Microestructura controlada y propiedades mecánicas de compuestos de nanocarbono a base de Al2O3 fabricados mediante el método de ensamblaje electrostático
Resumen
Este trabajo informa sobre la formación controlada por microestructura de Al 2 en capas de carbono interconectado O 3 cerámicas que utilizan nanopartículas de carbono (CNP) -alúmina (Al 2 O 3 ) partículas compuestas. El Al 2 O 3 Las micropartículas utilizadas en este estudio se obtuvieron por granulación de Al 2 de tamaño nanométrico O 3 nanopartículas con un diámetro medio de 150 nm. Entonces, CNP-Al 2 O 3 compuesto se fabricó utilizando un método de ensamblaje electrostático utilizando el Al 2 granulado O 3 y CNP. La decoración de CNP en la superficie de Al 2 granulado O 3 se investigó en función del tamaño de partícula primaria y el porcentaje de cobertura utilizando una cantidad fija de CNP. En particular, una capa interconectada de partículas de carbono en la interfaz de Al 2 O 3 que se asemejan a los límites de grano. Las propiedades mecánicas de las muestras obtenidas con diferente tamaño de partícula y cobertura de CNP sobre Al 2 O 3 También se investigaron partículas que presentaban la posibilidad de controlar las propiedades mecánicas a través del diseño microestructural de materiales cerámicos compuestos.
Introducción
Es bien sabido que la alúmina (Al 2 O 3 ) posee buenas propiedades como alta dureza, excelente resistencia al desgaste y alta estabilidad química. Por otro lado, los inconvenientes de la alúmina son su escasa tenacidad a la fractura, su baja resistencia a temperaturas elevadas y su escasa resistencia al choque térmico [1]. Esto ha impulsado una intensa investigación en el desarrollo de nanocompuestos basados en alúmina a micro y nanoescala. Se informa que los compuestos cerámicos funcionales con nanopartículas bien dispersas en la matriz cerámica mejoran no solo las propiedades mecánicas como la resistencia a la rotura, la tenacidad a la fractura, la fatiga y la resistencia al desgaste, sino también las propiedades eléctricas, magnéticas, térmicas y ópticas [2 , 3, 4, 5, 6, 7]. Con el fin de mejorar y controlar las propiedades mecánicas de las cerámicas, se han utilizado e informado la porosidad microestructural [8, 9], la incorporación de rellenos aditivos [10] y los perfiles de tratamiento térmico [11, 12]. Esto muestra que al controlar la microestructura de Al 2 O 3 , las propiedades mecánicas deseadas de Al 2 O 3 se podrían obtener cerámicas. Sin embargo, la mayoría del trabajo reportado simplemente utilizó el método simple de Al 2 O 3 polvos que se mezclan antes de la sinterización, lo cual es insuficiente para obtener un buen control sobre la microestructura y el diseño del Al 2 O 3 cerámicas que dan como resultado una mala capacidad de control de sus propiedades mecánicas. En la formación de nanocompuestos mediante un método de mezcla convencional, sigue siendo un gran desafío obtener una decoración homogénea de partículas de aditivo de tamaño nanométrico en una partícula primaria designada debido a la aglomeración de partículas de aditivo. La distribución desigual causada por la aglomeración daría lugar a efectos adversos en el diseño microestructural así como en las propiedades de un compuesto cerámico. Por lo tanto, en este estudio se utilizó un método novedoso a través del ensamblaje ascendente que utiliza un método de adsorción electrostática para demostrar la viabilidad de obtener un buen control y diseño microestructural que, en consecuencia, permitan que las propiedades controladas deseadas se introduzcan en Al 2 O 3 cerámicas tales como propiedades ópticas, eléctricas y mecánicas. Como uno de los posibles aditivos para Al 2 O 3 Se han desarrollado compuestos cerámicos, varias formas de materiales de carbono de tamaño nanométrico, como fibra (nanotubos de carbono (CNT), nanofibras) y placas (grafeno), así como partículas. Esto permite la aplicación de materiales a base de carbono como aditivo para la fabricación de materiales que se ha informado recientemente.
