Composites 4.0:Transformación digital, producción adaptativa, nuevos paradigmas
Composites 4.0 es una pequeña galaxia en el universo de la Industria 4.0, que es la transformación digital en cómo se diseñan, producen, entregan, operan, mantienen y desmantelan los bienes y servicios. Para la fabricación de compuestos, el objetivo es utilizar automatización, sensores y datos, comunicaciones 5G, software y otras tecnologías digitales en continua evolución para hacer que los productos y procesos sean más eficientes, inteligentes y adaptables.
Los fabricantes de composites están avanzando a través de esta transformación digital a lo largo de un espectro. Los pasos iniciales incluyen inspección en línea y procesos optimizados que reducen el desperdicio y los costos al tiempo que aumentan la calidad y el rendimiento de las piezas. Las soluciones más avanzadas funcionan hacia una producción inteligente y autónoma que no solo es ágil, sino que responde e incluso anticipa mercados cambiantes y demandas de los clientes.
“Composites 4.0 no es un fin, sino una herramienta”, explica el Dr. Michael Emonts, director gerente del Centro AZL Aachen para la Producción Integral Ligera en la Universidad RWTH Aachen (Aachen, Alemania), cuyo proyecto iComposite 4.0 demostró una cadena de proceso adaptativo con potencial para reducir el costo de una bandeja de piso automotriz en un 50-64%.
"Existe una diferencia entre simplemente hacer las cosas digitales y la transformación digital que realmente cambia los procesos detrás de su negocio y abre nuevas oportunidades y modelos de negocio", sostiene Christian Koppenberg, director gerente del productor de piezas compuestas Dynexa (Laudenbach, Alemania).
"Composites 4.0 no es solo usar robots", afirma el Dr. Michael Kupke, director del Centro de Tecnología de Producción Ligera del Centro Aeroespacial Alemán (DLR) (ZLP, Augsburg), que ha desarrollado una celda de trabajo equipada con inteligencia artificial [AI] donde los robots colaborativos pueden pasar de producir mamparos de presión traseros compuestos a paneles de fuselaje sin reprogramación o reentrenamiento. “Es la tecnología la que garantiza que no tenga que enseñar a los robots, porque no hay argumentos comerciales para eso. Composites 4.0 es más que aumentar la eficiencia y reducir los costos. Es un cambio en la forma en que las empresas piensan y enfocan la producción que determinará qué empresas sobreviven y cuáles no ".
Preformado adaptable, RTM
“La idea del proyecto iComposite 4.0 era crear preformas a partir de mechas y remolques rentables combinando fibra de vidrio larga seca (25-30 milímetros) rociada y posteriormente reforzada con una rejilla de fibras de carbono unidireccionales (UD) a través de la colocación automatizada de fibras. (AFP) ”, explica Emonts. “El demostrador elegido, un panel trasero debajo del piso del vehículo, se fabricó anteriormente con textiles más costosos que también producían más del 60% de desechos”.
La transformación de Composites 4.0 requirió la integración de los procesos de pulverización de fibra, deposición de fibra y posterior moldeo por transferencia de resina (RTM) para que reaccionaran entre sí y se adaptaran en función de la calidad de la pieza medida entre los pasos (Fig.1). “Usamos un sistema de visión artificial de Apodius GmbH [Aquisgrán, Alemania] con un sensor láser óptico y un módulo de cámara para caracterizar la topología de la superficie de la preforma rociada”, dice Emonts. “Apodius adaptó el software para analizar el porcentaje de fibras en cada dirección. La línea iComposite 4.0 comparó esto con el diseño digital y decidió si cumplía con los requisitos mecánicos. En caso afirmativo, aplicó la rejilla UD estándar para el refuerzo. En caso negativo, decidió dónde colocar capas de fibra UD adicionales ”.
