Las aeroestructuras primarias termoplásticas dan un paso más
Las características ventajosas de los compuestos termoplásticos, como la tenacidad, la resistencia fuera del plano comparativamente alta y la sostenibilidad / reciclabilidad, han atraído el diseño de aviones. ingenieros a la noción de estructuras primarias de compuestos termoplásticos durante décadas. Pero la fabricación de aviones Los ingenieros no estaban seguros de encontrar una manera rentable de hacerlos avanzar desde la simulación CAD al piso de producción. Sin embargo, no se ven disuadidos:los esfuerzos para desarrollar las tecnologías de fabricación necesarias han continuado en todo el mundo, quizás en ningún lugar con tanta tenacidad como en los Países Bajos.
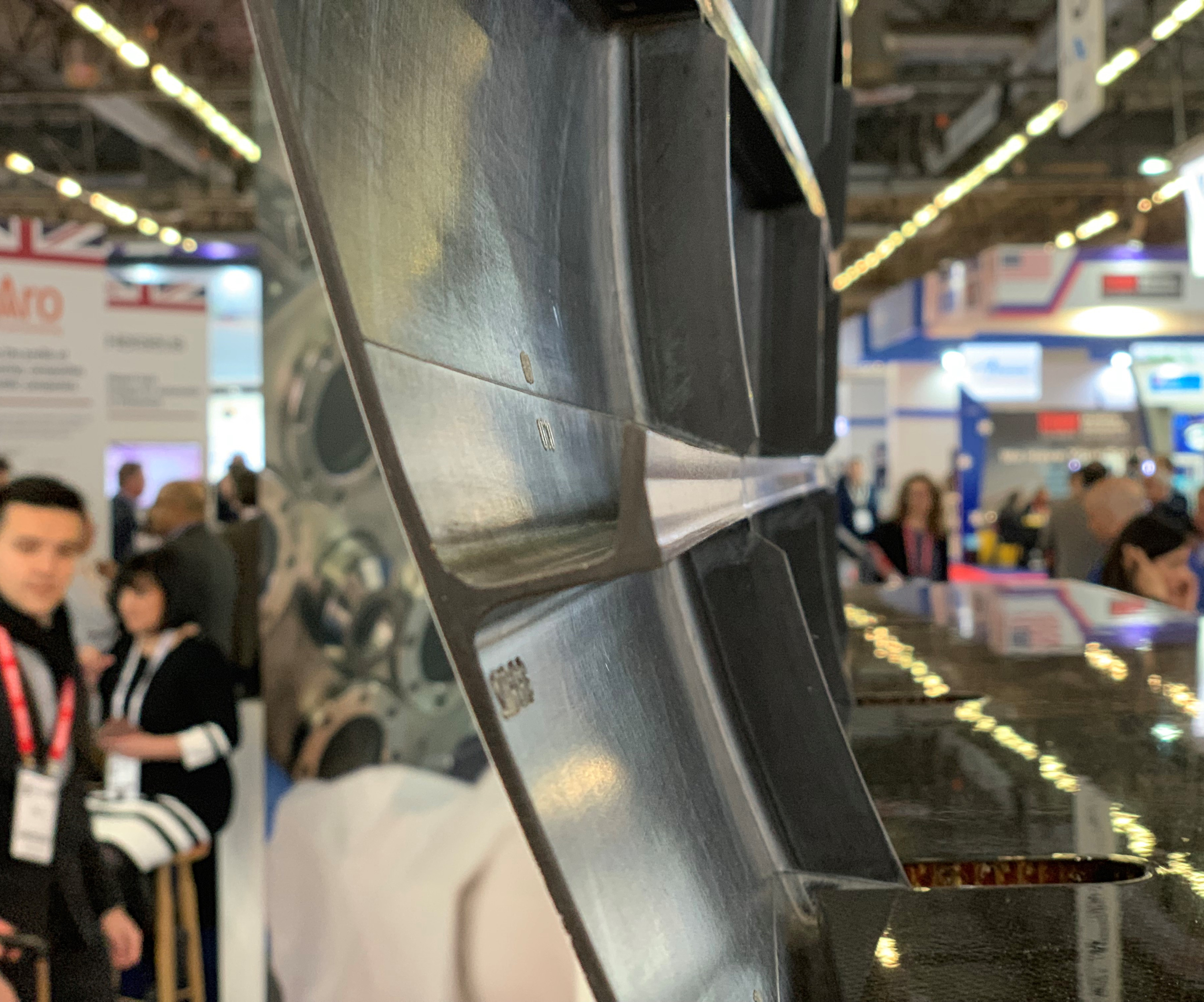
Largueros en L integrales. El fuselaje de fibra de carbono / PEKK GKN Fokker, diseñado y construido para Gulfstream, incorpora largueros en L longitudinales curvos con un ángulo ligeramente obtuso para permitir la liberación de la herramienta. CW foto | Jeff Sloan
En 2009, nueve empresas industriales e institutos de investigación holandeses, junto con Airbus (Toulouse, Francia), formaron el Consorcio Termoplástico Asequible de Estructura Primaria de Aeronaves (TAPAS). La iniciativa se expandió a 12 socios en 2014 y continuó como TAPAS2. Dirigido a aplicaciones desarrolladas por Airbus bajo TAPAS2, GKN Fokker (Hoogeveen, Países Bajos) desarrolló recientemente un demostrador de fuselaje utilizando lo que llama una "tecnología de ortogrid unidas a tope" que permite la producción rentable de un diseño de fuselaje compuesto termoplástico.
