Fabricación de nanocompuestos de Yolk-Shell Cu @ C como catalizadores de alto rendimiento en la carbonilación oxidativa de metanol a carbonato de dimetilo
Resumen
Se desarrolló una manera fácil de fabricar compuestos de cáscara de yema con núcleos de Cu sintonizables encapsulados dentro de esferas de carbono huecas (Cu @ C) con un diámetro promedio de aproximadamente 210 nm y un tamaño de cavidad de aproximadamente 80 nm. Durante la pirólisis, el nanoespacio confinado de la cavidad hueca asegura que el proceso de nucleación y crecimiento de los nanocristales de Cu tenga lugar exclusivamente dentro de las cavidades. El tamaño de los núcleos de Cu se puede ajustar fácilmente de 30 a 55 nm variando la concentración de sal de cobre. Al crear deliberadamente la porosidad de la cáscara a través de la activación química de KOH, en una relación de masa KOH / HCS optimizada de 1/4, el rendimiento catalítico para la carbonilación oxidativa de metanol a carbonato de dimetilo (DMC) de la muestra activada se mejora notablemente con TOF de hasta 8,6 h −1 a una conversión de metanol del 17,1%. El catalizador de cáscara de yema activado muestra propiedades catalíticas prometedoras que implican la reutilización con una ligera pérdida de actividad catalítica y una lixiviación insignificante de componentes activados incluso después de siete reciclados, lo que es beneficioso para la implementación de una producción limpia para el químico ecológico DMC a fondo.
Antecedentes
El carbonato de dimetilo (DMC) ha atraído mucha atención como un componente básico ampliamente utilizado debido a su excelente biodegradabilidad (por ejemplo, baja bioacumulación y persistencia) y baja toxicidad [1]. Las aplicaciones industriales potenciales del DMC cubren muchos campos, como el solvente no venenoso, sustituto alternativo del fosgeno, aditivo de combustible e intermedio para la síntesis de policarbonatos e isocianatos [2,3,4,5]. En vista de varios métodos sintéticos de DMC, la carbonilación oxidativa de metanol (MeOH) usando CO, O 2 , y MeOH como materias primas ha estado representando uno de los procesos favorables propuestos debido a la alta tasa de utilización de la fuente de carbono y los beneficios ambientales. Los catalizadores utilizados en esta reacción se pueden clasificar principalmente en dos tipos:catalizadores que contienen cloro y catalizadores sin cloro. Dado que existen algunos problemas, como problemas corrosivos graves, deterioro de la calidad del producto y desactivación del catalizador, que se derivan de la pérdida de cloro de los catalizadores que contienen cloro, los catalizadores libres de cloro se han estudiado exhaustivamente [6, 7]. Se ha demostrado que el cobre o el óxido de cobre soportados con carbón activado (AC) tienen una actividad catalítica prometedora para la síntesis de DMC [8,9,10], y los investigadores han sugerido que el Cu es el centro activo de esta reacción [10,11,12,13]. Sin embargo, la desactivación de los catalizadores de cobre soportados generalmente se atribuye a la aglomeración de partículas de cobre, la pérdida de especies activas y el cambio del estado químico del cobre, entre los cuales, el primero es más grave. Para superar estos inconvenientes, el diseño y la fabricación de nanopartículas encapsuladas en una capa protectora es beneficioso para reforzar la actividad catalítica y la estabilidad de los centros reactivos en la carbonilación oxidativa de metanol a DMC desde el punto de vista tecnológico.
En esta línea, las nanoestructuras de cáscara de yema (YSN) o nanocompuestos tipo cascabel, en los que las nanopartículas centrales (NP) están encapsuladas por una capa externa con un espacio libre intersticial entre ellas, han sido particularmente populares debido a sus nanoestructuras jerárquicas / multinivel únicas. , y las propiedades ópticas y eléctricas que lo acompañan y un gran potencial en la aplicación catalítica [14]. La capa protectora de los YSN puede mantener estable de forma eficaz el elemento central incluso en condiciones adversas y exponer suficientemente su superficie activa [15]. Se espera que el espacio vacío cerrado sea útil para el almacenamiento químico, la compartimentación y el confinamiento de interacciones huésped-huésped y, lo que es más importante, proporcionar un entorno único para crear acciones concertadas entre el núcleo y una capa permeable [16]. Estas notables características de textura permiten que los YSN funcionen como candidatos prometedores para satisfacer demandas como la estabilidad sinterizada y la reutilización para aplicaciones en catálisis. Entre ellas, las nanoestructuras de cáscara de yema y carbono han atraído inmediatamente un interés considerable debido a la conductividad inherente, así como a la excelente estabilidad química y térmica del recubrimiento de carbono [17,18,19,20,21].