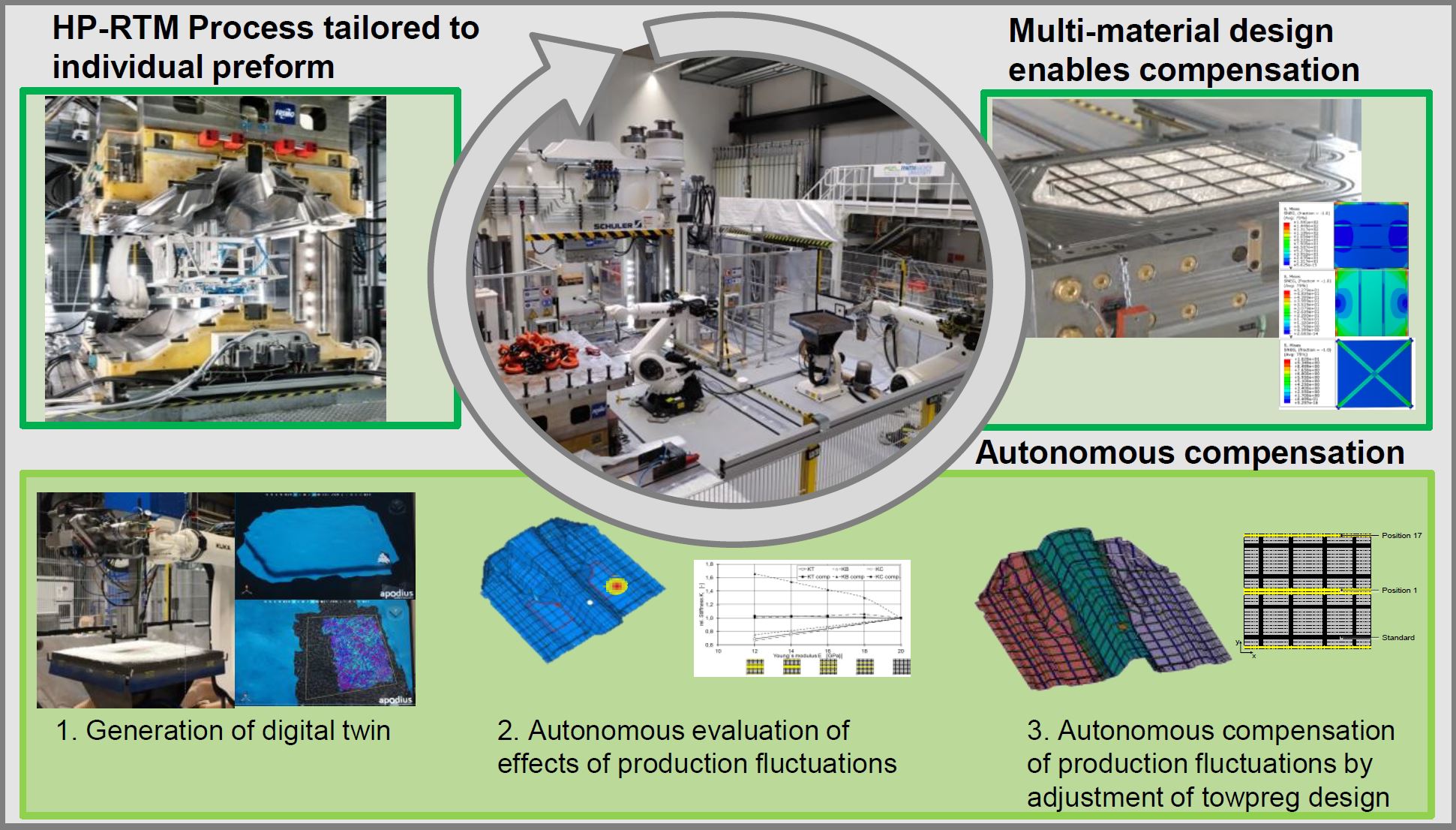
Sin embargo, estas capas de UD adicionales podrían hacer que el grosor y la geometría de la pieza excedan las tolerancias. “Por lo tanto”, explica, “combinamos la línea de preformado con un proceso RTM adaptativo que, si era necesario, ajustaba el espesor de la pieza aumentando la presión en ciertas partes de la prensa”. Esto también fue automatizado, con el objetivo de reemplazar la intervención del operador de línea, pero requirió la simulación del desempeño de la pieza utilizando datos de medición y software estándar FEA.
“Actualmente, la simulación de las propiedades mecánicas de la pieza se realiza fuera de línea”, dice Emonts. “Generamos una base de datos de variaciones de procesos y piezas, creamos algoritmos para reaccionar a cada variación y los validamos a través de FEA. Así, con base en las variaciones medidas por la línea, los algoritmos la dirigieron a realizar una mitigación adecuada. Para que la línea sea adaptable in situ, el siguiente paso sería agregar el aprendizaje automático ". Mientras tanto, AZL está llevando a cabo numerosos proyectos de Composite 4.0, incluida la producción autooptimizada de compuestos termoplásticos híbridos y piezas moldeadas por inyección con refuerzo integrado de espacios en blanco hechos a medida basados en cinta.
Pieles de alas de CFRP sin defectos
El proyecto ZAero (ver “Fabricación sin defectos de piezas compuestas”) es otro proyecto clave de Composites 4.0, que comenzó en 2016. Su objetivo era aumentar la productividad de grandes estructuras de plástico reforzado con fibra de carbono (CFRP) como las pieles de alas. Los defectos se reducirían mediante el uso de la inspección en línea automatizada con AFP preimpregnado o la colocación automática de material seco de Danobat (Elgoibar, España) (ADMP, consulte "Demostración de la viabilidad de tejidos secos, infusión para grandes aeroestructuras"). La monitorización del proceso durante la infusión de resina o el curado preimpregnado predeciría el estado de curado y acortaría el tiempo del ciclo. Los datos recopilados de procesos y defectos se utilizaron con FEA para predecir el rendimiento de la pieza. Esto luego se ingresó en una herramienta de apoyo a la toma de decisiones sobre cómo abordar los defectos identificados. Se desarrolló una simulación de flujo de piezas para pieles de alas de CFRP que, cuando se introdujo en esta herramienta, ayudó a optimizar una estrategia de retrabajo (Fig. 2). Hoy en día, muchas de estas piezas se vuelven a trabajar durante la fabricación, pero solo después de la NDI. El reprocesamiento anterior y el control mejorado del proceso eran de hecho los objetivos del proyecto ZAero, así como los facilitadores de su objetivo de aumento del 15% en la tasa de producción, reducción del 15-20% en costo de producción y 50% menos de desperdicio.
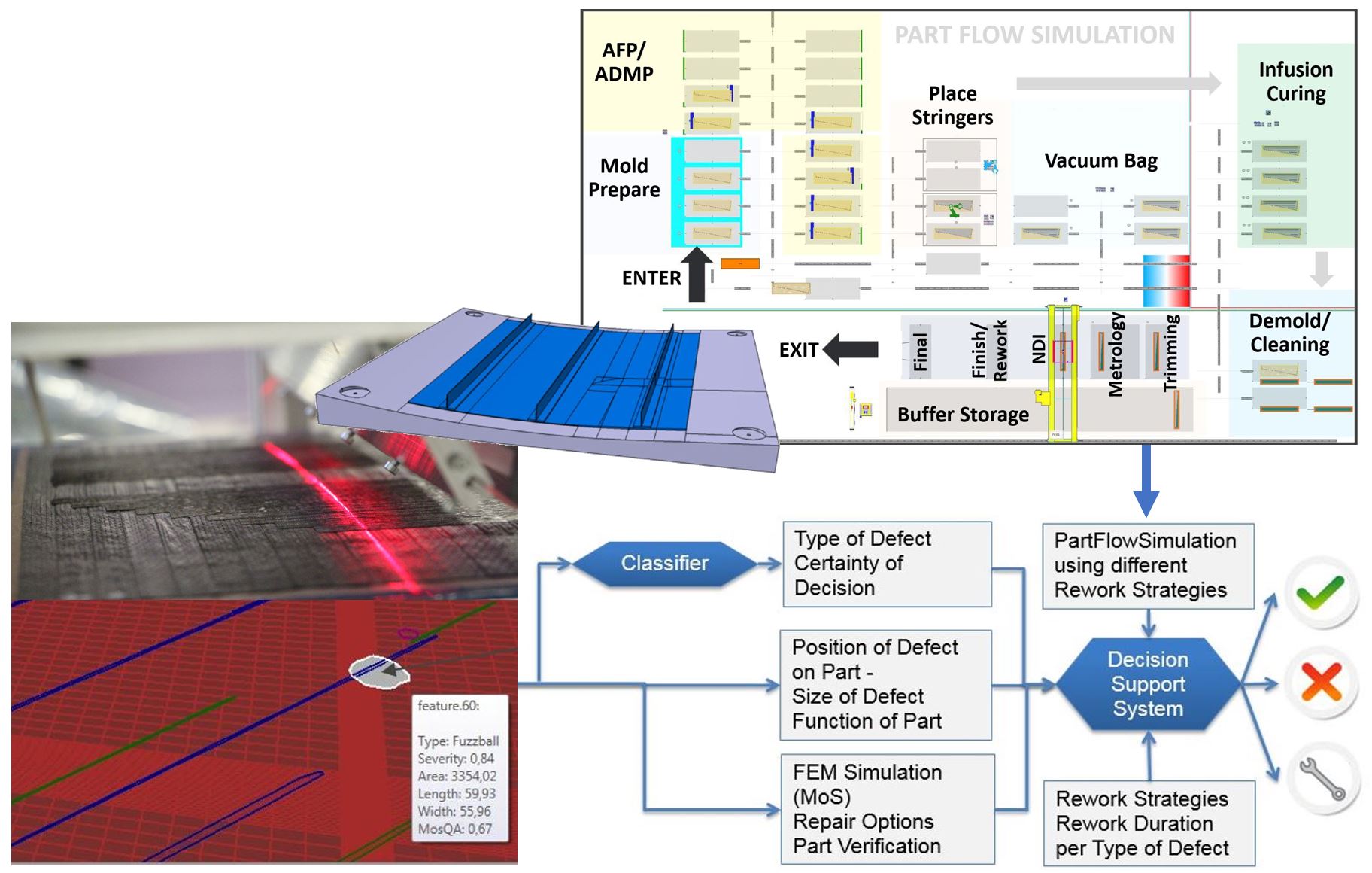
