El Instituto de Estructuras y Diseño DLR aumenta la madurez de las estructuras de fuselaje de compuestos termoplásticos
Como parte del proyecto “LuFoV-3 TB-Rumpf”, la consolidación sin autoclave de laminados preimpregnados termoplásticos y la soldadura por resistencia se está desarrollando y validando como ladrillos tecnológicos para futuros fuselajes de aviones. Este trabajo lo está llevando a cabo el Centro Aeroespacial Alemán (DLR), el Instituto de Estructuras y Diseño (Instituto BT) en Stuttgart, en colaboración con socios de la industria aeroespacial, incluidos Airbus y otros institutos de investigación.

DLR Institute BT ha demostrado una intersección de fuselaje totalmente integrada, que consta de revestimiento, largueros, bastidor y tacos. El demostrador se basa en una piel curva consolidada fuera de autoclave (OOA) con largueros co-consolidados e integración de marcos y tacos mediante soldadura por resistencia. Las soldaduras se caracterizaron mediante pruebas mecánicas y la línea de soldadura se examinó más a fondo con un microscopio óptico.
TB-Rumpf en proceso de consolidación y soldadura OOA
El estado de la técnica para la consolidación de componentes de gran superficie hechos de termoplásticos continuos reforzados con fibras de alta temperatura (por ejemplo, poliariletercetona o PAEK) es la consolidación en autoclave. Sin embargo, a través de una configuración de proceso optimizada y un control de proceso personalizado, es posible lograr una consolidación completa usando solo temperatura y presión de vacío. El uso de hornos o moldes autocalentados puede eliminar la necesidad de un autoclave y, por tanto, generar ventajas económicas. El proyecto TB-Rumpf tiene como objetivo madurar el proceso denominado VCT (técnica de consolidación al vacío) y determinar los límites del proceso, incluido el espesor máximo posible del laminado.
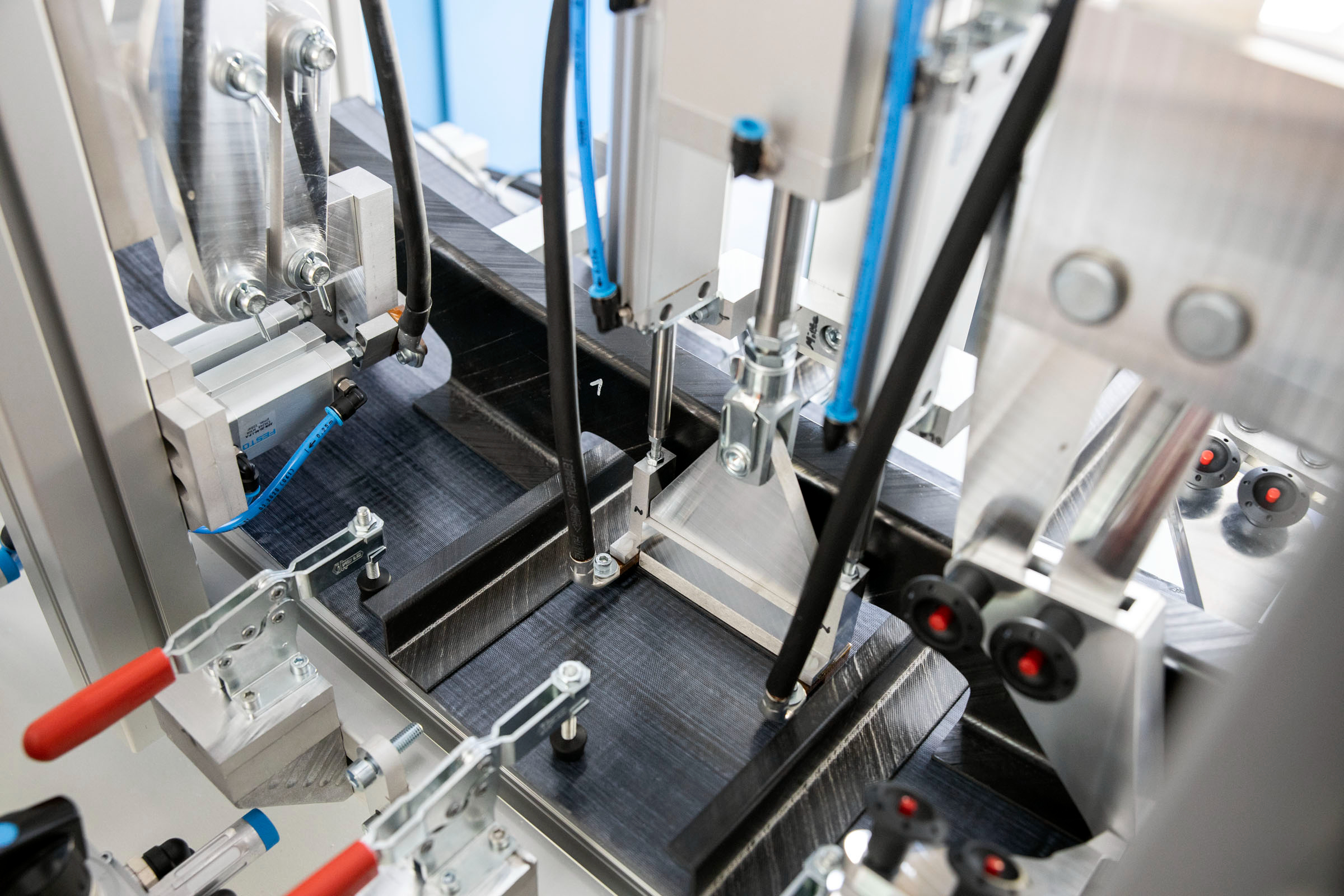
Otra tecnología clave para futuras aplicaciones de compuestos termoplásticos avanzados es la soldadura para ensamblaje. DLR y Airbus han identificado la soldadura por resistencia como una