Desentrañar la evolución morfológica y la cinética de grabado de nanocables de silicio poroso durante el grabado químico asistido por metales
Resumen
Muchas aplicaciones potenciales de nanocables de silicio poroso (SiNW) fabricados con grabado químico asistido por metal dependen en gran medida del control preciso de la morfología para la optimización del dispositivo. Sin embargo, los efectos de los parámetros clave de grabado, como la cantidad de catalizador metálico depositado, la relación molar HF-oxidante ( χ ) y la concentración de disolvente, sobre la morfología y la cinética de grabado de los SiNW todavía no se han explorado por completo. Aquí, los cambios en la nanoestructura y la tasa de grabado del silicio de tipo p dopado degeneradamente en un HF-H 2 O 2 –H 2 Se investigan sistemáticamente los sistemas de grabado O con catalizador de plata depositado sin electricidad. Se encuentra que la morfología de la superficie evoluciona desde una estructura microporosa y con cráteres hasta una matriz uniforme de SiNW a un χ suficientemente alto valores. Las tasas de grabado en la base y la punta de la nanoestructura están correlacionadas con el grabado primario inducido por Ag y el grabado secundario inducido por iones metálicos y agujeros difundidos, respectivamente. El H 2 La concentración de O también afecta la χ ventana en la que se forman los SiNW y las velocidades de ataque, principalmente mediante la modulación de la dilución del reactivo y la velocidad de difusión. Controlando el grabado secundario y la difusión del reactivo a través de χ y H 2 Concentración de O, respectivamente, se demuestra con éxito la fabricación de SiNW altamente dopados con control independiente de la porosidad de la longitud, lo que puede utilizarse potencialmente para mejorar el rendimiento de los dispositivos basados en SiNW.
Antecedentes
A pesar de los avances en la investigación de varios materiales novedosos, el silicio sigue siendo uno de los sustratos más atractivos para la fabricación de nanoestructuras debido a su abundancia en la naturaleza y la existencia de técnicas bien desarrolladas para la integración de dispositivos. En los últimos años, las nanoestructuras de silicio unidimensionales, como los nanocables de silicio (SiNW) y los nanopilares, han seguido atrayendo la atención en una amplia gama de aplicaciones, como la fotovoltaica [1, 2], la termoeléctrica [3, 4] y el almacenamiento de energía. [5,6,7], electrónica flexible [8], detección bioquímica [9] e interfaz biológica [10]. Aparte de las propiedades eléctricas, ópticas, térmicas y mecánicas únicas de tales nanoestructuras, un impulsor principal de su atractivo sostenido es el desarrollo de nuevas técnicas de fabricación que permiten la formación fácil de las nanoestructuras mientras mantienen un excelente control sobre la morfología y las propiedades físicas. Entre las diversas técnicas de fabricación, el grabado químico asistido por metales (MACE) se destaca desde el punto de vista industrial por su simplicidad, bajo costo y flexibilidad [11, 12]. Usando MACE, se pueden obtener SiNW a escala de oblea, sin defectos con longitud, porosidad, conductividad, nivel de dopaje y orientación de cristal definidos simplemente seleccionando la oblea de Si apropiada, la composición del grabador, la temperatura de reacción y el tiempo de reacción [13,14, 15,16,17,18,19,20,21,22,23]. El control del diámetro, la sección transversal y el paso de la matriz de SiNW también se puede lograr mediante técnicas de modelado de catalizadores, como la litografía de nanoesferas [24], la litografía de interferencia [25] y la litografía de copolímeros en bloque [26]. Esto contrasta con otras técnicas de fabricación, como el grabado con iones reactivos y los métodos de vapor-líquido-sólido, que requieren equipos costosos y pueden producir nanocables con defectos superficiales, orientaciones cristalográficas incontroladas y formas de sección transversal limitadas [11].
En la última década, la fabricación de SiNW a partir de obleas de Si altamente dopadas utilizando MACE ha sido de particular interés debido a los SiNW porosos resultantes con alta calidad cristalina [14, 17, 19]. La estructura porosa permite que los nanocables adquieran propiedades muy deseables, como fotoluminiscencia sintonizable [15], baja conductividad térmica [27] y alta superficie específica [28], lo que los convierte en materiales prometedores para optoelectrónica [14, 16], termoeléctrica [ 3, 27], fotocatálisis [28, 29] y almacenamiento de energía [5]. En combinación con su fotoluminiscencia y alta área de superficie, la biocompatibilidad y biodegradabilidad de los SiNW porosos en entornos fisiológicos también los convierten en candidatos adecuados para aplicaciones de bioetiquetado [15] y administración de fármacos [30]. Aunque se pueden obtener SiNW relativamente porosos con obleas de Si con bajo dopado utilizando altas concentraciones de oxidante en el grabador [15], el uso de Si con alto grado de dopado es ventajoso cuando es necesaria una alta conductividad eléctrica, ya que evita la necesidad de un dopaje posterior al grabado. paso. Esto es especialmente cierto en aplicaciones termoeléctricas de SiNW porosos donde el aumento en la figura de mérito se debe a la disminución de la conductividad térmica sin una degradación significativa de la conductividad eléctrica [27]. Por otro lado, se ha informado que la resistencia de los SiNW porosos es bastante grande en comparación con la de los SiNW sólidos [14], lo que implica una compensación entre el grado de porosidad y la conductividad eléctrica.
