Ganando tracción con Markforged:sobremoldeo y fundición de ruedas impresas en 3D
Nota del editor:esta publicación de invitado fue escrita por Charles Guan, un graduado de Ingeniería Mecánica del MIT y ex instructor de diseño y taller de maquinaria del MIT. También es el creador del robot Overhaul en los BattleBots de ABC. Trabaja como consultor de ingeniería en robótica y transporte, y está patrocinado por Markforged para competir en BattleBots y otras competencias de robótica. ¡Visite su sitio web y Equals Zero Robotics para obtener más información!
Diseño de ruedas
Ruedas Con más de 6.000 años de historia a sus espaldas, se imaginaría que ya los habríamos hecho perfectos. Como descubrí por las malas durante la temporada 2 de BattleBots, esto está lejos de ser cierto en muchos sentidos. De hecho, puedes reinventar la rueda y equivocarte. Diseñé Overhaul 2.0 con una potente y estable plataforma cuadrada de tracción en las 6 ruedas con la intención de usar la velocidad a mi favor para capturar a los oponentes en su levantador de agarre. Elegí las ruedas basándome en lo que sabía:ruedas giratorias industriales de dureza media con bandas de rodadura de elastómero termoplástico (TPE) que se habían utilizado en el combate de robots desde el principio. Poner motores de 16 caballos de fuerza a través de estas ruedas en un robot diseñado para alcanzar 19 mph en 1 segundo era un territorio desconocido.
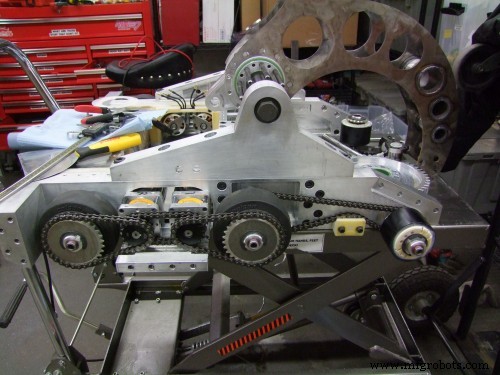
Esto no funcionó a mi favor en la arena en absoluto. Las ruedas de TPE comenzaron a desmoronarse, literalmente derritiéndose por la energía que se les aplicaba. Su pisada resbaladiza se deslizó sobre los escombros sueltos y las partículas de la caja como si el robot estuviera conduciendo sobre hielo. Como resultado, mis 16 caballos de fuerza de motores de transmisión sin escobillas fueron un desperdicio total. Si miras mi partido contra Beta la temporada pasada, verás que confundí a los BattleBots con el Gran Premio D1 durante una buena parte del partido.
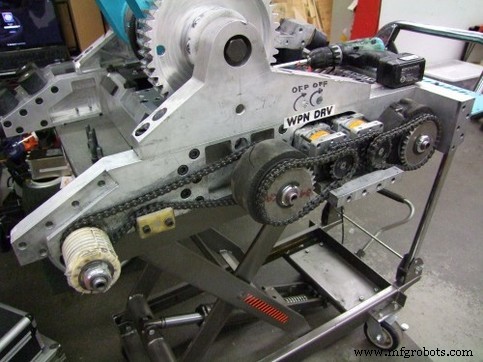
Después del torneo BattleBots Season 2, me quedé preguntándome sobre los próximos pasos. Las ruedas tendrían que cambiar para poner la potencia del robot en el suelo. Aquí es donde comencé a investigar compuestos de caucho moldeable. No me importó hacer algunos moldes, verter el material y luego trabajar en otra cosa en el tiempo que lleva curar. Durante la temporada 2 de BattleBots, vi a algunos competidores, incluido Beta, verter sus propias ruedas de uretano en el lugar.
No sabía nada sobre diseño de llantas y rines, ni sobre molduras y fundiciones. ¡Habla de un disparo en la oscuridad! Afortunadamente, había acorralado a algunos representantes de la compañía Smooth-On en la Detroit Maker Faire durante el verano, y hablé con ellos extensamente sobre sus pensamientos sobre cuál de sus productos era adecuado para fabricar ruedas de tracción. Smooth-On es una empresa orientada principalmente a la fabricación de moldes y fundición para efectos especiales, vestuario y accesorios, no para usos industriales. Sin embargo, sus distribuidores se encuentran en todo el país, por lo que sus materiales están fácilmente disponibles para la experimentación, a solo 15 minutos en automóvil de Boston. La misión:aprender el flujo de trabajo de fundición de resina produciendo ruedas personalizadas para un modelo a escala de 30 libras de Overhaul que estaba diseñando en ese momento para una competencia de otoño de 2016.
