Entrevista con el experto:el ingeniero principal de Oerlikon para AM, Matthew Donovan, sobre impresión 3D para la industria aeroespacial
Oerlikon, un grupo de ingeniería y tecnología global, presta servicios a algunas de las industrias más críticas para la seguridad, incluidas la aeroespacial y la defensa . Cada vez más, la fabricación aditiva se ha convertido en una parte clave de sus ofertas, y la compañía estableció un centro de innovación y una instalación de producción de componentes avanzados por $ 55 millones en los EE. UU. A principios de este año.
En la entrevista de expertos de esta semana, nos sentamos con Matthew Donovan, ingeniero principal de fabricación aditiva en Oerlikon, para analizar cómo continúa desarrollando una instalación de producción de AM de extremo a extremo, lo que entusiasma las tendencias de AM para tenga cuidado y por qué los estándares son fundamentales para el futuro de la industria.
¿Podría hablarme de Oerlikon?
Oerlikon es una empresa global y líder de fabricación en sus segmentos de Soluciones de superficie y Fibras artificiales. Parte del segmento Surface Solutions, Oerlikon AM, ofrece soluciones de fabricación aditiva, desde polvos metálicos hasta prototipos y producción en serie.
¿Cómo se involucró por primera vez en la fabricación aditiva?
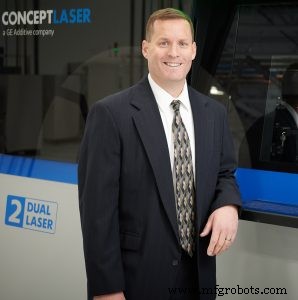
Mi experiencia es aeroespacial. Antes de llegar a Oerlikon, pasé los últimos 20 años trabajando, principalmente, en motores de turbina de gas, componentes de sección caliente y componentes de sección de combustión.
Tengo experiencia en sistemas de suministro de combustible, principalmente para motores de turbinas de gas aeroespaciales, pero también para turbinas de gas industriales y reformadores de pilas de combustible. También he trabajado en varios esfuerzos de I + D con la NASA y otras empresas. Así que tengo experiencia trabajando con materiales de alta resistencia y alta temperatura para entornos muy exigentes.
Comencé como ingeniero de fabricación, aprendiendo los entresijos de cómo fabricar y construir piezas y gastar tiempo como ingeniero de calidad realizando investigaciones de campo para esos mismos componentes.
Comencé a trabajar en manufactura avanzada en 2006. Comencé a encontrar geometrías y componentes desafiantes que realmente no podíamos hacer con la manufactura convencional.
En ese momento, estaba trabajando con Morris Technologies en componentes de metal impresos en 3D. Comenzamos a desarrollar componentes para inyectores de combustible mediante fabricación aditiva.
A lo largo de los años, desarrollé algunos componentes utilizando fabricación aditiva. Trabajé para United Technologies, asistiendo a toda la empresa en el desarrollo e implementación de tecnologías AM, principalmente con un enfoque hacia el hardware de certificación de vuelo.
Mientras trabajábamos para implementar estos componentes, una de las principales lagunas que descubrí fue que había una falta total de estándares sobre cómo fabricar piezas y cómo certificarlas.
Gran parte del costo asociado con la industria aeroespacial no son necesariamente los componentes en sí mismos, sino la certificación. Debemos proporcionar una trazabilidad completa para cada componente que fabricamos. Desarrollar los estándares sobre cómo lo hacemos e implementar eso para los aditivos fue todo un desafío.
Comencé a trabajar en las normas AM con ASTM F42 alrededor de 2009. Ayudé a redactar algunas normas y, posteriormente, participé en algunos comités. Fui coautor de la guía de diseño para la fusión de lecho de polvo metálico por láser, ISO ASTM 52911, con ISO / TC 261 y ASTM F42.
A través de ese trabajo con United Technologies, trabajando con muchas personas altamente talentosas y teniendo acceso a una serie de excelentes recursos, pudimos proponer varias innovaciones y desarrollar algunos productos realmente de vanguardia para AM. lecho de polvo de metal.
¿Qué implica su puesto en Oerlikon?
Comencé en Oerlikon en 2017 y mi función, ahora, es ingeniero principal de AM. Mi función se ha centrado en gran medida en la implementación y el desarrollo de tecnologías de metal AM listas para la producción.
Comenzamos como una división de puesta en marcha del Surface Solutions Group. Hemos construido una nueva instalación en Huntersville, Carolina del Norte, a la que nos mudamos hace poco menos de un año.
