Las estrategias de molienda van de buenas a excelentes
Cómo el software, la automatización y los avances en abrasivos están acelerando el rectificado de piezas y herramientas.
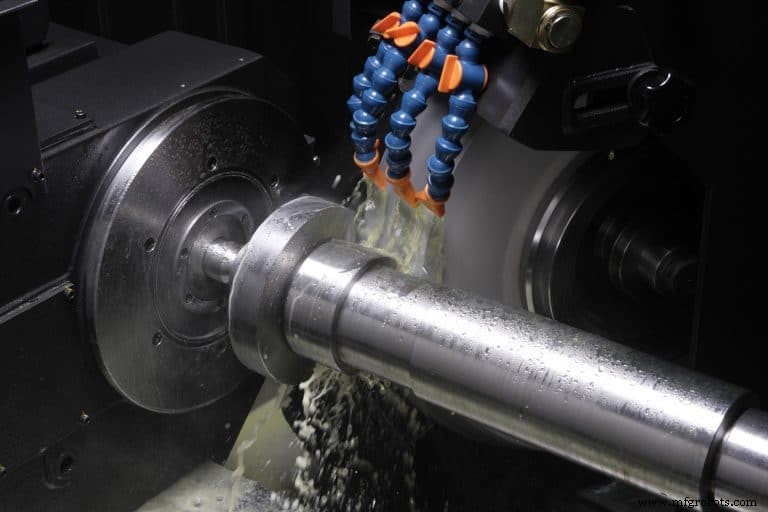
Tal vez su empresa se especialice en componentes aeroespaciales o médicos y necesite producir geometrías complejas en metales demasiado difíciles de cortar mediante métodos de mecanizado convencionales. O tal vez usted trabaja o es propietario de un taller de herramientas y cortadores, y está buscando formas más rápidas y rentables de producir brocas, fresas y herramientas de forma. Sea cual sea el motivo y sea cual sea el requisito, estás de suerte. Al igual que con la mayoría de las tecnologías metalúrgicas, el esmerilado, más propiamente llamado mecanizado abrasivo, ha mejorado mucho en los últimos años.
¿Cómo es eso? Para empezar, los fabricantes de muelas abrasivas han desarrollado nuevos aglomerantes y superabrasivos
que claramente merecen el título de "súper", capaces de eliminar más material en menos tiempo que nunca. Y los fabricantes de máquinas rectificadoras ofrecen equipos cada vez más capaces, lo suficientemente rígidos y potentes para aprovechar al máximo esos abrasivos avanzados, al tiempo que agregan funciones inteligentes como automatización, monitoreo remoto y sistemas de software inteligentes a sus máquinas herramienta.
En pocas palabras, el rectificado ha entrado en una nueva era de productividad y precisión de piezas; si no lo está aprovechando, podría estar perdiendo oportunidades significativas para la mejora de procesos, una mayor calidad del producto y un impulso en el resultado final.
Un mejor control es crítico
Un factor clave para esto es la escasez de maquinistas calificados. Eso es según Shane Farrant, gerente nacional de productos para molinillos en JTEKT Toyoda Americas Corp., Arlington Heights, Ill., quien agregó que hacer que la interfaz hombre-máquina (HMI) sea más fácil de entender es un primer paso necesario para minimizar los efectos de un mano de obra menos calificada.
“Un HMI más simple e intuitivo es una de las muchas mejoras que hemos desarrollado para nuestra línea de rectificadoras universales, cilíndricas, de árboles de levas y de cigüeñales”, dijo. "Esto significa un formato fácil de usar, con una mayor dependencia de imágenes y otros gráficos para ayudar en los procedimientos de configuración y programación".
También ha habido un gran impulso hacia un entorno de trabajo basado en Internet de las cosas (IoT). Por ejemplo, la página de diagnóstico del control táctil TOYOPUC de Toyoda muestra los niveles de refrigerante, la vibración de la máquina, la temperatura del aceite; cualquier cosa que pueda traducirse en una pieza de mala calidad o crear un problema de producción enviará una alerta inmediata a quien sea responsable de solucionarlo. Además, es posible recopilar esta información del control de la máquina y enviarla a una base de datos en red para su análisis histórico.
