Asegúrese de que los diseños de moldeo por inyección estén listos para la producción con esta lista de verificación
El moldeo por inyección permite la producción de grandes volúmenes de piezas idénticas a un bajo precio por pieza. El proceso consiste en inyectar material fundido en moldes de metal duradero a través de una boquilla presurizada, expulsar la pieza una vez que el material se haya fraguado y repetir. Una amplia gama de artículos cotidianos, incluidas botellas de agua, juguetes de plástico y carcasas electrónicas, se fabrican con moldeo por inyección. Si bien los termoplásticos y termoestables son los materiales más comunes utilizados en el moldeo por inyección, el metal también se puede moldear por inyección.
Cuando fabrica una pieza con moldeo por inyección, debe considerar una serie de variables que afectan la calidad y la funcionalidad del producto final. Hay muchas formas en que una pieza moldeada por inyección puede fallar, incluidas las líneas de flujo, las marcas de hundimiento y la deformación, pero puede evitar la mayoría de los problemas siguiendo algunos principios de diseño clave.
Aquí en Fast Radius, trabajamos con los clientes en sus piezas moldeadas por inyección todos los días. Los ingenieros a menudo acuden a nosotros con grandes diseños de piezas que deben ajustarse antes de que puedan fabricarse de manera efectiva. Nuestros expertos en diseño para fabricación (DFM) evaluaron y ajustaron miles de diseños de piezas e identificaron y recopilaron los problemas más comunes que detectan. La corrección de estos errores comunes en su diseño puede evitar errores costosos y ahorrar mucho tiempo en las revisiones de diseño.
Antes de enviar el diseño de su pieza para que se moldee por inyección, compruébelo con esta lista de reglas de diseño:
Utilice ángulos de inclinación apropiados
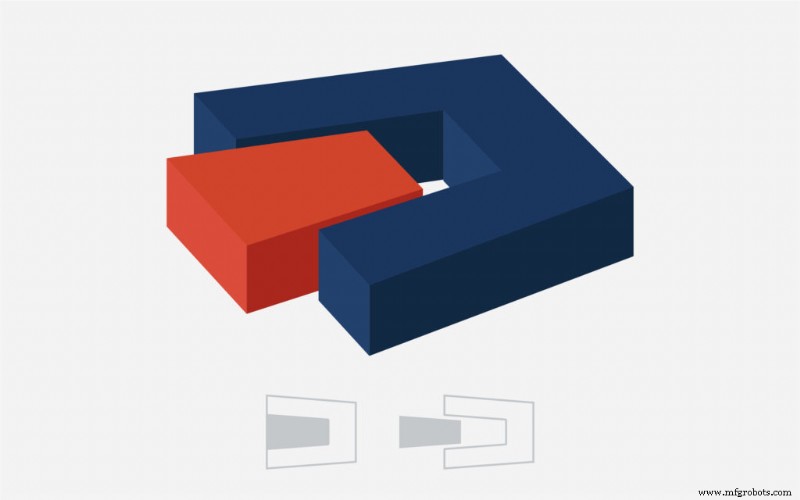
1,5-2 grados de inclinación suele ser un mínimo seguro para la mayoría de las piezas.
Los ángulos de desmoldeo se refieren a la conicidad suave que se agrega a las superficies de una pieza moldeada por inyección que se alinea con la dirección de extracción, lo que permite que la pieza se retire del molde sin dañarla por fricción o succión.
El ángulo de desmoldeo requerido para una pieza depende de algunos factores, incluido el grosor de la pared, la tasa de contracción del material de la pieza, la profundidad de estirado y si la pieza requerirá un acabado superficial o texturizado durante la posproducción. Si bien el ángulo de inclinación promedio debe aumentar 1 grado por cada pulgada adicional de profundidad de la pieza, 1,5 a 2 grados de inclinación suelen ser un mínimo seguro para la mayoría de las piezas.
