La utilidad se beneficia del monitoreo de condición, actualización del sistema de control
Este año, el Estados Unidos consumirá alrededor de 3,3 teravatios, un poco más del 20 por ciento de la energía utilizada en todo el mundo, según la Agencia Internacional de Energía (AIE). El uso global de energía está aumentando y podría duplicarse para 2050, según las proyecciones de la IEA, debido al crecimiento de la población mundial y la mejora de los niveles de vida en los países en desarrollo. A medida que el uso de electricidad continúa aumentando y las redes eléctricas se llevan al límite, las empresas de servicios públicos están buscando medios adicionales de producción eléctrica para garantizar que puedan satisfacer adecuadamente la demanda.
Para una gran empresa de servicios públicos del sur que genera electricidad para alrededor de 600.000 clientes minoristas y mayoristas, una revisión de las técnicas aplicadas anteriormente está ayudando a mejorar la generación eléctrica ahora y en los próximos años.
La empresa de servicios públicos desempolvó una flota de motores de turbina de gas de combustión sin usar y quería modernizarlos para generar electricidad de respaldo durante los períodos pico de consumo de energía. La tarea de reemplazar los sistemas de control envejecidos en los motores fue HPI LLC, un desarrollador de proyectos que se especializa en proporcionar controles de modernización para la generación de energía de turbinas de gas y vapor, compresores y sistemas de transmisión mecánica. HPI, con sede en Houston, abrió sus puertas en 2002 y desde entonces ha completado más de 70 modelos diferentes de turbinas de gas para más de 20 fabricantes. La empresa diseña, ensambla, prueba y empaqueta sistemas de reemplazo utilizando controladores programables de alta velocidad, de última generación, .
Un controlador ControlLogix y módulos XM ofrecen confiabilidad y control de turbina mejorado.
Desafío
Cuando el cliente decidió actualizar cuatro paquetes de turbogeneradores General Electric MS5001 (Estructura 5), quería que los motores estuvieran en línea lo más rápido posible. El principal obstáculo era el sistema de control obsoleto en los motores.
Además de la tecnología anticuada del controlador y el cableado envejecido, el sistema de control existente necesitaba urgentemente un monitoreo de condición actualizado y protección contra vibraciones. El controlador para un motor de turbina de gas asegura que la turbina se enciende y se detiene cuando se le solicita, mientras que los sistemas de protección y monitoreo de condición ayudan a que el motor funcione de manera segura y eficiente.
Falla del controlador o de la protección. sistema en una turbina de gas es una propuesta costosa y peligrosa. El sistema de protección contra vibraciones existente de la empresa estaba compuesto por una combinación del sistema Speedtronic de General Electric y un sistema de monitoreo y vibración Bently Nevada 3300. Para reducir los costos, el cliente deseaba conservar las sondas de vibración de General Electric existentes, pero debido a que el sistema de monitoreo y vibración Bently no interactuaba directamente con las sondas existentes, era necesario que HPI explorara otras soluciones.
Además del sistema de monitoreo de condición y vibración, HPI necesitaba actualizar otro circuito de protección crítico:el sistema de protección de exceso de velocidad. En situaciones de modernización, los clientes de HPI suelen tener un sistema de protección contra sobrevelocidad que es obsoleto o hidráulico, lo que dificulta la prueba y el mantenimiento del sistema. Este fue el caso del proyecto de servicios públicos del Sur, y HPI necesitaba un sistema de reemplazo confiable y fácil de mantener.
“Si fallara la protección contra exceso de velocidad, lo más probable es que toda la unidad se destruya, ”Dijo Wheelwright. “Para un cliente como este, eso significaría millones de dólares para comprar una nueva unidad y meses, si no un año completo, para estar en funcionamiento nuevamente”.
Soluciones
HPI suministró una solución de sistema de control digital estandarizado para la empresa de servicios públicos que ofrecía confiabilidad mejorada, información de diagnóstico y control de turbina mejorada, y capacidades de arranque remoto.
El éxito del nuevo sistema gira en torno al uso de control complementario, redes y tecnologías de visualización:núcleo de la arquitectura integrada de Rockwell Automation. Diseñado para facilitar la integración empresarial perfecta, el sistema de información y control de producción de Arquitectura Integrada consta de Logix Control Platform y el paquete integrado de producción y rendimiento FactoryTalk.
Aprovechando el Controlador de Automatización Programable (PAC) ControlLogix de Allen-Bradley , Las redes ControlNet y EtherNet / IP y el software de interfaz hombre-máquina (HMI) FactoryTalk View SE, el cliente tiene un sistema de control de turbina cohesivo. Esto se traduce en actividades estrechamente coordinadas y un mejor intercambio de información.
HPI eligió ControlLogix debido a su capacidad para integrar la gama completa de disciplinas de automatización que incluyen discreto, movimiento, control de procesos, lotes, sistemas de transmisión y seguridad mediante un entorno de desarrollo único y un único protocolo de comunicación abierto.
“Solíamos comprar controladores separados y cablearlos juntos, pero el controlador Logix de Rockwell Automation nos permite brindar soluciones llave en mano que van más allá del gas control de turbinas ”, dijo Jerry Wheelwright, vicepresidente de ingeniería de HPI.
Otro beneficio importante del reemplazo para el cliente vino con el esquema de red y la solución de visualización. HPI conectó módulos de E / S Allen-Bradley FLEX en red con comunicaciones de red de cobre y fibra óptica ControlNet y EtherNet / IP utilizando módulos 1756-ENTB y módulos 1756-CNB. Usando este esquema de red, construyeron un PAC remoto montado en panel que incluye módulos de E / S FLEX digitales, analógicos y de monitoreo de temperatura. Para reducir la cantidad de cableado necesario en el sitio, todos los terminales, fusibles, relés y conductos se preinstalaron en subpaneles.
