La tecnología VMC amplía las aplicaciones y la productividad
Los modelos avanzados continúan expandiendo el alcance de VMC en el taller.
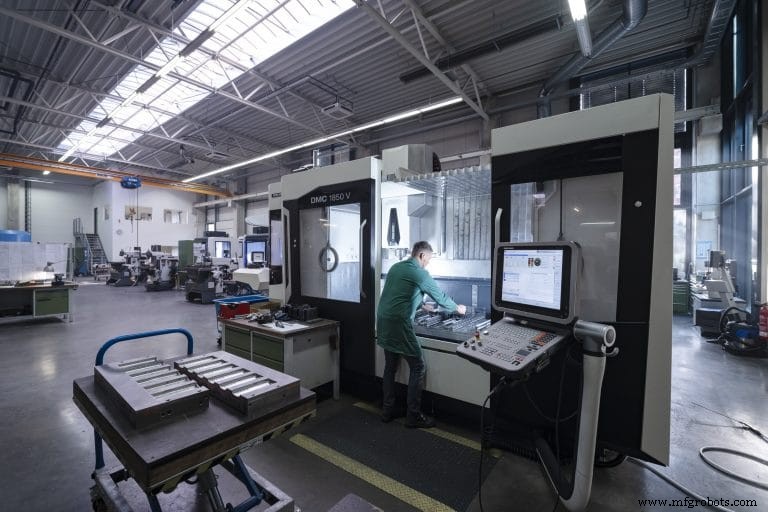
Los centros de mecanizado vertical con características y funciones avanzadas se están ganando el puesto como miembros más productivos del arsenal de equipos CNC de los talleres de mecanizado. Los VMC de hoy en día desafían la noción de que deben enviarse a un rincón oscuro del taller que rara vez se visita, o limitarse al mecanizado secundario. Tradicionalmente, los VMC han tenido un precio más bajo en comparación con los centros de mecanizado horizontales, pero sin la capacidad de producción.
Hasta cierto punto, las incorporaciones más recientes de tecnología avanzada han permitido a los VMC cerrar la brecha de productividad y asegurar una ventaja competitiva en aplicaciones de alta velocidad y alta precisión tan diversas como las industrias aeroespacial, médica, energética y de demanda similar. La funcionalidad de los VMC se ha incrementado significativamente con la adición de configuraciones de muñón y mesa sobre mesa de cuarto y quinto eje, cambiadores de paletas múltiples, más herramientas y husillos de alta velocidad. Los VMC son capaces de mecanizar las piezas de trabajo más complejas, como rotores con álabes para motores a reacción, álabes de turbinas para la generación de energía, grandes componentes aeroespaciales y trabajos de precisión con moldes y matrices.
Estudio de caso de VMC de moldes y matrices
Werkzeugbau Leiss GmbH es considerado uno de los productores líderes y más exitosos del mundo de moldes de extrusión-soplado y moldes de estirado-soplado. En estrecha colaboración con sus clientes, la empresa de Ludwigsstadt, Alta Franconia, Alemania, desarrolla nuevos diseños de envases para las industrias alimentaria, farmacéutica, química, automotriz y cosmética, así como matrices y moldes diseñados y fabricados por unos 65 expertos Leiss empleados.
