Cómo optimizar el mecanizado de aluminio en la industria automotriz
Con el aumento del uso del motor, el tren motriz, la bomba de agua y el sistema de frenos fabricados en aluminio en el sector automotriz, el desafío para los OEM y sus socios de la cadena de suministro es ofrecer operaciones de fresado más productivas. La selección de herramientas es la clave para una verdadera diferenciación del mercado en este segmento, donde la aplicación correcta de fresas optimizadas en toda la gama de operaciones de mecanizado de componentes del motor puede generar dividendos significativos.
Continúa habiendo un aumento año tras año en la cantidad de motores de aluminio que se producen, tanto para turismos convencionales como híbridos. De hecho, ahora se fabrican cerca de 100 millones cada año. Estos motores albergan piezas que suelen tener formas complejas y, después de la fundición, exigen una secuencia de operaciones de fresado variadas pero esenciales.
Sandvik Coromant cuenta ahora con una oferta completa para el mecanizado de aluminio en la industria del automóvil, desde el cubicado de la primera etapa hasta el desbaste, el semiacabado y el acabado. Cada herramienta de fresado diseñada, cinco en total, está diseñada para ofrecer una calidad y un costo por pieza optimizados. Para ayudar a lograr esto último, ciertas herramientas de la gama cumplen una combinación de tareas, como realizar desbaste y acabado en una sola operación para reducir los tiempos de ciclo.
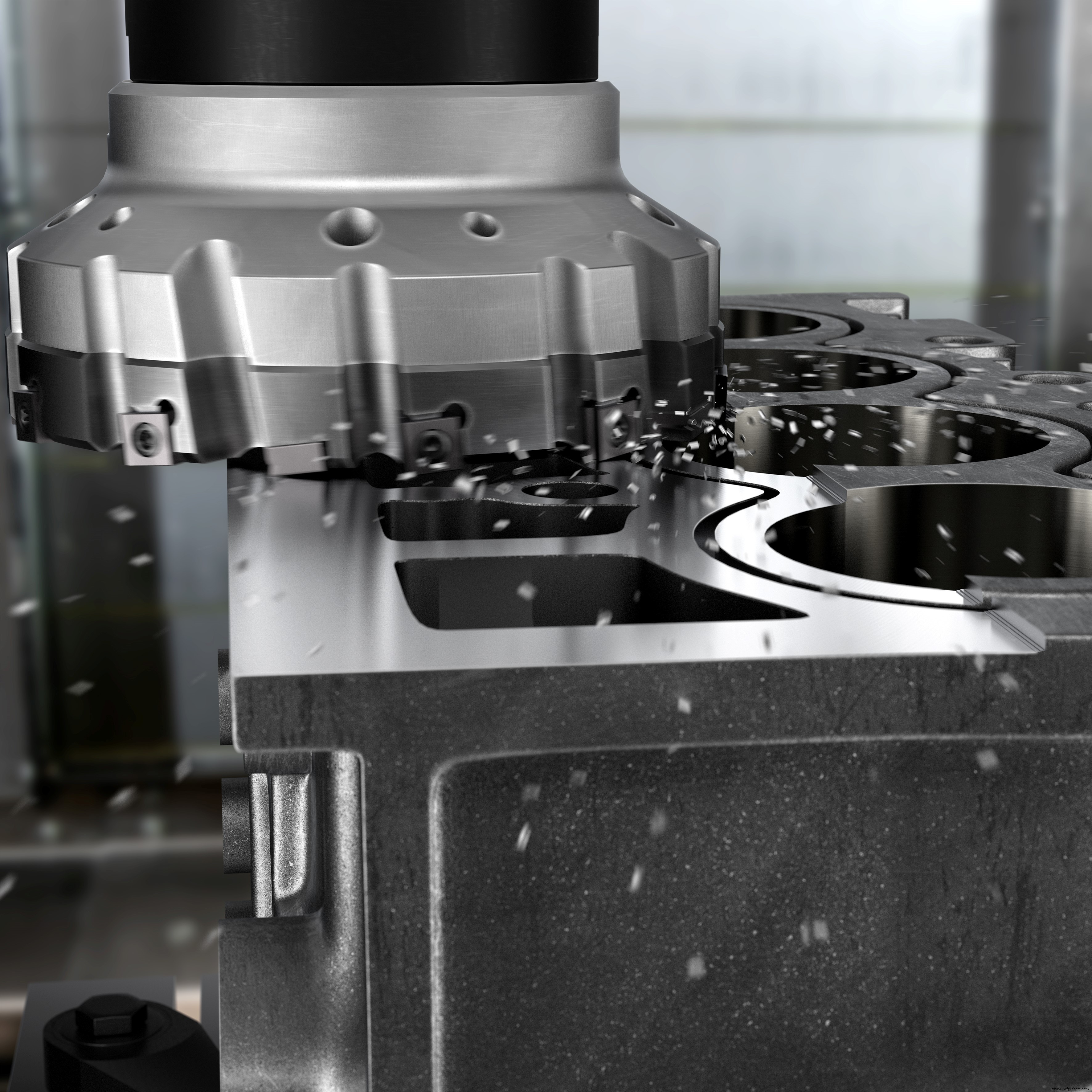
Un ejemplo de ello es el M5C90, un innovador cortador que combina desbaste y semiacabado en una sola herramienta. La M5C90 es una herramienta de fresado frontal de alta velocidad hecha a medida para eliminar largos tiempos de configuración en las instalaciones del cliente. M5C90 funciona con un número reducido de dientes en comparación con los cortadores convencionales, principalmente como resultado del exclusivo posicionamiento radial y axial del inserto en su fila de acabado/diámetro interior (no se requiere ajuste del inserto). Este posicionamiento garantiza un fresado sin rebabas y un acabado superficial óptimo en culatas, bloques de cilindros, piezas del sistema de frenos y todos los componentes de aluminio en los que se puede lograr un corte amplio (no aplicable en piezas de paredes delgadas).
