Entrevista con el experto:Yves Hagedorn, director general de Aconity3D, sobre cómo ayudar a las empresas a innovar con la fabricación aditiva
La adopción de la impresión 3D en metal puede ser un desafío debido a la necesidad de desarrollar aplicaciones, calificar materiales y procesos. Para superar estos desafíos, la empresa alemana Aconity3D proporciona sistemas flexibles de impresión 3D de metales de laboratorio que permiten a sus clientes experimentar con parámetros de proceso e investigar nuevas aplicaciones para la tecnología.
En la entrevista de expertos de esta semana, Yves Hagedorn, director gerente de Aconity3D, analiza los beneficios de los sistemas de hardware con arquitectura abierta y por qué el software de diseño es uno de los desafíos clave en la impresión 3D de metal.
¿Podría hablarme sobre Aconity3D?
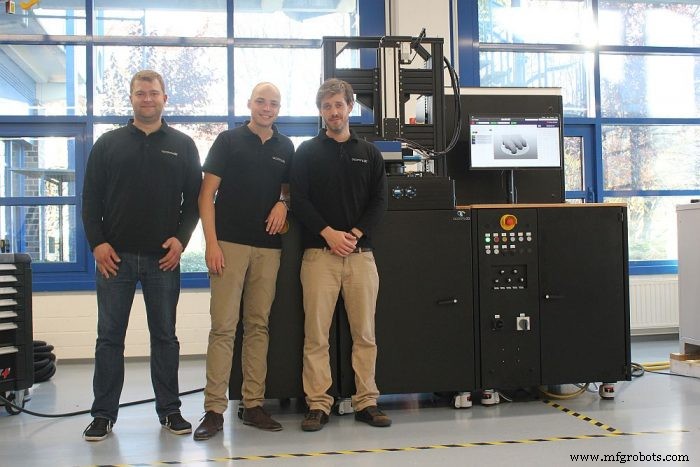
En Aconity3D, ofrecemos todo lo que se necesita para la fabricación aditiva de metales.
Proporcionamos componentes especiales para máquinas y diferentes módulos, que se pueden combinar para crear equipos diseñados para aplicaciones especializadas. Eso es porque creemos que no existe un sistema que se adapte a todas las aplicaciones posibles en todo el mercado.
El viaje de nuestro cliente comienza con la consultoría. Por ejemplo, un cliente podría acercarse a nosotros para ver si es posible imprimir magnesio en 3D. En este caso, investigamos un poco en nuestra segunda unidad comercial, que es la distribución de material, y averiguamos para nuestro cliente dónde obtener el material específico en cuestión.
En nuestra tercera unidad de negocios, haríamos algunas pruebas para asegurarnos de que el material sea factible para ser procesado con fabricación aditiva. Y si todo funciona y un cliente está satisfecho, actuaremos como un taller de trabajo y fabricaremos esa aplicación específica para el cliente.
A largo plazo, el cliente puede decidir comprar nuestro equipo que ha sido diseñado para esa aplicación específica.
Nuestro enfoque permite a nuestros clientes realizar una investigación eficiente en términos de ampliar el alcance de los materiales aplicables.
Si los clientes tienen ciertos materiales para aplicaciones especiales que aún no están calificados, pueden investigar mucho para calificar con nuestro equipo. Pueden usar varios parámetros, son completamente gratuitos desde el lado del software y también pueden realizar cambios en el hardware, dependiendo de los parámetros que necesiten.
En última instancia, queremos ser una ventanilla única para los clientes. Sin embargo, la venta de equipos es nuestro principal negocio.
¿Cuál fue la motivación para fundar la empresa?
Bueno, si desea ampliar el alcance de la fabricación aditiva, ya sea en términos de materiales aplicables o aumentando la productividad o precisión dimensional, necesita acceso completo al hardware y a todos los parámetros posibles en el proceso.
Vimos que no había ningún sistema en el mercado que le permitiera hacer esto. Y fue entonces cuando se nos ocurrió la idea de brindar a los clientes la posibilidad de afinar su proceso. Fue entonces cuando nació Aconity3D.
Pronto nos dimos cuenta de que tenemos un activo real y que podemos satisfacer una necesidad real del cliente de tener acceso tanto al hardware como al software.
¿Existen industrias específicas que se beneficiarían más de la tecnología y los servicios que brinda Aconity3D?