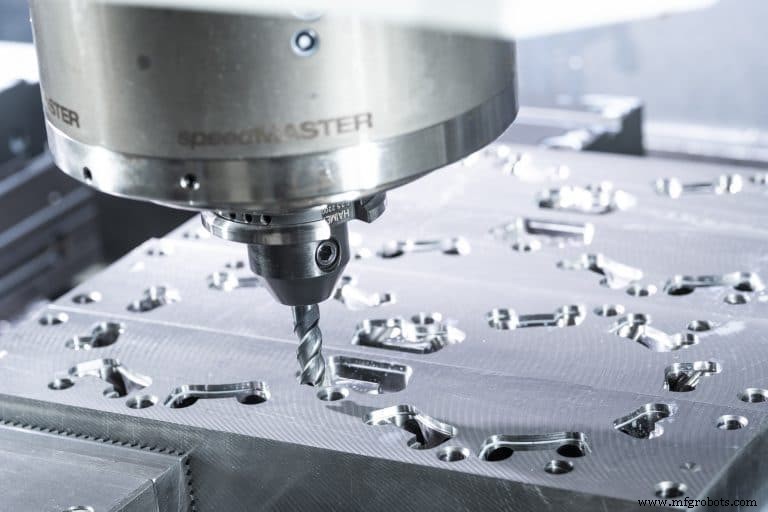
“Como proveedor de servicios en el diseño y construcción de herramientas, nos vemos como un socio para nuestros clientes”, dijo Daniel Leiss, explicando la estrategia de la empresa. Dirige la empresa junto con su padre Fritz Leiss. Las estrechas colaboraciones con los clientes a menudo comienzan con el desarrollo de nuevos diseños de envases. “Cuanto antes ayudemos al proceso con nuestra experiencia, más económica será la fabricación de los troqueles para todos los interesados”.
Esto hace posible que Werkzeugbau Leiss fabrique 250 nuevos troqueles por año con un total de alrededor de 1000 cavidades, así como componentes periféricos, como pernos de soplado, máscaras/punzones o troqueles/pasadores.
Werkzeugbau Leiss gestiona su producción de gran volumen en sus amplias y modernas instalaciones. El mecanizado de precisión lo realiza una potente flota de máquinas, incluidas diez máquinas CNC de DMG Mori. Además de dos tornos CTX, la flota de máquinas incluye cinco centros de mecanizado vertical de la serie DMG Mori DMC V. Esto incluye la DMC 1150 V, la DMC 1450 V y también la nueva DMC 1850 V.
Las máquinas funcionan a plena capacidad, mecanizando los moldes de soplado de extrusión de alta precisión, que representan el 80 por ciento de la producción de Leiss. Sus procesos de fabricación van desde el taladrado y fresado de los sistemas de refrigeración hasta el desbaste y el acabado. “Nos beneficiamos de la alta estabilidad y precisión de las máquinas, lo que nos ha permitido reducir al mínimo el trabajo de acabado, especialmente en el campo de los moldes grandes para máquinas de carrera larga”, dijo Daniel Leiss, refiriéndose al pulido posterior de la moldes.
El modelo más grande de la serie DMC V se instaló en julio de 2018 como máquina de prueba de campo, lo que Daniel Leiss considera el complemento perfecto:“Con la DMC 1850 V, DMG Mori ha adaptado un concepto de máquina probado y testado a la requisitos de calidad cada vez mayores al mecanizar componentes más grandes y pesados”. El centro de mecanizado vertical se expande a recorridos de 1.850 mm en el eje X, y 700 mm y 550 mm respectivamente en el eje Y y el eje Z. La capacidad de carga máxima es de 3.000 kg.
Según Daniel Leiss, la DMC 1850 V se adapta perfectamente a los requisitos de los fabricantes de moldes y matrices. “La estabilidad de la máquina se aplica tanto al mecanizado y taladrado 2.5D como al desbaste 3D. Con su precisión y dinámica, la máquina también es impresionante para el acabado fino en 3D y, por lo tanto, es adecuada para su uso en todas las fases de la producción de herramientas”, dijo. Después de solo unos meses de pruebas de campo, la DMC 1850 V se utilizó en una operación de dos turnos y ha estado funcionando de manera confiable desde entonces.
VMC con mesa basculante
Mazak Corp., Florence, Ky., continúa expandiendo su línea VMC diseñada y construida en Kentucky con el centro de mecanizado vertical VC-500A/5X que cuenta con una mesa basculante estilo muñón. El VMC está diseñado para el procesamiento preciso y rentable de piezas pequeñas y complejas a través del mecanizado completo de cinco ejes. El VC-500A/5X se une a los VMC de Mazak que incluyen capacidades de mecanizado de tres, cuatro y cinco ejes con sondeo integrado para la ubicación de piezas y la inspección de características. El VC-500A/5X cuenta con el CNC Mazatrol SmoothX, lo que facilita la generación de programas para la producción de piezas complejas.