tecnología líder debido a su capacidad para lograr estructuras de alta resistencia. Dentro del proyecto TB-Rumpf, se está optimizando el proceso de soldadura por resistencia y los elementos de soldadura necesarios. Los demostradores resultantes se prueban estructuralmente para validar el rendimiento mecánico de la junta y los laminados compuestos soldados.
Investigación de la técnica de consolidación por vacío (VCT)
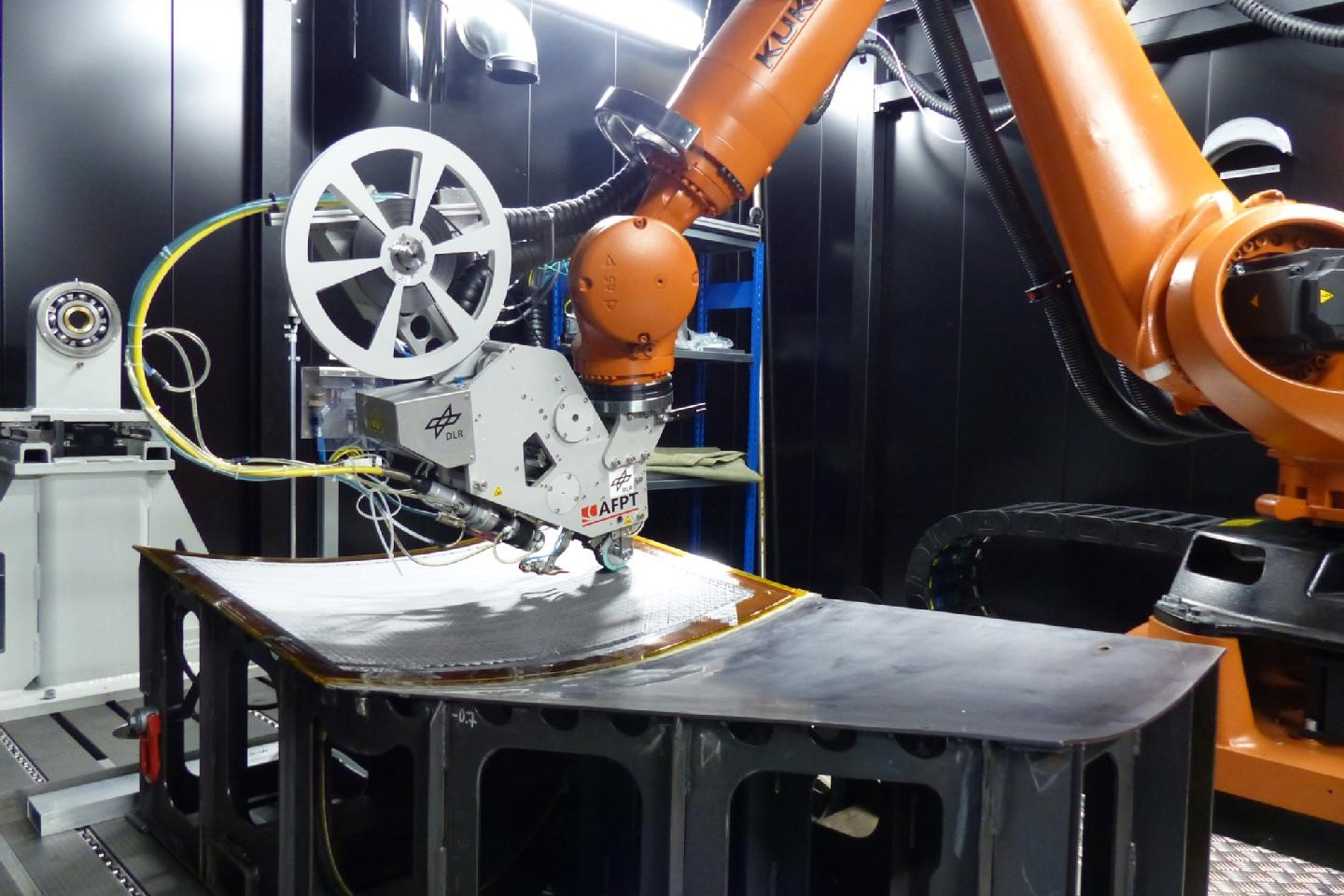
Matthias Horn, líder del proyecto en DLR Institute BT, explica que el demostrador TB-Rumpf utiliza poliariletercetona de bajo punto de fusión reforzada con fibra de carbono unidireccional (LM-PAEK). Esta cinta compuesta termoplástica se procesa mediante la colocación automatizada de fibra (AFP) lograda con un robot KUKA (Augsburg, Alemania) con un efector final AFPT (Doerth, Alemania) y un láser de 6 kilovatios para calentar la cinta.
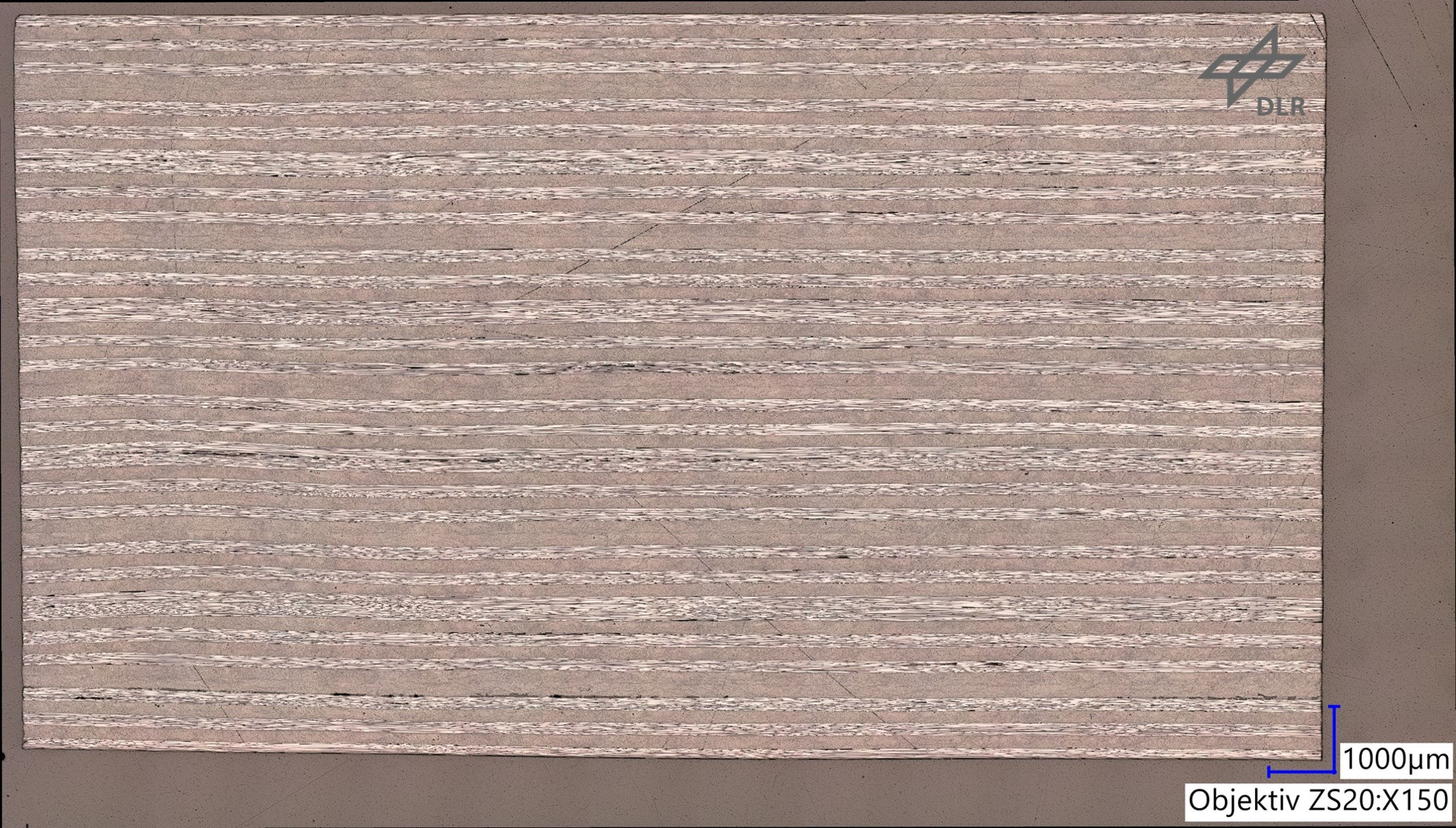