Es una instalación de 120,000 pies cuadrados que actualmente opera 18 sistemas de lecho de polvo metálico. En el sitio, tenemos capacidades de HIP (prensado isostático en caliente) y horno de vacío, así como capacidades de posprocesamiento, manejo de polvo e inspección.
El objetivo ha sido establecer esta instalación como un verdadero flujo de trabajo de producción de AM de extremo a extremo, con control de todos los aspectos de la cadena de suministro, para que podamos proporcionar trazabilidad a nuestros clientes.
Mi papel en eso ha sido, principalmente, en la certificación de máquinas. Trabajo en estrecha colaboración con los OEM de máquinas en la instalación y calificación de nuestras máquinas y luego las certifico por su capacidad y capacidad cruzada para componentes en diferentes máquinas.
Entonces podemos comprender las capacidades de la máquina, la tolerancia y la precisión de una máquina individual para producir la tolerancia geométrica de un componente AM y las diferencias entre nuestras máquinas y luego ajustarlas para que podamos entregar el mismo producto en varias máquinas.
La estandarización ha sido un gran tema de conversación, especialmente para industrias como la aeroespacial. ¿Cómo se han desarrollado las cosas a lo largo del tiempo que ha estado involucrado en la industria y cuál es el estado actual de la estandarización de AM?
Ha habido muy buenos desarrollos.
Necesitamos normas, especialmente en el sector aeroespacial, pero también en otras áreas críticas para la seguridad como la médica, la nuclear y la energía. La clave de los estándares es que permiten que todos hablen el mismo idioma y comprendan de lo que es capaz un producto.
Con la ausencia de estándares, todo el mundo estaba construyendo piezas de manera eficaz y realizando su trabajo de maneras a menudo muy similares, pero no de la misma manera. No hablaban el mismo idioma. Es muy común que las personas se refieran a diferentes términos para referirse al mismo proceso, o que se refieran al mismo término y se refieran a procesos radicalmente diferentes.
Desarrollar estándares le permite hablar en el mismo idioma en todos los ámbitos y comprender lo que quiere decir cuando se refiere, por ejemplo, a un nivel de calificación de construcción, materia prima o máquina.
En el sector aeroespacial, si no tiene un estándar contra el que pueda certificar una pieza o, por lo general, varios estándares para identificar la pieza que está fabricando, sus propiedades mecánicas, rendimiento y tolerancias y para ser capaz de rastrearlo hasta el lote original del que vino, hasta la composición química de los elementos que entraron en él, entonces no puede ponerlo en una plataforma aeroespacial.
Podemos hacer geometrías increíblemente complejas y hacer piezas con AM que simplemente no son físicamente posibles de otra manera. Podemos ahorrar mucho peso, tiempo, material y costos al fabricar piezas mediante AM.
La libertad de diseño y fabricación que nos brinda AM es clara. Pero el inconveniente es que es genial si puedes hacer la pieza, pero si no puedes demostrar que es una buena pieza, no le hace ningún bien a nadie.
Los estándares son lo que nos lleva a cruzar esa línea para poder fabricar y vender piezas y poder usarlas en la producción para la industria aeroespacial.
Por tanto, los estándares aeroespaciales son una de las piezas clave del rompecabezas antes de poder fabricar piezas.
Ha habido varias organizaciones de desarrollo que han estado trabajando muy duro en esta área durante mucho tiempo. He trabajado como voluntario en las normas de ASTM durante aproximadamente 10 años y he visto los beneficios de lo que hacemos.
Como mencioné, contribuí al estándar de titanio original para la fusión en lecho de polvo. Ese primero me tomó (y a varias otras personas) un poco más de dos años para que el primero fuera validado. Posteriormente, pudimos entregar otros adicionales en aproximadamente la mitad de ese tiempo.
Las cosas realmente están empezando a acelerarse ahora. ASTM lanzó recientemente su Centro de Excelencia con sede en Auburn, Alabama, junto con la Universidad de Auburn.
La intención detrás de eso era aplicar fondos y esfuerzos de investigación y desarrollo específicos a través de socios de colaboración para lograr más estándares rápidamente. Ha habido mucha colaboración entre la industria y los organismos gubernamentales para identificar las brechas y los estándares que percibimos en la industria, que es lo que necesitamos para avanzar.
Es posible que haya oído hablar de la hoja de ruta de ANSI. Es un muy buen documento al que algunos de nosotros en la industria hemos contribuido, para identificar cuáles son nuestras brechas clave, que debemos llenar para lograr una verdadera producción para la fabricación aditiva.