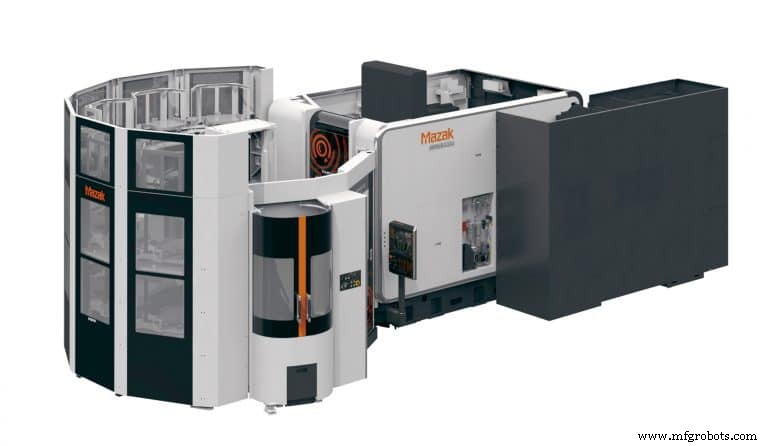
Las funciones avanzadas de la VC-500A/5X le permiten garantizar los tiempos de ciclo de mecanizado más cortos posibles, especialmente en programas de incrementos finos para operaciones simultáneas de cinco ejes y mecanizado de moldes de forma libre, dijo la compañía. Estas funciones incluyen control de avance de alta ganancia, velocidades rápidas del eje giratorio, control de aceleración variable y fresado inteligente de cajeras. El software especial de diseño de engranajes y una unidad de metrología se pueden integrar en un proceso de mecanizado de engranajes de bucle cerrado.
Los recorridos del eje del VC-500A/5X admiten tamaños de piezas de hasta 19,88″ (505 mm) de diámetro y 12″ (305 mm) de altura. Las velocidades de avance rápido para estos tres ejes lineales son 1181 ipm (30 m/min). La VC-500Z/5X está equipada con un husillo CAT-40 de 12 000 rpm de alto rendimiento para mecanizar todos los materiales comunes, incluidos acero, aluminio y hierro fundido. Se encuentran disponibles velocidades de husillo opcionales de 15 000 rpm y 20 000 rpm.
Un ATC de 60 herramientas ayuda a reducir el tiempo de configuración, permite el uso de herramientas redundantes y proporciona más operaciones ininterrumpidas y sin personal. Este proceso brinda a los talleres una opción rentable y de alta precisión para mecanizar engranajes de lotes pequeños a medianos con herramientas estándar.
Automatización de una sola máquina
Dado que el espacio en el piso de producción es muy importante, las máquinas de tamaño reducido son ampliamente valoradas, al igual que la automatización que puede optimizar el espacio disponible en el piso. Los sistemas de automatización de una sola máquina para centros de mecanizado vertical ofrecen una solución productiva para talleres pequeños con la capacidad de satisfacer las cambiantes demandas de producción con sistemas ampliables y rentables. Requieren un espacio mínimo en el piso y brindan una operación sin luz, manteniendo los husillos de la máquina en el corte mientras los operadores tienen libertad para cargar piezas nuevas, realizar controles de calidad o atender otras tareas del taller.
Cuando se trata de automatización, los OEM de máquinas-herramienta, como Mazak, se dan cuenta de que una talla no sirve para todos y continúan desarrollando sistemas de automatización escalables. Dichos sistemas son escalables en tamaño, costo y capacidad, pero brindan los beneficios típicos de cualquier forma de automatización:mayor producción de máquinas y mano de obra, esencialmente haciendo más con menos.
Así es como Mazak evalúa los beneficios de la automatización de una sola máquina. En comparación con los sistemas de automatización más expansivos, los sistemas de automatización de una sola máquina ocupan mucho menos espacio y, en muchos casos de talleres, eso es todo lo que se necesita.