Recientemente, Lu y colaboradores han informado de la preparación de esferas huecas a través de un ensamblaje inducido por interacción débil ácido-base con el uso de ácido oleico como plantilla blanda y ácido dihidroxibenzoico funcional (DA) como precursor [22]. En este documento, ampliamos su trabajo para desarrollar un fácil hacia los YSN con un tamaño de núcleo de Cu sintonizable encapsulado dentro de esferas de carbono huecas (HCS) (Cu @ C) mediante el empleo de una estrategia de envío en botella. La porosidad de la capa de los catalizadores heterogéneos de Cu @ C se puede ajustar mediante la activación de KOH, y también se investigan sus efectos sobre el rendimiento catalítico y la estabilidad en la síntesis de DMC.
Métodos
Productos químicos
El ácido 2,4-dihidroxibenzoico (DA) se obtuvo de J&K Scientific Ltd. Ácido oleico, solución de amoníaco (25%), formaldehído, nitrato de cobre (Cu (NO 3 ) 2 · 3H 2 O), hidróxido de potasio (KOH) y metanol (MeOH) se obtuvieron de Sinopharm Chemical Reagent Co. Ltd. Todos los productos químicos eran de grado analítico y se usaron sin ninguna purificación adicional. En todos los experimentos se usó agua desionizada obtenida del sistema Milli-Q (Millipore, Bedford, MA). O 2 (> 99,99%) y CO (> 99,99%) fueron suministrados por Beijing ZG Special Gases Science &Technology Co. Ltd.
Síntesis de esferas de carbono huecas (HCS)
Las esferas poliméricas huecas (HPS) con un núcleo hueco y una cubierta de polímero se prepararon primero usando ácido oleico como plantilla blanda y resina fenólica como precursor de carbono siguiendo el procedimiento informado por Lu et al. [22]. En un procedimiento típico, se disolvieron 2,5 mmol de ácido 2,4-dihidroxibenzoico y 7,5 mmol de formaldehído en 95 ml de agua desionizada. Se añadió un volumen de 5 mL de una solución acuosa que contenía 56 μL de ácido oleico y 180 μL de solución de amoníaco (25%) a la solución preparada anteriormente a 30 ° C con agitación lenta durante 30 min. A continuación, la mezcla se transfirió a un autoclave envejecido hidrotermalmente durante 4 ha 140 ° C. Después de centrifugar, lavar con agua desionizada y etanol, secar a 50 ° C durante la noche y luego pirolizar a 700 ° C durante 2 h bajo un flujo de nitrógeno, se obtuvo el HCS.
Síntesis de materiales nanocompuestos de Cu @ C
Típicamente, primero se dispersaron 0.3 g de los HCS preparados en 30 mL de solución de nitrato de cobre con un rango de concentración diferente de 0.03 a 0.24 M. Luego, la mezcla se transfirió a un autoclave para someterse a una impregnación hidrotermal a 100 ° C durante 10 h. La muestra impregnada resultante, denominada HCS-Cu 2+ , se recuperó por el mismo método que HPS. Después de calcinado a 400 ° C durante 2 h bajo H 2 / N 2 (10% / 90%), finalmente, se obtuvieron los nanocompuestos de cáscara de yema Cu @ C-X (X =0.03, 0.06, 0.12, 0.24).
Síntesis de catalizador Cu @ A-HCS con esfera de carbón activado con KOH como soporte
Se intenta el tratamiento de HCS con KOH, con la intención de modificar los caracteres del soporte de carbono y afectar aún más el rendimiento del catalizador de Cu. Normalmente, se mezclaron 0,3 g de HCS con 0,15 g de KOH físicamente en ausencia de agua. Después del pretratamiento, la muestra se calentó en una corriente de nitrógeno de 80 ml / min con una velocidad de rampa de 10 ° C / min hasta 700 ° C durante 2 hy luego se enfrió a temperatura ambiente. Los carbonos postratados con KOH se lavaron repetidamente con HCl diluido y posteriormente con agua destilada hasta que no se detectó ión de cloro (AgNO 3 prueba). Después de secar a 60 ° C durante la noche, se usó una solución de nitrato de cobre 0.12 M durante la impregnación hidrotermal y otros procedimientos fueron idénticos a los de [email protected], finalmente produciendo las muestras modificadas indicadas como Cu @ A-HCS.
