Solución de problemas de mantenimiento:más que prueba y error
Una guía completa para la resolución de problemas para el mantenimiento y consejos para mejorar sus habilidades de resolución de problemas para mejorar toda su operación.
Tabla de contenido
- ¿Qué es la resolución de problemas?
- Consejos para solucionar problemas de mantenimiento
- Uso de software de mantenimiento para solucionar problemas
- El resultado final
La resolución de problemas de mantenimiento puede ser tanto un arte como una ciencia. El problema es que, si bien el arte puede ser hermoso, no es conocido por su eficiencia. Cuando se lleva al siguiente nivel, la resolución de problemas puede deshacerse del apodo de prueba y error y convertirse en un esfuerzo puramente científico. Esto ayuda a los técnicos a encontrar los problemas y las soluciones correctos más rápidamente. Cuando la resolución de problemas se realiza correctamente, toda su operación de mantenimiento puede superar el retraso, la pérdida de producción y los problemas de cumplimiento de manera mucho más eficiente.
Veamos qué es realmente la solución de problemas, por qué es importante para los profesionales de mantenimiento y cómo su equipo puede ajustar su enfoque.
¿Qué es la resolución de problemas?
Los sistemas se rompen, eso es solo un hecho de la vida. Ya sea que se trate de una cinta transportadora o un taladro industrial, todos nos hemos topado con un equipo que no responde, está defectuoso o funciona de manera anormal sin ninguna razón aparente. Puede ser francamente frustrante.
La resolución de problemas es el proceso de identificar qué está mal con estos sistemas defectuosos cuando el problema no es inmediatamente obvio. La resolución de problemas suele seguir un enfoque sistemático de cuatro pasos; identificar el problema, planificar una respuesta, probar la solución y resolver el problema. Los pasos uno a tres a menudo se repiten varias veces antes de alcanzar una resolución.
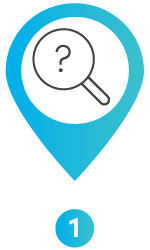
Identifique el problema
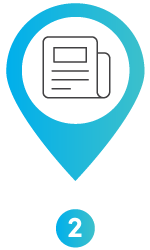
Planifique una respuesta

Pruebe la solución
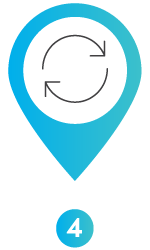
Repita hasta que se resuelva el problema
Piénselo de esta manera:cuando una cinta transportadora se rompe, puede probar algunos métodos diferentes para arreglarla. Primero, identifica qué parte de la cinta transportadora no está funcionando. Una vez que haya identificado el área del problema, planifique una respuesta y la pruebe, como realinear o lubricar una pieza. Si esto no soluciona el problema, puede reemplazar la pieza, lo que hace que la cinta transportadora vuelva a funcionar. Esta es la solución de problemas.
¿Cómo se suele solucionar los problemas de mantenimiento?
Deténganos si ha escuchado esta historia antes. Un activo se descompone y nadie sabe por qué. Hablas con el operador, lees algunos manuales y revisas tus notas sobre el activo. Intentas un par de cosas para que la máquina vuelva a funcionar sin suerte. Antes de que pueda probar una tercera o cuarta solución posible, lo llamarán para otra emergencia, con el activo aún fuera de servicio.
A menudo, así es como ocurre el proceso al solucionar problemas de mantenimiento, especialmente cuando una instalación se basa en registros en papel u hojas de cálculo de Excel. El proceso se basa en recopilar tanta información como sea posible de tantas fuentes como sea posible para identificar la causa más probable de la avería. Nunca puede equivocarse cuando recopila información, pero es la forma en que se recopila la información lo que puede convertir la resolución de problemas de una necesidad en una pesadilla.
¿Por qué es importante la resolución de problemas en el mantenimiento?
La falla inesperada del equipo es la única razón por la que existe la solución de problemas. Si los activos nunca se descomponen sin signos claros de falla inminente, no habría necesidad de solucionar el problema. Pero sabemos que ese no es el caso.
La falla de los activos no siempre sigue un patrón predecible. Sí, los equipos de mantenimiento pueden utilizar el mantenimiento preventivo y el mantenimiento basado en condiciones para reducir la probabilidad de tiempos de inactividad no planificados. Sin embargo, nunca podrá eliminarlo por completo. Lo que puede hacer es implementar procesos para reducir las fallas tanto como sea posible y solucionarlas lo antes posible cuando ocurran. Aquí es donde resultan útiles las sólidas técnicas de resolución de problemas.