Para brindar un ejemplo de las ganancias potenciales que se ofrecen al usar el M5C90, considere un caso de prueba de un cliente en curso que involucre una válvula del cuerpo del sistema de frenos hecha de AlSi12Cu1. Con una matriz de diámetro exterior de 10 insertos de carburo y un diámetro interior de cuatro insertos (más un inserto Wiper), la herramienta se implementa a una velocidad de husillo de 8000 RPM, una velocidad de corte de 4021 m/min. (13.192 pies/min.) y un avance de 0,25 mm/diente (0,009 pulg./diente). Además, la profundidad de corte axial es de 2 mm (0,078 pulg.) con una profundidad de corte radial de 140 mm (5,51 pulg.), lo que produce una tasa de extracción de metal de 5600 cm 3 /min. (342 pulg. 3 /min.). Aunque aún no se ha determinado la vida útil total de la herramienta, la misma herramienta sigue dentro de la máquina después de 18 meses de servicio.
Para aquellos que necesitan una fresa que también pueda acabar piezas de aluminio de paredes delgadas, como carcasas y carcasas de cajas de cambios, Sandvik Coromant tiene otra fresa igualmente eficaz, la M5F90. La M5F90 es otra herramienta de desbaste y acabado de una sola pasada. Dedicado al mecanizado de piezas de aluminio de pared delgada y operaciones de refrentado, el cuerpo del cortador (25-80 mm, 0,98-3,15 pulgadas de diámetro) alberga puntas de PCD soldadas. Cada punta contiene un borde de desbaste y un borde de acabado. El área de desbaste funciona como una herramienta de fresado convencional, con todos los filos del mismo diámetro y altura, mientras que el área de acabado consta de filos escalonados radiales y axiales. Este concepto permite un paso cerrado para ofrecer un mecanizado sin rebabas y un acabado superficial excepcional. En el breve video a continuación, Sandvik muestra las fresas de la serie M5 para el mecanizado de aluminio automotriz.