El rendimiento catalítico de Cu @ C-X (X =0.03, 0.06, 0.12, 0.24) y Cu @ A-HCS
La carbonilación oxidativa de metanol se llevó a cabo en un autoclave de acero inoxidable de 25 ml revestido con teflón y equipado con un agitador magnético. En un experimento típico, se cargaron 0,2 g de catalizador y 10 ml de metanol en el autoclave, que luego se selló herméticamente, se purgó tres veces con CO y luego se presurizó a 3,0 MPa con CO y O 2 (P CO :P O2 =2:1) a temperatura ambiente. La reacción procedió a 120 ° C con agitación continua a 750 rpm durante 1,5 h. Después de la reacción, el reactor se enfrió a temperatura ambiente y se despresurizó. Los catalizadores se separaron por filtración. Las concentraciones de productos en el filtrado se determinaron mediante cromatografía de gases (GC) utilizando un detector FID. La reciclabilidad del catalizador usado se estudió realizando una serie de corridas consecutivas.
La reacción principal de la carbonilación oxidativa de metanol a carbonato de dimetilo se muestra a continuación:
2CH 3 OH + 1/2 CO + O 2 =(CH 3 O) 2 CO + H 2 O.
La concentración de cobre, conversión de MeOH (C MeOH ), Selectividad DMC (S DMC ) y la frecuencia de rotación (TOF) se calcularon mediante las siguientes ecuaciones:
La concentración de cobre (C Cu , mmol / g) =Contenido de Cu (% en peso) / 63,55 × 1000.
Conversión de MeOH (C MeOH ,%) =metanol reaccionado / metanol introducido × 100%.
Selectividad DMC (S DMC ,%) =2 DMC producido / metanol reaccionado × 100%.
Frecuencia de rotación =DMC producido / (la cantidad molar de cobre × tiempo de reacción).
Caracterización
Los patrones de difracción de rayos X (XRD) se registraron en un difractómetro Rigaku D-Max 2500, utilizando Cu K Radiación α ( λ =0,154 nm) a 40 kV y 100 mA, con una velocidad de exploración de 4 ° min −1 en 2 θ de 5 ° –85 °. El análisis de microscopía electrónica de transmisión (TEM) se llevó a cabo en un microscopio electrónico de transmisión de emisión de campo JEM 2100F (JEOL, Tokio, Japón) que funcionaba a 200 KeV. Las muestras de TEM se prepararon sumergiendo rejillas de Cu recubiertas con C en soluciones de etanol de muestras y secando a temperatura ambiente. El análisis termogravimétrico (TG) se realizó en un analizador termogravimétrico, STA 449 F3 Jupiter (NETZSCH), con un N 2 o caudal de aire de 50 ml / min. Las áreas superficiales y los volúmenes de poros se determinaron a partir de isotermas de adsorción de nitrógeno a 77 K usando el analizador de área superficial 3H-2000PS2 (Beishide). Las áreas de superficie específicas de Brunauer-Emmett-Teller (BET) se calcularon utilizando datos de adsorción en un rango de presión relativa de P / P 0 =0,04-0,3. Las curvas de distribución del tamaño de los poros de los mesoporos se calcularon mediante el método BJH (Barrett-Joyner-Halenda) a partir de la rama de adsorción. Los volúmenes de poros totales se estimaron a partir de la cantidad de nitrógeno adsorbido a una presión relativa ( P / P 0 ) de 0,99. El contenido de cobre se determina disolviendo el catalizador en una mezcla de ácido fuerte seguido de análisis de espectrometría de adsorción atómica (AAS) utilizando equipo SpectrAA-220 AAS. El análisis del producto de reacción se realizó mediante cromatografía de gases (GC; Agilent 6890) utilizando un detector FID.
Resultados y discusión
Parámetros de textura y estabilidad térmica del soporte preparado
El área de superficie BET y el volumen de poros de las muestras involucradas en las diferentes etapas de preparación se resumen en la Tabla 1. Como se ve en la Fig. 1a y la Tabla 1, el HPS obtenido tiene áreas de superficie BET bajas (~ 23 m 2 g −1 ). Por tanto, es difícil continuar con la introducción de los precursores del catalizador mediante el método de impregnación convencional. Por lo tanto, utilizamos un proceso de impregnación hidrotermal para mejorar la capacidad de difusión de modo que el precursor de cobre se pueda introducir con éxito en la cavidad del HPS. El área de superficie BET de HPS y HPS-Cu cambió de 23 a 15 m 2 g −1 certificó la declaración. Además, las imágenes TEM en la Fig. 2 confirman aún más las nanopartículas de Cu formadas exclusivamente dentro de los confines de la capa de carbono.