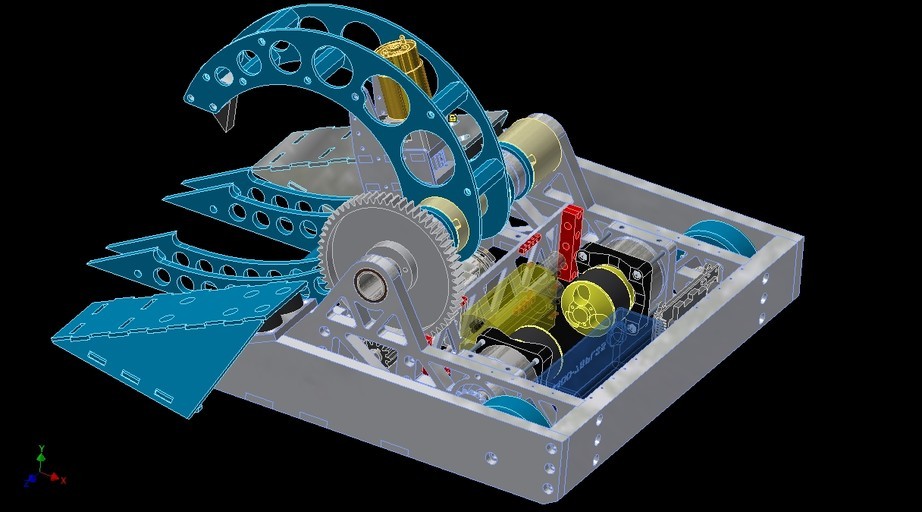
Diseño del molde
Los representantes me señalaron dos materiales que tenían una resistencia al desgarro y una resistencia a la tracción favorablemente altas, las series Reoflex y Simpact. Estos dos rasgos son deseables en un compuesto para ruedas, donde el caucho se corta constantemente a través del grosor de la banda de rodadura y se arrastra por el suelo. Conseguí una muestra de ReoFlex 50 (para durómetro 50A, que es razonablemente suave como la suela de un zapato) y me dispuse a diseñar el molde y el cubo.
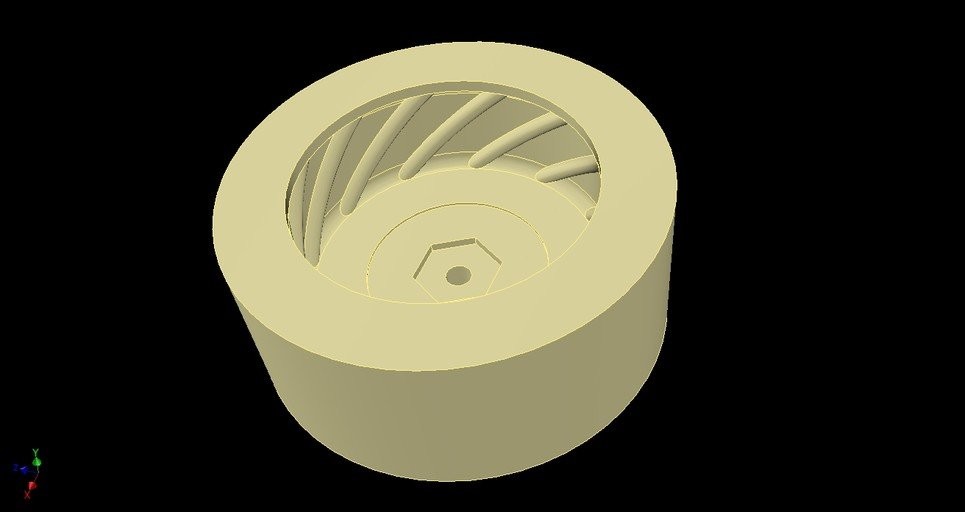
Después de la actuación de Overhaul en la caja, estaba bastante convencido de que se necesitaba algún tipo de función de limpieza de escombros en la superficie de la rueda. Si bien no estamos tratando de canalizar el agua o atravesar el barro como con las llantas de los automóviles, todavía hay detritos sueltos y escamas de pintura de la arena con los que lidiar. Para empezar, hice un patrón de banda de rodadura en espiral simple. Esto no se optimizó de ninguna manera, solo quería llegar rápidamente a la etapa de moldeo por ahora. Supuse que las ranuras helicoidales tenderían a empujar la suciedad hacia un lado lejos del parche de contacto. La orientación exacta y el número de ranuras es, obviamente, una ciencia aún sin resolver si alguna vez ha ido a comprar llantas.