En la revisión final de septiembre de 2019, el sensor AFP preimpregnado desarrollado por el líder del proyecto Profactor (Steyr, Austria) no solo logró una inspección en línea automatizada, sino que también se pudo utilizar para corregir piezas in situ. “Este sensor puede detectar los defectos estándar como huecos, superposiciones, FOD, bolas de pelusa y remolques torcidos, así como el corte temprano y tardío de cada remolque”, dice el Dr. Christian Eitzinger, jefe de visión artificial de Profactor. Un remolque faltante se puede corregir automáticamente con la colocación de un remolque adicional precisamente donde se omitió. Sin embargo, la máquina debe detenerse para eliminar bolas de pelusa o remolques torcidos. “Una base de datos creada con la experiencia 3D de Dassault Systèmes (París, Francia) para CATIA nos permite calcular los efectos sobre el rendimiento de la pieza en función del tamaño, la forma y el tipo de defecto. Procesar todos los defectos en una capa toma solo unos segundos. Luego, el operador de la máquina decide qué defectos se pueden dejar y qué se debe reelaborar ”.
Para la supervisión y el control del proceso de infusión, Airbus (Toulouse, Francia) trabajó a través de la filial InFactory Solutions (Taufkirchen, Alemania) para desarrollar tres sensores que miden la temperatura, el estado de curado y el frente de flujo de resina (consulte “Sensores para supervisar el frente de flujo de infusión de resina”. ) “Los hemos integrado con CATIA 3D Experience y hemos demostrado que los datos se pueden adquirir y agregar de manera confiable al hilo digital de cada pieza”, dice Eitzinger. (Consulte la barra lateral en línea "Composites 4.0:hilo digital frente a gemelo digital").
El final de los demostradores de tres partes fue una subsección de cubierta de ala superior con tres largueros (ver barra lateral en línea “Actualización del proyecto ZAero”). Para esta parte, la herramienta de soporte de decisiones de Profactor se demostró en vivo en el socio FIDAMC (Madrid, España), conectada a la simulación de flujo de piezas, basada en el software Siemens PLM (Plano, Texas, EE. UU.) Tecnomatix Plant Simulation, que se ejecuta en el servidor de Profactor en Austria. Además de crear una base de datos de defectos, ZAero realizó experimentos con aprendizaje automático. Modelos informáticos generativos diseñados manualmente, combinados con redes neuronales profundas, detectaron y clasificaron defectos, logrando una tasa del 95% de clasificación correcta de diferentes regiones (brecha, superposición, remolque, bola de fuzz) en datos de monitoreo ADMP reales, incluso cuando Los datos de defectos creados artificialmente se utilizaron para el entrenamiento profundo de la red (de forma análoga a cómo se calibran los sistemas de prueba ultrasónica en una variedad de defectos deliberados).
"Definitivamente buscaremos algún tipo de próxima fase", dice Eitzinger. Mientras tanto, Profactor comercializa sensores modulares para la orientación de la fibra y los defectos durante el laminado automatizado. InFactory Solutions también ofrece sus sensores de infusión de resina y AFP, y los socios de colocación de fibra Danobat y MTorres (Torres de Elorz, Navarra, España) ahora están vendiendo sus equipos con inspección en línea integrada.
El viaje de transformación digital de Dynexa
Dynexa es un fabricante de piezas compuestas que se especializa en tubos y ejes de CFRP. “Siempre habíamos intentado digitalizar todo”, dice el director gerente Koppenberg. “Ya nos deshicimos de los procesos manuales y analógicos, integrando todo principalmente en nuestro sistema ERP [planificación de recursos empresariales]. Pero, ¿cómo hacemos esto en la fabricación? Entendimos que todo lo que ponemos en un protocolo o procedimiento de trabajador es un código, y esto es una base para la transformación digital. Pero, ¿dónde se almacena? ¿En un servidor local, en la nube o dentro de la máquina? Preguntaríamos a cinco personas y obtendríamos siete respuestas sobre lo que deberíamos hacer ". (Consulte la barra lateral en línea, "Composites 4.0:¿Por dónde empezar?")
