¡Hola, talleres de trabajo:es hora de automatizar!
¿Piensa que la automatización es demasiado difícil en un entorno de bajo volumen y alta combinación? Piénsalo de nuevo
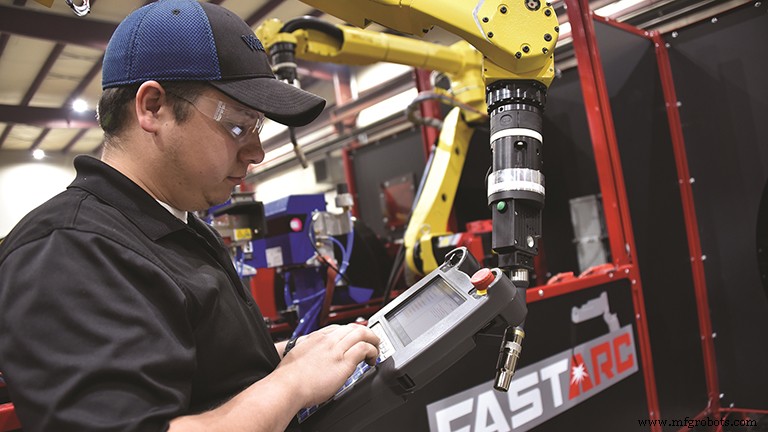
Por lo general, no se ha hablado de los robots y los talleres de trabajo juntos. Después de todo, todo el mundo sabe que la automatización solo es adecuada para la producción de alto volumen, y la operación típica de mamá y papá es todo menos eso:su agenda está llena de pedidos para trabajos de alta mezcla, bajo volumen y, a menudo, muy complejos. ¿Quién necesita un robot en este entorno, donde las configuraciones se realizan varias veces a la semana o incluso todos los días?
Sin embargo, antes de pasar al siguiente artículo, es posible que desee considerar algunas cosas. Para empezar, muchos expertos sugieren que, independientemente de lo que los propietarios se digan a sí mismos, los talleres de trabajo sufren la utilización de máquinas más baja de la industria. Los valores de efectividad general del equipo (OEE) del 50 por ciento o menos no son inusuales. La automatización es una solución clara para mejorar este número.
Y debido a que el cambio de máquina es más frecuente en los talleres, se necesitan maquinistas y programadores más calificados para realizar actividades relacionadas con la configuración, personas que cobran salarios más altos y son difíciles de encontrar. Esto aumenta los costos operativos, reduce las oportunidades de trabajo adicional y hace que la producción las 24 horas del día sea extremadamente desafiante. Dada la escasez de trabajadores calificados, la automatización debería ser, por lo tanto, el Santo Grial para cualquier taller, incluso si la implementación no es un camino fácil.
Posibilidades de Plug and Play
La pregunta es, ¿por dónde empezar? Zach Spencer tiene algunas ideas. Como ingeniero de propuestas personalizadas para Methods Machine Tools Inc., Sudbury, Mass., señaló que la automatización puede estar cerca de un asunto de conectar y usar, especialmente cuando se incluye como parte de la compra de una nueva máquina herramienta.
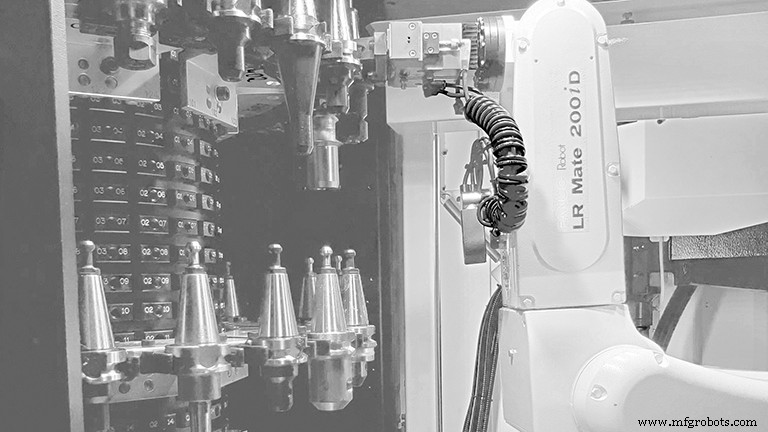
“Desarrollamos nuestra JobShop Cell hace casi 15 años, y desde entonces se ha convertido en una de nuestras soluciones de automatización más populares para FANUC RoboDrill”, dijo. "Está diseñado para tiendas que tienen al menos algunos cambios todos los días, tienen un espacio restringido y necesitan la flexibilidad para cambiar fácilmente de una parte a otra".
