lado que la resina MUF formó con éxito una capa protectora en la superficie del explosivo, correspondiente a los resultados de la prueba XRD. Es bien sabido que HMX tiene cuatro estructuras cristalinas diferentes, tres fases cristalinas puras (α-HMX, β-HMX y δ-HMX) y una fase hidrato (γ-HMX). Y el β-HMX se considera generalmente como la fase más estable con alta energía explosiva, gran densidad y baja sensibilidad, lo que por supuesto está relacionado con la estructura espacial de su monoclínico P21 / c [27]. En el espectro infrarrojo de MUF, hay un pico de absorción de vibración de estiramiento –C =O a 1735 cm −1 . Mientras que en el espectro infrarrojo de HMX, –NO 2 y –CH 2 los picos de absorción de vibraciones de estiramiento aparecen cerca de 1560 cm −1 y 2980 cm −1 , respectivamente (como se muestra en la Fig. 3b). Se puede notar que aparecen picos de absorción de vibración de estiramiento similares en las posiciones correspondientes en la banda característica de HMX / MUF, lo que significa que la estructura cristalina de HMX no cambiará durante la preparación mediante la mezcla física, el baño de secado y los métodos de polimerización interfacial. . Además, también se encuentra una situación similar en el espectro infrarrojo de las partículas CL-20 (Fig. 6f), especialmente el pico de vibración de estiramiento de las partículas CL-20 en la región de huellas dactilares 760 cm −1 demuestra que la estructura cristalina de Ɛ-CL-20 no cambió durante todo el experimento [28].
Propiedades térmicas
Sondear el proceso de descomposición térmica es muy importante para los materiales energéticos [29]. En nuestra investigación, las curvas de DSC recolectadas a una velocidad de calentamiento de 10 ° C / min se obtienen en la Fig. 7. Hemos encontrado algunos fenómenos interesantes sobre la descomposición térmica de estos tres explosivos de nitramina. En general, HMX y CL-20 tienen características de descomposición térmica similares (hay un pico endotérmico de transformación cristalina durante la descomposición térmica); sin embargo, el fenómeno de autocalentamiento de CL-20 es más serio que el de HMX. Esto se debe al hecho de que, como explosivo de nitrato de amonio tipo jaula, la escisión del esqueleto molecular y la "reacción de fase condensada heterogénea" de la fase condensada existen simultáneamente y se exacerban, mientras que el HMX es un tipo de "fusión-descomposición" material, y su proceso de fusión se ve afectado por el proceso de descomposición térmica. En la práctica, HMX y RDX también tienen comportamientos térmicos similares, porque ambos tienen las mismas cadenas ramificadas. La diferencia es que HMX libera calor rápidamente durante la descomposición térmica y su curva DSC muestra un pico pronunciado y pronunciado (Fig. 7a). Porque la descomposición de HMX es un proceso heterogéneo donde la reacción sólido-líquido procede simultáneamente, mientras que la descomposición de RDX es un proceso homogéneo en el estado fundido después de completar la fusión. La reacción acelerada causada por el cambio de fase simultáneo durante la descomposición hace que la descomposición de HMX sea más severa que la de RDX [30].
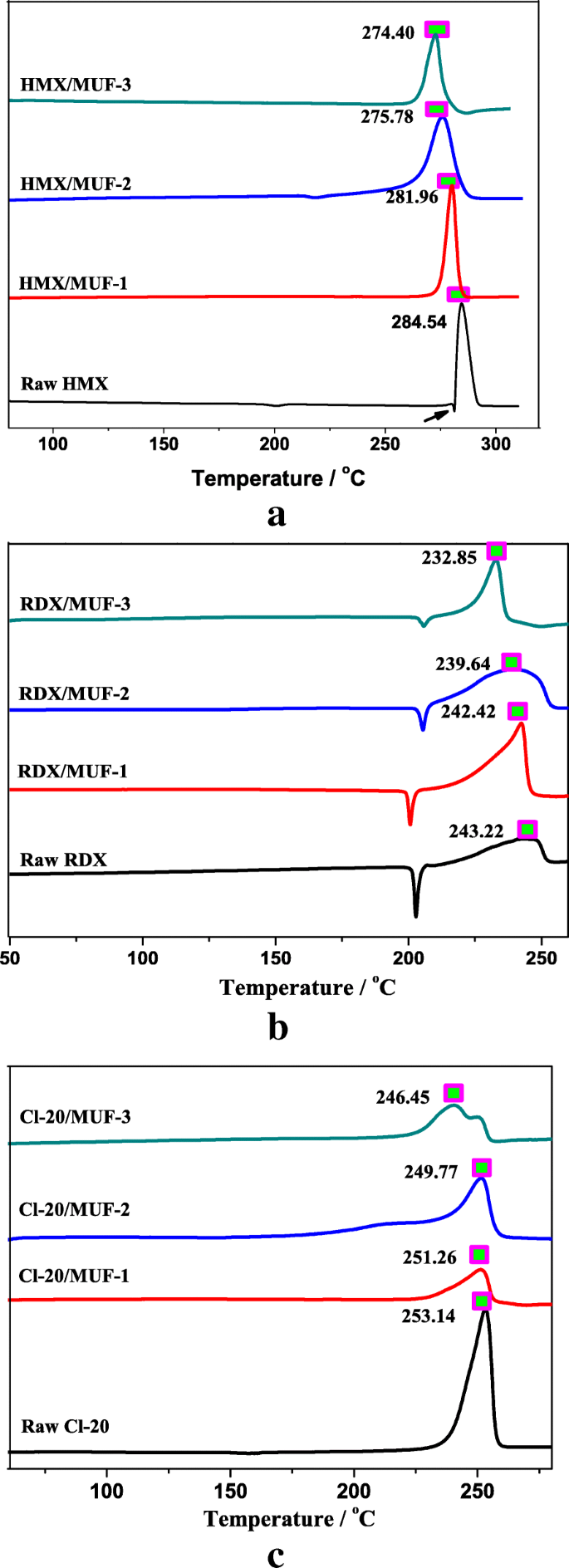
un - c Curvas DSC de muestras recolectadas a una velocidad de calentamiento de 10 ° C / min