Afortunadamente, el gobierno alemán había creado un programa para que las universidades ofrecieran consultoría gratuita de Industria 4.0 para pequeñas y medianas empresas (PYME). Dynexa comenzó a trabajar con el centro de competencia “Mittelstand (SME) 4.0” de Darmstadt. “Dijeron que no debían preocuparse por la arquitectura digital, sino mirar más hacia lo que necesita medir y cómo hacerlo”, recuerda Koppenberg. "Elegimos un proceso que implicaba una importante medición manual, en el que sabíamos que teníamos problemas de calidad, tiempo y costes".
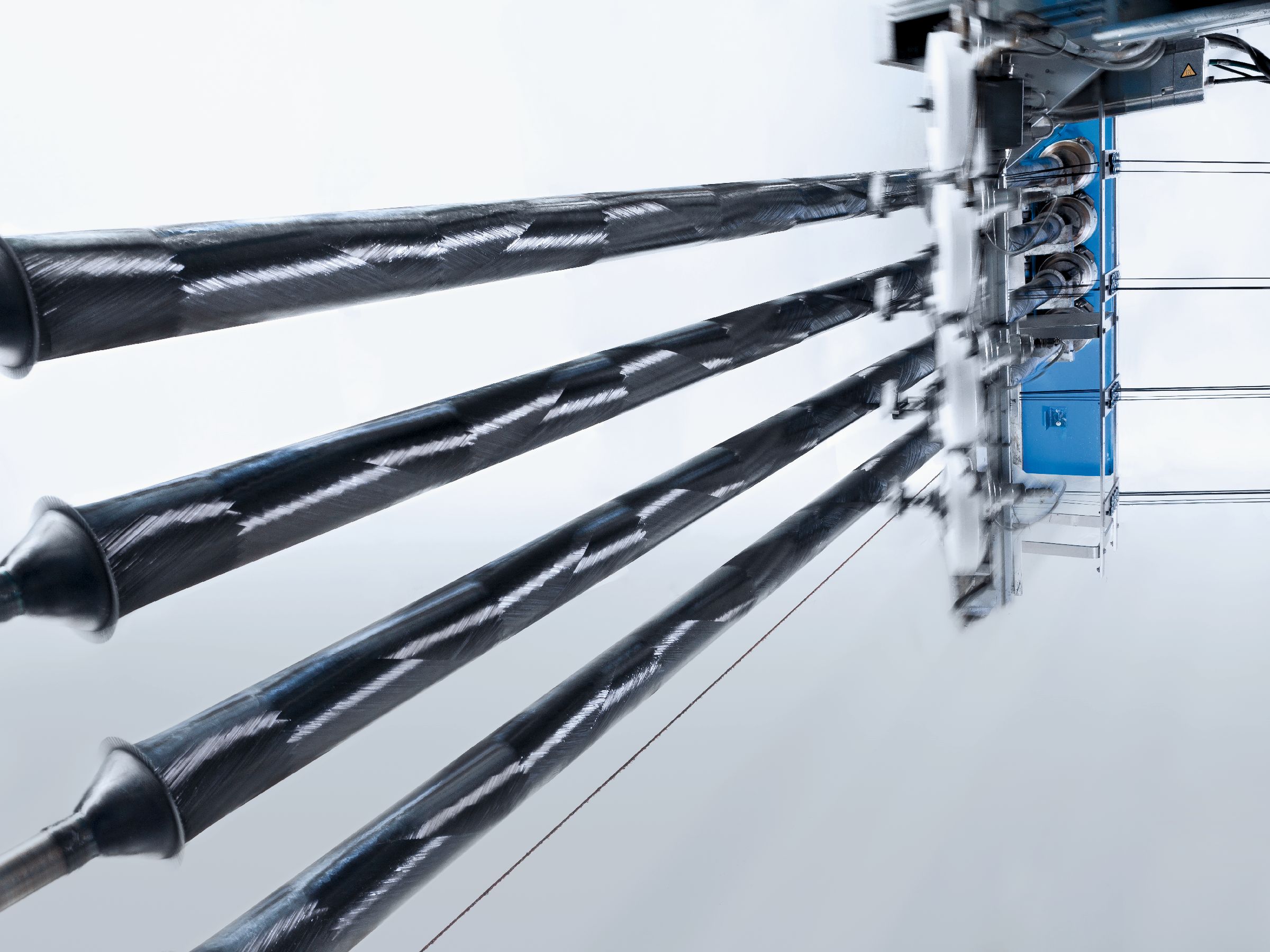
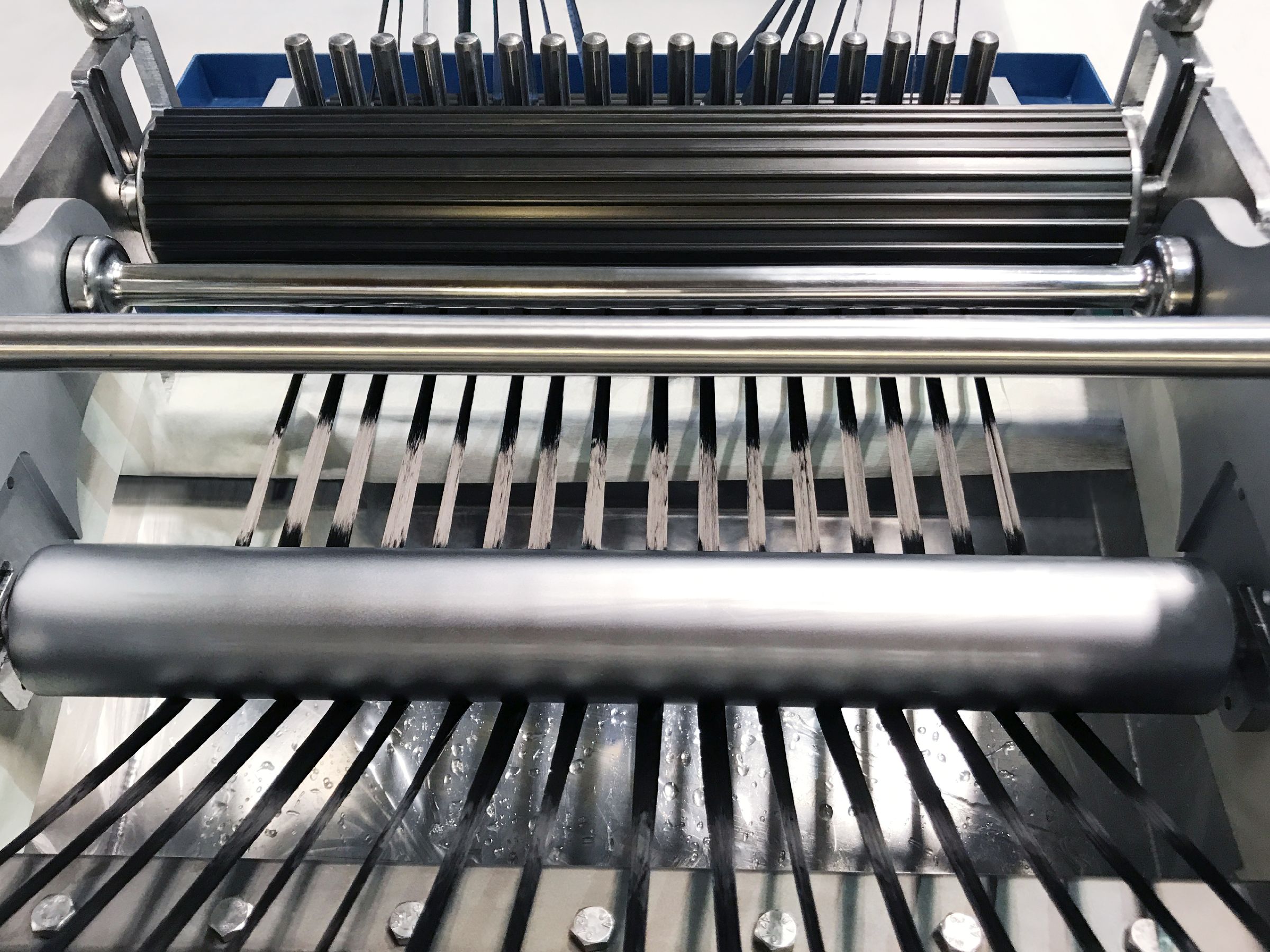
Dynexa utiliza un proceso de bobinado de filamento húmedo (consulte “Eje de salida compuesto listo para el campo de pruebas automotrices)”. Un paso clave es la recogida de resina, donde la fibra seca pasa a un rodillo de compactación que se enrolla fuera del baño de resina. Sentado contra el rodillo de compactación hay una rasqueta que determina la cantidad de resina que se combinará con el filamento seco antes de enrollarlo. "Si recogemos demasiada resina, es posible que superemos el diámetro del tubo especificado", dice Koppenberg, "pero con muy poca resina, corremos el riesgo de caer por debajo del diámetro mínimo permitido".
“Sin medir, solo se conoce el diámetro final después del curado, cuando se ha invertido todo el valor”, señala. “Entonces, el operador debe detener la máquina, medir la pieza, anotarla y luego reiniciar. Gracias a años de experiencia, sabemos cuál debe ser el espesor del laminado en cada etapa del bobinado. Por lo tanto, el operador compara la medición y ajusta la cuchilla dosificadora para corregir la recogida de resina según sea necesario, pero esto es muy manual y depende de la habilidad y experiencia del operador ”.
Para digitalizar esto, Dynexa habló con innumerables fabricantes de cámaras y láser. “Decían, 'tenemos la solución', pero nadie podía hacer que funcionara”, señala Koppenberg. Sin embargo, el equipo de la Universidad de Darmstadt permitió el uso de una cámara calculando las correcciones necesarias debido a ciertos factores físicos, como el reflejo de la luz de la superficie mojada. “Ahora tenemos la bobinadora conectada al dispositivo de medición, que funciona de forma muy estandarizada”, añade.