La rentabilidad total de una estructura de aeronave primaria compuesta termoplástica, aunque todavía faltan años, puede estar ahora a la vista, ya que Gulfstream Aerospace (Savannah, Ga., EE. UU.) Se ha asociado con GKN Fokker para avanzar en su tecnología de fuselaje TAPAS2, señalando el camino hacia la posible aplicación. los materiales y el proceso a un fuselaje completo. La historia detrás del panel de fuselaje recientemente desarrollado (que se mostró en JEC World a principios de este año) es uno de los avances en los métodos de diseño y fabricación y, además, en un enfoque de ingeniería de diseño y fabricación más completamente integrado.
“Tradicionalmente”, explica el ingeniero jefe de GKN Fokker, Andries Buitenhuis, “ya sea que usaran telas o cintas unidireccionales, los diseñadores se apegaban principalmente a capas convencionales de orientaciones de 0, 90 y 45 grados. Trabajarían desde sus mesas de capas de capas, independientemente de otras disciplinas ". El nuevo enfoque es una plataforma de software de fabricación y diseño integrada y digitalizada (desarrollada a través de TAPAS) en la que ingenieros de diversas disciplinas miran el mismo modelo digital y tienen la capacidad de conceptualizar diseños de piezas más complejos. “Esto abre un mundo completamente nuevo de posibilidades de optimización sin precedentes”, continúa Buitenhuis. “En formas complejas, las direcciones de las fibras pueden estar por todas partes. Podemos construir laminados no convencionales y echar un vistazo a los diseños permitidos, los huecos y superposiciones de fabricación, los radios…. Y puede optimizar la resistencia de la estructura localmente ". Estas opciones de diseño expandidas emplean de manera más completa la capacidad de dirección de fibra de las máquinas de colocación automatizada de fibra (AFP) y los avances en otras capacidades de fabricación que se analizan a continuación.
La libertad de diseño que ofrece este sistema digital integrado ha demostrado ser indispensable para el diseño y la fabricación de paneles para aviones comerciales. En los diseños de fuselaje TAPAS2, el panel de fibra de carbono / polietercetonacetona (PEKK) (fabricado con APC PEKK-FC de Solvay) presenta una unión de marco a piel soldada sin sujetadores, que es un factor esencial que contribuye a la rentabilidad del diseño. "Predecimos lograr la paridad de costos con las carcasas de fuselaje de aluminio", explica Arnt Offringa, director de tecnología de compuestos termoplásticos en GKN Fokker, "y esto se debe a que las carcasas de aluminio están remachadas". Se espera que la eliminación de los sujetadores mecánicos genere una reducción de costos del 20% y una reducción del peso del 10% en las estructuras primarias de las aeronaves en comparación con las soluciones compuestas convencionales. Por supuesto, gran parte de los ahorros en costos y peso provienen de la eliminación de los propios sujetadores, así como de los costos de mano de obra para instalarlos. También es de gran importancia la eliminación de orificios en los componentes compuestos para acomodar los sujetadores, orificios que requieren un refuerzo adicional y, por lo tanto, un peso adicional.
