Aplicación destacada:Impresión 3D para implantes médicos
[Crédito de la imagen:Health Canada]
La creación de implantes óseos de mejor ajuste, mayor duración y rendimiento es una búsqueda constante tanto para los ortopedistas como para los cirujanos. La impresión 3D está contribuyendo enormemente a los avances en esta área.
La tecnología permite a los fabricantes de implantes crear implantes con una funcionalidad mejorada y más personalizados para las necesidades específicas de los pacientes. Además, la impresión 3D abre la puerta a implantes personalizados que se pueden crear en el punto de atención.
Esta semana, continuamos con nuestra serie 3D Printing Application Spotlight analizando el uso de la impresión 3D para implantes médicos, así como los beneficios y las aplicaciones actuales de la tecnología.
Eche un vistazo a las otras aplicaciones cubiertas en esta serie:
Impresión 3D para intercambiadores de calor
Impresión 3D para rodamientos
Impresión 3D para la fabricación de bicicletas
Impresión 3D para odontología digital y fabricación de alineadores transparentes
Cohetes impresos en 3D y el futuro de la fabricación de naves espaciales
Impresión 3D para la fabricación de calzado
Impresión 3D para componentes electrónicos
Impresión 3D en la industria ferroviaria
Gafas impresas en 3D
Impresión 3D para la producción de piezas finales
Impresión 3D para soportes
Impresión 3D para piezas de turbinas
Cómo la impresión 3D permite componentes hidráulicos de mejor rendimiento
Cómo la impresión 3D apoya la innovación en la industria de la energía nuclear
El mercado de la impresión 3D médica en 2019
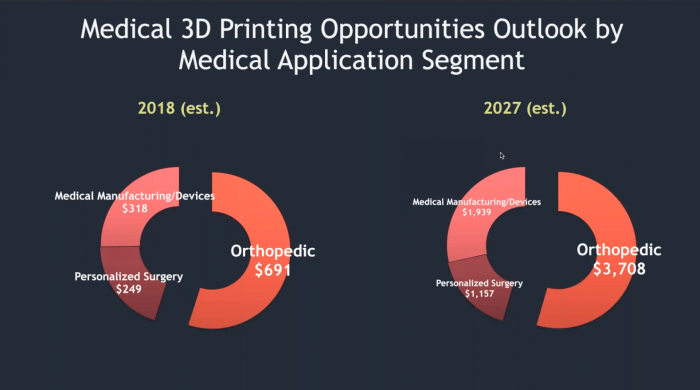
Los implantes ortopédicos, dispositivos médicos que se utilizan quirúrgicamente para reemplazar una articulación o hueso faltante, son solo una de las oportunidades que ofrece la impresión 3D a la industria médica.
El mercado de impresión 3D para ortopedia se valoró en $ 691 millones en 2018 y SmarTech Analysis prevé que crezca hasta convertirse en un mercado de $ 3.7 mil millones para 2027.
Aunque la fabricación de implantes es una nueva aplicación para impresión 3D - se utilizó por primera vez alrededor de 2007 - ha experimentado un rápido crecimiento durante la última década.
En 2010, uno de los primeros en adoptar la tecnología de impresión 3D de metal de fusión por haz de electrones (EBM) de Arcam recibió las primeras aprobaciones de la FDA para implantes impresos en 3D. Siete años después, más de 300 impresoras 3D de todo el mundo producían productos ortopédicos.
En la actualidad, la tecnología se utiliza para crear reemplazos de articulaciones de cadera y rodilla, implantes de reconstrucción craneal e implantes de columna. A partir de 2019, se estima que se producirán más de 600.000 implantes con la ayuda de la impresión 3D. Para 2027, esta cifra se prevé que supere los 4 millones.
Con una oportunidad de crecimiento tan grande, no sorprende que todos los principales fabricantes de dispositivos médicos estén adoptando cada vez más la tecnología de impresión 3D.
Stryker, una de las empresas de tecnología médica más grandes del mundo, ha lanzado recientemente sus propios implantes impresos en 3D, incluida la caja lumbar posterior curvada Tritanium TL impresa en 3D. Este implante de columna de cuerpo hueco recibió la aprobación de la FDA en marzo de 2018.
