¿Automatización de talleres? ¡Puedes apostar!
A veces, un solo operador puede atender a varios robots, cada uno de los cuales atiende a varias máquinas, ¡todo suma!
Si la "automatización" es el zumbido constante que escuchas de prácticamente todos en la metalurgia en estos días, los propietarios de los talleres podrían ser las únicas personas que gritan "¡No!" O al menos "¡Espera!" ¿Cómo, preguntan, puede automatizar de manera rentable piezas de bajo volumen y alta mezcla? Sin embargo, no solo es factible, sino probablemente necesario.
Como dijo Steve Alexander, vicepresidente de operaciones de Acieta LLC, un integrador de automatización con ubicaciones en Waukesha, Wis., y Council Bluffs, Iowa, “Estados Unidos lidera el mundo en manufactura, pero también tiene uno de los índices de manufactura por hora más altos. costes laborales. Los talleres de trabajo no solo compiten con otros talleres locales por negocios, sino que también compiten con otros países. La automatización puede reducir sus costos para que puedan competir mejor”.
Agregó que la demanda de capacidad de fabricación está superando la oferta de mano de obra disponible y que "los talleres de trabajo pueden tener dificultades para competir con los talleres de máquinas más grandes y establecidos" por el talento cada vez más costoso. Pero un robot puede atender varias máquinas y, en algunos casos, un solo operador puede atender varios robots, cada uno de los cuales atiende varias máquinas.
“Eso libera a los operadores para realizar operaciones secundarias, como desbarbar piezas, ensamblar o dedicar más tiempo a los controles de calidad”, dijo Alexander. Para citar solo dos ejemplos, Central United en Newburg, Wisconsin, utiliza un solo robot FANUC M-20iB para atender dos tornos. Otro cliente de Acieta en New Berlin, Wis., utiliza un solo robot FANUC R-2000iB para atender cuatro máquinas. "En ambos casos, solo hay un único operador responsable de cargar las piezas en bruto en el transportador o en la estación de cola para que el robot las agarre".
Alexander agregó otra razón de peso para automatizar:la ergonomía. “Las lesiones en el lugar de trabajo son una preocupación para talleres de cualquier tamaño. Algo tan simple como cargar una pieza en un mandril de torno puede convertirse rápidamente en una lesión por estrés repetitivo para un operador cuando ese proceso se repite cientos de veces al día. Entre el tiempo perdido y las reclamaciones, estas lesiones cuestan a las empresas miles de millones de dólares cada año. Los robots debidamente integrados pueden eliminar un proceso repetitivo del operador, mejorando así el bienestar de los empleados”.
Opciones e integradores
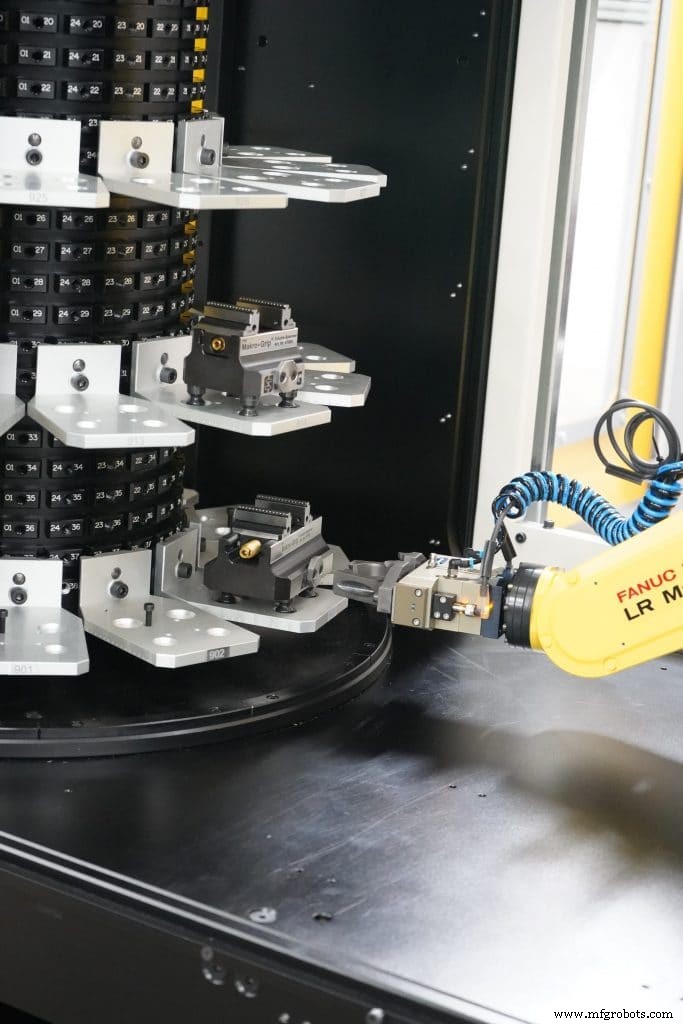
Hasta aquí todo bien. Pero como explicó John Lucier, gerente de automatización de Methods Machine Tools Inc., Sudbury, Massachusetts, el simple objetivo de "hacer más piezas de manera más eficiente" puede conducir a enfoques muy diferentes según el tipo de trabajo que se produzca y los volúmenes involucrados. .
