Nanomateriales:productos, cadena de suministro madura para compuestos de próxima generación
La promesa de los nanomateriales de ofrecer propiedades mecánicas sin precedentes, junto con una conductividad térmica y eléctrica adaptable para compuestos, se ha anunciado durante décadas. Debido a sus propiedades únicas y su enorme superficie, los nanomateriales tienen el potencial de impulsar el rendimiento del producto más allá de la macroescala actual. composicion. Aunque los nanomateriales como el grafeno y los nanotubos de carbono (CNT) están disponibles comercialmente en varias empresas y sitios web, la aplicación generalizada en compuestos no es tan evidente.
Mientras tanto, los materiales y la terminología evolucionan rápidamente; CW proporciona una introducción a los nanomateriales actuales, así como avances significativos en nuevos materiales y la cadena de suministro.
Nano paisaje para compuestos
Los nanomateriales pueden ser de metal, cerámica, polímero, a base de carbono o de fuentes naturales como la celulosa. Los nanomateriales forman un compuesto cuando se usan para reforzar una matriz de polímero, cerámica o metal, y generalmente se clasifican por forma (morfología) como partículas, fibras o plaquetas (consulte “Tipos y definiciones de nanomateriales” más adelante). A medida que el tamaño del material disminuye de micrómetro (10 -6 metro) a nanómetros (10 -9 metro), el área de la superficie aumenta de modo que la interfaz nanomaterial-matriz comprende más volumen del compuesto. Esta es la razón por la que se pueden lograr mejoras en las propiedades del producto terminado de un 20-50% con una o dos órdenes de magnitud menos de carga en comparación con los micromateriales como el negro de carbón y la fibra molida. Esta es también la razón por la que, al igual que las propiedades de un macrocompuesto dependen de la mecánica en la interfaz fibra-resina, comprender y controlar las interfaces de un nanocompuesto es aún más importante para administrar las propiedades y el rendimiento del material.
Sin embargo, la promesa de los nanomateriales se ha visto obstaculizada por las dificultades para ampliar los procesos de fabricación rentables de materiales de alta calidad con defectos mínimos. Además, lograr una dispersión homogénea de nanomateriales dentro de matrices ha sido un desafío debido a la tendencia de los nanomateriales a aglomerarse. Esto último puede superarse mediante la funcionalización de la superficie del nanomaterial. Las técnicas habituales, que a menudo se combinan, incluyen modificar la carga eléctrica del nanomaterial o la matriz, modificar el pH o añadir un tensioactivo.
La industria de los compuestos normalmente piensa en un nanocompuesto como cualquier matriz con un nanomaterial disperso en él. Sin embargo, los microcompuestos se pueden distinguir de los nanocompuestos según la escala primaria de las interfaces. La figura 1 proporciona ejemplos de diversas combinaciones e interfaces de micro / nanocompuestos. Una matriz de microescala (micrónica) está reforzada con nanopartículas, nanofibras o nanoplaquetas, como se ve en A, B y C, respectivamente, mientras que un nanocompuesto se diferencia como una fase de matriz mezclada en la misma escala como el nanomaterial, como se muestra en E y F.
