Combinación de plásticos y compuestos para piezas de Clase A sin herramientas
Producir piezas compuestas con un acabado de clase A no es el Santo Grial; hay muchas empresas que lo hacen de forma rutinaria. Sin embargo, al hacerlo utilizando infusión de resina sin herramientas caras o gelcoats y a razón de una parte por hora? Bueno, eso es algo único.
De plásticos a compuestos
Plastics Unlimited fue fundada hace 25 años por Terry y Nancy Kieffer, explica su hijo Dakota Kieffer, director de ventas y marketing de la empresa. “Eran agricultores en Iowa y habían comenzado a buscar una industria nueva y en crecimiento”, explica. “Pensaron que los plásticos serían mejores que la soldadura o la carpintería y no querían competir con sus vecinos. Miraron el moldeo por inyección, el moldeo rotacional y el reciclaje de plásticos, pero luego se encontraron con el termoformado y realmente lo entendieron ". (El termoformado utiliza calor y vacío / presión para dar forma a las láminas termoplásticas en piezas moldeadas).
Luego, los padres de Kieffer entraron en contacto con una empresa que fabricaba piezas de plástico reforzado con fibra de vidrio (FRP). “Vieron lo fuerte que era el FRP, pero también que requería un proceso largo de varios pasos, aproximadamente cuatro horas por pieza, por lo que solo se producían dos piezas por día”, continúa. “En comparación con nuestra producción de plásticos, consideraron que era demasiado lento. Estábamos torneando piezas cada 2 a 6 minutos, tal vez incluso produciendo de 5 a 6 piezas a la vez, por lo que miles de piezas por día ". Para cerrar la brecha, al padre de Kieffer se le ocurrió la idea de usar una carcasa de plástico termoformado como herramienta .
El resultado es un proceso de fabricación de piezas compuestas sin herramientas, que Plastics Unlimited denomina Compuesto de ingeniería sin herramientas (TEC). "Elimina el gelcoat y pasos de liberación de la herramienta ”, dice Kieffer. “Además, cuando termoforma, puede inspeccionar la superficie de Clase A y asegurarse de que sea perfecta”. En otras palabras, la superficie de Clase A no está oculta debajo de un laminado compuesto. "Todo lo que se necesitaba era una sola herramienta de termoformado, y el proceso aún tenía sentido para nuestros clientes de piezas de plástico".
Proceso compuesto patentado
Kieffer señala que un compuesto combina dos materiales para hacer un material mejor que cualquiera de los componentes por sí solo. "Estamos combinando dos tipos diferentes de materiales y dos procesos diferentes para hacer un mejor producto". En particular, un producto que comprende plástico, resina y fibra de vidrio para ofrecer una combinación única de beneficios. “Los plásticos se comportan mucho mejor en impacto que los gelcoats”, explica. “También es posible imprimir cualquier textura o diseño en el plástico, por ejemplo un patrón de camuflaje. Los plásticos también ofrecen mucha profundidad de imagen sin pulir posteriormente, lo que elimina las operaciones de acabado secundario ”.
Mientras tanto, en comparación con la pulverización de fibra cortada en un proceso de moldeo abierto, esta tecnología patentada permite un mayor contenido de fibra, mayor calidad y compuestos orgánicos volátiles (COV) bajos o nulos. Señala que la pulverización de fibra cortada sobre plásticos para bañeras y spas no está patentada. “Siempre usamos la infusión al vacío para hacer que el FRP sea parte del producto”, dice Kieffer, y agrega que “nuestras piezas tienen un acabado suave, por lo que somos más un RTM ligero con placas de calafateo. Siempre lo llevamos al siguiente nivel. Los clientes acuden a nosotros con un problema y tratamos de encontrar una solución que se adapte a sus necesidades. Somos muy innovadores y patentamos nuestros nuevos desarrollos ”.