Los sistemas de automatización de una sola máquina de hoy en día suelen ser soluciones estandarizadas, pero flexibles y ampliables. Por ejemplo, el sistema de automatización Multi Pallet Pool (MPP) de Mazak ofrece a los talleres la opción de tres configuraciones diferentes, con capacidad para 6, 12 o 18 palés. El sistema funciona con diferentes métodos de producción y el operador puede configurar el sistema MPP para ejecutar piezas de mezcla baja/volumen alto o piezas de producción corta con cambios frecuentes.
Inicialmente, un taller podría comenzar con un MPP de seis tarimas compuesto por dos filas de tres tarimas. Este sistema de dos niveles podría expandirse a seis tarimas en cada fila para un grupo total de 12 tarimas. Para un sistema de 18 tarimas, el MPP crecería a tres filas de seis tarimas. Independientemente de la configuración, el tamaño del MPP en términos de huella sigue siendo pequeño, lo que ahorra un valioso espacio en el taller.
Un cambiador de seis paletas MPP combinado con un VMC de cinco ejes Mazak Variaxis i-600, por ejemplo, utiliza un 29 por ciento menos de espacio en el piso que un sistema de tipo lineal de seis paletas y proporciona la misma capacidad. En comparación con un sistema de 12 paletas, el MPP reduce los requisitos de espacio en el piso en un 44 por ciento. Y cuando se utiliza con un VMC de cinco ejes Mazak Variaxis i-700, un MPP de seis tarimas es un 44 por ciento más pequeño que un sistema de disposición lineal de seis tarimas, y los sistemas de 12 y 18 tarimas de MPP necesitan menos de la mitad del espacio.
A diferencia de otros sistemas de automatización, el MPP utiliza palets de máquina reales en lugar de otros adicionales colocados encima del palet existente de una máquina. El MPP de la Variaxis i-600 cuenta con un palé de 400 mm cuadrados que admite una carga máxima de 300 kg en dimensiones de hasta 600 mm de diámetro y 425 mm de altura.
El palé Variaxis i-700 MPP es de 500 mm cuadrados y tiene una capacidad de carga de 400 kg. El MPP funciona con el mismo sistema de sujeción de palés que un cambiador típico de dos palés instalado en una máquina herramienta. Dentro del MPP, un robot servoaccionado toma y coloca palets dentro y fuera de la máquina.
El MPP utiliza el mismo software Smooth PMC que controla el extenso sistema de automatización Palletech de varias máquinas de Mazak. El control de la máquina herramienta muestra el software que se ejecuta en una unidad de controlador de celda separada. El software Smooth PMC facilita el monitoreo del sistema de mecanizado automatizado desde casi cualquier lugar usando un teléfono inteligente, PC o tableta. El software también permite que los talleres cambien los cronogramas sobre la marcha, administren archivos de programas de piezas, realicen un seguimiento de la vida útil/roturas de la herramienta, así como también emitan instrucciones para el taller.
Pasar de la impresión a la pieza más rápido
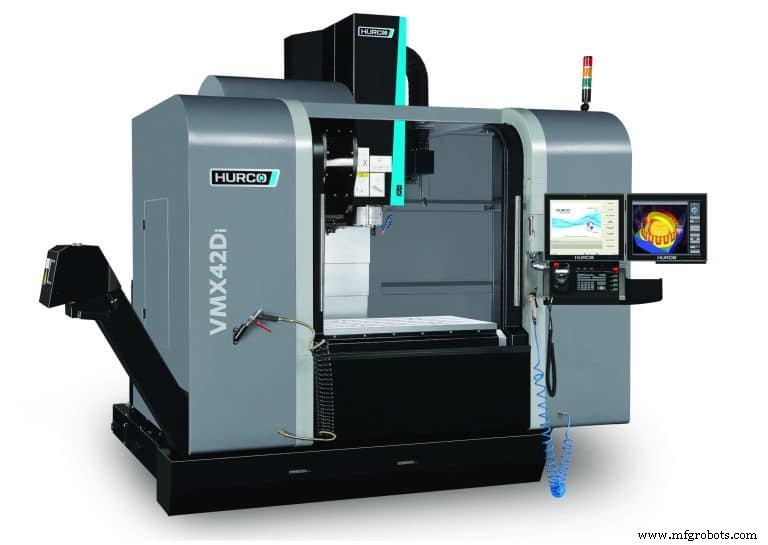
Es de esperar que Hurco Companies Inc., que inventó la programación conversacional, sea líder en la optimización del proceso de pasar de la impresión a la pieza más rápido con los centros de mecanizado CNC. Y lo es.