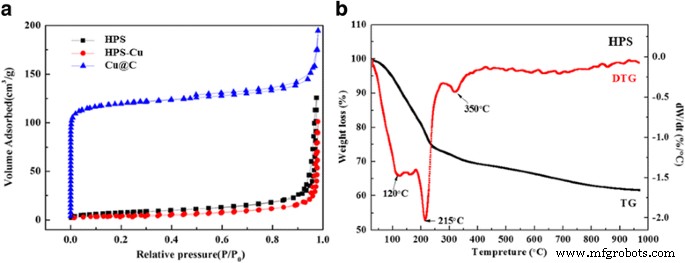
un N 2 isoterma de adsorción-desorción de los productos obtenidos tras cada paso:HPS, HPS-Cu 2+ y Cu @ C. b Perfiles TG-DTG de HPS
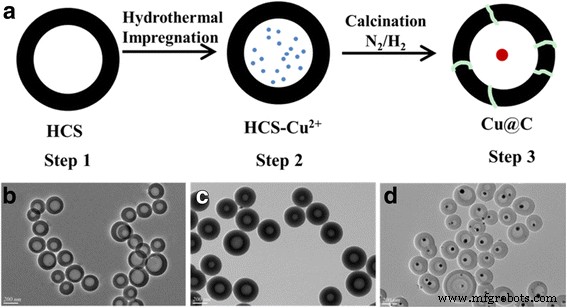
un Ilustración esquemática para la síntesis de nanocompuestos de Cu @ C en condiciones de impregnación hidrotermal. Imágenes TEM de los productos obtenidos después de cada paso: b HCS, c HCS-Cu 2+ y d Cu @ C
TG investiga el proceso de carbonización del HPS. La figura 1b muestra el resultado de TG-DTG en N 2 . A lo largo de todo este intervalo, la mayor pérdida de HPS aparece cerca de los 215 ° C y se completa alrededor de los 350 ° C. Esto puede atribuirse a la descomposición del ácido oleico incrustado dentro del HPS y la carbonización de la estructura del polímero [22]. Por lo tanto, en comparación con las curvas de TG de los catalizadores de Cu @ C (ver en la Fig. 5b), para asegurar la carbonatación completa de HPS y evitar la agregación de las nanopartículas de Cu, se determinó que 400 ° C era la temperatura óptima de preparación.
Propiedades estructurales de los nanocompuestos de Cu @ C
Tomado [email protected] nanocompuesto de cáscara de yema como ejemplo, el procedimiento de síntesis para la preparación de estructuras de cáscara de yema con Cu NP encapsulado por cáscara de carbono, siguiendo una estrategia de envío en botella, se ilustra en la Fig. 2a. La Figura 2b, c muestra imágenes TEM típicas del producto resultante obtenido en cada paso. Como se ve, se han sintetizado con éxito HCS con un tamaño uniforme de aproximadamente 210 nm (Fig. 2b). Durante el proceso de impregnación hidrotermal, no se pueden observar diferencias obvias entre HCS y HCS-Cu 2+ (Figura 2c). Sin embargo, después de la calcinación, la morfología hueca se mantiene, pero se pueden observar NP de Cu debido a la descomposición de las sales de cobre. Finalmente, se logra el Cu @ C con estructura de cáscara de yema (Fig. 2d) con un diámetro de ~ 200 nm y un tamaño de cavidad de ~ 80 nm. La microscopía electrónica de transmisión de alta resolución (HRTEM) (Fig. 3b) muestra que las partículas del núcleo tienen un espacio de 0,18 nm indexado al plano Cu (2 0 0). Esto es consistente con los resultados de XRD (Fig. 3c), donde la difracción alcanza un máximo de 2 θ =43,3 °, 50,4 ° y 74,1 ° se volvieron observables porque Cu 2+ especies en el precursor (HCS-Cu 2+ ) se reducen a metal Cu bajo una atmósfera reductora, correspondiente a los planos cristalinos específicos (1 1 1), (2 0 0) y (2 2 0) de Cu, respectivamente, que se basa en la tarjeta JCPDS 04-0836 . El N 2 La isoterma de adsorción-desorción del [email protected] resultante presenta una isoterma de tipo I, lo que demuestra que hay abundantes microporos en las capas de carbono de [email protected] (Fig. 3d). Esta muestra tiene una superficie BET de 365 m 2 / g acompañado de un volumen de poro de 0,23 cm 3 /gramo. El área superficial específica baja junto con la microporosidad estrecha generalmente se señalan como principales desventajas, lo que limita sus aplicaciones, que se discutirán a continuación. Los parámetros de textura detallados de las muestras se resumen en la Tabla 2.
