La fabricación médica se vuelve más inteligente
La fabricación digitalizada y automatizada está avanzando a pasos agigantados en el mundo de la fabricación médica, como lo demuestran los sistemas recientes que se pusieron en las líneas de producción durante la pandemia de COVID-19.
Dados los rigurosos estándares que regulan la fabricación de dispositivos médicos, el entorno de Industria 4.0 centrado en datos está hecho a medida para los fabricantes por contrato que intentan cumplir con las especificaciones y al mismo tiempo hacer frente a la dramática falta de operadores calificados.
Como siempre, los materiales son cada vez más sofisticados y las piezas cada vez más pequeñas, con geometrías más complejas y requisitos de tolerancia más estrictos.
En un sentido amplio, las tendencias de la atención médica (el envejecimiento de la población, el impulso de diagnósticos y terapias más remotos fuera del costoso entorno hospitalario, terapias más personalizadas) están impulsando el desarrollo de dispositivos médicos. Y con las continuas incertidumbres de la pandemia y las cadenas de suministro maltratadas resultantes, establecer una mayor visibilidad del funcionamiento de los proveedores y vendedores es la prioridad número 1.
Junto con la digitalización de la atención médica surge la necesidad de proteger todos los datos que se recopilan. Con ese fin, existen iniciativas como el nuevo Centro de Ciberseguridad de Dispositivos Médicos de la Universidad de Minnesota, anunciado el 9 de septiembre. Cinco grandes bateadores de la industria de la salud se han unido para trabajar juntos en el nuevo centro:Boston Scientific, Smiths Medical, Optum, Medtronic y Abbot Laboratorios. Su objetivo es eliminar las vulnerabilidades de software en los dispositivos médicos que podrían usarse para dañar a los pacientes o interrumpir las instalaciones de atención médica.
El futuro de alta tecnología del cuidado de la salud también significa más diagnósticos y procedimientos robóticos, de ahí la necesidad de más herramientas médicas y piezas dedicadas para usar con esos sistemas. Por ejemplo, XACT Robotics en Hingham, Massachusetts, el desarrollador del sistema robótico XACT ACE, anunció el 30 de agosto que completó con éxito la inscripción de pacientes en el primer estudio de EE. UU. que evalúa XACT ACE para su uso en procedimientos pulmonares percutáneos. Esto incluye biopsias para confirmar la presencia de cáncer. El sistema robótico de manos libres podría detectar el cáncer antes y de forma menos invasiva.
Mientras tanto, iData Research proyecta que se realizarán 3 millones de procedimientos quirúrgicos robóticos anualmente para 2025. Los brazos robóticos en equipos como el Sistema quirúrgico da Vinci requerirán una gran cantidad de instrumentos miniaturizados que los médicos controlan para realizar estas operaciones mínimamente invasivas. Las cirugías robóticas usan incisiones más pequeñas, lo que resulta en menos pérdida de sangre y cicatrices, estadías más cortas en el hospital y recuperaciones más rápidas.
La IA alimentada por datos también pasará a primer plano para mejorar los resultados de los pacientes. Un claro indicador de ese camino es la adquisición de Gauss Surgical de Menlo Park, California, por parte de Stryker. Gauss desarrolló Triton, una plataforma habilitada con inteligencia artificial para monitorear la pérdida de sangre durante la cirugía.
La fabricación aditiva también seguirá ampliando su papel fundamental en la producción de implantes, herramientas y modelos de formación quirúrgica específicos para cada paciente. Por ejemplo, Tsunami Medical de Italia está asombrando a la industria con el uso de los sistemas de impresión 3D de haz de electrones y láser aditivo de GE para producir una gama de implantes espinales altamente complejos.
Piezas pequeñas, desafíos de clasificación
A medida que los materiales de los dispositivos médicos evolucionan y las piezas se hacen más pequeñas, las máquinas de estilo suizo de la serie L de Marubeni Citizen-Cincom (MCC), Allendale, N.J., están respondiendo a la llamada.