JobShop Cell está disponible en dos configuraciones, explicó. Uno utiliza una disposición de transportador superior/inferior para llevar la materia prima al robot y retirar las piezas terminadas, mientras que el otro utiliza un gabinete que contiene una serie de cajones para el almacenamiento de piezas de trabajo y materiales. Ambos emplean un robot FANUC para cargar y descargar la máquina (o un par de máquinas, en el caso de Twin RoboDrill JobShop Cell de Methods), y ambos brindan una manera de dejar un CNC desatendido durante horas o incluso un turno completo, según el pieza de trabajo.
Para volúmenes más altos, Methods ofrece su Plus-E, un sistema de automatización estilo elevador de paletas múltiples para trabajos de volumen medio a alto, así como el Plus-K para talleres que desean automatizar la configuración y operación de la máquina. con la capacidad de intercambiar portaherramientas, prensas precargadas y accesorios. “Puede decirle al sistema que estas cinco prensas son la Parte A, las siguientes dos prensas son la Parte B, la siguiente es la Parte C y las siguientes diez serán la Parte D”, dijo Spencer. “Después de eso, simplemente lo cargas con material y te vas a casa. Las dos máquinas de la Serie Plus son unidades autónomas que se colocan junto a un RoboDrill y son perfectas para talleres que buscan una manera fácil de pasar a la automatización”.
Tomar el tranvía
Methods no es el único proveedor que adopta este enfoque. Eric Nekich, responsable de operaciones, tecnología y ventas internas de Lang Technovation Co., Hartland, Wisconsin, dijo que los sistemas de automatización RoboTrex de la empresa utilizan un robot FANUC y hasta cuatro carros móviles, cada uno con una serie de prensas precargadas. El RoboTrex 52, por ejemplo, puede almacenar hasta 42 prensas por carro (según el tamaño de la pieza y la configuración del carro), lo que podría ofrecer un mecanizado desatendido de 168 piezas de trabajo.
Al igual que JobShop Cell, RoboTrex es autónomo y está totalmente protegido, pero también se puede integrar con una variedad de marcas y modelos de centros de mecanizado. El único obstáculo es pensar en la necesidad de invertir en algunas de las prensas de cinco ejes Makro-Grip de Lang, necesarias para usar con el sistema (y fabricadas, coincidentemente, en 50 centros de mecanizado equipados con RoboTrex en la fábrica de Lang en Alemania) . “Sin embargo, es una inversión con un retorno de la inversión muy rápido, porque el tiempo de actividad de su eje aumentará drásticamente con el sistema RoboTrex USA”, dijo Nekich.
Michael Gamache es el gerente de desarrollo de negocios de Gamache Systems con sede en New Berlin, Wisconsin, una división de Metalcraft de Mayville y el integrador exclusivo de los sistemas RoboTrex en los Estados Unidos. Reconoce que algunos clientes pueden resistirse a invertir en un nuevo sistema de sujeción de piezas, pero ofreció algunas razones excelentes para hacerlo.
“Como dueño de un negocio, entiendo el hecho de que las prensas no son económicas, pero desde una perspectiva de automatización, la sujeción de trabajos de alta calidad es la mitad de la batalla”, dijo. “Necesita llevar la materia prima al robot de manera repetitiva y precisa, y el sistema Makro-Grip es una de las mejores formas de lograrlo. Además, el sistema es muy fácil de configurar y operar porque el robot maneja las prensas y no una gran variedad de tamaños de materia prima; por eso, un programa funciona para cada parte”.