GKN Fokker alcanzó el nivel de preparación tecnológica (TRL) 3 (prueba de concepto) con Airbus para un fuselaje presurizado, demostrando la paridad de costos con los paneles del fuselaje de aluminio, bajo TAPAS2 en diciembre de 2017. En el camino, el equipo de GKN Fokker amplió su visión para este termoplástico tecnología de fuselaje, desde aviones comerciales hasta aplicaciones de aviones comerciales.
Interés de Gulfstream
El historial de trabajo exitoso de GKN Fokker para Gulfstream en componentes compuestos termoplásticos hizo de la asociación con el fabricante de aviones comerciales el siguiente paso lógico. "Es ampliamente conocido que Gulfstream ha estado volando piezas de compuestos termoplásticos durante años", dice Mark Chapman, gerente de la Iniciativa de Estructuras y Materiales Avanzados de Gulfstream (ASMI). Agrega que el proyecto del panel del fuselaje "es una progresión natural de lo que hemos estado haciendo, comenzando con partes más simples y avanzando hacia partes estructurales primarias". GKN Fokker se ha asociado con Gulfstream en el desarrollo de numerosos componentes secundarios de compuestos termoplásticos, incluidos los elevadores de cola y timones, así como los paneles del piso del G650.
En 2015, Offringa y Buitenhuis presentaron los desarrollos del proyecto TAPAS2 a Gulfstream, y Chapman y su equipo reconocieron el potencial para obtener los beneficios de los resultados de TAPAS2. “Vimos los beneficios potenciales de reducción de peso, mejor resistencia al impacto y dureza, y desempeño mejorado”, recuerda Chapman. El diseño sin sujetadores también es atractivo. "La tecnología de soldadura nos permitiría ensamblar el fuselaje de manera más eficiente" que un ensamblaje sujetado mecánicamente, dice Chapman.
La asociación con GKN Fokker respalda la investigación y el desarrollo de Gulfstream de formas de fuselaje más complejas que pueden no ser económicamente viables de producir con estructuras metálicas. “Hasta ahora, sólo se puede estirar el metal”, señala Chapman. “Los empalmes y la estructura de soporte necesarios para formas complejas no son muy eficientes”. Offringa está de acuerdo:"Estas geometrías complejas son difíciles de fabricar con tecnologías convencionales".
Uniendo diseño y fabricación
Para lograr un diseño producible sin sujetadores, el enfoque de GKN Fokker se centra en resistir las dos fuerzas clave a las que están sujetas las juntas del fuselaje:la presión de la cabina y los impactos, como las caídas de herramientas. La presión de la cabina ejerce una fuerza radial sobre el fuselaje, creando grandes cargas en la unión del marco con la piel. En los diseños convencionales, los marcos del fuselaje incluyen "agujeros de ratón" a través de los cuales pasan los largueros longitudinales. Bajo la fuerza de la presión de la cabina, estos agujeros de ratón sirven como discontinuidades que están sujetas a altas fuerzas de desprendimiento, una preocupación importante para un diseño sin sujetadores, dada la baja resistencia fuera del plano de los compuestos en comparación con los metales. Los impactos también generan cargas elevadas en la unión del marco con la piel porque el marco no se dobla bajo el impacto.