Para HMX, la curva DSC muestra un pico endotérmico a 279,2 ° C, posteriormente un pico exotérmico a 284,54 ° C (Fig. 7a), atribuyéndose a la transición de fase de fusión y al pico característico de la descomposición térmica de HMX, respectivamente [31] . En comparación con el HMX sin procesar, las temperaturas de descomposición térmica de HMX / MUF-1, HMX / MUF-2 y HMX / MUF-3 disminuyeron. Y la temperatura de las partículas compuestas preparadas mediante polimerización interfacial, baño de secado y métodos de mezcla física se redujo en 2,58 ° C, 8,76 ° C y 10,14 ° C, respectivamente. Se informaron resultados similares como una disminución de la temperatura de descomposición de HMX cuando se revistió con aglutinante [32, 33]. Bajo la premisa de contener 5% de MUF, el grado decreciente es bastante diferente para las temperaturas máximas de descomposición de las partículas compuestas a base de HMX fabricadas por diferentes métodos; obviamente, el efecto de la polimerización interfacial sobre el rendimiento de descomposición térmica de HMX es mínimo. También se pueden ver situaciones similares en las partículas compuestas RDX / MUF y CL-20 / MUF (como se observa en la Fig. 7c). Esto puede ser relevante para la morfología del recubrimiento y la compacidad de HMX / MUF, y el recubrimiento uniforme contribuye a la estabilidad del proceso de descomposición térmica de las partículas compuestas. Por tanto, para mejorar la estabilidad térmica de las partículas compuestas, es un medio eficaz seleccionar un material de revestimiento con excelentes propiedades térmicas. Además, bajo la premisa de elegir un aglutinante en particular, puede ser una buena manera de considerar el uso del método de polimerización interfacial para preparar partículas compuestas.
Sensibilidades
Para investigar el desempeño de seguridad de las muestras, se realizaron pruebas de sensibilidad al impacto y al rozamiento, y los resultados se presentan en la Fig. 8. Como podemos ver, entre los tratamientos de desensibilización realizados en HMX, RDX y CL-20, MUF tiene el efecto desensibilizante más significativo sobre las partículas compuestas preparadas por el método de polimerización interfacial. En comparación con HMX, RDX y CL-20 en bruto, la altura característica H 50 aumentó de 21,6 cm, 31,8 cm y 15,3 cm a 73,4 cm, 85,6 cm y 64,03 cm, respectivamente (Fig. 8a), mejorando así significativamente el rendimiento de seguridad. Además, se puede ver en la Fig. 8b que la sensibilidad a la fricción de GPBX fabricada por estos tres métodos diferentes es menor que la de los compuestos explosivos sin recubrimiento. Curiosamente, las tres muestras preparadas por la polimerización interfacial exhiben la menor sensibilidad a la fricción. Más importante aún, en comparación con informes anteriores [7, 18, 26], el rendimiento de seguridad de GPBX fabricado por polimerización interfacial es óptimo. El efecto de desensibilización es asombroso. Esto puede explicarse por la teoría de los puntos calientes [34]. MUF se recubre con éxito en la superficie de HMX, lo que puede producir un cierto efecto amortiguador bajo estímulos mecánicos externos, lo que ralentiza eficazmente la formación de puntos calientes. Schematic diagram of desensitization effect of composite particles prepared by three different techniques can be seen from Fig. 9. Obviously, with the same proportion of MUF binder, the composite particles fabricated by interfacial polymerization possess the most distinct desensitization effect, attributing to more uniform particle morphology. The uniform, small particle size distribution between the particles increases the gap between themselves, and the force area of the same quality composite particles increases, which reduces the stress concentration between the particles and effectively prevents the formation of local hot spots.