Por ejemplo, supongamos que un taller de trabajo de volumen medio necesita cambiar un par de veces por semana. “Con una planificación adecuada, una celda podría cambiarse en el turno con personal, lo que permitiría una buena cantidad de producción desatendida en el siguiente turno”. Y dentro de este contexto, la velocidad requerida del robot dependería en gran parte del tiempo del ciclo de mecanizado de las piezas producidas. Cuanto más corto sea el tiempo del ciclo, más rápido debe ser el robot y menos probable es que un robot pueda soportar varias máquinas.
Pero las tiendas con volúmenes aún más bajos, incluso tamaños de lote de uno, también pueden ser buenos candidatos para la automatización, explicó Lucier. Excepto que “la consideración más importante es reducir el tiempo de cambio, o incluso eliminar por completo el tiempo de configuración. La gente se queda atrapada en el tiempo del ciclo y el tiempo de carga/descarga, pero si sus volúmenes son tan bajos que la mitad de su tiempo se dedica a cambiar, entonces atacar el tiempo de cambio, incluso a expensas del tiempo del ciclo, puede tener sentido”.
Una forma de "eliminar" la configuración es automatizarla, y los robots de hoy en día se pueden programar para cambiar tanto sus propias herramientas de final de brazo como la sujeción de piezas en la máquina. Otro enfoque es cargar palets comunes desde un carrusel (u otro tipo de apilador) independientemente de la pieza que se produzca. Esto elimina la necesidad de cambiar las herramientas del robot o de programar diferentes movimientos de carga/descarga para diferentes piezas.
El sistema Methods PlusK lleva este concepto un paso más allá y también carga portaherramientas desde el carrusel. Diseñado para admitir las máquinas de la serie RoboDrill de FANUC, el carrusel de PlusK tiene cinco anillos, cada uno de los cuales tiene 12 estaciones, para un total de 60 estaciones. Cada estación puede contener una paleta de piezas o un portaherramientas y el robot puede cargar ambas piezas en la mesa de trabajo del RoboDrill y las herramientas en la torreta integrada de 21 herramientas de la máquina.
Pero como señaló Lucier, si desea automatizar la producción de 30 o 40 piezas completamente diferentes, 21 herramientas pueden no ser suficientes. “Por lo general, cargamos piezas en pequeñas prensas de cinco ejes de proveedores como Lang Technovation”, explicó Lucier. “Y generalmente mezclamos y combinamos piezas y herramientas en el carrusel. Digamos que un trabajo requiere cinco herramientas que difieren de las herramientas utilizadas en el trabajo anterior. Puedo usar el robot para cargar cada herramienta según sea necesario, o para cargar las cinco herramientas en la torreta a la vez, como si un operador preparara un trabajo”.
Si estas consideraciones comienzan a hacer que te duela la cabeza, es comprensible. Porque si bien se ha vuelto mucho más fácil implementar la automatización en los últimos años, todavía es lo suficientemente difícil como para que la mayoría de los talleres de trabajo hagan bien en aprovechar integradores como Acieta y Methods. Desde la perspectiva de Lucier, programar el robot es la parte fácil. Cosas como lidiar con la sujeción automática de piezas, la eliminación de virutas en la zona de trabajo y la mejor manera de presentar las piezas al robot son el mayor desafío. Ahí es donde realmente vale la pena el asesoramiento de expertos.
