Tres consejos para crear piezas moldeadas por inyección más fuertes
El moldeo por inyección es un proceso de fabricación versátil que generalmente implica inyectar resina plástica fundida en moldes metálicos duraderos, lo que permite la producción de grandes volúmenes de piezas idénticas. Si bien el moldeo por inyección puede ser increíblemente rentable a escala, las piezas de plástico generalmente pasan por revisiones de diseño, impresión 3D, simulaciones y pruebas antes de moldear por inyección un producto final. Estos son algunos consejos que debe tener en cuenta al diseñar piezas moldeadas por inyección de plástico que ayudarán a mejorar la resistencia del producto final.
Selección de materiales:fundamental para crear piezas sólidas
Primero, una nota rápida sobre la selección de materiales. Puede parecer obvio decirlo, pero los materiales particulares de los que están hechos sus componentes tendrán un impacto significativo en la durabilidad, resistencia y dureza de la pieza o ensamblaje final. ¿Una forma sencilla de mejorar la resistencia de sus piezas y ensamblajes? Utilice termoplásticos más fuertes. Aquí hay algunos materiales de moldeo por inyección comunes que debe considerar si está buscando específicamente mejorar la resistencia de sus piezas moldeadas por inyección.
ABS
El acrilonitrilo butadieno estireno (ABS) es un termoplástico de ingeniería resistente a los impactos que tiene usos tanto domésticos como industriales:todo, desde controles remotos y carcasas de componentes electrónicos hasta compresores y nebulizadores de fabricación, se puede fabricar con esta resina asequible. Sin embargo, el ABS es susceptible a la intemperie y al agrietamiento por tensión cuando se le introducen ciertos productos químicos.
Policarbonato
También conocido como PC, este plástico ofrece una increíble resistencia al impacto (incluso más que el ABS) y se puede hacer transparente, lo que lo convierte en una alternativa común al vidrio. Los bienes de consumo como gafas protectoras, pantallas faciales, letreros interiores y exteriores y ventanas se fabrican con esta resina, que también se usa ocasionalmente para proteger el exterior de los edificios. Si bien es resistente a los impactos, la PC es propensa a rayarse y es costosa trabajar con ella.
Nail
Los nailons son una familia versátil de plásticos que son adecuados para aplicaciones que requieren un bajo coeficiente de fricción junto con una buena resistencia al desgaste, química y térmica. Si bien el nailon sin relleno tiende a tener un grado de flexibilidad y rigidez, se pueden incorporar estabilizadores y aditivos al material para optimizar las propiedades específicas de la pieza. Las fibras de vidrio, por ejemplo, mejoran la resistencia a la compresión, la rigidez y la temperatura de deflexión térmica del material, al mismo tiempo que lo vuelven quebradizo. El nailon es propenso a absorber la humedad de su entorno y se daña fácilmente con la luz ultravioleta sin el uso de estabilizadores.
Acetal
El acetal es valorado por su rigidez, bajo coeficiente de fricción y resistencia a la abrasión, el agua y los productos químicos. El acetal se usa comúnmente para producir componentes electrónicos, cremalleras y engranajes, componentes para automóviles, piezas para la industria alimentaria y muchas otras aplicaciones. El acetal no es compatible con las tecnologías de fabricación aditiva y, por lo tanto, tiende a usarse menos para la creación de prototipos que el nailon. Tampoco es adecuado para piezas cosméticas o que requieran pintura o impresión.
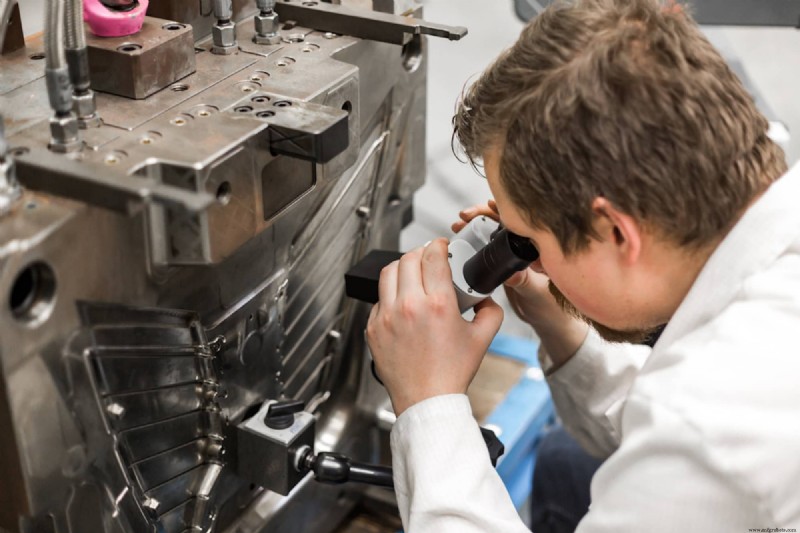
Consejos de diseño para construir piezas más fuertes
Evitar secciones gruesas
El tiempo de enfriamiento, típicamente la etapa más larga del proceso de moldeo por inyección, está determinado por las secciones más gruesas de la pieza. Un tiempo de enfriamiento más largo significa un tiempo de ciclo más largo, lo que a su vez aumenta el costo de producción. Las secciones transversales más gruesas también aumentan el riesgo de que las diferentes secciones de la pieza se enfríen a diferentes velocidades, lo que puede provocar defectos como deformaciones y hundimientos.
