Mantenimiento preventivo:del tiempo de inactividad al tiempo de actividad
Los fabricantes han lidiado durante mucho tiempo con fallas en los equipos. Si bien pueden ser inevitables, las fallas de los equipos no deberían causar un tiempo de inactividad grave, reducir las ganancias o hacer que los fabricantes gasten demasiado sus presupuestos. Estos suelen ser los peores escenarios y las razones por las que se deben evitar las fallas del equipo.
Estos desafíos se ven agravados por las complejas instalaciones de fabricación actuales, que consisten en redes de datos, hardware integrado y una gran cantidad de sistemas automatizados. Como resultado, la mayoría de los fabricantes no cuentan con suficientes metodologías de mantenimiento. De hecho, un informe de Infraspeak afirma que el 93 % de las empresas consideran que sus procesos de mantenimiento no son muy eficientes.
Esto arroja luz sobre la falta de programas de mantenimiento efectivos en el ámbito de la fabricación, lo que hace que las plantas sean inseguras, menos competitivas y mucho menos rentables.
Afortunadamente, el mantenimiento predictivo ofrece una solución.
Predecir el futuro
El mantenimiento predictivo es una forma de predecir cada escenario posible de falla de hardware, identificando cuándo se requiere mantenimiento y alertando al personal de mantenimiento, cuando sea necesario, además de brindar soluciones preventivas.
Cualquiera que opere dentro del ecosistema de fabricación comprenderá que las fallas y las averías ocurren día tras día. La intención del mantenimiento predictivo no es solo prevenir o reducir estas fallas, sino también ayudar a las plantas de fabricación a lograr estándares de alta eficiencia y entregar productos de calidad en el proceso.
Un programa de mantenimiento predictivo puede reducir las fallas inesperadas hasta en un 90 por ciento, eliminando casi por completo las averías. El primer paso para lograr esto es asegurarse de que su estrategia de mantenimiento siga las mejores prácticas. Por ejemplo, los gerentes de planta deben programar inspecciones periódicas, actualizaciones y resolución de problemas para evitar fallas, formando una base sólida para desarrollar un programa de fabricación predictivo.
Percibiendo el peligro
Para realizar la fabricación predictiva de manera efectiva, el gerente de la planta debe recopilar la mayor cantidad de datos posible. Esto es crucial al implementar cualquier estrategia de mantenimiento preventivo, ya que cuantos más datos estén disponibles para analizar, más precisas serán las predicciones de averías.
Un punto de partida sería utilizar sensores inteligentes. Los sensores inteligentes, junto con los algoritmos de aprendizaje automático, ayudan a detectar anomalías en las máquinas industriales. Además, con algoritmos mejor entrenados, el software puede predecir con precisión cuándo las máquinas corren el riesgo de fallar.
Por ejemplo, los sensores inteligentes que recopilan datos en entornos industriales de IoT pueden realizar un seguimiento de la temperatura e identificar componentes desgastados, como circuitos eléctricos que funcionan mal. Del mismo modo, los sensores inteligentes especializados pueden realizar análisis de vibración en un componente en particular, identificando cualquier caso de desalineación, ejes doblados u otros problemas del motor. A medida que la tecnología se vuelve más avanzada, los sensores inteligentes pueden monitorear más parámetros, brindando una imagen cada vez más precisa de la condición de una máquina.
A partir de estos datos, los fabricantes pueden realizar un análisis de los activos críticos para establecer modos de falla. En este caso, la atención se centra en la frecuencia de las fallas, la gravedad de la falla de la máquina y la dificultad de identificar la falla.
Al conectar dispositivos de monitoreo de condición a un CMMS, los gerentes de planta pueden configurar alertas para informar al personal de mantenimiento sobre cualquier falla o anomalía en el equipo. Esto brinda la oportunidad de planificar el mantenimiento programado cuando es necesario reemplazar las piezas, lo que elimina la posibilidad de que ocurra una falla grave.
Por ejemplo, la tecnología de sensores se puede integrar con varios productos de potencia de fluidos de bajo nivel diferentes, desde conectores, mangueras y tuberías hasta bombas, motores, actuadores y filtros. Algunos de los datos de diagnóstico generados por las válvulas de control podrían ser vitales para solucionar problemas de energía.
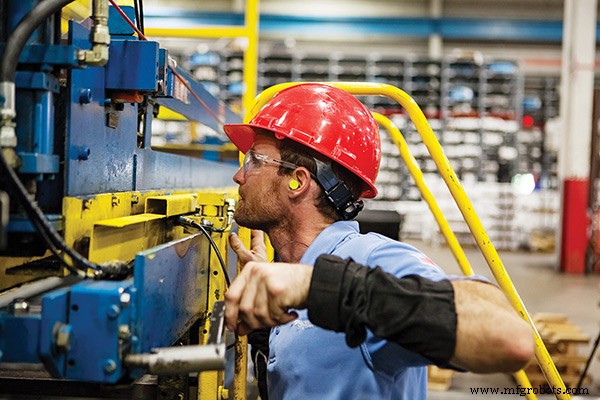
Sobre el tiempo de actividad
Una encuesta reciente realizada por PricewaterhouseCoopers encontró que el 95 % de los encuestados informaron que el mantenimiento predictivo mejoró al menos un factor clave de valor de mantenimiento, y el 60 % observó una clara mejora en el tiempo de actividad del equipo.
Sin embargo, para que los gerentes de planta vean este éxito en sus instalaciones, el uso de sensores para recopilar información sobre el equipo es un componente crítico requerido. Las máquinas recientes generalmente vienen con diferentes opciones para la adquisición de datos en tiempo real, pero los equipos heredados también se pueden adaptar con sensores adicionales de bajo costo. El mantenimiento predictivo puede ser una herramienta vital cuando se trata de activos obsoletos, que requieren una planificación cuidadosa para obtener repuestos obsoletos.
Aquí es donde los consultores expertos de los proveedores de piezas de automatización, como EU Automation, pueden ayudar a obtener piezas y ayudar a aquellos en su proceso de mantenimiento predictivo. Ya sea que los operadores de planta estén buscando sensores inteligentes para comenzar su viaje de mantenimiento predictivo o piezas de repuesto para realizar el mantenimiento correctivo en máquinas heredadas, desarrollar una relación con un proveedor de piezas confiable es esencial.
Si bien cierto grado de falla del equipo es inevitable, no debería causar tiempo de inactividad no programado ni mala calidad de los activos. Esto le cuesta a las industrias de fabricación y procesos miles de millones cada año. En cambio, un plan de mantenimiento predictivo completo y efectivo ayudará a prevenir y reducir significativamente el tiempo de inactividad, al mismo tiempo que aumentará la rentabilidad de una planta a través de un mayor tiempo de actividad.
Sistema de control de automatización
- Diferencia entre mantenimiento preventivo y mantenimiento predictivo
- Comprender los beneficios del mantenimiento predictivo
- Explicación del mantenimiento predictivo
- Medición del éxito del programa de mantenimiento predictivo
- Respuestas a preguntas sobre mantenimiento predictivo
- IoT para mantenimiento predictivo
- ¿Es mejor el mantenimiento preventivo o el predictivo?
- ¿Qué es el Mantenimiento Predictivo?
- Industrias en transición de IoT de mantenimiento programado a predictivo
- El servicio de mantenimiento predictivo reduce las averías de los robots
- 5 Beneficios del Mantenimiento Preventivo