Eliminación de obstáculos para optimizar los procesos de molienda recién instalados
Por lo general, las nuevas líneas de alto volumen que producen piezas complejas que incluyen procesos de rectificado, como motores de automóviles o álabes y paletas de motores de aviación, pasan por varias etapas, desde la adquisición de la máquina hasta la producción real, como se describe en la Figura n.º 1. Si estas líneas incluyen un proceso considerado de “alto riesgo ” se programará con el "tiempo de desarrollo" como parte de la evaluación y compra de la capacidad del molinillo (pasos 4 y 5) mediante pruebas y refinamiento. Esta es una estrategia efectiva y reduce sustancialmente los problemas asociados con el lanzamiento del programa, pero puede llevar mucho tiempo y ser costosa; muy a menudo, es posible que las muestras de piezas de trabajo ni siquiera estén disponibles o que los prototipos estén sujetos a cambios de diseño adicionales. En tales casos o para diseños de componentes que son diferentes, pero no radicalmente diferente a partir de los diseños existentes, el "tiempo de optimización" rara vez se programa antes de la calificación real de la máquina.
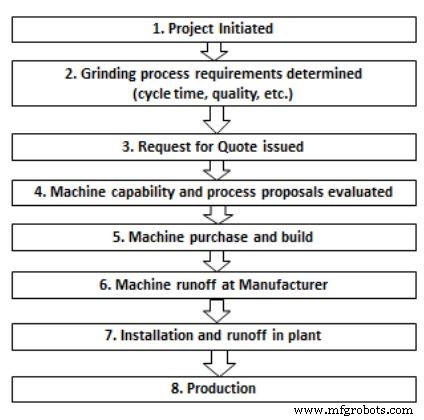
Cuando las máquinas están calificadas e instaladas con “no radicales ” procesos, la atención se centra en la calidad de la pieza y el tiempo del ciclo. Las especificaciones de las ruedas bien pueden seleccionarse para garantizar la más alta calidad en medio de las incertidumbres del nuevo diseño de la pieza y su impacto en mantener las tolerancias de la pieza en especificaciones de CpK a menudo más estrictas que las requeridas para la producción. Además, debido al costo o la disponibilidad, a menudo solo se proporcionan 50 o 100 piezas para la calificación, lo que hace cuestionable el establecimiento de un proceso estable a largo plazo. Por lo general, no hay mucho tiempo o componentes para optimizar las herramientas o el costo del abrasivo por pieza. Después de la instalación, en muchos casos, se impone una actitud de "si no está roto, no lo arregles" y los procesos se bloquean. Rara vez se intenta la optimización.
Por lo tanto, es muy importante que el “paso extra” de optimización sea considerado como una “auditoría” final del proceso. La mayoría de las veces, este paso podría ser simplemente un proceso de "ajuste" para que no sea necesaria la recalificación de todo el proceso, pero ocasionalmente se pueden descubrir oportunidades lo suficientemente grandes que justifiquen cambios importantes en el ciclo o la especificación de la rueda. Se realizaría un análisis de costo/beneficio para determinar si se debe realizar un cambio de proceso más sustancial.
Hay varias razones por las que la falta de "tiempo de optimización" puede causar procesos subóptimos:
- Los ciclos pueden funcionar aceptablemente en la máquina, pero no ser compatibles con las ruedas. es decir, la vida útil de la rueda puede ser inferior a la óptima
- La tecnología de ruedas evoluciona. Es posible que las estimaciones realizadas sobre la tecnología existente no sean óptimas para la nueva tecnología
- Las variaciones sutiles en la configuración de la pieza, el diseño de la máquina y los requisitos de calidad dificultan mucho la optimización del proceso fuera de la línea de producción. Esto se debe a que la línea de producción proporciona muchas piezas y un entorno con variaciones y metrología reales. Estas dos cualidades proporcionan una prueba de "robustez" del proceso "optimizado".