Para darse cuenta del potencial de los SiNW porosos en las aplicaciones mencionadas anteriormente, es imperativo comprender completamente los efectos de varios parámetros de grabado durante MACE de Si altamente dopado. Varios estudios [13,14,15,16,17, 19,20,21, 23] han fabricado con éxito SiNW altamente dopados con diferentes longitudes y porosidades utilizando MACE en HF – H 2 O 2 grabador. Sus investigaciones han arrojado luz sobre el efecto de H 2 O 2 concentración [14,15,16,17, 20, 21, 23], concentración de HF [21], HF-H 2 O 2 relación de volumen [19], duración del grabado [14, 16, 17, 19,20,21, 23] y temperatura del grabado [19,20,21, 23] en la porosidad [14, 16, 17, 19, 20] , longitud [16, 17, 19,20,21, 23], tasa de grabado [15] y morfología general [15, 16, 21] de las matrices SiNW. Sin embargo, los estudios sistemáticos sobre el efecto del grabador HF – H 2 O 2 relación molar, definida como χ =[HF] / ([HF] + [H 2 O 2 ]) y H 2 La concentración de O en la formación de nanoestructuras de Si altamente dopadas es limitada. Esto es a pesar del hecho de que χ es un parámetro clave para determinar la morfología y la tasa de grabado de nanoestructuras de Si [18, 31], mientras que [H 2 O] es fundamental en la formación de SiNW en áreas con micropatrones [18]. Hasta la fecha, solo Chiappini et al. [15] y Balasundaram et al. [19] han utilizado una amplia gama de χ valores (0,4–0,98 y 0,7–0,99, respectivamente) en la fabricación de SiNW altamente dopados, mientras que ninguno ha explorado completamente el efecto del grabador [H 2 O]. Además, a pesar de una serie de estudios que aclaran el mecanismo de la evolución morfológica, la porosificación y el estrechamiento de los SiNW ligeramente y altamente dopados fabricados con MACE [15, 17, 32], el mecanismo de evolución de la longitud debido a los efectos competitivos del metal depositado El grabado, el grabado de metales re-nucleados, la difusión por huecos y la difusión de reactivos no se han investigado completamente. En este estudio, MACE de dos pasos [33] en obleas de Si de tipo p dopadas degeneradamente utilizando un catalizador de Ag depositado sin electricidad y H 2 O 2 Se realizó oxidante. En comparación con MACE que utiliza un catalizador de Au con patrón, la deposición no electrolítica puede formar solo SiNW distribuidos aleatoriamente con diámetros variados [13], mientras que Ag puede limitar las relaciones de aspecto de SiNW alcanzables debido a su disolución más rápida que el Au [11]. No obstante, se considera que el uso de deposición sin electricidad y catalizador de Ag en MACE es la forma más sencilla y barata de formar nanoestructuras de Si, incluidos los SiNW. Para explorar los efectos de la composición del grabado en las nanoestructuras resultantes y las velocidades de grabado, los grabadores con una gama relativamente amplia de χ y [H 2 Se utilizaron valores de O]. Mediante la determinación de la cinética de grabado en la punta y la base de las nanoestructuras de Si, información sobre los efectos de la inyección de orificios y las velocidades de disolución de Si, el grabado secundario inducido por iones metálicos disueltos y los orificios difundidos, y la velocidad de difusión de los reactivos en la morfología y longitud resultante de se proporcionan las nanoestructuras. También se fabricaron SiNW altamente dopados de las mismas longitudes utilizando grabadores compuestos de diferentes χ y [H 2 O] valores, lo que muestra que la porosidad se puede ajustar eficazmente mediante la composición del grabado a pesar de las duraciones variables del grabado.
Métodos
Como material de partida se utilizaron obleas de Si (100) de tipo p dopadas con boro pulidas por una cara con una resistividad de 0,001-0,005 Ω cm y una capa de óxido térmico de 50 nm en la cara pulida. Las obleas se limpiaron a fondo con agua desionizada (DI), acetona y etanol, y el óxido térmico se eliminó con HF diluido, dando como resultado superficies de Si terminadas en H. Para confinar el grabado sobre la superficie pulida de Si, la parte trasera de las obleas de Si se revistió con fotorresistente (AZ5214). Las muestras de Si para los experimentos MACE se obtuvieron escindiendo las obleas en 1 × 1 cm 2 piezas. Se utilizaron muestras de Si de la misma oblea para cada conjunto de experimentos.
MACE se llevó a cabo utilizando un proceso de grabado de dos pasos que consiste en la deposición sin electricidad de un catalizador de Ag y luego el grabado en HF – H 2 O 2 soluciones, como se muestra esquemáticamente en la Fig. 1. Las piezas de Si se sumergieron primero en HF al 5% durante 3 min. A continuación, se realizó la deposición sin electricidad de nanopartículas de Ag (AgNP) sobre el sustrato de Si en una solución acuosa que contenía HF 4,8 M y AgNO 3 0,005 M para diferentes duraciones de tiempo (Fig. 1a). Después de un enjuague suave con agua desionizada, las muestras de Si recubiertas con AgNP se grabaron en HF – H 2 acuoso. O 2 soluciones con diferentes χ y [H 2 O] valores (ver archivo adicional 1:Tabla S1) para diferentes períodos de tiempo (Fig. 1b). Las muestras de Si grabadas se enjuagaron a fondo con agua desionizada y luego se sumergieron en 1:1 ( v / v ) HNO 3 durante 10 minutos para disolver los AgNP. Después de otro enjuague completo con agua DI, las muestras de Si se empaparon en HF al 5% durante 3 min para eliminar cualquier capa de óxido formada y luego se enjuagaron nuevamente con agua DI varias veces. Deposición de Ag y HF – H 2 O 2 los grabados se realizaron en la oscuridad. Todas las muestras se procesaron a temperatura ambiente (22–23 ° C) en vasos de precipitados de plástico separados que contenían 15 ml de la solución requerida.
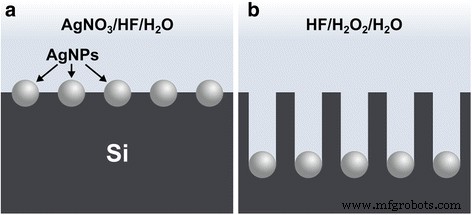
Vista esquemática en sección transversal de la fabricación de nanoestructuras de Si utilizando MACE de dos pasos. un En el primer paso, los AgNP se depositan sin electricidad sobre la superficie de Si en una solución acuosa que contiene AgNO 3 y HF. b En el segundo paso, los AgNP catalizan el grabado del sustrato de Si en una solución compuesta de HF, H 2 O 2 y H 2 O, que conduce a la formación de nanoestructuras de Si
Las superficies de Si grabadas se caracterizaron mediante microscopía electrónica de barrido (SEM, Phenom Pro o FEI / Philips XL-30) y microscopía electrónica de transmisión (TEM, Philips CM20). Para preparar las muestras para la observación SEM, se eliminó el fotorresistente en la parte posterior con acetona. Luego, las muestras de Si se enjuagaron con etanol y se secaron en una placa calefactora para minimizar la aglomeración de SiNW debido a la evaporación del agua [19].