Son posibles ahorros de tiempo impresionantes, como se vio en una prueba de caso de un cliente que involucró el fresado frontal de una culata de cilindro de aluminio (alto contenido de Si). Aquí, el uso de M5F90 contra un cortador de PCD especial fabricado por un competidor, no solo vio un ahorro de tiempo de ciclo del 150 %, sino que también eliminó la generación de rebabas. Datos de corte incluidos:velocidad del husillo de 15,915 RPM; 2000 m/min. (6562 pies/min.) velocidad de corte; una velocidad de avance de 0,16 mm/diente (0,006 pulg./diente); y 1,5 mm (0,06 pulg.) de profundidad de corte.
En otro ejemplo de M5F90, se lograron reducciones del tiempo de ciclo del 44 % en una caja de cadena de aluminio en comparación con el uso de una fresa intercambiable de 63 mm (2,48 pulg.) de diámetro de la competencia con seis insertos de PCD. Además, la solución eliminó una operación de desbarbado con cepillo que antes era necesaria.
Otra nueva herramienta diseñada es la M610, que se ha desarrollado para fresar la superficie de la plataforma/la parte superior de los bloques de cilindros del motor con interfaces bimetálicas, generalmente aluminio y hierro fundido gris (CGI).
Una gama de propiedades térmicas y mecánicas hace que el mecanizado sea un reto cuando se trata de materiales bimetálicos. Las fresas existentes para esta aplicación son complejas y requieren ajustes, lo que da como resultado tasas de rendimiento comprometidas. Además, tales herramientas a menudo causan astillado en las partes GCI del componente.
Por el contrario, M610 no requiere configuración ni ajuste, y da como resultado el potencial de implementar altas velocidades de avance sin astillar, rebabar o rayar las piezas. Esta capacidad es importante ya que las imperfecciones de la superficie tienen el potencial de producir fugas entre el bloque de cilindros y la culata, lo que a su vez compromete la potencia y el rendimiento. Algunos OEM automotrices globales ya se están beneficiando de la adopción de M610.
Para hacer referencia a un cliente en particular, se logró una enorme ganancia competitiva al terminar la cara de combustión en bloques de motor bimetálicos. Comparada con una cortadora ajustable con cartuchos de la competencia, la M610 logró una mejora de la vida útil de la herramienta del 833 %, completando más de 4000 piezas, en comparación con las 480 de la cortadora de la competencia. Además, la M610 funcionó a una velocidad 10 veces mayor. Datos de corte para la M610 de 15 plaquitas incluidos:3000 m/min. (9843 pies/min.) velocidad de corte; una velocidad de avance de 5720 mm/min. (225 pulg./min.); una velocidad de husillo de 3820 RPM; una velocidad de avance de 0,15 mm/diente (0,006 pulg./diente); y una profundidad de corte en aluminio de 0,5 mm (0,02 pulg.) y en hierro fundido de 0,05 mm (0,002 pulg.).
Otras herramientas de la familia incluyen la fresa de desbaste tangencial M5Q90, que realiza el cubicado de primera etapa (primer mecanizado de caras después de la fundición) en una sola operación sin rebabas. La herramienta está equipada con plaquitas tangenciales de PCD que proporcionan una acción de corte suave y estable para reducir el consumo de energía y eliminar la vibración.
Culatas y bloques de cilindros de aluminio se encuentran entre los componentes que se benefician del M5Q90. A modo de ejemplo, la operación de cubicación en una culata de cilindro fundido implicaría normalmente el mecanizado de la cara del árbol de levas, la cara de entrada/salida y la cara de combustión. En el caso de estudio de un cliente, el fresado frontal desbaste de culatas fundidas de aleación de aluminio AS-9 en un centro de mecanizado horizontal produjo resultados de vida útil de la herramienta muy impresionantes. A 3000 m/min. (9843 pulg./min.), velocidad de corte por diente de 0,2 mm (0,008 pulg.) y profundidad de corte axial de 2,0 mm (0,079 pulg.) (totalmente acoplado a 40 mm (1,57 pulg.), más de 10 000 componentes fueron completados.
