Hacia la fabricación digital de fibras multimateriales inteligentes
Resumen
Las fibras son ubicuas y generalmente pasivas. La optoelectrónica realizada en una fibra podría revolucionar múltiples áreas de aplicación, incluida la electrónica biosintética y portátil, la detección ambiental y la recolección de energía. Sin embargo, la realización de componentes electrónicos de alto rendimiento en una fibra sigue siendo un desafío exigente debido a la elusividad de una estrategia de procesamiento de materiales que permitiría envolver dispositivos fabricados en semiconductores cristalinos, como el silicio, en una fibra de forma ordenada y direccionable. y escalable. Los enfoques actuales de fabricación de sensores de fibra no son escalables o limitan la elección de semiconductores a los amorfos, como los vidrios de calcogenuro, inferiores al silicio en su rendimiento electrónico, lo que da como resultado un ancho de banda y una sensibilidad limitados de dichos sensores en comparación con un silicio estándar. fotodiodo. Nuestro grupo fundamenta una fabricación en fibra universal de circuitos lógicos y sistemas sensoriales análogos a la integración a muy gran escala (VLSI), que permitió la aparición del microprocesador moderno. Desarrollamos una metodología de fabricación híbrida versátil que ensambla arquitecturas de materiales en fibra típicas de dispositivos y sistemas microelectrónicos integrados en sílice, silicio y metales de alta temperatura. Esta metodología, denominada "VLSI para fibras" o "VLSI-Fi", combina la impresión 3D de preformas, un estirado térmico de fibras y un ensamblaje posterior al estirado de dispositivos integrados con fibra mediante la rotura capilar espacialmente coherente y selectiva del material. de los núcleos de fibra. Creemos que este método proporcionará una nueva clase de sensores y dispositivos de fibra penetrantes, duraderos y de bajo costo, que permitirán la integración de tejidos con objetos hechos por humanos, como muebles y ropa, en el Internet de las cosas (IoT). Además, impulsará la innovación en la impresión 3D, ampliando el enfoque de fabricación digital al ámbito de la nanoelectrónica.
Introducción
Aunque las fibras de vidrio estirado se remontan a la época romana, las primeras fibras ópticas funcionales fueron fabricadas en 1792 por los hermanos franceses Chappe con fines de comunicación [1]. En 1842, Jean-Daniel Colladon, un físico suizo, demostró que la luz podía ser guiada internamente a través de un chorro de agua [2]. Estos dos descubrimientos dieron lugar a décadas de mejoras en la ingeniería óptica y de materiales que condujeron a las fibras eficientes de hoy en día, que permiten el almacenamiento de datos y telecomunicaciones de alta velocidad a lo largo de kilómetros de distancia en todo el mundo, como el cable submarino transpacífico (TPC) de 25.000 km de longitud completado. en 1996 [3, 4]. Además, los sensores de fibra óptica (FOS) se utilizan para una amplia variedad de aplicaciones biomédicas, de petróleo y gas, marinas, arquitectónicas, químicas y aeroespaciales [5, 6].
El control y el rendimiento mejorado de la propagación de la luz utilizando fibras de cristales fotónicos (PCF) desarrollado en 1996 por Philip Russel abrió las puertas para la investigación en estructuras funcionales internas de fibra más complejas [7,8,9]. Las nuevas microestructuras también acogieron con satisfacción la integración de la diversidad de materiales en su constitución [10, 11] para diseñar fibras inteligentes para electrónica [12], optoelectrónica [11], síntesis en fibra [13], microfluídica [14], sistemas microelectromecánicos [15, 16] e interconexión biosintética [17]. Las fibras inteligentes se diferencian de las fibras tradicionales al incluir una función no tradicional más allá de la comunicación óptica y el uso típico de fibras en tejidos comerciales. Las fibras inteligentes se pueden utilizar para la estética en textiles electrónicos controlando la apariencia coloreada de las fibras debido a la interferencia óptica en su microestructura [18] o para mejorar el rendimiento, por ejemplo, en el caso de guías de fibra óptica convencionales y revestimiento de espejo dieléctrico que permite la guía de la luz. a través del aire [19, 20].
Para que una fibra sea funcional, debe estar compuesta de materiales con diferentes propiedades electrónicas, su arquitectura debe estar diseñada específicamente para realizar una función determinada y sus características internas deben reducirse a nanoescala, órdenes de magnitud más pequeñas que el núcleo de las telecomunicaciones actuales. fibras. Las fibras se crean típicamente mediante métodos de fabricación de fibra óptica, es decir, se extraen térmicamente a partir de varillas macroscópicas cilíndricas o cuboides llamadas "preformas". El proceso de fabricación comienza con una selección de materiales de revestimiento y núcleo adecuados, como metales, aislantes y semiconductores. Por ejemplo, la primera fibra que incluye estructuras de metal-aislante-semiconductor se desarrolló en 2004 para fotodetección [21]. Los materiales para la preforma se seleccionan de modo que sus viscosidades, μ , son comparables a la temperatura de extracción, cayendo aproximadamente en la ventana de 4
La preforma, que es esencialmente una versión ampliada de la fibra, se puede construir utilizando una variedad de técnicas como enrollar láminas de material como una alfombra, apilar piezas fresadas como un rompecabezas o imprimir en 3D, como se muestra en la Fig. 1a. (I) y discutido en esta revisión, y luego consolidado por una sinterización al vacío. Luego, la preforma se calienta en un horno y se alarga en una fibra como un caramelo o un caramelo (ver dibujo del cono en la Fig. energías, adhesión mutua y expansión térmica diferencial (Fig. 1a (III)) [22]. Este proceso, para el caso de una preforma impresa en 3D, se ilustra esquemáticamente en la Fig. 1a. Un estirado típico puede producir kilómetros de fibra con diámetros de sección transversal a nanoescala muy finos de alrededor de 5 nm [23, 24].
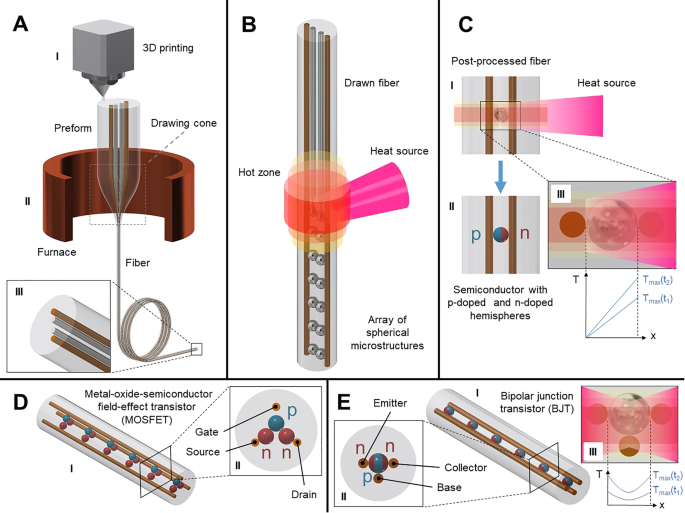
VLSI-Fi:Esquema conceptual de la técnica VLSI-Fi que representa el enfoque “2D + 1D + 0D” . un La preforma impresa en 3D a (I) está estirado térmicamente a (II) en una fibra larga y delgada que conserva la geometría de la sección transversal de la preforma (2D). b Modelado axial de la fibra a través de la ruptura capilar selectiva del material y espacialmente coherente (+ 1D), lo que da como resultado el ensamblaje de núcleos separados inicialmente continuos en conjuntos de dispositivos discretos contactados en paralelo. c Control de dopaje impulsado por segregación en partículas semiconductoras posteriores a la ruptura, lo que permite el control de la arquitectura interna de un dispositivo individual c (II) mediante gradiente térmico c (III). d (I) Ilustración esquemática del transistor de efecto de campo semiconductor de óxido metálico (MOSFET) a través de VLSI-Fi, donde los semiconductores de tipo p y tipo n se muestran en azul y rojo, respectivamente. Las varillas doradas continuas incrustadas en una fibra de sílice actúan como puerta, fuente y drenaje. La sección transversal de la fibra resultante se muestra en d (II). Del mismo modo, e (I) muestra una imagen esquemática de un transistor de unión bipolar (BJT) realizado por VLSI-Fi, logrado con fuentes de calor incidentes tanto del lado del emisor como del colector. La sección transversal de la fibra e (II) muestra el emisor, el colector y la base del BJT (varillas continuas incrustadas en la fibra), con los semiconductores tipo p y tipo n de la unión n-p-n mostrados en azul y rojo, respectivamente
En un paso posterior al estirado, jugando con las inestabilidades capilares, la fibra se puede volver a licuar mediante calentamiento para permitir la ruptura de los núcleos de una manera selectiva de material espacialmente coherente, lo que permite un control axial sobre las estructuras incrustadas de fibra [25,26, 27] como se ilustra en la Fig. 1b. Las técnicas alternativas para modelar los núcleos axialmente incluyen la exposición a los rayos UV a través de fotomáscaras en los núcleos fotopoliméricos, lo que da como resultado micropartículas de forma no trivial [28]. Otras técnicas de funcionalización híbrida incluyen el revestimiento de las superficies de las fibras con materiales funcionales [10, 29] y el confinamiento de un revestimiento de fibras mediante un estiramiento [12] a una matriz de dispositivos optoelectrónicos fabricados mediante la fabricación estándar de semiconductores de óxido de metal complementario (CMOS).
