¡Abróchate el cinturón con piezas funcionales impresas en 3D!
Una de las mejores partes de trabajar para una empresa de impresión 3D de fuerza industrial es que siempre tienes acceso para crear piezas sólidas y funcionales cada vez que se te ocurre una idea. En los últimos dos años, ha habido un fuerte aumento en la prevalencia de piezas funcionales impresas en 3D que aparecen en la vida de nuestros empleados, desde cepillos de dientes y portabolígrafos hasta bisagras de Kevlar para puertas de reemplazo (no estamos totalmente seguros de cómo las partes anónimas perdieron un bisagra de puerta ...) y un soporte de GPS para manillares de bicicleta de carretera, por nombrar solo algunos. Es increíblemente fácil fabricar componentes únicos, personalizados y de alta resistencia con una impresora 3D Mark Two, y con una gran granja de impresoras interna que requiere continuamente piezas nuevas para probar el rendimiento de nuestras máquinas, es común ver cómo se materializa su diseño. rápidamente.
Este fue el caso cuando Maggie, uno de nuestros ingenieros mecánicos, quiso mejorar el portaequipajes de su bicicleta para facilitar su transporte. Las alforjas son bolsas (generalmente impermeables) que se montan a ambos lados de las ruedas delanteras o traseras de una bicicleta, como puede ver en la imagen a continuación. Las maletas también son una vista común en las oficinas de Markforged:una parte significativa de nuestras bicicletas de oficina para trabajar y son una excelente solución para transportar equipos hacia y desde la oficina.
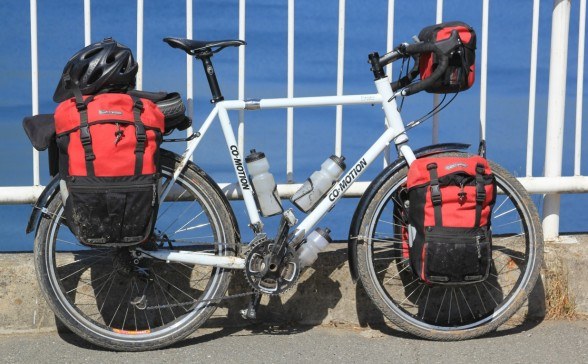
Las alforjas a veces tienen mochila o correas sobre los hombros, pero no a menudo, y a Maggie le resultaba difícil de manejar cargar con su alforja completamente cargada cuando la transportaba fuera de su bicicleta. Sin inmutarse, decidió diseñar una solución que aprovechara tanto la alta resistencia a la tracción de nuestro filamento Kevlar CFF como la confiabilidad de imprimir y olvidar del Mark Two. Esto le permitió iterar rápidamente a través de una serie de diseños funcionales antes de producir dos adaptadores de correa de hombro de alta resistencia terminados con un impacto mínimo en su apretada agenda de ingeniería (solo planificando y ejecutando casi la totalidad de las pruebas de impresión de nuestro nuevo filamento compuesto de fibra de vidrio HSHT, no mucho trato!).
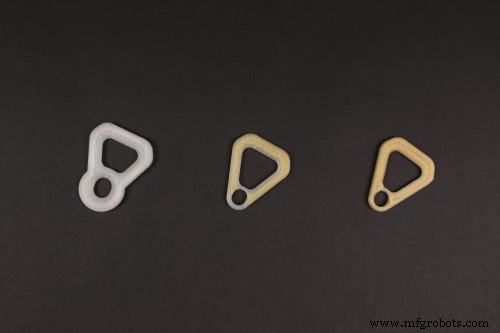
El adaptador permitió sujetar una correa para el hombro de una bolsa de lona lista para usar en los clips de plástico que normalmente sujetan la maleta en un portabicicletas de acero en la parte trasera de la bicicleta. Los clips de la alforja eran el punto de montaje perfecto para agregar una correa para el hombro, pero la correa en sí terminaba en su propio conjunto de clips de plástico que no podían interactuar con la alforja en un ángulo que fuera cómodo para llevar la bolsa. Para Maggie estaba claro que se necesitaría un adaptador para que este proyecto avanzara.
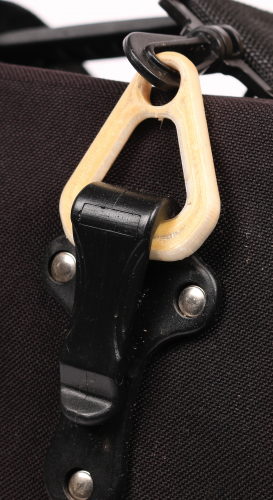
La primera iteración se hizo con las dimensiones aproximadas de los puntos de montaje tanto de la alforja como de los clips de la correa para el hombro. Era funcional, pero el orificio redondo para montar la correa para el hombro era demasiado grueso y el clip de la correa no se podía mover con suavidad, lo que dificultaba la colocación al transportar la bolsa.