Otra característica que ahorra tiempo es la generación automática de programas alternativos, a los que un operador puede llamar si hay un problema relacionado con el proceso. El gerente de ingeniería de propuestas de JTEKT Toyoda, Steve Earley, dijo que esta opción de control conversacional está disponible en la rectificadora de rodillos GE6 de la compañía, una máquina que también se ha beneficiado de algunas modificaciones en la fundición, los motores y otros componentes, todos diseñados para reducir la vibración y aumentar la precisión de la máquina en esta aplicación especial.
Los materiales con los que se fabrican las baterías de litio que se utilizan en los vehículos eléctricos son bastante delgados, explicó, por lo que los rodillos que producen este material deben ser extremadamente precisos, con acabados superficiales muy finos. “Cuando un operador está configurando la máquina, el control presentará un programa generalizado para comenzar, así como dos alternativas:una que es más agresiva para tiempos de ciclo más rápidos y un programa más conservador que produce mejores acabados superficiales”, dijo Earley. . “Basándose en los resultados iniciales, el operador puede decidir fácilmente cambiar a cualquier conjunto de parámetros de mecanizado que proporcione la mejor pieza en el menor tiempo posible”.
Se requieren menos operaciones
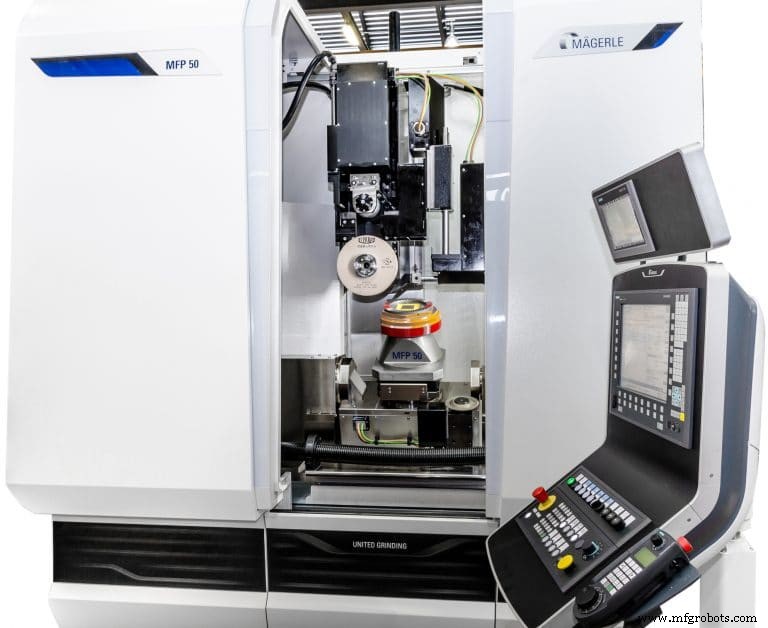
Larry Marchand, vicepresidente del grupo de perfiles de United Grinding North America Inc., Miamisburg, Ohio, estuvo de acuerdo con la necesidad de controles fáciles de usar, especialmente a medida que las máquinas rectificadoras se vuelven más capaces. Pero dijo que también hay un tremendo llamado en toda la comunidad manufacturera para reducir el trabajo en proceso y menos operaciones de maquinado, lo que lleva a United Grinding y otras compañías a adoptar el llamado enfoque "hecho en uno" para reducir el tiempo de contacto del operador y aumentar el valor por operación.
Para respaldar esto, United Grinding ha introducido "procesos, operaciones y características adicionales" en las máquinas rectificadoras de perfiles que alguna vez fueron de un solo propósito. “Los clientes quieren agregar más valor en el manejo de una sola pieza”, dijo Marchand. “Hemos visto una gran demanda de máquinas con cambiadores automáticos de herramientas, lo que permite rectificar la pieza de trabajo y luego traer un taladro o una fresa para completar la pieza. Esto elimina las operaciones secundarias, reduce el tiempo de entrega de las piezas y mejora la calidad”.
¿Significa esto que los talleres mecánicos deberían cambiar sus máquinas herramienta CNC por una súper amoladora que lo haga todo? De nada. Así como las máquinas multitarea hacen un muy buen trabajo al fresar una ranura o rectificar un muñón, una rectificadora multitarea ahora puede realizar tareas que antes estaban reservadas para los centros de mecanizado y las máquinas perforadoras; dicho esto, ningún estilo de máquina herramienta puede reemplazar al otro. Como señaló Marchand:"Si tiene una pieza que requiere mucho pulido, siempre estará mejor con una pulidora dedicada".