Automatización de máquinas heredadas
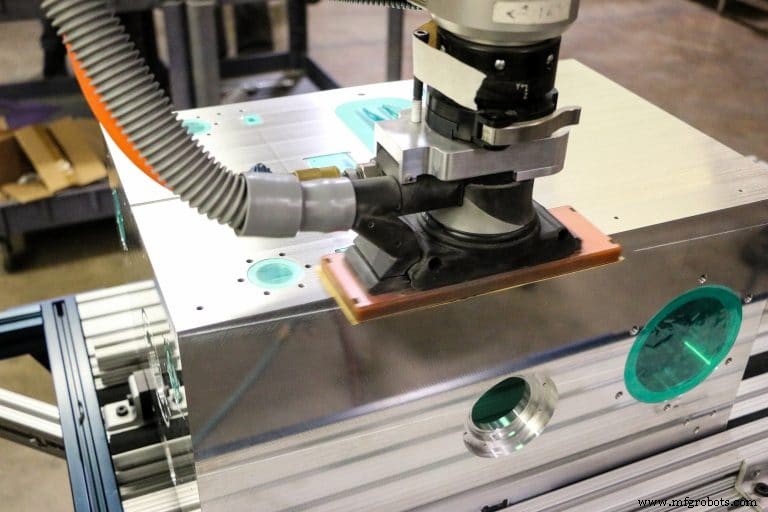
Aquí hay un ejemplo de cómo eso puede suceder. A mediados de 2017, Gary Kuzmin, propietario de All Axis Machining en Dallas, Texas, era un ejemplo de manual de frustración en el taller. Tenía más trabajo potencial del que podía soportar la mano de obra disponible y un taller lleno de centros de mecanizado de cinco ejes alemanes de alta gama, EDM y otras tecnologías que los OEM no podían automatizar económicamente con el tipo de versatilidad que podría sacarlo de esta situación. unir. Su solución fue invertir en un robot colaborativo de Universal Robots (UR), Ann Arbor, Michigan.
Como cualquier propietario de un taller, el principal requisito de Kuzmin era mantener una "flexibilidad total" en su operación. “Hacemos una parte durante dos o tres días y luego pasamos a otra. En un mes determinado, podríamos estar fabricando de 30 a 40 piezas diferentes en una máquina”. Así que necesitaba un robot que fuera fácil de configurar y cambiar. Y necesitaba características como pinzas de control de fuerza para que el robot pudiera adaptarse a diferentes piezas y el cambio de material en bruto a una pieza terminada de paredes más delgadas.
UR entregado en todos los aspectos. Sus robots tienen una interfaz de programación en un colgante de mano. Operan de forma segura junto a los humanos porque los robots se detienen automáticamente cuando contactan a un operador (de ahí el término robot colaborativo o "cobot"). Son fáciles de entrenar y no intimidan.
Kuzmin explicó que una razón clave de la flexibilidad de la solución de UR es una arquitectura abierta que ha permitido a terceros desarrollar software, sistemas de visión, efectores finales y otros accesorios que funcionan con robots de UR. UR facilita el esfuerzo de integración al proporcionar una sala de exposición en línea integral llamada UR+.
Incluso con eso, Kuzmin descubrió que no había una solución lista para programar el robot para realizar tareas de lijado o desbarbado, dos funciones que quería automatizar porque son difíciles para los humanos, y especialmente para los trabajadores mayores. Así que All Axis usó el kit de desarrollo de software gratuito de UR para crear sus propias rutinas, que siguen la curvatura de la pieza según el modelo CAD.
Estos complementos integran el control de la aplicación a través del propio dispositivo de enseñanza del cobot. “Universal Robots ha hecho un trabajo fantástico al poner esta solución a disposición de tiendas como la nuestra”, dijo Kuzmin. “No estamos encerrados en un entorno propietario. En cambio, recibimos un libro de cocina con una manera fácil de expandir la comunicación”, agregando que All Axis usa protocolos como TCP/IP, Ethernet, Modbus y Profinet para conectar cobots y máquinas.