Mantenga un espesor de pared uniforme, si es posible
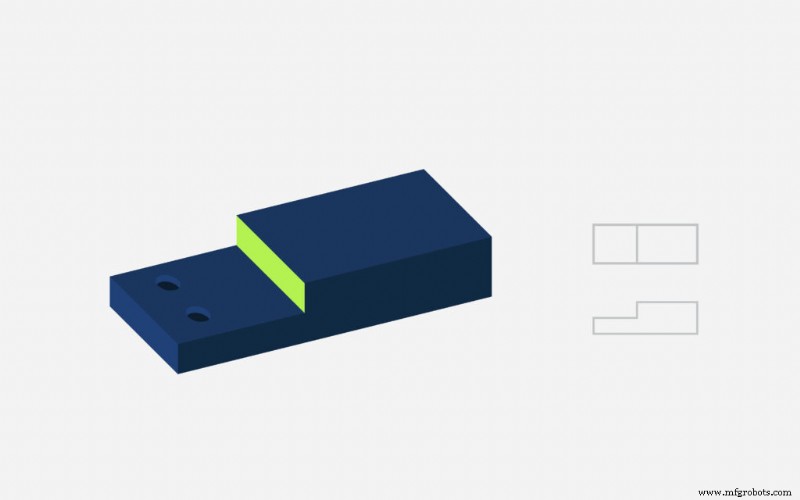
Si es posible, los componentes moldeados por inyección deben tener un espesor de pared uniforme en toda la pieza. Las variaciones en el grosor de la pared pueden hacer que el material inyectado se enfríe a diferentes velocidades, lo que puede provocar hundimientos, huecos y deformaciones.
En general, los espesores de pared entre 1,2 mm y 3 mm son ideales (aunque se pueden esperar algunas variaciones según el material). El grosor de la pared casi siempre debe permanecer por debajo de los 5 mm porque las paredes más gruesas aumentan los tiempos del ciclo de producción y también pueden afectar negativamente las propiedades mecánicas de la pieza.
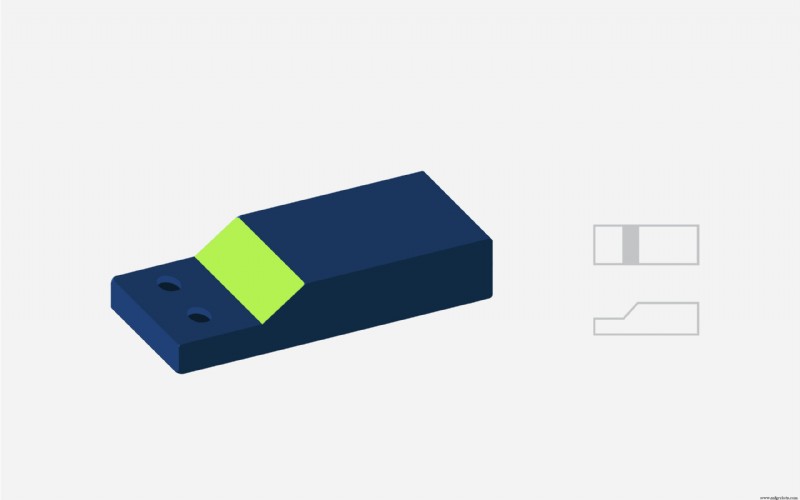
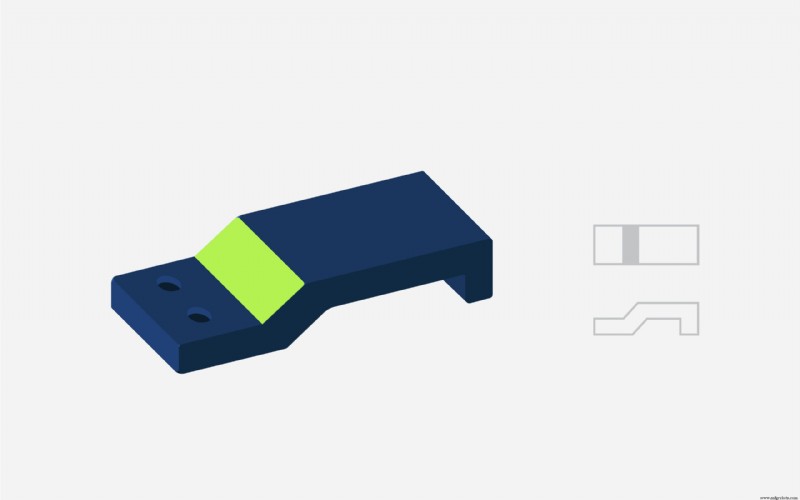
Si una pieza requiere variaciones en el grosor de la pared, debe hacer que la transición entre las secciones sea lo más gradual posible. Puede hacer esto incorporando chaflanes (esquinas o bordes inclinados) o filetes (esquinas o bordes redondeados) en el diseño de la pieza, lo que ayuda a garantizar que la inyección de plástico fundido llene completamente el molde, se enfríe por completo y de manera uniforme y evite que se deforme o no se deforme. -encogimiento uniforme.