Consigue un agarre
Tyler Mardaus, ingeniero de diseño de la División de Productos Industriales de Kurt Manufacturing, con sede en Minneapolis, estuvo de acuerdo con la necesidad de sujeción de piezas de alta calidad, aunque el enfoque de su empresa es significativamente diferente al propuesto por Lang. “Nuestro equipo de sujeción de piezas de ingeniería personalizada (CEW, por sus siglas en inglés) diseña una gran cantidad de sistemas hidráulicos de doble acción controlados por solenoide”, dijo. "El sistema hidráulico brinda mayor psi y, por lo tanto, mayor fuerza de sujeción que la sujeción manual, mientras que el solenoide admite la activación electrónica del tornillo de banco a través del robot o el control de la máquina, lo que crea un sistema verdaderamente automatizado".
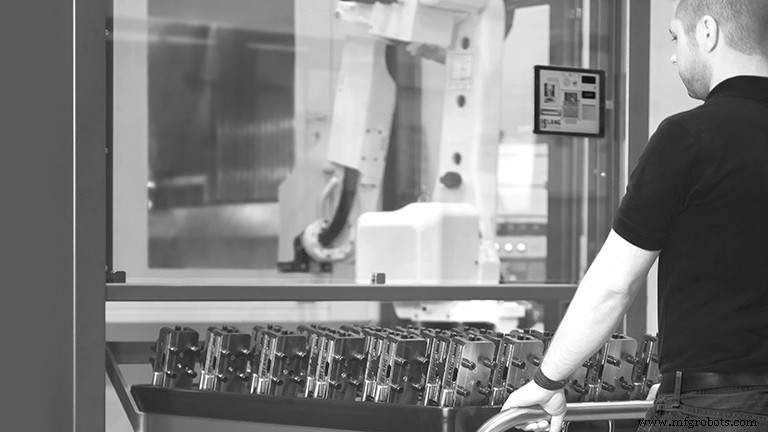
Agregó que los talleres deberían comenzar su viaje de automatización apuntando a los trabajos de mayor volumen. Y si hay piezas que pueden usar un tornillo de banco (o varios tornillos de banco) con mordazas mecanizables, estas se pueden cambiar durante el cambio, lo que reduce el tiempo de configuración. En cuanto a la inversión, no se puede evitar la necesidad de una bomba hidráulica y plomería, pero podría ser posible adaptar las prensas manuales existentes de un taller con conjuntos de tuercas y tornillos que no dañan el sistema hidráulico.
“Debe esforzarse por crear un sistema de control de circuito cerrado”, dijo Mardaus. “Esto comienza con la instalación de algún tipo de dispositivo de confirmación de asiento parcial, pero también debe verificar que el tornillo de banco se haya sujetado con la fuerza correcta antes de permitir que comience el ciclo, y que el tornillo de banco esté suelto antes de que el robot intente quitar el tornillo. pieza de trabajo Todos estos pasos son cruciales para cualquier solución de mecanizado automatizado”.
Aceleración del intercambio de sujeción de piezas
El comentario de Mardaus sobre la reducción del tiempo de configuración es acertado. Después de todo, ¿por qué molestarse en reducir los costos laborales a través de la automatización si va a incurrir en horas de tiempo de inactividad costoso cada vez que cambie de trabajo? Las mordazas de cambio rápido que mencionó son un excelente lugar para comenzar, pero si el presupuesto lo permite, un sistema de posicionamiento de punto cero, como el Makro-Grip de Lang (y otros), convierte el cambio de sujeción en un ejercicio de un minuto. También debe haber capacidades sólidas de CAM, con software de simulación que evalúe las trayectorias de herramientas, los portaherramientas, las herramientas de corte, las piezas de trabajo, la sujeción de piezas y la propia máquina herramienta procesadas posteriormente.