Al utilizar las redes ControlNet y EtherNet / IP, el cliente aprovechó las comunicaciones nativas ControlLogix sobre una topología de red estándar de la industria. EtherNet / IP amplía Ethernet comercial estándar con un protocolo industrial abierto para fines de automatización, el mismo protocolo que se usa en la red ControlNet.
El sistema de control habilitado para información permite al cliente operar el sistema, que es impulsado por un controlador ControlLogix desde un sitio a cinco millas de la turbina física.
“La capacidad de monitorear y controlar las turbinas en cualquier momento del día desde una ubicación remota es una beneficio significativo para este cliente ”, dijo Wheelwright. “La empresa de servicios públicos puede tener turbinas de gas repartidas por todo el estado y ejecutar los controles a través de plantas de turbinas de vapor más grandes que funcionan las 24 horas del día, lo que elimina la necesidad de tener personal en cada sitio individual”.
Porque HPI usó la plataforma de control Logix para estandarizar los paneles de control, la incorporación de los módulos de la serie XM de Rockwell Automation para el monitoreo de condición fue una combinación natural. HPI utilizó el módulo de medición dinámica XM-120 para protección contra vibraciones. El módulo XM-120 es un monitor inteligente de dos canales de uso general que le permitió al cliente usar sus sondas de vibración existentes.
HPI usó dos módulos en cada una de las cuatro turbinas. El módulo admite el control de la vibración del eje, la carcasa o el pedestal en equipos rotativos, como turbinas, donde se requiere protección o control de condiciones en tiempo real. El módulo XM-120 interactúa con el equipo a través de ControlNet a los módulos de interfaz DeviceNet.
El reemplazo del sistema de protección de sobrevelocidad también se simplificó usando la plataforma de control Logix. HPI reemplazó el obsoleto sistema de protección de exceso de velocidad con el módulo XM-220 de doble velocidad. El módulo XM-220 es un módulo de medición inteligente de dos canales que acepta la entrada de dos tacómetros. El módulo mide la velocidad, la aceleración del rotor y la velocidad máxima, y es capaz de detectar la velocidad cero, el rotor bloqueado y la rotación inversa.
Como el primer sistema de protección y monitoreo de máquinas de la industria que conecta exitosamente las herramientas de mantenimiento al arquitectura de control, el módulo XM-220 se puede implementar en un bus industrial estándar abierto, lo que permite el monitoreo continuo y rentable y la protección de los activos críticos.
Resultados
El sistema de control de reemplazo de HPI proporcionó la cliente con un rendimiento constante, repetible y confiable. Las turbinas de la empresa de servicios públicos no han experimentado una falla de arranque desde la actualización del control. HPI estaba tan satisfecho con la flexibilidad de la serie XM, la facilidad de configuración y la capacidad de ver que los circuitos de protección funcionan, que la empresa decidió estandarizar el equipo para futuras actualizaciones.
“Nosotros eligió la serie XM por dos razones ”, dijo Wheelwright. “Uno era la disponibilidad. Estaba en el estante cuando lo necesitábamos. La segunda razón fue su capacidad para interactuar con otras sondas y el resto del sistema ”.
Debido a la simplicidad de la plataforma de control Logix, HPI puede construir subpaneles modulares o construir un gabinete completamente nuevo que cumpla los requisitos de espacio específicos de una planta.
HPI ofrece servicio y asistencia técnica las 24 horas. Al utilizar la plataforma ControlLogix y los productos Allen-Bradley, sus clientes pueden obtener el hardware que necesitan en cualquier ubicación de distribuidor de Rockwell Automation en todo el mundo. Luego, los clientes pueden instalar el hardware ellos mismos. Desde su sede en Houston, HPI enviará por correo electrónico los parches de software, trabajará en los sistemas de control y se asegurará de que el modelo de E / S esté integrado.
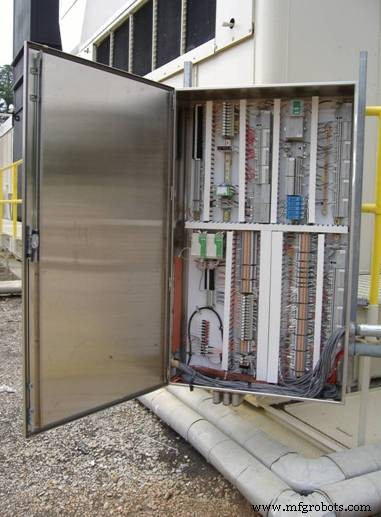
Para reducir la cantidad de cableado in situ necesario, HPI preinstalado todos los terminales, fusibles, relés y conductos en subpaneles.
Mantenimiento y reparación de equipos
- GEA se beneficia del extenso sistema de gestión de usuarios de IXON Clouds
- Cómo el monitoreo de condiciones mejora un programa de PdM
- ¿Es un sistema de monitoreo continuo adecuado para usted?
- La fábrica de motores Honda se beneficia de la supervisión de la máquina
- Cómo un molino Nucor se beneficia del monitoreo de condiciones
- Diseño del sistema de control:desde los diseños más simples hasta los más complejos
- Beneficios de la convergencia del control industrial
- Integración del sistema de control
- El monitoreo de condición de 4 vías beneficia a los equipos rotativos
- Beneficios del sistema de monitoreo de la calidad del aire ambiental basado en IoT
- 8 beneficios del sistema de monitoreo de peso de flota basado en IoT