En la última versión de esa hoja de ruta, creo que se identificaron 91 brechas, principalmente en áreas de estándares, y algunas de ellas son de muy alta prioridad. El Centro de Excelencia de ASTM es un vehículo que se está utilizando para aplicar I + D para cerrar esas brechas en los estándares.
En otra área, SAE International tiene su Especificación de Materiales Aeroespaciales (AMS). Los primeros para la fusión de aditivos en lecho de polvo fueron AMS 7000, 7001, 7002 y 7003 para la aleación de níquel 625, que se lanzó recientemente.
Esos son excelentes trabajos que producirán muchos resultados. Muchos de nosotros ya estamos usando estos estándares para desarrollar piezas de producción.
Con su experiencia en la adopción de AM, ¿cuáles han sido algunos de los desafíos en la integración de la tecnología internamente y cómo ha navegado ese proceso?
Oerlikon AM ha tenido como objetivo proporcionar soluciones de AM que cumplan con los requisitos de las industrias más exigentes, como la aeroespacial y médica, entre otras.
En nuestras diversas instalaciones contamos con los sistemas de calidad adecuados, como AS9100 para aeroespacial e ISO 13485 para médico. Pero con respecto a la integración de todos los sistemas necesarios para llegar allí, ha sido un desafío, aunque existen algunas soluciones que proporcionan piezas del rompecabezas.
Yo diría que no existe una solución única que cubra todos los aspectos de lo que necesitamos, de principio a fin. Pero hay muchas buenas herramientas que cubren partes de toda la cadena de suministro de un extremo a otro.
Por lo tanto, uno de nuestros desafíos es identificar las soluciones que cubren diferentes aspectos de nuestra cadena de suministro, traer incorpore aquellas que cubran los aspectos que necesitamos y las integre.
Por ejemplo, algunas soluciones manejan muy bien las finanzas y el inventario, pero no funcionan muy bien para los flujos de trabajo de fabricación. Otros manejan bien los flujos de trabajo de fabricación y la planificación de la producción, pero no manejan, digamos, la estimación del tiempo de construcción, los problemas de revisión de materiales o los problemas de componentes geométricos, como planos y modelos 3D.
Por lo tanto, hay muchos de diferentes aspectos, y nuestro desafío es integrar todas esas piezas diferentes para tener una solución perfecta de principio a fin. Actualmente, es un proceso bastante manual, pero estamos trabajando para que sea mucho más automatizado a medida que avanzamos.
¿Puede compartir alguna historia de éxito sobre cómo ha utilizado AM en producción?
Si bien no puedo referirme específicamente a esos clientes sin obtener su autorización, tenemos varios componentes que están activamente en producción. Algunos en los que puedo pensar, sin pensarlo, son componentes aeroespaciales y relacionados con la defensa.
Entonces, uno es un componente de vuelo que es parte de un sistema de misión en un helicóptero militar. Hemos estado en producción para ese componente durante dos años y hasta la fecha hemos entregado con éxito más de 200 unidades.
También fabricamos otro componente que se utiliza para un sensor de suelo, donde tienes un sistema integrado de 80 componentes individuales diferentes en una sola pieza monolítica. Ese también ha estado en producción durante casi dos años.
Tenemos una serie de otros componentes de producción que fabricamos — para áreas de exploración de petróleo y gas y submarinas, que están en producción activa para robótica submarina — para otro de nuestros clientes que estamos fabricando piezas para, que se utilizan activamente tanto en petróleo y gas, perforación y exploración, y robótica submarina.
¿Cómo cree que evolucionará la fabricación aditiva en los próximos cinco años, tanto en términos de tecnología como de la industria en general?
Durante los próximos cinco años, veo que la tecnología evolucionará con más sistemas multi-láser, lo que permitirá que las piezas se produzcan más rápido, reduciendo así el costo de los componentes. Esto impulsará aún más la implementación de piezas AM.
El costo de las piezas es un factor clave, y el tiempo del láser es su principal factor determinante del costo de un componente AM. Por lo tanto, si puede incluir más láseres en una pieza y ser capaz de certificar los componentes, utilizando esos sistemas multi-láser, podrá construir la misma pieza más rápido y por lo tanto más económico.
La otra evolución es que tendremos mejores sistemas de monitoreo en proceso. Hay algunos diferentes disponibles actualmente por diferentes fabricantes, pero mi impresión es que si bien muchos de ellos son buenos sistemas, aún no tienen el nivel de capacidad que los usuarios, como yo, necesitarían para poder implementarlos. a una tasa de producción real.