Hay varias razones para esto, dijo. El rectificado requiere sustancialmente más fluido de corte que las operaciones de fresado y torneado, dirigido precisamente a la intersección de la pieza de trabajo y la rueda. Manejar una rueda que mide un par de pies de diámetro requiere mucha potencia, mucha más de la que está disponible en una máquina de fabricación de chips promedio. Finalmente, mantener acabados superficiales de décimas y de un solo dígito todo el día es algo en lo que sobresalen la mayoría de las rectificadoras CNC porque están diseñadas para optimizar estas operaciones. ¿Centros de mecanizado? No tanto.
Hacer frente a las cosas difíciles
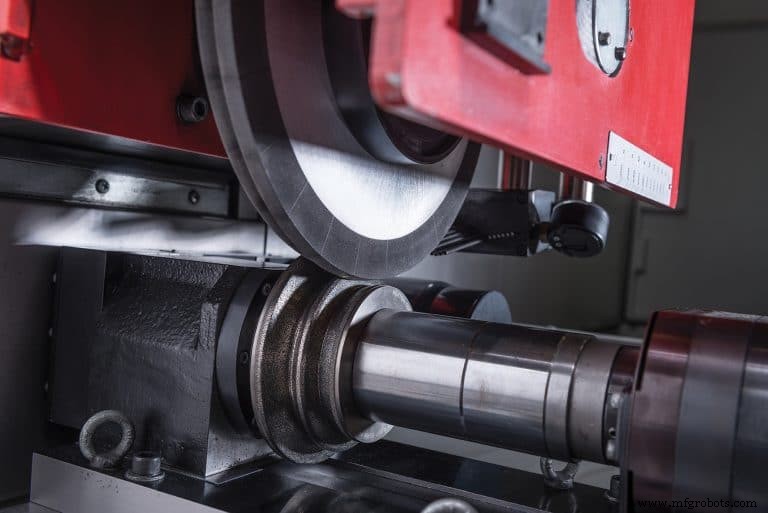
Estas capacidades son especialmente relevantes con metales con alto contenido de níquel, cromo y cobalto, dijo Marchand. “Gran parte de nuestro negocio proviene de clientes que producen piezas de Inconel y Rene, materiales que, al menos en su estado endurecido, casi no se pueden mecanizar. Su única opción es la electroerosión o el rectificado y, gracias a la rigidez, potencia y precisión de las rectificadoras modernas, además de la disponibilidad de superabrasivos que no estaban disponibles hasta hace poco, la mayoría opta por lo último”.
Uno de los principales fabricantes de superabrasivos es Norton|Saint-Gobain Abrasives, Worcester, Massachusetts. Alfredo Barragán, ingeniero senior de aplicaciones corporativas para superabrasivos de América del Norte, dijo que el esmerilado alguna vez se consideró un proceso de "solo acabado", pero, con el desarrollo de tecnología de rectificado cada vez más capaz, se ha convertido en un proceso de mecanizado convencional. Sin embargo, para lograr el mayor éxito con este proceso, se deben aplicar abrasivos igualmente modernos.
“Las muelas de matriz de diamante con aglomerante metálico o de resina tradicional tienden a ser muy densas”, dijo Barragán. “Ser denso es algo bueno porque le brinda una estructura robusta y ayuda a proporcionar un vínculo fuerte que mantiene unida esa estructura, pero plantea una consideración:la rueda tiende a cargarse más rápido, lo que a la larga reduce la productividad. Las ruedas de bonos híbridos Norton Winter Paradigm resuelven este problema”.
Se dice que las ruedas proporcionan una combinación de retención de grano mejorada con altos niveles de porosidad, lo que reduce las fuerzas de corte. Una porosidad más alta también reduce la carga:la rueda muele más fría, más libremente, con menos tiempo de inactividad y, en última instancia, produce más piezas por día. Dependiendo del abrasivo utilizado, las ruedas de aglomerante híbrido muelen de manera eficiente el carburo, la cerámica avanzada, los aceros endurecidos para herramientas y las aleaciones de alta temperatura que Marchand de United Grinding acaba de mencionar.
Sin embargo, hay más en esto que la tecnología de abrasivos. Al igual que las máquinas herramienta a las que están unidas, las propias ruedas se están volviendo más inteligentes, con etiquetas RFID integradas para una mejor gestión de activos, compras optimizadas, seguimiento de la información de uso y preparación, y protección contra errores del operador.