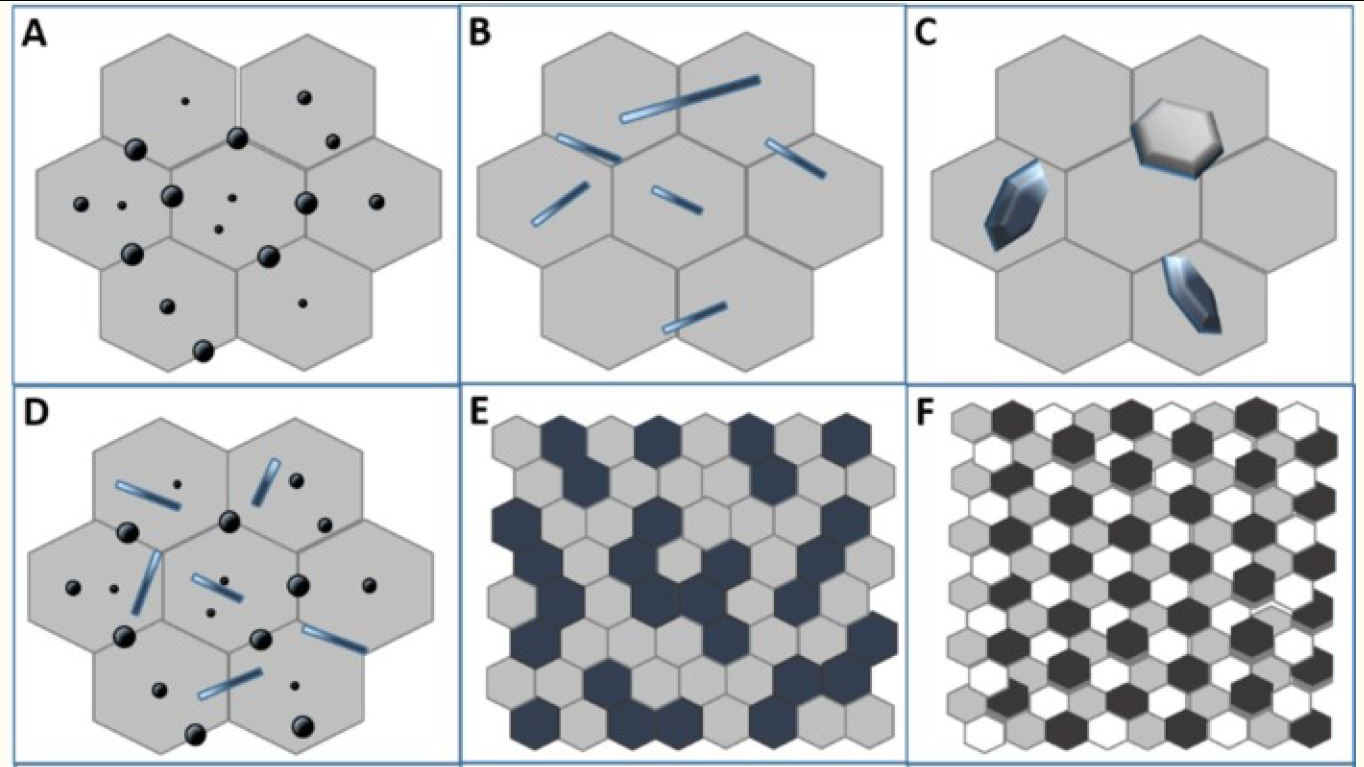
Fig. 1 Estructuras comunes de micro / nanocompuestos para materiales cerámicos. Micro / nanocompuesto que comprende una matriz micrónica con (A) nanopartículas redondeadas, (B) nano refuerzos de alta relación de aspecto, (C) nano refuerzos de tipo plaqueta y (D) nano refuerzos tanto redondeados como alargados; (E) compuesto bifásico formado por dos fases ultrafinas inmiscibles; (F) compuesto multifásico formado por tres (o más) nanofases inmiscibles. Fuente | "Nanocomposites de cerámica estructural:una revisión de las propiedades y los métodos de síntesis de polvos" por Paola Palmero, Nanomaterials (Basilea). Junio de 2015
Composites multifuncionales 2D nano a 3D
Dentro del nano paisaje, quizás la región más activa es la que comprende los nanomateriales 2D. El más popular de ellos es el grafeno, que ha ganado una popularidad sustancial gracias a sus extraordinarias propiedades. El grafeno es el peso más ligero (0,77 mg / m 2 ) y el material más resistente conocido (100-300 veces acero), más duro que el diamante pero más elástico que el caucho, con movilidad de electrones 100 veces más rápida que el silicio, conductividad eléctrica 13 veces mejor que el cobre y una superficie muy alta. El grafeno parece capaz de salvar ciertas lagunas en las limitaciones de propiedad convencionales. Por ejemplo, cuando se agrega al caucho, el grafeno puede aumentar simultáneamente el agarre del neumático y reducir el desgaste. Los fanáticos de la Fórmula 1 saben al ver cómo los autos de carrera cambian entre neumáticos blandos (alto agarre, menos resistencia al desgaste) y neumáticos duros (menos agarre, más resistencia al desgaste), que estas dos propiedades normalmente no coexisten. "El negro de carbón ha sido el relleno normal para el caucho en los neumáticos, pero el grafeno ofrece un rendimiento mucho más alto con un factor de carga mucho más bajo, reemplazando el 1-2% de negro de carbón con solo el 0.01% de grafeno", explica Terrance Barkan, director ejecutivo de The Graphene Council (New Bern, NC, EE. UU.), Una organización de apoyo y recursos de la industria.
Los investigadores han tenido la intención de desarrollar estos materiales, sintetizando cientos de nanomateriales en capas 2D durante la última década a partir de polímeros, metales y alótropos de carbono como el grafeno (consulte “Tipos y definiciones de nanomateriales”). Estos nanomateriales 2D se pueden combinar, unir, apilar y / o disponer para formar una variedad casi infinita de arquitecturas 3D para crear materiales novedosos y multifuncionales. El grafeno y otros nanomateriales 2D se han combinado en arquitecturas 3D con grandes volúmenes de poros, baja densidad, propiedades mecánicas aumentadas, áreas de superficie específicas altas, transporte rápido de electrones y masas (utilizado para enfriar superficies muy calientes), así como propiedades ópticas y capacidades fotónicas únicas. .