Las fibras se pueden tejer en telas o redes para lograr una funcionalidad colectiva que supere la de una fibra individual [30]. Diseñadas mediante biomimetismo, las fibras pueden moldearse de acuerdo con las características útiles de la naturaleza para mejorar la funcionalidad del tejido, como la hidrofobicidad [31]. Las fibras también pueden concebirse como plataformas de síntesis para la producción de material económico, como la conversión de núcleos de aluminio en silicio en fibras revestidas de sílice [13] o la fabricación inducida térmicamente de estructuras porosas mediante separación de fases [32]. Las fibras también pueden servir para la detección de señales remotas y distribuidas, como la detección química ambiental de volátiles peligrosos [29]. La flexibilidad en el diseño de la fibra es tal que se pueden integrar múltiples modalidades funcionales en una fibra para aplicaciones complejas como la estimulación espinocortical profunda y la monitorización en ratones para la investigación de enfermedades neurodegenerativas [33]. Estos ejemplos muestran algunos de los dominios en los que las fibras inteligentes son la solución natural.
Motivación
Aunque las fibras son universalmente ubicuas, la integración de sistemas microelectrónicos de alto rendimiento dentro de una fibra delgada sigue siendo un gran desafío [11, 12]. Se han propuesto diferentes enfoques para abordar este desafío, con esfuerzos principalmente centrados en materiales de baja temperatura. Por ejemplo, la deposición química en fase de vapor a alta presión (HPCVD) se ha utilizado para integrar semiconductores compuestos en fibras ópticas microestructuradas (MOF) [34], así como para crear fibras de unión p-i-n de silicio flexibles [35]. Alternativamente, un CO 2 Se utilizó láser para la recristalización del núcleo de SiGe en fibras de sílice para diseñar sus propiedades electrónicas [36]. Dichos enfoques dan como resultado dispositivos con un ancho de banda electrónico limitado, como es el caso de los materiales calcogenuros, que son intrínsecamente amorfos o inherentemente no escalables.
Como tal, el Laboratorio de Fibras y Sistemas Habilitados para Fabricación Aditiva (Laboratorio FAMES) ha desarrollado y actualmente implementa una técnica para controlar la arquitectura 3D de fibras, que se describe en esta revisión. Dado que la complejidad de la fibra final se correlaciona con la complejidad de la sección transversal de la preforma, la fabricación de forma libre de las preformas permite funcionalidades del dispositivo de fibra inalcanzables de otro modo. Además, la impresión 3D es ampliamente accesible, lo que la convierte en una alternativa tecnológica rentable y fácil de usar a los métodos empleados tradicionalmente, permitiendo una amplia gama de materiales, desde termoplásticos hasta materiales de alta temperatura, así como biomateriales [37].
Además, el Laboratorio FAMES tiene la capacidad de procesar materiales de alta temperatura, junto con el uso más tradicional de termoplásticos en la fabricación aditiva, lo que nos permite aprovechar propiedades como la alta movilidad de electrones en Si / Ge [38], así como el uso futuro de titanato de circonato de plomo (PZT) / BaTiO 3 compuestos para aplicaciones piezoeléctricas que tienen grandes coeficientes piezoeléctricos en comparación con los polímeros [39, 40] y un mayor ancho de banda acústico [41].
Con estos desafíos en mente, proponemos soluciones de optimización utilizando fabricación aditiva para lograr una fabricación de preformas más rápida y compleja, simulaciones de rotura capilar para optimizar el control axial de la fibra y combinaciones de nuestras fibras con ingeniería de tejidos. Estas estrategias permiten la creación de plataformas biomédicas realistas con capacidades de biodetección y biofuncionalización para el análisis de fármacos y tratamientos in vitro como una de las aplicaciones prometedoras de dispositivos de fibra.
Concepto
Para realizar fibras funcionales, nos inspiramos en la integración a gran escala (VLSI), una técnica de fabricación y diseño digital que dio origen al microprocesador moderno en la década de 1970. Esta técnica utiliza fotolitografía y tratamiento químico / térmico de las áreas expuestas de la oblea del sustrato semiconductor para definir las características del circuito integrado en esta capa (2D) mientras avanza la fabricación de un circuito completo apilando dichas capas individuales en la dirección perpendicular a la superficie de la oblea (+ 1D). Además, el dopaje electrónico de los componentes individuales del circuito (+ 0D) se puede controlar mediante implantación y activación térmica [42]. Nuestro enfoque de las fibras, denominado "VLSI para fibras" o "VLSI-Fi", es análogo:primero, la fabricación aditiva y el estirado térmico de una preforma definen la geometría de la sección transversal del dispositivo de fibra (2D); en segundo lugar, la fibra resultante puede luego modelarse axialmente (+ 1D), lo que permite el ensamblaje de matrices de dispositivos discretos integrados a partir de núcleos inicialmente continuos pero separados; y tercero, se puede realizar la estructuración impulsada por la segregación de dispositivos individuales integrados en fibra (0D). La Tabla 1 hace una comparación entre las dos técnicas, destacando la correspondencia entre cada grado de control de geometría hecho posible por cada técnica (“2D + 1D + 0D”). Los esquemas de los pasos descritos se muestran en detalle en la Fig. 1, donde se podrían realizar ejemplos de posibles dispositivos integrados en fibra utilizando la técnica VLSI-Fi.
Sección experimental
En esta sección, primero describimos nuestro trabajo en la impresión 3D de preformas de policarbonato, seguido de los avances recientes en la impresión 3D de vidrio mediante estereolitografía. Luego, nos acercamos al patrón axial de las fibras a través de una ruptura capilar selectiva del material, espacialmente coherente, que permite el ensamblaje de núcleos separados inicialmente continuos en arreglos de dispositivos discretos contactados en paralelo. Finalmente, proponemos la aplicación de nuestras fibras de biointerfacción, combinadas con ingeniería de tejidos para monitorear el crecimiento de tejido viable in vitro. Las funciones se habilitan mediante el uso de canales de microfluidos en fibra para entregar células y señalización de bioquímicos y alambres de aleación con memoria de forma para control de movimiento, y elementos piezoeléctricos para mapear el entorno mediante ondas de ultrasonido.