En el desarrollo de compuestos de alúmina a base de carbono, Kumari et al. informaron sobre la mejora de la conductividad térmica del compuesto de nanotubos de carbono (CNT) -alúmina de 60 a 318% en comparación con la alúmina pura al cambiar el porcentaje en peso de la adición de CNT y la temperatura de sinterización [4]. Además, debido a las excepcionales propiedades tribológicas de los materiales compuestos a base de carbono para aplicaciones como la generación de energía, el transporte y la fabricación, muchos investigadores han centrado su interés en el desarrollo de compuestos a base de carbono [13, 14]. Se ha informado que las cerámicas con superficies reforzadas con carbono exhiben una resistencia al desgaste mejorada y un coeficiente de fricción reducido. A pesar de los controvertidos informes sobre la mejora de la resistencia mecánica utilizando nanofibras de carbono (CNF) en alúmina y zirconia, la mayoría de los autores han informado de mejoras en las propiedades mecánicas. Un estudio reciente de CNT sobre la propiedad de fluencia de la alúmina llegó a una conclusión opuesta, ya que se informa que, dependiendo de la cantidad de CNT añadida, la resistencia a la fluencia podría fortalecerse o debilitarse debido a un impedimento de deslizamiento del límite de grano o promoción del límite de grano. difusión o deslizamiento, respectivamente [15]. Mientras tanto, Crepo et al. informó que el compuesto de alúmina reforzado con óxido de grafeno exhibe una mejor resistencia a la fluencia que la alúmina reforzada con CNF [16]. Además, debido a las excelentes propiedades lubricantes del grafito, los materiales a base de carbono son un buen candidato para la aplicación de lubricantes sólidos. Durante la fricción seca, se informa que los compuestos a base de carbono generan una película lubricante a partir de la exfoliación del carbono y su incorporación con los restos cerámicos sobre el área de contacto afectada [13]. Sin embargo, la mayor parte del trabajo informado implica el uso de mezcla única mediante mezcla ultrasónica de suspensiones o un fresado mecánico convencional, y no se ha demostrado ningún trabajo sobre la decoración controlada de materiales de carbono en cerámica que conduzca a la formación de carbono controlado por microestructura. cerámica a base de. Por lo tanto, en este estudio, CNP-Al 2 O 3 los compuestos se fabricaron utilizando un conjunto de adsorción electrostática que ofrece más capacidad de control en su conjunto y diseño de compuestos. El Al 2 O 3 Las micropartículas utilizadas en este trabajo se obtuvieron mediante granulación de control de Al 2 de tamaño nanométrico O 3 partículas. Luego, el Al 2 granulado O 3 Las micropartículas obtenidas se utilizaron para la formación de carbono CNP-Al 2 O 3 compuesto. El estudio se llevó a cabo de forma sistemática variando la cantidad de nanoesferas de carbono de 0,3, 0,6 y 1,0% en volumen (porcentaje en volumen) y el tamaño medio de las partículas de alúmina utilizadas. A continuación, se caracterizaron las propiedades mecánicas de las muestras compuestas a base de carbono y se compararon con una muestra de alúmina monolítica mediante una prueba de flexión e indentación de tres puntos. También se discute y aclara la inter-correlación entre la microestructura obtenida y las propiedades mecánicas.