Debido a que la resolución de problemas siempre será parte de la ecuación de mantenimiento, los humanos también siempre tendrán un papel. La tecnología de mantenimiento no elimina la necesidad de un toque humano en la resolución de problemas; simplemente hace que el proceso sea mucho más eficiente. Cuando la solución de problemas no se refina, podría provocar una pérdida de tiempo en el rastreo de información, una pérdida sustancial de producción, un entorno de trabajo inseguro y fallas más frecuentes. En resumen, conocer algunas de las mejores prácticas para la resolución de problemas podría marcar la diferencia entre una acumulación abrumadora y un programa de mantenimiento estable.
Sugerencias para la resolución de problemas de mantenimiento
Las siguientes son solo algunas de las formas en que su operación puede mejorar sus capacidades de resolución de problemas para conquistar el caos y tomar el control de su mantenimiento.
Cuantifique el rendimiento de los activos y comprenda cómo utilizar los resultados
Probablemente no hace falta decirlo, pero cuanto más profundamente conozca un activo, mejor equipado estará para diagnosticar un problema. Años de trabajo con un determinado activo pueden ayudarlo a reconocer cuándo no está funcionando del todo bien. Pero la solución de problemas excepcional no se trata solo de conocer los sonidos, velocidades u olores normales de una máquina en particular. En cambio, se trata de saber cómo analizar el rendimiento de los activos a un nivel más profundo, que es donde influyen los informes avanzados.
Obtenga las mejores prácticas para el seguimiento y el uso de datos de activos
Leer más
Cuando los operadores y técnicos confían únicamente en su propia experiencia pasada con un equipo, se quedan con grandes lagunas de conocimiento que perjudican el proceso de resolución de problemas. Por ejemplo, deja demasiado espacio para que el sesgo de actualidad afecte la toma de decisiones, lo que significa que es más probable que los técnicos intenten lo último que solucionó un problema en particular sin considerar otras opciones o profundizar en la causa raíz. Además, si la resolución de problemas se basa en el conocimiento exclusivo de algunos técnicos, significa que las reparaciones tendrán que esperar hasta que ese personal en particular esté disponible.
El personal de mantenimiento debe tener los conocimientos necesarios para realizar un análisis en profundidad del rendimiento de un activo. Por ejemplo, los técnicos deben comprender cómo ejecutar informes y comprender los KPI para equipos críticos, como el tiempo medio entre fallas y la efectividad general del equipo. Si usa mantenimiento basado en condiciones, el equipo de mantenimiento también debe conocer la curva P-F para cada activo y lo que significan las diferentes lecturas de los sensores. Cuando los técnicos están equipados con un conocimiento más profundo de un activo, será más fácil para ellos identificar dónde ocurrió un problema y cómo solucionarlo, tanto a corto como a largo plazo.
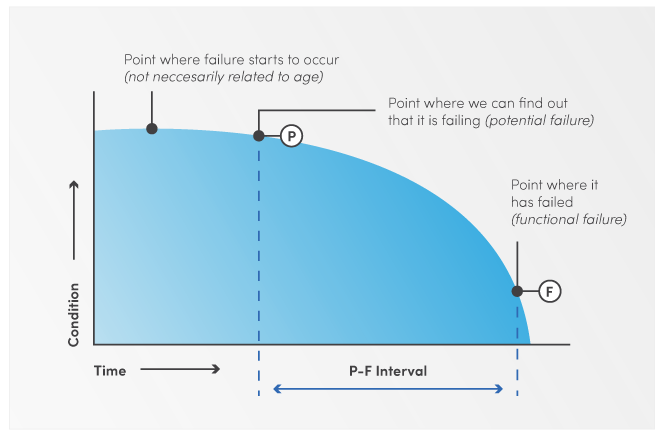
Cree historiales de activos detallados
La información es el combustible que impulsa la solución de problemas excepcional para el mantenimiento. Saber cómo ha funcionado y fallado un activo en particular para cientos de otros es un buen lugar para comenzar una reparación. Es por eso que los manuales son una herramienta útil para solucionar problemas. Sin embargo, cada activo, instalación y operación es diferente, lo que significa que la falla del activo no siempre sigue el guión. Las notas detalladas sobre el historial de un activo pueden abrir un callejón sin salida y llevarlo a una solución mucho más rápidamente.
