Métodos de inspección de calidad interna y superficial de piezas fundidas
La inspección de fundiciones incluye principalmente inspección dimensional, inspección visual de apariencia y superficie, análisis de composición química y prueba de propiedades mecánicas. Para fundiciones con altos requisitos, también se requieren pruebas no destructivas. Por ejemplo, las técnicas de prueba no destructivas para la inspección de calidad de fundiciones de hierro dúctil incluyen pruebas de líquidos penetrantes, pruebas de corrientes parásitas, pruebas de partículas magnéticas, pruebas radiográficas y pruebas ultrasónicas.
Pruebas de defectos superficiales y cercanos a la superficie de fundiciones
Pruebas de Líquidos Penetrantes
La prueba de líquidos penetrantes se usa para inspeccionar varios defectos de apertura en la superficie de las piezas fundidas, como grietas en la superficie, agujeros en la superficie y otros defectos que son difíciles de encontrar a simple vista.
La prueba de penetración comúnmente utilizada es la prueba de tinte, que consiste en humedecer o rociar el penetrante de alta permeabilidad en la superficie de la pieza fundida, infiltrar el penetrante en los defectos de la abertura, limpiar rápidamente la capa penetrante y luego rociar el revelador fácil de secar en la pieza fundida. superficie. Después de succionar el penetrante que permanece en los defectos de apertura, el revelador se tiñe para reflejar la forma, el tamaño y la distribución de los defectos.
Se señala que cuanto más lisa sea la superficie a ensayar, mejor será el efecto de la prueba de penetración. La superficie pulida por la amoladora viene con la más alta precisión de prueba, e incluso se pueden detectar grietas intergranulares.
Además de la prueba de colorante, la prueba de líquidos penetrantes también es un método de prueba de líquidos penetrantes de uso común. Debe estar equipado con una lámpara ultravioleta para la observación de la irradiación, y la sensibilidad de la prueba es más alta que la prueba del tinte.
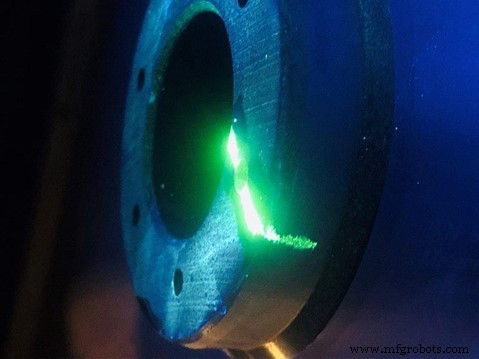
Pruebas de corrientes de Foucault
La prueba de corrientes de Foucault es adecuada para probar defectos debajo de la superficie que generalmente no tienen más de 6-7 mm de profundidad. Las pruebas de corrientes de Foucault se dividen en dos tipos:el método de bobina de tipo colocado y el método de bobina de tipo pasante.
Cuando la pieza de prueba se coloca cerca de la bobina con corriente alterna, el campo magnético alterno que ingresa a la pieza de prueba puede inducir corrientes de Foucault que fluyen en la dirección perpendicular al campo magnético de excitación en la pieza de prueba. La corriente de Foucault producirá un campo magnético opuesto a la dirección del campo magnético de excitación, lo que reducirá parcialmente el campo magnético original en la bobina, dando como resultado el cambio de impedancia de la bobina.
Si hay defectos en la superficie de fundición, las características eléctricas de la corriente de Foucault se distorsionarán para detectar la existencia de defectos. Las principales desventajas de las pruebas de corrientes de Foucault son que no pueden mostrar directamente el tamaño y la forma de los defectos detectados. Generalmente, solo puede determinar la posición de la superficie y la profundidad de los defectos. Además, su sensibilidad a la prueba de pequeños defectos de apertura en la superficie de fundición no es tan sensible como la prueba de penetración.
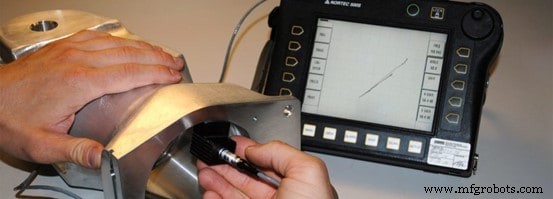
Pruebas de Partículas Magnéticas
La prueba de partículas magnéticas es adecuada para probar defectos superficiales y defectos de varios milímetros de profundidad debajo de la superficie. Requiere equipo de magnetización de CC (o CA) y partículas magnéticas (o líquido de suspensión magnética) para la prueba.
El equipo de magnetización se usa para generar un campo magnético en las superficies interna y externa de la fundición, y se usan partículas magnéticas o líquido de suspensión magnética para revelar los defectos. Cuando se genera un campo magnético dentro de un cierto rango de la fundición, los defectos en el área magnetizada generarán un campo magnético de fuga. Cuando se rocía la partícula magnética o el líquido de suspensión, la partícula magnética es atraída, de modo que se pueden mostrar los defectos.