Los primeros participantes avanzan
Los productos de película de CNT alineados verticalmente NanoStitch fueron introducidos por N12 Technologies (Somerville, Mass., EE. UU.) En 2015. Cuando se intercalan en laminados compuestos, NanoStitch aumenta la resistencia al corte interlaminar (ILSS) en> 30% y la compresión después del impacto (CAI) en 15% . CW informó en 2018 que N12 Technologies acordó incorporar la línea de producción continua de películas CNT de 60 pulgadas de ancho en el Instituto de Investigación de la Universidad de Dayton (UDRI, Dayton, Ohio, EE. UU.) como su segunda instalación de fabricación. “Ahora hemos validado completamente las operaciones de producción en las instalaciones de Kettering, Ohio”, dice Christopher Gouldstone, director de desarrollo de producción de N12, y señala que la compañía aún mantiene su sede corporativa y de aplicaciones en Somerville. Él dice que una de las aplicaciones más destacadas para NanoStitch en 2019 es convertirse en el socio tecnológico oficial de compuestos para el equipo de ciclismo de montaña de la Copa del Mundo de Santa Cruz Syndicate. “Después de un proceso de desarrollo colaborativo para implementar NanoStitch en los diseños de bicicletas de Santa Cruz, Syndicate está compitiendo con ruedas reforzadas con NanoStitch resistentes a los impactos esta temporada”, dice Gouldstone. “N12 continúa aplicando NanoStitch para mejorar las propiedades de impacto, compresión, cizallamiento y fatiga de los compuestos para múltiples mercados, incluidos el aeroespacial y los bienes de consumo. También hemos acelerado el desarrollo para la multifuncionalidad, utilizando la alta conductividad de los CNT alineados verticalmente para la conexión a tierra electrostática, la sensibilidad a la tensión y el calentamiento de superficies ”.
El nanocompuesto termoplástico reemplaza al aluminio
Mientras tanto, uno de los primeros termoplásticos comerciales Los nanocomposites fueron lanzados a principios de 2019 por Alpine Advanced Materials LLC (Dallas, Texas, EE. UU.). HX5 es un material de alto rendimiento diseñado para reemplazar el aluminio de grado aeroespacial 6061 T6, mejorando el rendimiento y reduciendo el peso hasta en un 50%. HX5 se comercializa a través de una licencia exclusiva de Lockheed Martin Corp. (Bethesda, Md., EE. UU.), Donde el producto se desarrolló como APEX (Advanced Polymers Engineered for the Extreme) y se probó y comprobó en piezas para aviones, helicópteros, transporte anfibio. vehículos, misiles, cohetes y satélites.
