Novedoso preimpregnado para moldeo por compresión en RAPM
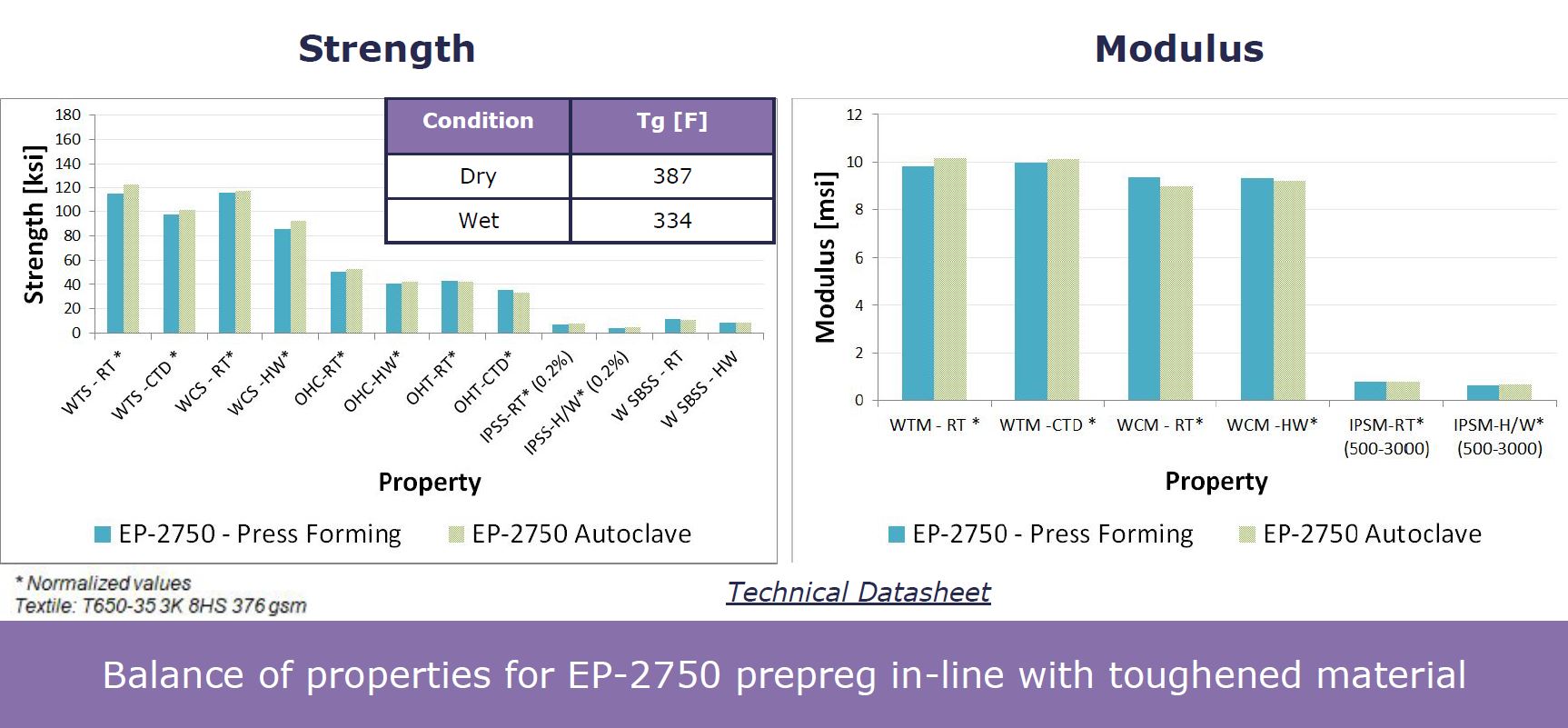
El preimpregnado de fibra de carbono / epoxi ha sido el material de referencia para los compuestos aeroespaciales durante décadas porque proporciona altas propiedades mecánicas y un contenido preciso de resina / fibra, así como facilidad de manejo para la colocación y curado en autoclave. Sin embargo, a medida que los fabricantes de aeronaves y movilidad aérea urbana (UAM) exploran tasas de producción más altas y costos más bajos, el moldeo por compresión es atractivo, lo que reduce los tiempos de ciclo y aumenta la eficiencia en comparación con el autoclave. En su forma más simple, el moldeo por compresión comprende precalentar el material de moldeo, colocarlo en una cavidad de herramienta abierta y consolidar con presión hidráulica a temperatura, durante la cual el material termoestable líquido se convierte en un sólido. Luego, la pieza curada se expulsa para realizar los pasos necesarios de recorte y acabado.

La combinación de moldeo por prensa y preimpregnado no solo ofrece un proceso eficiente y de alta velocidad con el rendimiento y el fácil manejo del preimpregnado, sino que también evita algunas de las complejas dinámicas del proceso de llenado de refuerzos secos con resina líquida durante procesos como la infusión de resina y el moldeo por transferencia de resina. (RTM). Especialmente para aeroestructuras más pequeñas, el moldeo por prensa preimpregnado ofrece el potencial de tiempos de takt de <30 minutos al mismo tiempo que logra piezas de geometría compleja de alta calidad.
Solvay Composite Materials (Alpharetta, Georgia, EE. UU.) Fue un socio clave en el programa RApid High-Performance Manufacturing (RAPM) dirigido por The Boeing Co. (Chicago, Ill., EE. UU.). RAPM es la parte de "formación" del programa de formación y materias primas adaptables (TFF) lanzado por la Agencia de Proyectos de Investigación Avanzada de Defensa (DARPA, Arlington, Va., EE. UU.) En 2015. Su objetivo es permitir fabricación de piezas compuestas pequeñas y de formas complejas y aumenta la capacidad de los compuestos para competir contra el aluminio mecanizado en aplicaciones de defensa.
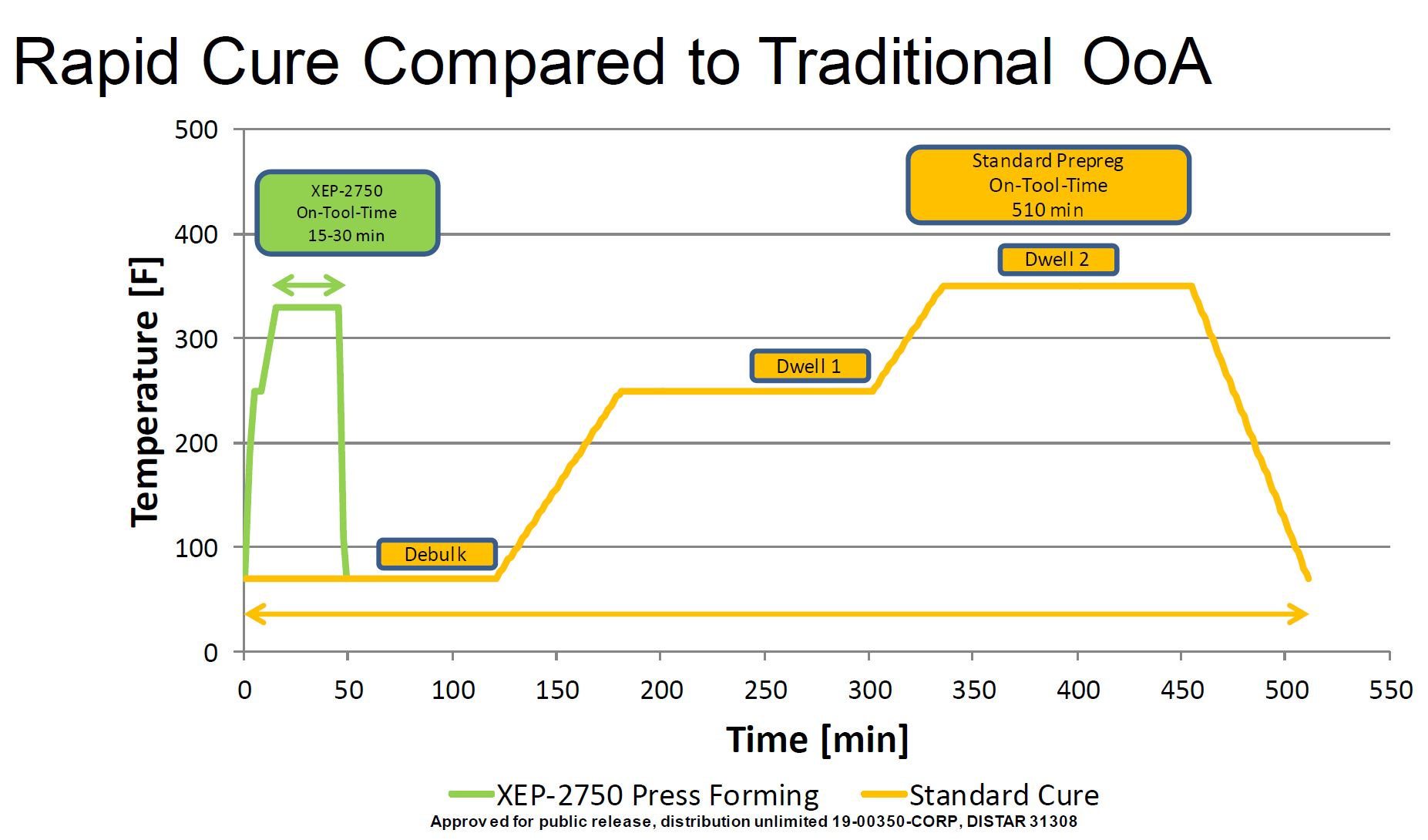
Solvay, proveedor desde hace mucho tiempo de Boeing para aplicaciones de defensa, también ha sido líder en soluciones novedosas para la industria aeroespacial comercial, como el preimpregnado epoxi fuera de autoclave (OOA) CYCOM 5320-1, y también para la automoción, como el preimpregnado de vinilo híbrido SolvaLite 730 de 1 minuto de takt time.