“Otra ventaja es que no tenemos que pagar acuerdos de licencia especiales; todo viene con la compra del cobot UR”, dijo Kuzmin. "Nos registramos en el sitio web de UR para convertirnos en desarrolladores y descargamos los elementos que necesitamos".
En otro ejemplo, All Axis decidió que quería la capacidad de mover un cobot de una máquina a otra lo más rápido posible. El desafío fue crear un sistema que reorientara el cobot a la siguiente máquina y lo asegurara al piso sin perforar agujeros en el concreto. La solución fue colocar un receptáculo con epoxi sobre el concreto y colocar un pasador de indexación.
“Si alguna vez necesita mover o reparar el robot, simplemente desbloquee y jale los pasadores y mueva el robot según sea necesario”, dijo Kuzmin. “Cuando reposicionas el robot y bloqueas los pines, todo sigue indexado. También adjuntamos la bandeja de presentación al soporte del robot, por lo que su posición relativa al eje del robot nunca cambia”.
En solo unos meses, Kuzmin y su equipo se volvieron tan buenos en la integración de cobots (ahora tienen siete) y estaban tan entusiasmados con los beneficios de la automatización que crearon una compañía separada llamada All Axis Robotics. Si bien Kuzmin dijo que es relativamente fácil automatizar una máquina nueva gastando alrededor de $150 000 con el OEM, él ve un gran potencial en la automatización de máquinas heredadas, que es su enfoque.
Para tomar un ejemplo de cómo la automatización ayudó al resultado final en All Axis Machining, un trabajo que generalmente tomaba seis meses para ejecutarse terminó en 2½ meses usando el robot. “Fue fenomenal. El retorno de la inversión fue de siete a ocho meses”, dijo Kuzmin.
Tal vez en su innovación más impresionante, All Axis combinó un robot UR con un microscopio y una cámara listos para usar, además de inteligencia artificial (IA) y aprendizaje profundo, para crear un sistema que detecta rebabas, bordes enrollados o cualquier anomalía (como hardware faltante) en una pieza.
Eso es importante porque, como explicó Kuzmin, muchas rebabas no se pueden identificar excepto con un aumento y los ojos de un humano se fatigarán después de solo 20-30 minutos de dicha inspección. Pero también es difícil de automatizar.
“Las rebabas son como copos de nieve, no hay dos iguales”, dijo Kuzmin. “Nuestro sistema, al que llamamos Aurora, usa IA para aprender cómo se ve una rebaba. Cuantas más rebabas vea, mejor podrá detectarlas. El sistema identificará la rebaba, la clasificará y clasificará la pieza después de que la haya rechazado debido a la rebaba. También registra la inspección y la ubicación de las rebabas para que los operadores puedan regresar para corregir la pieza de manera eficiente y moverla”.
All Axis presentó Aurora en 2018 y Kuzmin dice que la mayor respuesta individual ha sido:"¡Hemos estado buscando algo como esto durante años!" Una próxima versión del sistema incluirá la capacidad de insertar insertos helicoidales (comúnmente llamados Heli-Coils) y hardware en partes también.
¡Los robots industriales contraatacan!