Junto a Stryker, otros fabricantes de dispositivos ortopédicos notables como DePuy Synthes, una subsidiaria de Johnson &Johnson, y Medtronic están invirtiendo fuertemente en la impresión 3D. Este último lanzó una plataforma de impresión 3D, TiONIC Technology, en mayo de 2018, con el objetivo de permitir diseños más complejos y tecnologías de superficie integradas para implantes quirúrgicos de columna.
Además de los fabricantes de dispositivos médicos establecidos, también han surgido nuevas empresas médicas durante la última década, desarrollando enfoques patentados para implantes ortopédicos impresos en 3D.
Entre ellas se encuentran empresas como Osseus Fusion Systems, Nexxt Spine, 4WEB Medical y SI-BONE. Algunos de los productos de estas empresas ya han recibido la aprobación de la FDA y se han utilizado para tratar pacientes con éxito.
Claramente, ha habido una trayectoria ascendente para los implantes impresos en 3D durante la última década. Pero, ¿qué hace que esta tecnología sea tan útil para los implantes médicos?
Los beneficios de los implantes impresos en 3D
Flexibilidad de diseño
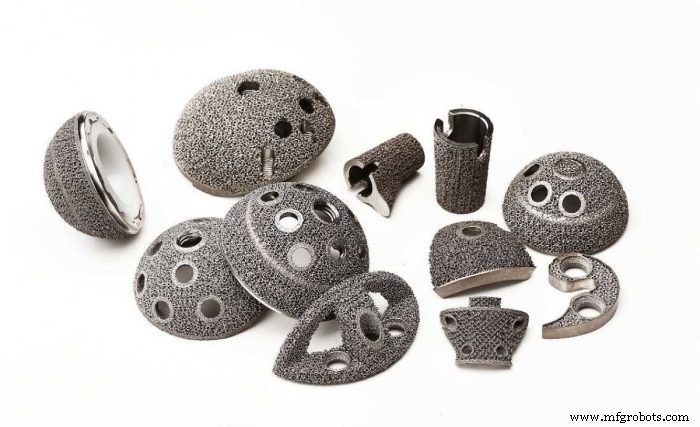
Con la impresión 3D, se pueden crear diseños complejos que de otro modo serían difíciles de lograr con las tecnologías tradicionales. Los fabricantes de implantes pueden utilizar este beneficio para producir implantes con intrincadas características de diseño, como estructuras trabeculares.
El hueso trabecular es uno de los dos tipos de tejidos óseos que se encuentran en el cuerpo humano. Tiene una estructura esponjosa y porosa que puede ser difícil de imitar en un implante. Tradicionalmente, los fabricantes de implantes utilizan un recubrimiento especial para crear una estructura trabecular en el implante. Sin embargo, esto conlleva el riesgo de delaminación y falla del implante.
Con la impresión 3D, por otro lado, los implantes con estructura trabecular se pueden producir directamente, sin pasar por el proceso de recubrimiento. Más importante aún, la estructura trabecular y porosa integrada en un implante impreso en 3D crea un implante más fuerte con un riesgo reducido de delaminación.
Tal flexibilidad de diseño es ofrecida por tecnologías de impresión 3D de metal como fusión láser selectiva o electrones. Fusión de vigas. Estas tecnologías aplican una poderosa fuente de energía como un láser (SLM) o un haz de electrones (EBM) en una capa delgada de un polvo biocompatible como el titanio.
Al repetir este proceso en cientos de capas, es posible crear un implante complejo que se adaptará a la estructura ósea humana de manera mucho más eficiente que los implantes fabricados tradicionalmente.
Otro beneficio significativo de los implantes porosos impresos en 3D es la mejora de la osteointegración.
La oseointegración es un proceso que permite que un implante se convierta en una parte permanente del cuerpo. La estructura trabecular porosa permite que un hueso crezca dentro de los poros, fortaleciendo aún más la unión entre el implante y el hueso existente.
Protección contra estrés reducido
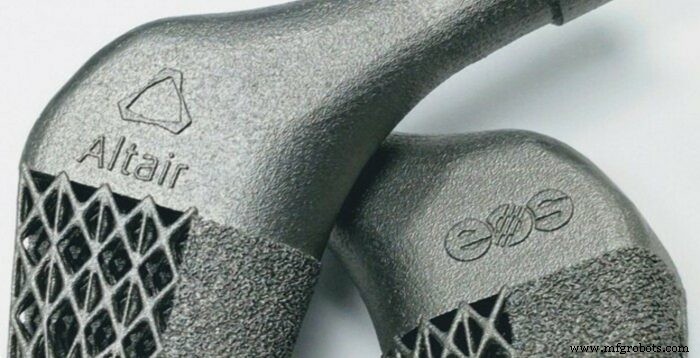
Además, los fabricantes de dispositivos médicos pueden diseñar implantes que imiten la rigidez y densidad ósea de un paciente. Además de mejorar la osteointegración, los implantes impresos en 3D pueden reducir la protección contra el estrés y mejorar aún más la función física.