No existe una industria específica, ya que las aplicaciones industriales de los aditivos son tan variadas como las posibilidades.
Tomemos la industria médica, donde hay un enorme campo de aplicaciones. Por ejemplo, puede tener implantes de titanio o incluso magnesio, que es bioabsorbible. También existen aplicaciones en la industria de sensores médicos.
Lo mismo ocurre con la industria aeroespacial. La industria aeroespacial tiene interés en ampliar el alcance de las aleaciones aplicables para galvanoplastia, por ejemplo, o aleaciones de alta temperatura.
La automoción también es otro ejemplo interesante porque la industria es muy consciente de los costes. Esto significa que las empresas automotrices solo quieren pagar por lo que obtienen.
Nuestra propuesta de valor es nuestra alta flexibilidad, que nos permite omitir todo lo que no se necesita para esa aplicación específica. Esto nos permite competir con las tecnologías de fabricación tradicionales.
En lo que respecta a la impresión 3D de metales, ¿qué aplicaciones son las más adecuadas para la tecnología y cómo pueden las empresas comenzar a identificar los tipos correctos de aplicaciones?
Es bueno considerar la fabricación aditiva si tiene componentes de tamaños pequeños y estructuras complejas. Otra razón para usar aditivos puede ser combinar nuevos materiales donde antes era imposible hacerlo; tome el cobre y el cromo como ejemplo.
El principal obstáculo aquí es que para casi todas las aplicaciones, producir una pieza es más caro con la fabricación aditiva en comparación con el fresado u otras tecnologías de fabricación tradicionales.
Una excepción son las restauraciones dentales:para ellas, la fabricación aditiva es más barata que el fresado. Por eso fue una de las primeras aplicaciones industriales para la fusión por láser en polvo. Otra excepción son los marcos de anteojos, que también son una excelente aplicación para aditivos.
Pero para todos los demás, a menudo existe un conflicto entre el caso comercial y los costos del ciclo de vida del producto. Ese es el principal obstáculo porque muchos clientes simplemente no tienen idea de los costos del ciclo de vida de sus productos.
Para decirlo de otra manera, ahora puede tener una integración funcional. Entonces, por ejemplo, puede integrar canales de enfriamiento en una carcasa, pero es realmente difícil ponerle una etiqueta de precio. Por lo tanto, el principal desafío es realizar el cribado de las piezas y encontrar un caso comercial válido para su aplicación y producción de aditivos.
¿Cuáles son los desafíos clave de la impresión 3D en metal y cómo los ha abordado?
En mi opinión, uno de los desafíos clave radica en el diseño de piezas y las soluciones de software correspondientes para la preparación de datos. Cuando se trata de fabricación aditiva, la estandarización sigue siendo un desafío y creo que esto se debe en parte al hecho de que el software no está realmente estandarizado. Por ejemplo, tome los diferentes formatos de datos para cada proveedor de sistema individual. Además, en términos de diseño de piezas, hay pautas limitadas o nulas como consecuencia de la gran flexibilidad de la producción de aditivos. Esta es también la razón por la que las estructuras de restauración dental fueron la primera aplicación industrial verdadera:una estructura de preparación de datos y diseño de piezas completamente automatizada, una condición previa para la producción en serie de piezas de un solo tamaño de lote.
Por primera vez Desde los años 70, ahora nos encontramos en una situación en la que podemos construir piezas más complejas de las que realmente podemos diseñar o simular.
Por lo tanto, el diseño y la preparación de datos siguen siendo un cuello de botella en esta industria, mientras que el énfasis se pone en sistemas de hardware de mayor productividad, y las soluciones de software inteligentes quedan excluidas de esta ecuación. Preparar las piezas para que sean adecuadas para la fabricación aditiva es una habilidad clave y también requiere bastante tiempo.
He visto ejemplos en los que el diseño de piezas y la preparación de datos tardaron más de dos semanas, mientras que la impresión de la pieza sólo llevó dos días. Esto es simplemente ineficaz para diseñar una pieza durante ese período de tiempo. Y ahí es donde entra el problema, en mi opinión.
¿Podría compartir alguna de las historias de éxito de sus clientes?
Sí definitivamente. Hemos tenido clientes que ahora producen piezas de magnesio para aplicaciones médicas. Tenemos otros que obtuvieron la aprobación de la FDA para sus implantes de titanio.