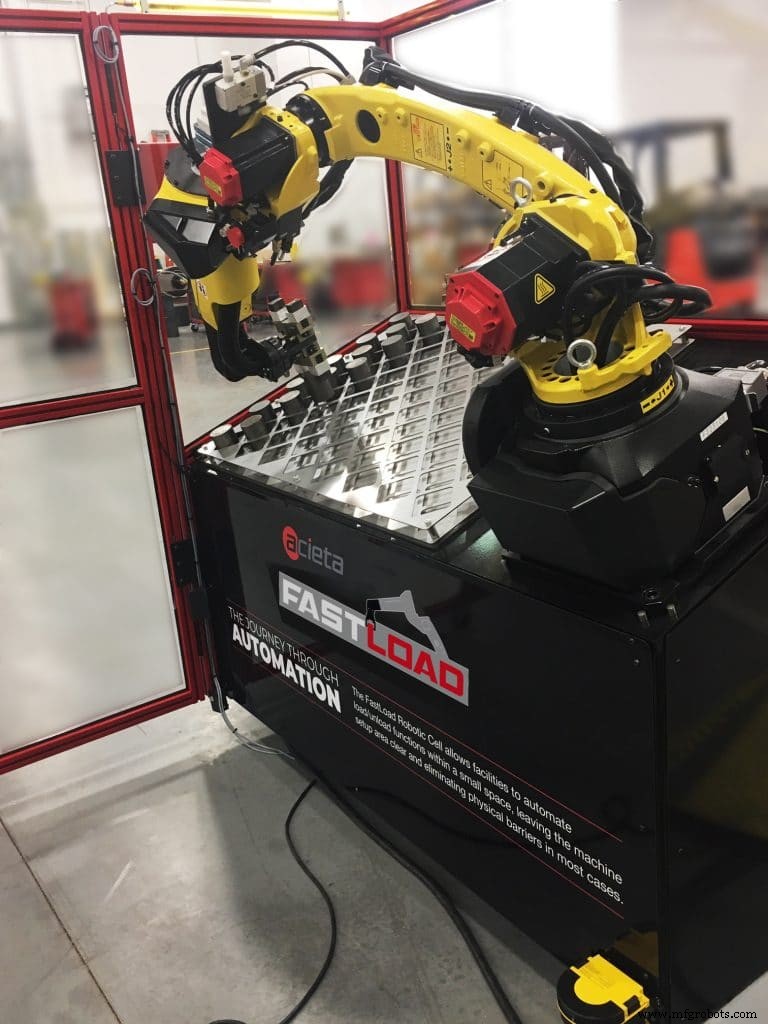
Como se mencionó, los cobots UR son fáciles de configurar e integrar con una variedad de máquinas y accesorios. Pero los proveedores de robots industriales como FANUC y KUKA Robotics se dieron cuenta de características como el mando manual intuitivo e introdujeron sus propias versiones.
Lucier de Method reconoció que “en un momento era absolutamente cierto que los robots colaborativos eran más fáciles de programar. Pero configurar un robot industrial ya no es realmente diferente de configurar un robot colaborativo”. Incluso la función de configuración "tómalo y arrástralo" está disponible en los robots tradicionales, aunque Lucier dijo que es mejor usarlo en casos en los que simplemente deseas colocar la pieza sobre una mesa o contra un bloque.
“Es perfecto para algo como enseñarle al robot a cargar una CMM porque la máquina solo necesita saber aproximadamente dónde está la pieza para encontrar el borde y luego realizar las mediciones”, dijo. "Pero si estoy cargando en un mandril o un tornillo de banco, tengo más control cuando lo enseño con el colgante de programación".
También hay una variedad de accesorios para robots industriales. Por ejemplo, dijo Lucier, las pinzas de cambio rápido y control de fuerza no son exclusivas de los cobots. “Schunk tiene una línea de pinzas con detección de fuerza que utilizan servomotores, alejándose de los neumáticos, que son más difíciles de cambiar. Realmente puedes ajustar la electricidad".
La gente de robots industriales también tiene soluciones que le permiten reposicionar rápidamente el robot de una máquina a otra. En el caso de FANUC, una cámara en el robot escanea tres calcomanías en la "nueva" máquina para reorientarse automáticamente.
Pero después de meses de intentarlo, Lucier dijo que no pueden encontrar una situación en la que tal capacidad sea útil. “Mover un robot de una máquina a otra implica más que simplemente mover el robot. Piense en todas las cosas que necesita cambiar:tal vez las herramientas del final del brazo, la entrada, la salida…” La mejor solución es aquella en la que cada máquina tiene su propio robot o un robot da servicio a varias máquinas, tal vez con efectores finales duales para que pueda cambiar entre tipos de piezas sin intervención.
También se da el caso de que integradores como Acieta y Methods pueden agregar robots tradicionales a máquinas heredadas, y los robots tienen un precio similar al de los cobots. Entonces, considerando las ofertas actuales, la mayor ventaja de los cobots es su capacidad para funcionar cerca de los humanos sin el espacio y el costo de cercas.