Los defectos revelados por las pruebas de partículas magnéticas son básicamente aquellos que atraviesan la línea de fuerza magnética, pero los defectos de tira larga paralelos a la línea de fuerza magnética no se pueden mostrar. Por lo tanto, es necesario cambiar constantemente la dirección de magnetización durante la operación para garantizar que se pueda probar cada defecto en la dirección desconocida.
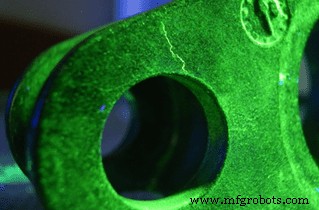
Pruebas de Defectos Internos de Fundición
Para los defectos internos, los métodos de prueba no destructivos comúnmente utilizados son las pruebas radiográficas y ultrasónicas. Entre ellos, el efecto de las pruebas radiográficas es el mejor. Puede obtener una imagen intuitiva que refleje el tipo, la forma, el tamaño y la distribución de los defectos internos. Sin embargo, para fundiciones grandes más gruesas, las pruebas ultrasónicas son muy efectivas, ya que pueden medir con precisión la ubicación, el tamaño equivalente y la distribución de los defectos internos.
Pruebas radiográficas
Se necesitan pruebas radiográficas, generalmente rayos X o rayos γ como fuente de rayos, equipo generador de rayos y otras instalaciones auxiliares. Cuando la fundición se expone al campo de rayos, la intensidad de radiación del rayo se verá afectada por los defectos internos de la fundición. La intensidad de la radiación emitida a través de la fundición varía localmente con el tamaño y la naturaleza de los defectos, formando una imagen radiográfica de los defectos, que se refleja y registra en una película radiográfica.
El método de registro mediante imágenes de películas radiográficas es el método más comúnmente utilizado, que comúnmente se conoce como prueba radiográfica. La imagen del defecto reflejada por la radiografía es intuitiva y se pueden presentar la forma, el tamaño, la cantidad, la posición del plano y el rango de distribución de los defectos.
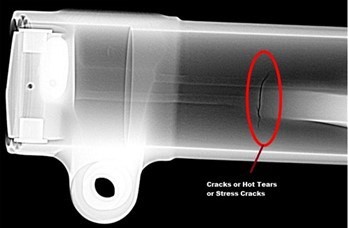
Pruebas ultrasónicas
Las pruebas ultrasónicas utilizan la propagación de haces de sonido con energía de sonido de alta frecuencia dentro de la fundición para generar reflejos cuando golpean las superficies internas o los defectos. La magnitud de la energía acústica reflejada es función de la directividad y las propiedades de las superficies internas o defectos y la impedancia acústica de tal reflector. La energía acústica reflejada por varios defectos o superficies internas se puede aplicar para detectar la ubicación de los defectos, el grosor de la pared o la profundidad de los defectos debajo de la superficie.
Como método de prueba no destructivo ampliamente utilizado, la prueba ultrasónica tiene las principales ventajas:alta sensibilidad de prueba, que puede probar pequeñas grietas; gran capacidad de penetración, que puede detectar fundiciones de sección gruesa. Sus principales limitaciones son:formas de onda de reflexión difíciles de interpretar para defectos discontinuos con dimensiones de contorno complejas y poca directividad; Las estructuras internas no deseadas, como el tamaño de grano, la microestructura, la porosidad, el contenido de inclusiones o los precipitados finamente dispersos, también dificultan la interpretación de la forma de onda.
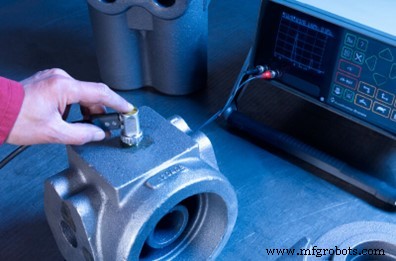
Tecnología Industrial
- El uso de la inspección visual en la gestión de activos y el control de calidad
- Mejora de la calidad y la seguridad en la trazabilidad del producto
- 4 razones por las que las pruebas e inspecciones de equipos son importantes
- ¿Qué es la prueba de calidad de soldadura? - 10 defectos comunes de soldadura
- Guía de métodos de prueba de PCB
- Introducción a NDT (ensayos no destructivos) para fundiciones
- Los fundamentos del control de calidad y la inspección en el mecanizado CNC
- Rectificadora de superficies rotatorias y calidad de procesamiento
- Pruebas de PCB:un enfoque en las pruebas funcionales y en circuito
- Métodos especializados de rectificado interno
- Información:Inspección y prueba de piezas robóticas