Dibujo de preformas impresas en 3D
Como se indicó anteriormente, las técnicas de fabricación de preformas convencionales, como el laminado de película delgada y el apilado y sin procesar [10], están limitadas en la producción de estructuras geométricas complejas, requieren una cantidad significativa de tiempo en el proceso de estiramiento de la fibra y requieren mano de obra y equipo caro. La impresión 3D aborda estos problemas con la ayuda de material de soporte soluble y su proceso parcialmente automatizado y fácil de usar. Esto permite la impresión de geometrías muy complejas con facilidad en un período de tiempo relativamente corto.
Para evaluar la influencia del ángulo de impresión de las preformas de policarbonato (Hatchbox 3D), se imprimieron barras cilíndricas y cuadradas utilizando una impresora FDM Prusa i3 MK2 de un solo cabezal. Las temperaturas de la extrusora y del lecho de impresión se establecieron en 235 ° C y 105 ° C, respectivamente, y la impresora se configuró para producir preformas de relleno al 100% con una boquilla de 0,35 mm. La orientación de las capas en la preforma depende de la orientación horizontal de la pieza con respecto al lecho de impresión, y cuando la preforma se introduce en el horno durante la extracción térmica, el flujo de calor se ve afectado por la orientación de la capa. Para probar qué orientación era la más adecuada para el estirado térmico, se imprimieron preformas con orientaciones de 0 °, 15 °, 30 °, 45 ° y 90 °. Todos los ángulos se midieron entre el eje longitudinal de la preforma y el eje horizontal. Las preformas impresas en 3D se sometieron al proceso de estirado térmico en un horno con tres zonas de temperatura de 90 ° C, 100 ° C y 200 ° C. Para las preformas cilíndricas, el estiramiento térmico fue exitoso en ángulos de 0 ° y 45 °. Los estiramientos de la preforma de 90 ° siempre fallan debido a la delaminación de la capa.
También pudimos dibujar con éxito estructuras que no estaban en equilibrio, como una varilla cuadrada con un patrón de relleno improvisado como se muestra en la Fig.2a (I), donde en lugar del patrón de relleno rectilíneo, el relleno también se configuró para seguir los perímetros e imprimir en estructura ordenada. El estiramiento de la preforma basado en un cuadrado de 0 ° tuvo éxito y, aunque se deformó ligeramente, la fibra aún podía conservar la forma de la preforma. Se estiraron con éxito fibras con dimensiones tan bajas como 40 µm × 60 µm y se muestran en la Fig. 2a, sin deslaminación de capas. Además, todas las capas se consolidaron correctamente. Un ejemplo de una sección transversal de fibra se muestra en la Fig.2a (IV), y las imágenes de una fibra antes y después del recocido se muestran en la Fig.2a (V) y 2a (VI), respectivamente, donde vemos que la fibra recocida logra la transparencia óptica, que se caracterizará en trabajos futuros. De estos experimentos, llegamos a la conclusión de que las preformas más exitosas son las impresas a 0 °, mientras que a 90 ° siempre se deslaminan durante el proceso de estirado. La consolidación de capas en las fibras termoestiradas mejoró a medida que disminuyó el ángulo de orientación de la preforma impresa en 3D.
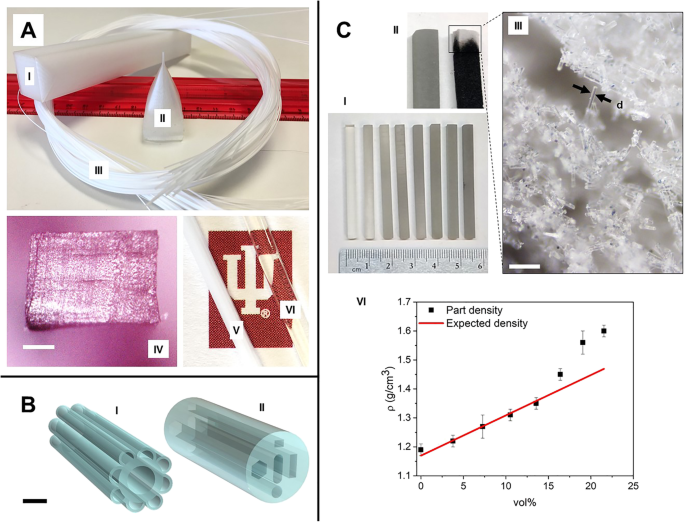
Preformas impresas en 3D: a (I) Preforma de policarbonato impresa en 3D de base cuadrada. un (II) Dibujo de cono. un (III) Fibra de policarbonato resultante después del estirado térmico. un (IV) Sección transversal de la fibra después del proceso de estirado, sin deslaminación de capa. La sección transversal es rectangular debido a la porosidad no isotrópica del patrón de relleno (barra de escala 200 μm). un (V) Fibra estirada antes del recocido. un (VI) Fibra estirada después del recocido con aparente transparencia óptica. b Modelos CAD de preformas de vidrio, realizados con éxito en vidrio sodocálcico con impresión 3D basada en extrusión de alta precisión. b (I) La estructura imita el pelo de la tarántula azul. b (II) Modelo de preforma con geometría de sección transversal en no equilibrio (barra de escala 1 cm). c (I) Muestras de vidrio de forma cuadrada con relleno de vidrio creciente (de izquierda a derecha), impresas con técnica SLA. c (II) Detalle de la muestra de vidrio antes de hornear (izquierda) y durante el horneado (derecha). En este último, es posible ver la coloración negra resultante de los residuos carbonizados de resina, mientras que la punta presenta una coloración blanca después de la ceniza de estos residuos. c (III) Fotografía microscópica de la sección de cenizas (barra de escala 200 μm), donde la coloración blanca es el resultado del color natural de las fibras trituradas compactadas en una estructura porosa interconectada. Además, el ancho nominal de la fibra de vidrio, indicado en la imagen por d, se correlaciona con los valores esperados de 16 μm (# 38 Fiber Glast). c (IV) Un gráfico de las densidades de las preformas de vidrio impresas ( ρ ) en función de la fracción de volumen de fibras de vidrio mezcladas con resina, junto con la densidad media del material de impresión
Impresión 3D de preformas de vidrio
Más allá de los termoplásticos, los vidrios, incluido el cuarzo fundido, tienen importantes aplicaciones científicas y de ingeniería en óptica, comunicaciones y electrónica [43]. Las fibras de sílice estructuradas podrían beneficiarse de múltiples aplicaciones, por ejemplo, la coloración sin tintes de telas para la moda, fibras de cristal fotónico para detección óptico-química o fibras monomodo para telecomunicaciones y enfoque estrecho de la luz. Estas fibras se fabrican generalmente mediante un proceso de dos pasos:la fabricación de la preforma y el estiramiento térmico de las preformas en una fibra. Si bien el proceso de estirado es relativamente simple y económico, la fabricación de preformas, en este punto, requiere un tratamiento caso por caso, y para cada configuración de preforma específica, se debe desarrollar y aplicar una tecnología separada.
La Figura 2b muestra modelos de diseño asistido por computadora (CAD) de preformas de vidrio sodocálcico que se realizaron con éxito con alta precisión en tecnología de impresión basada en extrusión similar a los productos descritos por la empresa Micron3DP [44]. Este material tiene propiedades ópticas prometedoras, especialmente en longitudes de onda largas como IR [45], lo que lo convierte en un candidato interesante para la fabricación de fibras con nuevas funcionalidades ópticas. El modelo de preforma que se muestra en la Fig. 2b (I) imita la estructura del pelo de la tarántula azul, similar a la estructura presentada en [46], y en la Fig. 2b (II), la sección transversal de la preforma contiene geometrías que no están en equilibrio y es por lo tanto, propenso a la remodelación debido a la minimización de la tensión superficial. Estos modelos fueron diseñados y realizados como una verificación de la posibilidad de lograr secciones transversales complejas de preformas que no están en equilibrio.
