Entrevista con el experto:Pat Warner, especialista en fabricación aditiva del equipo Renault Formula One Team
Pat Warner es ADM Manager en Renault Sport Formula One Team, un especialista interno en fabricación de aditivos que trabaja para ofrecer componentes impresos de primera clase tanto para la creación de prototipos como para la producción. Después de haber estado profundamente involucrado en la fabricación aditiva dentro de la F1 durante más de 19 años, Pat ha sido testigo de una serie de desarrollos clave en la tecnología y sus aplicaciones, que tuvo la amabilidad de discutir con AMFG en la siguiente entrevista:
AMFG:¿Cómo se involucró originalmente en la fabricación aditiva?
Pat:Originalmente era un maquinista de CNC en el entonces Benetton Formula Team y me mudé al departamento de CAM en 1997. Compramos nuestra primera máquina SLA en 1998, pero realmente no sabíamos qué hacer con ella. La máquina se colocó en una habitación adyacente al taller de máquinas y se le dio la tarea de programación al grupo CAM. Para el año 2000, habíamos encontrado suficientes aplicaciones para PX de la máquina SLA para dos modelos más nuevos y más rápidos. En 2002, compramos dos más. En 2003, agregamos la sinterización láser al departamento y desde entonces nos hemos expandido gradualmente al departamento existente de nueve máquinas.
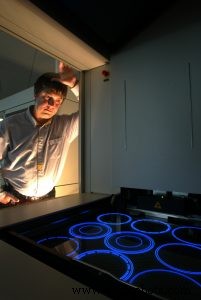
AMFG:¿Cuáles han sido algunas de las mayores historias de éxito de AM que haya presenciado durante su tiempo en Renault?
Pat:Ha habido tantos a lo largo de los años.
Hacemos un prototipo de cada componente nuevo del automóvil y lo ensamblamos para que funcione y se ajuste. Esto no es nada nuevo en el mundo de los aditivos, pero significa que podemos encontrar nuestros errores muy rápidamente. El embalaje de un automóvil de F1 moderno es un desafío para el equipo de diseño, ya que dejar espacio para que los mecánicos accedan a las partes del automóvil es algo difícil de lograr mirando una pantalla.
Fabricamos nuestros propios patrones de fundición a la cera perdida para nuestros componentes estructurales de titanio, como la carcasa de la caja de cambios. Hemos invertido mucho tiempo y esfuerzo en perfeccionar este proceso y, por lo general, terminamos con la fundición que usamos solicitando que nos compre patrones (en este punto, solo fabricamos componentes para el equipo).
Sin duda, la fabricación aditiva ha aumentado la tasa de desarrollo en los túneles de viento de la F1. Cuando trabajábamos sin restricciones en el túnel de viento, producíamos más de 600 piezas a la semana, solo para alimentar el túnel. La cantidad de recursos de fabricación convencionales necesarios para lograr el mismo objetivo sería inmensa.
Las rápidas plantillas y los accesorios han ayudado con la producción del coche y con las modificaciones de última hora en el circuito. En muchas ocasiones ha ocurrido encontrar un problema el viernes, hacer artículos de reemplazo y entregarlos en la pista a tiempo para que se ajusten para la calificación.
Por supuesto, también hemos tenido nuestros pequeños desastres, pero todos ayudan con el proceso de aprendizaje.
AMFG:¿Cuáles son los desafíos clave que ha experimentado cuando se trata de AM como herramienta tanto para la creación de prototipos como para la producción?
Pat:Nuevamente, ha habido tantos.
Cuando empezamos con él, la longevidad de la pieza era un gran problema, los materiales SLA eran muy frágiles y no se adaptaban bien a la humedad. Si pudiera mantener una pieza en su escritorio durante una semana sin que alguien la rompa, se distorsionaría al absorber la humedad del aire. El desarrollo de materiales se ha ocupado de estos problemas y ha realizado grandes mejoras a lo largo del camino.