“Medical tiene materiales de los que no ha oído hablar antes”, bromeó el presidente y director de operaciones, Brian Such. Los materiales resistentes se pueden usar para piezas simples o componentes más complejos que requieren el uso de muchas herramientas para crear las diferentes funciones.
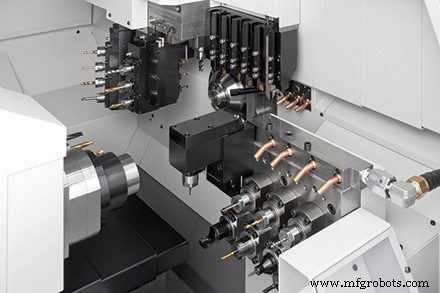
“Nuestras máquinas de la serie L son una máquina múltiple con subhusillo”, y su ventaja significativa para la producción médica es que son modulares, explicó Such. "Con una cantidad de herramientas disponibles en cualquier momento, podemos deslizar una y colocar tres en el mismo lugar".
Para manejar los diámetros más pequeños típicos de las fresas y taladros médicos actuales, MCC ofrece aceleradores de hasta 4x de aceleración. “Nuestras herramientas motorizadas alcanzan velocidades de hasta 6000 o 9000 rpm según los modelos, pero podemos introducir un portaherramientas diferente y ahora tenemos 36 000 rpm. Cuando eso no es suficiente, podemos adaptar nuestros husillos eléctricos, que pueden alcanzar hasta 80 000 rpm”.
Como ejemplo, señaló Such, un cliente podría estar perforando un orificio de ocho milésimas, "por lo que necesita algo de velocidad para eso, o utilizar una fresa de extremo de 16 milésimas o tal vez incluso una fresa de extremo de ocho milésimas para inclinar una esquina en algún lugar . Con nuestros husillos eléctricos de 80 000 rpm, podemos deslizarnos en estos bolsillos. Y esta misma herramienta se puede usar como una herramienta frontal, una herramienta cruzada o una herramienta orientada hacia atrás, por lo que es muy modular”. MCC se asoció con el vendedor de husillos de alta velocidad NSK para crear estos husillos patentados.
Hace aproximadamente dos años, MCC amplió la funcionalidad del eje B de sus máquinas al presentar la versión ATC (cambiador automático de herramientas) de su máquina L20. "Ahora tenemos la capacidad de 13 herramientas en el eje B", dijo Such, mientras que normalmente un eje B tiene solo cuatro herramientas, y eso "es algo muy atractivo para el mercado médico" dados los ángulos estrechos de las piezas actuales.
Otra innovación de MCC, introducida alrededor de 2016, es el corte por vibración de baja frecuencia (LFV). En este proceso, la máquina herramienta “oscila la trayectoria de corte del eje Z o X, moviéndose hacia adentro y hacia afuera a una velocidad muy alta para hacer pequeños cortes de aire y romper las virutas mientras se está mecanizando”, dijo Such. “El campo de la medicina ama la tecnología LFV, y la mayoría de los clientes que la usan por primera vez dicen:'Nunca volveré a comprar una máquina sin ella'”. Con LFV “usted 100 por ciento romperá los chips; no hay intermedio. Una vez que ejecuta el proceso, está garantizado. Todavía tiene que conocer sus herramientas de corte, y las herramientas de corte aún pueden fallar, pero el problema de la envoltura de virutas desaparece”.
Los clientes de MCC van desde OEM con 300 o 400 máquinas hasta fabricantes más pequeños con 10 máquinas. Y esos clientes “están fabricando todas las piezas diferentes”, desde tornillos óseos comunes y jaulas para cirugía de columna hasta varias herramientas quirúrgicas como escariadores óseos necesarios para cirugías de cadera y rodilla. Hay pequeños tornillos para huesos de aproximadamente 4 mm de diámetro con orificios para suturas. “Vienen nueve herramientas diferentes para cortar las diferentes formas”, dijo Such. "Este pequeño tornillo para huesos tiene muchas características:no es solo un tornillo con cabeza".
Una vez que se fabrican esas piezas diminutas, la clasificación se convierte en el problema principal, continuó Such. MCC fabrica equipos de automatización a la medida de la tarea.
