Cómo implementar un plan de mantenimiento productivo total (TPM)
La implementación exitosa y sostenible del Mantenimiento Productivo Total (también conocido como TPM) debe ser una preocupación clave para cualquier gerente de planta o líder de producción consciente. TPM conduce a un tiempo de inactividad reducido, menos paradas y averías, y una menor probabilidad de que los productos sufran defectos de calidad durante el proceso de fabricación.
¿Por qué TPM es una herramienta tan efectiva? En resumen, porque los operadores capacitados que asumen un papel activo en la inspección y el mantenimiento de sus propios equipos siempre contribuirán a mejorar la producción y la confiabilidad de los equipos.
A lo largo de los años, los estudios han confirmado la correlación positiva entre la implementación de un programa TPM y el rendimiento general de la fabricación. Algunos hallazgos indican que una empresa puede reducir la pérdida de producción en aproximadamente un 20% mediante la ejecución de un plan de mantenimiento productivo total. Aún así, surge una pregunta importante:¿Cómo puede una empresa implementar TPM de manera eficaz? ? La siguiente información responderá a esa pregunta.
¿Interesado en ahorrar dinero en costos de mantenimiento?
Puede acceder a más recursos útiles y trabajos de investigación aquí.
Qué es el Mantenimiento Productivo Total
A modo de revisión, cualquier programa TPM involucra al menos 8 conceptos básicos que juegan un papel importante en la determinación del éxito final de la iniciativa. Estos 8 conceptos son:
-
Mantenimiento autónomo
Este elemento fundamental de TPM se centra en capacitar y capacitar al personal de mantenimiento, como los operadores de máquinas, para realizar la gestión de mantenimiento de rutina por su cuenta. -
Mejora enfocada
Este pilar de TPM se refiere a las técnicas de mantenimiento proactivo:examinar un proceso actual de manera holística e identificar formas de mejorarlo. -
Mantenimiento planificado
Un programa de mantenimiento planificado aprovecha los datos históricos de tiempo de inactividad y el análisis predictivo para programar las tareas de mantenimiento clave en función de las tasas de falla probables o los tiempos de inactividad anticipados. -
Mantenimiento de calidad
El proceso de mantenimiento de calidad está diseñado para garantizar que las tareas de mantenimiento reales que se realizan cumplan de manera eficiente los objetivos generales de detección de errores, prevención de defectos y garantía de calidad. -
Administración temprana de equipos
Aprovechando los comentarios de los operadores con experiencia práctica, la gestión temprana de equipos garantiza que el diseño de nuevos equipos optimizará la vida útil, la accesibilidad y la productividad de la maquinaria. -
Entrenamiento
Cada programa de TPM debe incluir un elemento de capacitación y educación tanto para los operadores como para los gerentes. -
Seguridad y salud
Todos los procesos de TPM deben tener en cuenta los factores de seguridad y salud para fomentar un entorno de trabajo seguro para los operadores y otros empleados. -
Administración orientada a TPM
Aparte de las consideraciones puramente mecánicas, un programa TPM bien diseñado también tendrá en cuenta las funciones administrativas, como el procesamiento de pedidos y la gestión de programaciones, y buscará formas de mejorarlas para respaldar la planta de producción.
Cómo implementar TPM
Si bien un programa TPM debe adaptarse a las necesidades y circunstancias específicas de la empresa, existen 7 pasos básicos para implementar TPM, como se indica a continuación:
1. Anunciar planes para la implementación de TPM
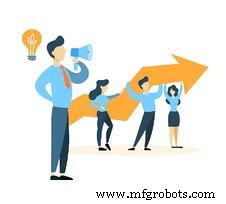
2. Identificar un área para un programa piloto de TPM
Podría concentrarse en una pieza de equipo que sería más fácil de mejorar, o en un área de producción que ha demostrado ser problemática y necesita ser reparada para mejorar rápidamente la rentabilidad. En esta etapa inicial del proceso TPM, identifique metas que sean SMART:específicas, medibles, alcanzables, realistas y programadas.3. Concéntrese en restaurar el equipo objetivo a las mejores condiciones de trabajo
