Tiempo de inactividad:definición, causas y cómo reducirlo
El tiempo de inactividad es una frase que a menudo escuchará en el espacio de gestión de la fuerza laboral y la fabricación, ya que está estrechamente relacionada con la productividad.
No es exagerado decir que, al reducir el tiempo de inactividad, las organizaciones pueden ver un impulso en sus resultados finales. Sin embargo, para poner esto en práctica, primero debe comprender qué es el tiempo de inactividad y qué no.
En esta descripción general, definiremos el tiempo de inactividad, mostraremos cómo calcularlo, discutiremos las causas más comunes del tiempo de inactividad y describiremos los pasos que puede seguir para minimizar el tiempo de inactividad en su organización.
¿Qué es el tiempo de inactividad?
Tiempo de inactividad es un período de tiempo en el que un activo (máquina o empleado) está listo y disponible, pero no está haciendo nada productivo. Esta es la razón por la que el tiempo de inactividad a veces se denomina tiempo de espera . .
El tiempo de inactividad es cuando una máquina está esperando material de entrada. Es un empleado de oficina que espera a que vuelva la conexión a Internet. Un camión en un sitio de construcción esperando que una excavadora se mueva para que pueda llegar a su ubicación objetivo. Es un mecánico de mantenimiento que espera que haya una sierra circular disponible para poder terminar su trabajo.
La razón por la que desea comprender y realizar un seguimiento del tiempo de inactividad es porque señala la brecha entre su producción actual y su nivel de productividad teóricamente máximo. En pocas palabras, cada minuto que su máquina o empleado está inactivo es un minuto de productividad perdida .
Dicho esto, ninguna empresa puede funcionar al 100% de eficiencia. Es inevitable cierto tiempo de inactividad. El objetivo de todo gerente solo debe ser minimizar el tiempo de inactividad, no eliminarlo. Eliminar el tiempo de inactividad es casi imposible y solo se puede considerar para sistemas cerrados y altamente automatizados.
tiempo de inactividad =tiempo de inactividad?
El tiempo de inactividad no igual tiempo de inactividad. Si bien en ambos casos la máquina no está haciendo nada productivo, la diferencia clave radica en por qué ¿Está sucediendo eso?
En el contexto de un tiempo de inactividad anormal, la máquina es capaz de realizar su función prevista, pero por alguna razón no lo hace. Hay muchas causas posibles del tiempo inactivo de la máquina como:
- sin entrada de materia prima
- esperando que otra máquina termine su trabajo
- diferentes ineficiencias en el flujo de trabajo y los procesos
- la producción debe ralentizarse o detenerse (por razones como el inventario a plena capacidad)
- cortes de energía o problemas técnicos similares que no están relacionados con la máquina en sí
- …
Cuando hablamos de tiempo de inactividad de la máquina, el activo no está operativo por una de dos razones:
- Mantenimiento programado: Esto es cuando programa el tiempo de inactividad planificado para realizar el mantenimiento preventivo de un activo. Esto a veces se denomina tiempo de inactividad normal porque el mantenimiento programado es algo que debe realizarse para mantener las máquinas en buenas condiciones.
- Fallo de la máquina: Avería inesperada de la máquina que debe corregirse antes de que la máquina pueda seguir funcionando. Puede ser denominado tiempo de inactividad anormal ya que representa un evento que está fuera de nuestro control y perjudica la productividad empresarial en general.
En términos generales, cuando hablamos de tiempo de inactividad, el activo puede ejecutarse pero no . Y cuando hablamos de tiempo de inactividad del equipo, la máquina no funciona porque no puede .
Debido a esta diferencia, los equipos de mantenimiento deben realizar un seguimiento del tiempo de inactividad de la máquina planificado y no planificado por separado desde el tiempo de inactividad.
Reducir el mantenimiento reactivo en un 73,2%
Ver los resultados que disfruta Red Hawk con Limble
Lea nuestroCaso de estudio
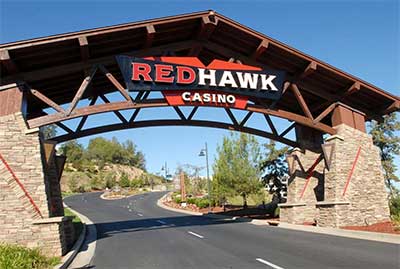
¿Cómo calcular el tiempo inactivo?
El tiempo de inactividad representa la disparidad entre el tiempo que está programado para ejecutarse un activo y la cantidad de horas productivas reales que se han gastado.
Por ejemplo, en un turno de 8 horas, un empleado puede realizar un seguimiento de 7 horas y 20 minutos de trabajo productivo. Esto sugiere que tenían 40 minutos de inactividad, suponiendo que rastrearan todo con precisión en función del tiempo.