RAPM fue una oportunidad perfecta para que Solvay probara y perfeccionara su sistema experimental XEP-2750, ahora comercializado como CYCOM EP2750, que fue desarrollado para unir la producción de compuestos aeroespaciales y automotrices. Este blog, una barra lateral en línea de la función de mayo de 2020 "Revolucionando el paradigma de costos de compuestos, Parte 2:Conformado", revisa ese desarrollo, así como los procesos de moldeo por compresión utilizados y lo que CYCOM EP2750 ofrece a los fabricantes de compuestos aeroespaciales y automotrices.
Las referencias para este blog incluyen:
- "Fabricación de componentes de producción aeroespacial mediante prensa de marco de resorte" por Timothy J. Luchini
1
, Alejandro J. Rodríguez
2
, Scott A. Rogers
2
, Aurele Bras
3
, Adam Whysall
3
, Richard Russell
3
, Scott Lucas
2
, Gail L. Hahn
1
. Actas de la conferencia SAMPE. Charlotte, NC, 20-23 de mayo de 2019.
- "Desafíos de las geometrías de piezas estructurales aeroespaciales para el moldeo por compresión de alta velocidad" por Aurele Bras
1
, Alejandro J. Rodríguez
2
, Richard Russell
1
, Timothy J. Luchini
3
, Travis Adams
3
, Adam Whysall
1
, Scott A. Rogers
2
, Scott Lucas
2
, Gail L. Hahn
3
. Sociedad para el Avance de la Ingeniería de Materiales y Procesos - América del Norte. Actas de la conferencia SAMPE. Seattle, WA, del 4 al 7 de mayo de 2020. Sociedad para el Avance de la Ingeniería de Materiales y Procesos - América del Norte.
- "Moldeo rápido de alto rendimiento de preimpregnado estructural xEP-2750 para moldeo por compresión" por Timothy J. Luchini 1 , Alejandro J. Rodríguez 2 , Scott A. Rogers 2 , Aurele Bras 2 , Adam Whysall 2 , Richard Russell 2 , Scott Lucas 2 , Gail L. Hahn 1 . SAMPE 2019.
1 The Boeing Company, Saint Louis, MO 63134, 2 Materiales compuestos de Solvay, Anaheim, California, EE. UU. Y 3 Materiales compuestos de Solvay, Heanor, Reino Unido
- Seminario web CompositesWorld:"Procesos automotrices para la fabricación de compuestos aeroespaciales de alta velocidad" por Alejandro Rodríguez, Solvay Composite Materials, Anaheim, California, EE. UU.
Objetivos de material y proceso
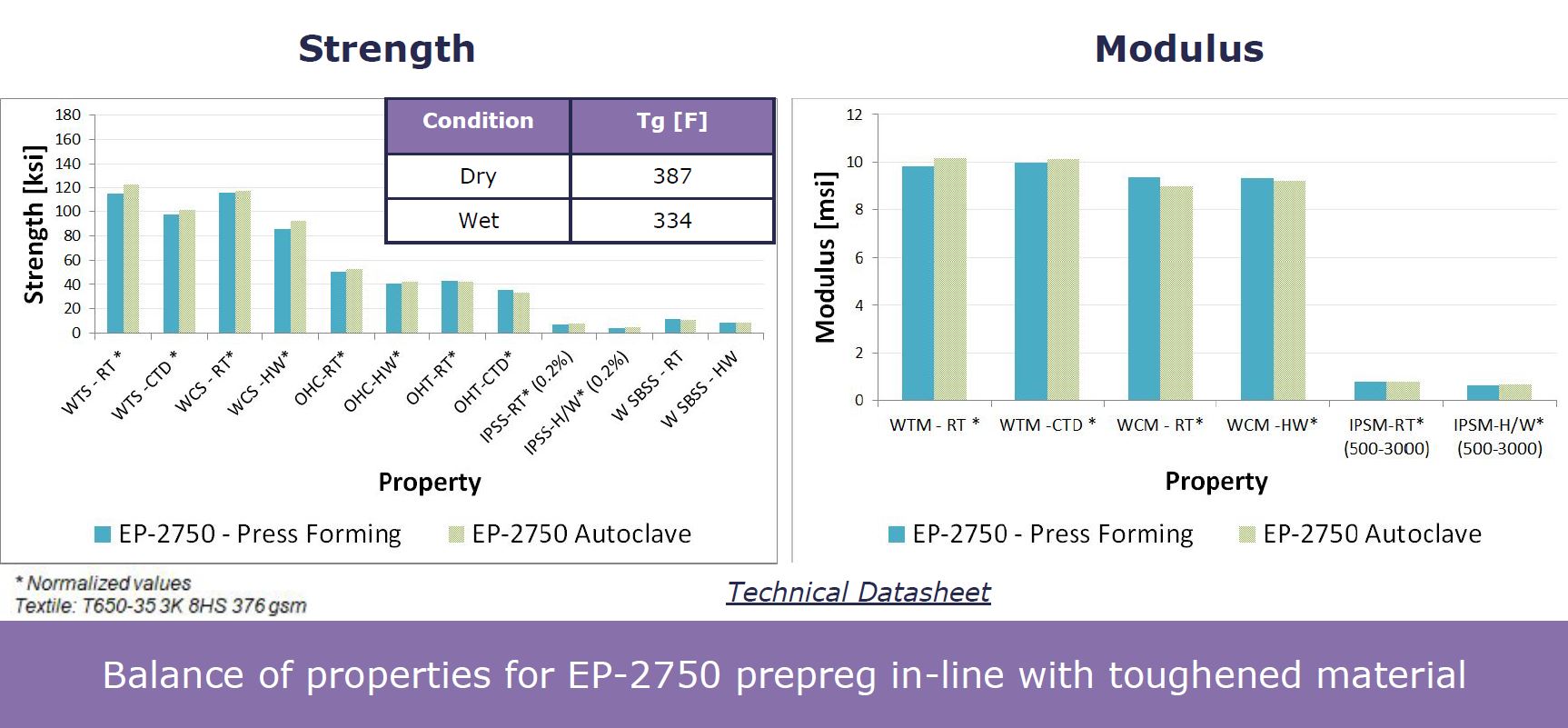
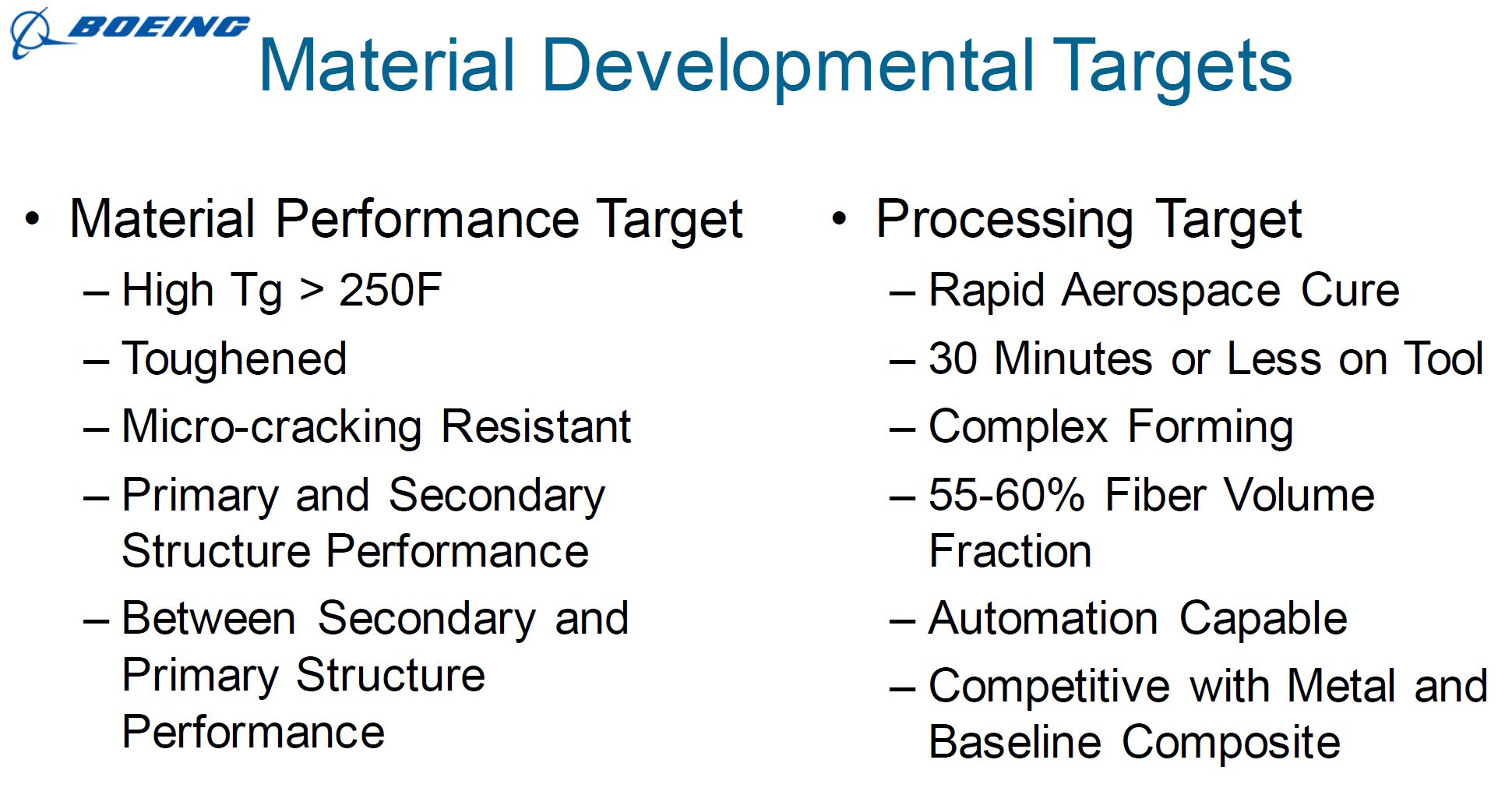
CYCOM EP2750 fue desarrollado para cumplir con los objetivos de rendimiento establecidos por Boeing para un epoxi endurecido aeroespacial, que exhibe un equilibrio de temperatura de transición vítrea (Tg) de hasta 350 ° F, buenas propiedades de muescas, por ejemplo, compresión en pozo abierto (OHC) y tensión en pozo abierto. (OHT) - y resistencia a solventes. Esta nueva clase de preimpregnado es aplicable tanto a aeroestructuras primarias como secundarias y es compatible con múltiples refuerzos (por ejemplo, fibra de vidrio y carbono).
