Rockwell cuenta todas las formas en que el 'viaje' digital ha valido la pena
Tom O'Reilly, vicepresidente de desarrollo comercial global de Rockwell Automation, habla con la revista Smart Manufacturing.
Tom, cuéntenos sobre el plan de cinco años de Rockwell Automation para reestructurar sus instalaciones y redes de proveedores, y llegar a la "empresa conectada".
Este viaje comenzó hace más de cinco años. A medida que avanzamos en este proceso, trazamos un proceso de seis pasos que creo que ilustra lo que hicimos y cómo hacemos estas cosas ahora, y también cómo hablamos con los clientes. El primer paso es entender las necesidades del negocio. El segundo paso es determinar dónde se encuentran las principales brechas en la cadena de suministro. Luego, también determinar su preparación:evaluar el estado actual de sus instalaciones y procesos de fabricación. El cuarto es desarrollar planes de implementación, luego hacer la gestión del proyecto a medida que ejecuta los planes de implementación y luego una fase de mejora continua.
Tenías 20 plantas diferentes para coordinar. ¿Qué lecciones aprendió la empresa que ahora aplica a los clientes?
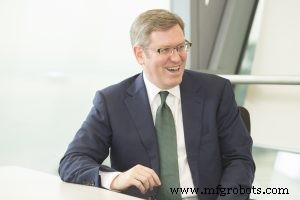
El mayor problema que descubrimos fue la falta de conectividad, específicamente entre el sistema ERP y la fábrica para nuestros sistemas de automatización. En muchos casos, no teníamos los datos correctos. En algunos casos, no había datos. Y en algunos casos, hubo datos incorrectos. Cuando está mirando esos datos y analizándolos y son incorrectos o no lo suficientemente sólidos, puede llevarlo a tomar decisiones equivocadas. Una de las cosas clave, en la fase de determinar la preparación, es evaluar las capacidades de su infraestructura. Esa fue una lección clave aprendida. Y hablamos con nuestros clientes al respecto.
La segunda cosa que es realmente importante para las empresas que buscan emprender viajes de fabricación inteligente es que primero debe encontrar el valor. Mirando dentro de las necesidades del negocio, ¿cuáles son los impulsores de valor real? ¿Cuáles son los grandes problemas reales que debe abordar, que proporcionan el mejor valor por su dinero? A veces, las personas se envuelven solo con la tecnología.
Escuché que Rockwell atribuye una mejora anual del cuatro al cinco por ciento en la productividad debido a ese cambio. ¿Cómo es eso posible? ¿Y cree que la mayoría de los fabricantes pueden esperar eso?
Para la mayoría de los fabricantes, diría que sí. Pero depende de su industria y su estado actual. Así que es difícil generalizar. Si observa cómo lo hicimos/lo hacemos, aquí hay algunos ejemplos:los días de inventario se redujeron de 120 a 82. Redujimos nuestro CAPEX, lo que llamamos CAPEX evitado, en un 30 por ciento por año. Nuestra entrega dentro de nuestra cadena de suministro pasó del 80 por ciento al 96 por ciento. Nuestros plazos de entrega se redujeron en un 50 por ciento. Y luego, para el servicio al cliente, nuestra fecha de entrega al cliente pasó del 82 por ciento al 98 por ciento. Y con respecto a la calidad, redujimos nuestro PPM (partes por millón) en un 50 por ciento. Ya sabes, esto no sucede todo el primer día. Por lo tanto, debe seguir centrándose en las áreas y seguir eliminándolas con el tiempo. Creemos que podemos reducir continuamente los costos en un cuatro o cinco por ciento.
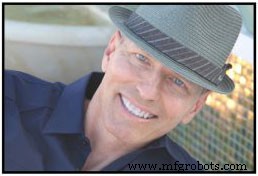
En su práctica de MES, usted Estamos trabajando con FANUC en oportunidades en todo el mundo. ¿Qué problema principal está surgiendo en ese tipo de colaboraciones?
Tenemos una gran asociación con FANUC que comenzó hace unos siete años. No se trata solo de MES. Estamos enfocados principalmente con FANUC en el área del tren de fuerza en la industria automotriz. El mayor problema que enfrentaban nuestros clientes, y uno de los impulsores de la asociación, era la integración entre los sistemas de automatización y su CNC o robots. Entonces, para ayudar a nuestros clientes a abordar eso, ayudamos a FANUC a adoptar EtherNet/IP para las comunicaciones. Nos basamos en lo que llamamos perfiles adicionales dentro de nuestra programación. Básicamente son pantallas que aparecen para configurar automáticamente las comunicaciones en el CNC. Por lo tanto, hicimos que la integración fuera perfecta y la preconstruimos para que sea muy fácil integrar tanto los CNC como los robots con nuestro sistema de automatización.