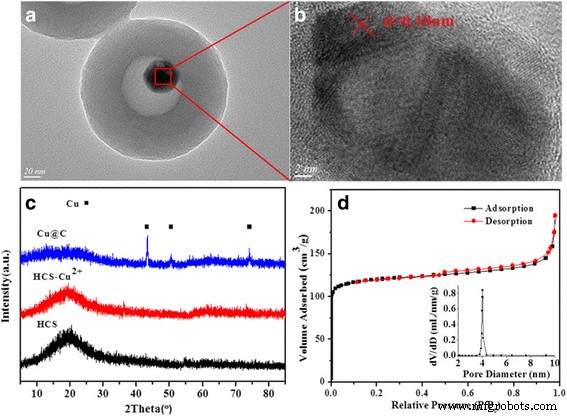
un , b Imágenes TEM del núcleo de cobre en [email protected]. c Patrones XRD de los productos obtenidos después de cada paso:HCS, HCS-Cu 2+ y [email protected]. d N 2 isoterma de adsorción-desorción y distribución del tamaño de poro de [email protected]
La vía mecanicista para la formación de un solo Cu NP dentro de la capa de carbono puede explicarse por el proceso de nucleación y crecimiento confinado. En el progreso de la pirólisis, muchos núcleos minúsculos iniciales de CuO se formaron y distribuyeron completamente dentro de la cavidad hueca debido a la descomposición del Cu incorporado (NO 3 ) 2 moléculas. Cuando el agente reductor H 2 se difunde en la cavidad, los núcleos de CuO formados se reducen aún más a núcleos metálicos de Cu, que tienden a migrar y agregarse para formar partículas más grandes. Una vez que se forman los más grandes, los núcleos de Cu restantes dentro de la cavidad serán absorbidos sucesivamente en la superficie de las partículas preformadas, lo que da como resultado el crecimiento de nanocristales de Cu. También se ha propuesto un mecanismo similar en otro lugar [23]. Con base en el proceso de nucleación y crecimiento, se podría inferir que el tamaño del núcleo de Cu resultante se puede controlar ajustando la cantidad de precursor de sal de cobre alojado en la cavidad confinada.
Control de tamaño del núcleo de Cu
Variando Cu (NO 3 ) 2 Se obtuvieron concentraciones de 0.03 a 0.24 M, una serie de nanocompuestos de cáscara de yema, denominados Cu @ C-X (X =0.03, 0.06, 0.12, 0.24). TEM examinó la morfología y el tamaño de los productos. Como se ve en la Fig. 4a-d, casi todas las nanoesferas huecas consisten en una sola partícula en su interior. Sin embargo, el tamaño del núcleo de Cu de las nanoesferas resultantes aumenta de 30 ± 1,3 a 55 ± 2,5 nm (Fig. 4e-h) con un Cu (NO 3 creciente) ) 2 concentraciones, determinadas a partir de imágenes TEM teniendo en cuenta al menos 150 partículas. En particular, una fracción de esferas de carbono huecas (HCS) coexisten con YSN para el bajo Cu (NO 3 ) 2 concentración (Fig. 4a). Además, unas pocas NP de Cu pequeñas decoradas en la superficie exterior de la capa de carbono (Fig. 4d), que podrían ser causadas por la descomposición y agregación del Cu residual (NO 3 ) 2 fuera del caparazón.