Como regla general, la longitud de la transición entre secciones con diferentes espesores de pared debe ser 3 veces el cambio en el espesor de la pared (por ejemplo, si el espesor de la pared disminuye en 1 mm, la transición debe ocurrir a lo largo de 3 mm).
Evite socavaduras
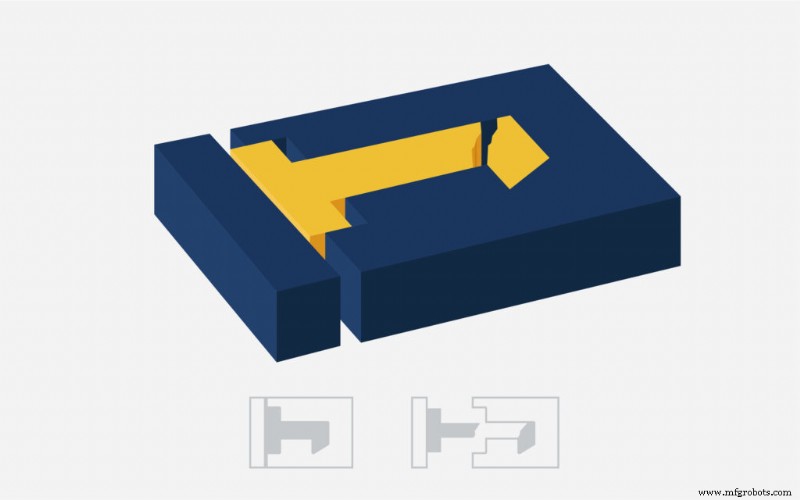
Las socavaduras son superficies o características empotradas o que sobresalen, como roscas, ranuras o encajes a presión, que evitan que una pieza sea expulsada del molde con un solo tirón unidireccional sin dañarla. Es posible evitar socavaduras ya sea orientando las características paralelas a la línea de dibujo o incorporando acciones en el diseño de su molde.
Redondear bordes afilados y esquinas
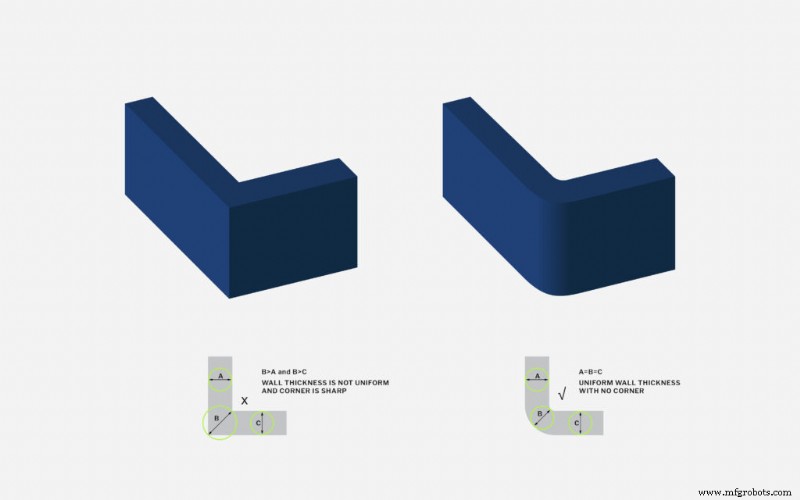
Siempre que sea posible, los diseñadores e ingenieros deben optar por elementos redondos en lugar de bordes y esquinas afilados. Los bordes requieren una presión adicional para llenarse, lo que dificulta que una inyección fluya de manera eficiente y uniforme hacia el molde. Los bordes afilados también tienden a adherirse al molde durante la expulsión, lo que aumenta el riesgo de daños y defectos en las piezas. Puede evitar ambos problemas con esquinas internas y externas redondeadas.
Las esquinas internas, o aquellas donde las paredes parciales se encuentran con el piso, deben tener un radio de al menos el 50% del espesor de la pared adyacente. Las esquinas externas, o aquellas en la parte superior de las paredes parciales, deben tener un radio del 150 % de la pared adyacente para permitir que el plástico fluya de manera más eficiente y eficaz. Esto también ayuda a minimizar la tensión residual y el agrietamiento.
La base de todas las características verticales dentro de una pieza (como salientes, nervaduras o ajustes a presión) también debe estar redondeada. Los radios de protuberancia deben ser el 25 % de la pared adyacente, con un radio mínimo de 0,015" (o 0,381 mm).