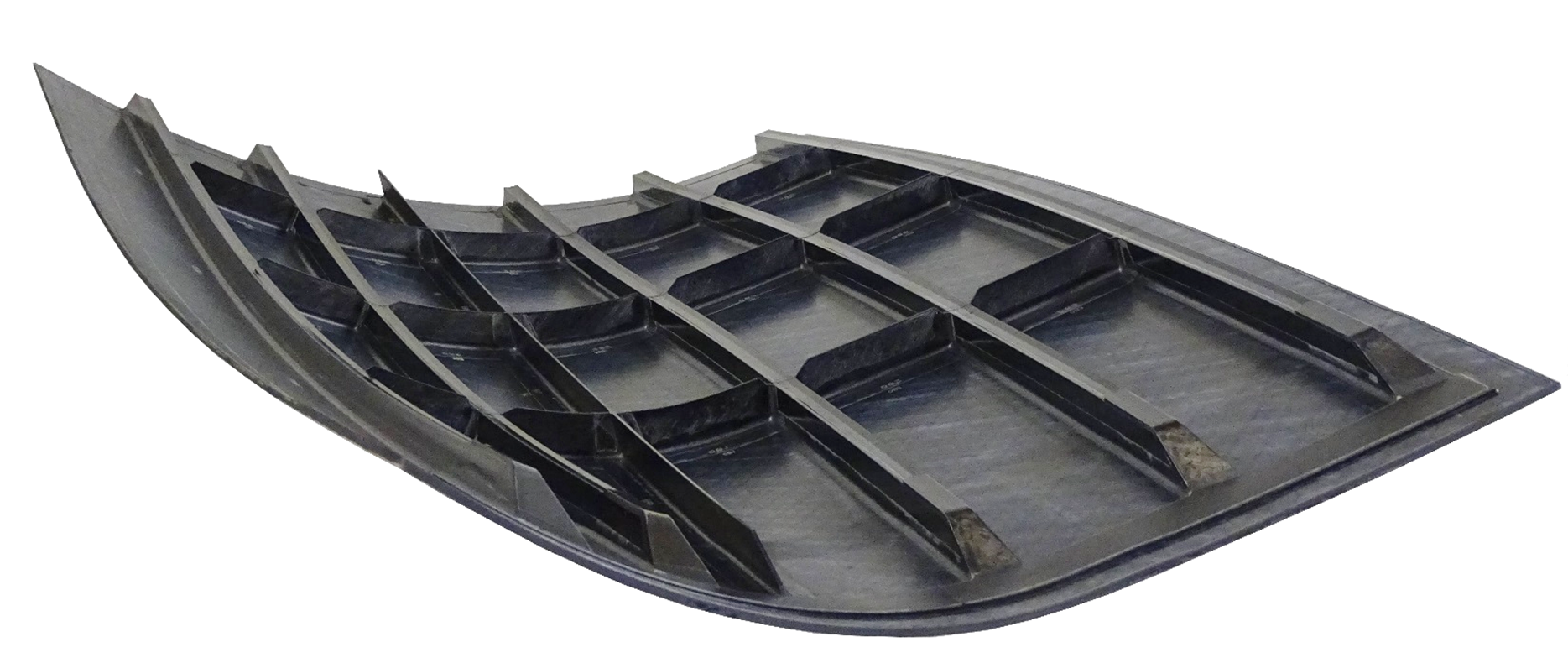
Doble curvatura. El panel de fuselaje de material compuesto termoplástico se adapta a la compleja geometría del fuselaje de popa de un jet de negocios Gulfstream con una capa de AFP dirigida por fibra de la piel y la co-consolidación de la ortogrid. Tenga en cuenta los largueros circunferenciales de la hoja, que luego se sueldan al marco. Fuente | GKN Fokker
El equipo de GKN Fokker / Gulfstream sabía que no era factible enfrentar los desafíos creados por una curvatura compleja, ya sea con metal o con enfoques convencionales de diseño y fabricación de compuestos. En particular, señala Buitenhuis, "un diseño de fuselaje complejo no sería posible sin dirección de fibra". Esta capacidad de las máquinas AFP es lo que liberó a los diseñadores para optimizar la orientación de la fibra localmente basándose en la forma compleja de la carcasa y para divergir de las opciones de orientación de fibra estándar 0/45/90. “La dirección de fibra para optimizar las formas y el peso es uno de los avances más importantes de este proyecto”, cree Chapman.
GKN Fokker hizo la piel del panel del fuselaje en una máquina AFP ultrasónica que la compañía desarrolló para la colocación rápida de cinta termoplástica. La cinta es unidireccional, lo que también mejora el rendimiento del laminado en comparación con las cintas de tela.
Manejando con éxito las altas cargas creadas por la presión de la cabina y las fuerzas de impacto, así como otras demandas de rendimiento, el nuevo concepto desarrollado bajo TAPAS y TAPAS2, y que ahora se emplea en el panel Gulfstream, es lo que se describe como una “junta a tope reforzada ortogonalmente piel con marcos soldados ". Al desembalar esta descripción se destacan tres características de diseño clave y los desarrollos de fabricación necesarios para implementarlas:(1) la ortogrid, (2) la junta a tope y (3) la tecnología de soldadura.
Orthogrid
Los requisitos de resistencia del panel se cumplen en parte mediante el refuerzo de la rejilla ortogonal completamente interconectada. Esta rejilla elimina las cargas máximas asociadas con los agujeros del ratón, eliminando el diseño de puntos en los que se magnifican las fuerzas de desprendimiento. La ortogrid consta de largueros longitudinales continuos y marcos que comprenden dos componentes distintos:largueros de cuchilla circunferenciales discontinuos pero conectados y marcos soldados en la parte superior de estos.