Consolidación de OOA mediante VCT: “El objetivo era validar la viabilidad de este proceso para laminados gruesos”, dice Georg Doll, investigador del Instituto BT y líder de TB-Rumpf para la consolidación. “Hemos mostrado buenos resultados para laminados de hasta 11 milímetros de espesor, sin poros u otras imperfecciones, validados por cortes transversales micrográficos e inspección ultrasónica. Las claves de este éxito son una configuración de VCT optimizada, un ciclo de calentamiento personalizado y una calidad preimpregnada homogénea y constante ".
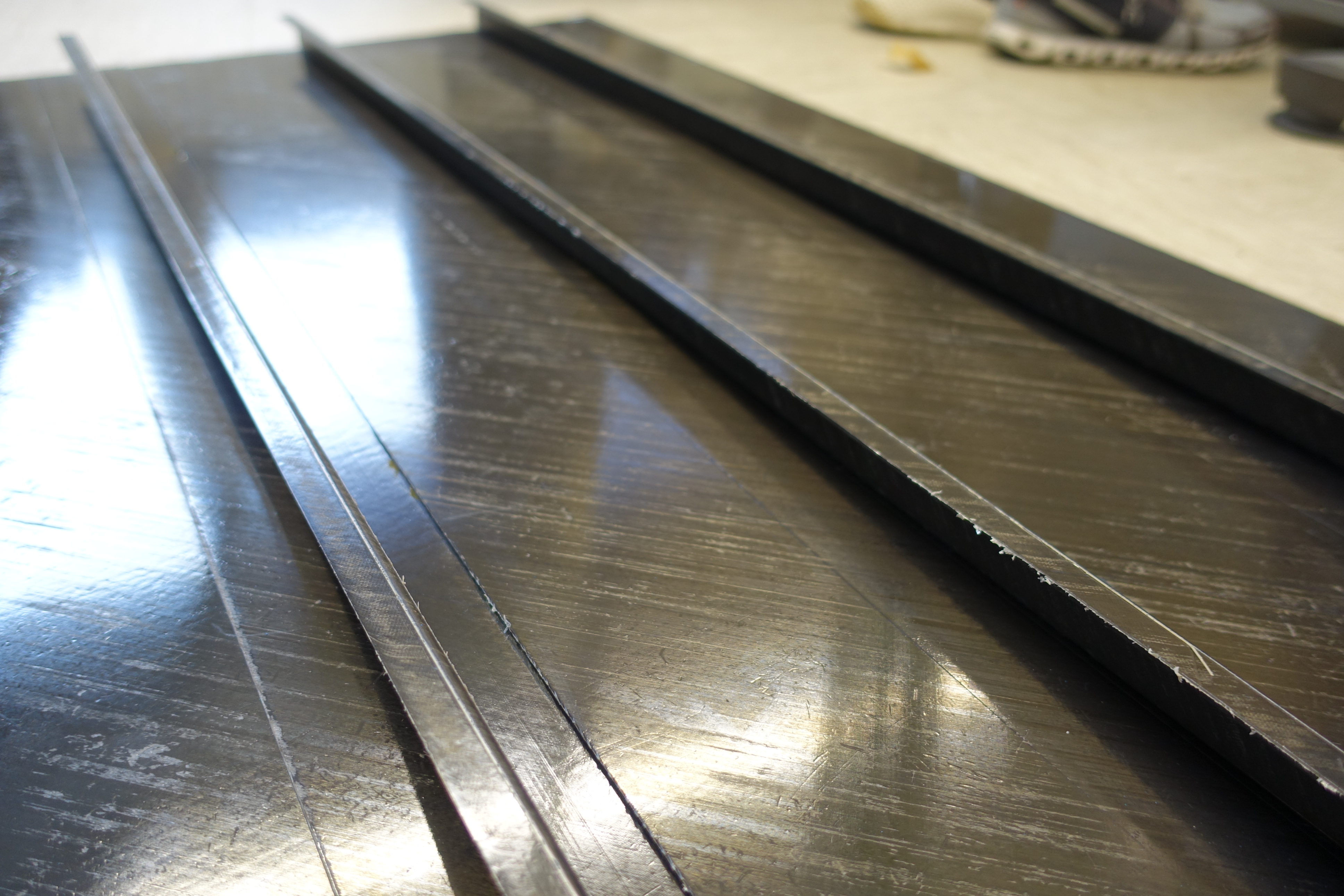
Co-consolidación OOA de elementos de refuerzo: Además de utilizar VCT para la producción de paneles de revestimiento de fuselaje sin autoclave, el proyecto TB-Rumpf también ha tenido éxito en el desarrollo de la co-consolidación para la integración directa de los elementos de refuerzo del larguero con el revestimiento durante un único ciclo de proceso de VCT.
Disposición AFP de formas curvas y de doble curva: Se investigó el AFP basado en láser como un proceso complementario del VCT, incluidos los límites de proceso y material (por ejemplo, dirección máxima de