“Alpine Advanced Materials tiene acceso total y derechos globales a la tecnología APEX para aplicaciones militares y comerciales”, dice Jon Bennett, vicepresidente de desarrollo corporativo de Alpine Advanced Materials. "HX5 se puede mecanizar, recubrir, pintar, soldar y unir con adhesivo como el metal, pero se puede procesar mediante moldeo por inyección". Debido a que actualmente Alpine no tiene permitido compartir muchos detalles, CW ha compilado un historial del desarrollo del material a partir de información disponible públicamente.
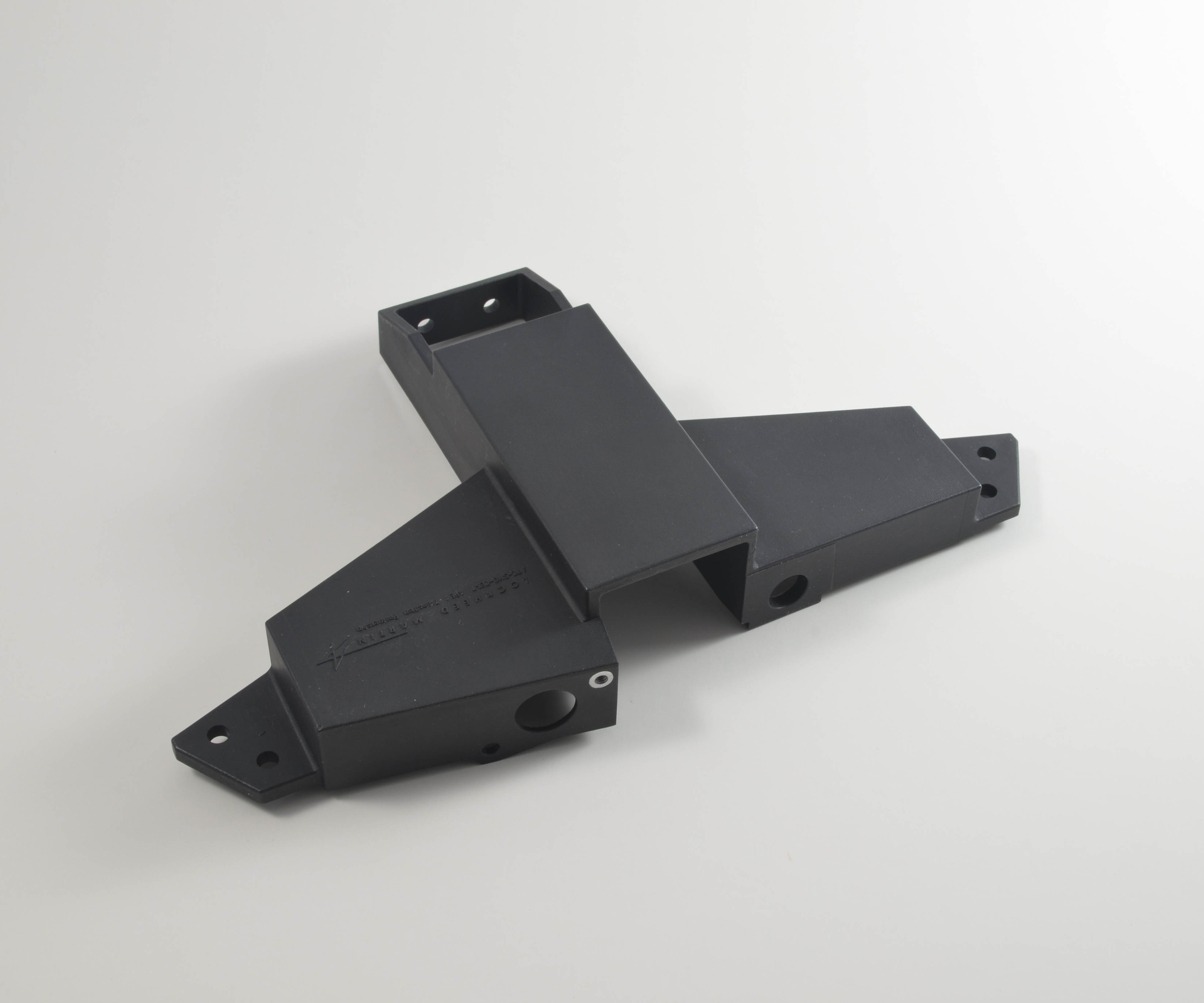
Fig. 2 soportes de nanocompuestos termoplásticos. Esta vista frontal de un soporte de destrucción de misiles hacia adelante muestra el beneficio del moldeo por inyección con nanocompuesto termoplástico HX5, reduciendo el costo en un 93% y el peso en un 15% en comparación con la línea base de aluminio. Fuente | Alpine Advanced Materials LLC
Según el folleto APEX 2013 de Lockheed Martin, HX5 es compatible con la gama completa de procesos de compuestos termoplásticos, incluidos el moldeo por compresión, extrusión, termoformado, colocación automatizada de fibras, bobinado de filamentos e impresión 3D. También permite métodos de unión como soldadura y sobremoldeo. Según los artículos publicados entre 2011 y 2016, el desarrollo del nanocompuesto termoplástico fue supervisado por el Dr. Slade Gardner, ahora asesor principal de tecnología de Alpine Advanced Materials y anteriormente miembro de Lockheed Martin en Fabricación y materiales avanzados para Lockheed's Space Systems Co. Gardner reunió un equipo de los investigadores que desarrollaron la formulación para APEX en 2008 y estaban creando prototipos de piezas para los clientes en 2009. El equipo comenzó a producir prototipos de hardware de naves espaciales en 2010, incluido un soporte de destrucción hacia adelante para misiles que era 93% más barato y 15% más liviano que la línea base de aluminio ( Figura 2). “La pieza de aluminio tenía un plazo de producción de 28 días; a la inversa, moldeamos 300 piezas APEX en un solo día de trabajo ”, dijo Gardner en un artículo de noticias de Lockheed de 2014.