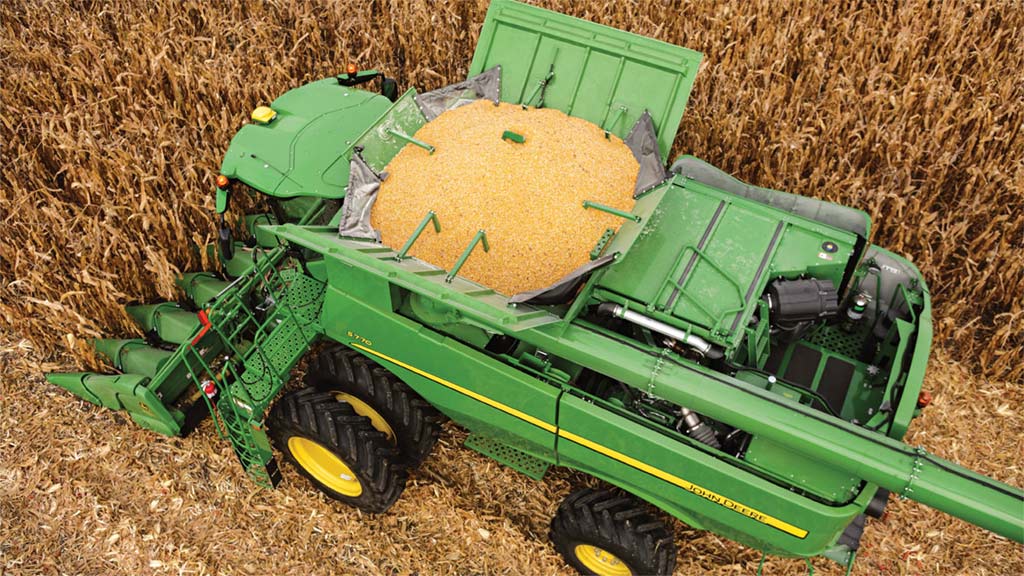
Partes de ejemplo
Una de las piezas que Plastics Unlimited produce mediante este proceso es una extensión del tanque de grano para las cosechadoras John Deere fabricadas por Deere &Company (Moline, Ill. EE. UU.). "Esta es la parte superior de la cosechadora, que está abierta, donde se asienta el grano", explica Kieffer. “Comparado con el tanque de acero original, el nuestro es más duradero. Lo hacemos con un acabado liso en el interior y verde John Deere en el exterior con inserciones negras en las esquinas. Es la extensión de tanque de grano más grande disponible y se puede plegar. Es un producto más diseñado en comparación con nuestros competidores, con espuma y nervaduras agregadas para aumentar la rigidez ". También se requiere algo de refuerzo de acero, que en realidad está moldeado, dice Kieffer, "no adherido de forma secundaria".
Esta combinación de materiales y proceso confiere mucha tenacidad a la pieza terminada. “Tenemos videos de cómo se arrojan bloques de concreto en estas partes”, dice Kieffer. Al moldear accesorios de acero, dice que la resistencia a la extracción puede ser de 4 a 5 veces mayor que la que se logra con la unión secundaria utilizando adhesivos de metacrilato de metilo estándar de la industria.
Plastics Unlimited puede fabricar hasta 2500 de estas piezas por mes, y algunos de los paneles miden 5 pies por 7 pies. “Esto requeriría herramientas costosas, si no se fabricaran con nuestro método”, dice Kieffer, señalando que TEC se puede usar para piezas bastante grandes, de hasta 8 pies por 11 pies. “Nuestras piezas pueden tener más forma y geometría que el acero. Esto es importante para nuestros clientes porque les permite diferenciarse mediante el estilo. Nuestra resistencia a los rayos UV también es mejor que la mayoría de los gelcoats ”.
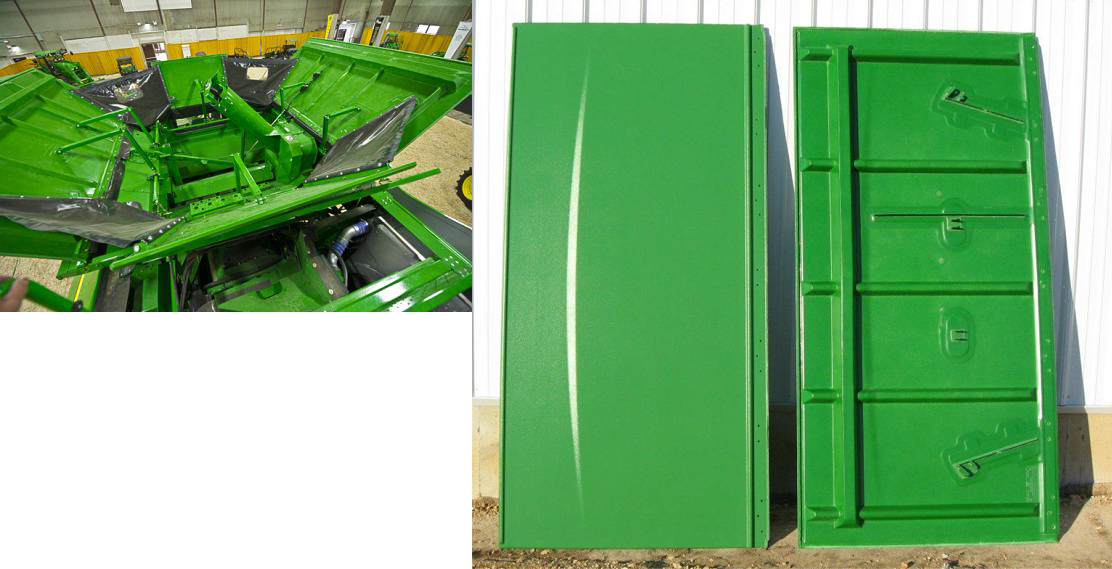
Plastics Unlimited suministra piezas para una amplia gama de empresas, incluidas las elevadoras telescópicas Harley-Davidson y Gehl. “También fabricamos piezas suaves al tacto que se ven y se sienten como cuero”, dice Kieffer. La empresa también ha fabricado componentes de camiones para Navistar y piezas de vehículos recreativos (RV) para Winnebago. "Preferimos la producción en volumen, desde 100.000 piezas por año hasta unos pocos cientos".