cinta), mediante la fabricación de laminados de doble curva que miden aproximadamente 800 x 1200 milímetros. Los resultados de estas pruebas de fabricación se pueden utilizar para avanzar en la consolidación OOA, así como en la consolidación in situ, que se logra durante la AFP sin una operación secundaria.
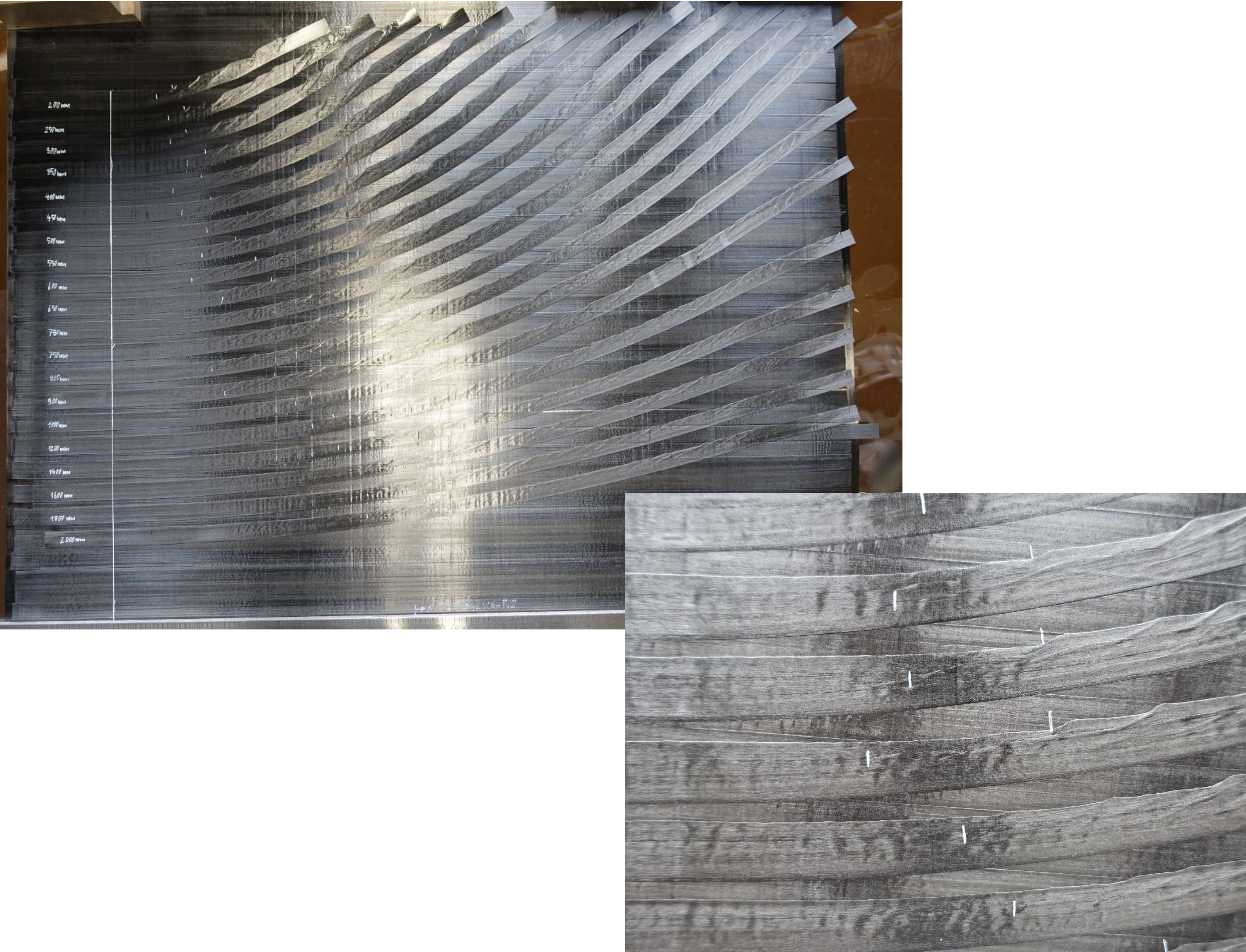
Soldadura por resistencia
“Para integrar elementos estructurales del fuselaje, y así hacer factible la producción de futuros conceptos de fuselaje termoplástico, investigamos la soldadura por resistencia con respecto a una mayor robustez del proceso y valores de resistencia optimizados”, dice Simon Bauer, investigador del Instituto BT y líder de TB-Rumpf para soldadura. "La atención se centró en una configuración optimizada del elemento de soldadura, basada en fibra de carbono como elemento calefactor, y una conducción eléctrica mejorada, en combinación con los parámetros de soldadura más adecuados, como el ciclo de calentamiento, la temperatura, la presión, la corriente y el voltaje". Se utilizó soldadura por resistencia para sujetar los listones tanto al marco como a los largueros; también se utilizó para sujetar el marco a la piel.