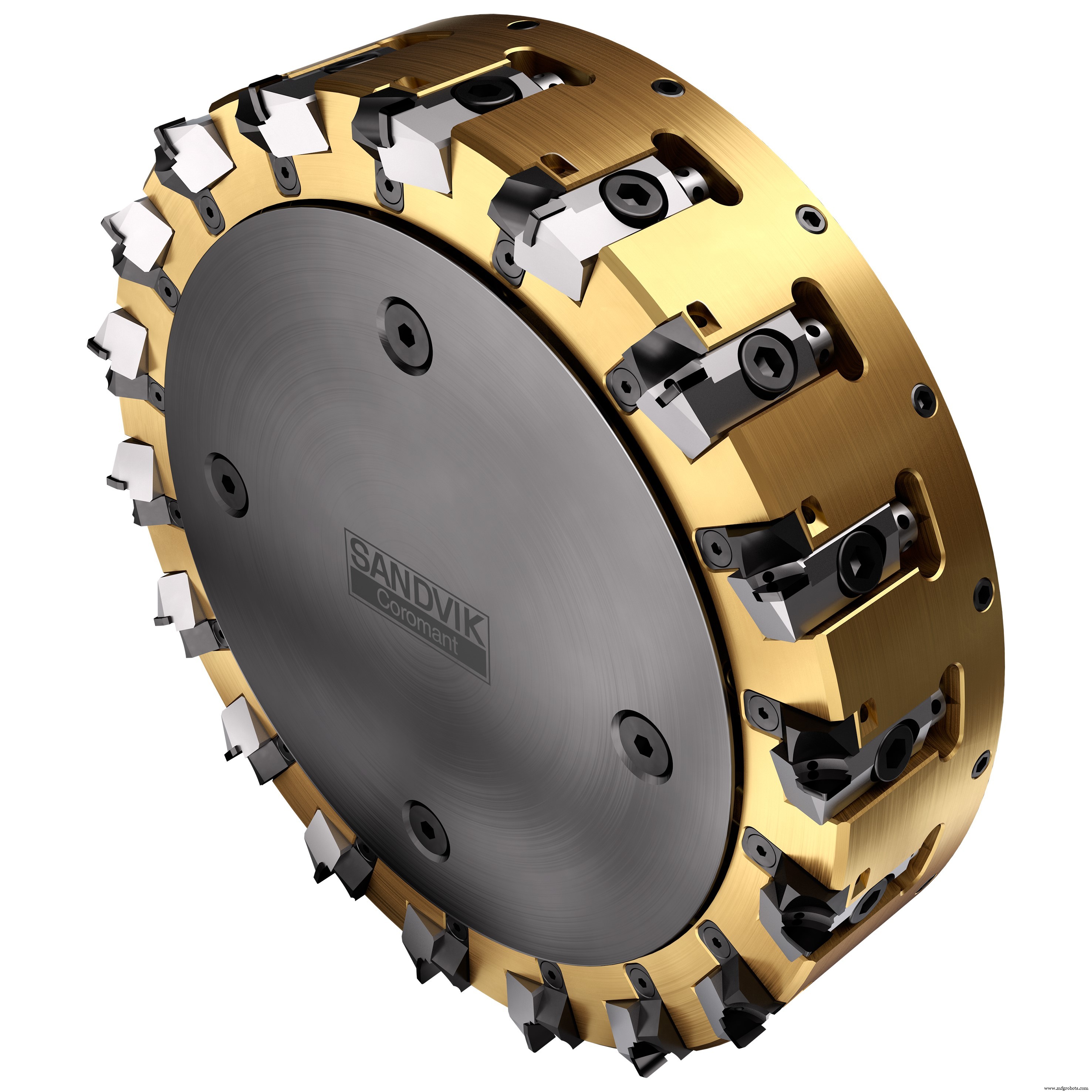
Otra herramienta es la M5R90 para desbaste/semiacabado de segunda etapa. Este cortador estándar funciona con cartuchos ajustables y admite una profundidad de corte de hasta 8 mm (0,315 pulg.) con un radio de 0,4 o 0,8 mm (0,016 o 0,031 pulg.), según el cartucho utilizado. Los cartuchos fáciles de ajustar son beneficiosos en muchas aplicaciones automotrices, como se pudo ver en una prueba reciente de un cliente que involucró el fresado frontal de una cubierta de motor. Fundido en aleación de aluminio MRHB Si12, el M5R90 se desempeñó extremadamente favorablemente contra el cortador competidor titular. Basado en datos de corte idénticos, el M5R90 extendió la vida útil de la herramienta de 8000 a 10 000 piezas de trabajo. Además, el cortador de la competencia necesitaba ajustarse cada 1000 piezas debido al movimiento del cartucho que comprometía el acabado de la superficie. Por el contrario, el M5R90 produjo 8000 piezas antes de que se requiriera ningún ajuste en el cartucho.
También se incluye en la familia la fresa frontal de superacabado M5B90 con su exclusivo posicionamiento axial y radial de plaquitas. Esta configuración, junto con el inserto rascador, garantiza un corte sin rebabas con una calidad superficial excelente, como descubrió recientemente un fabricante de culatas para turismos. La empresa estaba experimentando inestabilidad en el proceso y problemas con las rebabas, mientras que otro problema era la vida útil impredecible del inserto, que dependía de los ajustes del cartucho que diferían de una configuración a otra. El cambio al cortador M5B90 proporcionó una operación de acabado uniforme con un desgaste predecible y sin rebabas. La herramienta produce solo virutas muy finas, que se eliminan fácilmente durante el proceso de corte para evitar daños en la cara del componente. Además, cambiar a M5B90 prolongó la vida útil de la herramienta de 30 000 a 45 000 piezas en promedio.