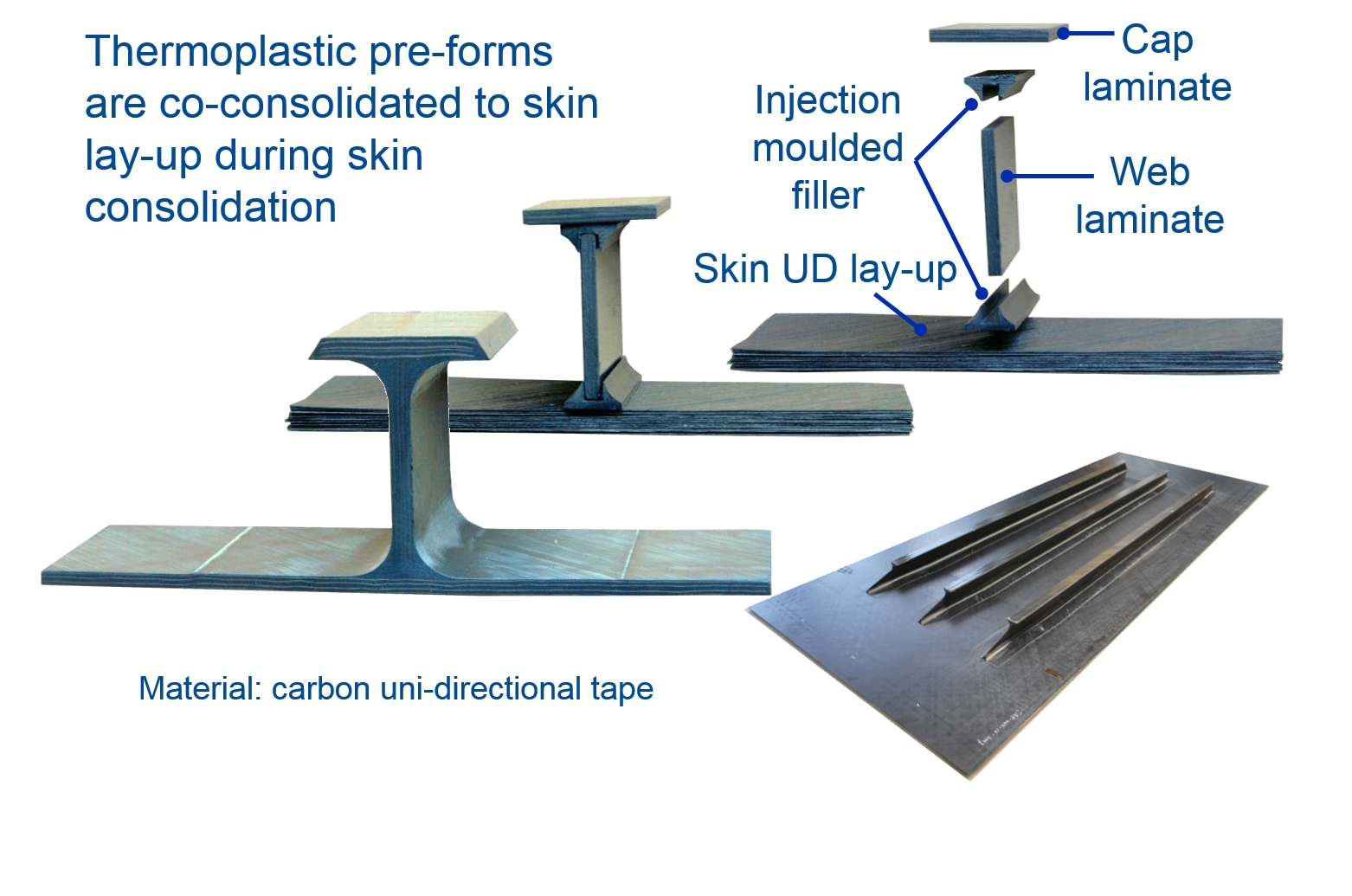
Articulación a tope rentable. GKN Fokker innovó y patentó una junta a tope que permite la unión entre la rejilla y la rejilla con la piel utilizando elementos rentables moldeados por inyección de fibra corta y laminados planos de fibra continua para la red y la tapa del larguero (aquí un larguero en T; el panel Gulfstream incorpora Largueros en L con la misma técnica). Fuente | GKN Fokker
Por lo tanto, esto representa una nueva generación en el diseño de refuerzos de fuselaje que ha evolucionado durante años de desarrollo de ortogrid. Inicialmente, GKN Fokker usó largueros en T en los que las tapas de los miembros longitudinales y circunferenciales eran continuas y se superponían en las esquinas. La unión con el marco, sin embargo, requirió la remoción de la tapa circunferencial. Por lo tanto, los largueros en T se convirtieron en largueros en L y los marcos se convirtieron en largueros de cuchillas circunferenciales con marcos que luego se soldaron a ellos.