Ubicar líneas de separación estratégicamente
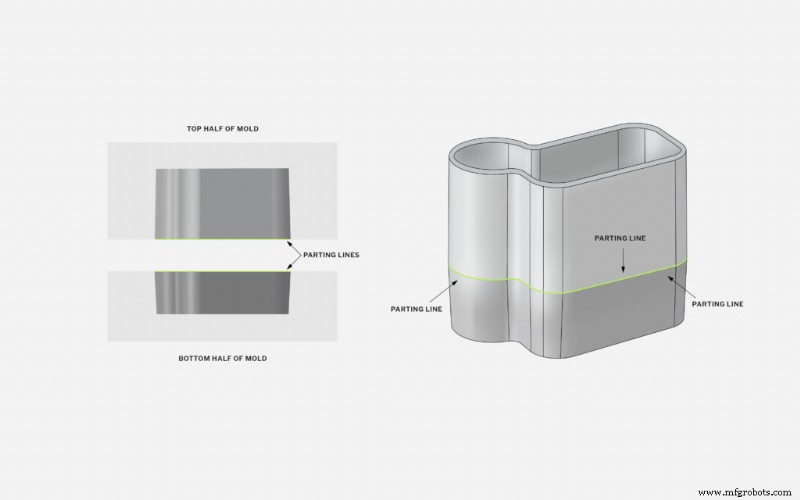
Aparecerá una marca física, conocida como línea de partición, donde se unen las dos mitades de un molde. En muchos casos, las líneas de separación se pueden ver y sentir fácilmente, pero es más que una cuestión estética. La ubicación de la línea de partición dicta cómo se abre el molde (y, por lo tanto, la dirección en la que debe agregar ángulo de inclinación a las características de la pieza), y puede influir tanto en el costo de las herramientas del molde como en cualquier procesamiento posterior requerido.
A menudo, puede mejorar la apariencia y la funcionalidad de una pieza colocando la partición a lo largo de un borde en lugar de sobre una superficie plana. Esto ayuda a ocultar la costura y también reduce las posibilidades de rebaba (exceso de material alrededor de donde se une el molde).
Considere la colocación del pasador eyector
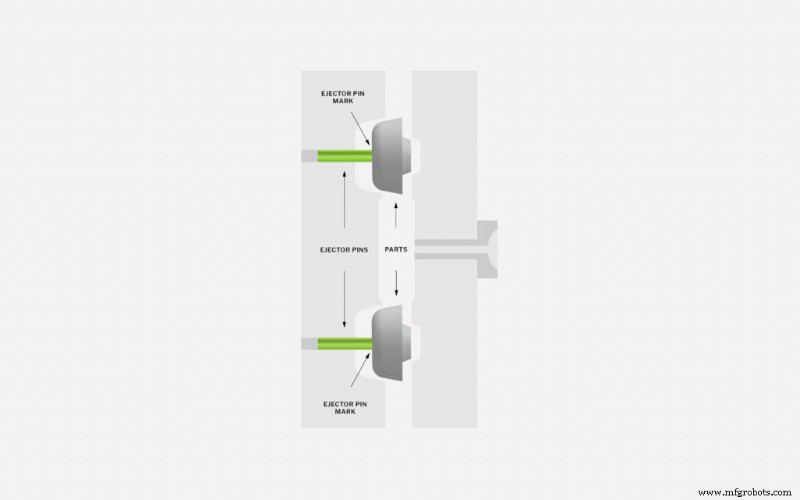
Para funcionar correctamente, los pasadores eyectores requieren superficies planas, o almohadillas, colocadas perpendicularmente a la dirección del movimiento del pasador. La ubicación y el número de pasadores deben estar informados por la forma de la pieza, los ángulos de desmoldeo, la textura de la pared lateral y la profundidad de la pared, todo lo cual influye en cómo se adherirá una pieza a las paredes del molde.
La elección del material también debe tenerse en cuenta en la ubicación o el tamaño de los pines. Las resinas más pegajosas, por ejemplo, tienden a requerir más fuerza para expulsarlas. Del mismo modo, los plásticos más blandos probablemente necesitarán una mayor cantidad de clavijas o clavijas más anchas para distribuir efectivamente la fuerza de expulsión y evitar dañar la pieza.
Optimizar el tamaño de las nervaduras de apoyo
Las nervaduras se utilizan a menudo para fortalecer las paredes parciales en situaciones en las que dos paredes parciales se encuentran en un ángulo de 90 grados, o donde la longitud de una sección en particular se debilita por el grosor de la pared de la sección.