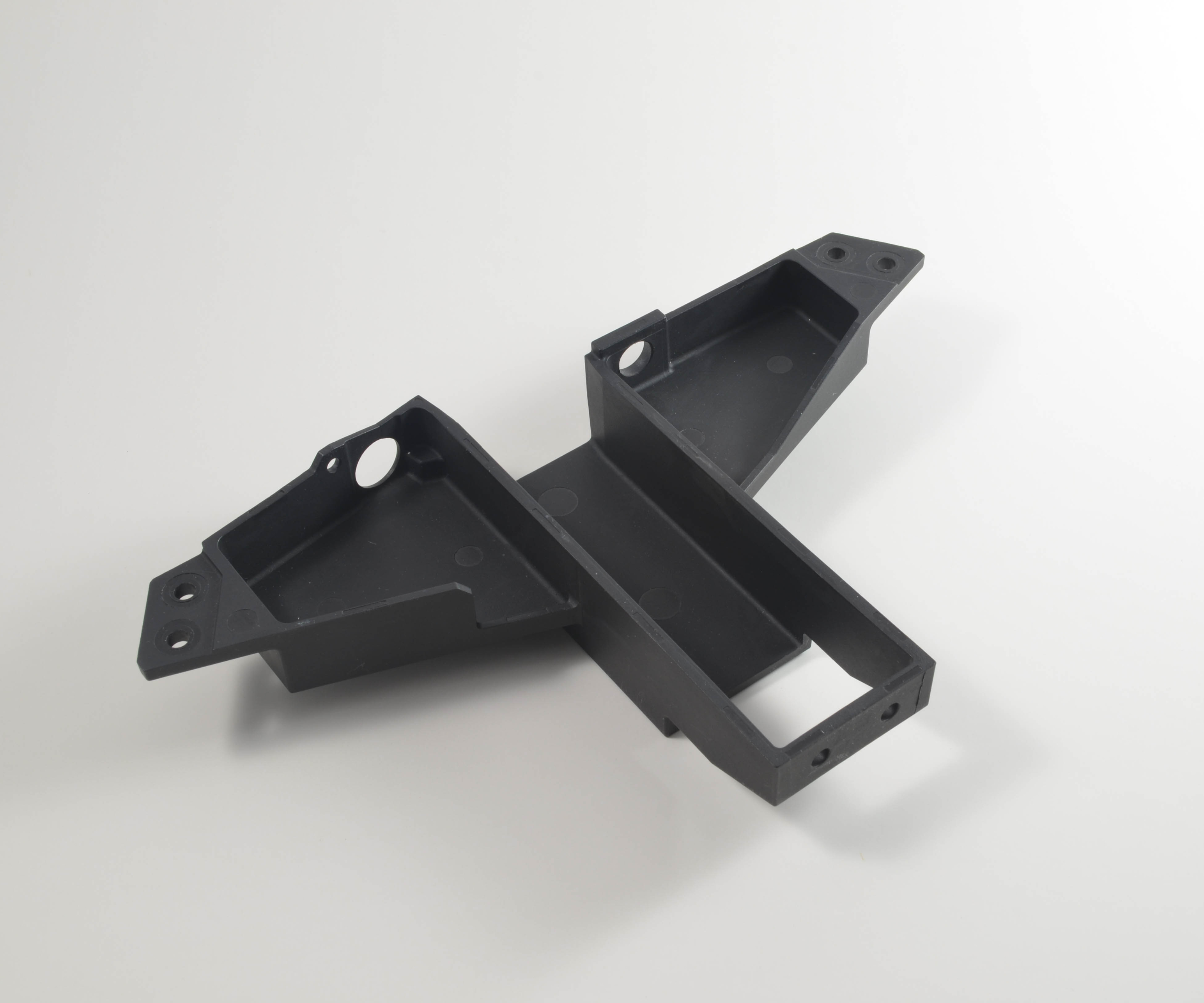
Vista posterior del soporte de nanocompuesto termoplástico. Fuente | Alpine Advanced Materials LLC
El equipo comenzó a trabajar para combinar APEX moldeado por inyección con compuestos de fibra larga para fabricar estructuras híbridas que ofrecen la máxima asequibilidad y alto rendimiento. En una aplicación, una carcasa de motor de cohete sólido de próxima generación y bajo costo, se moldearon por inyección 40 conos de punta de cohete en dos turnos de trabajo para demostrar la capacidad de piezas a gran escala. “Nuestros conos de nariz representan un ahorro de costos del 98% y una mejora del 99% en el tiempo de entrega”, dijo Gardner. En 2011, APEX fue aprobado para reemplazar un compuesto reforzado con fibra continua más costoso en los carenados de las puntas de las alas del avión de combate F-35. El material también se utilizó en más de 1,000 clips que estabilizan la estructura principal del satélite A2100, y para clips, soportes y bandejas de cables en otros productos de defensa antimisiles Lockheed.
Gardner describió el material APEX como una mezcla de "ultrapolímero" reforzada con fibras cortas y nanofibras. También se explica como una plataforma que no se limita a un solo polímero, lo que permite formulaciones personalizadas y fabricables, incluido el uso con refuerzos de fibras tejidas continuas y unidireccionales. HX5 ha superado las pruebas de fuego, humo y toxicidad (FST) para interiores de aeronaves y pruebas de rendimiento a alta temperatura a 520 ° F / 270 ° C.
“Alpine tiene planes de comercializar una variedad de materiales especiales, pero HX5 es nuestro producto estrella en el futuro previsible”, dice Bennett. La empresa no vende el material HX5, pero diseña y fabrica piezas personalizadas. "Estamos creando prototipos de piezas HX5 que se implementarán en muchas industrias", agrega, y señala el reemplazo del aluminio en aviones comerciales y helicópteros con un enfoque específico en interiores y piezas para peso ligero, lo que a su vez reduce las emisiones de carbono. HX5 es ideal para rediseñar ensamblajes compuestos convencionales o de aluminio para reducir el número de piezas.