Métodos
Se adquirieron nanopartículas de alúmina con un diámetro medio de 150 nm de Taimei Kagaku Kogyo Co. y se utilizaron como precursor para obtener Al 2 granulado. O 3 micropartículas. La granulación se llevó a cabo mediante secado por atomización de una mezcla de Al 2 O 3 micropartículas con ligante acrílico. El Al 2 O 3 A continuación, se tamizaron las micropartículas para obtener tres diámetros medios diferentes 37, 62 y 98 µm que luego se utilizaron como partículas primarias. Se adquirió CNP con un diámetro medio de 260 nm de Tokai Carbon Co. y se utilizó como nanopartículas de aditivo. Como el CNP es hidrófobo y no se puede dispersar en un medio acuoso, primero se dispersó en una solución de SDC (desoxicolato de sodio) y luego se sometió a un tratamiento de hidrofilización para el recubrimiento posterior. Se añadieron cuarenta mililitros de una solución de SDC al 0,1% en peso a 1 g de CNP y se dispersaron por ultrasonidos durante 30 min. Luego, la solución se centrifugó y se lavó tres veces usando agua de intercambio iónico que se llevó a cabo agitando el agua con un mezclador. Después de eso, se llevó a cabo la modificación de la carga superficial usando policatión y polianión. Se utilizaron cloruro de polidialildimetilamonio (PDDA) (peso molecular medio 100.000 a 200.000, Sigma-Aldrich) y estirenosulfonato de polisodio (PSS) como polianión (peso molecular medio 70.000, Sigma-Aldrich) como policatión y polianión, respectivamente. Después de eso, el CNP recubierto con SDC se sumergió alternativamente en PDDA, PSS y PDDA para inducir una carga superficial positiva estable. Después del proceso de adsorción, la suspensión restante se secó y luego se recogió. En la primera investigación, el Al 2 O 3 Se utilizaron partículas con un diámetro de 62 μm y la viabilidad del control de cobertura de CNP en Al 2 O 3 se realizaron partículas. El porcentaje en volumen de CNP añadido fue 0,3, 0,6 y 1,0% en volumen. En la investigación del efecto de Al 2 O 3 tamaño, se estableció un 0,6% en volumen fijo de adición de CNP mientras que Al 2 O 3 Se utilizaron partículas con diferentes diámetros promedio de 37, 62 y 98 μm para la formación del material compuesto. El CNP-Al 2 O 3 Las partículas compuestas se prensaron primero uniaxialmente utilizando una matriz con un diámetro de 12 mm. La presión aplicada fue de 300 MPa y el tiempo de mantenimiento fue de 5 min. Posteriormente, el gránulo obtenido se introdujo en una matriz de grafito con polvo de h-BN para sinterización en caliente (Diavac Inc. Ltd.) La sinterización en caliente se realizó en atmósfera