El equipo desarrolló una base de datos de tablas de corrección y algoritmos de decisión que permite que la máquina de bobinado de filamentos sepa cuál debe ser el objetivo para cada etapa del tubo específico que se está enrollando. "Si la entrada del dispositivo de medición muestra que la recogida de resina no está donde debería estar", explica Koppenberg, "la máquina de bobinado de filamentos responde ajustando la cuchilla dosificadora para devolverla a las especificaciones sin detener el bobinado para medir".
Cada máquina bobinadora ahora tiene el sistema de medición digital, y una tarjeta ethernet. "La parte más cara fue instalar y pasar los cables al servidor", bromea Koppenberg, "pero ahora podemos hablar con cada máquina y recopilar todos los datos". Y hay otro beneficio. “Antes, los operadores programaban en las máquinas, pero una vez que las conectamos al servidor, podemos programar en cualquier computadora de escritorio o portátil. Esto ha reducido aún más el tiempo de inactividad y eliminado otro cuello de botella de producción ".
Este primer paso digital ha permitido a Dynexa mejorar el control, la calidad y la eficiencia de sus procesos, lo que le permite ser más rentable. También ha estimulado una mayor transformación.
Cambio de paradigmas para compuestos
"Estamos en un proceso gradual para proporcionar un nuevo ecosistema para nuestros clientes", dice Matthias Bruckhoff, director de ventas y marketing de Dynexa. Da un ejemplo:“En Amazon, puedes ver qué compraste y cuándo, así como sugerencias de nuevos productos. Solíamos tomar los requisitos del cliente y luego responder en unos días utilizando nuestros cálculos y herramientas de ingeniería. Ahora, esto estará en línea. Nuestros clientes verán los productos y calcularán lo que necesitan, el costo y la entrega en cuestión de minutos. Esto no es nuevo, pero sí para nuestra industria. Así como liberamos a nuestros operadores de máquinas para que se concentren en más máquinas y tareas de mayor nivel, ahora liberaremos a nuestro equipo de ingeniería para que se concentre en productos más especializados y sofisticados ”.