Aunque las primeras piezas del HX5 se moldearán por inyección, Alpine planea explotar otros procesos de fabricación avanzados, como el sobremoldeo. “Alpine también mantiene su compromiso de mejorar la posición competitiva de Estados Unidos mediante la participación en numerosos programas de desarrollo de defensa”, dice Bennett.
Nano-CMC para hipersónicos
Más lejos del suelo y a velocidades mucho más altas, se encuentra otra área de aplicación emergente para los nanomateriales:los compuestos de matriz nanocerámica (CMC) para hipersónicos. Hipersónico es un término aerodinámico para velocidades mucho mayores que la velocidad del sonido, por lo general menos de Mach 5. En términos más generales, hipersónicos es una categoría de armas y vehículos militares diseñados para viajar a velocidades hipersónicas. Dicha tecnología está en desarrollo en todo el mundo, incluso en EE. UU.
Las velocidades superiores a Mach 5 exigen materiales estructurales livianos que puedan soportar temperaturas de 2480 ° C sin derretirse ni deformarse, al tiempo que resisten la erosión y los proyectiles. Esto significa que deben ser duros, mecánicamente resistentes y resistentes a las fracturas. Estos vehículos también requieren propiedades eléctricas y térmicas específicas para conducir la electricidad y / o proteger los componentes cerrados. Incluso las últimas tecnologías de metales están luchando por satisfacer todas estas demandas.
Las cerámicas refractarias, incluidos los carburos metálicos, los nitruros metálicos y los boruros metálicos, tienen la durabilidad liviana para manejar ambientes tan extremos, pero su síntesis y densificación requiere altas presiones y temperaturas superiores a 1980 ° C, lo que las hace costosas y de uso intensivo de energía. Las cerámicas refractarias puras también son demasiado frágiles.
El Laboratorio de Investigación Naval de EE. UU. (NRL, Washington, D.C., EE. UU.) Está utilizando su experiencia en el desarrollo de resinas de ftalonitrilo novedosas, resistentes al fuego y a altas temperaturas para avanzar en un método potencialmente económico para la fabricación directa de cerámicas refractarias de forma nanocristalina. La tecnología utiliza compuestos poliméricos novedosos para sintetizar y densificar estas cerámicas in situ, en un solo paso, sin necesidad de sinterizar polvos cerámicos a altas presiones y temperaturas. Este desarrollo está dirigido por el Dr. Matthew Laskoski, químico de investigación de NRL y jefe interino de la sección de materiales avanzados, y se describe en su artículo de 2018 “Naval Research Lab diseña compuestos para nuevas plataformas”, publicado en Vol. 5, N ° 2 Fuerza futura de ciencia y tecnología navales revista.
En este proceso, una nueva resina rica en carbono con química de tipo polifenol se mezcla con polvos metálicos mediante molienda de bolas, una técnica común utilizada en el procesamiento de nanomateriales. El precursor cerámico resultante se puede compactar en discos, conos, esferas u otras formas específicas de la aplicación. Un proceso de infiltración de masa fundida reactiva, tales procesos se usan comúnmente para producir (CMC), produce carburos densificados en un horno relleno de argón sin presión a 1370 ° C. Los carburos densos se forman así en una reacción de un solo paso a una temperatura más baja que y sin la presión de las técnicas convencionales de sinterización y prensado en caliente. Debido a que el tamaño de los cristales de los carburos es inferior a 40 nanómetros, las nanocerámicas resultantes no son tan frágiles como los materiales de grano más grueso.
Otra ventaja es que el polímero termoendurecible actúa como una fuente fundible de carbono que reacciona con las partículas de polvo metálico. También facilita el refuerzo de la cerámica con metales, fibras de carbono y cerámicas secundarias. (Se puede ver un ejemplo de cerámica secundaria en la Fig. 1 (E) donde el compuesto bifásico comprende una matriz cerámica primaria y un refuerzo cerámico secundario). Las CMC resultantes proporcionan una vía para un mayor control de los procesos mecánicos, térmicos, eléctricos y ablativos. propiedades.
Según Laskoski, los carburos refractarios como el carburo de circonio y el carburo de titanio no se ven afectados por temperaturas extremadamente altas y son impermeables al fuego, plasma o calentamiento atmosférico durante el viaje a hipervelocidad. Sin embargo, las cerámicas nanocristalinas derivadas de polímeros de NRL se extienden más allá de los carburos para incluir resinas ricas en nitrógeno que pueden reaccionar con metales para formar nitruros metálicos. NRL ha desarrollado compuestos de nitruro de silicio, nitruro de circonio y diboruro de titanio, así como métodos para reforzar las CMC resultantes con fibras resistentes. Estas cerámicas refractarias exhiben alta resistencia, estabilidad térmica y conductividades eléctricas y térmicas variables que les permiten satisfacer las demandas de los componentes de vehículos hipersónicos.