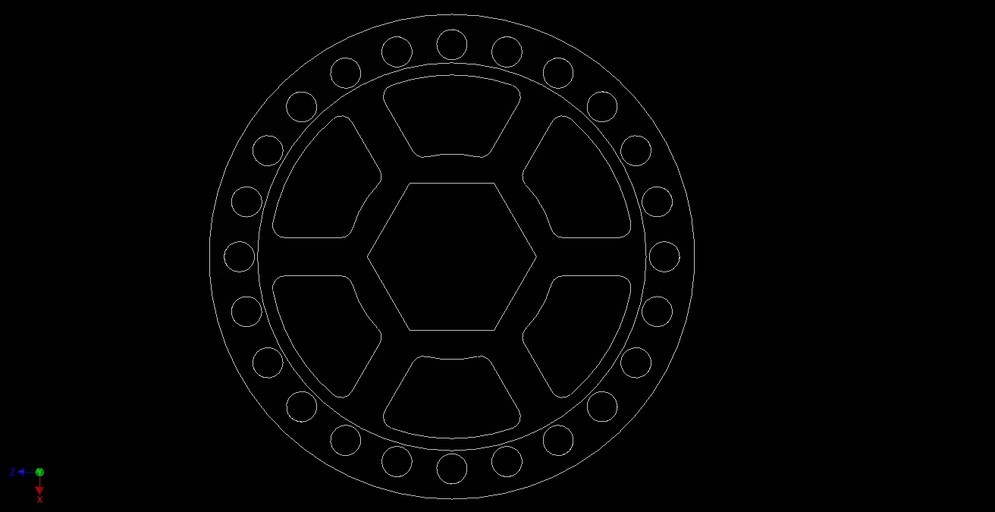
A continuación, me enfrenté a la tarea de diseñar el cubo de la rueda. Eché un vistazo a mi caja de ruedas de patineta y scooter en busca de inspiración. Todos tenían una característica común:orificios pasantes o ranuras en las que el uretano fluía alrededor y hacia adentro. Estaba muy interesado en asegurarme de que el material de la banda de rodadura pudiera permanecer en el buje incluso con fallas de adherencia. Modelé un buje cilíndrico bastante básico, pero con muchas características de orificios pasantes en una nervadura central cónica para dar el máximo área y sección transversal para que el uretano se adhiera a él. Elegí Onyx sobre Nylon regular para el buje debido a su mayor rigidez y resistencia. factorizado con propiedades de adherencia. La mayor rigidez me permitiría hacer que el cubo de la rueda fuera liviano, mientras que la resina se adheriría mejor a la textura microscópicamente rugosa de Onyx que al nailon brillante.
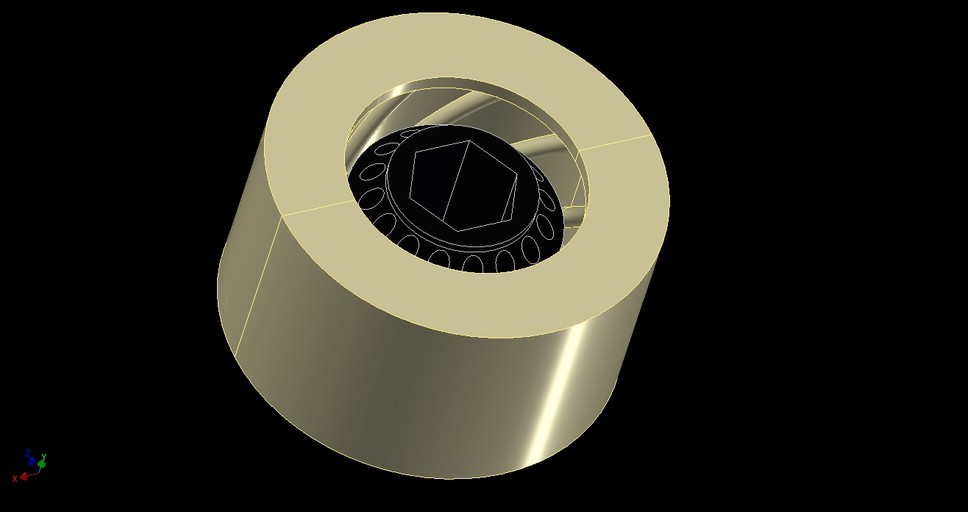
Dado que el Tiny Overhaul también necesitaría algunas ruedas delanteras más pequeñas, utilicé las funciones paramétricas de Autodesk Inventor para generar rápidamente un modelo de 2 pulgadas. Este molde tenía un área bastante restringida para verter, así que estaba interesado en cómo se comportaría el material.