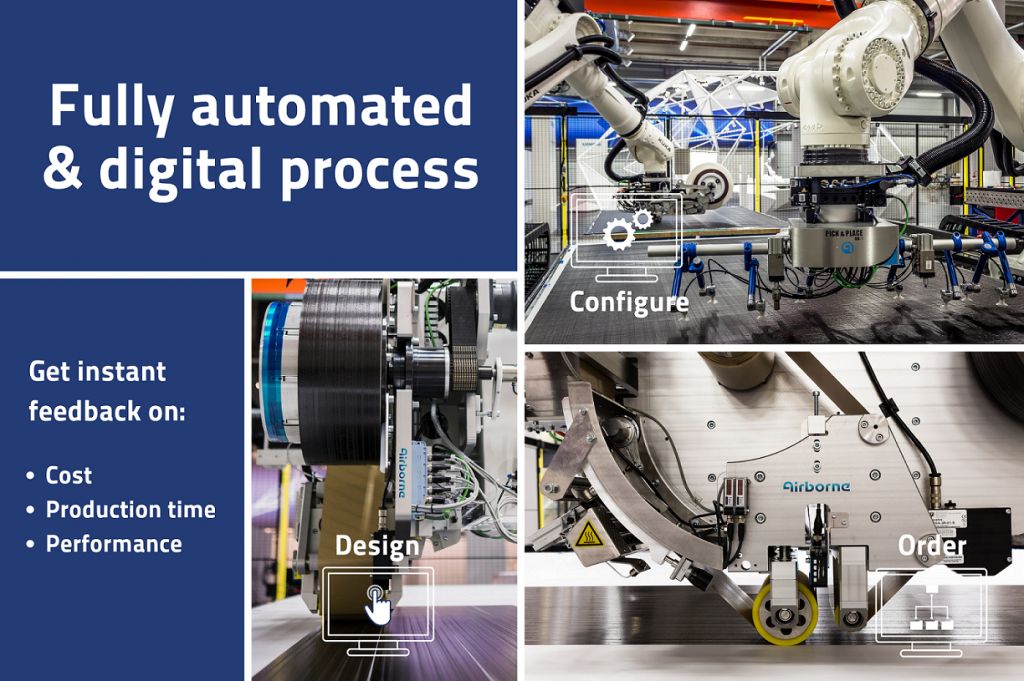
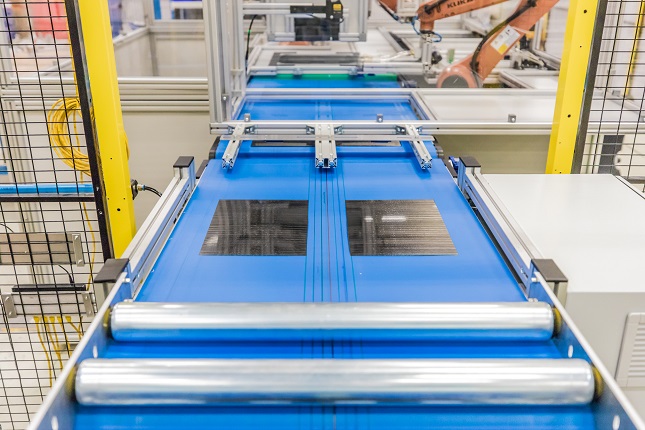
Airborne (La Haya, Países Bajos) lanzó su Portal de fabricación bajo demanda para la fabricación automatizada de materiales compuestos en septiembre de 2019 (consulte “Airborne lanza el portal de impresión de materiales compuestos”). Con esta herramienta, los clientes ingresan diseños en la plataforma basada en web. Luego, el sistema crea el código de la máquina sobre la marcha y determina la duración y el costo de producción. Luego, los productos se pueden personalizar y, una vez que se solicitan, se pueden producir en una celda de fabricación automatizada. El portal se lanzó utilizando la celda de laminación automatizada (ALC) de Airborne para procesar el preimpregnado termoestable. Se extenderá a otros procesos, por ejemplo, la línea de producción de compuestos termoplásticos de alto volumen (TPC) desarrollada para la unidad de negocios Specialties de SABIC (Riad, Arabia Saudita).
"Este portal es un componente clave de cómo vemos el futuro digital de la fabricación de compuestos", dice Marcus Kremers, director de tecnología de Airborne. “Hace cinco años, cambiamos de un modelo comercial de fabricación de piezas a ayudar a los clientes con la automatización y la digitalización. Estamos desarrollando una cartera de soluciones que facilitan a los clientes la construcción con materiales compuestos ". Esta cartera incluye el ALC, el encapsulado en forma de panal automatizado, el ensamblaje automatizado de capas y la línea de alto volumen que utiliza cintas TPC, denominada Línea de fabricación de compuestos digitales (DCML) por SABIC y Falcon por Airborne. Este último es un ejemplo de las soluciones a medida de Airborne. "Estamos incorporando nuestro conocimiento de fabricación de piezas y materiales compuestos en estos sistemas automatizados para que los clientes no tengan que ser especialistas", dice Kremers.
Airborne tiene tres modelos de negocio:comprar la automatización, alquilarla o dejarla en manos de Airborne para que opere a través de la fabricación como servicio (MaaS). Las celdas automáticas aerotransportadas cuentan con sensores y sistemas de inspección en línea que generan alertas basadas en una base de datos de defectos y tolerancias definida por el cliente. “La línea Falcon tiene tolerancias muy bajas para los defectos de calidad visual”, señala Kremers, “pero nuestra automatización para la industria aeroespacial se basa más en las tolerancias estructurales. También estamos avanzando continuamente en nuestras tecnologías para que sean autodidactas y autoadaptables. Por ejemplo, nuestra próxima versión de software para la colocación de cintas ALC tendrá la capacidad de identificar defectos y modificar el programa de producción sobre la marcha ”.
A más largo plazo, la visión es expandir el portal bajo demanda para recopilar la capacidad de producción de piezas compuestas distribuida en múltiples empresas y regiones. Kremers cita a Protolabs (Maple Plains, Minnesota, EE. UU.), Que proporciona prototipos moldeados por inyección, en chapa, mecanizados por CNC o impresos en 3D a pedido en tan solo un día. De manera similar, la aplicación en línea de Plyable (Oxford, Reino Unido) proporciona moldes para fabricar compuestos, y ofrece materiales que van desde tableros de poliuretano hasta acero, incluidos materiales compuestos y herramientas impresas en 3D. “Esa es una forma diferente de organizar la cadena de valor”, dice Kremers. "Estamos fabricando las máquinas y el software que harán esto posible para las piezas compuestas".