Norton|Saint-Gobain tampoco restringe sus esfuerzos a los productos abrasivos. Su sistema de monitoreo y diagnóstico de procesos 4Sight proporciona una funcionalidad de IoT similar a la que se mencionó anteriormente, con monitoreo en tiempo real e independiente de la marca de los valores de la máquina rectificadora, como la carga del husillo y la utilización de la máquina, y la capacidad de almacenar datos para análisis de tendencias o enviar alertas según sea necesario. . "Esta es una de las mayores iniciativas del año para nosotros y, junto con nuestros sistemas de etiquetas inteligentes, sirve como base de nuestra solución Industry 4.0", dijo Barragan.
Llegando a tu pantalla:V@dison
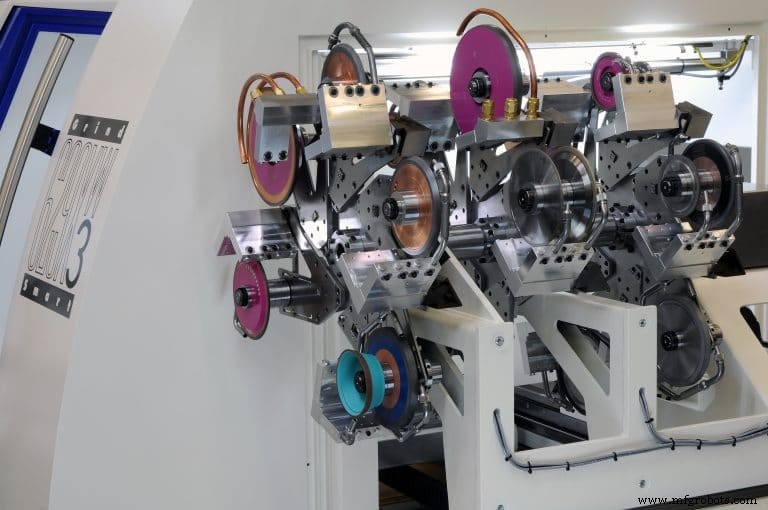
No están solos. Vollmer of America Corp., Carnegie, Pa., junto con su empresa matriz, Vollmer Group, está trabajando en una serie de herramientas y servicios diseñados para "transformar digitalmente" las operaciones de molienda. Con la marca V@dison, estos incluyen la pantalla V@ para mejorar la visibilidad de los parámetros de la máquina, la verificación V@ para la simulación de procesos, el impulso V@ para optimizar el rendimiento de la máquina según la pieza de trabajo y la guía V@ para un mantenimiento preventivo más consistente.
Vollmer aún se encuentra en las primeras etapas de esta iniciativa, pero la gerente de ventas de América del Norte, Shannon Fox, dijo que todavía hay muchas mejoras disponibles para la comunidad de molienda. El principal de ellos es la automatización:Fox señaló como ejemplo las capacidades robóticas de carga de piezas y cambio de ruedas de su rectificadora de herramientas y cortadora VGRIND 360, opciones que Vollmer y, de hecho, la mayoría de los fabricantes de máquinas-herramienta instalan de manera rutinaria a medida que sus clientes trabajan para lograr luces- fuera de la fabricación.
La simulación es otra solicitud de rutina. Aunque el sistema de verificación V@ de Vollmer aún está en desarrollo, Fox señaló que el software NUMROTOplus ofrecido en Vollmer y otras marcas de equipos de molienda es una alternativa madura y bien aceptada. “La simulación se está volviendo más importante a medida que los molinillos se vuelven más capaces”, dijo. “Los cuartos son más ajustados, las geometrías de las herramientas son cada vez más complejas y muchas máquinas, incluida la nuestra, permiten el uso de varios paquetes de ruedas en un solo trabajo, lo que genera problemas de interferencia. Sin simulación, se corre el riesgo de estrellar una máquina herramienta muy costosa”.