Cuando hablamos de máquinas, las cosas se complican un poco más porque hay que diferenciar entre el momento en que una máquina se enciende y el trabajo productivo real.
Imaginemos que tiene una máquina que funciona durante 16 horas. Para este ejemplo, digamos que necesita 10 minutos para encenderse, 5 minutos para apagarse, tiene un descanso de 30 minutos para limpiar y se detiene durante 15 minutos para un cambio de turno.
En otras palabras, se supone que la máquina debe realizar un trabajo productivo durante 15 horas . o 900 minutos .
Uno puede imaginar fácilmente una situación en la que una máquina estaba inactiva:
- 5 minutos cada hora esperando material de entrada ( 75 minutos en total)
- 10 minutos porque un cambio de turno tomó 25 en lugar de los habituales 15 minutos
- 40 minutos porque otra máquina en la línea de producción tuvo una avería inesperada
Todo esto equivaldría a 125 minutos de inactividad .
¿Necesitarías reducirlo a cero? No necesariamente. Quizás esos 5 minutos cada hora también sean necesarios para que los operadores de la máquina tomen los descansos necesarios o limpien las cosas. Dicho esto, definitivamente querrá eliminar el tiempo de inactividad causado por averías no planificadas de la máquina.
Causas comunes del tiempo inactivo
Antes de describir las mejores prácticas para reducirlo, analicemos brevemente las causas comunes del tiempo de inactividad:
- Ineficiencias de los trabajadores: Los trabajadores no son máquinas y algunos son más eficientes que otros. Necesitan descansos para evitar el agotamiento. Algunas ineficiencias son el resultado de que los empleados recién contratados atraviesan un período de ajuste. Para abordar las ineficiencias de los trabajadores, puede trabajar para mejorar su proceso de incorporación y desarrollar una cultura empresarial en la que todos tengan que hacer su propio peso.
- Ineficiencias en el proceso y el flujo de trabajo: Los procesos comerciales y de producción mal optimizados, la espera de aprobaciones y la falta de herramientas disponibles para realizar la orden de trabajo asignada son cosas que debe considerar para reducir las ineficiencias del proceso y el flujo de trabajo.
- Equipo defectuoso: Las averías inesperadas de la máquina pueden provocar graves problemas operativos. Los departamentos de mantenimiento deben utilizar un sistema CMMS y tener un plan de mantenimiento proactivo para todos los activos de prioridad media y alta.
- Accidentes y desastres naturales: Cosas que en su mayoría están fuera de nuestro control. Por lo general, tiene más sentido intentar prepararse para tales eventos que tratar de prevenirlos.
¿Cómo se reduce el tiempo inactivo?
Una pregunta que debe hacerse antes de sumergirnos en consejos prácticos es algo a lo que ya hemos aludido anteriormente: ¿Quiere eliminar el tiempo de inactividad?
Esto es especialmente importante cuando hablamos de empleados. No puede esperar que las personas sean productivas cada segundo de cada día. Hay una razón por la cual la mayoría de las escuelas y universidades trabajan en bloques de 40 a 60 minutos con breves descansos. Para evitar el agotamiento y mejorar la productividad general, diferentes investigaciones sugieren un bloque de trabajo ideal es entre 50-90 minutos con descansos que duran 5-20 minutos.
Las cosas son diferentes cuando empezamos a hablar de máquinas, ya que no se cansan, pierden la concentración y hacen un lío. Dicho esto, existen razones para no llevar todas las máquinas al límite. Si bien las máquinas no se cansan, sí se desgastan. Por ejemplo, algunas máquinas tienen componentes que no deben exceder ciertos niveles de temperatura. Un poco de tiempo libre podría ser justo lo que necesitan para enfriarse.
Esos son casos específicos que desea tener en cuenta.
Sin embargo, no hay duda de que una gran cantidad de tiempo de inactividad es algo que debe abordarse, ya que puede arruinar una organización a largo plazo, ya sea por pérdida de productividad o aumentando los costos sin agregar valor (esto es especialmente notable en las industrias de la construcción y el transporte a través del costo del combustible desperdiciado de las máquinas y camiones que están inactivos).
A continuación, se muestran algunas formas en las que puede reducir el tiempo de inactividad y mejorar la productividad:
N.º 1) Optimice su flujo de trabajo
Como mencionamos anteriormente, las ineficiencias en el flujo de trabajo y los procesos son una causa común de tiempo inactivo. Es por eso que todas las organizaciones deben trabajar para detectar y eliminar los cuellos de botella y otros problemas causados por esas ineficiencias.
El primer paso para resolver cualquier problema es darse cuenta de que tiene uno. Si desea verificar si el tiempo de inactividad está perjudicando a su departamento, el primer paso debe ser implementar un programa para rastrear y reportar el tiempo productivo versus el no productivo.