AZL Aachen también persigue este objetivo con su Máquina Consolidadora Ultra Rápida, desarrollada para producir laminados TPC multicapa en menos de cinco segundos. Comercializado en 2019, utiliza aplicadores AFP robóticos asistidos por láser de Conbility (Aquisgrán, Alemania) y cintas UD de 25 milímetros de ancho, así como un principio de flujo de piezas, lo último en la industria de la impresión de alta velocidad. para producir laminados de TPC, simplemente tachonados o totalmente consolidados, en una variedad de espesores, con refuerzos locales. “Nuestra visión es proporcionar máquinas escalables que permitan plataformas en línea”, dice Emonts. “Las líneas pueden tener varias estaciones, cada una con varios aplicadores de AFP. El cliente ingresará los requisitos y obtendrá opciones para el libro de pliegos, el costo y la entrega. Una vez finalizados, los aplicadores se comunican entre sí para organizar la producción, no con el operador. Se trata de una producción completamente inteligente de compuestos a medida ”.
Automatización de la automatización
El enfoque principal de ZLP es la producción automatizada de estructuras CFRP. “La automatización para una sola pieza o programa es difícil de justificar”, señala Florian Krebs, líder del equipo de ZLP para automatización flexible. “Sin embargo, si pasa de las máquinas para tareas específicas a una plataforma de automatización que se puede reconfigurar casi sin configuración adicional, ahora tiene una solución comercial. Cuanto más flexible sea la plataforma, más rápido será el retorno de la inversión ".
La celda de trabajo que se muestra en las imágenes de apertura se diseñó como parte del proyecto PROTEC NSR de ZLP para construir una familia de piezas que siga la misma ruta de proceso:colocación de recogida y colocación de telas secas que no se arrugan e infusión de resina (consulte la barra lateral en línea “No caso de negocio para la enseñanza de robots ”). “Este proceso fue diseñado para el mamparo de presión trasero del Airbus A350, pero también puede hacer un panel de fuselaje o una cubierta de ala en esta línea porque los pasos son similares”, dice Krebs.
“Para lograr plataformas de automatización flexibles se requieren ciertos ladrillos tecnológicos, incluidos algoritmos para los robots, así como sensores y cómo comprender los datos que producen”, dice Kupke. “Por ejemplo, la línea de producción PROTEC NSR está diseñada con la máxima modularidad:todos los módulos están interconectados entre sí para demostrar un sistema de autoconfiguración, corrección y optimización, escalable en tamaño y complejidad”.
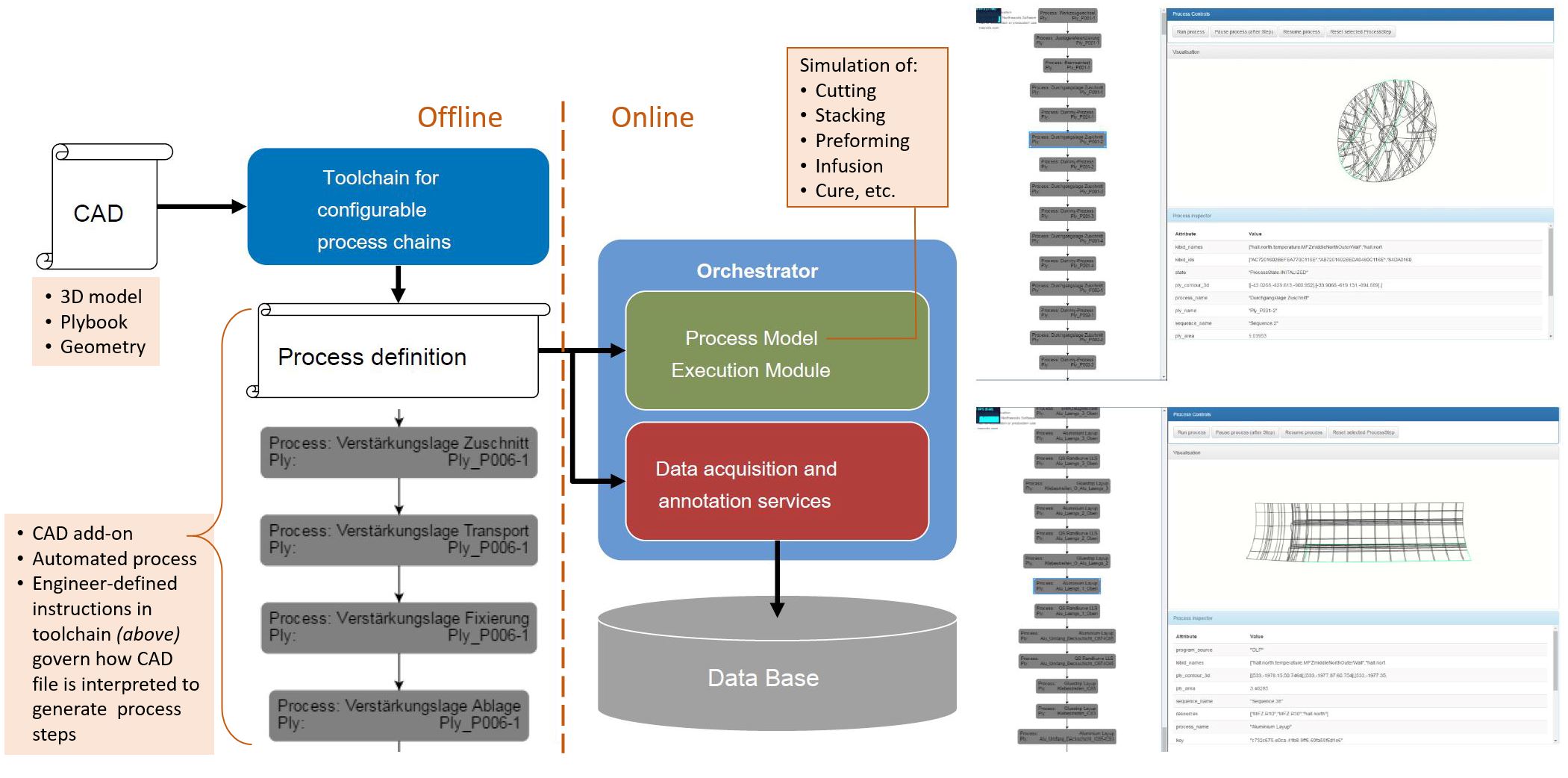
Explica los módulos como se muestra en la Fig.5, que incluyen modelo CAD, definición de proceso, modelo de proceso que permite la simulación y ejecución del proceso, módulo de ejecución de fabricación, sensores para adquirir datos, software para anotar los datos y base de datos para almacenamiento.