Dado que la estructura del revestimiento proporciona integridad mecánica a la fibra durante el proceso de estirado, ya que está compuesta del material más viscoso, nuestros esfuerzos hasta ahora se han centrado en este componente de la fibra, donde, en última instancia, nuestro objetivo es la conservación de la geometría de la sección transversal. de la preforma. A largo plazo, nuestro objetivo es desarrollar técnicas de extrusión multimaterial, que nos permitirán integrar múltiples materiales de forma monolítica en una misma impresión. Alternativamente, es posible llenar la estructura con materiales en polvo como Si o Ge. A continuación, la estructura cargada se puede sinterizar para obtener la preforma. Gumennik y col. han descrito un enfoque similar [47].
Si existe interés en producir una fibra con vidrio de cal sodada como material de núcleo, un enfoque simple sería imprimir una preforma de núcleo suspendido. Las fibras de núcleo suspendido son de interés para diversas aplicaciones, incluida la detección [48] y la guía de terahercios de baja pérdida [49], y normalmente se realizan con polímeros [49]. En este tipo de geometría de fibra, el núcleo está soportado por puntales que lo conectan a la capa exterior. Después del dibujo, estas estructuras se reducen a dimensiones del orden de la longitud de onda de interés, de manera que, para la luz guiada, el efecto es el de un núcleo suspendido. Monro y col. han informado fibras de núcleo suspendido en varios materiales, como sílice y vidrio de bismuto [48]. También proporcionan una serie de ejemplos de aplicaciones de detección de estas fibras, particularmente en detección biológica y química, lo que confirma la viabilidad de estas geometrías de fibra.
Se han diseñado enfoques novedosos para la impresión 3D de vidrio basada en estereolitografía utilizando resinas personalizadas utilizando nanocompuestos de sílice fotocurables [50]. Aquí, proponemos un método en el que las preformas de fibra de vidrio se fabrican mediante impresión 3D basada en resinas comerciales disponibles en el mercado, lo que lo convierte en un método rentable y más simple para lograr piezas de vidrio impresas en 3D mediante estereolitografía (SLA). La impresora SLA (Form 2 de Formlabs) funciona con un láser con una longitud de onda de 405 nm para entrecruzar la resina a través del fondo de la tina a medida que la plataforma construida aumenta gradualmente capa por capa.
Para obtener impresiones de vidrio, utilizamos una mezcla de resina transparente comercial (Formlabs FLGPCL04 Clear) con fibras de vidrio de borosilicato de 0,79 mm (1/32 ") (# 38 Fiber Glast) para el proceso de impresión. Esto permite un gran control de la composición final del material de impresión y flexibilidad para lograr las propiedades deseadas de la fibra. Las fibras de vidrio se dispersaron en resina transparente usando un agitador magnético. El vidrio se agrega en pequeños incrementos y se homogeneiza durante aproximadamente 3 minutos después de cada adición. Para el proceso de impresión, la impresora se configuró en modo abierto para permitir el uso de nuestra resina personalizada. Se imprimieron preformas cuboides de dimensiones 4 × 4 × 50 mm con una orientación de 90 °. Después de la impresión, las piezas se sumergieron en isopropanol durante 10 minutos para eliminar el exceso de resina , y poscurado con luz ultravioleta durante 30 min a 60 ° C.En la Fig. 2c (I) se muestran preformas de vidrio curado con una proporción de volumen creciente de fibras de vidrio mezcladas con la resina de impresión (de izquierda a derecha).
A continuación, las preformas se procesan posteriormente para desligar la resina residual y sinterizar las partículas de vidrio, lo que da como resultado una parte compuesta completamente de vidrio. Los efectos de estos procesos sobre la preforma se ilustran en la Fig. 2c (II), donde vemos una preforma después del curado (izquierda) y después del proceso de horneado (derecha). En este último, se puede apreciar la coloración negra resultante de la cocción en un horno de incineración, mientras que la punta presenta una coloración blanca después de la desunión. La Fig. 2c (III) muestra una imagen microscópica de una preforma antes de la sinterización, donde se puede ver que toda la resina de hecho se hornea fuera de la pieza, dando como resultado una estructura interconectada formada solo por las fibras de vidrio. Se deben controlar varios parámetros, como la temperatura de horneado y el perfil de calentamiento, para controlar las reacciones químicas y la contracción. La desaglomeración térmica del aglutinante se logró utilizando un horno de incineración. Las partes marrones resultantes se sinterizaron en un horno tubular de alta temperatura. La sinterización se realizó a una temperatura de 1300 ° C y una presión de 5 × 10 −2 mbar, siguiendo el protocolo prescrito en [51]. Se fijó una fase de mantenimiento a 800 ° C para evaporar el agua unida a moléculas y los grupos silanol unidos a la superficie. La sinterización al vacío mejora la transparencia óptica, ya que reduce la retención de aire dentro de la pieza de vidrio sinterizado [52].
Después del posprocesamiento, se miden el volumen y el peso de las piezas para obtener la densidad. Luego, esto se compara con la densidad promedio del material de impresión, compuesto por la resina curable y la mezcla de fibra de vidrio, que se calcula mediante ρ prom = ρ resina (1 - χ v ) + ρ vidrio ( χ v ), donde ρ resina =1,17 g / cm 3 es la densidad de la resina transparente curada, ρ vidrio =2,55 g / cm 3 es la densidad de las fibras de vidrio molidas, y χ v es la relación de volumen de las fibras de vidrio mezcladas con la resina.
Los resultados se muestran en la Tabla 2 y gráficamente en la Fig. 2c (IV), donde presentamos la densidad de las piezas impresas para diferentes proporciones de volumen de fibra de vidrio en la resina, en comparación con la densidad promedio del material de impresión. Observamos que, para menores proporciones de volumen de vidrio mezclado con la resina, los resultados obtenidos caen dentro de lo esperado. Sin embargo, a concentraciones de vidrio más altas, vemos una desviación del comportamiento lineal de la densidad ideal. Esto se puede atribuir a la sedimentación durante la impresión, que se vuelve significativa en estas proporciones de volumen, produciendo así efectivamente concentraciones más altas de vidrio en esas impresiones. El proceso de impresión ocurre en el fondo del tanque, donde la concentración de vidrio, debido a la sedimentación, crece constantemente durante la impresión. Comienza desde (y por encima) la concentración uniforme inicial que debe caer en la curva calculada.
En la Tabla 2, podemos ver que a un 21,54% en volumen de fibras de vidrio molidas en piezas de relleno, la densidad medida fue 1,61 g / cm 3 , lo que significa que la proporción de volumen real es 31,88% en volumen. Durante el proceso del experimento, obtuvimos una muestra con un relleno real de fibras de vidrio molidas al 34,78% en volumen. Este resultado no estaba muy lejos del relleno de sílice al 37,5% en volumen que fue fabricado por Kotz et al. [53], donde se desarrolló una resina personalizada, en contraste con la resina comercial que usamos en este trabajo. Las direcciones futuras de este trabajo incluyen procedimientos de tratamiento térmico, sinterización de piezas y el estudio de las propiedades mecánicas y ópticas de las piezas resultantes.