El moldeo por inyección como proceso es generalmente estable y consistente cuando se utiliza para producir piezas con espesores de pared que van desde 0,040” (1,016 mm) hasta 0,140” (3,556 mm), pero el espesor de pared nominal ideal variará según el material. Las piezas con un grosor de pared superior a 0,120” (3 mm) generalmente se pueden moldear, pero a menudo requieren atención adicional para garantizar que la cavidad del molde se llene durante cada ciclo. Alrededor de 3,8 mm (0,150 in), las secciones transversales se vuelven propensas a desarrollar sumideros, lo que hace que se necesiten procesos o soporte adicionales para mantener la viabilidad de la pieza.
Reforzar muros o salientes con nervaduras
Las paredes y las protuberancias son dos características que a menudo superan las pautas de grosor máximo de pared anteriores, en parte porque deben ser lo suficientemente fuertes para funcionar correctamente. Las nervaduras agregan resistencia a las áreas clave que requieren un espesor de pared superior al nominal, características en relieve y paredes altas, todo sin afectar el tiempo del ciclo. En algunos casos, incorporar más nervaduras en el diseño de la pieza puede reducir el uso de material.
Para minimizar el riesgo de sumideros o huecos a medida que la pieza se enfría, el espesor de pared de una protuberancia debe ser del 40 al 60 % del espesor de pared nominal del componente. Los salientes deben fijarse en su lugar con costillas o filetes para minimizar la deformación. Los salientes pueden introducir puntos de tensión adicionales, pero en realidad pueden reforzar los puntos de tensión en el diseño de una pieza si se incorporan correctamente.
Utilice filetes y radios para reforzar las esquinas
Las esquinas afiladas no son amigas de nadie en la fabricación, especialmente para las piezas moldeadas por inyección. ¿La solución para moverse por las esquinas? Radios de filete y radios redondos. Los dos son similares:los radios de filete son el redondeo de una esquina interna y los radios redondos son el redondeo de las esquinas externas de una pieza.
El redondeo de las esquinas internas brinda una serie de beneficios, incluida la mejora de la resistencia a la carga de la pieza y, al mismo tiempo, ayuda a mitigar la concentración de tensiones. Esto también garantiza un relleno de la cavidad más uniforme durante la producción, lo que ayuda a evitar que el material de las esquinas se expanda y agriete la calidad de la pieza. Se pueden agregar radios de filete entre salientes y nervaduras, conectándolos a paredes cercanas para mayor resistencia. Redondear aún más una esquina exterior ayuda a aumentar la resistencia de carga, reduce la probabilidad de fracturas y elimina las esquinas difíciles de rellenar del diseño de la pieza, lo que facilita garantizar rellenos de molde más uniformes.
Mejore la resistencia de sus piezas moldeadas por inyección con un experto calificado
La durabilidad y la tenacidad no son las únicas propiedades materiales que buscan los equipos de productos; es vital encontrar el equilibrio adecuado entre resistencia, función, asequibilidad y otras características deseadas del material. De lo contrario, corre el riesgo de terminar con una pieza demasiado flexible o demasiado frágil.
Trabajar con un socio de fabricación experimentado como Fast Radius significa que puede descansar tranquilo. Nuestro equipo trabaja arduamente para ayudar a cada uno de nuestros clientes a optimizar sus diseños y brindar la información necesaria para garantizar que cada pieza que producimos con usted supere las expectativas en lo que respecta a la resistencia de la pieza, el cronograma de producción y el costo. ¿Preparado para comenzar? Contáctenos hoy para saber más sobre nuestros servicios de moldeo por inyección.
Tecnología Industrial
- Cinco consejos para crear un proceso de incorporación de proveedores eficiente
- Moldeo por inyección robótico para compuestos funcionalizados
- Materiales para moldeo por inyección de reacción (RIM)
- Consejos de diseño para moldeo por fundición
- Herramientas blandas frente a herramientas duras para moldeo por inyección
- Ángulo de inclinación para moldeo por inyección:guía de diseño y prácticas recomendadas
- El moldeo por inyección y la impresión 3D se combinan para hacer piezas "imposibles"
- Opciones de materiales para moldeo por inyección
- 7 consejos para mejorar las piezas mecanizadas por CNC
- Consejos y trucos de diseño de moldeo por inyección de pared delgada
- Consejos de diseño para moldeo por inyección