Los motores de dichos vehículos absorben grandes cantidades de calor y deben disiparlo de manera eficaz, lo que ni siquiera las aleaciones metálicas más avanzadas pueden hacer sin pérdida de resistencia e integridad estructural. Laskoski afirma que los componentes de nitruro y boruro de metal son más aptos para resolver este desafío, mientras que los compuestos de nitruro de silicio ofrecen potencial para radomos de comunicaciones de alta resistencia y resistentes a la oxidación. NRL está desarrollando tecnología de fabricación aditiva que incorporará nanoestructuras en estos materiales y ajustará aún más las propiedades de blindaje dieléctrico, térmico y electromagnético a una resolución más alta que la posible con los materiales disponibles actualmente.
Toxicidad de nanocompuestos y manipulación segura
Debido a que los nanomateriales son más pequeños que las células del cuerpo humano y las células sanguíneas, existe preocupación por su toxicidad, no solo por la exposición de los trabajadores durante la fabricación y procesamiento de materiales, sino también cuando las piezas se mecanizan, lijan y reciclan. El Graphene Council publicó recientemente un seminario web en el que el Instituto Nacional de Seguridad y Salud Ocupacional (NIOSH, Washington, DC, EE. UU.) Discutió estos temas y enumeró sus recursos, incluidas tres publicaciones de 2018:"Protección de los trabajadores durante las operaciones de reactores de nanomateriales", "Protección de los trabajadores" durante la manipulación de nanomateriales ”y“ Protección de los trabajadores durante el procesamiento intermedio y posterior de nanomateriales ”.
NIOSH afirma que ha completado extensos estudios toxicológicos en solo unos pocos nanomateriales, incluidos los nanotubos de carbono (CNT). Debido a que las ratas y ratones expuestos a CNT y nanofibras de carbono (CNF) han mostrado inflamación pulmonar persistente, tumores y fibrosis (cicatrización pulmonar progresiva que dificulta la respiración), NIOSH enfatiza que es importante controlar la exposición de los trabajadores durante la producción de nanomateriales. La recolección de nanomateriales de reactores y la limpieza de reactores resulta en exposiciones potencialmente altas. Los trabajadores también pueden estar expuestos durante la pulverización y el mecanizado (por ejemplo, molienda de bolas), así como durante la manipulación de nanomateriales para pesar, envasar y mezclar / componer. NIOSH afirma que el control de la exposición de los trabajadores parece factible con técnicas estándar que incluyen el cerramiento de la fuente, la ventilación de extracción local, el equipo de protección personal (PPE) y las mejores prácticas en la limpieza y limpieza de partículas finas.
El límite de exposición recomendado por NIOSH (REL) para CNT / CNF es inferior a 1 μg / m 3 como promedio ponderado en el tiempo (TWA) de 8 horas. Se pueden utilizar técnicas analíticas como la microscopía electrónica de barrido y transmisión (SEM, TEM) para garantizar que se mantenga este umbral. NIOSH advierte específicamente que no es seguro usar el límite de exposición permisible (PEL) de OSHA para el grafito (5,000 μg / m 3 ) o negro de carbón (3500 μg / m 3 ), y también que se necesita más investigación para caracterizar completamente los riesgos para la salud de los CNT y los CNF, incluidos estudios en animales a largo plazo y estudios epidemiológicos en trabajadores.