Entonces, ¿diría que la integración es muy sencilla ahora o sigue siendo un desafío en algunas circunstancias?
Depende de lo que intente hacer. Pero definitivamente es mucho más fácil de lo que era en el pasado. Y eso no lo dice solo Rockwell. Esos son nuestros clientes, como General Motors, quienes nos dicen eso. Su integración y luego el flujo de información desde ambos sistemas, ya sea FANUC o nuestro sistema, hasta el sistema MES y luego continúa hacia el ERP, es mucho más fácil. Así que no sé si dirían que es pan comido, pero dirían que es mucho más fácil.
¿Ese trabajo conjunto es principalmente automotriz? ¿Qué otros mercados son importantes en esa relación? ¿Y puede hablar sobre dónde está trabajando con ellos en el mundo?
La asociación surgió de la necesidad de integración entre la robótica CNC y los sistemas de automatización en la automoción. Entonces, hasta la fecha, la mayor parte del trabajo ha sido automotriz. Una de las áreas de más rápido crecimiento de la robótica se encuentra en las industrias de productos de consumo. Por lo tanto, estamos trabajando bastante juntos con FANUC en todo el mundo, principalmente para la robótica y los productos de consumo, en América del Norte y Europa. Ahora, el trabajo que hemos estado haciendo con FANUC, diría que los principales mercados serían América del Norte, China, Europa, Japón y Corea. Eso es porque esos son centros automotrices donde se toman las decisiones y/o se construyen las maquinarias.
¿Qué tipo de productos de consumo?
Ya sea alimentos y bebidas o productos envasados.
¿Y están en diferentes países?
Esos son principalmente los mercados más desarrollados, donde buscan mayores reducciones de costos, mayores eficiencias, tal vez incluso un mayor rendimiento sin tener mayores gastos de capital:Europa occidental y América del Norte.
¿Qué países seguramente serán mercados de gran crecimiento en su práctica MES?
América del Norte es uno. Hay muchas iniciativas de fabricación avanzada. Y para ser competitivo, debe comenzar a ejecutar la conectividad y tener la convergencia entre TI y OT. (Nosotros decimos la empresa conectada). MES es un habilitador clave para eso. También vemos algunos mercados emergentes como China o India que están más temprano en su desarrollo desde el punto de vista de la madurez de la fabricación. Pero reconocen que para ser continuamente competitivos a nivel mundial, casi tienen que dar un salto en su desarrollo para volverse competitivos a nivel mundial.
Hablemos de la plataforma FactoryTalk Cloud Gateway, que se trata de obtener información de las instalaciones de fabricación que usan su automatización, llevándola a una estructura de datos en la nube donde puede ser combinado con otros datos de terceros y datos de ERP, por ejemplo, y luego colocar la inteligencia comercial en la parte superior para realizar análisis para sus clientes y brindarles nuevos conocimientos comerciales.
Con FactoryTalk Cloud Gateway, nos asociamos con Microsoft. Lo estamos basando en la nube de Microsoft Azure. Pero el software se basa en nuestros años de experiencia con implementaciones en las instalaciones, aprovechando el modelado de la planta de nuestro FactoryTalk VantagePoint con otras tecnologías web y basadas en la nube modernas. El beneficio de la plataforma FactoryTalk Cloud Gateway es que podemos transmitir datos desde múltiples sistemas industriales y comerciales. Y luego, cuando se combinan, podemos contextualizarlos, dar significado a los datos y luego presentarlos en paneles e informes muy fáciles de usar, de modo que los que no son científicos de datos puedan interpretar las tendencias en el proceso y tomar medidas para optimizar.
¿Qué tan importantes son las soluciones en la nube como FactoryTalk Cloud cuando trabaja con empresas fuera de los EE. UU.? ¿Su actualización de esa plataforma en la nube el otoño pasado ayudó con socios y/o clientes internacionales?
Estamos actualizando nuestra plataforma en la nube más rápido que nuestros productos de software tradicionales. Muchos de nuestros clientes globales están interesados en la ubicación geográfica de sus datos, el almacenamiento de datos y la infraestructura de Microsoft Azure es la mejor relacionada con la transparencia y el cumplimiento de los datos en la nube. Por lo tanto, la aceptación de la plataforma en la nube por parte de una base de clientes global es sorprendentemente alta.
¿Qué está haciendo para incentivar a los fabricantes a adoptar FactoryTalk Cloud?
Estamos tratando de hacerlo muy fácil. Por ejemplo, la configuración de los cuadros de mando y la conectividad a nuestro portal es realmente sencilla. Con un par de pasos simples, puede conectar la puerta de enlace al sistema de control. Los datos fluirán automáticamente a la nube y luego podrá configurar inmediatamente sus paneles.