“En el lado izquierdo de este diagrama, haces un plan. Luego, el módulo de ejecución implementa ese plan ”, dice Kupke. “Durante los pasos del proceso, adquirimos datos de todas las máquinas y procesos involucrados, por ejemplo, la cortadora, los robots, el edificio (temperatura, presión, humedad), las cámaras durante el pick-and-place, etc. Analizamos los datos en tiempo real durante el proceso y también anotar los datos recopilados automáticamente con metadatos para alimentarlos en la base de datos, que forma la base del gemelo digital del proceso. El punto más importante del gemelo digital es tener un depósito central, una fuente de verdad. El modelo CAD de cada pieza y la definición del proceso son parte de su única fuente de verdad ".
Con estos módulos en su lugar, la línea funciona de forma autónoma con solo presionar un botón. A partir del modelo CAD, el plan de producción y las cámaras, los robots infieren qué pieza cortada viene a continuación y la buscan en la mesa (por ejemplo, de otras 100 piezas cortadas). “Ellos deciden cómo configurar las pinzas para levantarlo y colocarlo en la herramienta, y saben dónde colocarlo”. Según el plan de producción, los robots determinan cada ruta de inicio / finalización para todos los pasos del proceso y saben cuándo se realiza cada uno. “Por lo general, estos caminos los enseña un humano”, señala Kupke. “Pero en nuestro sistema, cada ruta se define automáticamente, sin colisiones y en tiempo real. Si cambia el modelo CAD o la definición del proceso, los robots se adaptarán sin ningún esfuerzo de enseñanza adicional. Pero, ¿y si cambia la pieza por completo? Con este tipo de automatización, podría realizar ese cambio muy rápidamente. Ésta es la ruta hacia la producción flexible. Nuestro papel en ZLP es allanar esta ruta desarrollando ladrillos tecnológicos y uniéndolos ”.
Oportunidad y ontología
La pandemia de COVID-19 ha puesto de relieve el valor de la producción flexible. También ha creado un entorno empresarial cada vez más impredecible. “En los últimos dos o tres años, todo se ha vuelto más volátil”, señala Bruckhoff de Dynexa. “Nuestros clientes quieren respuestas muy rápidas para poder responder a sus clientes. Al ofrecer nuestro nuevo ecosistema en línea, hacemos que toda la cadena de suministro sea más competitiva ”.
Esto es bien reconocido por la industria de la aviación. "Necesitamos una base digital para las líneas de producción y sitios completos que permita la integración horizontal y vertical", dice Marc Fette, presidente de la División Técnica de Tecnologías Aeroespaciales de VDI, la Asociación Alemana de Ingenieros y COO del Centro de Tecnología de Compuestos (CTC, Stade, Alemania), una filial de I + T de Airbus. Los proyectos de CTC en Composites 4.0 incluyen seguimiento de materiales y activos, robots colaborativos, cadenas de procesos avanzados y más. Pero Fette enfatiza la necesidad de ontología:una terminología y un protocolo común para la comunicación digital y el intercambio de datos. (Consulte la barra lateral en línea "Arquitectura y ontología de compuestos 4.0").
“Se necesita una red holística para todas las máquinas y sistemas de producción en una planta determinada”, explica, “pero esto también debe extenderse a toda la cadena de creación de valor, incluidas disciplinas como ingeniería, aprovisionamiento, logística y certificación de materiales y procesos. , Por un lado. Por otro lado, todas las partes interesadas, como los proveedores, deben ser consideradas e involucradas en este proceso de cambio. Vemos muchos proyectos piloto, pero cuando se mira en detalle, todavía falta una estrategia para un enfoque holístico por empresa o cadena de producción ".
Continúa:“Tenemos una red global muy grande de proveedores y ellos tienen los mismos requisitos para operar como una cadena de suministro conectada digitalmente. La mayoría de nuestros proveedores son pymes que trabajan para fabricantes de aviones, Airbus y Boeing. Si no hay una discusión sobre un estándar común, entonces transfiere estos desafíos a los proveedores. Lo más probable es que no puedan permitirse cumplir con dos conjuntos de estándares diferentes para todas sus máquinas, incluida la documentación, la evaluación de datos, la seguridad cibernética, etc. "
Fette admite que se trata de grandes ideas y dice que los fabricantes de equipos originales de aviones están creando planes para abordar estos desafíos. “Pero hay muchos obstáculos como este, y es realmente complejo, que involucra no solo a la tecnología sino también a cuestiones sociales, económicas, ergonómicas y legales; es un proceso de cambio mental. Estamos apenas al principio. Pero para tener éxito, debemos comprender que estos nuevos sistemas dependen de las personas y estas personas deben participar, no solo en los OEM, sino en toda la red global ”.
“Markets are becoming more fragmented across all industries and everyone is facing a paradigm shift,” notes ZLP’s Krebs. “Many people don’t see that as an opportunity,” adds Kupke, also of ZLP. But those who do see that opportunity envision democratized access to composites enabled by Composites 4.0, and with that, a much broader market, including applications that we are only beginning to conceive.
Resina
- Optimización de la transformación digital en la fabricación de CPG
- La estrategia de transformación digital exige un nuevo enfoque de talento
- La transformación digital basada en datos impulsa a Airbus a nuevas alturas
- ¿Cómo está cambiando el sector de servicios públicos la nueva era de la transformación digital?
- Evonik construirá una nueva planta de producción de PA12
- Plan para el éxito en la transformación digital
- ¿Qué es la transformación digital en la fabricación?
- 7 impulsores de la transformación digital
- Desafíos de la transformación digital en la fabricación
- Transformación de la fabricación digital:una resolución de año nuevo
- GE Digital:un viaje de transformación digital en curso