Control coherente de separación y desintegración capilar selectiva por material del dopaje
Una vez que se estira térmicamente una preforma, el resultado es una fibra larga y delgada en la que se conserva la sección transversal, como se muestra en la Fig. 1a (III). En el caso de una fibra con uno o más núcleos, estos pueden modelarse axialmente a través de un proceso de ruptura capilar selectivo de material y espacialmente coherente [26], que se muestra en la Fig. 3. Mientras que el modelo de Tomotika explora la formación de inestabilidades periódicas en un cilindro de fluido infinito, uniformemente calentado, que tiene en cuenta los efectos del fluido circundante [55], la propagación de las inestabilidades de Rayleigh introduce el concepto de propagación frontal [56]. Aunque en la literatura se pueden encontrar varios ejemplos de tratamientos matemáticos de inestabilidades capilares, como en Liang et al. [57], estos trabajos se centran principalmente en regímenes isotérmicos, que no son aplicables en nuestro caso. Además, nuestro caso tiene la complicación adicional de propagar el gradiente térmico y, por lo tanto, el gradiente de viscosidad. Como tal, probablemente esté más cerca del proceso impulsado por criterios de inestabilidad marginal, como se menciona en Powers et al. [56]. Al combinar nuestros resultados computacionales y experimentales, nuestro objetivo es establecer un modelo matemático para la ruptura de la fibra a través de fenómenos de gradiente térmico axial.
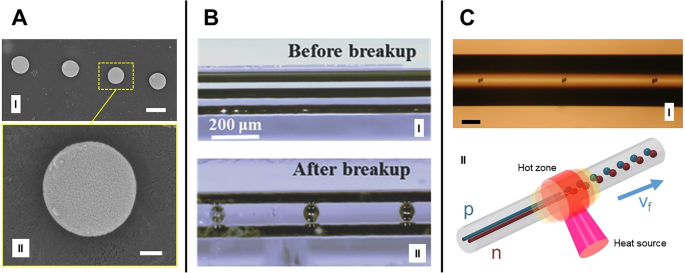
Desintegración capilar: a (I) Sección de fibra que muestra esferas de Si formadas por rotura capilar (barra de escala 0,5 μm). un (II) Imagen de esfera única que representa la calidad de la forma (barra de escala de 100 nm), de Gumennik et al. [26]. b (I) Ejemplo de dispositivo fotodetector de metal-semiconductor-metal en una sola fibra de sílice antes de b (I) y después de b (II) proceso de ruptura, de Wei et al. [54]. c (I) Descomposición de una fibra de doble núcleo en grupos biesféricos (barra de escala de 100 μm), de Gumennik et al. [26]. c (II) Representación esquemática del proceso mostrado en c (I), con núcleos de tipo p y n mostrados en azul y rojo, respectivamente
La etapa actual de la simulación de ruptura capilar se centra en el régimen estacionario. Nos interesa analizar cómo se desarrollan por primera vez las inestabilidades en una fibra inicialmente estacionaria sometida a un gradiente térmico. Este proceso es análogo al paso inicial de los experimentos de ruptura capilar realizados por Gumennik et al. [26], donde una fibra de sílice con un núcleo de Si de 4 μm de espesor se alimenta a través de la zona caliente de una llama de hidrógeno-oxígeno a flujos de 0,3 y 0,1 L / min, respectivamente. Aunque la temperatura máxima alcanzable con este tipo de soplete puede alcanzar hasta 2800 ° C, la temperatura máxima experimentada por la fibra debe estar por debajo del punto de ebullición de la sílice de 2230 ° C.
Considering that the flame width is between 3 and 3.5 mm and that the fiber has a diameter of about 300 μm, it is easy to understand why it is not feasible to experimentally measure the temperature gradient to which the fiber is exposed. Furthermore, the dynamic nature of the breakup process and the fact that it involves multiple materials with varying emissivities further adds to the complexity of the problem, while the fiber’s high aspect ratio and sharp viscosity ratios render the numerical simulation of the full Navier-Stokes equations computationally challenging.
In our simulations (using COMSOL Multiphysics® 5.3a, with its Microfluidics and Heat Transfer modules) shown in Fig. 4a, we assume an axisymmetric fiber with radius r fiber = 140 μm, composed of a thin Silicon core (r core = 2 μm) enclosed in a Silica cladding. Initial heat-transfer simulations showed that a fiber length of 15 mm is sufficient to ensure that the fiber extremities remain at room temperature, thus avoiding influence from the boundaries to the breakup process. Through the sweep of different parameters such as heat source length and distance to the fiber surface, as well as power, we can observe the changes produced in the breakup behavior, thus collecting information about the temperature gradient. Also of importance are the breakup period and speed, parameters which can be compared to experimental results and used for the refinement of the simulations.
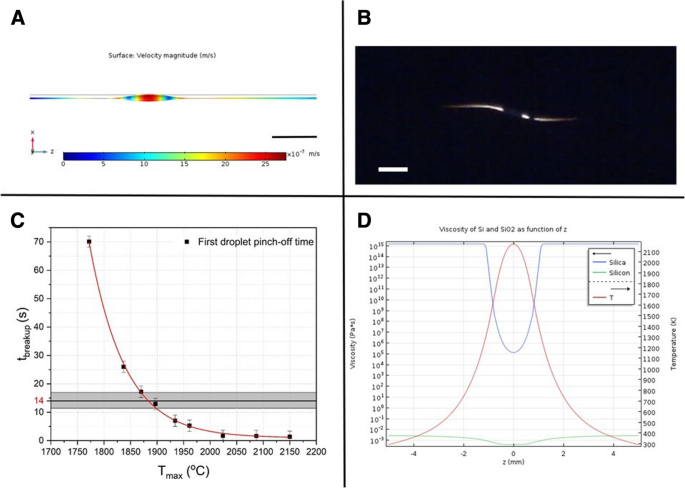
Capillary breakup simulations:a Image of the simulated Si core during the first droplet formation, right before the pinch-off for T max = 1900 °C. Color scale represents surface velocity (scale bar = 50 μm). b Snapshot of fiber breakup experiment recording just after the first droplet pinch-off, indicating a breakup time of 14 ± 3 s (scale bar = 60 μm). c Breakup time t breakup for different values of T max . The exponential dependence of t breakup on T max is evident, a behavior that is expected due to the dependence of t breakup on the core’s viscosity, which in turn depends exponentially on the temperature. The shaded rectangle encompasses the temperature range compatible with this breakup time-scale. d Si core and SiO2 cladding viscosities as a function of axial position, with temperature pro le over-imposed, for T max = 1900 °C
The simulations are performed in two steps:first, the steady-state temperature profile is calculated for different heat source powers, in order to achieve the desired maximum temperature T max . The results are then exported to a time-dependent fluid-flow simulation, where the Navier-Stokes equation is solved with time steps of 0.05 s, from 0 s until the first droplet pinch-off (t breakup ), which is dependent on T max , as can be seen in Fig. 4c, where t breakup is plotted for different values of T max . It is possible to observe that t breakup has an exponential dependence on T max , which is expected since t breakup is proportional to the core’s viscosity, which in turn is exponentially dependent on the temperature.
The relevant parameters used in these simulations are listed in Table 3. Preliminary simulations indicate that the phase transition of the Si core has no significant influence on the steady-state temperature pro le obtained, neither on the subsequent fluid-flow simulations since, in the entire region where the capillary instabilities occur, the temperature is higher than the melting point of Si. Therefore, in order to maintain the model as less computationally intensive, we simulate a core of liquid Si as a first approximation. Moreover, although a fully coupled heat-transfer and fluid-flow simulation is preferable, we consider that the effects of coupling bring second-order corrections to the solution and thus can be neglected at this stage. An image of the simulated core during the first droplet formation, right before the pinch-off, is shown in Fig. 4a, for T max = 1900 °C. A plot of the densities of silica and silicon, as a function of the axial position (in the simulation, the z-axis) for this particular simulation, is presented in Fig. 4d, with the temperature profile over-imposed.