En la industria automotriz, teníamos una solicitud específica de un sistema de alta productividad. Así que proporcionamos un sistema de cuatro láser con superposición total en una placa de 400 milímetros de diámetro. Creo que somos los únicos en el mercado que pudimos hacerlo y eso tiene un impacto significativo en la productividad.
Otros clientes aprovechan la posibilidad del precalentamiento a alta temperatura para ampliar el alcance de los materiales aplicables hacia aceros para herramientas de alta aleación, aluminuros de titanio y ciertas superaleaciones a base de níquel.
¿Cómo cree que evolucionará la industria de la FA en los próximos años?
La industria definitivamente ha madurado en los 12 años que he estado involucrado en aditivos. Cuando comencé, había mucho entusiasmo. Ahora, el bombo ha disminuido un poco.
La evolución de la tecnología ha ayudado a desbloquear muchas aplicaciones para la fabricación aditiva, pero todas estas aplicaciones aún requieren un alto nivel de experiencia.
Hoy en día, puede comprar ciertas impresoras 3D de escritorio por menos de 1000 euros, lo que hace que mucha gente crea que puede comprar herramientas industriales, como esos costosos sistemas de fusión por láser a base de polvo, presione play y usted Inmediatamente tendrás tu caso de negocios.
Obviamente, ese no es el caso de la fabricación aditiva industrial. Existe un gran desafío en la formación y el desarrollo de conocimientos especializados. Y creo que ahí es donde toda la industria deberá seguir evolucionando.
Tener más experiencia dentro de la industria y, sobre todo, tener procesos más estandarizados y productos confiables será clave para la adopción industrial de la fabricación aditiva.
¿Hay algún avance en la industria de la FA que le entusiasme?
Sí definitivamente. Tenemos un fuerte enfoque no solo en el monitoreo en proceso, lo que significa usar diferentes sensores para obtener la mayor cantidad de información posible de su proceso, sino también en usar esa información para hacer control en el proceso.
Creo que ese es el Santo Grial de la AM porque con el control en proceso puede reaccionar casi de inmediato ante las deficiencias dentro de su proceso.
Esto hará que los sistemas sean mucho más inteligentes.
¿Podría hablarnos un poco más sobre la supervisión y el control en proceso, y lo que Aconity3D está haciendo en ese espacio?
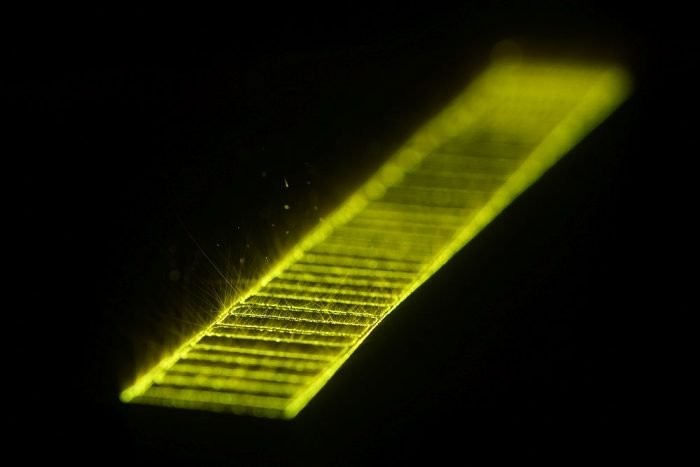
Nuestra empresa es una empresa derivada del Instituto Fraunhofer de Tecnología Láser, donde se originó la fusión por láser de lecho de polvo.
Con esos antecedentes, pudimos implementar diferentes sensores ópticos para acompañar al láser de procesamiento. Y eso le permite extraer mucha información inmediatamente de la zona de interacción, la piscina de fusión y el láser.
Esto, sin embargo, conduce a otros desafíos asociados con Big Data. ¿Qué haces con esa enorme cantidad de datos registrados? ¿Cómo se asegura de omitir los datos que en realidad no necesita? ¿Y cómo distingue entre datos útiles e inútiles?
Creo que ahí es donde se encuentra la industria actualmente. Y eso es lo que también estamos haciendo. Usamos una cámara de alta velocidad para mirar dentro del proceso y aprender de él, y también tenemos diferentes sensores que permiten un circuito cerrado en el control del proceso.