“Estas piezas son tan pequeñas que cuando caen en el balde, podría haber 300 allí. Si vas a tratar de elegir el último para intentar medirlo, ¿cuál fue ese? Podemos tener un dispositivo que tenga diferentes bandejas para contar”, dijo Such.
El cliente puede colocar 100 piezas en una bandeja, luego, cuando la bandeja se mueva, colocar una en la siguiente bandeja, 100 en la siguiente bandeja, una en la siguiente bandeja, y así sucesivamente. Si hay 10 bandejas, puede funcionar durante ocho horas o toda la noche sin supervisión. Al medir las piezas a intervalos, los clientes pueden aislar si las piezas anteriores son buenas o malas gracias a las bandejas de recolección.
La ventaja de los seis ejes
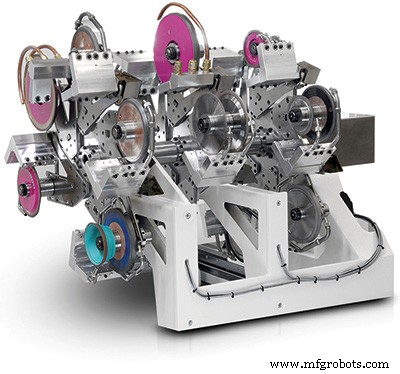
La demanda constante de rectificadoras de herramientas de corte de Rollomatic USA Inc., Mundelein, Illinois, es un claro indicador de la capacidad de recuperación de la fabricación de dispositivos médicos, afirmó el presidente Eric Schwarzenbach.
Entre los muchos instrumentos que los fabricantes de equipos originales y los fabricantes contratados solicitan a las máquinas Rollomatic para fabricar, se encuentran varias herramientas de corte ortopédicas como raspadores, brocas para huesos, perforadores de cráneo y fresas artroscópicas. Durante la pandemia, “nuestros clientes invirtieron como antes, ni más ni menos” a pesar del aplazamiento de cirugías ortopédicas o electivas. "Había suficiente negocio para que estas empresas siguieran funcionando y para mantener su necesidad de reinversión".
En los últimos dos años, señaló, la demanda de varios instrumentos para cirugías robóticas está creciendo. Pero esos dispositivos plantean un desafío particular.
“Un taladro que usa un cirujano con una pieza de mano para perforar el hueso es diferente a lo que emite un robot”, explicó. “Los robots usan taladros más largos que los cirujanos. La naturaleza de hacer un taladro largo es más difícil que un taladro más corto. En primer lugar, las piezas brutas de herramientas quirúrgicas se mecanizan en un estado blando en un torno tipo suizo y posteriormente se endurecen. Estos procesos causan inherentemente deformaciones en estos espacios en blanco, y cuanto más largos son, más doblados están. Y cuando están doblados, tenemos problemas para cargar, moler y descargar de manera confiable. Cuando enseñamos a los clientes nuestra máquina y configuración, debemos tener mucho cuidado de enseñarles con cierta profundidad y asegurarnos de que comprendan las características para evitar un espacio en blanco doblado. Los espacios en blanco doblados a menudo son enderezados por el fabricante, pero aun así nunca son perfectos, aunque no tienen que ser perfectos. La máquina es capaz de manejar una pequeña distorsión”.
Cuanto más robótica se vuelve la industria, “más enfoque debe haber en el punto de perforación. Mientras que un cirujano siempre puede perforar el hueso porque puede mirar, ver, ajustar la mano y la presión para que la punta no se aleje, el robot no lo hace. Entonces, esos puntos deben diseñarse para que sean más egocéntricos. Ayudamos a los fabricantes de dispositivos médicos a enseñarles cómo es un punto de autocentrado”.
Schwarzenbach también notó más variantes en acero inoxidable 17-4 para cortadores ortopédicos. “El material se ha vuelto más blando y menos endurecido, lo cual es un desafío para nosotros en términos de encontrar las muelas abrasivas adecuadas para rectificarlas. Como sabes, cuanto más suave es el material, más difícil es moler”. Para responder a esa necesidad, Rollomatic se asoció con fabricantes de ruedas en Suiza y EE. UU. para adquirir ruedas adecuadas para materiales más blandos.