CoroDrill ® y CoroTap ® La familia de herramientas de taladrado y roscado también se puede ofrecer a los clientes como parte de la misma familia de soluciones para mecanizar componentes de aluminio para automóviles, al igual que CoroMill ® estándar. Fresa de acabado de planeado Century 590.
En todos los casos, el potencial para reducir los tiempos de ciclo y el costo por pieza, al mismo tiempo que se mejora la vida útil y la calidad de la herramienta, es muy real, como se puede ver en los ejemplos de casos de clientes descritos. En la industria automotriz, donde prevalece la producción de alto volumen, incluso un pequeño ahorro en el tiempo del ciclo puede equivaler a importantes beneficios financieros. Con este pensamiento en mente, es difícil ignorar cualquier tecnología que pueda demostrar la capacidad de generar mayores ganancias.
Tecnología Industrial
- El valor de la fabricación aditiva en la industria automotriz
- ¿Cómo está transformando la impresión 3D la industria automotriz? (2021)
- Cómo la impresión 3D impulsa el cambio en la industria automotriz
- Cómo la industria de la logística automotriz se enfrenta a COVID-19
- Cómo afecta la automatización a la industria manufacturera
- Cómo la tecnología IoT está supervisando las operaciones en la industria automotriz
- Certificación NADCAP y cómo se aplica a la industria del mecanizado de precisión
- Mecanizado CNC en la industria automotriz
- Cómo se utiliza el aluminio en la industria artesanal naval
- Las propiedades de mecanizado de los grados de aluminio 6061
- Mecanizado de latón frente a aluminio:la ventaja de la tradición