Y como explicó Dietmar Moll, director de desarrollo comercial de Zoller Inc., Ann Arbor, Michigan, los talleres deben otorgar una alta prioridad a la administración de herramientas, comenzando con un sistema de preajuste fuera de línea y el software asociado. “Uno de los mayores beneficios de cualquier estrategia de automatización es que un robot o cobot se hace cargo de la atención de máquinas y otros trabajos sin valor agregado, lo que libera al personal calificado para realizar tareas más importantes”, dijo Moll.
El preajuste de herramientas fuera de línea es una de estas tareas, pero también hay una planificación exhaustiva del trabajo, el mantenimiento y la organización del portaherramientas, la inspección de herramientas de corte y el análisis de los datos del taller. Con este fin, Zoller ofrece una variedad de soluciones mucho más allá de la configuración de herramientas. Sus soluciones de administración de herramientas (TMS) de nivel Bronce, Plata y Oro permiten que un taller aumente sus capacidades según sea necesario, brindando una visibilidad significativamente mayor de los procesos de producción y los activos relacionados con las herramientas. Y debido a que estos pueden comunicarse con el robot colaborativo "cora" de Zoller, agregó Moll, sirven para "cerrar el ciclo" al automatizar las tareas del cuarto de herramientas, como la limpieza y el almacenamiento de herramientas.
Del mismo modo, las soluciones integradas de almacenamiento de herramientas de la empresa ayudan a organizar estos activos, lo que reduce aún más el tiempo de inactividad y la ineficiencia. Y cuando se completa el trabajo, estos mismos sistemas se pueden usar para volver a colocar las herramientas en la cuna, revisar su rendimiento y registrar la vida útil restante de la herramienta. "Esto ayuda a los talleres a comprender mejor qué herramientas de corte funcionan bien y cuáles no, lo que les da la capacidad de mejorar aún más los procesos y reducir los costos de las herramientas", dijo.
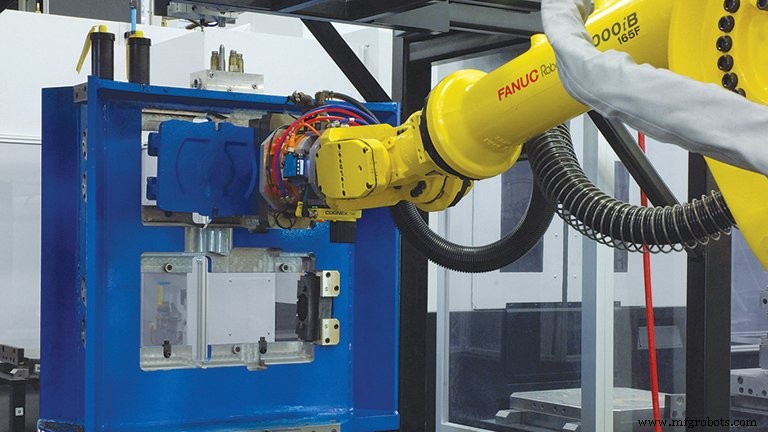
Sugerencias de programación
La gestión robusta de herramientas también es una parte esencial de la programación de trabajos, algo crítico para la utilización de máquinas herramienta y robots por igual. Para Moll, esto significa saber qué trabajos son los siguientes y qué herramientas se necesitan para ejecutarlos. Para Daniel Carranco, significa más que eso, especialmente en el contexto de la automatización. El director de mejora continua de Global Shop Solutions Inc., The Woodlands, Texas, señaló que todos los talleres, automatizados o no, deben tener un buen ERP y un sistema de programación, uno que también pueda monitorear el piso de producción y recopilar información sobre el proceso de mecanizado.
Sin embargo, lograr la parte de monitoreo y recopilación de datos de esa ecuación requiere software ERP, máquinas herramienta y robótica fáciles de integrar. “Tuvimos situaciones en las que el cliente quería integrar su equipo con nuestro sistema, pero descubrió que la plataforma de software utilizada por ese equipo era casi imposible para nosotros”, dijo. “Entonces, el primer consejo para cualquiera que busque un entorno de producción integrado es asegurarse de que todo pueda comunicarse de manera efectiva y que todos tengan claro los tipos y volúmenes de datos que se intercambiarán”.