Se requiere otra modificación porque los larguerillos curvos que se usan tanto longitudinalmente como circunferencialmente hacen que la liberación de la herramienta sea mucho más desafiante. Por lo tanto, los largueros en L están diseñados con un ángulo entre la tapa y la banda de más de 90 grados, de modo que las piezas de la herramienta siempre se puedan deslizar hacia los lados fuera de la rejilla del larguero.
Juntas a tope
GKN Fokker desarrolló no solo el diseño de la rejilla, sino también un nuevo enfoque de fabricación para la rejilla, así como el mecanismo de unión entre la rejilla y la piel. “La rejilla puede ser prohibitivamente cara de fabricar”, señala Offringa, “pero nuestra rejilla está formada por laminados planos y 'rellenos' simples moldeados por inyección”.
Más específicamente, GKN Fokker aplicó su tecnología patentada de juntas a tope al panel Gulfstream (también a los paneles TAPAS anteriores). La banda y la tapa de los componentes del larguerillo en T o L, así como los componentes del larguerillo de la cuchilla, se fabrican a partir de preformas cortadas con chorro de agua a partir de un laminado plano de fibra de carbono / PEKK. Los elementos de unión (piel a red y red a tapa) son un relleno en forma de pi moldeado por inyección hecho de un material de fibra corta de carbono / PEKK. Tanto la resina como el tipo de fibra de carbono coinciden con los de los miembros de la rejilla.
La piel y la rejilla se consolidan conjuntamente en una herramienta de línea de molde interno (IML) Invar. La herramienta presenta ranuras en las que se cargan los componentes de la ortorejilla y los bloques de herramientas. Luego, la piel formada por AFP se coloca sobre el IML y todo el conjunto se embolsa y se consolida en autoclave.