Resultados y discusión
Deposición de catalizador de plata y formación de SiNW porosos
El efecto de la duración de la deposición de Ag (10 sa 15 min) en una solución de 0.005 M AgNO 3 y se investigó HF 4,8 M sobre la formación de SiNW altamente dopados. Cuando las muestras cargadas con Ag se grabaron en una solución que contenía 4.8 M H 2 O y χ =0,95 durante 30 min, los tiempos de deposición cortos (≤ 2 min) dieron como resultado una matriz densa de poros verticales con algunas picaduras laterales, como se muestra en la Fig. 2a. Sin embargo, los poros no eran lo suficientemente densos como para formar estructuras de nanocables bien separadas si el tiempo de deposición es ≤ 1 min. Por otro lado, los SiNW que casi no tenían defectos se obtuvieron con un tiempo de deposición de Ag de 4 min (Fig. 2b), con tiempos de deposición más altos dando como resultado SiNW sin picaduras. Aparte de los cambios en la morfología de SiNW, también se observó una variación no monótona en la velocidad de grabado de SiNW con respecto al tiempo de deposición de Ag, como se muestra en la Fig. 2c (símbolos de diamante). La velocidad de grabado de SiNW aumentó de un tiempo de deposición de 10 sa 4 min, pero disminuyó inesperadamente entre 4 min y 6 min. Posteriormente, la velocidad de grabado volvió a aumentar hasta los 15 minutos, aunque con valores de velocidad de grabado relativamente más bajos.
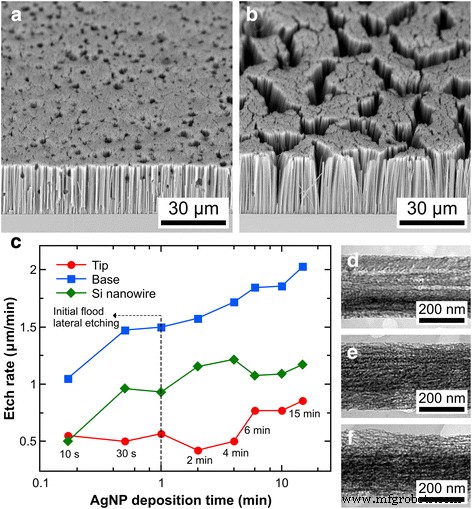
SiNW fabricados con una solución de deposición de Ag que contiene 0,005 M de AgNO 3 y HF 4.8 M y una solución de grabado compuesta de H 2 48 M O y 0,95 HF – H 2 O 2 relación molar. Imágenes SEM de los SiNW para tiempos de deposición de Ag de a 30 sy b 4 min. c Tasa de grabado de los SiNW para diferentes tiempos de deposición de Ag. Imágenes TEM de la sección media de los SiNW para tiempos de deposición de Ag de d 4, e 10 y f 15 que muestra el grado de porosidad. La duración del grabado para todas las muestras fue de 30 minutos
Para tener en cuenta la tendencia peculiar en la tasa de grabado de SiNW, las tasas de grabado en la punta y la base de los SiNW también se determinaron a partir de las imágenes SEM de sección transversal alineando la micrografía de una muestra de Si grabada con la de una muestra de Si sin grabar. muestra de la misma oblea en la parte posterior (consulte el archivo adicional 1:Figura S1). En la Fig. 2c, se puede ver que la tasa de grabado en la base de SiNW (símbolos cuadrados) aumenta monótonamente con el tiempo de deposición de AgNP. Por otro lado, se pueden ver tres dominios en la línea de tendencia de la tasa de grabado de la punta de SiNW (símbolos circulares):(a) ≤1 min, donde la tasa de grabado es relativamente alta; (b) entre 1 y 6 min, donde la velocidad de grabado es relativamente baja; y (c) ≥6 min, donde la velocidad de grabado es la más alta. Por lo tanto, el aumento inicial en la velocidad de grabado de SiNW desde el tiempo de deposición de 10 sa 1 min se debió al aumento constante en la velocidad de grabado en la base, mientras que el aumento posterior en la velocidad de grabado en tiempos de deposición de 2 y 4 min se debió a las tasas de grabado relativamente bajas en las puntas. Mientras tanto, la caída en la tasa de grabado de SiNW en el tiempo de deposición de 6 minutos y las tasas de grabado relativamente bajas en los tiempos de deposición posteriores fueron causadas por el aumento en la tasa de grabado en las puntas.
Dado que la cobertura de superficie de los AgNP está directamente relacionada con el tiempo de deposición de Ag [22, 34, 35], las picaduras laterales para tiempos de deposición bajos se pueden atribuir a una red de Ag escasa [18, 34, 36] con algunos AgNP aislados moviéndose en direcciones <100> aleatorias debido a su forma irregular [37]. Se espera que la tasa de grabado de SiNW en la base aumente con el tiempo de deposición de Ag debido al aumento en la cantidad de catalizador de Ag, que proporciona más área de superficie para la inyección del agujero por H 2 O 2 . Además, una mayor cantidad de Ag también significa más Ag oxidado por H 2 O 2 [15, 17], lo que resulta en una mayor concentración de Ag + iones que pueden contribuir a la disolución del Si a través de una reacción de desplazamiento galvánico [31]. Por otro lado, las tasas de ataque relativamente altas en las puntas para tiempos de deposición de Ag ≤ 1 min pueden explicarse por un ataque lateral de inundación inicial causado por AgNP de forma irregular de la red dispersa de Ag. Los aumentos subsiguientes en la tasa de grabado de la punta con el aumento del tiempo de deposición de Ag pueden atribuirse al aumento de las tasas de re-nucleación del metal [17, 38] en las puntas y, en menor medida, a la difusión del orificio [31, 39].