“Los CNT se han estudiado bastante bien”, dice Jo Anne Shatkin, presidente de Vireo Advisors LLC (Boston, Mass., EE. UU.), Una consultora de salud y seguridad en el lugar de trabajo. "Hace diez años, no lo sabíamos, pero ahora los estudios muestran que la toxicidad más drástica que temíamos no se ha materializado realmente". Señala que la preocupación por los nanomateriales de alta relación de aspecto, como los CNT, es que se comportan como sílice cancerígena y fibras de asbesto. “Pero muy pocos de los estudios de materiales CNT cumplen con ese paradigma de fibra en este momento”, explica. “Sin embargo, todavía hay muchos desafíos. En su mayoría, hemos probado nanomateriales prístinos, no funcionalizados, ya que están en uso. La incertidumbre permanece porque los nanomateriales son muy variados en composición, forma y funcionalización ". Todos estos factores pueden afectar la toxicidad, incluido el método de funcionalización y la química utilizada. "Está creando propiedades que hacen que el CNT reaccione mejor con un polímero, pero no sabemos cómo afecta eso a las interacciones del material con la sangre o las células del cuerpo", dice. Todavía no estamos en una etapa predictiva. Eso es lo que estamos explorando ahora. ¿Podemos idear un modelo estandarizado para evaluar la exposición y la toxicidad que tenga en cuenta todas estas variables? ”
Shatkin describe el trabajo que se está realizando y una serie de métodos de prueba estándar en desarrollo en la Sociedad Estadounidense de Ensayos y Materiales (ASTM, Conshohocken, Pensilvania, EE. UU.) Y el Instituto Nacional Estadounidense de Normas (ANSI, Washington, D.C., EE. UU.). “El Grupo de Desarrollo de Estándares de Nanotecnología ISO / ANSI TC 229 tiene docenas de estándares para probar nanomateriales”, dice, “así como métodos de seguridad y salud ocupacional, como cómo realizar SEM y TEM para mediciones de distribución de partículas en relación con PEL y REL . " Shatkin señala que tanto ISO como ASTM tienen un estándar en desarrollo que analiza el riesgo de liberación de nanomateriales de compuestos a través del mecanizado, lijado y otras operaciones secundarias. Aquí, al menos, se ha dado luz verde preliminar. Shatkin dice que el trabajo completado por los consorcios de la industria NanoRelease muestra que el lijado y el mecanizado de piezas que contienen nanomateriales no representan nuevas amenazas para la salud y la seguridad. “Obtienes liberación de nanomateriales, pero están unidos al polímero, no a partículas a nanoescala libres”, explica. "Por lo tanto, nuestras pautas actuales para las partículas de compuestos de mecanizado son suficientes". Sin embargo, es posible que las empresas, especialmente aquellas con trabajadores y recursos limitados, no vean el polvo de mecanizado como una amenaza grave para la salud. Por lo tanto, es posible que no siempre sigan las pautas y las mejores prácticas para el PPE y los respiradores, sin mencionar los recintos y el equipo de ventilación. But because there is still uncertainty, such complacency isn’t an option when working with nanomaterials.
Nanocomposites are indeed enabling higher performance, greater multifunctional capabilities and potentially lower-cost and lighter-weight structures for numerous applications and markets. “There is a huge opportunity for benefit with nanomaterials, and we’ve learned a lot,” says Shatkin, “but there’s still a lot of uncertainty. Our best path forward is to be cautious, minimize exposure and make sure, as much as possible, that we make manufacture, handling and use as safe as possible.”
Verifying producers and supporting developers
One of the challenges facing a dynamic, fast-maturing technology is to build trust in the supply chain. To that end, the Graphene Council is working to mature the global supply chain through its Verified Graphene Producer program. Versarien plc (Cheltenham, U.K.) is the first graphene supplier to successfully complete this independent, third-party verification system that involves a physical inspection of the production facilities and review of the entire production process and safety procedures. “We also take random samples of their products and submit them for blind testing to be rigorously characterized at the National Physical Laboratory (NPL, Teddington, U.K.), a world-class institution that follows ISO/TR 19733:2019 for Nanotechnologies,” says the Graphene Council’s Barkan. NADCAP is an analogous audit program long used by the aerospace industry for the same purpose. “Without this type of program, customers have no clue what they are getting when they buy and receive graphene products,” says Barkan. “Our Verified Graphene Producer program is an important step to provide a level of confidence in the both products and producers worldwide.”
The Graphene Council also works to improve development of graphene applications. “We connect companies with resources to help them quickly navigate products, producers, materials science and testing for faster, more successful development,” says Barkan. “We also provide independent, third-party advisory services to help companies that want to use graphene, but don’t know where to start. We not only have reach into our formal members, but also track more than 200 companies involved with graphene worldwide. We monitor what is being developed and the latest scientific and research results, helping to understand what type of graphene to use, how to functionalize and disperse it and how to test for performance.” He notes a close relationship with the Graphene Engineering &Innovation Center (GEIC) at the University of Manchester (Manchester, UK), where graphene was first discovered. “This is a rapid prototyping center,” says Barkan, “and helps us to leverage what graphene can do.”
Resina
- Estuvimos cerca de un avance crucial para la visibilidad de la cadena de suministro
- Tres buenos argumentos para una cadena de suministro flexible
- ¿Es Blockchain un ajuste perfecto para la cadena de suministro?
- ¿Cuándo estará listo Blockchain para la cadena de suministro?
- Remodelación de la cadena de suministro y la logística para la resiliencia
- Preparar su cadena de suministro para el futuro para la nueva normalidad
- Modernización de la cadena de suministro para mejorar la experiencia del cliente
- Cómo prepararse para la próxima interrupción de la cadena de suministro
- ¿Su empresa está lista para recibir una alerta de cumplimiento de la cadena de suministro?
- Cuatro consideraciones para las cadenas de suministro posteriores a Covid
- Refuerzo de la seguridad de la cadena de suministro para las fiestas