Kieffer reconoce que la inyección de fibra larga (LFI) y el moldeo por inyección de resina (RIM) son procesos competitivos, “pero las piezas no son tan estructurales como lo que hacemos. Por ejemplo, un tanque de grano combinado tiene capacidad para 400 bushels, lo que ejerce 10 toneladas de fuerza. Las piezas de RIM, que no están muy reforzadas, simplemente no pueden cumplir con este tipo de requisito de carga y las herramientas de RIM son muy caras ".
Desarrollo continuo
“Hacemos mucho trabajo de I + D con nuestros clientes”, dice Kieffer. “Exploramos diferentes resinas, espumas, laminados, capas de refuerzo y acabados, y luego les mostramos prototipos para que puedan hacer pruebas muy rápidamente. Intentaremos hacer que la pieza sea más fácil de fabricar, buscando cómo reducir los costos y mejorar el rendimiento, además de cumplir con los diversos requisitos en servicio, como las temperaturas extremas de frío y calor y el impacto ”.
Plastics Unlimited tiene 100.000 pies cuadrados de espacio de producción y 75 empleados, incluido un equipo de tres ingenieros. Su máquina CNC Thermwood de 5 ejes permite la producción interna de herramientas y también la creación rápida de prototipos, esta última importante para los clientes que buscan acortar los plazos de desarrollo.
“También estamos trabajando con empresas aeroespaciales y de transporte público”, continúa. “Muchos de los interiores del metro son actualmente de FRP con gelcoat más estructura de aluminio detrás. Necesitan un acabado superficial ligero pero también cosmético. Estamos analizando una amplia gama de aplicaciones, incluidas las médicas, eléctricas y de construcción ".
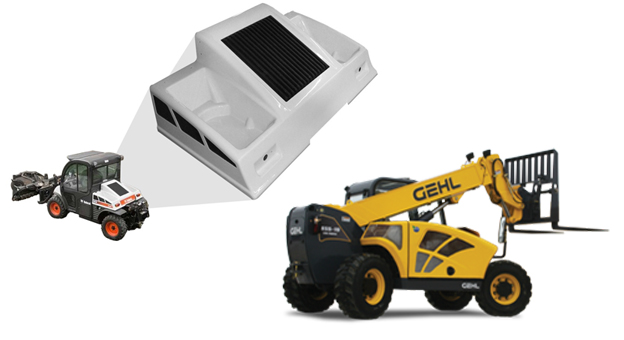
La empresa también está estudiando el termoformado de plásticos reforzados con fibra de carbono (CFRP). “Hemos formado materiales Tepex y Polystrand y estamos trabajando en varios desarrollos con un cliente médico”, dice Kieffer. “Podemos usar materiales plásticos de alta calidad como Kydex y respaldarlo con CF / epoxi para la industria aeroespacial, o materiales como poliuretano, policarbonato y ABS, que brindan un acabado exterior agradable y son rentables. Detrás de estos últimos plásticos podemos utilizar laminados de poliéster, viniléster o epoxi reforzados con fibra de vidrio ”.
Plastics Unlimited opera en la intersección de plásticos, metales y compuestos, dice Kieffer. “Nuestras piezas suelen ser entre un 30 y un 40 por ciento más ligeras que el acero. Pero encontramos que el mercado todavía necesita bastante educación sobre qué son los compuestos y qué pueden hacer ". De todos modos, la empresa ve un gran potencial de crecimiento futuro. “No todos los materiales funcionan juntos y, especialmente, no todas las resinas funcionan con todos los plásticos”, señala. “Hemos realizado tantas pruebas y desarrollo a lo largo de los años que comprendemos muy bien el panorama y las posibilidades. Tenemos una experiencia única y ofrecemos una gama única de posibles soluciones ".
Resina
- Kubernetes en Azure:herramientas y sugerencias para el éxito
- Patrones de programación y herramientas para Cloud Computing
- TPE de "tacto suave" para requisitos de diseño de piezas y embalaje emergentes
- Piezas de brazo robótico para automatización de selección y colocación
- Personalización de sensores ultrasónicos para la optimización y el control de procesos compuestos
- Resinas epoxi reprocesables, reparables y reciclables para composites
- Combinación de medidas dieléctricas de CA y CC para el control del curado de compuestos
- Victrex y Bond se asocian para la impresión 3D de piezas PAEK
- 20 herramientas y equipos básicos de soldadura para principiantes
- Procesos de acabado de piezas y componentes
- MANTENIMIENTO DIARIO Y PERIÓDICO PARA TRANSPORTADORES Y PIEZAS