Our results allow us to define the ranges of viscosities for which the time scales for breakup are comparable to those observed experimentally, thus assessing qualitatively the temperature profile imposed on the fiber. Fig. 4b shows a snapshot of a fiber breakup experiment recording just after the first droplet pinch-off, at the frame corresponding to t = 39 s. Since the resolution of the images before this frame is not ideal, judging on the basis of the symmetry of the breakup behavior, it is possible to assess that the pinch-off of the first droplet occurs at t = 35 ± 3 s, which translates to a breakup time after the temperature steady-state regime is achieved, of 14 ± 3 s. The shaded rectangle in Fig. 4c encompasses the temperature range compatible with this breakup time-scale, from which we can infer that the maximum temperature to which the fiber is exposed is 1885 ± 15 °C. With the collection of statistics on the breakup behavior in the future, we aim to develop a procedure for the temperature measurement of the process, which is otherwise unattainable by conventional means [26, 58, 59].
Moreover, segregation-driven control of doping in post-breakup semiconducting particles is attainable, allowing to control an individual device’s internal architecture. It is possible to control the structure of a single sphere, as was demonstrated by Gumennik et al. [47] shown in Fig. 5. When the droplet is exiting the flame, it experiences a thermal gradient:it is colder on the end distant from the flame, and consequently, it is expected to solidify laterally, starting from the colder side. If the sphere is doped with a material that is more soluble in a liquid than in a solid, this dopant will be repelled into the liquid as the solidi cation front propagates, collecting predominantly on the hot side. This effect is shown schematically in Fig. 1c and can be used to synthesize structured particles, composed for example of Ge-rich Si, (as shown in Fig. 5):Starting with 50:50 Si-Ge mixture in the fiber core, after the breakup the sphere will solidify, such that the Ge is extruded into the melt as the solidi cation evolves, leading to anisotropic distribution and resulting in axially oriented Janus particle heterojunctions [47]. This method can be extremely useful in assembling complex fiber-embedded devices such as heterojunctions, as shown in Fig. 1d and e.
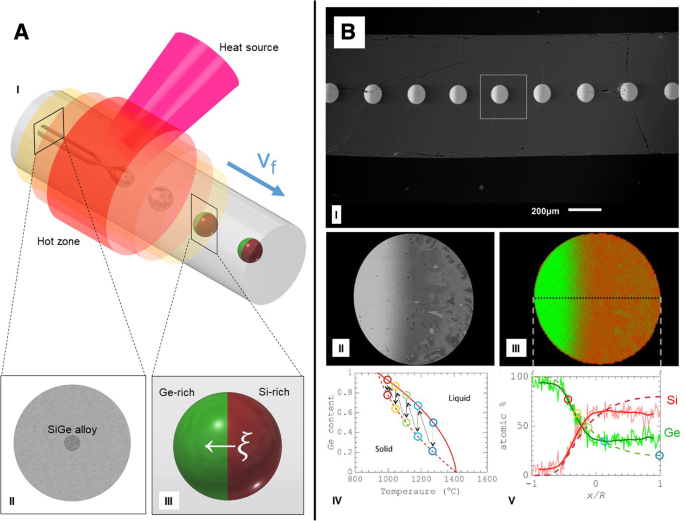
Segregation control of doping:a (I) Schematic illustration of the segregation-driven control of doping in post-breakup semiconducting particles. Details:cross section of a Ge-rich Silicon continuous core in silica fiber a (II) and post-breakup schematic drawing of doping-segregated sphere, or Janus particle, with the Ge-rich side indicated in green a (III). b (I) Scanning Electron Microscope image in backscattered mode of the fiber, polished along its axis, showing an array of Janus particles. b (II) Detail of single Janus particle cross section. b (III) Energy-dispersive X-ray spectroscopy (EDS) map of Janus particle, indicating non-homogeneous distribution of Ge along the cross section, from overlaid maps of Si (in red) and Ge (in green). b (IV) Si-Ge equilibrium phase diagram, liquidus (solid line), and solidus (dashed line). b (V) SiGe atomic content distribution along the dashed line in b (III). (From Gumennik et al. [47])
Biomedical Application
Fiber technology is frequently utilized in various biomedical applications as chemical, biological, and physical sensors. Fiber-embedded sensors have been designed to monitor physical parameters such as stresses, temperature, pressure, and humidity or chemical parameters such as pH level, oxygen concentrations, and carbon dioxide concentrations [60]. Fiber bundles are beneficial to embed multiple sensors together in a single system and in increasing signal reception levels, resulting in higher signal-to-noise ratios. Lightness, flexibility, and unique optical properties are the main characteristics that lead the demand for fiber sensors in biomedical studies. To meet clinical usage requirements, preforms must be fabricated from biocompatible, non-toxic, and chemically inert materials to prevent immune reaction from the patient. Examples of smart fiber development include a neural fiber probe composed of a polymer and metal core composition that enables flexibility and bending stiffness of the neural probe as it provides in vivo optogenetic stimulation and delivers drugs as an input in order to record feedback electrical and physiological output signals [33]. Another example is a fiber integrating microfluidic principles with complex cross-sectional geometries and meter-long microchannels which analyzes cell separation by dielectrophoresis (DEP). Live and dead cells are separated by inertial and dielectrophoretic forces by sheathless, high-throughput microfluidic cell separator which contains conductive materials in the microchannels [14]. The following strategies show a new array of possibilities where smart fibers can be used in biological interfacing.
Consider an artificial gut that can serve as a bioactivity testing platform at the microscale and at the macroscale. With today’s progress in tissue engineering, a variety of functionalities can be integrated in bioink-coated fibers co-extruded using a bioprinter for tissue fabrication, as shown in Fig. 6(I). Traditionally, bioprinting research aims at creating tissue grafts for regenerative medical practice and does so by carefully designing the hydrogel (Fig. 6(II)) with the appropriate nutrition and signaling molecules for the type of cells required based on the application (Fig. 6(III)). Tissue engineering is very challenging to study as the whole biology of the system completely changes microseconds after the experiment has been launched. Monitoring and regularly tuning a tissue’s maturation remains very complex.
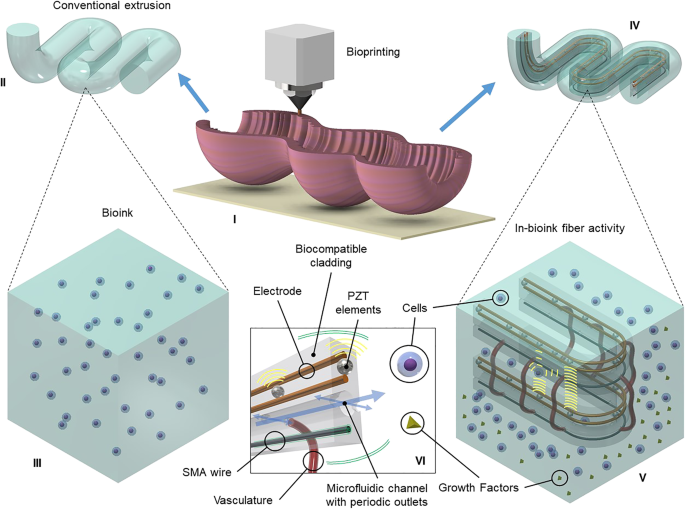
Biological interfacing. (I) Three-dimensional bioprinting of a tissue. (II) Standard microextrusion of bioink. (III) Conventional bioink with cells suspended in hydrogel. (IV) Novel coaxial microextrusion of biointerfacing fiber coated in bioink. (V) Close-up view of fiber where biointerfacing occurs:epithelial cells and vascular epithelial growth factors are excreted from different microchannels and result in cellular self-assembled vasculature between two orifices; piezoelectric elements measure surrounding cell density by ultrasound; and shape memory alloy wires provide peristaltic motion in the tissue. (VI) Visualization of biointerfacing fiber and its components
We propose here a solution by introducing smart fibers in the design (Fig. 6(IV)) to provide a better understanding of the climate and environmental growth. The embedded fiber holds multiple functionalities (Fig. 6(VI)) such as inducing vasculogenesis, ultrasonic imaging, peristaltic movement, and microfluidic flow. Control of the microenvironment takes place via the fiber hooked to syringe pumps and wired to an analytical software. The features of this application (Fig. 6(V)), including pilot experimental data, are detailed in the next subsections.