de vacío (8 × 10 -3 Pa) a 1350 ° C (velocidad de calentamiento de 10 ° C / min) durante 2 h con una presión de 30 MPa. Las morfologías del CNP-Al 2 O 3 Los materiales compuestos y la microestructura sinterizada obtenida se observaron utilizando un microscopio electrónico de barrido de emisión de campo S-4800 (FE-SEM, Hitachi S-4800). El potencial zeta se midió utilizando un Otsuka Electronics Co. Ltd., ELSZ-1 y Micro Tech Nission, ZEECOM Co. Ltd. En cuanto a la determinación de las propiedades mecánicas, el módulo de elasticidad de la muestra obtenida se midió mediante un ensayo de flexión de 3 puntos. . La muestra se cortó primero en una hoja de prueba en forma de tira y la dimensión se ajustó con precisión utilizando una amoladora de superficie. La dimensión de la muestra de ensayo preparada fue de 3 x 4 x 40 mm. Posteriormente, se realizó el pulido con alúmina de 0,5 mm y pasta de diamante con un grado de 30 y 9 µm, respectivamente. La prueba de flexión de 3 puntos se midió utilizando un comprobador compacto tipo Instron. Primero, el estrés ( σ ) se calculó utilizando la Ec. 1 donde, l , b y h son la distancia del tramo y las dimensiones de cada pieza de prueba, mientras que P representa la carga. A continuación, se trazó la relación entre la tensión y la deformación y se calculó el módulo elástico a partir de la pendiente de mínimos cuadrados. La velocidad de la cruceta se probó a 0,02 mm / min y el tramo a 30 mm.
$$ \ sigma =\ frac {3 lP} {2 bh} $$ (1)Las propiedades de dureza de la muestra compuesta se evaluaron adicionalmente usando indentación. El penetrador de Rockwell utilizado consistió en un diamante ( E i =1050 GPa, υ =0,20) con un radio de curvatura nominal, R =200 incrustado en una punta cónica con un ángulo de vértice de 120 °. El indentador se colocó en un probador de tipo Instron (Sanwa Instruments) y se introdujo a una velocidad de cruceta de 0,05 mm / sa una profundidad fija (20 µm). La carga obtenida durante la indentación se midió con una celda de carga (TCLZ-100KA, Tokyo Gakko), y la profundidad de la indentación se midió con un medidor de desplazamiento electrostático sin contacto (VE-222, Ono Sokki).
Resultados y discusión
La Figura 1 muestra el potencial zeta de carga superficial de Al 2 O 3 partículas y CNP después de recubrimientos alternos de PDDS y PSS, según corresponda. Se pudo observar que la alúmina y el CNP exhibieron un potencial zeta de + 55 y -55 mV, respectivamente, después de tres capas de recubrimiento. El potencial zeta logrado después de tres capas de recubrimiento tanto en CNP como en Al 2 O 3 micropartículas era estable. Las morfologías superficiales del CNP-Al 2 O 3 Los compuestos con diferente 0,3, 0,6 y 1,0% en volumen de adición de CNP se muestran en las imágenes SEM de la Fig. 2. A partir de las imágenes SEM de mayor aumento, se puede observar claramente que la cantidad de CNP que se adsorbe en la superficie de Al 2 O 3 la partícula aumentó con un