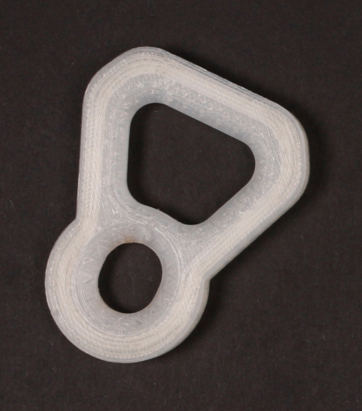
En la segunda iteración, Maggie redujo el tamaño del orificio del clip de la correa y rediseñó el cuerpo del adaptador en general para tener un diseño más delgado y elegante que se ajusta mejor a la estética del diseño de la bolsa y la correa. Con un clic, ella actualizó el archivo STL para ser cortado, usando el botón "Actualizar STL" en Eiger (resaltado en rojo en la imagen de abajo). También cambió el tipo de fibra a Kevlar, porque es capaz de retener más de su resistencia a la tracción que la fibra de vidrio o la fibra de carbono, en caso de que una bolsa sobrecargada deforme la pieza.
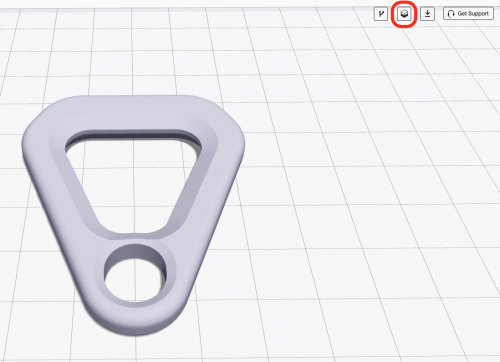
La iteración del diseño final no implicó ningún cambio en la geometría y, de hecho, usó el mismo archivo STL, sino que requirió un cambio en la configuración de corte. A Maggie le gustó cómo había quedado la parte, pero quería una parte más fuerte que la impresa en la segunda iteración. Ella modificó la configuración del Eiger para incorporar fibra en todas las capas, en lugar de solo unas pocas en la parte superior e inferior de la pieza, para una parte más fuerte en general.
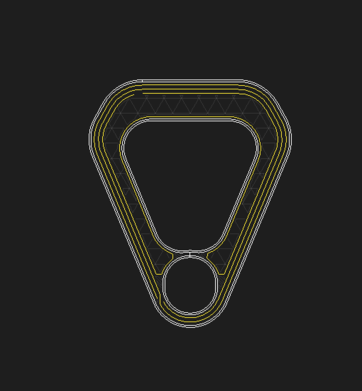
Con la iteración final completa, Maggie imprimió otra copia y ensambló la bolsa a continuación. Piezas funcionales:¡directamente desde la impresora!
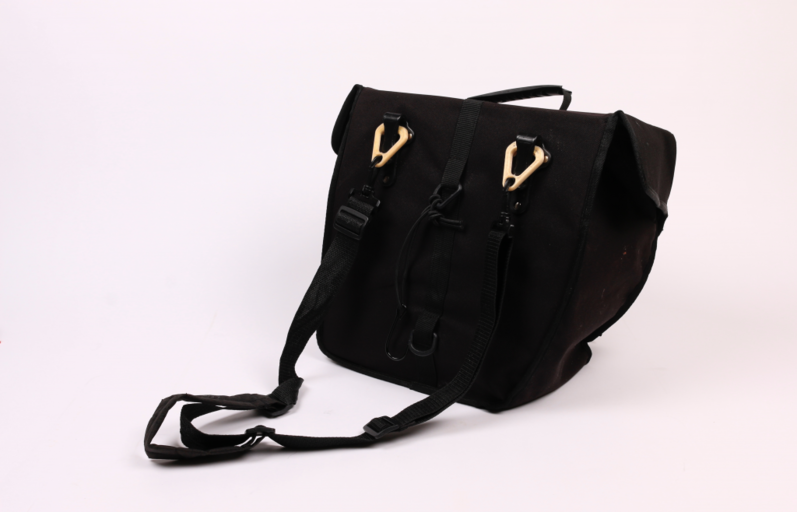
Impresión 3d
- Memoria con partes móviles:"Drives"
- ¿Acabado de piezas impresas en 3D con… crayones?
- Cómo hacer que las piezas de metal sean más ligeras con la impresión 3D de metal
- Impresión del fusible 1 con el fusible 1
- Mejor control de calidad con piezas impresas en 3D
- Inspección en proceso:mejora de las piezas impresas en 3D
- Re-imaginando el Go Kart con piezas impresas en 3D
- Cómo dominar un volante impreso en 3D
- Seminario web:Impresión de piezas sólidas impresas en 3D con Eiger
- Drones extremos impresos en 3D
- Precisión dimensional de piezas impresas en 3D