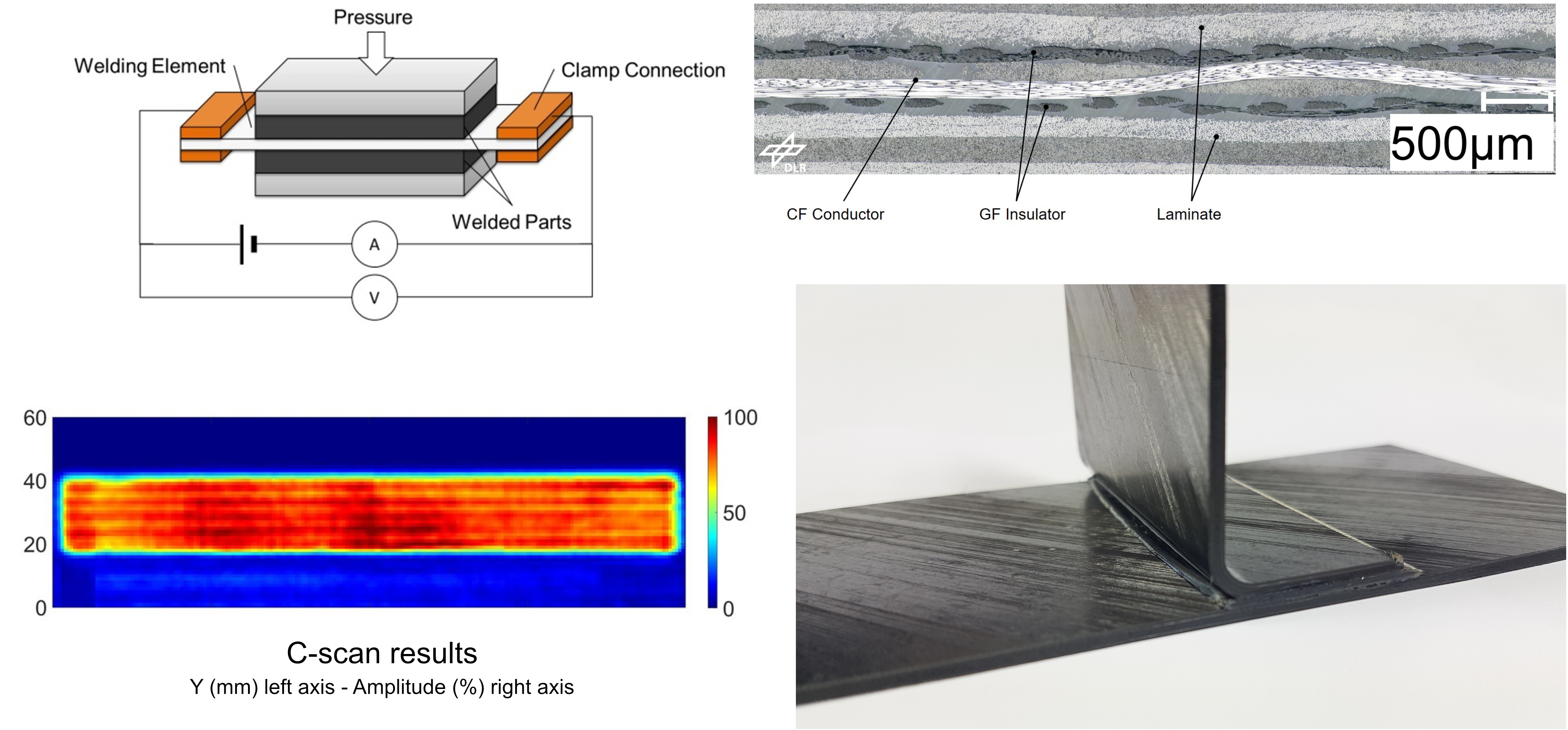
Ladrillos tecnológicos para los próximos diseños de fuselaje
“Debido a la madurez tecnológica demostrada, tanto la consolidación fuera del autoclave como la soldadura por resistencia pueden desempeñar un papel importante para los diseños de fuselaje futuros”, subraya el Dr. Paul Jörn, jefe del proyecto Airbus correspondiente.
Para acercar aún más las tecnologías a la aplicación industrial, se investigarán más aspectos desafiantes en un futuro próximo. Para la consolidación al vacío, se enfocará el escalado de tamaño y la transferencia a contornos de doble curva. Para la soldadura por resistencia, se abordarán aspectos de tolerancia, así como aspectos de automatización.
Los resultados presentados aquí se lograron dentro del proyecto de investigación TB-Rumpf (FKZ:20W1721D) en el marco del Programa Federal de Investigación de Aviación V-3, financiado por el Ministerio Federal de Asuntos Económicos y Energía de Alemania.
Para obtener más información, visite dlr.de/bt.
Resina
- Beneficios de diseño de los termoplásticos en componentes de bombas y válvulas
- Solvay expande la capacidad de compuestos termoplásticos
- El proyecto RECONTRAS valida el uso de microondas y soldadura láser para obtener composites reciclables
- Las cintas termoplásticas continúan mostrando potencial para aeroestructuras compuestas
- Los kits fáciles de usar permiten la reparación dentro del campo de estructuras compuestas
- Desarrollo de estructuras de isogrid compuestas utilizando tecnología innovadora de deposición
- Las innovaciones de diseño mejoran la eficiencia de la mesa médica compuesta
- Costillas Wing of Tomorrow:consolidación OOA, termoplástico, de un solo uso
- La estructura compuesta termoplástica reemplaza los metales en los pedales de freno críticos para la seguridad
- El consorcio busca soluciones para estructuras compuestas termoplásticas de fibra de carbono
- Soldadura de compuestos termoplásticos