CYCOM EP2750 también se desarrolló con la capacidad de aumentar la producción mediante el manejo automatizado y el moldeo por compresión. Esto incluye un tiempo de curado en la herramienta de 15 a 30 minutos a 330-370 ° F, con un poscurado de 1 hora a 350 ° F. Este tiempo de takt de 30 minutos o menos permite un volumen de producción anual de 10,000 piezas por herramienta.
Solvay utilizó dos variaciones de moldeo por compresión durante el programa RAPM:moldeo de marco de resorte y conformado de doble diafragma (DDF). Ambos utilizan el principio de sostener una pieza en bruto plana y llevarla a través de una etapa de precalentamiento de infrarrojos (IR) antes de transportarla a una cavidad de herramientas de metal combinada. Luego, la prensa cierra el molde de acero siguiendo un programa automatizado y aplica toda la presión al preimpregnado durante el tiempo restante en la herramienta.
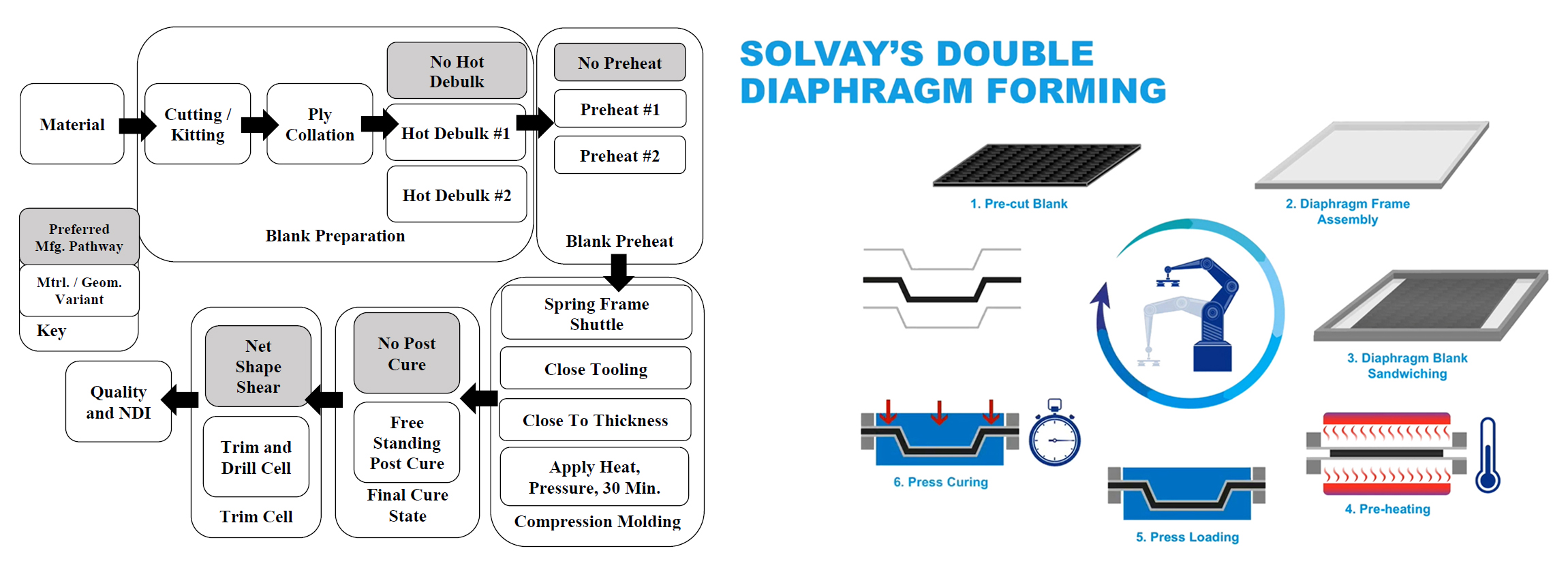
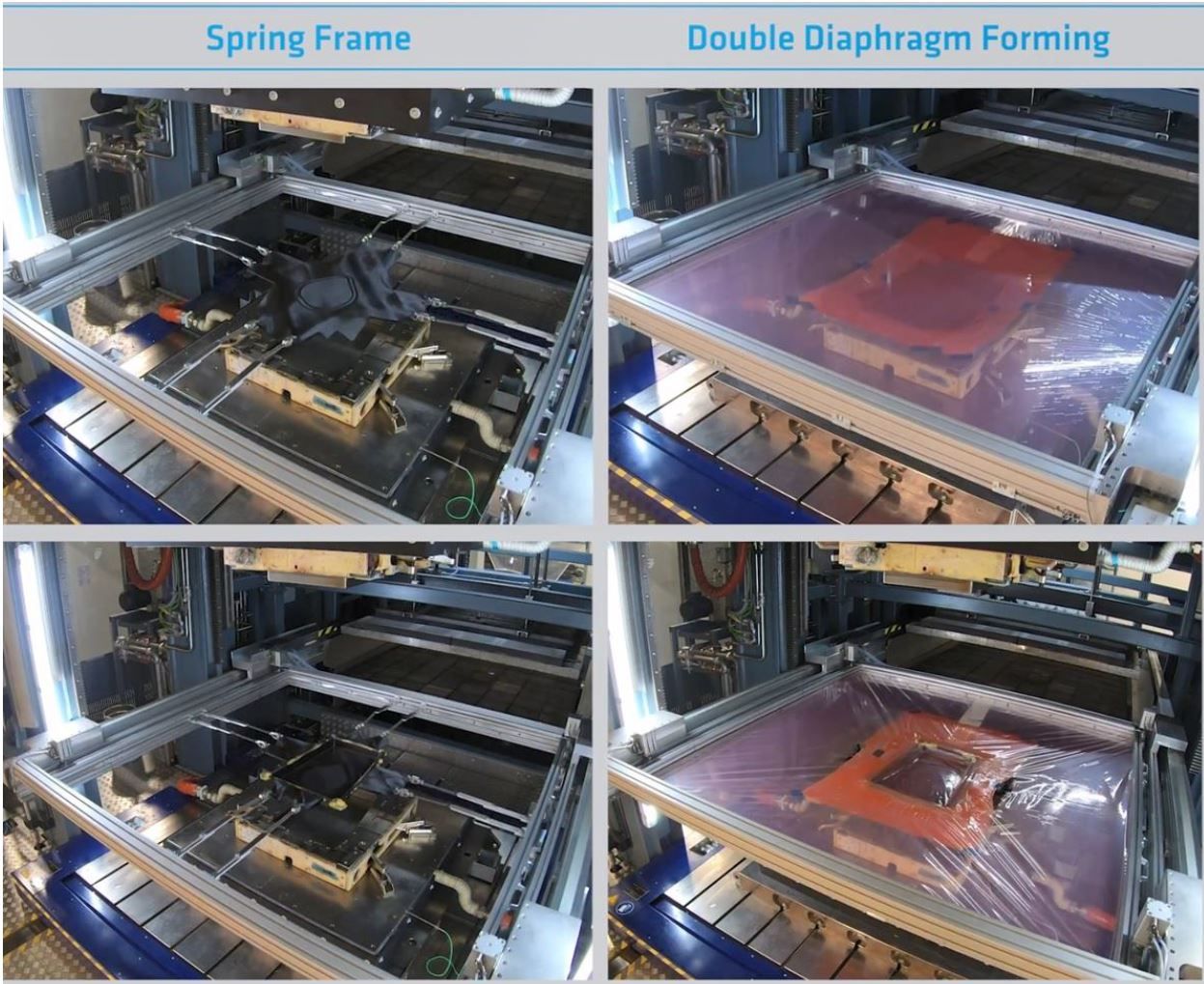
Tanto la moldura con marco de resorte como la DDF utilizan herramientas de metal combinadas y ofrecen un enfoque de entrada y salida en caliente, eliminando el calentamiento y enfriamiento de la herramienta, para una producción de alta velocidad. Ambos se utilizaron para moldear con éxito múltiples tipos de piezas de geometría compleja con rellenos, bridas verticales y variaciones de grosor de 3,8 a 8,9 milímetros. Estas piezas se fabricaron en el centro de aplicaciones de Solvay en Heanor, Reino Unido. tiempos de 3 minutos o menos para piezas pequeñas a medianas que utilizan preimpregnados para automóviles. Solvay ve múltiples beneficios en el proceso de DDF que incluyen:
- Eliminación del paso de preformado:pieza en blanco 2D a pieza 3D
- No requiere desmoldeo ni limpieza
- Reducción de materiales auxiliares (p. ej., respiradero, purgador, embolsado, cinta) frente a autoclave
- Mejora de la compra para volar frente a la moldura de marco de resorte porque se necesita menos material sobrante para sujetar las abrazaderas de resorte.