porcentaje en volumen más alto de adición de CNP. Es importante tener en cuenta que los CNP se distribuyen de manera homogénea en todo el Al 2 O 3 superficie sin signos de aglomeración que retrata la ventaja del método EA para obtener una distribución uniforme y uniforme. El tamaño de partícula del CNP observado es de aproximadamente 260 nm. Fijando la adición de CNP al 0,6% en volumen y variando el tamaño del Al 2 O 3 micropartículas de 37, 62 y 98 μm, las distribuciones de CNP en la superficie de Al 2 O 3 Las partículas se muestran en las imágenes SEM en la Fig. 3. A partir de la observación de las imágenes SEM, se pudo ver que a medida que aumentaba el diámetro del tamaño de partícula, se observó que la cantidad de CNP adsorbido en la superficie aumentaba en consecuencia. Como mayor Al 2 O 3 las partículas poseen un área de superficie general más baja en comparación con el Al 2 más pequeño O 3 partículas, el área de superficie colectiva disponible para la adsorción de CNP también es menor en comparación con Al 2 más pequeño O 3 partículas. Por lo tanto, con una adición constante de 0,6% en volumen de CNP, se adsorbió una mayor cantidad de CNP en el área de superficie general más baja de Al 2 más grande O 3 partículas. Como resultado, la cantidad de CNP adsorbido en el Al 2 O 3 Se observa que la superficie aumenta con el tamaño del diámetro de Al 2 O 3 partículas que llevaron a una mayor densidad de adsorción de CNP en la superficie de 98 μm Al 2 O 3 partículas. Por otro lado, a medida que se redujo el tamaño de partícula, el área de superficie total disponible accesible para la adsorción de CNP en Al 2 O 3 aumenta y, por lo tanto, se observa una distribución escasa de CNP debido a la cantidad insuficiente de CNP en la suspensión (a un 0,6% en volumen fijo). La microestructura sinterizada obtenida con el CNP-Al 2 O 3 compuesto y gran aumento en la interfaz como se muestra en la Fig. 4. De la imagen SEM en la Fig. 4a, se puede ver que la microestructura obtenida refleja la forma del CNP-Al 2 obtenido O 3 compuesto. Es de destacar que los límites de los granos están conectados formando una red a lo largo de los límites de los granos. A partir de la observación de la red de CNP que se forma a lo largo de los límites de los granos, la homogeneidad de la distribución de CNP en la superficie de Al 2 O 3 se pueden determinar las partículas. Este resultado muestra que es factible obtener un material compuesto controlado por microestructura diseñando el precursor del compuesto. De la imagen SEM de mayor aumento en la Fig. 4b, la presencia de una capa de carbono entre la interfaz del Al 2 O 3 se puede observar el límite de grano. Esto muestra que la sinterización del CNP entre el Al 2 O 3 las partículas durante la sinterización por prensado en caliente condujeron a la formación de un recubrimiento uniforme de una capa de carbono a lo largo de los límites de los granos. También es importante tener en cuenta