Los VMC de Hurco abarcan toda la gama, desde el modelo de valor de espacio compacto VM CNC VMC hasta las máquinas de la serie VMX de cinco ejes, y para las piezas aeroespaciales más grandes, la serie DCX de centros de mecanizado de doble columna con ejes X de 2 y 3 m. Los VMC de Hurco se utilizan para fabricar piezas para las industrias automotriz, aeroespacial, de equipos médicos, de energía, de moldes y herramientas de inyección, de transporte y electrónica.
En sus centros de mecanizado CNC de gama alta, Hurco ofrece control de doble pantalla para un procesamiento más rápido y sencillo. Una búsqueda de bloques de datos ayuda a los operadores a editar un programa de pieza para corregir una característica, por ejemplo. En lugar de buscar a través de líneas de código, el programador usa la pantalla de gráficos para seleccionar la característica de la pieza que necesita editarse y la línea de código correspondiente aparece en la otra pantalla para que el cambio se pueda realizar rápidamente.
La función de programación simultánea de Hurco se ha mejorado con el control de pantalla dual. Mientras el centro de mecanizado ejecuta una pieza, el operador puede programar la siguiente pieza sin interrumpir el ciclo de mecanizado.
DXF Transfer permite al operador importar la imagen CAD, seleccionar las características deseadas y el control WinMax CNC crea automáticamente el programa. El programa de la pieza se puede verificar en la pantalla con el sistema de gráficos de verificación de Hurco, que incluye una representación sólida en 3D de la trayectoria de la herramienta con rotación dinámica y visualización de la herramienta en tiempo real para que la pieza se pueda ver desde cualquier ángulo sin tener que volver a dibujarla. .
Las funciones recientes de control y software de Hurco están diseñadas para agilizar todo, desde optimizar el tiempo del ciclo hasta capturar información de herramientas. UltiMotion reduce el tiempo del ciclo hasta en un 30 %, lo que, según Hurco, aumenta significativamente la calidad del acabado superficial.
UltiMonitor permite el monitoreo remoto de la máquina desde cualquier navegador web, o es posible ver la pantalla de control o el video desde una cámara USB en la máquina. La longitud absoluta de la herramienta permite que la configuración de la herramienta sea independiente de la pieza y la máquina. Como resultado, la información de la herramienta solo debe capturarse una vez, lo que permite que la herramienta se use en otros centros de mecanizado, lo que facilita el uso de un preconfigurador de herramientas fuera de línea. Además, Tool Change Optimization analiza el programa de piezas y reduce automáticamente la cantidad de cambios de herramienta al reorganizar el programa para una eficiencia óptima.