Cuando comenzamos a comprar componentes de proveedores externos, descubrimos que rara vez obtendría la misma pieza dos veces, incluso si provenía de la misma construcción, en algunos casos. Esto nos animó a incorporar más recursos internos, dedicar más tiempo a comprender el equipo y los materiales y perfeccionar nuestros procesos. En 2004, nos asociamos con Boeing. Esta asociación nos ayudó a ambos en ese camino y nos ha llevado a poder poner más componentes en nuestros vehículos. Hemos desarrollado materiales específicamente para nuestras necesidades, que están disponibles comercialmente (las regulaciones de la FIA dictan que deben estarlo) y se están utilizando en otros lugares.
La educación también ha sido un desafío, aunque la tecnología existe desde hace bastante tiempo, su adopción en la fabricación convencional ha sido gradual, al igual que la educación. Como resultado de esto, todavía tenemos nuevos diseñadores que no han estado expuestos a la fabricación aditiva.
AMFG:¿Qué nuevas innovaciones le gustaría ver en términos de plataformas y materiales de impresión?
Pat:Ambas áreas han avanzado mucho en los 19 años que he estado involucrado, pero aún hay más margen para que la tecnología madure. Todavía tenemos que prestar mucha atención a nuestros procesos para lograr los resultados que requerimos y todavía vemos inconsistencias en algunos de los componentes que compramos. Algunas de estas inconsistencias podrían estar en el equipo que utilizamos, pero recientemente se han tomado buenos pasos en esta área, algunos están en la forma en que los proveedores utilizan dichos equipos y reciclan los materiales. Sin embargo, no se trata solo de plataformas y materiales; también necesitamos mejores herramientas de diseño para AM.
Todos hemos visto las estructuras huecas ligeras con celosía en el interior. Esto debería ser perfecto para los deportes de motor y la industria aeroespacial, pero en realidad, no podemos predecir los mecanismos de resistencia, rigidez y falla de dichos componentes lo suficientemente bien como para poder utilizarlos en todo su potencial.
AMFG:¿Cómo cree que evolucionará el uso de AM dentro de la F1 en los próximos años?
Pat:Estamos encontrando nuevas aplicaciones todo el tiempo. A medida que aumente aún más el tamaño de la caja de herramientas, también lo hará el número de aplicaciones.
Los metales están dando grandes pasos cada año, al igual que los polímeros de alta temperatura. A medida que avancen más y comprendamos mejor cómo usarlos, podremos obtener mucho más de las piezas de AM.
Es un momento muy emocionante para AM, está ganando mucha atención y financiación. Esto solo puede ser bueno para toda la industria, ya que aún queda mucho camino por recorrer antes de que podamos desafiar por completo la fabricación convencional.
www.renaultsport.com
Impresión 3d
- Reconsideración del proceso de integración de software para operaciones de fabricación aditiva
- Entrevista con el experto:Felix Ewald, director ejecutivo de DyeMansion
- Entrevista con un experto:Ibraheem Khadar de Markforged
- Entrevista:Dominic Parsonson de Fuji Xerox Australia
- Entrevista con el experto:James Hinebaugh de Expanse Microtechnologies
- Entrevista con el experto:Director ejecutivo de PostProcess Technologies sobre cómo resolver el cuello de botella de posprocesamiento para la fabricación aditiva
- Entrevista con el experto:Doug Hedges, presidente de Sintavia, sobre cómo lograr la producción en serie con la impresión 3D en metal
- Entrevista con el experto:Brian Alexander de Solvay sobre el desarrollo de polímeros de alto rendimiento para la impresión 3D
- Entrevista con el experto:Rush LaSelle de Jabil sobre el futuro de la fabricación aditiva
- Entrevista con el experto:Nanci Hardwick, CEO de MELD Manufacturing, sobre cómo alcanzar el potencial de la fabricación de aditivos metálicos
- Fabricación aditiva en la industria aeroespacial