que el Al 2 O 3 la matriz obtenida es densa y bien sinterizada sin observación de poros como se muestra en la Fig. 4b. Esto se debe a la formación de Al 2 granulado densamente empaquetado. O 3 nanopartículas (150 nm) que permite una buena capacidad de sinterización que demostró la novedosa técnica de este trabajo. Los módulos elásticos del CNP-Al 2 O 3 compuesto obtenido usando una prueba de flexión de 3 puntos graficada como una función de Al 2 O 3 El tamaño de partícula y el porcentaje de cobertura de la superficie se muestran en la Fig. 5. De la Fig. 5a, el módulo elástico exhibido de la muestra fabricada usando Al 2 O 3 partículas es de aproximadamente 390 GPa, lo que es consistente con los resultados informados sobre Al 2 policristalino O 3 que está entre 300 y 400 GPa [6, 12]. El logro de este valor de módulo elástico se corrobora con la observación SEM donde se logró una buena microestructura y compactación utilizando Al 2 granulado. O 3 nanopartículas. En el estudio de Ashizuka et al. sobre el efecto de la porosidad sobre las propiedades mecánicas de las cerámicas de alúmina, el módulo de elasticidad de la cerámica sin porosidad (0%) es ligeramente inferior a aproximadamente 380 GPa [17]. En cuanto a los módulos elásticos del CNP-Al 2 O 3 compuestos, se puede ver que la propiedad podría controlarse ya que disminuyó linealmente con una mayor adición porcentual de volumen de CNP o con un incremento en el Al 2 O 3 tamaño de partícula. También se observó una tendencia similar en el trabajo de Shin et al., Donde los módulos elásticos de sus compuestos de óxido de grafeno reducido y de alúmina-CNT de pared simple se redujeron al aumentar el contenido de aditivos [6]. Como ambos factores (cantidad de CNP y tamaño de partícula de Al 2 O 3 ) influyen en gran medida en el área de superficie específica y conducen a una mayor adsorción de CNP en el Al 2 O 3 superficie de la partícula, esto inhibiría la sinterización de Al 2 O 3 y un posible efecto de deslizamiento de la capa de carbono dio como resultado módulos elásticos inferiores [6]. Este hallazgo es consistente con los reportados por Gopalan et al. donde el CNT utilizado en su compuesto retardó el crecimiento del grano pero no tuvo ningún efecto sobre el deslizamiento del límite del grano, lo que resultó en la aparición de superplasticidad [15]. Este hallazgo indica la posibilidad de alterar y controlar el módulo elástico de un Al 2 O 3 cerámica controlando la formación microestructural mediante el diseño del compuesto precursor utilizado en la formación de CNP-Al 2 O 3 . En la Fig. 5b, el gráfico de los módulos elásticos obtenidos en función del índice de cobertura de CNP en Al 2 O 3 se muestra. Se observa una correlación lineal entre el índice de cobertura de CNP y la resistencia del módulo elástico que corrobora aún más con los resultados antes mencionados. Por lo tanto, a partir de estos resultados, se demuestra que las propiedades mecánicas de un