Capacidad completa de VMC
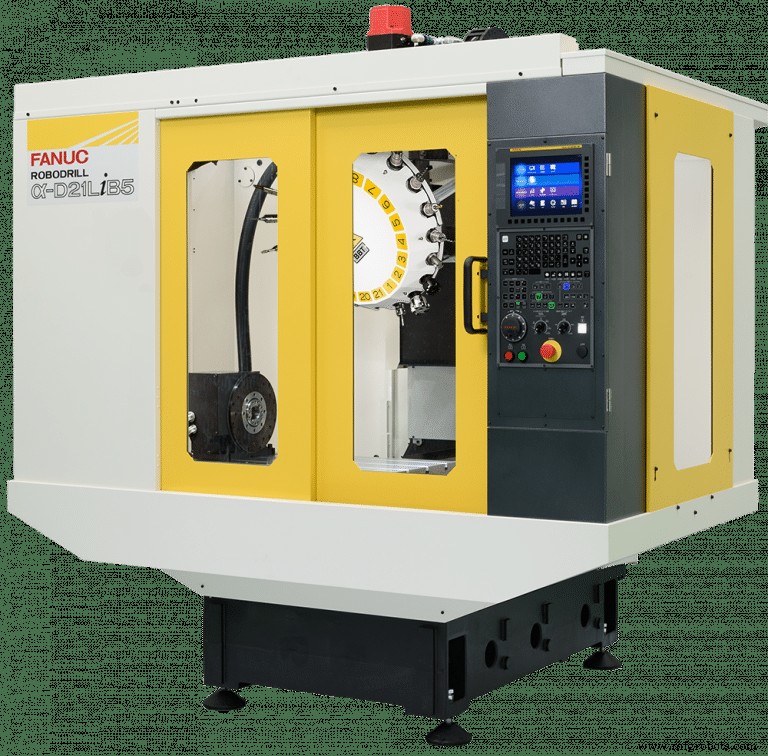
El familiar RoboDrill de FANUC imita la capacidad de un centro de mecanizado vertical para realizar operaciones de fresado, taladrado, roscado, refrentado, embolsado y ranurado:todo lo que puede hacer un VMC, dijo Ken Corklin, gerente de productos de RoboDrill, Methods Machine Tools Inc., Sudbury, Massachusetts.
“El RoboDrill compite muy bien con los VMC de 20 x 30″ y 20 x 40″ y puede hacer la misma cantidad de trabajo que un VMC de 20 x 30″ de cono 40 y hacerlo entre un 15 y un 50 por ciento más rápido. Las razones son el cambio rápido de herramientas, el encendido y apagado rápido del husillo y los motores de alta tasa de aceleración. Incluso si un cono 40 puede hacer un desbaste más pesado, el RoboDrill los supera en ranurado, roscado, taladrado, embolsado e interpolación circular. Con el desbaste, el RoboDrill suele ser un 15 por ciento más rápido; sin desbaste tanto como un 20-40 por ciento más alto”, dijo.
Hay más de 7000 RoboDrills instalados en América del Norte, aproximadamente la mitad en talleres de trabajo y la otra mitad en talleres específicos de la industria. Las aplicaciones incluyen el mecanizado de alta velocidad de aluminio para piezas aeroespaciales, cromo de titanio y cobalto para piezas médicas y piezas de armas, así como ingeniería general.
“La tecnología de husillo BIG Plus le ha dado al RoboDrill con marco en C de cono 30 el área de contacto de la superficie que le permite realizar cortes más pesados y de alta calidad y hacerlo a la velocidad del rayo, algo que las máquinas con cono 40 tienen problemas para igualar”, dijo Corklin. “Por ejemplo, RoboDrill puede realizar trabajos típicos de moldes y matrices o aplicaciones médicas con una fresa de extremo esférico de alta velocidad con velocidades de avance de 200 ipm (50 m/min) o más debido a sus rápidas tasas de aceleración/desaceleración”.
RoboDrill está disponible en tres tamaños:plataforma corta, plataforma mediana y plataforma larga con el control CNC 31i-B5 Nano de FANUC más reciente. Los recorridos X/Y/Z en el modelo de bancada corta son de 300 x 300 x 300 mm; 500 x 400 x 330 mm en el modelo mediano; y 700 x 400 x 330 mm en la cama larga. Las velocidades de avance rápido son de 2125 ipm (54 m/min) en los tres modelos. Los husillos BIG Plus son de 10 000 rpm y 24 000 rpm con un ATC de 21 herramientas.
Las adiciones más recientes al RoboDrill incluyen un servomotor para la torreta, que reduce el tiempo de ciclo, así como características como Ai Overlap, que permite movimientos de radio de arco en el eje Z para reducir el tiempo de ciclo en lugar de esquinas de 90º que requieren una parada. Un control iHMI con pantalla táctil de FANUC permite un uso cada vez mayor de aplicaciones, como Go Probe de Renishaw.