“Cuanto más suave es el material, más rebabas arroja”, explicó Schwarzenbach, “por lo que la eliminación de las rebabas es un problema. Nuestros clientes suelen utilizar cepillos de nailon para eliminar las rebabas después del esmerilado, especialmente con materiales más blandos. Pero ninguna rueda o proceso es perfecto; siempre habrá un poco de rebaba suelta que debe eliminarse con algún método. Utilizamos cepillos de nailon o, a veces, impregnados con cerámica o abrasivos para eliminar esas rebabas".
Los mangos de desconexión rápida para herramientas médicas son otra área de crecimiento, continuó. Un cirujano puede hacer clic en estas herramientas en una pieza de mano o asegurarlas a un brazo robótico. Tales agarres “se han vuelto mucho más complejos de lo que jamás hayamos visto. Usamos un molinillo de cáscara para la mayoría de ellos”.
La capacidad de seis ejes de Rollomatic cambia las reglas del juego para los fabricantes médicos que necesitan más flexibilidad para la programación y una configuración más sencilla de las ruedas, dijo Schwarzenbach.
“No necesitas usar ruedas complejas; puede usar ruedas de forma más sencilla, particularmente en los puntos de perforación”, dijo. “Puede producir una punta de perforación más fácilmente que en una máquina de cinco ejes. Y no olvide:los puntos de perforación ahora se están volviendo tan bajos como 50 a 60 grados inclusive. Son muy pronunciados, a diferencia de un taladro de carburo en metal a 120 o 130 grados. Nuestras máquinas de seis ejes realmente ayudan a esmerilar esos puntos de perforación mucho más fácilmente que tener que lidiar con la configuración de una máquina de cinco ejes”.
Y el cambiador rápido de ruedas de Rollomatic ofrece aún más ventajas, agregó. “Hemos estado vendiendo muchas más máquinas de cambio de ruedas. El cambiador de ruedas básico tiene seis estaciones, por lo que puede colocar paquetes de seis ruedas para aumentar la flexibilidad, lo que sirve para lotes más cortos. Los lotes más cortos necesitan más flexibilidad con el cambio frecuente. Las máquinas de cambio de ruedas son muy buenas para eso”. Si bien alrededor del 80 por ciento de las máquinas que Rollomatic vende en la industria médica conservan los ejes estándar que albergan un par de ruedas delanteras y traseras, algunos fabricantes "están comenzando a adoptar nuestra nueva tecnología".
El papel de las pruebas de fuerza
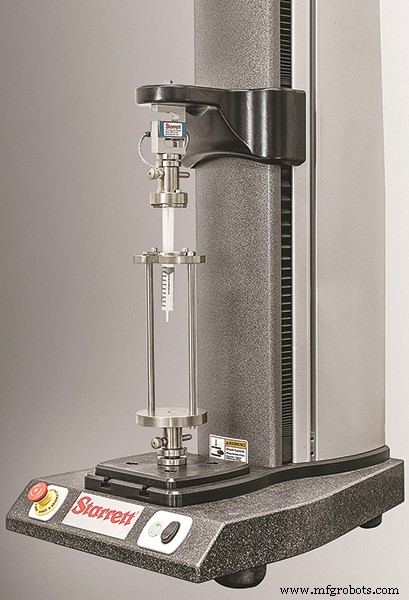
Desde la preparación para la fabricación hasta después de la fabricación de la pieza, el equipo de prueba de fuerza y su software integrado realizan funciones importantes para los productos médicos, a menudo con el objetivo de la comodidad del paciente.
Por ejemplo, los contornos y el revestimiento de una aguja se pueden probar para determinar la facilidad con que penetran en la piel, mientras que los adhesivos se pueden evaluar para determinar qué tan bien se adhieren a la piel o qué tan fácil se eliminan.