Ejemplos:
El ciclo de molienda que se muestra en la Figura n.º 2 se envió desde el OEM instalado en una planta y actualmente se encuentra en producción. Este ciclo funciona bien y produce piezas aceptables, pero no es "amigable con las ruedas".
La "incomodidad" de la rueda de este ciclo se debe al gran pico (potencia/fuerza) al comienzo del ciclo. El desgaste de la rueda es proporcional al cuadrado de la fuerza de rectificado, las fuerzas altas harán que la rueda se desgaste rápidamente. En este caso, reducir el Avance rápido y aumentar el Avance medio extendería la vida útil de la rueda mientras se mantiene el tiempo del ciclo y la calidad de la pieza.
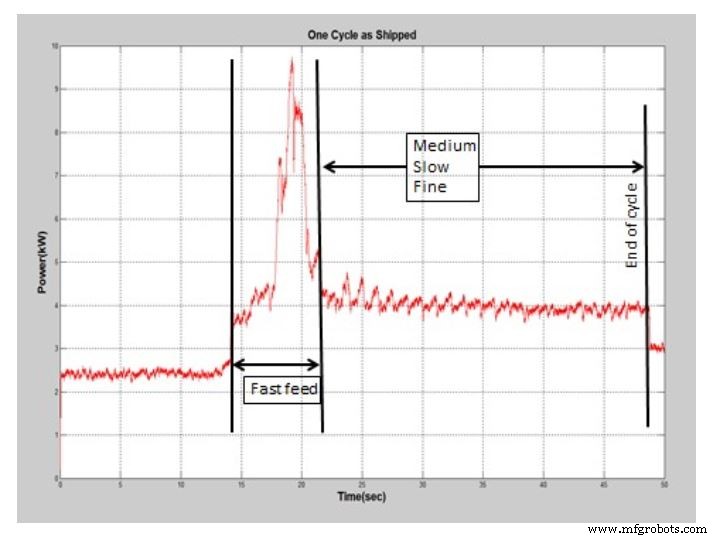
Un ciclo en proceso de optimización
En un caso inusual reciente, el fabricante acordó realizar una optimización "in situ" del proceso de molienda. Inicialmente, el ciclo de rectificado se cambió para hacerlo más "amigable con las ruedas", como se mencionó anteriormente. En este caso, el ciclo más amigable también fue ~5 segundos más corto que el ciclo inicial.
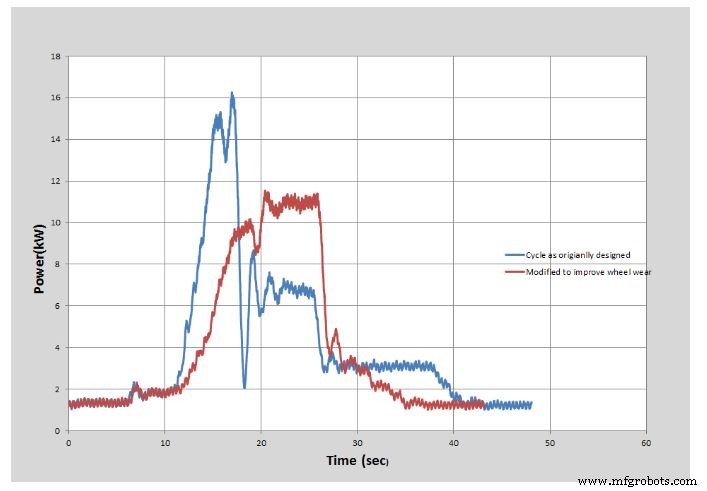
Después de ejecutar el ciclo modificado durante varias semanas para validar la calidad continua de las piezas, las piezas por revestimiento se aumentaron de 8 a 20 y la profundidad del revestimiento se redujo de 0,03 mm a 0,02 mm. Este proceso lleva ya unas 6 semanas sin cambios significativos en la calidad de la pieza. El resumen de los ahorros de costos por año se muestra a continuación.