Una vez que haya identificado su área piloto, registre un estándar de referencia para la productividad actual. Organice y defina su plan para la implementación de TPM . Utilice la metodología 5S (Ordenar, Establecer, Brillar, Estandarizar, Sostener). Concéntrese primero en ejecutar un programa de mantenimiento autónomo y brinde capacitación a los operadores de equipos según sea necesario. Así como el propietario de un automóvil puede ahorrar una cantidad significativa en los costos de reparación al realizar el mantenimiento de rutina básico, las empresas también pueden extender la vida útil de la máquina e identificar problemas mecánicos desde el principio al permitir que sus operadores participen regularmente en los procedimientos básicos de mantenimiento.4. Comience a medir la eficacia general del equipo (OEE)
Independientemente de cómo decida realizar un seguimiento de OEE, es imperativo que se documenten los tiempos de parada no planificados y que se proporcione una razón para cada ocurrencia. Proporcione una categoría para "causa desconocida" o "tiempo de parada no asignado" para los casos en los que el operador no esté seguro de la causa de la parada. Con el tiempo, esto le ayudará a identificar primero principales causas de pérdida, lo que a su vez conduce al paso n.º 5: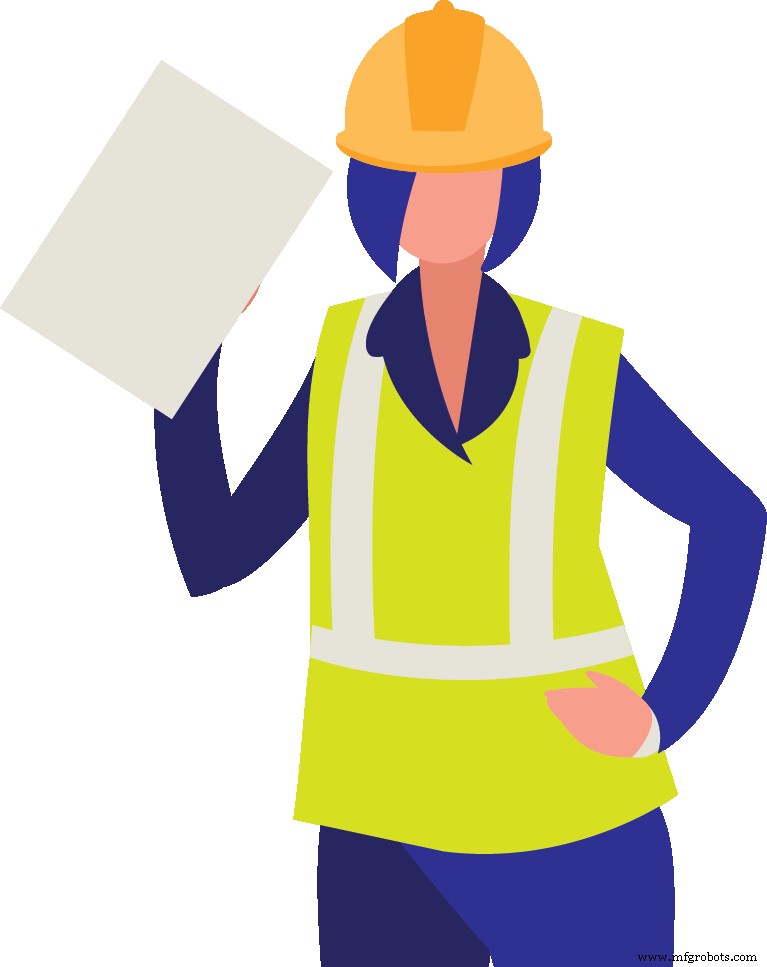
5. Abordar las principales causas de pérdidas
En este paso, deberá designar un equipo multifuncional de aproximadamente 4 a 6 empleados para investigar una de las principales causas del tiempo de inactividad. . Este equipo creará un plan para eliminar la causa de la pérdida y programará un tiempo de parada planificado para ejecutar esta iniciativa. Por ejemplo, si sus principales pérdidas provienen de frecuentes atascos de llenado, entonces este equipo examinará los procesos actuales del operador y las opciones de reparación, creará un plan para detener los atascos y luego programará el tiempo para poner el plan en acción. Una vez que se haya completado la acción designada, medirán el OEE en el futuro y reiniciarán el proceso si es necesario.
6. Implementar un mantenimiento proactivo
En este paso, su atención se centra en la prevención de averías o tiempos de parada. Identifique los principales "puntos débiles" que podrían causar fallas en los equipos y cree un programa de mantenimiento preventivo a intervalos regulares. Finalmente, instituya un proceso de retroalimentación que le permita monitorear continuamente la efectividad de su programa. Este sistema de retroalimentación podría incluir registros de mantenimiento, auditorías mensuales o bimensuales y recopilación de datos de termografía y/o análisis de vibraciones.
7. Implemente conceptos específicos de TPM según sea necesario
Por ejemplo, la gestión temprana de equipos debería entrar en juego al diseñar y/o instalar nuevas máquinas para la planta de producción. Tal vez el diseño de los nuevos equipos deba optimizarse para incluir una mejor accesibilidad, procedimientos de limpieza o lubricación más fáciles, o la adición de características de seguridad. Por otro lado, si hay problemas de adquisición o demoras en el procesamiento de las órdenes de trabajo, debe abordar estos cuellos de botella administrativos lo antes posible.Aprovechamiento de TPM para mejorar la gestión del mantenimiento
El mantenimiento productivo total es un elemento clave para reducir las pérdidas de producción por tiempo de inactividad. Un programa TPM efectivo puede empoderar a los empleados para que tomen medidas proactivas en el mantenimiento de maquinaria vital; esto, a su vez, permitirá que los equipos de producción disfruten de una vida útil funcional más larga. La implementación de TPM también ayudará a reducir los defectos de calidad y los tiempos de ejecución subóptimos.
Hay muchas herramientas disponibles en el mercado, como plataformas de gestión de activos empresariales y programas relacionados, que pueden ayudar a las empresas en la implementación de TPM. En el análisis final, mientras que un plan de mantenimiento productivo total requiere un poco de esfuerzo para un diseño y una ejecución adecuados, ¡las recompensas de hacerlo bien valen la inversión!
Mantenimiento y reparación de equipos
- Poniendo su plan TPM en acción:una guía paso a paso
- Cómo mantener el mantenimiento en modo proactivo
- Cómo implementar el mantenimiento productivo total
- Vodcast:Introducción al mantenimiento productivo total
- Cómo crear un programa de mantenimiento eléctrico
- Unilever expande el programa de Mantenimiento Productivo Total con la ayuda de Informance
- Cómo los gerentes de planta pueden planificar el mantenimiento regular de la máquina
- Mantenimiento Productivo Total e IoT Industrial
- Cómo implementar el mantenimiento centrado en la confiabilidad (RCM)
- Mantenimiento Productivo Total:¿una palanca de desempeño?
- Comprender el mantenimiento productivo total (TPM)