Hubo un aumento general en la porosidad de los SiNW fabricados a medida que aumentó el tiempo de deposición de Ag, como se muestra en la Fig. 2d-f. (Consulte el archivo adicional 1:Figura S2a – c para obtener imágenes de TEM suplementarias). Se esperan tales aumentos en la porosificación debido a concentraciones más altas de Ag + iones, que dan como resultado un metal re-nucleado y un grabado inducido por iones [15, 17, 38]. Además, tasas más altas de inyección de agujeros también podrían haber resultado en agujeros más difusos, lo que puede contribuir a la formación de poros [19, 39]. La estructura porosa de los SiNWs parece ocurrir como una capa porosa en la mayoría de los nanocables, similar a lo observado en estudios previos [14, 17]. Para algunos SiNW con un tiempo de deposición de Ag de 15 min, las paredes laterales parecen considerablemente más ásperas con manchas oscuras relativamente grandes (≈20 nm de diámetro), probablemente debido a partículas de Ag nucleadas más grandes. Sin embargo, la distribución de la porosidad no está bien definida:algunos SiNW con un tiempo de deposición de Ag de 4 min tienen casi la misma porosidad que la de SiNW con un tiempo de deposición de Ag de 10 min; lo mismo puede decirse de los SiNW con tiempos de deposición de Ag de 10 y 15 min. Esto probablemente se debió a los SiNW obtenidos de diferentes áreas de la muestra, que experimentaron tasas de porosificación ligeramente diferentes según la cantidad real de AgNP depositados (o re-nucleados) y la concentración de grabador sin reaccionar, que se espera que sea mayor hacia los lados. de la muestra. Sin embargo, la tendencia general observada aquí indica que la cantidad total de Ag depositada proporciona otro grado de libertad para controlar la porosidad de los SiNW.
El grado de porosidad aumenta desde la base hasta la punta de los SiNW (ver archivo adicional 1:Figura S2d – l), similar al de estudios anteriores [16, 19]. Esto se espera de la exposición más prolongada de las regiones superiores de los nanocables al grabador [19]. Por otro lado, la mayoría de los SiNW tienen un perfil longitudinal cónico, que es característico de los SiNW altamente dopados fabricados con Ag-MACE debido a la disolución continua de los AgNP en la base del SiNW y la re-nucleación en otros sitios [15, 17 ]. Sin embargo, había unos pocos SiNW que tenían un perfil ligeramente bicónico o de reloj de arena, es decir, la sección transversal central era más grande o más pequeña, respectivamente, que las secciones transversales superior e inferior. Esto sugiere que el Ag + móvil Los iones podrían volver a depositarse no solo en las secciones superiores de los nanocables, sino también en los AgNP vecinos en la base.
Composición del grabador y evolución morfológica de nanoestructuras de Si
La morfología de las nanoestructuras resultantes en Si dopado degeneradamente se determinó utilizando χ valores de 0,7 a 0,99 y H 2 Concentraciones de O de 46, 48 y 50 M. La deposición sin electricidad de AgNP se realizó en una solución de 0,005 AgNO 3 y 4.8 M HF durante 4 min, mientras se graba en HF – H 2 O 2 –H 2 Se llevaron a cabo soluciones de O durante 30 min. La Figura 3 muestra la morfología de la superficie de Si como se ve desde el SEM. Para [H 2 O] =46 M y 48 M, las características del Si grabado evolucionan de Si microporoso con cráteres ( χ =0,7 y 0,75, Fig. 3d, e), a macroporos con poros profundos ( χ =0,75 y 0,80, Fig. 3f), y luego a SiNWs ( χ ≥ 0,85). Para [H 2 O] =50 M, la evolución de la superficie de Si es ligeramente diferente:del Si pulido ( χ =0,7), a macroporos con poros profundos ( χ =0,75), a Si microporoso con cráteres ( χ =0.8–0.85), y luego a SiNWs ( χ ≥ 0,9). En contraste con el trabajo de Chiappini et al. [15], SiNWs sobre una película de Si porosa para 0,7 < χ <0,95 no se observaron, y se obtuvieron estructuras de solo SiNW en un χ más grande rango ( χ ≥ 0,85 en lugar de χ > 0,95). Estas diferencias probablemente se debieron a las variaciones en la cantidad de AgNP depositados, el tiempo de grabado, H 2 Concentraciones de O y HNO 3 y tratamientos posteriores al grabado por HF.
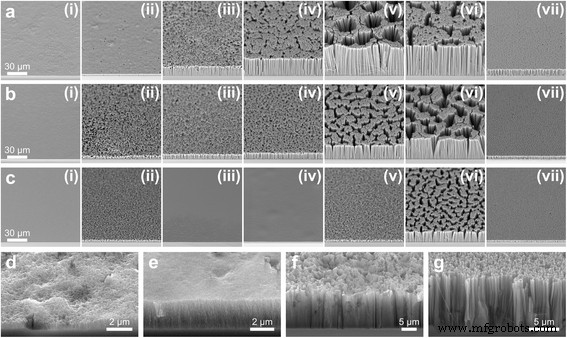
Imágenes SEM de la superficie de Si grabadas en soluciones con H 2 O concentraciones de a 46 M, b 48 M y c 50 M y HF – H 2 O 2 proporciones molares de (i) 0,7, (ii) 0,75, (iii) 0.8, (iv) 0,85, (v) 0.9, (vi) 0,95 y (vii) 0,99. d - g Imágenes SEM de gran aumento de las muestras en a (i) , (ii ), ( iii ) y (vii ), respectivamente. Las muestras se grabaron en HF – H 2 O 2 durante 30 min
Las morfologías de Si obtenidas se pueden explicar en términos de densidad de corriente en la interfaz Ag-Si y Ag + grabado inducido por iones [15, 17, 31, 38]. La formación de SiNW en niveles altos χ Los valores (≥0,85 o 0,9) pueden atribuirse a la formación de Si microporoso a bajas densidades de corriente con la posterior disolución del Si microporoso mediante pulido [31, 38]. Un mecanismo similar probablemente fue responsable de la formación de Si macroporoso con poros profundos en χ más bajos valores, excepto que las densidades de corriente más altas en el extremo de los poros dieron como resultado la formación de óxido y la posterior difusión del orificio [31], lo que resultó en macroporos poco profundos en la superficie superior. Se espera que dicha difusión de los orificios sea particularmente significativa para el Si tipo p altamente dopado debido a la altura de la barrera Schottky positiva que separa los orificios inyectados de la interfaz metal-Si [40]. También es posible que el [H 2 relativamente alto O 2 ] a [HF] dio lugar a una disolución significativa de Ag, que a su vez resultó en la baja densidad de poros profundos en el sustrato de Si. Por otro lado, la aparición de Si microporoso con cráteres en χ =0.7–0.85 indica la ocurrencia de bajas densidades de corriente en este χ rango, que es consistente con la observación de Chartier et al. [31] Además, la porosificación concomitante de Si por Ag + También se espera que ocurran iones en este régimen. La formación de SiNW en un χ más alto valor para el grabador más diluido (50 M H 2 O) es consistente con la observación de Chiappini et al. [15] que las concentraciones más altas de etanol favorecen la formación de Si poroso y pulido en lugar de SiNW. Estos resultados podrían deberse a la lenta difusión de los reactivos a la base de la nanoestructura debido al bajo HF y H 2 O 2 gradientes de concentración a lo largo de la profundidad de la nanoestructura de Si. En este caso, el impacto del grabado en las puntas se vuelve relativamente significativo y las partículas metálicas no pueden formar poros profundos.