La protección contra el estrés se refiere al fenómeno por el cual los implantes metálicos eliminan las tensiones típicas del hueso de un paciente. El resultado es la reducción de la densidad ósea, lo que hace que el hueso se debilite. La protección contra el estrés puede provocar fracturas y dislocaciones. Por esta razón, diseñar un implante lo más cerca posible del tejido óseo del paciente es clave para reducir la protección contra el estrés y eliminar estos efectos no deseados.
En un ejemplo reciente de esto, la empresa de TI Altair combinó la impresión 3D y el software de optimización de topología para crear un implante de vástago de cadera mejorado.
Al ingresar parámetros como el tamaño, el peso y la carga esperada que soportaría el implante, se utilizó un software de optimización de topología para crear un nuevo diseño para un implante de cadera. El diseño optimizado distribuye el estrés y la deformación de una manera más eficiente que un implante genérico.
Además, el software de optimización de topología ayudó a determinar dónde se podría reemplazar el material con estructuras de celosía para hacer el implante más liviano.
Cuando se probó, el implante optimizado ofreció una reducción de protección contra el estrés del 50,7%. Al mismo tiempo, su límite de resistencia aumentó a aproximadamente 10 millones de ciclos. Esto significa que el implante de cadera podría soportar trotar de Los Ángeles a Nueva York y viceversa, dos veces.
Impresión 3D de implantes específicos para el paciente
En casos más complejos, los implantes estándar a menudo no pueden proporcionar la flexibilidad necesaria requerida. La impresión 3D podría ayudar en tales casos, ya que ofrece la posibilidad de personalizar y personalizar los dispositivos médicos, incluidos los implantes.
Para producir un implante específico para el paciente, los fabricantes utilizan los datos adquiridos a partir de una exploración del paciente, como una tomografía computarizada (TC) o una exploración por resonancia magnética (MRI). Luego, los datos del paciente se importan a CAD, se preparan para la producción, se imprimen en 3D y se terminan.
El uso de un implante personalizado impreso en 3D ofrece la posibilidad de reducir el tiempo quirúrgico y mejorar el ajuste del implante.
Actualmente, la impresión 3D se puede utilizar para crear implantes craneales y maxilares personalizados donde los requisitos estéticos son tan importantes como la funcionalidad.
Por ejemplo, un niño chino de 10 años recibió un implante de mandíbula impreso en 3D en 2018. Tenía un tumor en la mandíbula que no podría haber sido extirpado sin causar una malformación facial significativa.
El equipo quirúrgico concluyó que una reconstrucción facial convencional era demasiado peligrosa para un paciente tan joven. Buscando una mejor solución, recurrieron a la impresión 3D, utilizando modelos digitales de la mandíbula del niño para diseñar un implante de titanio personalizado perfectamente adaptado.
Según los cirujanos, el implante de mandíbula era fácil de colocar ya que se basó en la anatomía del paciente. Tres meses después del procedimiento, la implantación resultó exitosa, con la mandíbula bien alineada y una gran cantidad de tejido creciendo.
3 ejemplos de implantes impresos en 3D
Un implante de cadera impreso en 3D permite escalar montañas extremas
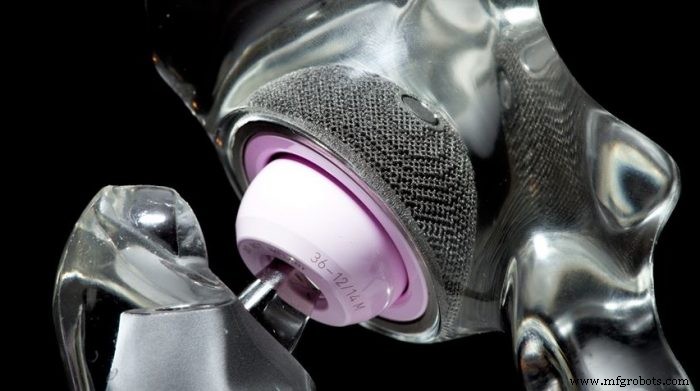
Romano Benet y su esposa, Nives Meroi, llevan muchos años escalando las montañas más peligrosas del mundo. En 2017, el equipo de montañismo se convirtió en la primera pareja en escalar los 14 picos más altos del mundo. Sin embargo, lograr esta hazaña probablemente habría resultado imposible sin la ayuda de la impresión 3D.