Para reducir el tiempo de inactividad de los empleados, puede:
- busque crear horarios y cargas de trabajo más equilibrados, especialmente para proyectos más grandes con varios miembros del equipo donde una tarea debe completarse antes de que pueda comenzar la siguiente
- eliminar tareas administrativas innecesarias (como (pre) aprobaciones, rastrear una cosa en varios lugares, etc.)
- crear procedimientos operativos claros para las tareas de rutina (en el espacio de mantenimiento, esto se traduciría en la creación de cosas como procedimientos operativos estándar y listas de verificación de mantenimiento preventivo)
- asegurarse de que los empleados tengan herramientas disponibles cuando las necesiten (ya sea una llave inglesa o acceso a una herramienta de gestión de proyectos)
- adoptar prácticas lean
Cuando se trata de optimizaciones de flujo de trabajo para máquinas, sus opciones son de alguna manera limitadas, ya que no puede cambiar el funcionamiento de una máquina. Todavía puede mirar a:
- organice las máquinas de tal manera que la salida de una máquina fluya de manera eficiente para ser la entrada de otra máquina
- tiene suficiente mano de obra calificada para apoyar / operar las máquinas
- busque formas de maximizar la producción y aumentar el tiempo activo de sus activos
# 2) Mantenga sus activos en buen estado
El hecho inevitable es que los activos dañados no pueden alcanzar sus niveles máximos de productividad. Si los activos no funcionan a su máxima capacidad, significa que tiene margen de mejora.
A continuación se ofrecen algunos consejos para mantener los activos en óptimas condiciones operativas:
- poner activos importantes en un plan de mantenimiento preventivo
- implementar monitoreo de condición y mantenimiento autónomo para detectar el deterioro del equipo lo antes posible
- utilizar material de entrada de calidad (en bruto)
- reduzca la cantidad de soluciones improvisadas y repuestos de baja calidad e intente utilizar principalmente repuestos aprobados por los OEM
- use CMMS móvil para asegurarse de que se realice el trabajo de mantenimiento requerido y que se realice a tiempo
# 3) Mejorar el flujo de información
Este consejo podría fácilmente titularse " mejorar las líneas de comunicación ”Ya que la noción es básicamente la misma.
Existe la teoría de que la principal razón por la que las corporaciones fracasan (aparte de la corrupción y las prácticas comerciales ilegales) es porque se vuelven demasiado rígidas e ineficientes. En otras palabras, cuando un mercado los obliga a cambiar, no son lo suficientemente ágiles para implementar cambios estructurales lo suficientemente rápido y se quedan atrás de la competencia.
Esto se relaciona muy bien con el tiempo de inactividad. A medida que crece la organización, también crece el número de tareas administrativas porque los departamentos necesitan intercambiar más información.
Si una pregunta tiene que pasar por varios niveles gerenciales antes de que un empleado obtenga una respuesta clara, se perderá una cantidad significativa de tiempo esperando las aprobaciones.
Una solución para eso es, siempre que sea posible, eliminar a los intermediarios , defina claramente quién es responsable de qué y garantice canales de comunicación directa entre las partes que dependen unas de otras.
Otras soluciones, especialmente en el entorno de la oficina, consisten en utilizar soluciones de software disponibles para acelerar la comunicación, automatizar tareas que se pueden automatizar, realizar un seguimiento del trabajo y generar informes útiles. Casualmente, estas son todas las cosas que hace un CMMS para un departamento de mantenimiento.
Identificar, profundizar, corregir
Averiguar si el tiempo de inactividad es un problema para su organización suele ser mucho más fácil que reducirlo.
El principal desafío es descubrir la causa principal del tiempo de inactividad . ¿Está una máquina inactiva porque el proceso de producción es ineficiente? ¿Es porque una máquina anterior en la línea de producción no funciona a plena capacidad? ¿Se debe a que el material de entrada de baja calidad provoca una mayor intervención de los operadores de la máquina, lo que ralentiza la producción? ¿Es una combinación de diferentes razones?
Si bien reducir el tiempo de inactividad no siempre es tan sencillo como nos gustaría, el efecto que puede tener en sus resultados hace que valga la pena.
Mantenimiento y reparación de equipos
- ¿Cómo obtener la fecha y hora actuales en Python?
- Cómo optimizar los sistemas de fabricación y ahorrar tiempo
- Cómo reducir el uso de energía en la fabricación
- 4 causas principales de fallas en los interruptores y cómo evitarlas
- ¿Qué es el humo de soldadura? - Riesgos y cómo reducirlo
- ¿Qué son las salpicaduras de soldadura y cómo reducirlas?
- Principales causas de fallas en las máquinas y cómo prevenirlas
- Cómo reducir el tiempo de transición con SMED y trabajo estándar
- Cómo reducir el tiempo de inactividad y aumentar la productividad
- Cómo reducir los costos de transporte por carretera
- Cómo reducir el tiempo de capacitación para la soldadura robótica