Cabe señalar que para valores relativamente bajos de χ (≤0,8), la morfología en toda la superficie de Si no fue uniforme (consulte el archivo adicional 1:Figura S3). Para [H 2 O] =50 M, también se produjo un grabado no uniforme para χ =0,85. En todos los casos, se obtuvo una superficie uniformemente grabada solo cuando se formaron SiNW. Para superficies grabadas de manera no uniforme, las secciones con morfologías homólogas tienden a ocurrir aproximadamente en la misma ubicación general desde el centro de la muestra. La dinámica de grabado no uniforme en diferentes áreas de la muestra puede explicarse por el aumento en la concentración de iones catalizadores disueltos en la solución y su posterior difusión y re-nucleación en otras áreas de la muestra. Esto fue facilitado hasta cierto punto por la difusión hacia afuera concurrente de H 2 burbujas como el Si fue grabado.
Muy alto χ valor (0,99), se obtuvo una matriz muy densa de SiNW finos, lo que dio lugar a una superficie de muestra negra (consulte el archivo adicional 1:Figura S3a-c (vii)). Sin embargo, muchos de estos SiNW tenían paredes laterales inclinadas y algunos hoyos laterales, los cuales ocurren cerca de la base (Fig. 3g) y en tiempos prolongados de grabado (Archivo adicional 1:Figura S4d). También se pueden ver una serie de protuberancias en las que la formación de nanocables terminó prematuramente. Estas características probablemente fueron causadas por el agotamiento de H 2 O 2 en la solución de grabado que condujo a diferentes velocidades de hundimiento de varias porciones de la película de AgNP. A medida que la red de Ag se desintegró, algunas secciones de película de AgNP o pequeñas comenzaron a grabar en direcciones <100> horizontales.
Cinética de grabado de nanoestructuras de Si durante MACE
La variación de la tasa de grabado con χ para diferentes [H 2 Los valores O] se muestran en la Fig. 4. La tasa de grabado aparente de las nanoestructuras generalmente aumenta con χ y alcanza su punto máximo en χ =0,95, después de lo cual las tasas de grabado disminuyen significativamente. Esta tendencia es cierta independientemente del [H 2 O] y la morfología de la nanoestructura de Si. Sin embargo, [H 2 Se puede ver que O] ha afectado considerablemente la magnitud de las tasas de grabado, aumentando la magnitud al disminuir [H 2 O] valores (es decir, grabadores más concentrados). La Figura 4b muestra que la velocidad de grabado en la punta disminuyó considerablemente después de χ =0.85 para [H 2 O] =46 y 48 M y después de χ =0.9 para [H 2 O] =50 M. Por otro lado, la Fig. 4c muestra que la tasa de grabado en la base aumentó considerablemente en χ =0.85 y 0.9 para 46 M H 2 O etchant pero solo ligeramente para 48 y 50 M H 2 O atacantes. La tasa de grabado en la base se mantuvo alta en χ =0,95 pero disminuyó significativamente en χ =0,99.
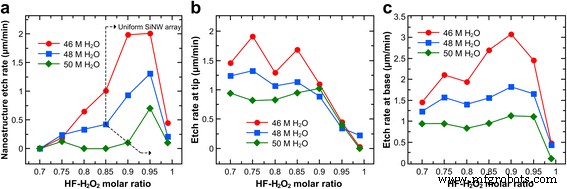
Tasas de grabado aparentes observadas después de 30 minutos de grabado en soluciones compuestas de diferentes HF – H 2 O 2 proporciones molares y H 2 O concentraciones. un Tasa de grabado de las nanoestructuras de Si basada en la longitud resultante. b , c Tasa de grabado del Si a granel con respecto a la punta y la base de las nanoestructuras de Si, respectivamente
A partir de las tendencias en las tasas de grabado en la punta y la base de las nanoestructuras de Si, se puede determinar que el aumento en la longitud de SiNW para [H 2 O] =46 M se debió principalmente a la aceleración del grabado en la base, mientras que el alargamiento de los SiNW para [H 2 O] =48 y 50 M fueron dictados principalmente por la supresión del grabado en las puntas. Además, la tendencia de la tasa de grabado de la nanoestructura general no es exactamente la misma que la tendencia de la tasa de grabado en la base. En particular, el χ valor donde ocurre la tasa máxima de grabado en la base y el χ Los valores en los que se alcanza la mayor altura de nanoestructura no son los mismos (0,9 frente a 0,95, respectivamente) debido al efecto competitivo de la tasa de grabado de la punta.