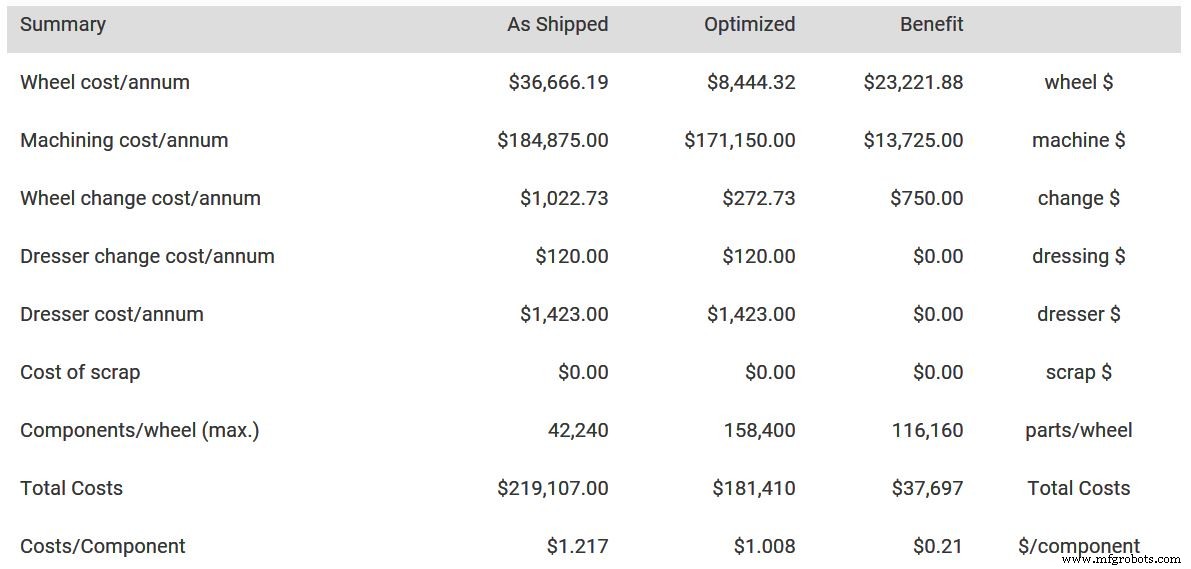
Estrategia de Optimización
La solución, como se ilustra en el segundo ejemplo, es programar el tiempo y las piezas en las primeras etapas de producción (entre los pasos 7 y 8 en la Figura n.º 1) para trabajar en la optimización del proceso con el fabricante de la máquina y el equipo de ingeniería de aplicaciones de herramientas/abrasivos. . Como mínimo, se debe usar un equipo de monitoreo de energía durante esta fase para ayudar en la evaluación y el desarrollo del ciclo. Con este paso adicional, se puede controlar la estabilidad del proceso en tiradas de piezas más largas, lo que puede sacar a la luz problemas y/o presentar oportunidades de mejora.
El beneficio potencial de este paso es grande, ya que las mejoras/ahorros de costos realizados en esta etapa se mantendrán durante todo el ciclo de vida del proyecto.
Aparecido anteriormente en Norton Abrasives
Compre nuestra selección de ruedas de rejilla Norton en MSCdirect.com.
Tecnología Industrial
- Desarrollo de estándares y procesos operativos
- Airbus presenta la fábrica del futuro
- Modos de falla de los procesos de confiabilidad del equipo
- Optimización de las operaciones de fabricación en su taller
- Muelas abrasivas:fabricación y grado | Industrias | Metalurgia
- El valioso papel de la automatización de procesos en la búsqueda de ESG
- Procesos FASTMET y FASTMELT de fabricación de hierro
- ¿Qué es el bruñido? - Definición, proceso y herramientas
- Cómo implementar la gestión de procesos empresariales
- Servicios de rectificado de superficies:proceso y precisión
- Fundamentos del rectificado OD