Los RoboDrills están diseñados para combinarse a la perfección con los robots FANUC para paquetes de automatización estándar o para soluciones de automatización personalizadas. Methods tiene una serie de soluciones de automatización estándar "agregadas" en la nueva Serie Plus, incluida la Plus K.
El Plus K permite que RoboDrill funcione sin supervisión a través de un cambiador de herramientas automático extendido y un cambiador de palets automatizado. Las soluciones de automatización personalizadas han sido un enfoque de Methods Automation durante años, según la empresa.
Con el control FANUC 31iB5, RoboDrill tiene capacidad para cinco ejes. Las opciones como AICCII y la búsqueda anticipada de miles de bloques lo hacen capaz de contornear y mecanizar a alta velocidad. Su tamaño y aceleración de 1,5 g lo hacen muy maniobrable y capaz de reducir el tiempo de ciclo entre un 15 y un 50 % en comparación con los VMC estándar, según Corklin.
VMC lineales y en caja
Muchos fabricantes de máquinas-herramienta ahora se inclinan exclusivamente por las máquinas con guías lineales. Pero Doosan Machine Tools America, Pine Brook, N.J., ofrece VMC tanto lineales como en caja, lo que proporciona una amplia gama de opciones de mecanizado.
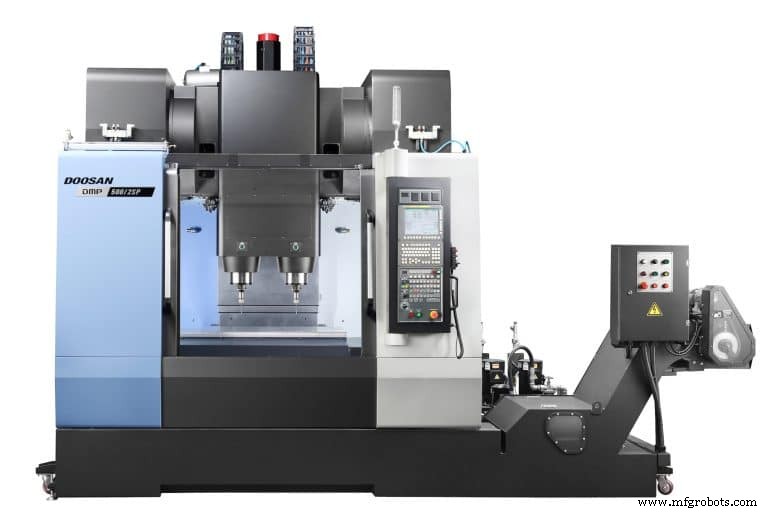
La serie DNM cuenta con guías lineales, husillos BIG Plus de cono 40 y 50 (que vienen de serie en los VMC de Doosan) y velocidades de husillo de 8000 a 15 000 rpm. El modelo S está equipado con 15.000 rpm y rápidos más rápidos. Los recorridos del eje X varían de 20,5″ a 85″ (520-2160 mm) en la línea de modelos.
Para el mecanizado más pesado en materiales más duros, la serie Mynx presenta un diseño de forma de caja, husillos BIG Plus de cono 40 y 50 con cabezal de engranajes o transmisión directa, según el modelo, y un rango de 6000 a 12 000 rpm.
Para los talleres de producción, los modelos incluyen la serie VC con cambiadores de tarimas giratorios y la DMP 500/2SP con dos husillos y dos cambiadores de herramientas. La DMP tiene una mesa de 47,2 x 20,5″ (1200 x 520 mm) y un cargador de hasta 40 herramientas accesible por cada husillo en aproximadamente el mismo espacio que una máquina de un solo husillo. Cada husillo se puede ajustar ligeramente con el eje W para evitar la necesidad de una alineación perfecta de las alturas de fijación o sujeción.
Los verticales de cinco ejes de Doosan incluyen el DNM con mesas giratorias de dos ejes integradas en la plataforma de la máquina. Con una mesa giratoria emparejada con un husillo de 12 000 rpm de cono 40 de transmisión directa, la máquina ofrece un paso adelante con respecto a un VMC estándar.
