Implementación del mantenimiento basado en riesgos (RbM) | Desglosado en términos simples
¿Alguna vez se preguntó si podría ahorrar tiempo y recursos si no gasta sus recursos ya limitados en activos que no los necesitan?
¿Se pregunta si ahorraría tiempo y dinero creando una estrategia de mantenimiento para la gestión de sus activos?
Nuestra guía de mantenimiento basado en riesgos (RbM) le mostrará paso a paso en términos sencillos cómo analizar rápidamente la forma más eficiente de usar sus recursos de mantenimiento mientras mejora la confiabilidad, reduce los costos y aumenta el ciclo de vida del equipo y la integridad de una manera económica.
¡Un estudio de la Universidad de Aalborg en Dinamarca sobre estructuras de acero en alta mar describió cómo una empresa pudo ahorrar más del 80% en los costos totales de reparación!
¿Qué es el mantenimiento basado en riesgos y por qué es importante?
El mantenimiento basado en riesgos puede volverse bastante sólido y complejo, pero en pocas palabras, le ayuda a determinar el uso más económico de sus recursos de mantenimiento. ¿Cuál es la diferencia entre el mantenimiento basado en riesgos y el mantenimiento centrado en la confiabilidad?
Esto puede parecer complicado, pero el proceso puede ser relativamente sencillo. A continuación, profundizaremos en los detalles prácticos de cómo hacerlo, pero la esencia del mantenimiento correctivo basado en riesgos es encontrar los activos críticos / problemáticos y dedicarles sus recursos de mantenimiento mientras desvía los recursos de los activos no críticos.
Cuando se hace bien, las recompensas son excelentes. Una empresa de petróleo y gas en Europa pudo ahorrar más de $ 15 millones al año utilizando el mantenimiento basado en riesgos.
¿Cómo se implementa el mantenimiento basado en riesgos?
Con el mantenimiento basado en riesgos, tenemos la misión de analizar dos medidas clave:prevención (probabilidad de fallas) y recuperación (consecuencias de fallas).
Para comenzar, primero debemos comprender qué significan esas dos frases:
La probabilidad de fracaso simplemente significa, "¿cuál es la probabilidad de que este equipo falle?"
A menudo, la probabilidad de falla (PoF) se correlaciona con la edad (tiempo de ejecución) del equipo.
Sin embargo, el tiempo no debe ser su única consideración. Las condiciones laborales son importantes en lo que respecta a la toma de decisiones y la probabilidad de fracaso.
Los activos ubicados en lugares húmedos o polvorientos pueden requerir más mantenimiento y es más probable que fallen. Como puede imaginar, factores como la geografía, el clima y otras condiciones ambientales juegan un papel importante en la determinación de PoF.
La consecuencia del fracaso significa, "¿cuánto costará la falla de esta máquina?"
Debe considerar tantos factores como sea posible para determinar la consecuencia de la falla (CoF). Querrá hacerse preguntas como:
- ¿Cuál es el costo promedio de reparación?
- ¿Cuánto pierdo cada año en tiempo de inactividad (pérdida de producción) debido a que esta máquina no funciona correctamente?
- ¿Hay accidentes relacionados con la falla de este equipo? ¿El proceso de mantenimiento de esta máquina ralentiza otras áreas de producción?
- ¿Existen riesgos de seguridad relacionados con el enfoque de mantenimiento de esta máquina o la falta de mantenimiento?
Como puede ver, hay más que considerar que solo los costos de reparación.
Ahora que entendemos la terminología, comencemos el proceso.
1. Recopile sus datos de mantenimiento
Antes de hacer cualquier otra cosa, debemos recopilar y analizar sus datos de mantenimiento actuales. El objetivo aquí es utilizar los datos disponibles para identificar áreas problemáticas.
Deberá obtener un inventario decente de sus activos y lo que le están costando. Para hacer esto, consulte su CMMS y otros registros de mantenimiento. Para ver en profundidad qué es un CMMS, consulte nuestra guía ¿Qué es un sistema CMMS y cómo funciona?
A partir de esos registros, querrá saber lo siguiente para cada equipo en su instalación:
- ¿Qué edad tiene este equipo?
- ¿Con qué frecuencia falla el equipo? (MTBF)
- ¿Cuánto tiempo se tarda en restaurar el equipo para que funcione correctamente? (MTTR)
- ¿Cuánto cuesta cuando este equipo falla? (Interrupción en la producción, costo de las piezas, costo de la mano de obra, etc.)
- ¿Con qué frecuencia realiza el mantenimiento de este equipo?
Una vez que tenga los datos de todo su equipo, querrá identificar qué activos necesitan su atención.
Hay varios métodos excelentes para hacer esto, pero en esta publicación, usaremos la Matriz de Criticidad como ejemplo.