El χ El valor en el que se produjo la longitud máxima de SiNW (0,95) es cercano al obtenido por Qi et al. [21] ( χ =0,91) para un sustrato de Si de tipo n altamente dopado. La disminución inicial en la tasa de grabado de la punta que ocurre cerca de χ =0,85 es coherente con la evolución morfológica observada de la superficie de Si, en la que la baja difusión del orificio y la re-nucleación de Ag permitieron la formación de SiNW en χ ≥ 0,85. La caída casi simultánea en la tasa de grabado de la punta y el salto en la tasa de grabado base alrededor de χ =0.85 significa que los agujeros y Ag + iones que previamente se difundieron lejos del frente de grabado en la parte inferior χ los valores ahora estaban restringidos en la base debido a la inhibición de la formación de óxido en la interfaz Ag-Si. Al mismo tiempo, el aumento de [HF] a mayor χ Los valores aceleraron la disolución del Si, lo que condujo a un aumento en la tasa de penetración del Ag. Dado que tanto [HF] como [H 2 O 2 ] disminuir cuando [H 2 O] aumenta para un χ dado valor (ver archivo adicional 1:Tabla S1), la disminución en la tasa de grabado en las puntas y la base para mayor [H 2 Se esperan valores O]. Los aumentos más pequeños en la tasa de grabado base entre χ =0,85 y 0,95 para [H 2 O] =48 y 50 M se deben a la difusión más lenta de los reactivos a través de la longitud de SiNW para grabadores más diluidos.
En χ =0,9, la tasa de grabado en la base es máxima debido a las tasas óptimas de inyección del agujero por H 2 O 2 y disolución de Si por HF. Por debajo de este valor, [HF] es el factor determinante de la velocidad, ya que la disolución del Si oxidado no es lo suficientemente rápida; por encima de este valor, [H 2 O 2 ] determina la velocidad de reacción ya que el número de orificios inyectados es demasiado bajo. Este agotamiento de H 2 O 2 en la solución explica por qué la tasa de grabado en la base comienza a disminuir en χ =0.95 y cae abruptamente en χ =0,99. Tal dependencia de la tasa de grabado tanto en [HF] como en [H 2 O 2 ] se observó anteriormente [21] e implica que ambas concentraciones de reactivo deben considerarse en cualquier expresión para la velocidad de reacción de MACE de Si. Por otro lado, un valor máximo para χ no es evidente a partir de la tasa de grabado de la punta. En cambio, la tasa de grabado de la punta está determinada principalmente por [H 2 O 2 ]. Dado que el grabado en la punta de las nanoestructuras de Si se puede atribuir principalmente a la reasignación de iones metálicos y la difusión de huecos, esta correlación es razonable ya que [H 2 O 2 ] valores con respecto a [HF] conducen a mayores concentraciones de Ag + móvil iones [15, 17] y orificios inyectados [31, 32].
Evolución de la duración de SiNW con el tiempo para diferentes composiciones de grabador
La longitud de los SiNW es un parámetro importante en aplicaciones fotovoltaicas [2], almacenamiento de energía [6], detección [41] y termoeléctricas [4]. Para fabricar SiNW de una longitud especificada, se determinó la variación temporal de la longitud de SiNW para grabaciones con χ =0.9, 0.92, 0.95 y 0.98 y [H 2 O] =46, 48 y 50 M. Para estos experimentos, el tiempo de deposición de AgNP se aumentó a 10 minutos para minimizar las picaduras laterales en los SiNW fabricados con largos tiempos de grabado (ver archivo adicional 1:Figura S4a-c). Asimismo, el χ más alto El valor utilizado fue 0,98 porque se obtuvieron SiNW con paredes laterales inclinadas y hoyos laterales para χ =0,99 incluso con un tiempo de deposición de AgNP de 10 min (consulte el archivo adicional 1:Figura S4d).
La Figura 5a muestra que la longitud de los SiNW formados aumenta con el tiempo de reacción de MACE, en consonancia con las observaciones de estudios anteriores [14, 16, 17, 18, 19, 21, 23]. Sin embargo, se puede ver que el aumento en la longitud de SiNW disminuye con el tiempo, es decir, la tasa de grabado está disminuyendo (consulte el archivo adicional 1:Figura S5a), lo que podría deberse al aumento de las tasas de grabado en las puntas de SiNW o al descenso de las tasas de grabado en la base o ambas. La Figura 5d muestra el aumento de las tasas de grabado de la punta a lo largo del tiempo para χ =0,92 y 0,95, siendo el aumento más pronunciado en el primero (ver archivo adicional 1:Figura S5b). Esto indica una cantidad creciente de Ag nucleado en las puntas de SiNW, que se espera que sea más significativa para χ inferiores valores. Por otro lado, la Fig. 5e muestra que en tiempos de grabado superiores a 5 min, la velocidad de grabado en la base de SiNW fue casi constante para χ = 0.9 and 0.92 but decreasing for χ = 0.95 and 0.98 (see Additional file 1:Figure S5c). The latter was probably due to impeded diffusion of reactants to the SiNW base caused by the longer diffusion lengths (SiNW lengths were longer for χ = 0.95 and 0.98) and depletion of H2 O 2 in the etching solution.
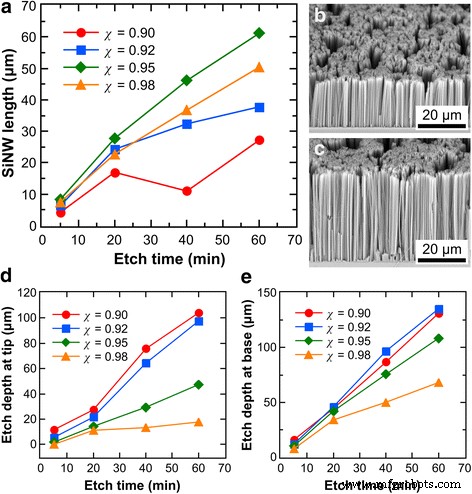
Evolution of SiNW length with time for different HF–H2 O 2 molar ratios at 48 M H2 O. a Effect of etch time on SiNW length. b , c SEM images of SiNWs after etching for 1 h in a solution composed of 48 M H2 O and HF–H2 O 2 molar ratios of 0.9 and 0.98, respectively. d , e Etched bulk Si thickness with respect to the tip and base of the SiNWs over time
It should be noted from Fig. 5 that at χ = 0.9, the evolution of length with time is erratic because of the non-monotonic trend of the etch rate at the tip (see Additional file 1:Figure S5b). This may be due to differing amounts of re-nucleated Ag as more mobile Ag + ions were generated. Nevertheless, lower χ values have the advantage of forming defect-free SiNWs (Fig. 5b) as higher χ may result in some lateral pits, as shown in Fig. 5c for χ = 0.98. The trend of the overall etch rates and etch rates at the tip and base of the SiNWs with respect to χ mirrors those observed in Fig. 4. However, it can be seen in Fig. 5e that χ = 0.92, which is not included in Fig. 4, actually results in a higher base etch rate than χ = 0.9.