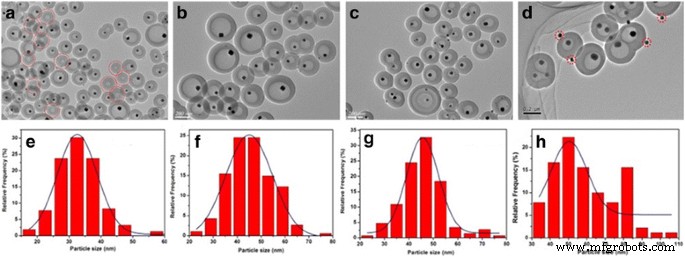
Imágenes TEM e histogramas de distribución de tamaño correspondientes de NP de Cu en muestras: a , e [email protected], b , f [email protected], c , g [email protected] y d , h [email protected]
La Figura 5a muestra los patrones de XRD de Cu @ C-X tal como se preparó (X =0.03, 0.06, 0.12, 0.24). Todas las muestras presentan tres picos de reflexión típicos indexados a cristales de Cu (tarjeta JCPDS nº 04-0836). A medida que aumenta la concentración de sal de cobre, los picos de difracción son mucho más fuertes y nítidos, mientras que el tamaño de Cu NP aumenta de 26,6 a 52,2 nm mediante el uso de la ecuación de Scherrer basada en el pico más fuerte de los patrones, que concuerda bien con los resultados de TEM. . Además, se realizó un análisis de TG para determinar el contenido de Cu de las nanoesferas en la Fig. 5b. Suponiendo que los residuos consisten completamente en CuO, las cantidades de carga de Cu de Cu @ CX (X =0.03, 0.06, 0.12, 0.24) se calculan en aproximadamente 5.9, 7.5, 8.0 y 9.9% en peso, respectivamente, lo cual es idéntico a los valores determinados a partir del análisis AAS.
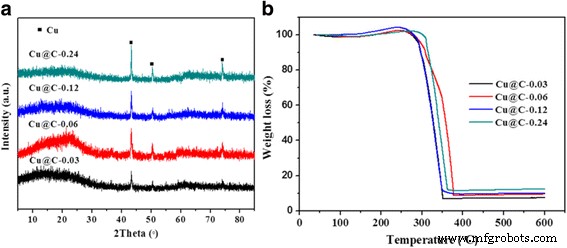
un Patrones XRD y b Curvas TG de muestras:[email protected], [email protected], [email protected], [email protected]
Rendimiento catalítico de Cu @ C-X (X =0.03, 0.06, 0.12, 0.24)
El catalizador de Cu @ C preparado tal como se preparó se probó para la carbonilación oxidativa en fase líquida de metanol a DMC (Tabla 2). Inesperadamente, aunque era mejor que otros, el catalizador [email protected] solo dio una conversión de metanol extremadamente ineficaz de 0,82%. La baja actividad catalítica podría estar asociada con la falta de suficiente porosidad y gran volumen de poros en la cáscara. Hasta donde sabemos, los poros ubicados en el caparazón actúan como canales que conectan el vacío de las esferas con el entorno externo [24]. Aunque el espesor de capa de [email protected] es ~ 15 nm, la falta de porosidad suficiente (el volumen de poro estructural es 0.23 cm 3 / g con una superficie específica baja de 365 m 2 / g) restringe la cantidad de moléculas reactivas para que se difundan en las cavidades y entren en contacto con el componente activo enterrado de los núcleos de Cu. Por lo tanto, es fundamental crear más porosidad en las conchas para facilitar el transporte de masa. Como se sabe, la activación de KOH es un método bien establecido para ajustar la porosidad de los materiales de carbono [25, 26, 27]. Con este método, se pueden introducir microporos y mesoporos en el carbono, junto con un aumento significativo de la superficie específica y el volumen de los poros [28]. Durante el procedimiento de activación, la cantidad de KOH generalmente se considera un factor crítico para influir en la estructura porosa; por lo tanto, se han realizado diferentes relaciones de masa de KOH / HCS para optimizar el [email protected] activado.