La impregnación total frente a la parcial mantiene la presión
Las características de EP2750 que facilitan el moldeo por compresión incluyen su baja adherencia para el manejo automático de pick and place y su naturaleza completamente impregnada en comparación con CYCOM 5320-1, que está parcialmente impregnado para facilitar la respiración de los bordes, necesario para laminados sin huecos que utilizan procesamiento OOA. Sin embargo, el moldeo por compresión aprovecha un flujo de resina forzado muy rápido debido a las presiones más altas aplicadas, por ejemplo, hasta 350 psi (máximo típico para EP2750) en comparación con 35 psi comunes en el procesamiento en autoclave y 14,7 psi en el procesamiento OOA solo al vacío.
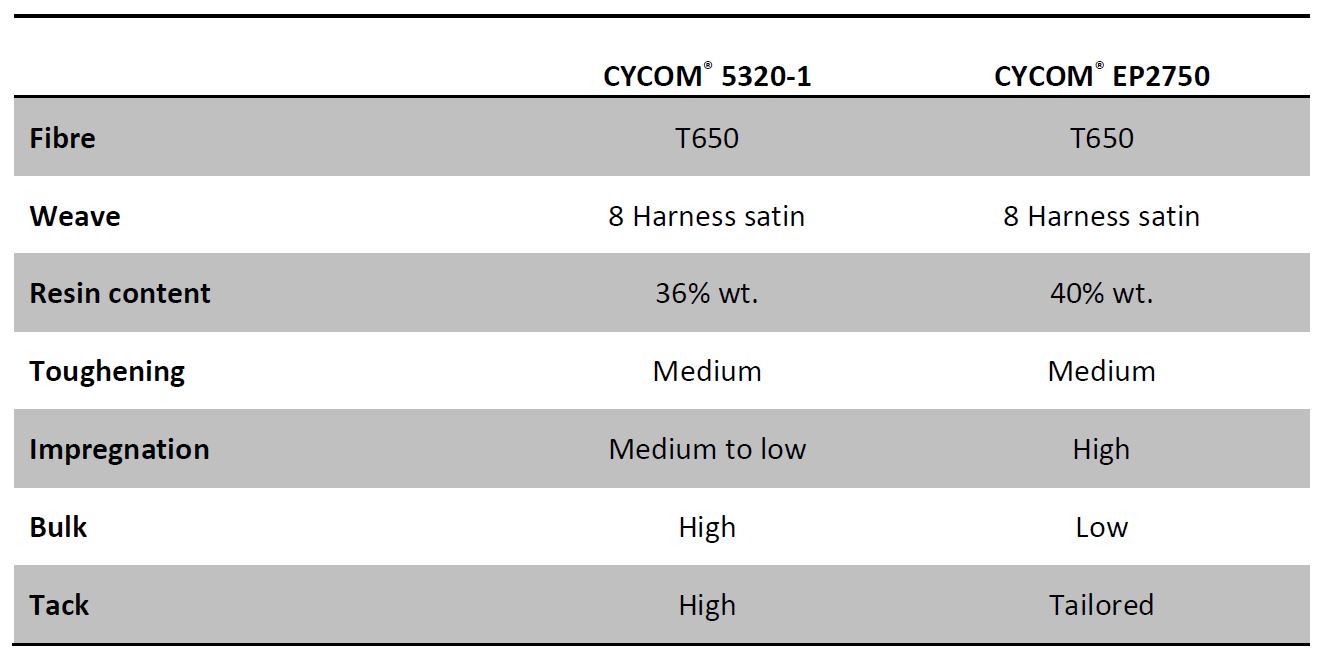
Tener un preimpregnado más completamente impregnado, a pesar de que el contenido de resina es solo un poco más alto (40% en CYCOM EP2750 en comparación con 36% en CYCOM 5320-1) mantiene la presión hidrostática durante la compactación y el curado en la cavidad de la herramienta de metal combinada, lo que resulta en un menor riesgo de áreas secas, grosor inconsistente de la pieza curada (CPT), arrugas y otros defectos al tiempo que se garantiza una buena calidad de la superficie.
En particular, Solvay desarrolló una película transformadora patentada para aumentar la presión hidrostática cuando se usa preimpregnado CYCOM 5320-1 con un contenido de resina más bajo. Aplicada a la disposición de la pieza antes del moldeo por compresión, la película Transformer aumenta el contenido de resina y ayudó a que el CPT cumpliera con los requisitos en las pruebas de moldeo de piezas RAPM.
Pruebas de moldeo de piezas RAPM
Como se explica en el artículo destacado de CW de mayo de 2020, CYCOM EP2750 fue uno de los materiales principales probados en la pista de preimpregnado termoestable de RAPM. Se incluyen las piezas de Pathfinder probadas en la fase inicial de fabricación y desarrollo
Paneles de acceso con reborde TS-RAPM-001 y -009, nervadura TS-RAPM-002 y canal en C curvo TS-RAPM-003. Las piezas se diseñaron en Boeing (en varias ubicaciones a nivel mundial), las herramientas se fabricaron en C-Con GmbH (Múnich, Alemania), las piezas se fabricaron en el Centro de aplicaciones de Solvay en Heanor, Reino Unido y luego se probaron en Solvay Anaheim, California, EE. UU. Y Boeing St. Louis, Missouri, EE. UU.