Por último, las máquinas de cinco ejes DVF ofrecen una solución más integrada, ya sea con una mesa de cinco ejes estilo voladizo o estilo muñón. Los VMC de mesa fija de cinco ejes de la serie VCF ofrecen más en la gama de piezas, ya que los viajes de la máquina y el tamaño de la mesa son más grandes. Los ejes adicionales están en el husillo del cabezal giratorio del eje B o en el eje giratorio incorporado sobre la mesa.
Lista de verificación para evaluar VMC avanzados
Los últimos modelos de centros de mecanizado vertical que salen al mercado tienen características avanzadas, atributos de construcción y componentes que contribuyen a niveles de confiabilidad y eficiencia que nunca se creyeron posibles en un VMC. Según Ellison Technologies, un proveedor de soluciones de mecanizado para las operaciones de corte de metales de América del Norte y sus filiales globales, estas son algunas de las características y capacidades más nuevas que querrá incorporar en su próxima VMC.
Para obtener información sobre las características favorables de los VMC, consulte "Los VMC de nueva generación son más productivos y eficientes que nunca", Ingeniería de fabricación, junio de 2017, que incluye esta información:"Revise cómo se construye la máquina para que en 10, 15 o incluso 20 años , sigue funcionando con la misma precisión que el día que lo instaló. Verifique que el fabricante utilice el análisis de elementos finitos (FEA) para diseñar las piezas fundidas para la cabeza del husillo, la base, la columna y la silleta. La idea es sacar los armónicos naturales de la estructura fuera del rango operativo de la máquina.
“Asegúrese también de que el método de fundición utilizado tenga la licencia de la organización Meehanite Worldwide. Este proceso patentado exige procedimientos de producción de hierro de la más alta calidad, proporcionando rigidez a largo plazo, capacidad de corte de servicio pesado y amortiguación de vibraciones adecuada durante la vida útil de la máquina.
“Otros aspectos destacados de la construcción de una máquina de calidad incluyen una columna piramidal arqueada que se raspa a mano hasta la cama, lo que hace que las dos piezas de fundición se comporten casi como una sola, y también garantiza una geometría ajustada de la máquina que se refleja en la precisión de la pieza. Los cojinetes de husillo de cerámica de alta calidad, los husillos de bolas pretensados de doble anclaje y las guías de movimiento de rodillos lineales se encuentran entre otros aspectos de construcción a considerar. Las guías de rodillos tienen el triple de rigidez y el doble de vida útil que las guías de movimiento con cojinetes de bolas.
“Sobre una estructura sólida, analice los componentes adicionales, como los husillos, el sistema de refrigeración y el mecanismo de transporte de virutas. Todo esto contribuye a la eficiencia. Busque características como un husillo de contacto doble (cónico/frontal) como BIG Plus, monitoreo de carga de herramientas, refrigerante a través del husillo y control de velocidad de avance adaptativo para una aplicación de herramientas y tiempo de ciclo óptimos. Además, comprenda cómo está diseñada la máquina para manejar el calor. Podría decirse que el mayor avance en los últimos años es la aplicación de una variedad de mejoras en la estabilidad térmica”.
Sistema de control de automatización
- ¿Qué es el mecanizado VMC?
- Aplicaciones de la tecnología de impresión 3D de aleación de titanio
- Conozca cómo el mecanizado CNC de precisión contribuye a la productividad
- Mecanizado de Delrin:consejos, ventajas y aplicaciones
- Mecanizado de PEEK:consejos, ventajas y aplicaciones
- Mecanizado de teflón/PTFE:consejos, ventajas y aplicaciones
- Aplicaciones de Centros de Maquinado. ¿Modelos y aplicaciones?
- Introducción al Mecanizado Vertical o CNC VMC
- ¿Necesita una máquina VMC de 5 ejes?
- Cómo la máquina VMC aumenta su productividad
- Tecnología de centro de mecanizado CNC