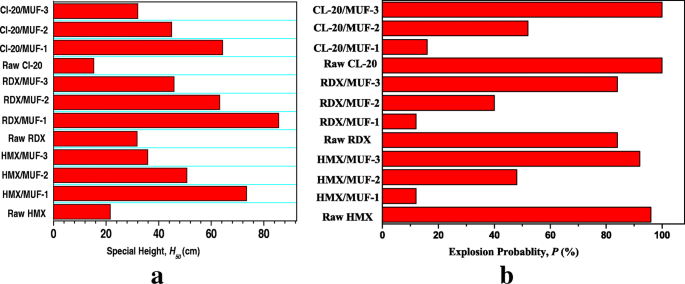
Impact sensitivity of samples:a impact sensitivity and b friction sensitivity
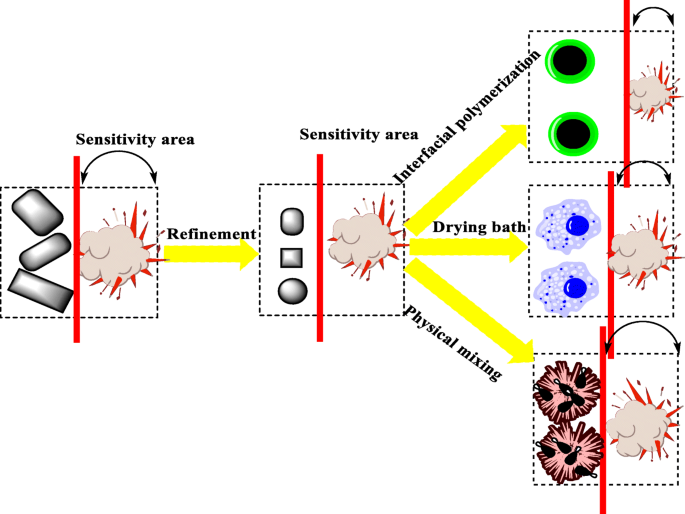
Schematic diagram of sensitivity
Conclusiones
Via ultrasonic assistance, nine different composite particles were fabricated by a simple physical mixing method, an improved drying bath method, and an optimized interfacial polymerization method. XRD and FT-IR analysis did not show any change in the crystal structure before and after the preparation of HMX and CL-20, still maintaining β-HMX and Ɛ-CL-20, respectively. Compared with the raw explosives, the thermal decomposition peak temperature of the composite energetic particles after adding MUF was reduced; however, the reduction effect of the thermal decomposition peak temperature of the sample 3 was not significant. The characteristic height H50 of the composite particles prepared by interfacial polymerization method increased by three to four times, most obviously improving the safety performance. In short, HMX/MUF, RDX/MUF, and CL-20/MUF particles prepared by each method have similarities in morphology, particle size, and even performance. In particular, the three composite particles fabricated by interfacial polymerization method possess better thermal stability and safety performance with smooth surfaces, dense and uniform coating layers. Therefore, in order to improve the thermal stability of the composite particles, it is an effective approach to select a coating material with excellent thermal performance. And under the premise of choosing a specific binder, it may be effective to prioritize the use of interfacial polymerization method to prepare composite particles. This study provides certain reference for the application of high-energy and low-sensitivity ammunition in weapon firepower and rocket systems.
Abreviaturas
- CL-20:
-
Hexanitrohexaazaisowurtzitane
- DSC:
-
Calorimetría diferencial de barrido
- ESV:
-
Emulsion solvent evaporation
- FI-IR:
-
Fourier-transform infrared spectra
- GPBX:
-
Green polymer-bonded explosives
- HMX:
-
Cyclotetramethylenetetranitramine
- IHEs:
-
Insensitive high explosives
- MF:
-
Melamine formaldehyde
- MUF:
-
Melamine-modified urea-formaldehyde
- NC:
-
Nitrocelulosa
- PF:
-
Phenolic resin
- RDX:
-
Cyclotrimethylenetrinitramine
- SEM:
-
Microscopía electrónica de barrido
- UF:
-
Urea formaldehyde
- XRD:
-
Difracción de rayos X
Nanomateriales
- Recubrimiento nano para varios colores
- Control completo de polarización de terahercios con ancho de banda ampliado a través de metauperficies dieléctricas
- Efectos de la coadsorción en la transferencia de carga interfacial en un compuesto cuántico dot @ dye
- Respuesta de osteoblastos a recubrimientos microporosos dopados con cobre sobre titanio para una mejor integración ósea
- Síntesis de puntos cuánticos de carbono codopados N, S ricos en piridínicos como imitadores enzimáticos eficaces
- Ajuste de la química superficial de la polieteretercetona mediante revestimiento de oro y tratamiento con plasma
- Ajuste de las morfologías de la superficie y las propiedades de las películas de ZnO mediante el diseño de la capa interfacial
- Eficacia antitumoral y farmacocinética mejoradas de la bufalina mediante liposomas pegilados
- Efecto del recubrimiento de nanocapa de tungsteno en el electrodo de Si en una batería de iones de litio
- Las nanopartículas de oxohidróxido de cobre dopado con ligando son antimicrobianos eficaces
- Chase Plastics se asocia con Interfacial en soluciones de resina