Benet sufría de necrosis avascular bilateral, que, esencialmente, conduce al colapso del hueso.
Cuando se les diagnosticó por primera vez, a Benet y su esposa les faltaban tres cumbres para completar el circuito mundial de las 14 montañas. Para continuar su viaje, el alpinista necesitaba un implante estable que le permitiera recuperarse rápidamente.
Por esta razón, el cirujano de Benet decidió optar por un implante impreso en 3D.
El implante, conocido con la marca de copa Delta Trabecular Titanium (TT), fue producido por la empresa italiana de dispositivos médicos, Lima Corporate, utilizando la impresora 3D EBM de Arcam.
Al combinar la tecnología Trabecular Titanium de Lima y la impresión 3D, fue posible crear implantes que imitaban la estructura porosa del hueso natural.
Gracias a esta estructura trabecular, un implante impreso en 3D puede soportar tensiones mecánicas durante una actividad rigurosa. El cirujano de Benet, que había implantado copas TT varias veces en otros pacientes, creía que, además de ofrecer una gran estabilidad y resistencia, los implantes impresos en 3D también tenían el potencial de durar más allá de la vida útil de los implantes convencionales.
Cuando Benet recibió su primer implante no impreso en 3D, había sufrido muchos meses de inactividad antes de comenzar a escalar de nuevo. Con un implante impreso en 3D, el alpinista pudo reanudar su actividad después de dos meses y medio.
Al final, el implante impreso en 3D hizo su trabajo:permitió a Benet recuperarse rápidamente y completar con éxito su búsqueda de alcanzar los últimos tres picos de gran altitud.
Osseus Fusion Systems:en camino hacia implantes metálicos personalizados

Fundada en 2012, Osseus Fusion Systems es una empresa con sede en EE. UU. que se centra en el desarrollo de productos médicos avanzados para lesiones relacionadas con la columna.
Para mejorar la calidad y funcionalidad de sus productos, Osseus ha desarrollado una tecnología de impresión 3D patentada llamada PL3XUS.
La tecnología se basa en la impresión 3D de fusión en lecho de polvo, específicamente la fusión selectiva por láser (SLM), y puede crear implantes de titanio poroso al 80%, optimizados para la fusión ósea y la fijación biológica (el proceso mediante el cual un hueso vivo se adhiere permanentemente a la superficie del implante).
En agosto de 2018, Osseus obtuvo la autorización 510 (k) de la FDA para Aries, su familia de dispositivos de fusión intersomática lumbar fabricados de forma aditiva. La familia de implantes Aries está diseñada para ayudar a los cirujanos a aliviar el dolor de espalda y reducir el tiempo de recuperación de la columna.
A principios de este año, Joseph Spine puso en práctica por primera vez el producto Aries de Osseus. un centro de cirugía de columna y escoliosis. La tecnología PL3XUS hizo posible diseñar el implante con una arquitectura similar a la del hueso de un paciente, lo que facilitó el crecimiento del hueso.
En los próximos años, Osseus planea lanzar dispositivos personalizados basados en tomografías computarizadas, radiografías y resonancias magnéticas del paciente.
Con este próximo paso, la compañía busca empoderar a los hospitales para brindar una atención superior al paciente y, en última instancia, mejorar aún más los resultados de la cirugía para los pacientes.
Implantes de impresión 3D con termoplásticos de alto rendimiento
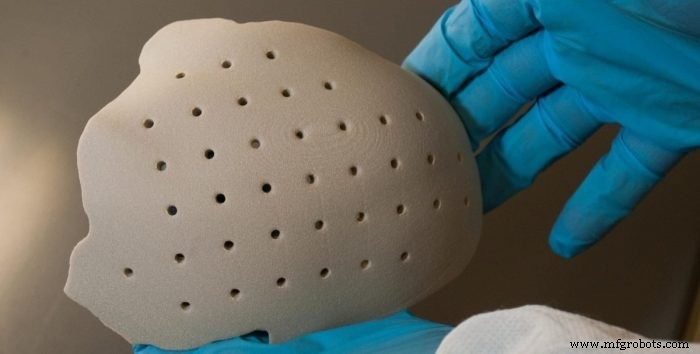
Además del titanio y otros metales biocompatibles, la impresión 3D se puede combinar con polímeros como PEEK y PEKK para producir implantes. Estos termoplásticos son conocidos por su alta resistencia y biocompatibilidad, y también ofrecen algunos beneficios sobre los implantes metálicos, como menores costos y radiolucidez.