La comunicación, al parecer, significa más de lo que alguna vez significó. Mientras que los sistemas ERP se han destacado durante mucho tiempo en la recopilación de datos de los humanos en el taller, ahora también deben recopilarlos de los robots y los controladores de las máquinas. Además, estos datos no solo contienen el número de trabajo omnipresente, el tiempo de producción y la cantidad completada (o desechada) que los usuarios esperan, sino que también pueden mostrar información en tiempo real sobre el consumo de material, la inspección y la calidad de la pieza, el estado de la máquina y el robot, y así sucesivamente.
“Ciertamente hay mucha más información disponible hoy en día de la que había antes, y con el software, el equipo y la integración de ERP correctos, todo se puede recopilar sin problemas y de forma automática”, dijo. “Hacerlo brinda oportunidades completamente nuevas para la mejora continua, pero lo que es más importante, libera a los empleados para que se concentren en cosas más importantes. No se pierde más tiempo en la recopilación manual de datos, que a menudo es irregular, y las personas pueden trabajar en la planificación y el análisis de procesos”.
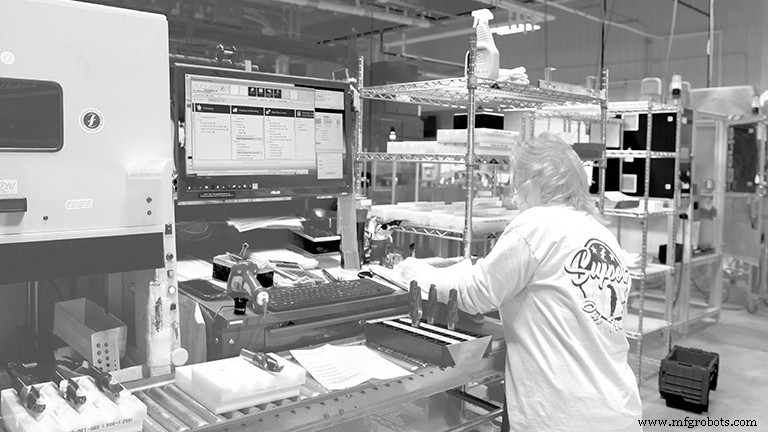
Impulsar las mejores prácticas
Como sugirió Carranco, estas tecnologías deben buscarse independientemente de los planes de automatización de un taller, ya que todas sirven para hacer que las operaciones sean más eficientes y sus niveles de OEE mucho más altos. Y cuando se dé el siguiente paso, implementar un robot o un sistema de manejo de materiales, la inversión se amortizará mucho más rápido. Suponiendo que no le interese o no pueda utilizar ninguno de los sistemas preconfigurados que ya se han comentado, la pregunta será "¿qué robot deberíamos comprar y cómo deberíamos implementarlo?"
Dean Elkins puede recomendar uno. Elkins, líder del segmento de manejo de materiales en Motoman Robotics Division de Yaskawa America Inc., Miamisburg, Ohio, dijo que los talleres de trabajo a menudo presentan una gama de aplicaciones robóticas adecuadas, ya sea cuidado de máquinas, desbarbado de piezas, ensamblaje automatizado o soldadura robótica. Finding the right equipment for these applications, though, requires a good deal of evaluation and talking to knowledgeable people.
“Justifying an investment in automation depends on several factors,” said Elkins. “Obviously, the larger the production quantity, the more it makes sense to automate it. But even lower volume, repeat work can be profitable, provided the shop takes the necessary steps to reduce setup time as much as possible. Parts with longer run times are also good candidates, as are parts with simple handling requirements.”
Elkins noted that most job shops find a small to medium-sized floor-mounted robot—meaning a payload of 5-25 kg—is all that’s needed to deburr a batch of parts, weld a crateful of brackets, or tend a CNC lathe after everyone’s gone home for the night. With that, however, some level of safety guarding will be required, as will grippers, an interface to the machine tool, and possibly programming and simulation software.