Si es uno de los pocos afortunados con un gran CMMS, automáticamente le informará sobre los activos problemáticos. Por ejemplo, en Limble CMMS, hemos creado una poderosa sección de informes donde los activos problemáticos flotan en la parte superior de la lista, lo que le permite ver de un vistazo qué activo le está costando más y por qué.
2. Visualice con una matriz de criticidad
Una matriz de criticidad (esto suena súper nerd y complejo, pero no lo es) es simplemente un gráfico donde la probabilidad de falla se traza en el eje X (horizontalmente) y la consecuencia de la falla se traza en el eje Y ( verticalmente). Así:
Para mostrarle cómo crear el gráfico, lo desglosaremos un poco con un ejemplo.
Supongamos que hicimos un inventario del siguiente equipo: Generadores 11, 12 y 13 .
Hemos examinado los registros de mantenimiento de cada equipo y tenemos los datos necesarios para determinar el PoF y el CoF de cada uno.
Para graficar esto, necesitamos puntuar la probabilidad de falla (PoF) de los generadores 11, 12 y 13 asignando una puntuación que represente la probabilidad de que cada generador falle.
El rango de puntuación podría verse así:
1 =es muy poco probable que ocurra una falla dentro de tres años
2 =es poco probable que ocurra una falla dentro de tres años
3 =la falla no es probable o improbable
4 =la falla es probable
5 =es muy probable que falle
SUGERENCIA # 1:Puede utilizar cualquier tipo de sistema de puntuación que desee. Si es más fácil para usted pensar en porcentajes (es decir, 10% de probabilidad de falla, 20% de probabilidad de falla, etc.), entonces, ¡hágalo!
Ahora que tenemos nuestro marco de puntuación configurado, hagamos la puntuación.
Nuestros datos nos dicen que en los últimos 3 años el Generador 11 se averió 5 veces, el Generador 12 se averió 2 veces y el Generador 13 se averió 3 veces. Basándonos en estos números, demos las siguientes puntuaciones:
Escala de probabilidad de falla
Generador 11 - puntuación de 5
Generador 12 - puntuación de 2
Generador 13 - puntuación de 3
A continuación, es el momento de asignar a cada generador una puntuación de consecuencia de la falla. Nuevamente, necesitamos crear un sistema de puntuación que represente el nivel de consecuencia para cada activo. (También puede puntuar su CoF de la forma que desee).
Midamos el impacto de la falla:
Generador 11 - Este generador es utilizado por la tripulación nocturna móvil para proporcionar electricidad para la iluminación. Si se rompe, la cuadrilla no puede continuar con su trabajo, que cuesta $ 5,000 en tiempo perdido, demoras en el proyecto de mano de obra, etc. Los costos de reparación son normalmente de $ 300 por avería.
Generador 12 - Este es un generador antiguo que rara vez se usa. La falla de este generador no tiene un gran impacto. El trabajo de reparación, el tiempo perdido, la mano de obra, etc. cuesta solo $ 500. Los costos de reparación son normalmente de $ 300 por avería.
Generador 13 - Esta máquina se utiliza para ejercicios aleatorios en el patio. El ejercicio aleatorio en el patio no es urgente, pero cuesta dinero cuando no se puede completar. La pérdida estimada en tiempo perdido, mano de obra, etc. es de $ 2500. Los costos de reparación son normalmente de $ 200 por avería.
Consecuencia de la escala de fallas
1 =Menos de $ 2,500 costos anuales
2 =Entre $ 2,500 y $ 5,000 costos anuales
3 =Más de $ 5,000 costos anuales
Y luego, le asignamos a cada generador una puntuación basada en las consecuencias (costos) particulares de cada máquina. Así:
Generador 11 =3
Generador 12 =1
Generador 13 =2
SUGERENCIA # 2:La mejor manera de averiguar las consecuencias del fracaso es hablar con su equipo. Pregúnteles qué sucede si un equipo en particular no funciona y cuánto les cuesta. Mire su GMAO o registros de mantenimiento para ver los costos de reparación. Estas acciones le brindarán una gran comprensión del verdadero costo de las fallas del equipo.
Ahora que tenemos las puntuaciones de Probabilidad de falla y Consecuencia de falla, es hora de graficar nuestros datos. Este gráfico se vería así:
Los generadores que bordean o están dentro del área roja (números 11 y 13) tienen un nivel de riesgo mucho más alto que los equipos hacia la parte inferior izquierda del gráfico (número 12). En este caso, podríamos considerar nuevas estrategias de mantenimiento para los generadores 11 y 13.