The SiNW length also increases with etch duration for more concentrated (46 M H2 O) and dilute (50 M H2 O) etchants, as shown in Fig. 6a. Likewise, the etch rate decreases with etch time for all H2 O concentrations used (see Additional file 1:Figure S6a). Figure 5d, e show that, while the etch depth at the tip and base of the SiNWs both increase with time, the amount of increase at the tip is almost constant but that at the base is decreasing (see Additional file 1:Figure S6b, c). These trends are consistent with those observed for χ = 0.95 in Fig. 5 and Additional file 1:Figure S5. Hence, for χ = 0.95, the increase in the amount of re-nucleated Ag at the SiNW tips with time is negligible, while the increasing SiNW lengths progressively hampers reactant diffusion to the SiNW base. Figure 6 also shows that regardless of the etching time point, lower [H2 O] generally results in more etched Si, similar to what was observed in Fig. 4. However, Fig. 6b, c show that low [H2 O] solutions may result in some lateral pitting in the SiNWs whereas high [H2 O] solutions do not. This could be due to fast etching at sites with re-nucleated Ag particles for low [H2 O] etchants.
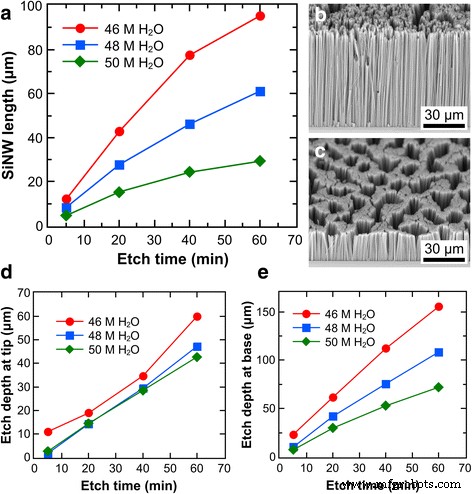
Evolution of SiNW length with time for different H2 O concentrations at a fixed HF–H2 O 2 molar ratio of 0.95. un Effect of etch time on SiNW length. b , c SEM images of SiNWs after etching for 1 h in a solution composed of HF–H2 O 2 molar ratios of 0.95 and H2 O concentrations of 46 and 50 M, respectively. d , e Etched bulk Si thickness with respect to the tip and base of the SiNWs over time
Fabrication of Highly Doped SiNWs with Controlled Porosity
SiNW porosity is another key parameter in SiNW-based devices [5, 16, 27, 29], making its controlled formation during SiNW fabrication highly important. The degree of porosity of SiNWs fabricated using two-step MACE is directly related to the H2 O 2 concentration [14,15,16,17, 20], etching time [14, 16, 17, 20], and temperature [20] and inversely related to the HF–H2 O 2 volume ratio [19] and wafer resistivity [17]. In our Ag deposition experiment, SiNW porosity was also found to be directly related to the amount of deposited Ag. However, the extent of SiNW porosification cannot be easily tuned without affecting other parameters. For example, length and porosity are expected to vary together if one of them is adjusted using either [H2 O 2 ], etch time, or temperature. If a SiNW of a specific length needs to have higher porosity, the [H2 O 2 ] can be increased, but the etch duration needs to be decreased as higher [H2 O 2 ] may have a higher etch rate. This raises the question of whether the desired porosity can still be achieved given the shorter etch time.
Here, the extent of SiNW porosification caused independently by χ and [H2 O] was compared for χ = 0.92, 0.95, and 0.98 ([H2 O] fixed at 48 M) and [H2 O] = 46, 48, and 50 M (χ fixed at 0.95). The SiNW length was fixed at 20 μm by using different etch durations based on the etch rate of the respective etchant composition (see Additional file 1:Table S2). The porosity, in general, was found to be inversely related to χ and directly related to [H2 O], as shown in Fig. 7a–c and Fig. 7d, b, e, respectively. (The trends are more apparent in Additional file 1:Figure S7 where more samples are shown.) Comparing the SiNWs for χ = 0.95 and χ = 0.98 (Fig. 7b, c), the samples for χ = 0.95 appear to have a higher pore density and most are surrounded by a thin porous shell [14, 17]. Meanwhile, for χ = 0.98, some SiNWs appear to be rough and solid rather than porous, which indicates a much lesser degree of porosification. On the other hand, the overall porosity obtained for χ = 0.92 (Fig. 7a and Additional file 1:Figure S7a) appears to depart from the expected trend. While some SiNWs have a porous shell, others seem to be only roughened although to a higher extent compared with those for χ = 0.98. In contrast, the increase of porosity with [H2 O] is more consistent. Although no rough solid SiNWs were obtained for [H2 O] = 46 M, highly porous SiNWs were formed for [H2 O] = 50 M unlike in the case of χ = 0.92.

TEM images of fabricated SiNWs with a length of ≈20 μm showing the variation of porosity at the middle section with a –c HF–H2 O 2 molar ratio and d , b , c H 2 O concentration. un –c HF–H2 O 2 molar ratio of the etchant was 0.92, 0.95, and 0.98, respectively, with [H2 O] = 48 M. d , b , c H 2 O concentration of the etchant was 46, 48, and 50 M, respectively, with HF–H2 O 2 molar ratio = 0.95. TEM images of SiNWs with f –h low and i –k high porosity corresponding to those shown in c and e , respectively, but including the f , i top and h , k bottom secciones. The scale bar in e and k also applies to the images in a - d y f –j , respectivamente
The higher SiNW porosity obtained for χ = 0.95 than χ = 0.98 is consistent with the fact that metal re-nucleation, metal ion-induced etching, and hole diffusion are higher for lower χ valores. It also shows that the longer etch time utilized for χ = 0.98 to obtain 20-μm long SiNWs did not overcome the porosification caused by the etchant χ valor. The seemingly lesser degree of porosification for χ = 0.92 could not have been due to the difference in etch time as a longer etching period was utilized for it than for χ = 0.95. It is possible that more porous SiNWs were actually obtained for χ = 0.92; however, due to the very high porosity, HF–H2 O 2 etching of porous Si both at the surface and inside the pore walls resulted, leading to the rapid collapse of the porous shells [42] and subsequent exposure of the less porous Si surface underneath. That more porous SiNWs were obtained for higher [H2 O] values confirms that etch duration has a significant effect on porosity [14, 16, 17, 20]. (Note the large differences in etch times in Additional file 1:Table S2 for different [H2 O] values.) The high degree of porosity obtained for 50 M H2 O without the collapse of the porous shell could be due to minimized HF–H2 O 2 etching inside the pore walls because of the lower diffusion rate of reactants in dilute etchants.