¿Con quién trabajó para construir la puerta de enlace?
El software de puerta de enlace es nuestro propio desarrollo, pero está diseñado para ser muy ampliable con adaptadores y aplicaciones personalizados. Pronto ofreceremos estas API a toda nuestra comunidad de socios.
¿Qué otras plataformas y aplicaciones está ofreciendo o creando para obtener valor para sus clientes en el extranjero?
En la feria de automatización de noviembre pasado, anunciamos FactoryTalk Analytics for Machines, FactoryTalk Analytics for Devices, la aplicación FactoryTalk TeamONE, y muchas de estas son aplicaciones diseñadas específicamente. Muy escalable, fácil de usar, fácil de implementar. Esperamos que al producir estas aplicaciones modulares que son muy rentables, las personas puedan adoptar un enfoque paso a paso, en lugar de tratar de comerse al elefante de un solo bocado.
Cuando usa este software para detectar y eliminar fallas, ¿cuáles son las dos o tres fallas más comunes que encuentra y elimina?
Uno de los beneficios clave que hemos visto es que los clientes están descubriendo problemas desconocidos. Por lo general, en una instalación de fabricación, el operador o el personal de tecnología operativa saben dónde tienen desafíos relacionados con el rendimiento, la calidad o el rendimiento. Una vez que los clientes instalan el sistema y comienzan a resolver esos problemas, muchas veces encuentran otros problemas de los que muchos no estaban al tanto. Podrían tener cuellos de botella en los procesos de fabricación anteriores o posteriores, por ejemplo.
Como todo el mundo, los clientes de Rockwell han sido cautelosos a la hora de adoptar la nube. ¿Qué estás haciendo para convencerlos de que es el momento adecuado para presentarlo? ¿Y los ataques de ransomware de esta semana van a complicar los esfuerzos para promover la adopción de la nube?
Primero, la confiabilidad y la capacidad de las soluciones en la nube han mejorado enormemente. (Además, nuestros clientes no tienen que mantener su propia infraestructura, y eso se está volviendo más importante para muchos de nuestros clientes). En segundo lugar, la escalabilidad de los servicios en la nube es casi imposible de reproducir con capacidades locales. Nuestros clientes pueden comenzar poco a poco y escalarlo mucho más rápido que si lo construyeran y mantuvieran ellos mismos. La seguridad de las soluciones en la nube es probablemente mucho mejor que la de las soluciones locales. Y esto, creo, juega con el segundo punto. Los servicios en la nube se actualizan con mucha más frecuencia.
Creemos que gran parte del ransomware actual [afectó] a lo que la gente llamaría activos de TI no administrados en nuestros clientes, donde no los mantuvieron actualizados o no lo hicieron tener la seguridad adecuada en su lugar. Ese fue el punto de entrada o el comienzo. Los servicios en la nube potencialmente serían una mayor prevención. Ese es nuestro pensamiento inicial. Obviamente, la gente tendría miedo de salir de esto y tratar de entender qué sucedió. Pero nuestro pensamiento inicial es que esto podría empujar a más de nuestros clientes hacia un mayor uso de la nube.
Cuando Rockwell necesitaba construir plantas en Singapur y México, ¿cómo transfirió el conocimiento tribal de los procesos de fabricación en Rockwell a esos mercados?
Hicimos las instalaciones de Singapur y México más adelante en nuestro viaje, por lo que habíamos desarrollado nuestro proceso de seis pasos para implementar Connected Enterprise en cualquiera de nuestras instalaciones, y lo ejecutamos en al menos 10 plantas. Es importante contar con los mejores expertos en la materia sobre aspectos específicos del proceso que fueron complejos, únicos o muy críticos. Trajimos a esos expertos en la materia a cada planta para trabajar y asegurarnos de que esos procesos se aceleraran de la manera correcta. Por último, determinamos que era muy importante contar con sistemas y arquitecturas estandarizados antes de comenzar el viaje.
Sistema de control de automatización
- Cinco formas en que la tecnología Digital-Twin está ayudando a las empresas a superar la pandemia
- En el nuevo panorama logístico, no hay vuelta atrás a las viejas formas
- Clientes desde Noruega hasta nuestra fábrica de enrutadores CNC
- GE Digital:un viaje de transformación digital en curso
- ¿Cómo ha alterado la transformación digital el COVID-19?
- Censornet:asegurar el futuro de la industria manufacturera
- El gran impacto de la Industria 4.0 en el back office
- CS Ellis:cuatro formas de digitalizar la cadena de suministro
- El auge de las plataformas digitales en la fabricación
- Rockwell Automation:aceleración de la transformación digital
- ¿Automatización y el futuro de la fabricación digital?