Propiedades fisicoquímicas de Cu @ A-HCS
La imagen TEM (Fig.6a) muestra que la muestra de Cu @ A-HCS activada mantiene la morfología esférica en la relación de masa más baja de KOH / HCS (1/4), pero grabada parcial o severamente con una relación de masa de KOH / HCS superior a 1 / 2 (Consulte la información complementaria Fig. 2a, b). Este resultado está de acuerdo con informes anteriores de que una cantidad excesiva de KOH conducirá a una mayor quema de carbono y destruirá la morfología [29]. Curiosamente, para los nanocompuestos de Cu @ A-HCS, después de la activación, las partículas de cobre altamente dispersas se incrustan predominantemente en la cubierta de las esferas huecas, que coexisten con varias encapsuladas en las cavidades. En comparación con [email protected], las NP de Cu que insertan la cáscara muestran un tamaño de partícula relativamente más pequeño centrado en 18 ± 2 nm (Fig. 6b) porque la matriz de la cáscara evita que los pequeños cúmulos de Cu crezcan más. La existencia de puntos blancos en el caparazón sugiere la existencia de microesporas desordenadas. La Figura 6c muestra el N 2 -isotermas de adsorción-desorción de Cu @ C-HCS, que exhiben curvas representativas de tipo IV asociadas con la característica de mesoporo, revelando que las muestras activadas poseen estructuras jerárquicamente micro- / mesoporosas. Además, se puede encontrar que después de la activación de KOH a 700 ° C durante 2 h, el área de superficie de A-HCS aumentó de 471 a 989 m 2 / g, incluso más grande que el carbón activado (812 m 2 / g) y el volumen de microporos (V mic ), el volumen del mesoporo (V mes ) y el volumen total (V T ) también aumentó, pero la proporción de V mic a V T tiende a disminuir. Este resultado indica que se crean más mesoporos después de la activación de KOH, lo que posiblemente esté relacionado con el ensanchamiento de microporos o la creación de mesoporos por la presencia de KOH [30]. La gran superficie típica y la porosidad desarrollada de los catalizadores Cu @ A-HCS favorecen la dispersión de la fase activa sobre el soporte, garantizan la rápida transferencia de materia entre el catalizador confinado y el entorno externo (reactivos) y aumentan su resistencia a la sinterización. con cargas elevadas de metal [31]. Como lo confirma el patrón XRD en la Fig. 6d de Cu @ A-HCS, todos los picos pueden indexarse indiscutiblemente a Cu cúbico (JCPDS 04-0836); mientras tanto, el ensanchamiento de los picos característicos implica la formación de NP de Cu de pequeño tamaño. De hecho, el tamaño medio de las NP de Cu en Cu @ A-HCS se estima en 15 nm según la ecuación de Scherrer, lo que concuerda con el resultado obtenido por TEM. Como se predice, los catalizadores Cu @ A-HCS con 11% en peso de Cu determinado por AAS se obtuvieron usando el mismo método, mayor que [email protected]. Más importante aún, durante el proceso de activación, los grupos funcionales que contienen oxígeno posiblemente originados a partir de la activación de KOH se introducen inevitablemente en los HCS [27]. En general, la generación de grupos de superficie, el aumento de la superficie y el volumen de los poros, sinérgicamente dan como resultado una alta dispersión de Cu NP, lo que es beneficioso para la promoción de la actividad catalítica [32,33,34]. Las propiedades de textura detalladas se resumen en la Tabla 3.
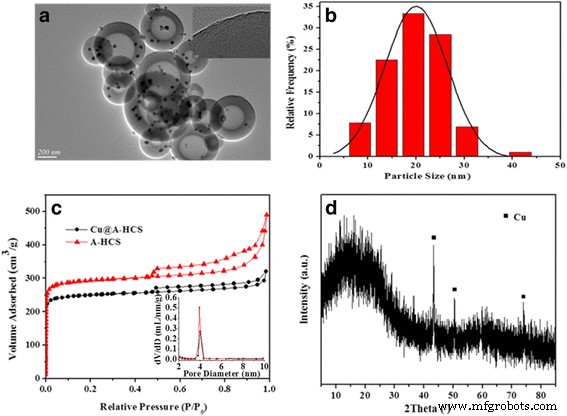
un Imagen TEM de Cu @ A-HCS y b su correspondiente tamaño de partícula de Cu. c N 2 isotermas de adsorción-desorción y distribuciones del tamaño de poro de A-HCS y Cu @ A-HCS. d Patrones XRD del catalizador Cu @ A-HCS
Rendimiento catalítico de Cu @ A-HCS
Los rendimientos catalíticos de A-HCS y Cu @ A-HCS se resumen en la Tabla 4. Como se muestra en la Tabla 4, está claro que el soporte A-HCS no exhibió actividad catalítica en la síntesis de DMC. Como era de esperar, las propiedades catalíticas de la muestra activada mejoraron drásticamente en comparación con las no activadas. Es de destacar que en comparación con 2.04 h −1 y 4,38% para Cu@C-0,12, la actividad incipiente de Cu @ A-HCS exhibe un aumento de casi cuatro veces en el TOF de 8,6 h −1 acompañado de un aumento dramático correspondiente en C MeOH del 17,1%, respectivamente, en las mismas condiciones. Estos notables resultados son razonables al considerar el aumento en el área de la superficie y los volúmenes de poros