Antes de la fabricación, "puede crear pruebas para asegurarse de que su equipo funcione como debería antes de usarlo en la fabricación", explicó Jacob Morales, ingeniero de soporte técnico de The L.S. Starrett Co., Athol, Mass. Y para los vendajes, “puede probar el adhesivo antes de usarlo en su línea de fabricación”, en lotes que varían, por ejemplo, de una en 100 a una en 10,000 muestras. "Después del proceso, puede ejecutar esas pruebas nuevamente para garantizar la coherencia".
Tales pruebas son particularmente importantes cuando se fabrica de acuerdo con las normas ASTM e ISO, así como para producir documentación crítica para la trazabilidad, agregó Eric Perkins, gerente de tecnología de Starrett para pruebas de fuerza y materiales. El software de Starrett permite realizar pruebas tanto de fuerza como de propiedades del material, y con solo hacer clic en el icono de la derecha, el software puede realizar la prueba adecuada. La medición de fuerza cubre escenarios pasa/no pasa, incluye pruebas de carga máxima, carga promedio, pruebas de compresión y más. Las jeringas, un excelente ejemplo que requiere la aplicación de fuerza uniaxial, se pueden probar con sustancias de muestra para determinar la fuerza de inyección para tasas de inyección controladas.
Si bien estas pruebas brindan información de la muestra, no siempre arrojan datos específicos del material que compone la muestra. Las pruebas de materiales van más allá, utilizando las propiedades de los materiales para probar el alargamiento y la tensión-deformación, por ejemplo.
El software de Starrett se puede integrar en el proceso de fabricación, explicó Morales.
“Si tiene un sistema de fuerza que prueba una muestra, puede programarlo con un sistema de entrada y salida para que la prueba se ejecute constantemente. El equipo de fabricación mueve una muestra a la máquina y envía una señal; la máquina responde ejecutando la prueba y proporciona una salida de señal basada en los resultados de la prueba. El resto de su equipo de fabricación puede responder adecuadamente. Si obtiene un resultado que está fuera de tolerancia, la señal puede alertar a un operador.”
Esa flexibilidad significa que "puede conectar el sistema de fuerza a un PLC y ponerlo en línea con el entorno de producción, por lo que ha eliminado el posible error de entrada de datos humanos", dijo Perkins. "Los usuarios pueden probar automáticamente un producto cada vez que se pone en cola".
Desde el software de fuerza básico L1 de Starrett hasta sus opciones más avanzadas L2, L2Plus y L3, "brindamos a los clientes la capacidad de realizar pruebas exactamente como establece cualquier estándar de fabricación", dijo Perkins. Y dado que el software de Starrett es compatible con todas las plataformas, agregar sistemas ópticos y de visión crea una solución de metrología extremadamente amplia.
Sin embargo, ese nivel de personalización no se detiene en el software. Starrett ha estado trabajando con fabricantes para crear sistemas completamente automatizados.
“Estamos utilizando robots para insertar piezas en nuestro sistema de prueba de fuerza”, dijo Perkins. “Usamos pinzas neumáticas para agarrar las piezas”. Con una plataforma de prueba en constante ejecución casada con este nivel de automatización, "nuestro sistema le dirá si tiene una pieza buena o mala, luego el robot ejecuta cualquier programa que se requiera y coloca esas piezas en el contenedor designado".
Vista general de GE
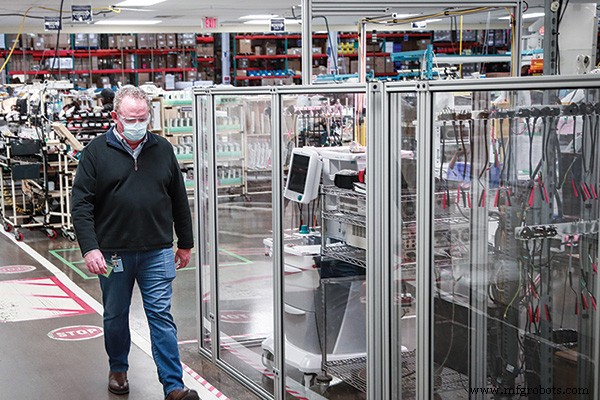
Mejorar los flujos de trabajo de los hospitales y mantener la resiliencia de la cadena de suministro ha sido una prioridad para GE Healthcare durante la pandemia.