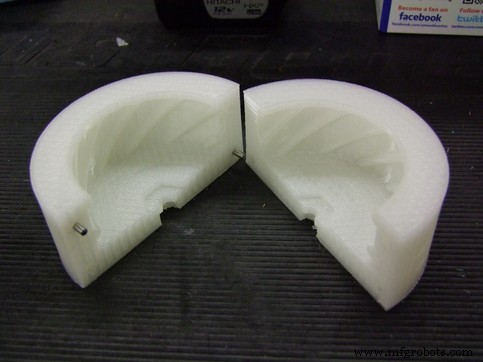
Imprimí un molde de prueba usando Nylon liso sin refuerzo en el Mark Two. El molde era muy escaso:4 paredes y 4 capas de techo y piso, pero solo un 25% de relleno, impreso en la configuración de capa más gruesa de 0,2 mm. Modelé los orificios de los pines de registro en las mitades para asegurar la alineación.
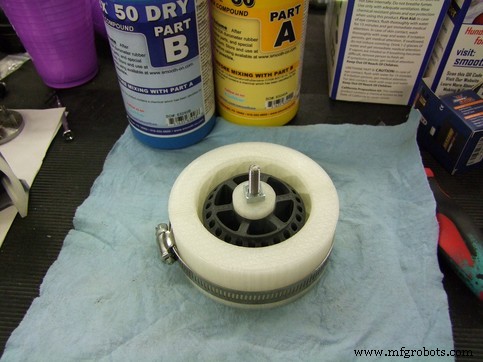
Verter el molde
Las mitades del molde están diseñadas para mantenerse juntas con una sola abrazadera de manguera regular. En el interior, el cubo de la rueda se asienta sobre un buje adaptador para mantenerlo centrado en el molde, y este buje adaptador tiene un orificio pasante en la parte inferior de las mitades del molde para poder ejecutar una tuerca de retención y un perno verticalmente para sellar la cara inferior de el cubo de la rueda contra el molde. Antes de ensamblar esto, cubrí las mitades del molde con desmoldeante en aerosol.

Siguiendo el consejo de amigos que tenían una experiencia más extensa en moldeado y fundición, pedí prestada una olla de vacío para sacar todas las burbujas de aire de la resina mezclada. Smooth-on anuncia sus resinas como "minimizando el aire atrapado", pero ver la mezcla hervir me mostró que esto era menos que efectivo. Las burbujas de aire atrapadas reducirían la integridad de la banda de rodadura ya que presentaría muchas interrupciones en el material. Desgasifiqué la taza de material mezclado en lugar de poner todo el molde con resina líquida en la cámara, ya que todo el aire dentro de las mitades del molde al ser impresas huecas probablemente las deformaría o incluso gotearía y burbujearía lentamente.
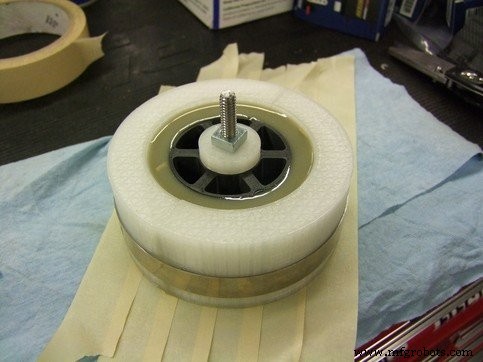
Me tomó alrededor de 2 minutos verter el molde de rueda de 3 pulgadas; incliné la taza de mezcla solo lo suficiente para mantener el flujo continuo de líquido, dejando que la resina se asentara en el fondo y no se amontonara o formara una cresta sobre el molde. Dejar que la resina "encuentre su línea de flotación" es la forma de evitar atrapar grandes burbujas de aire en la pieza.
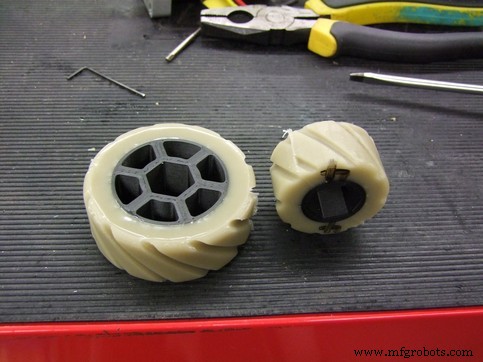
Vertí una rueda de 3 ″ y una rueda de 2 ″ como lote inicial. Después de que las dos primeras ruedas al menos salieran sólidas, llegó el momento de dedicarse a la producción. Imprimí moldes adicionales de modo que pudiera verter 4 o más ruedas a la vez; una de mis tazas de mezcla era perfecta para dos ruedas de 3 ″ y dos ruedas de 2 ″, por lo que se convirtió en el estándar.