Es importante tener en cuenta que las nervaduras más gruesas no significan necesariamente un mayor soporte; de hecho, las nervaduras que son demasiado gruesas a menudo provocan marcas de hundimiento. El grosor de la base de las nervaduras de apoyo debe ser como máximo dos tercios del grosor de la pared contigua.
Tenga en cuenta el grosor de la pared del molde
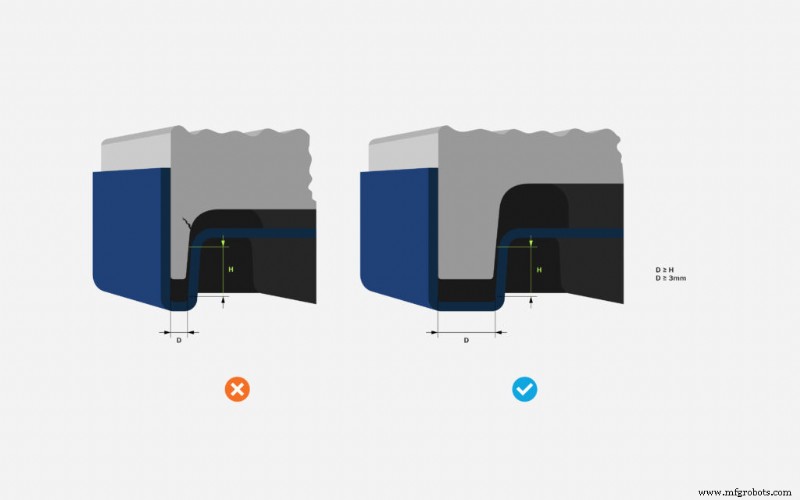
El grosor de las paredes del molde es otra consideración importante, que estará determinada principalmente por el espacio entre las características de la pieza. Asegúrese de que las características verticales, como las nervaduras y las protuberancias, no estén demasiado cerca unas de otras, en las paredes parciales o en las áreas delgadas, ya que esto complica el proceso de enfriamiento.
El espesor de la pared del molde también puede afectar los costos de las herramientas. La mayoría de los moldes de inyección se crean mediante mecanizado CNC y las paredes de metal más delgadas en el molde son más difíciles de mecanizar correctamente. Las paredes más delgadas también dan como resultado ciclos de vida del molde más cortos.
Si bien el grosor mínimo permitido de la pared del molde está dictado por las cualidades físicas y mecánicas del material de la pieza, generalmente es aceptable un espacio de 3 mm entre las características de la pieza.
Diseñar piezas moldeadas por inyección de manera eficiente y eficaz
Los errores de diseño son caros. Recortar una herramienta para corregir un error de diseño podría retrasar semanas a los equipos de productos y costarles miles de dólares. Un buen socio de fabricación lo ayudará a evitar revisiones costosas con DFM, pero ese proceso también se suma a su cronograma. Revisar su diseño para detectar los problemas de esta guía antes de enviarlo a un socio de fabricación lo ayudará a obtener mejores piezas más rápido.
Hay muchas cosas que pueden salir mal en el moldeo por inyección, por lo que necesita encontrar un socio en el que pueda confiar para obtener las piezas correctas. Aquí en Fast Radius, estamos aquí para facilitarle las cosas y estamos comprometidos con el éxito de su proyecto. Contáctenos hoy para comenzar con su próximo proyecto de moldeo por inyección.
Para obtener más información sobre el moldeo por inyección, desde la selección de materiales hasta las diferencias entre moldes de una sola cavidad y de múltiples cavidades y cómo aprovechamos el proceso para fabricar máscaras faciales que combaten la propagación de COVID-19, visite el centro de aprendizaje Fast Radius .
¿Listo para fabricar tus piezas con Fast Radius?
Inicia tu cotizaciónTecnología Industrial
- Moldeo por inyección con tecnología PolyJet
- Interfaz de robots de seis ejes con prensas de moldeo por inyección
- Cómo las principales empresas de moldeo por inyección generan más oportunidades con el marketing digital
- Qué son los defectos de moldeo por inyección y cómo prevenirlos:10 defectos de piezas de plástico
- Micromoldeado con poliuretanos
- ¿Qué es el moldeo por inyección de reacción?
- Moldeo por fundición frente a moldeo por inyección
- Moldeo por inyección frente a moldeo por inyección de reacción (RIM)
- Moldeo por fundición frente a moldeo por inyección de reacción
- ¿Cuáles son los beneficios del moldeo por inyección de plástico?
- Moldeo por inyección con muescas:uso efectivo de muescas en diseños de moldeo por inyección