Ver para creer
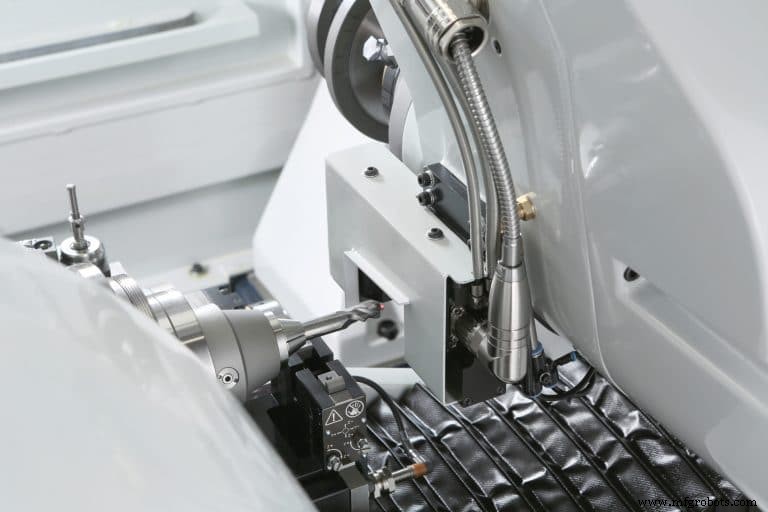
La simulación también es importante por otras razones. ANCA CNC Machines, con sede en Melbourne, Australia, por ejemplo, lo utiliza para predecir el desequilibrio de herramientas en fresas de extremo de paso variable. “Esa es una de las ventajas y desventajas de los cortadores de alto rendimiento:debido a que el espacio entre canales es irregular, están inherentemente desequilibrados”, dijo Lucas Hale, gerente de marketing global. “Para combatir esto, hemos desarrollado un software de simulación que calcula el desequilibrio y ajusta el programa NC para compensarlo mediante la eliminación de material adicional en ubicaciones estratégicas. La herramienta sale de la amoladora perfectamente equilibrada, lo que ofrece una mayor vida útil de la herramienta y un mejor acabado superficial en la pieza mecanizada”.
Hale estuvo de acuerdo con la llamada de automatización, incluida la manipulación robótica de piezas y ruedas, pero ofreció varias formas adicionales de aumentar la productividad. Donde antes se hacía manualmente el "pegado" rutinario de la rueda para quitar la carga, ANCA lo ha automatizado, reduciendo los costos de mano de obra y extendiendo la vida útil de la rueda. Se dice que el software y las máquinas de ANCA brindan una "significativa facilidad de uso", lo que reduce el tiempo de configuración. Y los sistemas de medición basados en láser brindan una verificación en el proceso de la precisión y la geometría de la herramienta de corte, seguida de compensaciones automatizadas o rectificado de ruedas para compensar el desgaste.
Y ANCA ha llevado ese proceso un paso más allá. A través de la colaboración con empresas como Zoller Inc., un proveedor líder de equipos de ajuste de herramientas, ANCA ha desarrollado una interfaz que admite la inspección automatizada y la retroalimentación a la amoladora CNC:un robot coloca el cortador en el dispositivo de ajuste, que lo mide y envía los resultados. a un sistema de software que ajusta la máquina según sea necesario. Esto "cierra el ciclo", explicó Hale, y junto con los sistemas integrados de administración de espacios en blanco, permite a los clientes "cargar cientos de herramientas, presionar Continuar y volver al día siguiente para completar las herramientas de corte", dijo.
“La construcción de máquinas básicas también ha mejorado durante los últimos cinco años”, continuó Hale. “Por ejemplo, los motores lineales se han vuelto mucho más comunes en nuestra industria. No solo contribuyen a la calidad de las herramientas de corte y, por lo tanto, a la calidad de las piezas que se fabrican con ellas, sino que las máquinas lineales se mueven mucho más rápido que las de husillo de bolas, lo que reduce los tiempos de ciclo. Y debido a que hay menos desgaste en los componentes de la máquina, se extiende la vida útil del equipo. Esta es la razón por la que los motores lineales se han convertido prácticamente en un componente estándar de cualquier rectificadora de alta precisión y alto rendimiento”.