En 2013, Oxford Performance Materials (OPM) se convirtió en la primera empresa en recibir la autorización de la FDA para un implante craneal PEKK impreso en 3D para pacientes específicos. Para 2017, OPM había enviado más de 1400 implantes craneales y recibió la autorización de la FDA para otros dos dispositivos:implantes maxilofaciales y espinales.
La empresa utiliza la tecnología de sinterización selectiva por láser, que impulsa la plataforma OsteoFab® patentada de OPM para el desarrollo y la producción de implantes. En un ejemplo, esta plataforma permitió diseñar, fabricar, probar y enviar un implante craneal específico para el paciente desde OPM en solo 3 días hábiles. En menos de una semana, los cirujanos realizaron la cirugía con éxito, sin realizar ningún corte o perforación para remodelar el implante.
Impresión 3D para implantes médicos:impactando
La biocompatibilidad, la capacidad de carga y la durabilidad son los requisitos fundamentales de los implantes ortopédicos. La impresión 3D cumple totalmente con estos requisitos al tiempo que mejora la funcionalidad y el ajuste de los implantes.
Esto se puede atribuir principalmente a la capacidad de la tecnología para crear formas complejas como estructuras porosas, que ayudan al cuerpo del paciente a adaptarse a un implante más rápido y con menos complicaciones.
En el futuro, la impresión 3D para implantes seguirá evolucionando. Un área particularmente interesante de investigación en curso es la combinación de implantes y sensores impresos en 3D. Al desarrollar implantes alimentados por sensores, los proveedores de atención médica pueden mejorar potencialmente los resultados de los pacientes de manera significativa.
Los sensores incorporados podrían recopilar datos como la temperatura alrededor del implante, el movimiento y la tensión que se ejerce sobre el implante. Esto permitirá a los cirujanos reaccionar a cualquier problema potencial desde el principio y adaptar el tratamiento a las necesidades de cada paciente.
Renishaw, un fabricante británico de impresoras 3D de metal, y Western University ya han establecido el Centro de Diseño Aditivo en Soluciones Quirúrgicas (ADEISS) en el campus de la universidad. El centro reúne a académicos y médicos para trabajar en el desarrollo de nuevos dispositivos médicos impresos en 3D como los descritos anteriormente.
Claramente, la tecnología de impresión 3D está ganando terreno dentro del segmento de la ortopedia.
Sin embargo, la tecnología deberá madurar para realmente desbloquear su potencial para implantes creados a medida producidos en el punto de atención.
Es cierto que solo un pequeño porcentaje de los implantes se crean actualmente a medida con impresión 3D. Si bien la tecnología tiene un gran potencial, aún deben abordarse las preguntas sobre la estandarización y la regulación.
Dicho esto, la creación de implantes médicos personalizados es donde la tecnología podría tener el mayor impacto y permitir que más personas se beneficien de la atención médica personalizada. Creemos que esta dirección verá una tracción significativa en los próximos años.
En nuestro próximo artículo, veremos cómo la impresión 3D puede mejorar la fabricación de cohetes. ¡Estén atentos!
Impresión 3d
- Polvos de micro tantalio para aplicaciones médicas
- Aplicación destacada:Impresión 3D para odontología digital y fabricación de alineadores transparentes
- Aplicación destacada:Impresión 3D para la fabricación de bicicletas
- Aplicación destacada:Impresión 3D para rodamientos
- Aplicación destacada:Impresión 3D para intercambiadores de calor
- Aplicación destacada:Impresión 3D en la industria ferroviaria
- Aplicación destacada:5 componentes electrónicos que pueden beneficiarse de la impresión 3D
- Aplicación destacada:Impresión 3D para calzado
- Aplicación destacada:Cohetes impresos en 3D y el futuro de la fabricación de naves espaciales
- Aplicación destacada:Gafas impresas en 3D
- 10 materiales más fuertes para impresión 3D