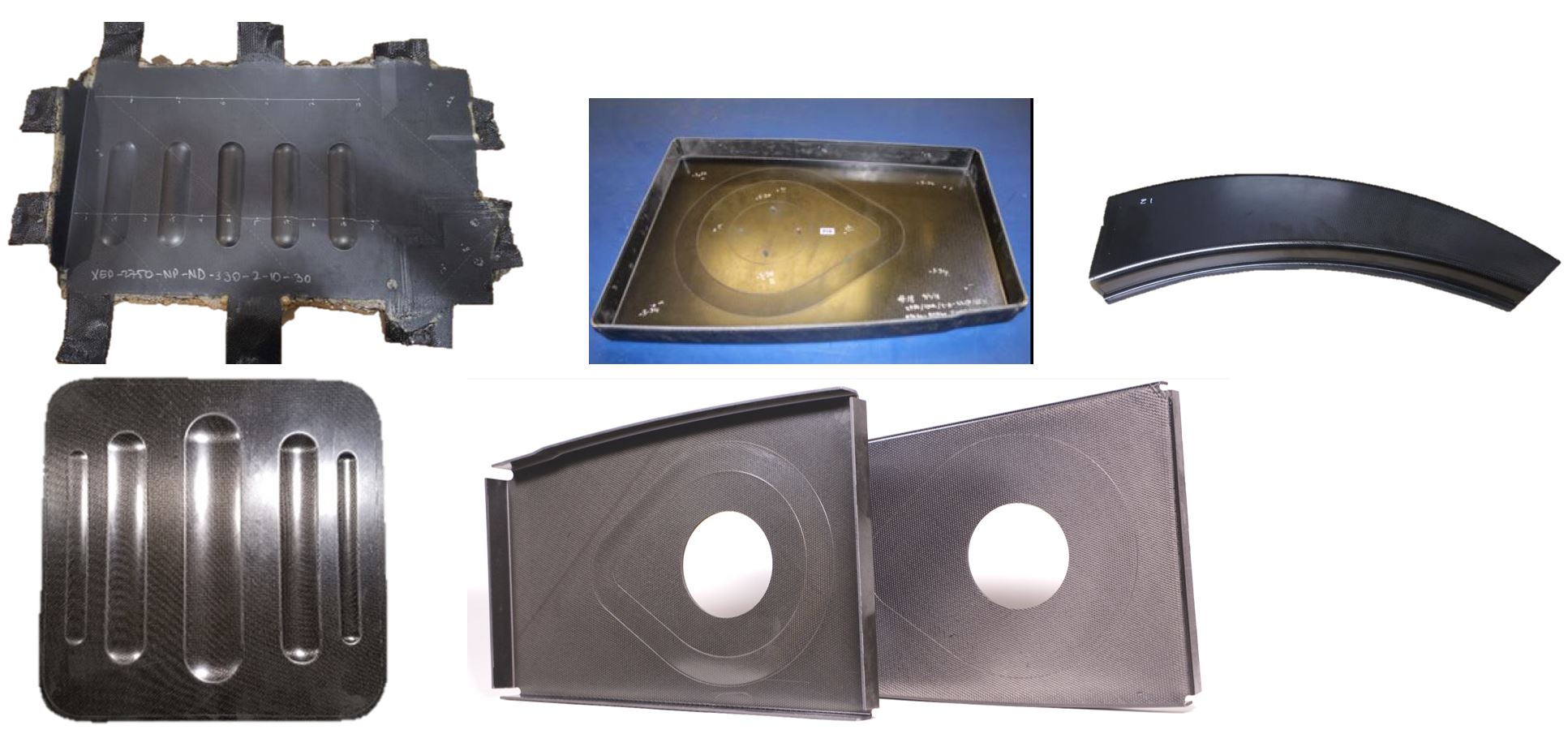
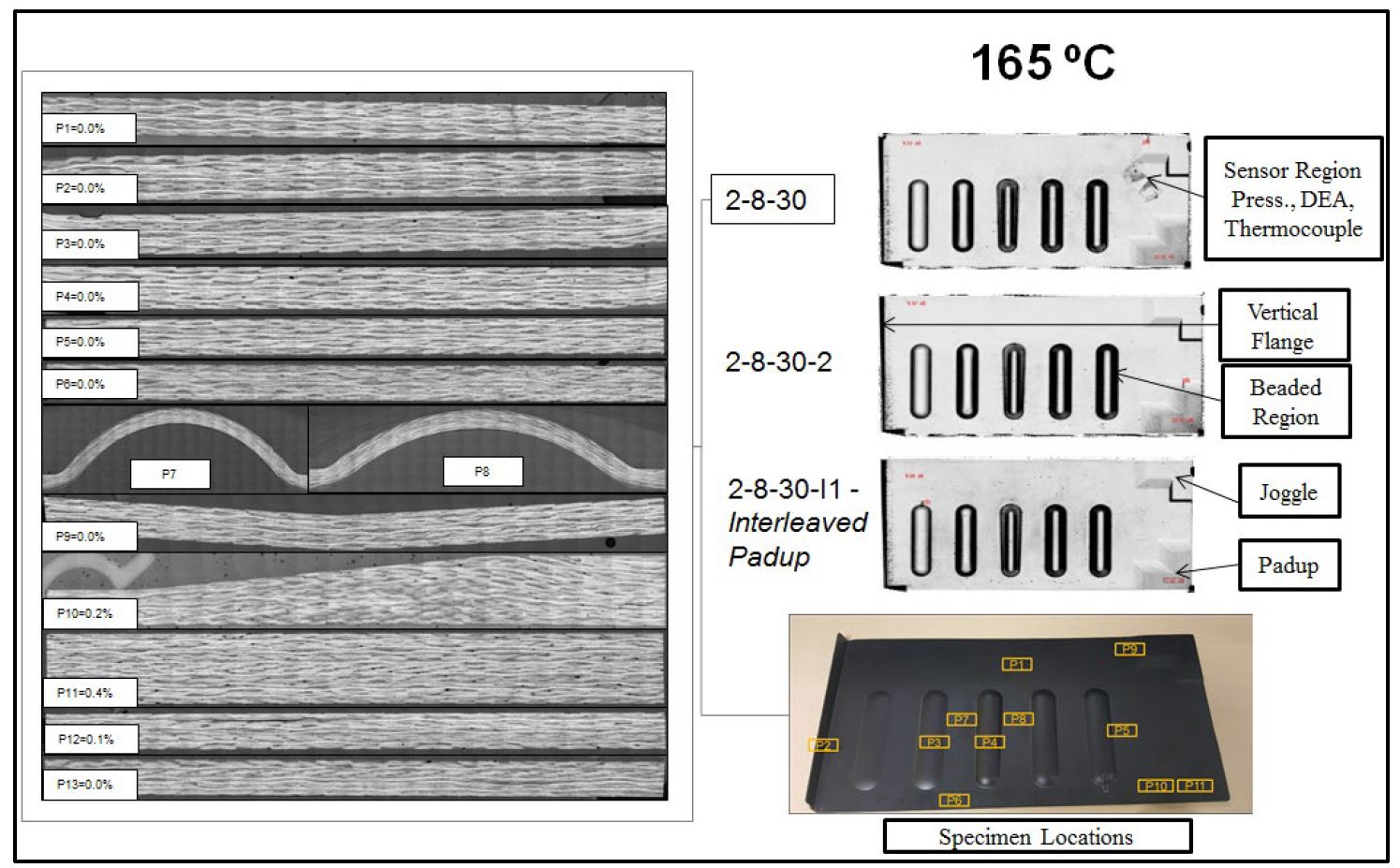

La calidad de la superficie se evaluó mediante inspección no destructiva (NDI) y los paneles seleccionados se seccionaron para determinar la porosidad, la cizalladura de haz corto, la fracción de volumen de fibra, el contenido de resina, el grado de curado y la temperatura de transición vítrea.
Se lograron fácilmente niveles de porosidad por debajo del 0,5%, atribuidos a las altas presiones de consolidación del moldeo por compresión. Aunque los parámetros del proceso tenían que optimizarse para cada parte diferente, una vez bloqueados, se demostró que el proceso era repetible.
Panel de cuentas TS-RAPM-009
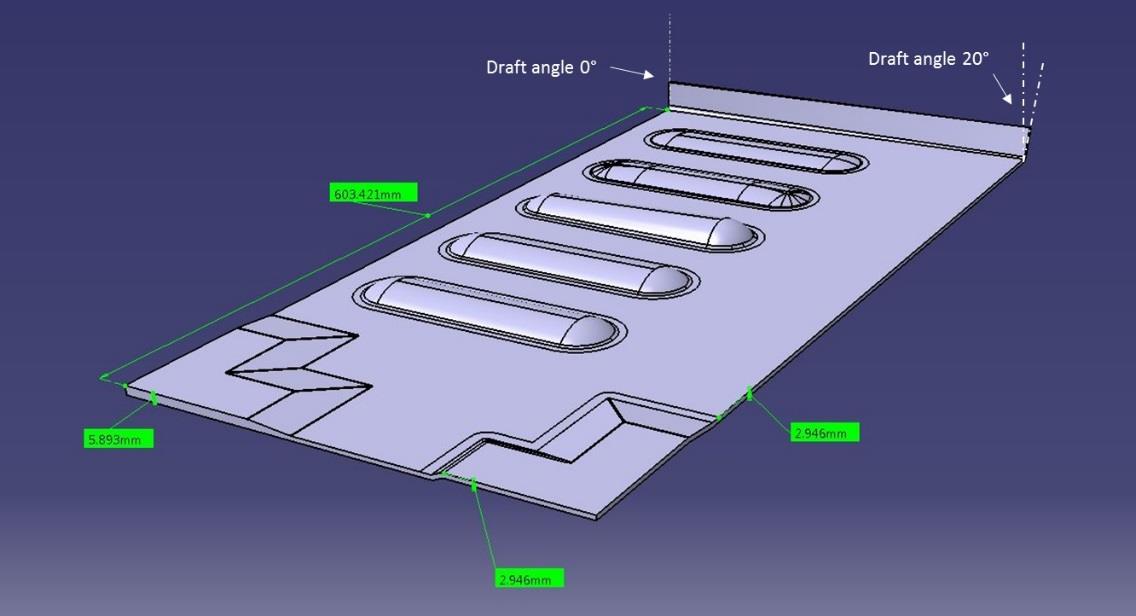
Esta parte plana de 600 milímetros de largo presentaba cuentas paralelas de varias geometrías. El grosor aumentó de 3 a 6 milímetros en una esquina (pad-up) mientras que la esquina opuesta presentó un movimiento de grosor constante. El borde opuesto comprendía un ala vertical con un ángulo de desmoldeo que variaba linealmente de 0 ° a 20 °.
Deslizamiento de acolchados
Las pruebas iniciales se realizaron con rellenos apilados en la superficie de la bandeja. Sin embargo, debido a que las capas acolchadas estaban ubicadas cerca del borde de la pieza, era posible que salieran de la pieza, lo que resultaba en una región de baja presión durante el curado y porosidad. La solución fue intercalar las capas acolchadas dentro de la pila de laminado. El riesgo de deslizamiento y porosidad no se observó en las partes posteriores en las que las almohadillas se ubicaron lejos de los bordes y quedaron bloqueadas de manera efectiva por el material circundante.
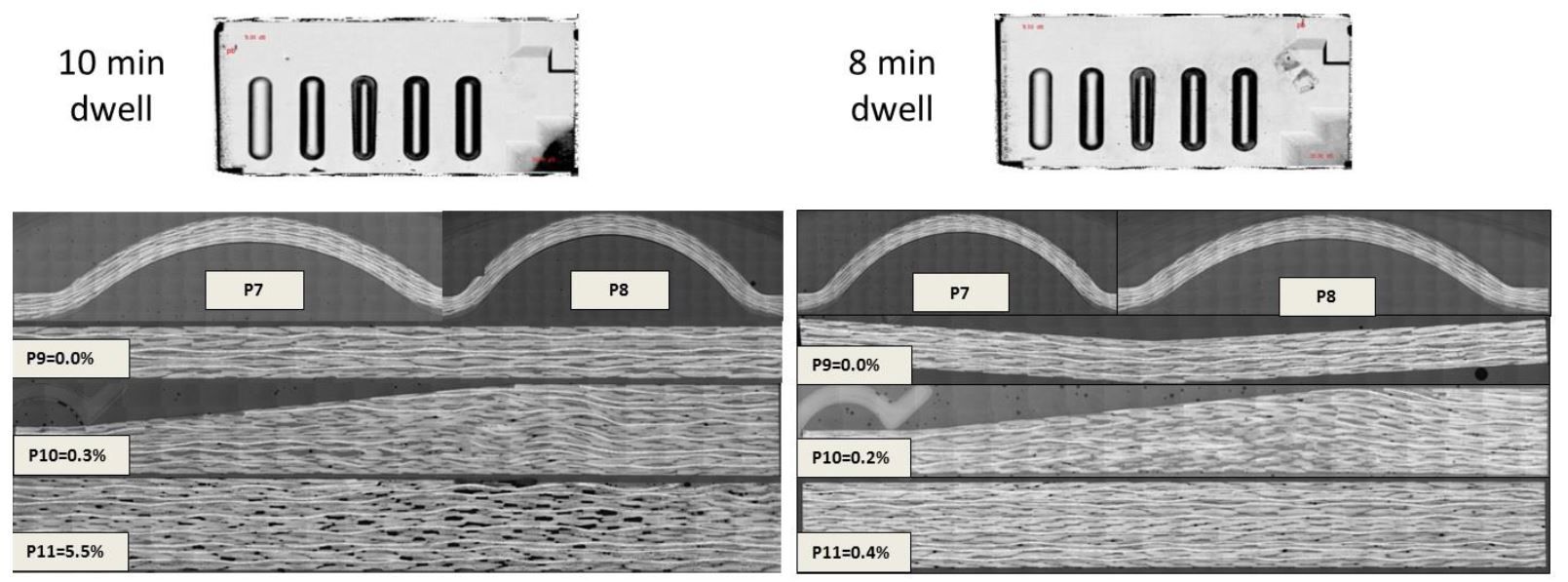
Porosidad con tiempo de permanencia
También se observó un aumento de la porosidad si el tiempo de permanencia era demasiado largo. Los paneles con cuentas hechos con un reposo de 8 minutos tenían un contenido de huecos menor que los hechos con un reposo de 10 minutos. Esto fue particularmente cierto en el área de relleno, donde el contenido de vacíos fue del 5,5% para la pausa de 10 minutos y del 0,4% para la pausa de 8 minutos. El tiempo de permanencia más corto mantiene un alto flujo de resina, humedeciendo las fibras de manera efectiva y manteniendo la presión en la cavidad de la herramienta durante el curado.