The Extracellular Matrix and Vasculature
Tissue engineering is widely explored with the increase of artificial tissue needs [61, 62], and the ability to bioprint realistic tissue has an important role to play in tomorrow’s drug and treatment development [63, 64]. One of the biggest challenges is the design of the extracellular matrix (ECM), composed of proteins, growth factors, and other biomolecules, that guide the cell’s contribution to the tissue [65]. Naturally, the ECM gives purpose and structure to the cells, and its extraction typically works by decellularizing tissue and recycling or reusing the ECM for a new cellular construct. The ECM comes in the form of solvents, hydrogels, biopolymers, bioceramics, aerogels, or foams to provide biodegradable or resorbable structure to the tissue [66]. Due to tissue engineering’s high complexity in defining the specifics of the biosystem—mechanical properties, scaffold dissolvability or absorption rates, initial cell types, nutrition, density and ratios, growth factors introduction, and its resulting bioactivity and tissue self-assembly—it is vital to assess the behavior of different types of naturally produced ECM or artificially developed biomaterials in the presence of interacting cells. Moreover, viable tissue requires an organized vascular system that supplies nutrition and oxygen to the tissue for the health and growth of cells. Vascularization provides the natural microfluidic feed of biochemicals to initiate proliferation, specialization, interactions, and motion. The vascular network is formed by vasculogenesis, arteriogenesis, and angiogenesis. Vasculogenesis develops its network through the differentiation and division of endothelial stem cell [67]. Angiogenesis forms new sprouts from existing vessels that are formed in the early embryonic vasculogenesis stage [68].
In-Fiber Microfluidic Feed
Microfluidic conduits with periodic microchannels for content delivery can be used to weave microfluids to specific locations in tissue constructs. The liquefaction front at the boundary of the hot zone defines the droplets’ pinch-off location as described previously. Multiple cores can therefore be broken up in a spatially coherent manner. For example, a silica fiber including a platinum and a silicon core can become a fiber tube with multiple outlets, by inducing the silicon core into an array of spheres and then thinning the fiber using hydrogen fluoride, etching the silicon spheres with potassium hydroxide and etching the platinum core with regal water. An example of the result is shown in Fig. 6(V). The flexibility of fibers allows the microfluidic feed to be integrated in multiple ways in tissue construct. In Fig. 6(IV), the microfluidic channels are used to provide the necessary cell type and growth factors to initiate vascularization and angiogenesis as the tissue reaches maturity.
Biomaterial and Biochemical Testing
In parallel to fiber development, a new testing platform (Fig. 7a (I)) was designed to analyze vascularization and cell-to-cell interactions in the presence of growth factors (Fig. 7a (II)). The platforms were printed in high resolution at an orientation of 30 from biocompatible resin by stereolithography (Formlabs’ Form 2 and Dental LT Clear resin). The print result, shown in Fig. 7a (III), was assembled with two glass capillary tubes with outer diameters of 1.8 mm and 1.0 mm where biological agents are fed. Initial trials will assess diffusion parameters of biochemicals and the growth of cellular colonies in various biocompatible materials. These platforms are designed to be single-use. In 2 h, 24 testing wells can be printed at a relatively low cost. The distance between each capillary outlet of two parallel fibers can be adjusted between 100 and 400 m to investigate the optimum vasculogenesis range that is accepted around 200 m [67]. The medium of interaction in the well’s chamber will first host commercial bioinks (Cellink, USA), one containing sodium alginate and nanofibrillar cellulose and the other containing gelatin methacryloyl, before developing our own in-house biomaterials. The glass capillary tubes shown in Fig. 7a (I) will eventually be replaced by the microfluidic fiber shown in Fig. 6a (V) which will be discussed in the next section.
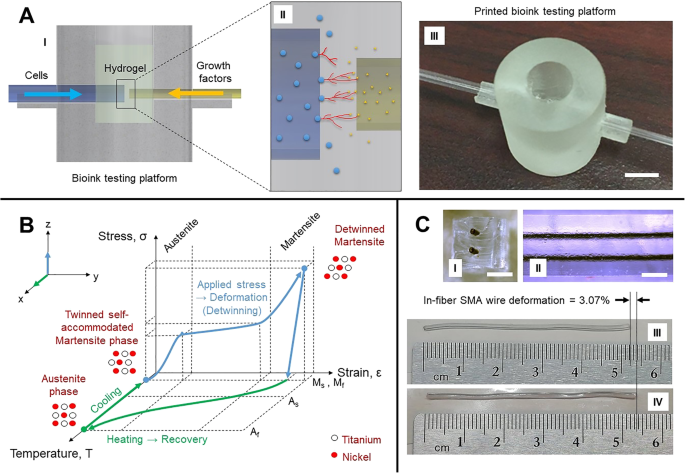
Pilot experiments for biointerfacing:a (I) Cross section of biotesting well showing fluidic feed. un (II) Example of the interaction of epithelial cells (blue circles on the left) with vascular endothelial growth factors (yellow dots on the right) resulting in vasculogenesis excreted by the cells (red lines in the center). un (III) Printed testing platform in biocompatible resin (scale bar = 5 mm). b Temperature-stress-strain graph of the shape memory effect. c (I) Cross section of in-fiber SMA wires (scale bar = 1 mm). c (II) Side view of in-fiber SMA wires (scale bar = 1 mm). c (III) 5.2-mm segment of an in-fiber SMA wire in contraction after being heated at 80 °C. c (IV) 5.36-mm segment of extended in-fiber SMA wire at room temperature
Peristaltic Motion
Shape memory alloy (SMA) wires are lightweight, non-corrosive, and cost-efficient actuating materials for refined applications in a variety of applications such as prosthetic biomimicry [69], self-expandable surgical implants [70], and aerospace engineering [71].
SMAs are metal compounds known for their shape memory effect and pseudoelasticity. Although such properties are typically found in nickel-titanium, these properties can be found in a range of different other metal alloys. Figure 7(b) shows the shape memory effect in terms of temperature, stress, and strain. As shown, at low temperatures, the SMA in its martensite solid state can be deformed by mechanical force, and when thermally induced, goes through a non-diffusive molecular reordering, converting to an austenite solid state. When cooled, the material will return to its initial martensite form, hence the shape memory effect. This thermal cycle is defined by four temperatures, the starting and finishing martensite and austenite temperatures (M s, M f , A s , and A f ), which specifies the start and end of transition periods between states. When the SMA is deformed in as martensite, the molecular de-ordering is defined as detwinning, and it allows the material to experience elongation, which is particularly useful for actuation applications. Essentially, the shape memory effect cycle can occur hundreds of times for an average elongation of 6% and contraction [72], hence its nickname “muscle wire” for its close similarity to muscular myofibrils.
This unique characteristic was first reported by Alden Greninger and Victor Mooradian in 1938 [73], can also be triggered by magnetic field energy [74], namely ferromagnetic shape memory alloys (FSMA), and can be found in polymers (SMP) as well [75]. Today, SMA’s mechanical fatigue and fracture, elasticity, and thermodynamics have been characterized well experimentally [76] and mathematically [77], and its behavior has been modeled [78].