Soldadura
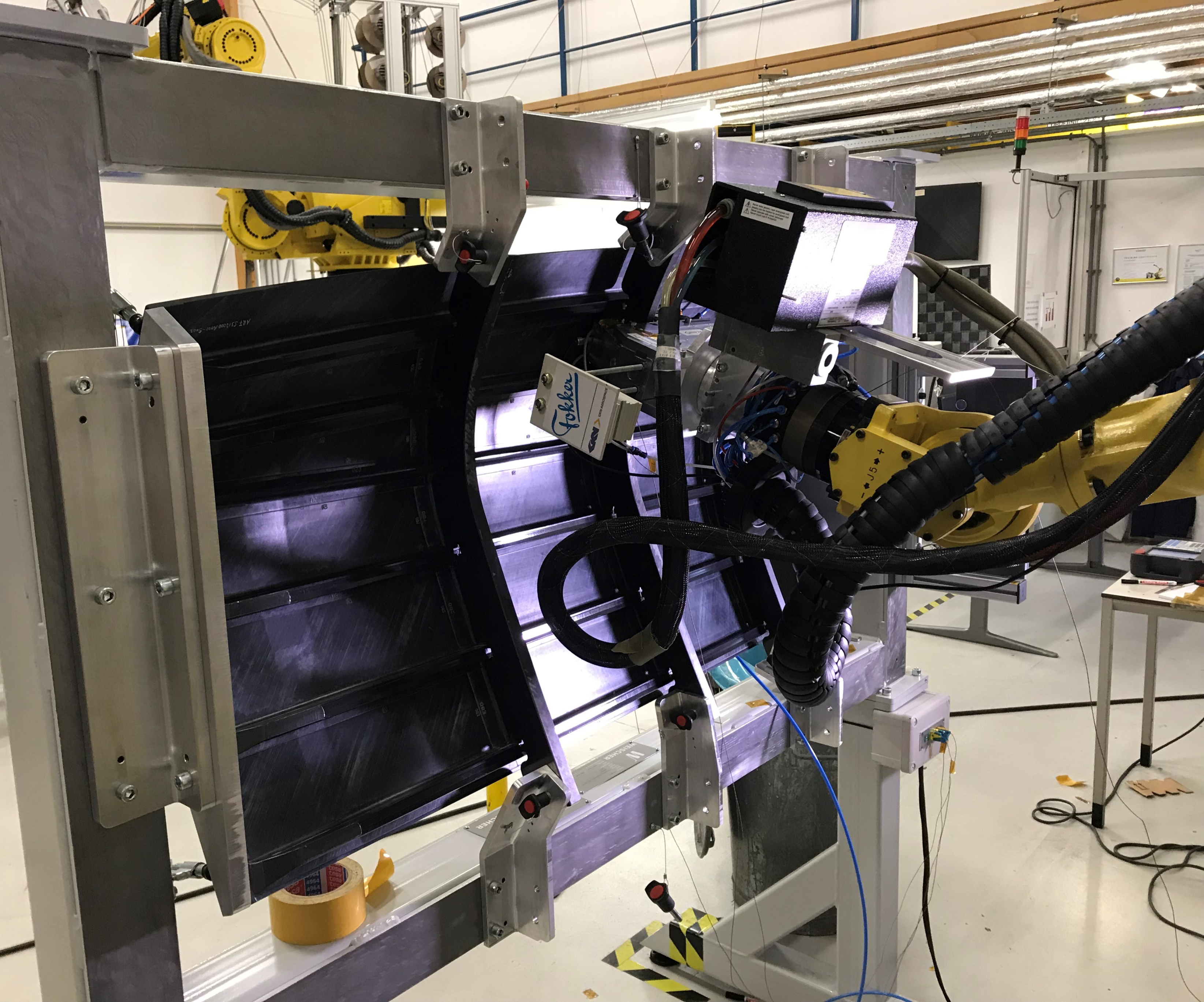
Soldadura automatizada. Contribuyendo a la viabilidad económica del panel de fuselaje compuesto termoplástico, GKN Fokker desarrolló y empleó una técnica de soldadura robótica. Fuente | GKN Fokker
La combinación del diseño de la ortogrid y la junta a tope permite una unión sin sujetadores de la ortogrid y el marco mediante soldadura. Los miembros del equipo de TAPAS desarrollaron varias tecnologías de soldadura durante la fase TAPAS2, incluidas tecnologías de soldadura por inducción, conducción y ultrasónica. El panel Gulfstream empleó soldadura por conducción para unir la red del marco al larguero circunferencial de la hoja. Esta tarea se realiza con el cabezal de soldadura montado en un robot, otro desarrollo que contribuye a una fabricación rentable.
Un paso de varios
GKN Fokker comenzó su colaboración con Gulfstream en 2017, creando conceptos de diseño para el panel del fuselaje. El diseño y la fabricación de varios paneles curvos siguieron en 2018 y 2019, y el primer demostrador de panel histórico se exhibió en el JEC World de este año.
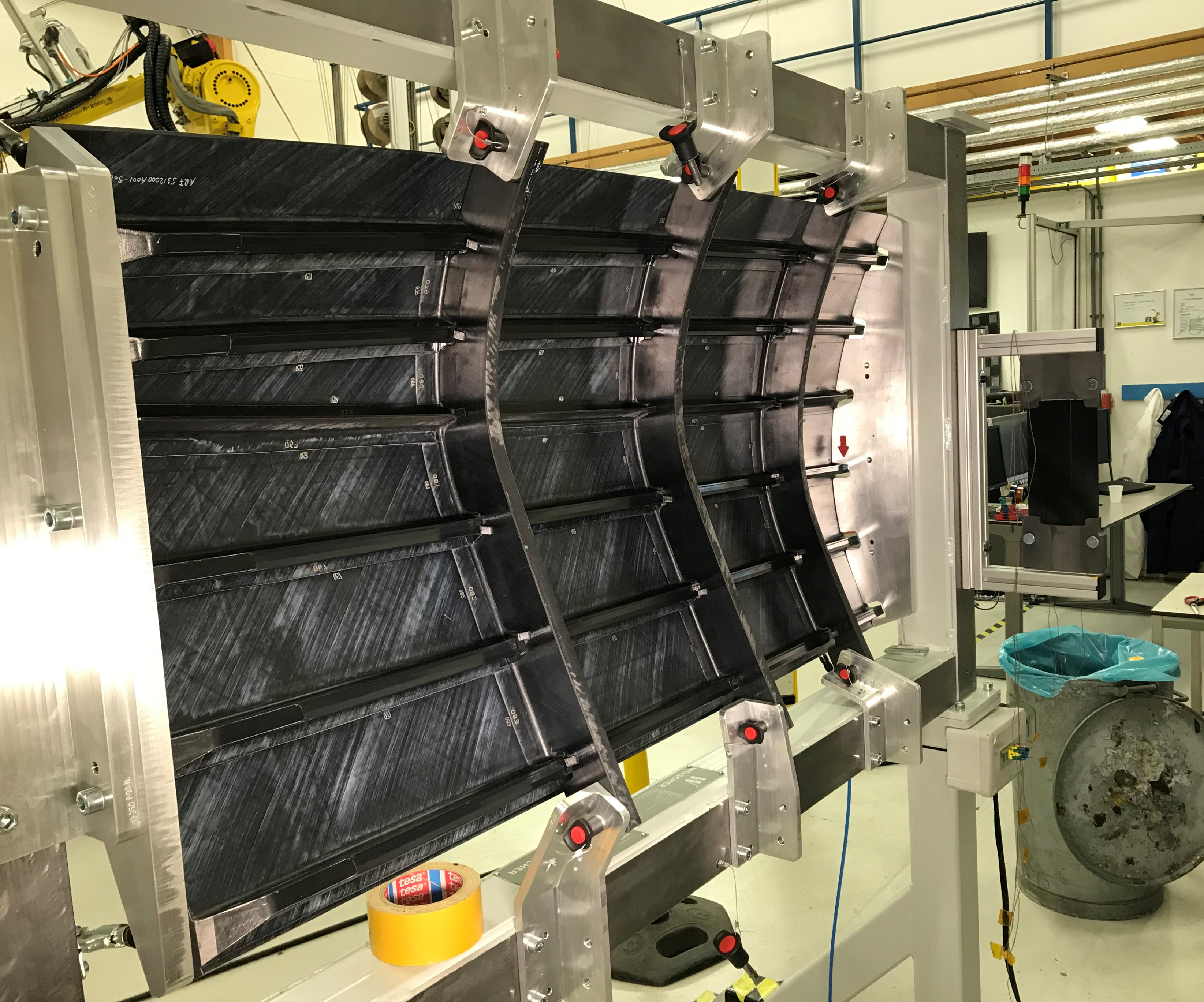
Componente completado. Con los elementos del marco soldados a los largueros circunferenciales de las palas, el panel de fuselaje Gulfstream está listo para pruebas, evaluación y desarrollo continuo mientras las empresas trabajan en la producción de fuselajes compuestos termoplásticos. Fuente | GKN Fokker