Un historial de activos detallado puede brindarle una ventaja en la resolución de problemas de varias maneras. Ofrece un método simple para hacer referencias cruzadas de síntomas del problema actual con elementos de problemas pasados. Por ejemplo, un técnico puede ver si un determinado tipo de material estaba siendo manipulado por una máquina o si se identificaron señales de advertencia tempranas de una falla anterior. Cuanto más se alinea una situación presente con un escenario pasado, es más probable que necesite la misma solución. Las soluciones se pueden priorizar de esta manera, lo que genera menos errores, menos tiempo de inactividad, menos piezas de repuesto innecesarias y más.
Cuando la resolución de problemas se realiza correctamente, toda su operación de mantenimiento puede superar el retraso, la pérdida de producción y los problemas de cumplimiento de manera mucho más eficiente.
Al crear historiales de activos detallados para ayudar con la resolución de problemas (así como el mantenimiento preventivo), es importante incluir tanta información como sea posible. Asegúrese de registrar la hora y las fechas de cualquier acción notable realizada en un activo o pieza de equipo. Esto puede incluir averías, mantenimiento preventivo, inspecciones, reemplazo de piezas, programas de producción y comportamiento anormal, como humo o sonidos inusuales. A continuación, documente los pasos tomados durante el mantenimiento, incluidos los MP o las reparaciones. Por último, resalte la solución exitosa y lo que se necesitaba para lograrla, como las piezas necesarias, la mano de obra y el equipo de seguridad. Asegúrese de agregar también las métricas e informes relevantes al historial de activos.
Una forma de capturar toda esta información en un solo lugar es crear un registro de mantenimiento de equipos bien construido, como este:
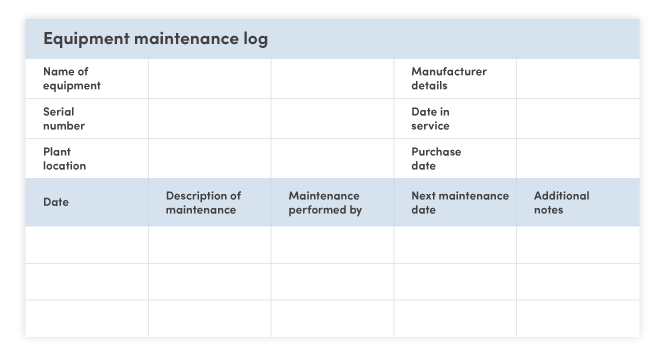
Descargue su propia plantilla de registro de mantenimiento de equipos aquí
Utilice análisis de causa raíz y códigos de falla
La resolución de problemas eficaz para el mantenimiento comienza con la eliminación de la ambigüedad y las soluciones a corto plazo. Encontrar la raíz de un problema rápidamente, resolverlo de manera eficaz y asegurarse de que permanezca resuelto es una fórmula ganadora. El análisis de la causa raíz y los códigos de falla son un par de herramientas que lo ayudarán a lograr este objetivo.
El análisis de la causa raíz es una técnica que le permite identificar la razón detrás de una falla. El método consiste en preguntar "por qué" hasta llegar al meollo del problema. Por ejemplo:
- ¿Por qué falló el equipo ?:Porque se desgastó un cojinete
- ¿Por qué se desgasta el rodamiento ?:Porque un acoplamiento estaba desalineado
- ¿Por qué se desalineó el acoplamiento ?:Porque no se le dio servicio recientemente.
- ¿Por qué no se le dio servicio al acoplamiento ?:Porque no se programó el mantenimiento.
- ¿Por qué no se programó el mantenimiento ?:Porque no estábamos seguros de la frecuencia con la que debería programarse.
Clave su próximo análisis de causa raíz con esta plantilla de RCA
Este proceso tiene dos ventajas a la hora de solucionar problemas de mantenimiento. Primero, le permite identificar la causa inmediata de la falla y solucionarla rápidamente. En segundo lugar, lo lleva al núcleo del problema y a una solución a largo plazo. En el ejemplo anterior, está claro que se requiere un mejor programa de mantenimiento preventivo para mejorar la gestión de activos y reducir el tiempo de inactividad no planificado.
Los códigos de falla proporcionan un método consistente para describir por qué falló un activo. Los códigos de falla se basan en tres acciones:enumerar todos los problemas posibles, todas las causas posibles y todas las soluciones posibles. Este proceso registra los aspectos clave de una falla de acuerdo con categorías predefinidas, como desalineación o corrosión.
Los códigos de falla son útiles para solucionar problemas de mantenimiento porque los técnicos pueden ver de inmediato los códigos de falla comunes, determinar la mejor solución e implementarla rápidamente. Los códigos de falla también se pueden usar para descubrir un problema común entre un grupo de activos y determinar una solución a largo plazo.