Although the shape memory effect allows for nice contraction behavior of a material, for appropriate robotic applications, the motion needs to be reversable. Typically, an SMA is set in tandem with an opposite mechanism, such as springs, electric drives, elastic bands, or simply another SMA wire. Furthermore, the assembly changes whether it is a linear or rotatory actuation and if the opposing contractions of the actuation are equal. Although wires are thin and weak alone, they can be bundled together to reach the desired force and keep its shape memory effect response time. SMA wires can also be coiled around a capstan to provide greater elongation over shorter distances. Various strategies have been reviewed and chosen for specific applications [79]. The thermal induction is typically best controlled by powering the SMA wire and varying the input current of the order of hundreds of milliamperes. Cooling can be done naturally or by including heat sinks and ventilation.
Fiber drawing technology allows us to play on different material characteristics and to provide to an SMA wire an elastic coating that helps preserve the disorder state of the SMA fiber. As shown in Fig. 7c (I) and c (II), a fiber can be drawn with multiple embedded SMA wires. Styrene-ethylene-butylene-styrene (SEBS) was chosen as the surrounding structure to the SMA wires. SEBS is a copolymer elastomer that can withstand the drawing temperature of 80 °C. While preliminary results show that the actuation can work but with lower efficiency than bare SMA wires, the back-and-forth motion through heating (Fig. 7c (III)) and cooling (Fig. 7c (IV)) cycles is observed for a deformation of approximately 3.07%. More research is required to optimize the setup, but this early stage of experimentation in-fiber SMA actuation shows promising outlooks. The wires were physically pulled and heated using a hot plate to prove the concept. Heating by current would allow speeding up the shape memory effect and controlling better the heat’s diffusion through the fiber. The 5.35-mm wire was measured to have a diameter of 0.11 mm and a resistance of 18.2 was recorded across the fiber segment. To provide a frame of reference, according to SMA wire manufacturers (Dynalloy, Inc.), a 0.1-mm-thick wire made of nickel and titanium requires approximately 200 mA of current for a 1 s contraction. Controlling each wire individually would allow for directional movement, and adding more SMA wires to the design would allow multi-directional motion and greater contraction strength. Moreover, if ferromagnetic SMA wires were used, the control of the motion could become locally controllable via tuning of the interacting magnetic field. Additionally, the FAMES Lab’s drawing tower having the ability to rotate a preform as it is drawing into a fiber enables the possibility to manufacture spring-like structures of SMA wires in the fiber which allows for greater deformation, similar to commercially available SMA springs. Clearly, varieties of strategies are enabled with in-fiber SMA wires.
Biosensing
Biosensors are developed in a wide variety of ways. They can be designed label-based or label-free to detect specific expressions from biological elements such as cells, bacteria, hormones, proteins, DNA, and more [80, 81], from sampling blood, urine, saliva, sweat, or tears. Psychophysiological conditions can be observed from real-time biofeedback such as blood pressure, electrodermal activity, skin conductance, respiration and heart rates, and more [82, 83]. Bioimaging has been done by optical imaging, ultrasound, magnetic resonance frequency, computed tomography, near-infrared spectroscopy, quantum dot probing, and by many more techniques [84].
In optical fiber research, previous biosensing fibers have been fabricated relying on silicon photonic crystal detection of biological radiation [85]. Photonic crystal technology has been used before to monitor in label-free real-time cellular morphology and survival [86]. Such progress in biophotonics has led to hollow-core microstructured fibers visible under magnetic resonance imaging (MRI) [87]. The hollow core allows the propagation of the optical radiations along the fiber over very long distances. The geometry of the hollow fibers varies to tune the photonic bandgaps and dispersion of different detected wavelengths. The inner walls of these hollow tubes are coated with oppositely charged polyelectrolytes and magnetite nanoparticles which are used as contrast agents for MRI. Such design therefore enables new biomedical precision diagnosis opportunities, for example, in the observations of neural activity in vivo [87, 88].
Ultrasonography technology enables us to observe density of cells in liquid or gel in a non-intrusive manner [89, 90]. Ultrasonic probes typically function according to the piezoelectric effect (generation of electricity from applied stress), which was first discovered by Jacques and Pierre Curie in 1880 [91]. The inverse piezoelectric effect (deformation of a piezoelectric crystal from an applied electric field) was induced mathematically by Gabriel Lippmann in 1881 [92] and later in 1916, Chilowsky Constantin and Paul Langevin developed ultrasonic submarine detection for World War I military applications [93]. Thereon, sonar applications have been diverse, such as underwater imaging and fish-finding [94, 95] and energy harvesting [96, 97].
The piezoelectric elements convert electrical energy to and from mechanical energy and transmit sound waves between each other. All frequency and bandwidth parameters require precise regulation, and good energy transmission requires good acoustic and damping matching impedances. Two fibers with integrated piezoelectric elements, designed as pulsing emitter and receiver, can create an ultrasonic waveguide between each other to measure density over the wave’s trajectory. This fiber enables us to sense the microstructures of the environment as the tissue reaches maturation. The piezoelectric elements are created by capillary breakup from a PZT core for example. PZT elements have an acoustic impedance of 33.7 × 10 6 kg/m 2 s with a resonance frequency below 25 MHz. The produced spheres are lined with conductive electrodes to a transducer. This setup provides the feedback in a control system to better adjust microfluidic and motion feed. The in-fiber ultrasonic imaging of the microenvironment clearly helps understand how the tissue environment behaves over time.
Conclusiones
We have formulated the concept of VLSI for fibers (VLSI-Fi)—a combination of liquid-phase processing techniques in microelectronic materials forming a toolbox for fabrication of high-performance devices and systems in fibers and textiles. Our experimental work focuses on a set of demonstrations substantiating our control over narrower aspects of VLSI-Fi, such as preform 3D printing, in-fiber circuit assembly by material-selective spatially coherent capillary instability, and segregation-driven doping control at the level of an individual fiber-embedded device. We envision that VLSI-Fi will enable realization of product in multiple technological areas, one of which is fabrication of active biomimetic scaffolds for engineered tissues with realistic microstructures.
Disponibilidad de datos y materiales
Not applicable.
Abreviaturas
- BJT:
-
Bipolar junction transistor
- CAD:
-
Computer-aided design
- CMOS:
-
Semiconductor de óxido de metal complementario
- DEP:
-
Dielectrophoresis
- ECM:
-
Extracellular matrix
- EDS:
-
Energy-dispersive X-ray spectroscopy
- FAMES Lab:
-
Fibers and Additive Manufacturing Enabled Systems Laboratory
- FOS:
-
Fiber optic sensors
- FSMA:
-
Ferromagnetic shape memory alloys
- HPCVD:
-
High-pressure chemical vapor deposition
- IoT:
-
Internet of Things
- MOF:
-
Microstructured optical fibers
- MOSFET:
-
Metal-oxide-semiconductor field-effect transistor
- MRI:
-
Magnetic resonance imaging
- PCF:
-
Photonic crystal fiber
- PZT:
-
Lead zirconate titanate
- SEBS:
-
Styrene-ethylene-butylene-styrene
- SLA:
-
Stereolithography
- SMA:
-
Shape memory alloy
- SMP:
-
Shape memory polymers
- TPC:
-
Trans-Pacific undersea cable
- UV:
-
Ultravioleta
- VLSI:
-
Very large-scale integration
- VLSI-Fi:
-
Very large-scale integration for fibers
Nanomateriales
- Optimización de la transformación digital en la fabricación de CPG
- GE abre una planta inteligente en Alabama
- La madurez del hilo digital en la fabricación inteligente
- Desafíos de la fabricación basada en datos
- ¿Qué es la transformación digital en la fabricación?
- Aprovechamiento de la tecnología digital en la fabricación
- La fábrica digital:la fabricación inteligente impulsa la industria 4.0
- GE Digital:transformando la fabricación con Smart MES
- Fabricación inteligente de Autodesk
- Fabricación digital:la industria del mañana
- ¿Qué es la fabricación inteligente?