CNP-Al 2 O 3 La cerámica compuesta se puede controlar a través de la relación de cobertura de CNP, ya sea alterando la cantidad de adición de CNP o el tamaño de partícula de Al 2 primario O 3 . En la determinación de la microdureza del CNP-Al 2 O 3 muestras compuestas, una comparación entre Al 2 puro O 3 y CNP-Al 2 O 3 muestras fabricadas con 1,0% en volumen de adición de CNP con diferentes Al 2 O 3 Se realizaron tamaños de partícula de 37, 62 y 98 µm. Los resultados de indentación obtenidos se muestran en la Fig. 6. Los resultados obtenidos muestran que la muestra de alúmina pura exhibió el valor de dureza más alto mientras que la dureza de CNP-Al 2 O 3 muestras compuestas reducidas con Al 2 más grande O 3 tamaño de partícula. Esto se debe a la menor superficie total de Al 2 O 3 cuando el tamaño de las partículas aumenta dando lugar a una mayor cantidad de CNP adsorbido en la superficie. Posteriormente, la mayor cantidad de CNP en el Al 2 O 3 interfaz condujo a una dureza reducida debido a la inhibición de una sinterización efectiva entre el Al 2 O 3 interfaz o el deslizamiento de la capa de carbono conectada continua a lo largo de los límites de grano de Al 2 O 3. Por lo tanto, es crucial tener una distribución controlada de CNP en la superficie de Al 2 O 3 para inducir la formación de una microestructura deseada que conduzca a las propiedades mecánicas deseadas de CNP-Al 2 O 3 compuesto.
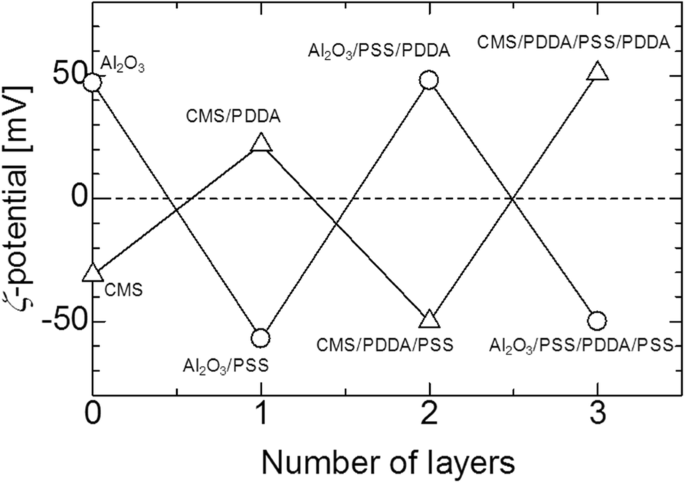
Potencial zeta del Al 2 controlado por carga superficial O 3 y nanopartículas de carbono
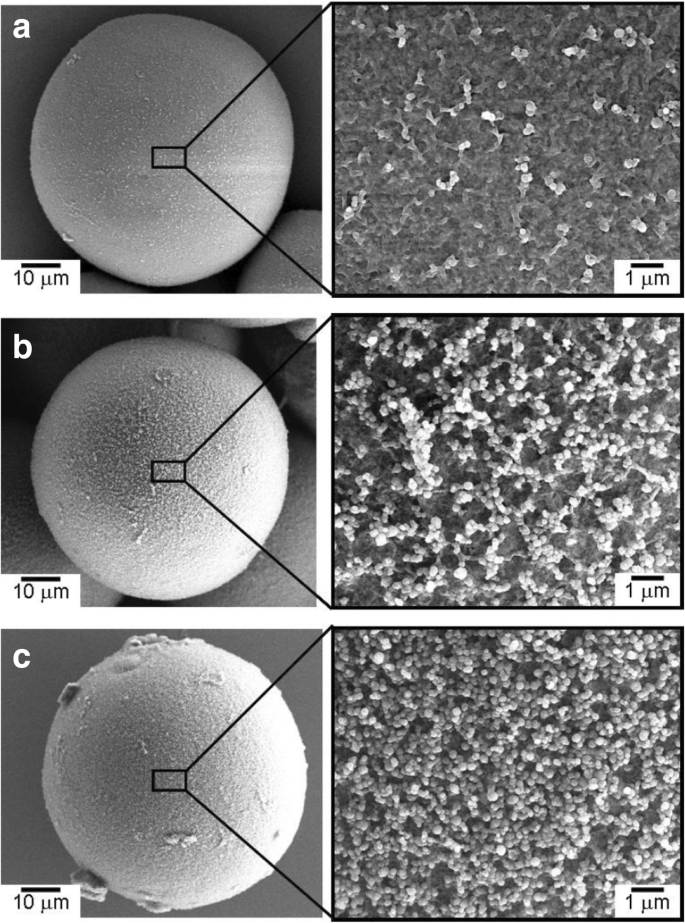
Imágenes SEM de la a 0,3% en volumen, b 0,6% en volumen y c 1.0% en volumen de CNP recubierto de Al 2 O 3 partícula de granulación con un diámetro medio de 62 μm
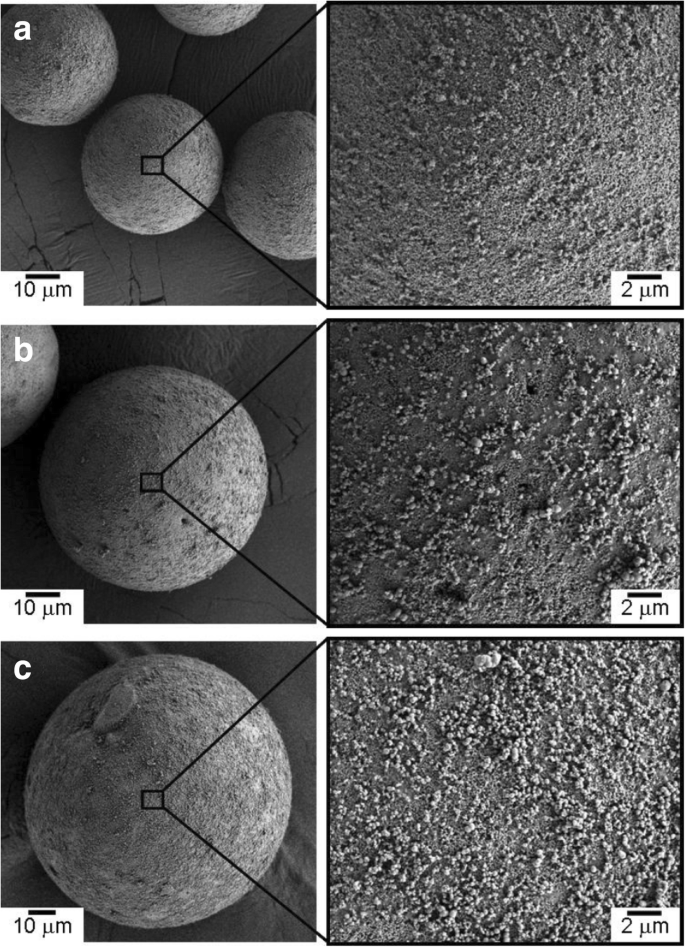
Imágenes SEM del 0,6% en volumen de CNP recubierto con Al 2 O 3 partículas de granulación con un diámetro medio de a 37, b 62 y c 98 micras
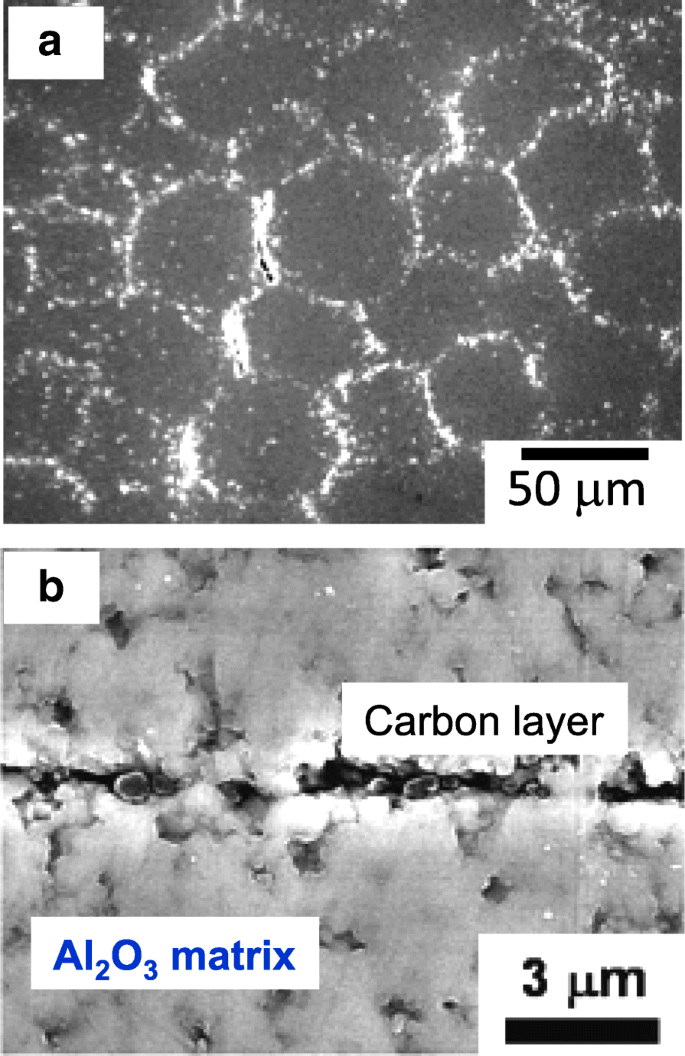
un Microestructura de 0,6% en volumen de CNP-Al 2 O 3 compuesto usando Al 2 O 3 con un diámetro medio de 62 μm. b Límite de grano de CNP-Al 2 O 3 compuesto. Se pudo observar una capa de carbono en la interfaz entre el Al 2 O 3 matriz
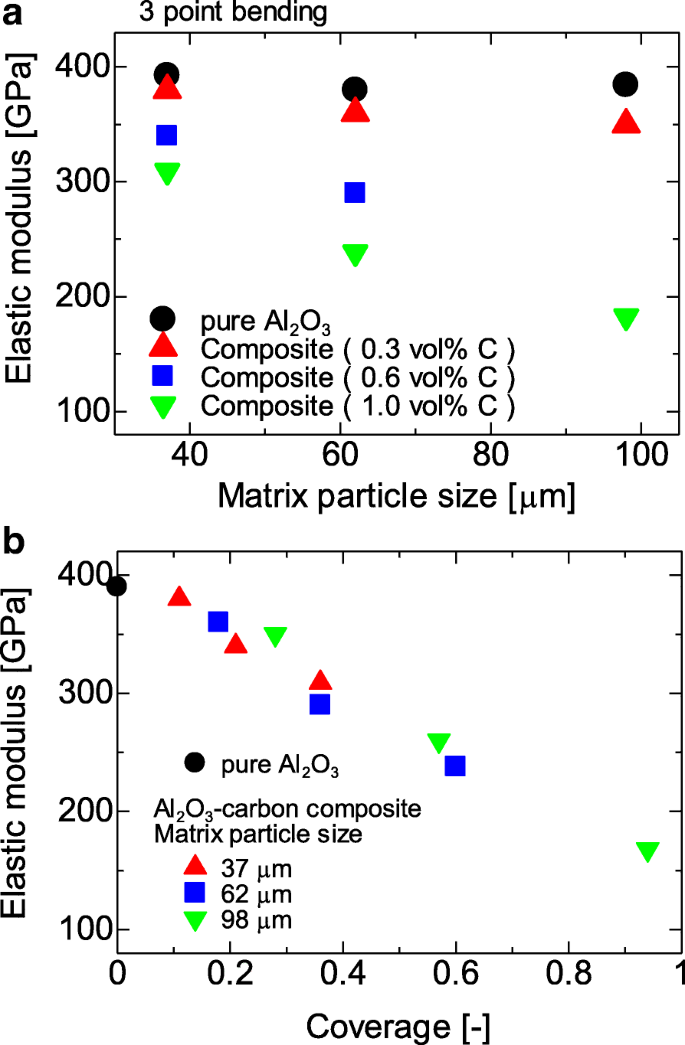
Módulos elásticos de CNP-Al 2 O 3 compuestos en función de a tamaño de partícula de la matriz y b Cobertura de CNP en Al 2 O 3 partículas
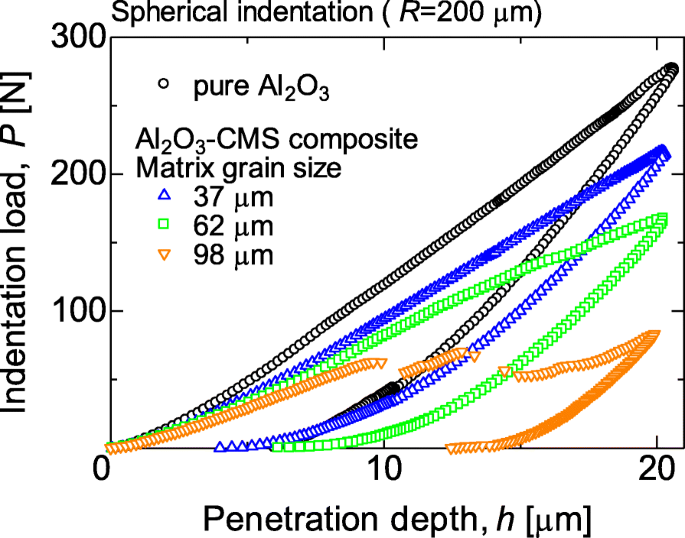
Curvas de histéresis de carga de indentación y profundidad de penetración de 1.0 vol% CNP-Al 2 O 3 compuestos
Desde la carga de sangría ( P ) -profundidad ( h ) curva ( P - h curva) durante el ciclo de carga y descarga, se podrían obtener cambios microestructurales y el mecanismo de deformación de la superficie [18]. La ecuación cuadrática simple que involucra la carga de indentación ( P ) y profundidad de penetración ( h ) que se muestra en la ecuación. 2 se puede utilizar para el análisis del proceso de carga [18,19,20].