El proceso de curado
La mayoría de los fabricantes de resinas recomiendan un curado lento a temperatura ambiente inicial y luego calentar el material para fortalecer más las reticulaciones del polímero. Por ejemplo, la hoja de datos de Reoflex 50 dice calentar el material a 65 grados Celsius durante 4 a 8 horas. Usé una cámara calentada a aproximadamente 70 grados Celsius:las nuevas ruedas que emergieron de este curado acelerado por calor eran definitivamente más resistentes y resistentes al tacto.
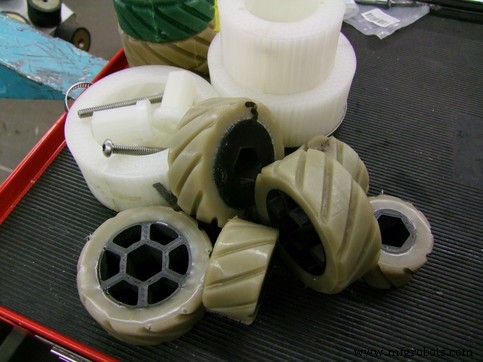
El resultado después de una semana de experimentación fue media docena de ruedas de cada tamaño. Revisé mi suministro de ReoFlex 50, así que decidí que este era un buen lugar para detenerme y asegurarme de que las ruedas realmente funcionaran en competencia antes de gastar más dinero en material. Entré en un ciclo agradable los últimos días antes:vertía los moldes como lo último que hacía por la noche antes de irme, los desmoldeaba por la mañana y luego los horneaba a lo largo del día.
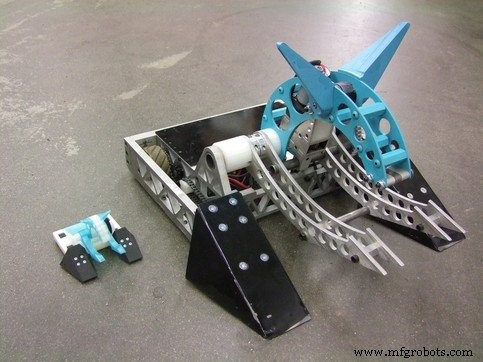
Y así es como se ven instalados en el bot. Si está interesado en el desarrollo de "30-Haul", como lo apodamos, puede consultar su hilo de compilación en mi sitio web.
¿Qué es lo siguiente? Ahora que tengo el proceso de producción explorado y un diseño básico frente a mí, es hora de que comience la ciencia real. Estén atentos a la Parte II de esta serie, donde trato de hacer ruedas de diferentes compuestos y probar su tracción en un piso de acero pintado. Por ahora, ¡así es como se veían estas ruedas después de algunos partidos de conducción dura!
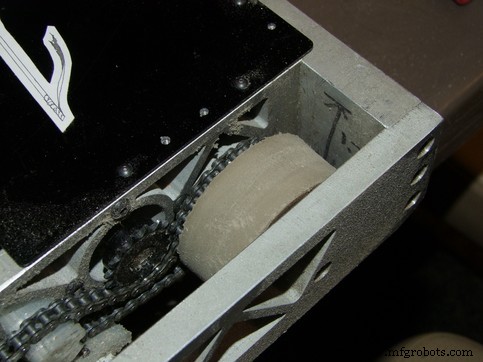
Obtenga más información sobre las impresoras Markforged y cómo pueden adaptarse a sus aplicaciones.
Impresión 3d
- Entrevista con un experto:Spencer Wright de pencerw.com y nTopology
- ¿Acabado de piezas impresas en 3D con… crayones?
- Entrevista con un experto:Ibraheem Khadar de Markforged
- Stratasys se asocia con GrabCAD y e-Xstream
- Stratasys revive MakerBot con el método
- Fundición en arena con tecnología FDM
- Mejor control de calidad con piezas impresas en 3D
- ¡Abróchate el cinturón con piezas funcionales impresas en 3D!
- Re-imaginando el Go Kart con piezas impresas en 3D
- Cómo dominar un volante impreso en 3D
- Creación de prototipos y producción de tiradas cortas con fundición a presión