Tomorrow, Today
And don’t forget the training, he warned. Automation is much simpler than it once was, yet the savvier job shop owner is still going to make an additional investment in training, and have a dedicated person on staff to manage the shop’s robotics. That said, collaborative and force-limiting robots are becoming quite popular, especially where floor space is a concern. Robots can be equipped with self-changing or quick-change grippers, increasing flexibility. Vision systems can often eliminate or at least simplify part conveying systems, and the ability to teach a robot its tasks helps reduce the need for offline programming systems. “There’s a lot to consider,” said Elkins. “That’s why I encourage anyone interested in automation to do their homework, ask questions, and partner with a reputable integrator.”
Acieta LLC, Waukesha, Wis., is one such company. Steve Alexander, vice president of operations, warns that not all integrators are created equal. “Make sure you work with someone who has experience with your type of work and the skill level to implement your robotic automation project,” he said. “Get references, go see their previous installations, and understand the quality of their work. Industrial robots are designed to last well over 10 years, so you want to make sure everything else in the cell is designed for an automated environment and is just as reliable as the robot itself.”
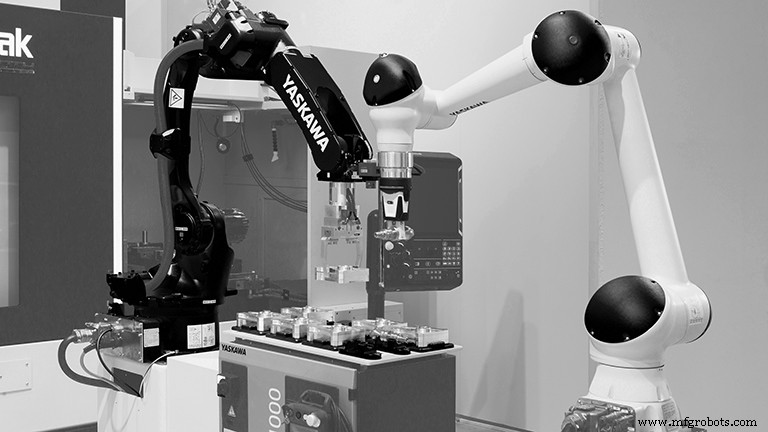
Doing so can lead to a return on investment (ROI) of just a few months, although a year or two is probably a more realistic expectation. Much of that depends on the application, of course, but the type of robot also plays a role. As Elkins noted, collaborative robots—or cobots—have become all the rage over the past few years, mainly due to their ease of use and seemingly safer operation in proximity to humans. Yet appearances can be deceiving. Cobots can be slower and less accurate than so-called “industrial robots,” possibly slowing ROI, and even the friendliest cobot can harm a human if established safety procedures aren’t followed.
This is why Elkins and others strongly recommend a risk assessment with any robot installation. He also suggested that the best approach for automation newbies is to start small and easy. “Find a single pain point and conquer that one first before looking at adding additional processes or complexity,” he said. “You want to have success right out of the gate so that everyone—the shop owner, the machine operators, and the people doing the integration—are comfortable moving on to larger or more complex projects. Sometimes, the biggest challenge is getting employee buy-in. There’s always the fear that robots will replace humans, so it’s important to make them part of the implementation. Educate them, get them involved in the roll-out, and when they find that the robot actually makes their job easier and more interesting, they’ll end up being your biggest cheerleaders.”
Sistema de control de automatización
- Automatizar ... o bien
- Hahn presenta un 'amplio espectro' de soluciones de automatización en Automate
- Cómo la automatización puede ayudar a acelerar una vacuna
- Alcanzar el potencial de automatización total - Modelo operativo de automatización (Parte 3)
- Creación del equipo:modelo operativo de automatización (parte 2)
- ¿Podría la automatización ser la clave para la creación de empleo en la fabricación?
- ¿Soy demasiado pequeño para no automatizar?
- Determinar cuándo invertir en automatización
- Consejo interno del integrador de sistemas:cuándo automatizar
- Automatización precisa:Comunicado de prensa de Automatización 2019
- Microautomatización:automatización de piezas pequeñas "Ninguna pieza es demasiado pequeña"