La desventaja es que son más lentos que los robots industriales tradicionales y se limitan a piezas más ligeras. El modelo más grande de UR maneja piezas de hasta 24 lb (10 kg). Los tiempos de carga/descarga más lentos no son significativos en piezas con tiempos de ciclo largos, pero pueden disminuir la producción en trabajos de volumen medio a alto con tiempos de ciclo más cortos.
Kuzmin de Axis Machining no ve la necesidad de velocidad, “solo consistencia y confiabilidad, especialmente en piezas con un tiempo de ciclo largo. Es mejor tener un cobot que cargue piezas a una velocidad confiable y luego usarlo para desbarbar otras piezas mientras la máquina funciona. Y si no necesitas la velocidad, ¿por qué arriesgarte?”
Lucier y Alexander advierten que no se debe exagerar el beneficio de poder trabajar junto al robot. Por un lado, señaló Lucier, ya tiene que proteger al operador del área de mecanizado. Alexander agregó que si un cobot está manipulando una pieza con bordes afilados (como suele ser el caso en el mecanizado), "de todos modos, no es colaborativo ni seguro para un operador trabajar en su proximidad".
Tanto Lucier como Alexander dijeron que combinar "técnicas de colaboración" con robots industriales ofrecía un compromiso útil. “Para aquellos fabricantes que buscan un piso abierto con cercas mínimas, los robots industriales tienen la capacidad de trabajar en un entorno sin cercas mediante el uso de escáneres de seguridad de área”, explicó Alexander. “Y pueden trabajar en este entorno sin vallas sin sacrificar la velocidad. Cuando un operador ingresa a la primera zona de seguridad, el robot reduce la velocidad. Cuando el operador ingresa a la segunda zona de seguridad, el robot se detiene por completo”.
Por otro lado, dijo Lucier, dado que la zona de seguridad para este enfoque es de 3 a 4 pies, el robot a menudo reduciría la velocidad si las carretillas elevadoras u otro tráfico pasara con frecuencia.
Como se sugirió anteriormente, un área perfecta para los cobots es la atención de un CMM. “Para empezar, las MMC son intrínsecamente seguras”, como dijo Lucier. “No hay protección, excepto alrededor de los componentes móviles. No son rápidos. Puedes pararte justo al lado de ellos. Y, por lo general, no está colocando la pieza en un accesorio, tal vez simplemente sosteniéndola contra un bloque en V o algo similar. Ahí es donde he visto brillar a un robot colaborativo”.
Ambos expertos están de acuerdo, como resumió Alexander, en que "los robots industriales son mucho más aplicables que los cobots en la mayoría de las aplicaciones de fabricación y taller".
Consideraciones de software
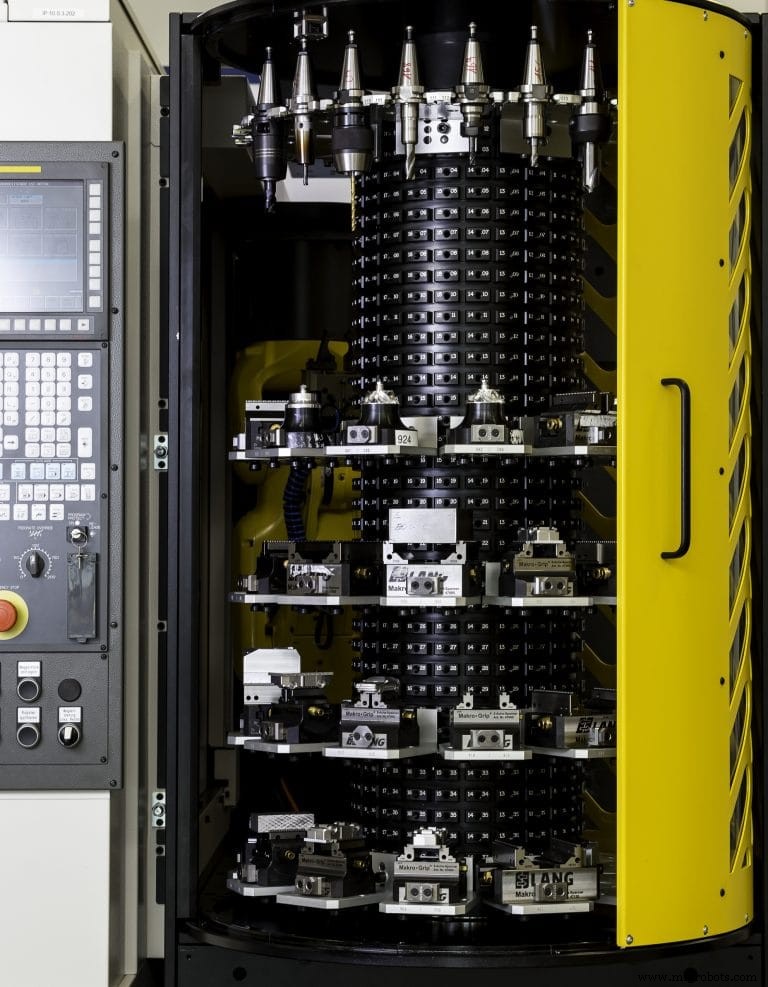
Según Greg Mercurio, presidente de Shop Floor Automations, La Mesa, California, "el software es el componente más esencial en la automatización de talleres". Dijo que el software de control numérico directo (DNC, por sus siglas en inglés) (también conocido como software de control numérico distribuido o software de “alimentación por goteo”) “permite una comunicación optimizada con la máquina, así como un control de revisión para gestionar la calidad/los desechos, y un medio para organizar miles de programas .”