Primera parte, buena parte
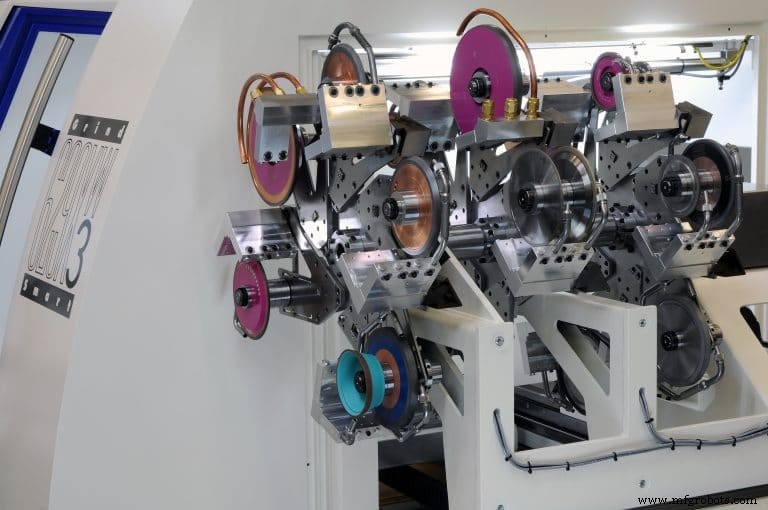
Así como JTEKT Toyoda está abordando la escasez de maquinistas calificados con un software de control más intuitivo, Rollomatic Inc., Mundelein, Ill., está trabajando para hacer que las configuraciones de las máquinas sean más fáciles y rápidas. Esto se debe a que la mayoría de los fabricantes de herramientas y cortadores no son diferentes a cualquier taller de corte de metales; se enfrentan a tamaños de lote más pequeños y tiempos de entrega más cortos, lo que hace que el tiempo de configuración sea un porcentaje mayor de cualquier ciclo de producción. ¿Una parte de la solución? Mejor software.
“Durante décadas, los talleres han quemado tres, cuatro, cinco piezas de trabajo en bruto por configuración, ajustando gradualmente la máquina hasta obtener una buena pieza”, dijo Eric Schwarzenbach, presidente de Rollomatic Inc. “Pero mediante el uso de software inteligente, es muy posible para reducir el número de piezas de trabajo de desecho, siendo cero el objetivo final. Esto no solo reduce los costos de materiales, sino también el tiempo de configuración”.
El software ayuda al operador al hacer una representación en 3D de la máquina herramienta, la pieza de trabajo y la muela abrasiva, dijo Schwarzenbach, eliminando la necesidad de una ejecución en seco. El operador puede acelerar la animación, ralentizarla, retroceder o acercar las áreas problemáticas, ayudándole a evitar posibles colisiones entre el paquete de ruedas y la pieza de trabajo. Y cuando la animación está terminada y la máquina realmente está fabricando piezas, el software funciona para eliminar los "movimientos vacíos" y acorta las distancias de seguridad al mínimo.
El software inteligente es excelente, pero Schwarzenbach se apresuró a señalar que la máquina herramienta y sus sistemas relacionados son igualmente importantes. Cuanto más precisa y estable sea la máquina herramienta, más fácil será alcanzar la dimensión objetivo en el primer intento. Además, la tecnología mejorada de preparación de ruedas, los procedimientos de calibración automatizados, los controles más rápidos que procesan los cálculos con mayor rapidez y las uniones de ruedas híbridas que son resistentes al desgaste, de corte libre y retienen las esquinas afiladas por más tiempo son fundamentales. Estos factores juegan un papel importante en configuraciones más rápidas y una capacidad mejorada para hacer que la primera parte sea buena, con tiempos de ciclo más cortos para arrancar.
Como otros han mencionado, el cambio automático de ruedas es otro punto de inflexión en el rectificado:Schwarzenbach dijo que los cambiadores de alta velocidad de Rollomatic pueden cambiar un paquete de ruedas en cinco segundos, eje a eje, y lograr tiempos de esmerilado a esmerilado de 11 segundos. Sin embargo, el beneficio va más allá de los tiempos de ciclo más cortos. “Si tiene un paquete con cuatro ruedas, el potencial de colisión es mayor que uno con una o dos ruedas. Esto complica la configuración. Por lo tanto, si puede dividir un paquete de ruedas grande y pagar los 11 a 12 segundos de tiempo de cambio de rueda, entonces esa es la forma preferida de hacerlo en este día y edad".
Sistema de control de automatización
- ¿Qué tan bueno es GCP como una elección de carrera?
- Bueno a genial:mírate en el espejo
- Estrategias para componentes de transmisión de potencia más confiables
- Por qué las órdenes de trabajo merecen más cariño de todos nosotros
- Por qué y cuándo actualizar de luces indicadoras a una pantalla HMI
- Cómo obtener más de su inversión en camiones articulados
- Beneficios de usar una muela abrasiva o un disco de láminas de 5 o 6 pulgadas
- EU Automation:las mejores tendencias tecnológicas de 2020
- 7 estrategias de los grandes gerentes de seguridad
- Rectificado de superficies:algo más que girar
- Rectificado Cilíndrico y Gran Productividad