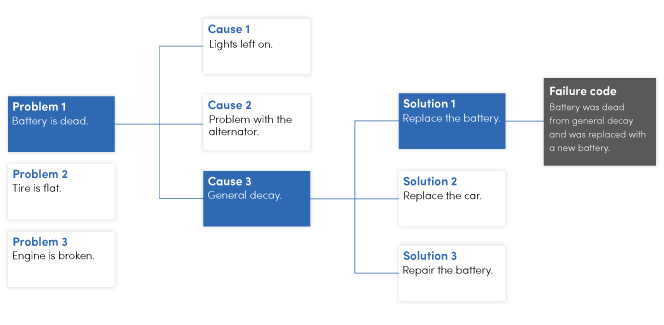
Cree asombrosos códigos de falla con esta plantilla FMEA gratuita
Cree listas de tareas detalladas
La solución de problemas excepcional requiere una planificación y una previsión sólidas. Los procesos claros proporcionan un plan para los técnicos para que puedan identificar rápidamente los problemas e implementar soluciones más efectivas. Crear listas de tareas detalladas es una forma de reforzar su planificación y evitar dolores de cabeza en el futuro.
Una lista de tareas describe una serie de tareas que deben completarse para terminar un trabajo más grande. Garantizan que no se pierdan los pasos cruciales al realizar inspecciones, auditorías o PM. Por ejemplo, el trabajo más importante puede ser realizar una inspección de rutina de los desfibriladores de su instalación. Este trabajo se divide en una lista de tareas más pequeñas, como "Verificar la instalación de la batería" e "Inspeccionar los componentes exteriores en busca de grietas".
La tecnología de mantenimiento no elimina la necesidad de un toque humano en la resolución de problemas; simplemente hace que el proceso sea mucho más eficiente.
Las listas de tareas detalladas son extremadamente importantes a la hora de solucionar problemas de mantenimiento. Actúan como una guía cuando se prueban posibles soluciones para que los técnicos puedan solucionar el problema o descalificar un diagnóstico lo más rápido posible. Cuanto más explícita sea la lista de tareas, más completo será el trabajo y menos probable será que un técnico cometa un error. Las listas de tareas completas también pueden ofrecer datos valiosos cuando ocurre una falla. Proporcionan información sobre el tipo de trabajo realizado recientemente en un activo para que pueda determinar si se omitió alguna acción y si esta fue la fuente del problema.
Existen algunas prácticas recomendadas para crear listas de tareas detalladas. Primero, incluya todas las acciones individuales que componen una tarea. Por ejemplo, en lugar de indicarle a alguien que "Inspeccione el ventilador de enfriamiento", incluya los pasos que comprenden esa inspección, como "Verifique si hay grietas visibles" e "Inspeccione si hay piezas sueltas". Organice todos los pasos en el orden en que deben realizarse. Por último, incluya cualquier información adicional que pueda ser útil para completar las tareas, incluidos los suministros, los recursos (es decir, manuales) y el PPE necesarios.
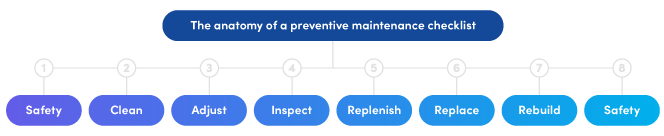
Cree listas de verificación de PM de clase mundial con esta plantilla gratuita
Hacer accesible información adicional
Lo hemos dicho antes y lo diremos de nuevo; una gran resolución de problemas es a menudo el resultado de una gran información. Sin embargo, si es difícil acceder a esa información, perderá cualquier ventaja que proporcione. Por eso es crucial para su operación no solo crear un gran centro de recursos, sino también hacerlo altamente accesible. Esto elevará sus capacidades de resolución de problemas y hará que sus activos vuelvan a estar en línea más rápido cuando ocurra un tiempo de inactividad no planificado.
Comencemos con los elementos de un gran centro de información. Hemos hablado sobre la importancia de los informes, los historiales de activos, los códigos de fallas y las listas de tareas al solucionar problemas de mantenimiento. Algunos otros recursos clave incluyen diagramas, procedimientos operativos estándar (POE), videos de capacitación y manuales. Todos estos deben incluirse y organizarse por activo. Si un técnico llega a un callejón sin salida al solucionar un problema, estas herramientas pueden ofrecer una solución que puede haberse pasado por alto en el análisis inicial.