Entonces, si tiene ese sistema en su lugar, puede detectar si su piscina de material fundido está demasiado caliente o demasiado grande, y puede regularlo mediante la potencia del láser, reaccionando así a esa señal del proceso.
Eso es realmente fascinante para mí. Y creo que todavía hay mucho potencial aquí.
Aconity3D ha anunciado recientemente una asociación con Aerosint. ¿Qué significa esta asociación para su empresa en el futuro?
Desde que estoy en la industria, la gente se ha interesado por las piezas metálicas de múltiples materiales. Y siempre fue el problema de lo que debería venir primero, la aplicación o el desarrollo técnico.
Durante algún tiempo, nada sucedió realmente en esa dirección. Y luego nos reunimos con Aerosint, una empresa belga que ha desarrollado un dispositivo de deposición de polvo capaz de depositar dos materiales diferentes en las dimensiones X e Y en un lecho de polvo. Esto es básicamente lo que ha faltado en la fabricación aditiva de múltiples materiales.
Ahora entramos en la ecuación con la capacidad de reaccionar al patrón de polvo o patrón de material alterado en nuestra placa de construcción cambiando los parámetros de proceso requeridos para cada material individual.
Esto significa que ambos socios, Aconity3D y Aerosint, tienen una base sólida para hacer realidad ese sueño de AM multimaterial.
¿Qué nuevas aplicaciones se podrían abrir con la posibilidad de la impresión 3D de metales con múltiples materiales?
Una industria que realmente podría beneficiarse es la industria de la joyería.
La creación de materiales clasificados, desde el cobre hasta el cromo, puede ser otra oportunidad. Aquellos podrían usarse para herramientas dentro de las industrias de moldeo o forja. Por ejemplo, con la impresión 3D de múltiples materiales, podría usar cobre para crear estructuras de enfriamiento y cromo o acero para crear la superficie exterior de la pieza.
Si tiene gradientes, también puede calificar sus propiedades mecánicas. Esto podría resultar útil en el campo médico para la reducción del blindaje contra el estrés. Este efecto ocurre cuando los implantes de metal son demasiado densos, lo que hace que un hueso pierda su fuerza. La protección contra el estrés también podría reducirse cambiando las propiedades mecánicas del implante con la ayuda de la impresión 3D de múltiples materiales.
Sin embargo, antes de que se desarrollen nuevas aplicaciones, creo que debe haber un impulso tecnológico para mostrar las capacidades similares a las capacidades actuales de la fabricación aditiva.
¿Qué le depara el futuro a Aconity3D?
Continuaremos ampliando el alcance de los materiales aplicables que, al igual que los multimateriales, nos permitirán ofrecer nuevas aplicaciones para nuestros socios industriales. Queremos profundizar en las aplicaciones de series especializadas.
Entendemos que con aplicaciones de nicho, puede ser realmente difícil calificar nuevos materiales, especialmente cuando es solo para un cliente. Sin embargo, nuestro pan y mantequilla es asegurar que nuestros clientes estén satisfechos y puedan explotar las aplicaciones que tienen en mente.
En última instancia, queremos ser el facilitador de la innovación para nuestros clientes.
Para obtener más información sobre Aconity3D, visite: aconity3d.com
Impresión 3d
- ¿Cómo pueden las empresas aeroespaciales llevar la fabricación aditiva al siguiente nivel con MES?
- ¿Por qué las empresas deberían adoptar la fabricación aditiva distribuida?
- Entrevista con el experto:Pat Warner, especialista en fabricación aditiva del equipo Renault Formula One Team
- Entrevista con un experto:el profesor Neil Hopkinson, director de impresión 3D de Xaar
- Entrevista con un experto:Dr. Alvaro Goyanes de FabRx
- Entrevista con un experto:Dr. Bastian Rapp de NeptunLab
- Entrevista con el experto:Felix Ewald, director ejecutivo de DyeMansion
- Entrevista con un experto:Ibraheem Khadar de Markforged
- Mejora de la fabricación aditiva con ingeniería inversa
- Entrevista con el experto:James Hinebaugh de Expanse Microtechnologies
- Entrevista con el experto:Director ejecutivo de PostProcess Technologies sobre cómo resolver el cuello de botella de posprocesamiento para la fabricación aditiva