La permanencia más prolongada permitió que el flujo de resina y la presión disminuyeran, especialmente en el área de relleno, debido a su proximidad al borde de la cavidad de la herramienta, que no tenía borde cortante ni reducción en la sección. Por tanto, la presión en la cavidad de la herramienta disminuyó en el borde de la pieza, especialmente en regiones más gruesas donde la sección transversal era mayor. La ausencia de presión aquí también exacerbó el riesgo de deslizamiento de las capas acolchadas. "Al diseñar herramientas, una reducción en la sección alrededor de la cavidad de la herramienta ayudará a generar y mantener la presión, particularmente para piezas con diferentes espesores", explica Gail Hahn, investigadora principal y compañera de investigación de Boeing para el proyecto RAPM. "Es necesario presentar algún tipo de pellizco o sellado para fomentar un estado de presión hidrostática en la cavidad".
TS-RAPM-002 nervio
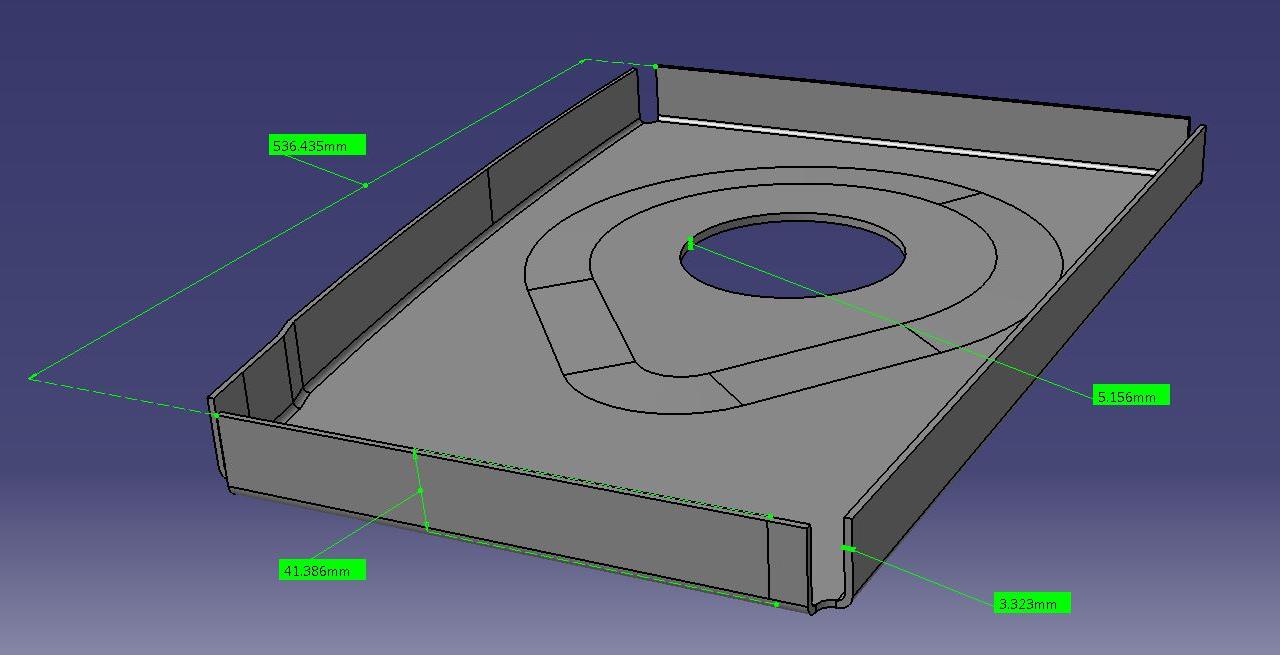
Una vez que se establecieron los parámetros de procesamiento para los paneles con cuentas TS-RAPM-009, se repitió el proceso para la nervadura TS-RAPM-002, que medía 540 milímetros en su borde más largo. La nervadura acumuló un espesor en el centro de 3,3 a 5,2 milímetros y la profundidad del estirado fue de 42 milímetros en la parte final recortada. Los cuatro bordes presentaban bridas verticales. Tenga en cuenta que se determinó un ángulo de compensación de resorte durante las pruebas del panel rebordeado y luego se aplicó a la geometría de la herramienta de la nervadura. Las pruebas de paneles moldeados también llevaron a una mayor capacidad de tensión y modularidad en la ubicación del resorte en el marco del resorte.
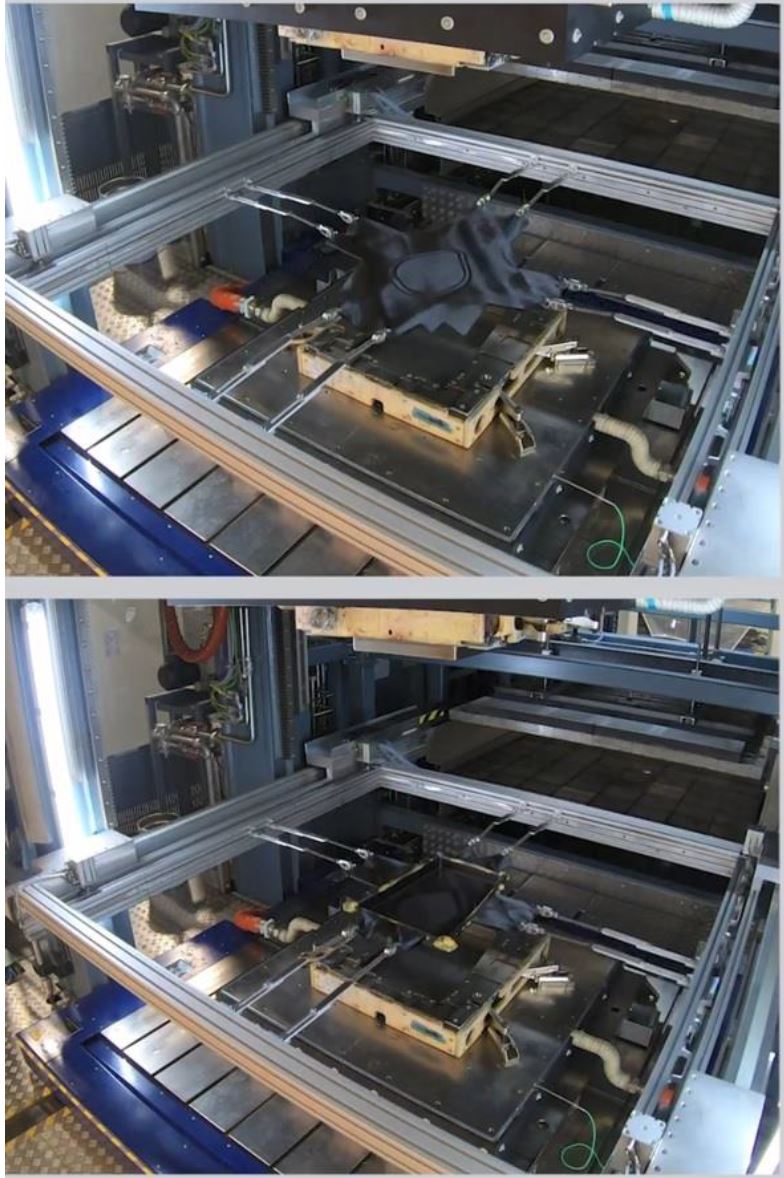
Exceso de material para abrazaderas
Las nervaduras se hicieron utilizando molduras de marco de resorte y DDF. Debido al estiramiento profundo de la nervadura, se requirió un exceso de material para sujetar las abrazaderas del marco de resorte, pero esto podría reducirse cuando se usa DDF. Otro problema fue que el diseño de la herramienta limitaba el espacio para que las abrazaderas de resorte estuvieran cerca de la cavidad de la herramienta.
Variaciones en CPT
El espesor de la capa curada (CPT) fue mayor en las partes planas de la nervadura que en sus bordes verticales. Se razonó que la geometría de la pieza mantenía la resina dentro del área plana central, notando que las bridas verticales actuaban como un sello de resina. Esto ayudó a la compactación y al acabado de la pieza en el área plana central. Sin embargo, las bridas verticales sufrieron un fuerte cizallamiento durante el cierre de la herramienta, lo que provocó la rugosidad de la superficie pero no la porosidad (consulte los datos de porosidad a continuación). CYCOM EP2750, un material de menor volumen, ayudó a mitigar este efecto:su menor espesor disminuyó el cizallamiento.
Variaciones en el grosor de la banda con contenido de resina preimpregnada
Las investigaciones de calidad mostraron nervaduras repetibles con porosidad <0,1% y arrugas / ondulaciones mínimas de la fibra. Sin embargo, si bien se asumió que la variación del espesor de la pieza se minimizaría con el procesamiento de moldes emparejados, la revisión de los parámetros de procesamiento del material y el CPT de la pieza terminada mostró que, si bien el espacio de la herramienta en las bridas verticales de la nervadura era fijo y consistente, el espesor de la red podría variar como una función. del contenido de resina preimpregnada (menos de +/- 2%) y el proceso:el CPT podría variar entre las bridas y la red, ya que se permitió que la resina migrara dentro de la cavidad.