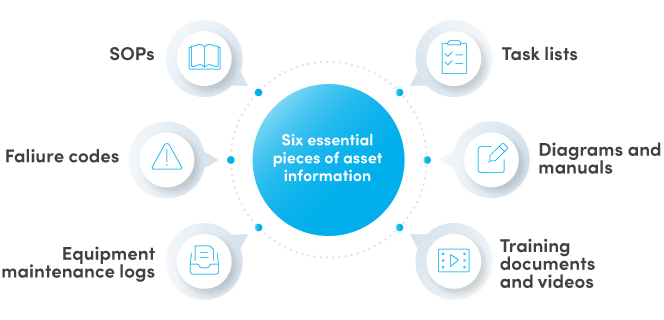
Ahora que ha reunido todos sus documentos, es hora de que todo el equipo de mantenimiento pueda acceder a ellos fácilmente. Si los recursos están atrapados en un archivador, en una hoja de cálculo o en la mente de una sola persona, no le hacen mucho bien al técnico. Pueden perderse, extraviarse y ser difíciles de encontrar, sin mencionar la ineficiencia que implica la necesidad de caminar desde un activo hasta la oficina solo para tomar un manual. Una forma de sortear este obstáculo es crear un centro de conocimiento digital con software de mantenimiento. Al hacer que todos sus recursos estén disponibles a través de un dispositivo móvil, los técnicos pueden acceder a cualquier herramienta que necesiten para solucionar un problema. En lugar de examinar archivos en papel para encontrar un historial o diagrama de activos, pueden acceder a esa misma información en cualquier lugar y en cualquier momento.
Todo lo que necesita saber sobre las métricas de mantenimiento
Leer más
Uso de software de mantenimiento para solucionar problemas
Si parece mucho trabajo recopilar, organizar, analizar y hacer circular toda la información necesaria para tener éxito en la resolución de problemas, no está equivocado. Sin las herramientas adecuadas, este proceso puede ser un trabajo pesado para los equipos de mantenimiento abrumados. El software de mantenimiento es una herramienta que puede ayudar a aliviar la carga en cada paso del camino. Una plataforma digital, como un CMMS, se encarga de procesar los números, organizar los datos y hacerlos disponibles donde y cuando sea, para que pueda concentrarse en usar esa información para tomar grandes decisiones y solucionar problemas de manera más efectiva.
Por ejemplo, al crear un historial de activos detallado, es importante documentar cada encuentro con un equipo. Esto es mucho trabajo para un técnico que se apresura de un trabajo a otro y es difícil seguirlo después del hecho. Una inversión en software de mantenimiento le ayudará a superar estos obstáculos. Lo hace al permitir que los técnicos utilicen un conjunto predeterminado de preguntas para tomar y recuperar notas en tiempo real con unos pocos clics.
Lo mismo ocurre con los códigos de falla. La clave para utilizarlos de forma eficaz es la organización y la accesibilidad adecuadas. Sin esos dos ingredientes clave, los códigos de falla se vuelven más un obstáculo que una ayuda. Una forma de lograrlo es utilizar software de mantenimiento. Una plataforma digital puede organizar los códigos de falla mejor que cualquier archivador u hoja de cálculo de Excel y facilitar que los técnicos los clasifiquen rápidamente e identifiquen los relevantes desde el sitio de la falla.
La conclusión
La solución de problemas siempre existirá en el mantenimiento. Nunca estará 100 por ciento seguro el 100 por ciento de las veces al diagnosticar la causa de la falla. Lo que puede hacer es tomar medidas hacia un proceso de resolución de problemas más eficiente para garantizar que el equipo se repare de manera rápida y eficaz. Al combinar una buena comprensión de las métricas de mantenimiento con historiales de activos detallados, códigos de falla, listas de tareas y otros recursos de activos, y hacer que toda esta información sea accesible, puede llevar la solución de problemas más allá de la prueba y error a un enfoque más científico.
Mantenimiento y reparación de equipos
- Mantenimiento móvil:más que una simple tendencia de la industria (PODCAST)
- Está roto, llame al mantenimiento:un proceso de solicitud de trabajo que es más que simples tickets
- Una lección de manejo para operaciones y mantenimiento
- El nuevo libro ayuda a transformar la fabricación y el mantenimiento
- Estrategia y soluciones del ejército para el mantenimiento basado en condiciones
- El esfuerzo de múltiples habilidades para el mantenimiento
- 5 reglas para las operaciones de asociación y el mantenimiento
- Mejorar la disponibilidad es mucho más que mantenimiento
- Tramos de control para planificadores de mantenimiento y otros
- Estrategias para componentes de transmisión de potencia más confiables
- 3 llaves para alquiler y mantenimiento de equipos industriales