de las capas de carbono pueden adsorber positivamente más moléculas de reactivo de la solución a granel, facilitar las tasas de difusión a través de los canales de manera significativa y enriquecerlas en el espacio vacío de la solución. catalizadores, lo que da como resultado una mayor concentración de reactivo para catálisis confinada accesible. Un catalizador con una vida útil razonablemente larga es fundamental para su aplicación en la industria. El catalizador elegido es una muestra de Cu @ A-HCS activada con una actividad prometedora para probar la durabilidad en un sistema por lotes descrito anteriormente. Los catalizadores heterogéneos a menudo sufren una disminución de la actividad como una extensa lixiviación de especies de metales activos durante las reacciones [35]. E igualmente importante es la estabilidad frente a la coalescencia del catalizador basado en nanocristales [36]. En nuestro caso, como se resume en la Tabla 3, el catalizador de Cu @ A-HCS recuperado (separado por filtración) mantiene una actividad catalítica mucho más alta que el CuCl incluso después de siete corridas (entradas 2-8), y la lixiviación promedio de Cu, que es el componente activo del catalizador es de alrededor del 0,004%, permaneciendo casi igual al nuevo. Mientras tanto, la estructura cristalina y la morfología de los catalizadores apenas cambiaron después de ciclos sucesivos (Archivo adicional 1:Figura S2). Aparentemente, la presencia de la capa de carbono porosa es suficiente para estabilizar las especies metálicas activas evitando su agregación y lixiviación; al mismo tiempo, las carcasas son lo suficientemente permeables para que las superficies catalíticas sigan siendo accesibles y ventajosas para los reactivos y productos [12]. Por lo tanto, los catalizadores YSN son sistemas catalíticos efectivos y no corrosivos, donde los NP de Cu como materiales del núcleo encapsulados en la cavidad de los HCS proporcionan centros reactivos, y la capa de carbono poroso evita que el núcleo se agregue y lixivia en las condiciones de reacción.
Conclusiones
En resumen, hemos presentado una estrategia fácil de enviar en una botella para la fabricación de nanoestructuras de cáscara de yema de carbono compuestas de NP de Cu con tamaño personalizado en distribuciones estrechas ajustando la concentración de sales de cobre. Como se demostró, las propiedades catalíticas de este sistema tipo cascabeleo en la carbonilación oxidativa de metanol a DMC dependen en gran medida de la porosidad. La muestra activada con un área de superficie extremadamente alta permite la creación de nanoreactores confinados altamente eficientes para reacciones catalíticas con una conversión considerablemente más alta (17,1%) y TOF (8,6 h −1 ), una larga vida útil y una lixiviación insignificante en cada ciclo, lo que indudablemente satisface la producción limpia del químico verde DMC. Además, la ruta de síntesis descrita en este documento puede abrir nuevas oportunidades para preparar nanoestructuras de cáscara de yema con varias composiciones confinadas dentro de la cáscara de carbono.
Nanomateriales
- Nanocups pueden doblar la luz
- Síntesis fácil de WS2 / Bi2MoO6 heteroestructurados como fotocatalizadores impulsados por luz visible de alto rendimiento
- Nuevos nanocompuestos de poliestireno con polianilina dopado con ácido lauril sulfúrico
- Fabricación de alto rendimiento de nanofibras de calidad utilizando un electrohilado de superficie libre modificado
- Rendimiento fotocatalítico de luz visible de nanocompuestos de ZnO / g-C3N4 dopado con N
- Fabricación y caracterización de un nuevo catalizador anódico compuesto de nanofibras de carbono Tio2 para celdas de combustible de metanol directo mediante el método de electrohilado
- Nanocompuestos magnéticos de poli (N-isopropilacrilamida):efecto del método de preparación sobre las propiedades antibacterianas
- Fabricación, caracterización y citotoxicidad de nanopartículas de carbonato de calcio derivadas de concha de oro-berberecho conjugado de forma esférica para aplicaciones biomédicas
- La fabricación y el rendimiento de absorción de ondas electromagnéticas de alta eficiencia de los nanocompuestos estructurados CoFe / C Core-Shell
- Fabricación y caracterización de nanoclips de ZnO mediante el proceso mediado por poliol
- Detector UV autoamplificado de alto rendimiento basado en matrices de nanomace SnO2-TiO2