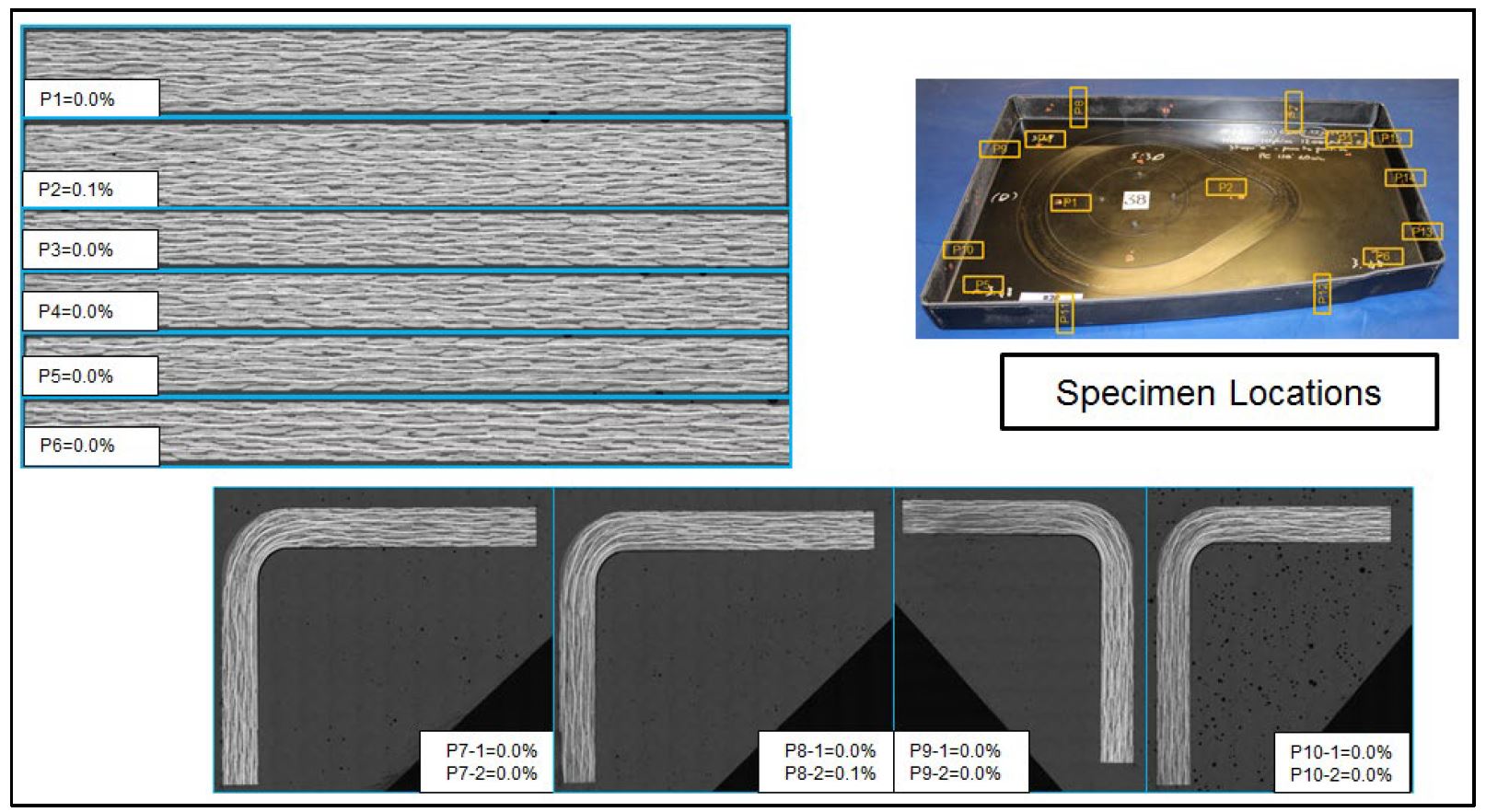
TS-RAPM-003 canal C curvo
Esta pieza tenía 640 milímetros de largo con una sección en U de 40 milímetros de profundidad en la pieza final recortada. El radio interior de la sección era mayor que el radio exterior, y el grosor aumentó de 6,6 milímetros en la sección estrecha a 8,8 milímetros en el extremo ancho. Debido a su grosor, la parte del canal C era sustancialmente más pesada que las partes anteriores discutidas. Por lo tanto, el marco de resorte requería más puntos de sujeción que con las piezas anteriores.
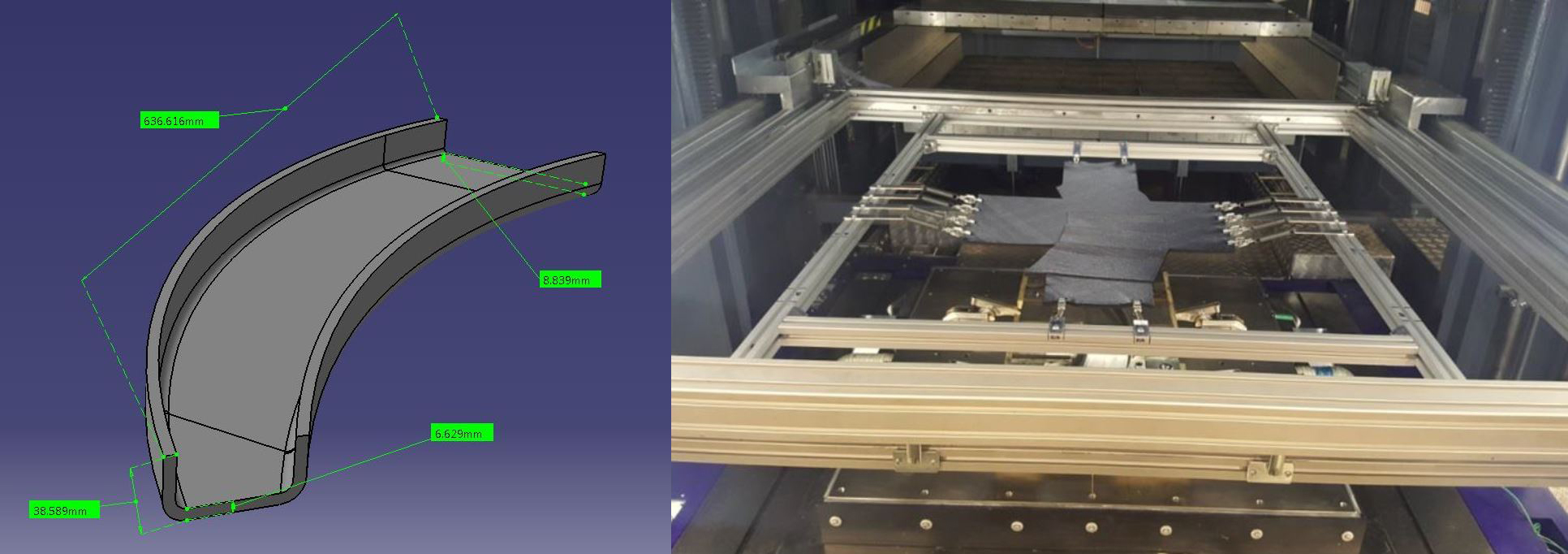
Doble permanencia para mantener la presión en partes gruesas
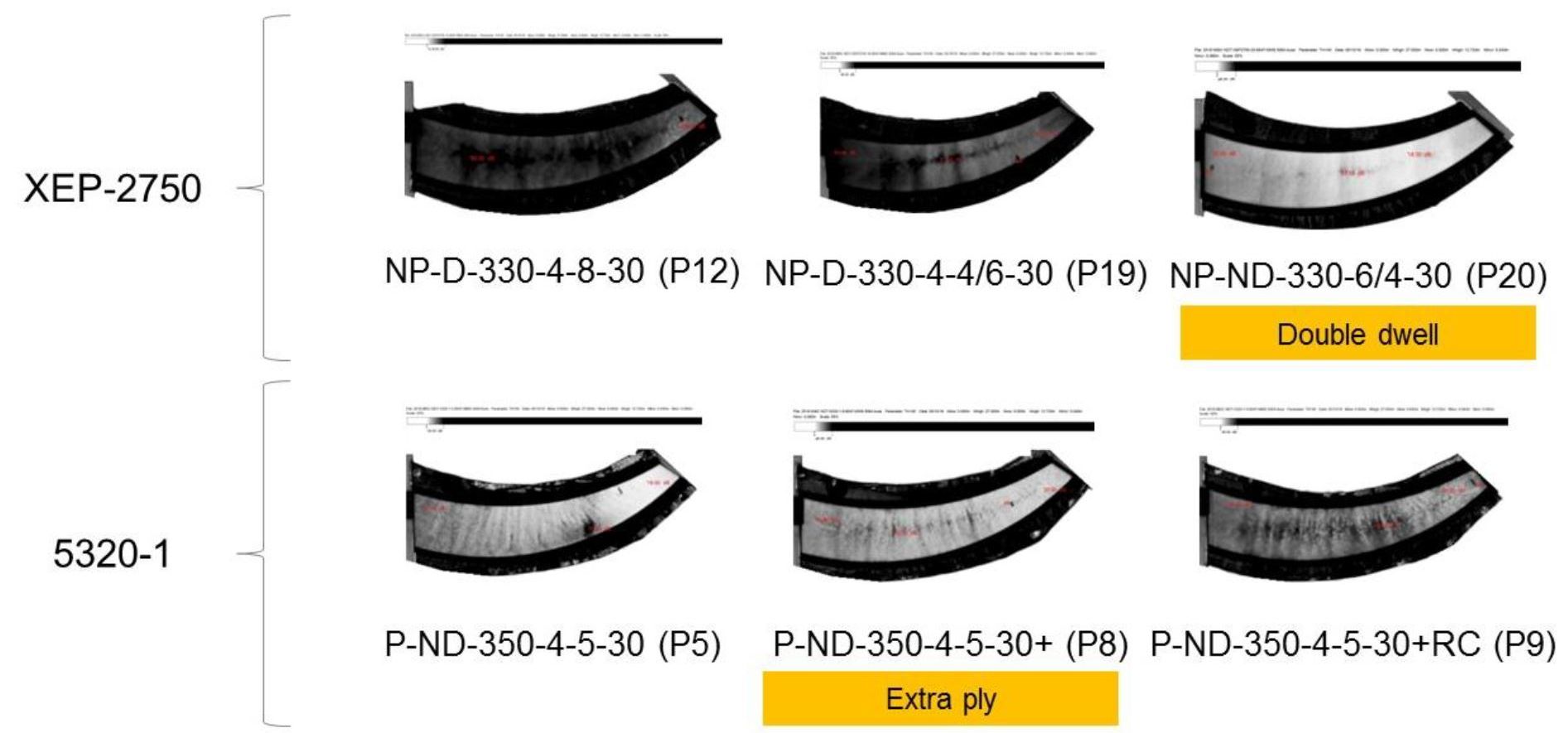
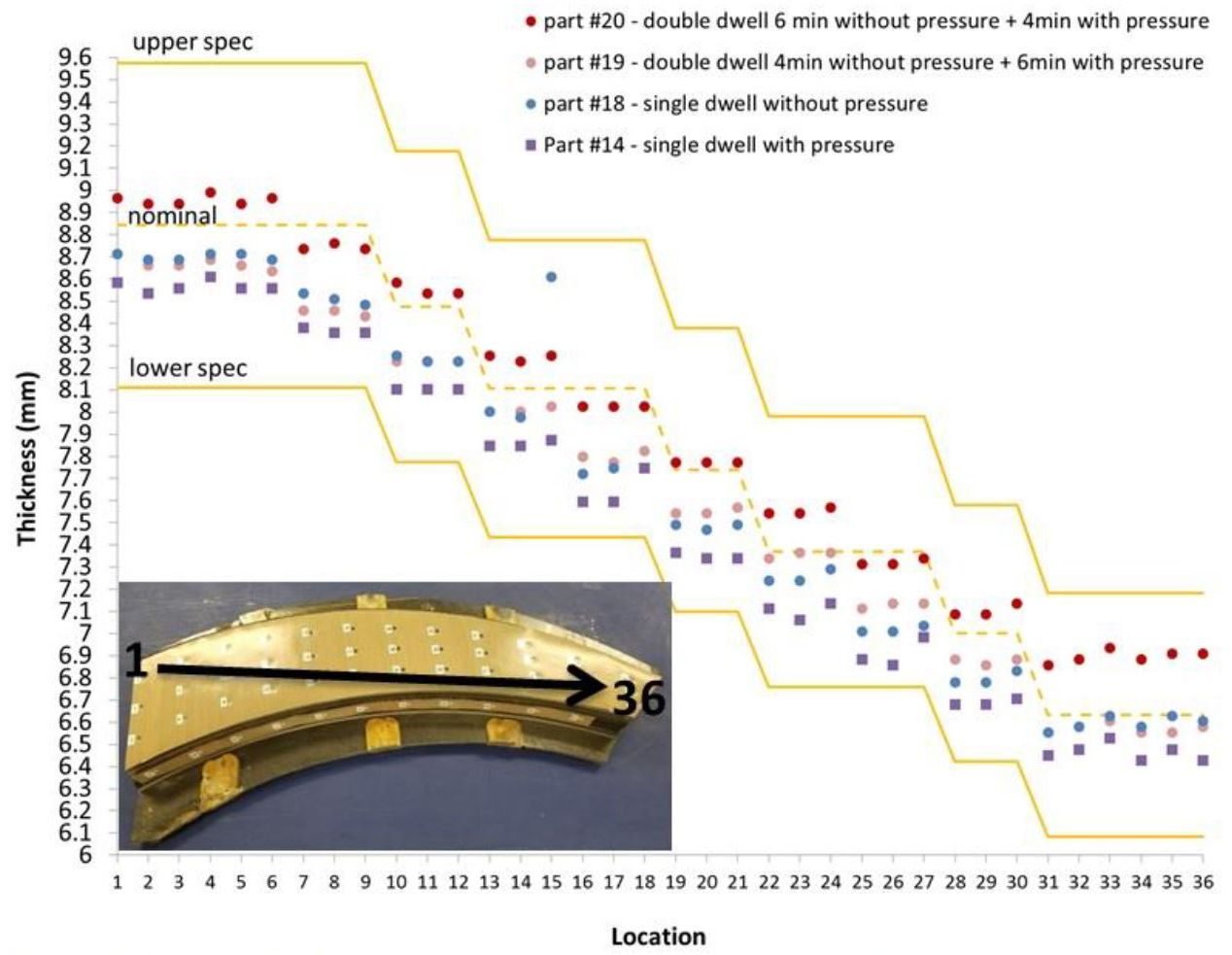
Los escaneos en C de piezas moldeadas resaltan una arruga que se propaga desde el radio interior al radio exterior para piezas que utilizan espacios en blanco preconsolidados. La escala de grises indica que las arrugas también tienen porosidad.
Estas arrugas y la porosidad se eliminaron para las piezas preimpregnadas CYCOM EP2750 mediante el uso de una "doble permanencia" proceso. Consiste en aplicar una cierta cantidad de presión durante la permanencia inmediatamente después de la acumulación de viscosidad del material. “Esto se determinó utilizando los datos proporcionados por la prensa y las herramientas durante el desarrollo del proceso”, explica Hahn. “Básicamente, hay dos pasos de acumulación progresiva de presión antes de la aplicación de presión total. Como resultado, el perfil de presión en función del tiempo tiene una forma similar al perfil de viscosidad de la resina. Se utiliza una permanencia inicial en el espesor aparente para aumentar la viscosidad de la resina y evitar que la carga de material [en bruto o preforma] se adelgace. Si la carga es de un espesor significativo, se utilizan dos tiempos de espera para evitar la pérdida de presión debido a la contracción de la resina. La primera permanencia está en un espacio de X, y el segundo en un espacio de Y, con Y
La Fig. 18 anterior muestra el efecto de la doble permanencia en el espesor de la pieza del canal C. Hacer coincidir la presión con la viscosidad de la resina permitió retener más resina dentro de la pieza, lo que humedeció las fibras para lograr una baja porosidad y un espesor de construcción para alcanzar la distorsión de fibra nominal requerida pero mantenida. Sin embargo, el equipo de RAPM enfatizó que este proceso de doble permanencia se favorece solo para partes más gruesas, y señaló que puede inducir irregularidades de CPT en partes de diferentes espesores.
Las pruebas de piezas RAPM que se analizan aquí han contribuido al conocimiento hacia la fabricación de piezas estructurales aeroespaciales de alta velocidad utilizando moldeo por compresión preimpregnado. Las lecciones aprendidas incluyen:
RAPM ha demostrado que el moldeo por compresión preimpregnado puede producir estructuras de grado aeroespacial de alta calidad al tiempo que reduce el tiempo de ciclo y la mano de obra. Esto permite que los compuestos compitan mejor en estudios comerciales para aplicaciones aeroespaciales al tiempo que ofrecen un mayor ahorro de peso y rendimiento de los componentes (por ejemplo, resistencia a la corrosión, agrietamiento y fatiga, etc.).
Solvay y Boeing han trabajado juntos para perfeccionar el novedoso sistema preimpregnado EP2750, demostrando tiempos de takt hasta 20 minutos, gracias a una combinación de química de materiales, preimpregnado y conocimiento y automatización de procesos.
Además de las piezas de desarrollo de fabricación mencionadas anteriormente, RAPM también ha producido varias piezas de desafío y transición, destinadas a desafiar desarrollos iniciales y transición candidatos con potencial para ganar frente al aluminio mecanizado en aplicaciones de defensa. Estos incluyen:
Los resultados y las lecciones aprendidas de estas pruebas de piezas y otros estudios de características de fabricación de RAPM se publicarán en 2020/2021.
Solvay también ha ilustrado cómo se desempeña EP2750 en piezas de automóviles, como un pilar B de 36 por 16 por 2 pulgadas con un grosor de 0,0725 pulgadas, que comprende 5 capas de fibra de carbono de remolque Solvay THORNEL T650-35 de módulo estándar 3K en un 376 gramos / metro cuadrado tejido satinado de 8 arneses. Esta pieza se hizo en Solvay Heanor, Reino Unido, utilizando DDF. En comparación con el preimpregnado estándar esterilizado en autoclave, la combinación de CYCOM EP2750 y DDF ofrece una reducción del 60% en el tiempo de ciclo y del 85% en el tiempo de takt (tiempo entre el inicio de una pieza y la siguiente en una línea de producción, es decir, el tiempo de pulso de la línea) .
Lecciones aprendidas de RAPM y más pruebas de piezas
Pruebas de piezas de automóvil de Solvay
Resina
- Moldeo por compresión vs moldeo por inyección:¿Cuál es la diferencia?
- Moldeo por compresión:cómo funciona
- Moldeo por compresión y moldeo por fundición:pros y contras
- Agente de purga altamente eficiente para poliolefinas de moldeo por soplado
- PEEK de alta viscosidad para moldeo por inyección y extrusión
- Transportador personalizado para moldeo de preformas
- Tercera patente emitida para preimpregnados termoplásticos flexibles
- Solvay lanza preimpregnado epoxi para moldeo por compresión de aeroestructuras
- Compression RTM para la producción de futuras aeroestructuras
- Preimpregnado aeroespacial Toray optimizado para moldeo a presión asistido por vacío
- Cintas continuas, D-LFT se encuentran en un nuevo proceso de moldeo por compresión