La función principal del software DNC es enviar programas de mecanizado directamente a la máquina, lo que permite que una máquina con un control de grado relativamente bajo maneje una superficie compleja.
Mercurio y todos los expertos están de acuerdo en que cierto grado de monitoreo de la máquina es útil "para aumentar el tiempo de actividad y la capacidad de la máquina". Mercurio agregó que el software de gestión de datos de producción permite a las empresas dejar de usar papel y que “la gestión del depósito de herramientas también es una necesidad. La mejor parte es que todas estas soluciones se pueden integrar con CAD/CAM, ERP, MES, CMMS y más”.
Por otro lado, señaló que las tiendas más pequeñas pueden beneficiarse enormemente de una simple adición de hardware antes de gastar miles de dólares en software. Por ejemplo, agregar una interfaz RS232 a USB a equipos más antiguos facilita los programas de alimentación por goteo.
“El hardware es fácil de usar, configurar y mantener, por lo que es la opción de automatización
que menos tiempo consume para un taller más pequeño. Las máquinas RS232 más antiguas pueden usar una unidad USB como las máquinas CNC más nuevas que tienen esa función incorporada de fábrica. También es una forma más económica de modernizar su taller sin reemplazar el equipo por completo. También permite actualizaciones de memoria asequibles”, agregó Mercurio.
Volviendo a los robots, Alexander dijo que existen numerosos paquetes de software ofrecidos por OEM de robots y terceros que permiten la programación de robots fuera de línea en una PC mientras el robot sigue funcionando. "Estos paquetes de software le permiten cargar un archivo CAD y luego le dan la libertad de 'dibujar' la ruta de su robot con un lápiz óptico o un mouse", explicó Alexander. "El software luego convertirá su ruta dibujada en un código de robot que se puede cargar directamente en el robot".
Es apropiado que el propietario del taller, Kuzmin, tenga la última palabra:“Quería mejorar la productividad. Lo hice agregando robots. Y estoy muy satisfecho con lo que hemos logrado. Mientras lo hacía, dije que deberíamos ponerlo a disposición de todos, porque eso es lo que hará que la fabricación en nuestro país sea mucho más competitiva”.
Sistema de control de automatización
- Apueste a la nube adecuada para usted
- ¿Cuántos detalles para los planes de trabajo?
- No tiene tiempo para descuidar la seguridad del trabajador
- La torreta de acabado reduce el tiempo de ciclo
- Si quieres mejorar algo, mídelo
- La automatización de pequeñas tareas de programación de NC da grandes frutos con el tiempo
- 5 señales de que necesita reparaciones de grúa
- Cómo saber si necesita piezas de grúa nuevas
- ¿Necesita hardware de freno industrial nuevo?
- Razones por las que necesita un mecanizado personalizado
- 5 señales de que necesita una nueva pieza de grúa