Examination of the surface roughness along the length of the SiNWs reveals the characteristic increase in porosity from the base to the tip of highly doped SiNWs fabricated with MACE [16, 19], as shown in Fig. 7f–k (also in Additional file 1:Figure S8). The increase in porosity towards the tip of the SiNWs is due to the longer exposure time of these portions in the etchant solution [19]. Figure 6f–k and Additional file 1:Figure S8 also show that the SiNWs are tapered, with the tapering being more severe in SiNWs which are more porous (Fig. 7i–k and Additional file 1:Figure S8a–c). This is expected considering that porosification is directly related to the amount of dissolution of the metal catalyst at the SiNW base [15, 17]. However, a closer look at the SiNWs reveals that some nanowires exhibit a slightly biconic or hourglass longitudinal profile, which seems to occur more often among those with higher porosity. Likewise, more porous SiNWs generally have larger diameters than the less porous ones (see Additional file 1:Figure S7). In order to achieve highly porous SiNWs with smaller diameters, it might be necessary to use a more inert catalyst like Au [32].
Based on the results obtained here, porosity control in highly doped SiNWs of a given length is possible through the use of the appropriate etchant composition. To achieve low porosity, it is best to use high χ values as rough solid nanowires could be obtained. To achieve highly porous SiNWs, on the other hand, the use of dilute etchants with moderate χ values (≈0.95) is advisable as this avoids the disintegration of the porous shell which occurs in etchants with low χ valores. It is conceivable that lower porosities could be achieved using an etchant of both high χ and low [H2 O] values and higher porosities using an etchant of both (slightly) lower χ and high [H2 O] values. In the case of low-porosity SiNWs, the maximum χ and minimum [H2 O] values would probably be dictated by the values where considerable lateral pitting occurs. On the other hand, for high-porosity SiNWs, the minimum χ and maximum [H2 O] values would be determined by the values where the porous shell dissolves and the SiNW structures are lost, respectively. These methods can be combined with our earlier finding of porosity control via the amount deposited Ag in order to obtain a wide range of SiNW porosities.
Conclusions
Porous SiNWs were fabricated from degenerately doped p-type Si substrates using metal-assisted chemical etching in HF–H2 O 2 with electrolessly deposited Ag catalyst. The effect of Ag deposition time, etchant HF–H2 O 2 molar ratio, and etchant H2 O concentration on the morphology and etch rate of the Si nanostructures was systematically studied. It was shown that there is an optimal amount of deposited Ag particles necessary to form damage-free SiNWs. Furthermore, the amount of deposited Ag particles affects the SiNW etch rate in a non-monotonic manner and provides an additional mechanism to control the porosity of the resulting nanowires. Likewise, the etchant composition has a significant effect on the resulting nanostructures. There is an appropriate χ window within which uniform SiNW arrays can be formed. For H2 O concentrations between 46 and 48 M, this χ range is 0.85–0.98; more dilute etchants increase the minimum χ due to sluggish etching at the SiNW base. The formation of Si nanostructures during Ag-catalyzed chemical etching is a result of the competing effects of different factors, namely, deposited Ag-catalyzed Si dissolution, re-nucleated Ag-catalyzed Si dissolution, hole diffusion, and reactant diffusion through etched pores, as reflected by the etching kinetics at the tip and base of the Si nanostructures. These factors result in a gradually decreasing etch rate over time, with re-nucleated Ag-catalyzed etching being dominant for low χ values and impeded diffusion being more pronounced for high χ valores. These mechanisms can be exploited to control the porosity of SiNWs of the same length fabricated with different etch times. In particular, suppressing Ag re-nucleation and hole diffusion using higher χ values can effectively decrease pore density, while more controlled porosification can be achieved using dilute etchants owing to slower reactant diffusion and longer etch times. Since the general mechanism of Ag- and Au-catalyzed MACE of Si is similar [11, 33, 35], the findings of this study may also apply to porous SiNWs fabricated with Au metal catalyst, except that metal ion-induced etching is expected to be greatly suppressed and hole diffusion acts as the main mechanism of porosification and tip etching.
Abreviaturas
- AgNP:
-
Ag nanoparticle
- DI:
-
Deionized
- MACE:
-
Metal-assisted chemical etching
- SEM:
-
Scanning electron microscopy
- SiNW:
-
Silicon nanowire
- TEM:
-
Microscopía electrónica de transmisión
- χ :
-
HF–oxidant molar ratio
Nanomateriales
- Héroes en Silicon Valley (y en la reunión del grupo de usuarios de RTI)
- La evolución del mercado de materiales de impresión 3D:tendencias y oportunidades en 2019
- La evolución de SLS:nuevas tecnologías, materiales y aplicaciones
- Instrumentos de control de benceno para las industrias química, farmacéutica y petroquímica
- Matrices de nanopilares de GaAs con tapa de Au fabricadas mediante grabado químico asistido por metal
- Características ópticas y eléctricas de los nanocables de silicio preparados por grabado electrolítico
- Desentrañar las complejidades de las leyes contra el soborno y la corrupción
- La evolución y el futuro de las entregas minoristas en la acera
- La asombrosa evolución de la impresión 3D en la industria aeroespacial y de defensa
- Sistemas de mantenimiento preventivo y software CMMS:la evolución
- El acero inoxidable y la evolución de la montaña rusa