$$ P \ propto {h} ^ 2 $$ (2)La carga de Al 2 monolítico O 3 demostró una correlación con la P - h curva similar a la ecuación cuadrática. 2 mientras que CNP-Al 2 O 3 compuesto fabricado con Al 2 O 3 partícula con el tamaño de 37 y 62 μm demostró una curva lineal con desviación del Al 2 monolítico O 3 curva de carga, respectivamente. Esto indica la presencia de CNP dentro de la microestructura (en la interfaz del límite del grano) que resultó en una deformación local a lo largo de los límites del grano. En cuanto a CNP-Al 2 O 3 compuesto fabricado con Al 2 O 3 con un tamaño de partícula de 98 μm, la alta densidad de CNP en los límites de los granos resultó en una discontinuidad de P - h curva de histéresis y demostró la dureza más baja debido a la aparición de deslizamiento del límite de grano o microfractura de la superficie.
Conclusiones
En este trabajo, una formación controlada factible de CNP-Al 2 O 3 compuesto por un método de adsorción electrostática. El Al 2 O 3 Las micropartículas utilizadas se obtuvieron por granulación de Al 2 de tamaño nanométrico (150 nm) O 3 partículas que permitieron una mejor compactación y sinterización. En la formación de cerámicas compuestas, parámetros que involucran la cantidad de CNP (0.3, 0.6, 1.0 vol%) y Al 2 granulado primario O 3 Se investigaron los tamaños de micropartículas (37, 62, 92 µm). Está demostrado que controlando la cantidad de aditivos CNP y Al 2 O 3 tamaño de micropartícula, se podría obtener una cobertura de superficie diferente que conduzca a la formación de microestructuras controladas con diferentes propiedades mecánicas. Usando el CNP-Al 2 homogéneo O 3 compuesto, se obtuvo una capa continua de carbono interconectada a lo largo de los límites de grano de Al 2 O 3 . Un Al 2 denso y compacto O 3 También se observó matriz debido a la buena sinterización de Al 2 O 3 nanopartículas. A partir de los resultados de una prueba de flexión e indentación de 3 puntos, se demostró el control de las propiedades mecánicas ajustando la cobertura de CNP en Al 2 O 3. El cambio en el módulo elástico se debió a la inhibición de la sinterización efectiva o al deslizamiento de la capa de carbono generada en el Al 2 O 3 interfaz. A partir de este estudio, hemos demostrado la viabilidad del diseño microestructural de cerámica con una interfaz interconectada utilizando CNP-Al 2 O 3 compuesto. Este método de diseño microestructural abrirá mayores posibilidades y potencial para el diseño de materiales a través del ensamblaje ascendente para inducir las propiedades deseadas para una amplia gama de aplicaciones.
Disponibilidad de datos y materiales
Todos los datos generados o analizados durante este estudio se incluyen en este artículo publicado (y sus archivos de información complementaria).
Historial de cambios
Abreviaturas
- CNP:
-
Nanopartículas de carbono
- PDDA:
-
Cloruro de polidialildimetilamonio
- PSS:
-
Estirenosulfonato de polisodio
- SDC:
-
Desoxicolato de sodio
- SEM:
-
Microscopio electrónico de barrido
Nanomateriales
- Las propiedades de los compuestos de resina y fibra y por qué son beneficiosos
- Propiedades paramagnéticas de nanomateriales derivados del fullereno y sus compuestos poliméricos:efecto de bombeo drástico
- Efecto sinérgico del grafeno y los MWCNT en la microestructura y las propiedades mecánicas de los nanocompuestos de Cu / Ti3SiC2 / C
- Preparación y propiedades ópticas de las películas GeBi mediante el método de epitaxia de haz molecular
- Síntesis sonoquímica de un solo paso y propiedades fotocatalíticas fáciles de compuestos de puntos cuánticos de grafeno / Ag3PO4
- Material y propiedades ópticas de los puntos cuánticos de carbono fluorescente fabricados a partir de jugo de limón mediante una reacción hidrotermal
- Influencia del parámetro de ajuste de pH para la modificación sol-gel en las propiedades estructurales, microestructura y magnéticas de la ferrita de estroncio nanocristalina
- Sobreenfriamiento de agua controlado por nanopartículas y ultrasonido
- Nanocristales de núcleo / capa de ZnInS / ZnS dopados con Cu sin Cd:Síntesis controlada y propiedades fotofísicas
- Síntesis controlada y propiedades de adsorción selectiva de las nanohojas de Pr2CuO4:una discusión del mecanismo
- Propiedades de los materiales de ingeniería:generales, físicas y mecánicas