Esta es una versión extremadamente simple de una Matriz de criticidad, ya que solo hemos trazado unos pocos activos y mantuvimos nuestra puntuación de PoF y CoF muy básica. Sin embargo, aún tiene una excelente vista de qué activos se beneficiarían más de un plan de mantenimiento. Cuantos más activos, más beneficioso sería este gráfico para seleccionar rápidamente los activos para los programas de mantenimiento.
Reducir el mantenimiento reactivo en un 73,2%
Ver los resultados que disfruta Red Hawk con Limble
Lea nuestroCaso de estudio
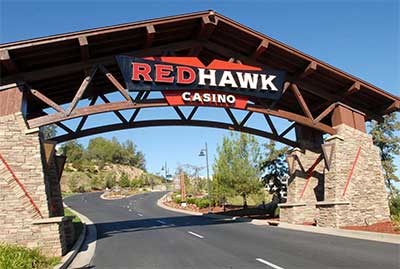
¿Cómo sabe qué tipo de mantenimiento implementar?
Ahora que sabe qué activos requieren planes de mantenimiento, ¿cómo puede elegir el plan adecuado para cada máquina?
Odiamos decírselo, pero no existe una estrategia estándar predeterminada que funcione mejor automáticamente para su empresa. Cada instalación es diferente, llena de diferentes equipos, fabricando diferentes productos, con diferentes humanos operando el equipo.
Dicho esto, aquí hay algunas preguntas que le resultarán útiles a la hora de determinar qué estrategias de mantenimiento implementar.
¿Cuánto y cuáles son mis recursos de mantenimiento?
Lamentablemente, en el mundo del mantenimiento, se espera que haga más cada año con un grupo de recursos cada vez más reducido. En un mundo perfecto, su personal de mantenimiento sería lo suficientemente grande como para hacer bien el trabajo, pero eso rara vez es el caso. Al considerar las estrategias de mantenimiento, debe considerar los recursos.
Por ejemplo, un plan de mantenimiento preventivo no servirá de mucho si no tiene la mano de obra para realizar los MP cuando están programados.
¿Qué recomienda el fabricante?
El fabricante debe ser su fuente de información de referencia. A menudo, un manual de equipo proporcionará un esquema detallado de qué trabajo se debe hacer para mantenerlo adecuadamente mantenido. Dicho esto, tenga en cuenta que estas son pautas generales y, según su situación, es posible que desee aumentar o disminuir la frecuencia.
¿Cuánto cuesta reemplazar cada activo y cuál es su vida útil restante esperada?
En situaciones con activos muy antiguos que tienen una vida útil restante corta, puede que sea mejor ejecutar el activo hasta que falle y luego comprar un reemplazo. Esto puede no ser cierto si el activo tiene un CoF muy alto, pero afortunadamente ahora sabe cómo encontrar esta respuesta 🙂
¿Dónde aterrizó en su Matriz de Criticidad?
Si un activo aterrizó en la esquina superior derecha (área súper arriesgada) de su matriz, entonces necesita ALGUN tipo de estrategia en su lugar. Puede asignar inspecciones de rutina o implementar un plan de mantenimiento predictivo que le permitirá reparar el equipo solo cuando sea absolutamente necesario.
Antes de tomar decisiones importantes, asegúrese de conocer todas sus opciones. Consulte nuestra comparación en profundidad de las estrategias de mantenimiento para conocer los pros y los contras de cada enfoque.
Reduzca el riesgo comenzando con algo pequeño y luego escale
Una vez que haya identificado qué métodos de mantenimiento podrían funcionar para sus activos, puede aumentar sus posibilidades de éxito comenzando con algo pequeño. Es decir, ponga su plan en acción con solo unos pocos equipos para comenzar. Supervise el progreso y escale su estrategia a partir de ahí si tiene éxito.
Si ha decidido implementar un plan de mantenimiento, entonces debería considerar invertir en una solución CMMS (si no tiene una o está usando un paquete antiguo y desactualizado).
Con Limble CMMS, puede optimizar su flujo de trabajo, recopilar datos de calidad y tomar decisiones clave rápidamente para optimizar la producción de su empresa desde la palma de su mano.
Mantenimiento y reparación de equipos
- La evolución del mantenimiento industrial
- Beneficios de implementar una estrategia de mantenimiento de planta móvil
- Propiedad del equipo para los técnicos de mantenimiento
- Cómo implementar el mantenimiento productivo total
- Participar en la encuesta de referencia de mantenimiento de equipos
- 5 claves para mantener la confiabilidad del equipo
- 5 beneficios a largo plazo del mantenimiento preventivo
- El papel de las inspecciones de equipos en el mantenimiento
- Instalaciones y mantenimiento industrial
- Mantenimiento de equipos de construcción
- Mantenimiento de equipo pesado en los meses de invierno