“Estamos viendo un aumento en las solicitudes de más automatización, no solo desde el punto de vista de la productividad típica, sino también en términos de aprovechar la automatización para que podamos mantener la producción en diferentes ubicaciones”, dijo Jimmie Beacham, ingeniero jefe ejecutivo de fabricación avanzada en GE Healthcare en Milwaukee. “Eso es más fácil que tener que capacitar a una fuerza laboral nueva o rotatoria. No se trata necesariamente de la mano de obra sino de la seguridad de la cadena de suministro donde la automatización tiene sentido. Si tengo que cambiar la producción de una región a otra, es mucho más fácil si el proceso ya está automatizado".
Una parte importante de esa filosofía es la prueba de errores, agregó. “Entrenaríamos a los operadores y tendríamos procedimientos escritos”, explicó Beacham. “Ahora estamos buscando emplear otras tecnologías que digitalicen lo que los operadores deben hacer y que interactúen con ellos. Digamos que tiene una estación de torque, donde está apretando pernos, seguido de un ensamblaje complejo y luego un cobot. Estamos buscando tecnologías que conecten digitalmente todo eso, que funcionen al unísono con el operador, de modo que interactúe con esa persona y no requiera que el operador lo recuerde todo. Eso nos da mucha flexibilidad cuando fabricamos el mismo producto en tres regiones del mundo. Ahora tenemos un proceso de control. No confiamos en que los operadores memoricen los procedimientos en papel cuando tienen que pasar por varias partes complejas de la operación”.
Eso es vital para GE Healthcare, que produce una variedad de equipos de diagnóstico inteligentes. La fabricación aditiva es una gran parte de la ecuación, y GE Healthcare también ha perfeccionado sus procesos en ese sentido.
“Cuando comenzamos, probablemente invertimos entre el 80 y el 90 por ciento de nuestro tiempo en I+D, tratando de descubrir cómo funcionan los aditivos, cómo se desarrollan los materiales y los parámetros para cumplir con nuestros requisitos de ingeniería”, dijo. “Ahora estamos en alrededor del 80 por ciento de ejecución, donde estamos moviendo las cosas a producción, y el otro 20 por ciento de nuestro tiempo lo dedicamos a desarrollar nuevos materiales para los nuevos embudos que llegan. Tenemos una planta de producción en Monterrey, México, y tenemos un embudo bastante activo de cosas que van allí. Luego tenemos otras aplicaciones adicionales que ejecutamos en el punto de uso”.
En última instancia, si bien la pandemia ha demostrado ser un desafío, GE Healthcare ha capeado la tormenta.
“Nuestro gran desafío fue el suministro, llevar a las personas de manera segura a la planta”, dijo Beacham. “En algunos casos, como con los ventiladores, confiamos mucho en la automatización para poder satisfacer una demanda sin precedentes. Trajimos a mucha gente para hacer el trabajo, pero aún teníamos que encontrar formas creativas de fabricar el volumen de productos que nuestros clientes necesitaban desesperadamente. Y aprendimos que podemos fabricar las cosas de manera diferente; eso ha inspirado aún más ideas”.
Sistema de control de automatización
- Evaluación del impacto de la industria 4.0 en la fabricación
- 8 mitos destacados sobre la fabricación de metales desmentidos
- Tecnologías para una fabricación de componentes médicos más efectiva vista en MD&M West 2018
- 6 maneras en que IIoT hace que la fabricación sea más eficiente
- Stratasys:Ser más sostenible con la impresión 3D
- INFORME:2016 será un 'punto de inflexión' para la tecnología de fabricación
- Hacer que la fabricación en Gran Bretaña sea más inteligente:expectativas para 2018
- Cerrando la brecha de habilidades en la fabricación automotriz
- Stora Enso:el futuro de la fabricación ahora es más inteligente
- Creación de una cadena de suministro de fabricación resiliente
- Made Smarter:Robotics and Automation Creates Jobs