Mi esperanza es que pronto tengamos un verdadero monitoreo en proceso, de modo que podamos monitorear lo que está sucediendo en la máquina durante el proceso y poder identificar problemas con un componente antes de que salga del máquina.
El escenario ideal sería tener un software inteligente que pueda identificar problemas y potencialmente hacer correcciones con soporte de ingeniería sobre la marcha. Por supuesto, mejor aún sería tener máquinas verdaderamente robustas que no tengan ningún problema y que funcionen las 24 horas del día, los 7 días de la semana.
¿Hay alguna tendencia que le entusiasme?
Estoy entusiasmado con varios desarrollos, y los sistemas de monitoreo en proceso, como mencioné, son uno.
También se están desarrollando y lanzando algunos materiales nuevos. Estamos desarrollando algunos materiales diferentes que permiten a algunos de nuestros clientes fabricar componentes muy revolucionarios.
La otra cosa que me entusiasma es que hay mucha más diversificación en los fabricantes de todo el mundo. Al principio, la mayoría de las máquinas AM se producían en un puñado de países de Europa. Ahora hay nuevos fabricantes y varios países que están aplicando enfoques diferentes y novedosos para construir máquinas.
Están reduciendo el costo de las máquinas y están aprendiendo, de su uso en la industria, para hacerlas más intuitivas para los operadores.
Mi experiencia durante los primeros años con estas máquinas, fue que son muy quisquillosas y requieren mucha atención y "cuidado de niños". Y, francamente, gran parte del diseño de la máquina no fue muy amigable con la fabricación.
Veo que se está incorporando mucha facilidad de uso a las máquinas ahora, ya que los fabricantes de máquinas obtienen comentarios de sus usuarios.
Pero también, creo que la creciente competencia de diferentes fabricantes en todo el planeta está ayudando a impulsar la innovación en los sistemas, reducir los costos y aumentar la usabilidad de los sistemas de las máquinas.
¿Qué sigue para Oerlikon, especialmente para las instalaciones que estás ayudando a supervisar y administrar?
Nuestro objetivo a corto plazo para esta instalación es instalar y certificar todo el equipo que hemos comprado. Tenemos 18 sistemas de lecho de polvo metálico en línea y en funcionamiento actualmente, y estamos haciendo hardware de producción en muchos de esos sistemas.
Nuestro siguiente paso para ellos es completar las propiedades del material para todos nuestros sistemas de materiales en todas nuestras máquinas y los conjuntos de datos para ellos. Pero eso lleva mucho tiempo y es caro.
Afortunadamente, tenemos mucha gente muy talentosa aquí con mucha experiencia en materiales, metalurgia e ingeniería, y estoy muy orgulloso de ser miembro de ese equipo.
El otro objetivo es poner en pie todos los demás equipos para lograr esa verdadera instalación de producción de fabricación de extremo a extremo.
Recientemente, pusimos en línea nuestro horno HIP y el horno de vacío, y estamos trabajando para obtener la certificación.
También hemos traído algunos equipos de CNC, y también tenemos una cantidad sustancial de hornos y equipos de CNC adicionales para el posprocesamiento. Por lo tanto, el objetivo es instalar, certificar e integrar operativamente todo este equipo para crear un sistema de fabricación completo y cohesivo.
Para obtener más información sobre Oerlikon, visite: https://www.oerlikon.com/en/
Impresión 3d
- Entrevista con un experto:el profesor Neil Hopkinson, director de impresión 3D de Xaar
- Entrevista con un experto:Philip Cotton, fundador de 3Dfilemarket.com
- Entrevista con un experto:Spencer Wright de pencerw.com y nTopology
- Entrevista con un experto:Dr. Alvaro Goyanes de FabRx
- Entrevista con el experto:Guillaume de Calan, CEO de Nanoe, sobre el futuro de la impresión 3D de cerámica
- Entrevista con el experto:John Kawola, presidente de Ultimaker, sobre el futuro de la impresión 3D
- Cómo Ford Motor Company está innovando la impresión 3D para la industria automotriz:Entrevista de experto con Harold Sears
- Entrevista con el experto:Simon Fried, cofundador de Nano Dimension, sobre el auge de la impresión 3D para electrónica
- Entrevista con el experto:Brian Alexander de Solvay sobre el desarrollo de polímeros de alto rendimiento para la impresión 3D
- Entrevista con expertos:una mirada a las impresoras 3D SLA ultrarrápidas de grado industrial de Nexa3D
- Entrevista con expertos:AMendate sobre su software de optimización de topología automatizada para impresión 3D