GKN Fokker continúa construyendo paneles y espera lograr TRL4 (validación de componentes) a finales de este año. “Actualmente estamos discutiendo el camino a seguir hacia la madurez total”, informa Offringa. Al señalar que el diseño del panel no apunta a una plataforma en particular, Chapman informa que las pruebas del panel ayudarán a profundizar la comprensión de Gulfstream sobre las propiedades y el rendimiento de los materiales. Con respecto al caso comercial más amplio de las estructuras primarias de compuestos termoplásticos, incluido el rendimiento del avión, el costo de fabricación, el costo de uso y la durabilidad, Chapman comenta:“Obtendremos una mejor comprensión de estos a medida que avancemos en el camino de la investigación y el desarrollo. Por ahora, nuestro objetivo es hacer que estas formas complejas sean rentables ".
Resina
- Covestro intensifica la inversión en compuestos termoplásticos
- Lanzamiento de masterbatches termoplásticos reforzados con grafeno
- Solvay expande la capacidad de compuestos termoplásticos
- Las negociaciones sobre tarifas dan otro giro
- Compuestos termoplásticos en Oribi Composites:CW Trending, episodio 4
- El Instituto de Estructuras y Diseño DLR aumenta la madurez de las estructuras de fuselaje de compuestos termoplásticos
- Suprem expande las capacidades termoplásticas
- Las cintas termoplásticas continúan mostrando potencial para aeroestructuras compuestas
- Soldadura de compuestos termoplásticos
- Los diseñadores deben aprovechar las tendencias de la industria de fundición a presión
- Consejos de diseño para moldeo por inyección