El software de simulación despliega sus alas
Cuando luchan con problemas desconcertantes como la complejidad del producto, el peso ligero, los materiales avanzados y los nuevos métodos de fabricación, los ingenieros de fabricación actuales utilizan cada vez más simulaciones de alta fidelidad para visualizar soluciones a estos desafíos. El último software de simulación puede ofrecer pistas para mejorar el diseño y el rendimiento del producto con paquetes CAE de alta gama y software de simulación NC que ayudan a determinar no solo los mejores diseños, sino también las formas más eficientes de lograrlos.
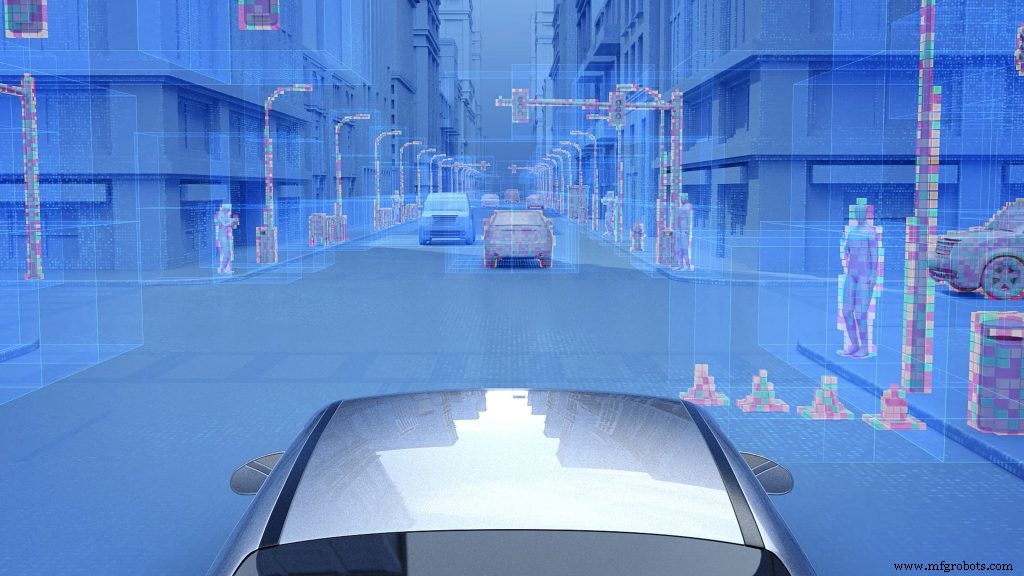
Los nuevos procesos de fabricación, como la fabricación aditiva (FA), presentan diferentes problemas para los fabricantes, y la simulación puede determinar por adelantado qué soluciones funcionan mejor. Muchos paquetes de software de simulación ahora ofrecen simulaciones específicas de aditivos que pueden ayudar a iluminar los procesos de estratificación mediante los cuales se construyen productos aditivos, al mismo tiempo que visualizan cómo hacer que los procesos de corte de metales sustractivos tradicionales sean más eficientes.
Resolviendo el Problema de la Complejidad
En la fabricación discreta, los ingenieros de desarrollo de productos se enfrentan a enormes desafíos, ya que cualquier cosa, desde automóviles hasta aeronaves, barcos masivos y maquinaria pesada, contienen millones de líneas de código que programan sistemas con componentes electrónicos adaptados al Internet industrial de las cosas (IIoT).
“Las tendencias más importantes que vemos son la creciente complejidad de los productos”, dijo Ravi Shankar, director de mercadotecnia global de productos de simulación, Siemens PLM Software (Plano, TX), al señalar el nivel creciente de componentes electrónicos en los componentes mecánicos. "Lo que impulsa eso es el gemelo digital y la ingeniería basada en modelos".
Los vehículos autónomos y los drones son el último ejemplo de sistemas complejos que requieren sistemas de software de simulación, dijo Shankar. “También hemos visto el enfoque en la eficiencia del combustible y las emisiones de los automóviles, con el aumento del peso ligero y el uso del diseño generativo”, agregó.
Siemens presentó recientemente una solución para automóviles autónomos que incorpora sus soluciones de simulación Simcenter con nueva tecnología de sensores. En el Día de la Innovación de EE. UU. de Siemens en marzo en Chicago, la compañía presentó el sistema, utilizando imágenes de sensores virtuales Tass PreScan con la plataforma Mentor DRS360 que automatiza el desarrollo de algoritmos para la fusión y el procesamiento de sensores.
“La primera tendencia es que se pueden crear modelos mundiales basados en la física y modelos de sensores basados en la física”, dijo Martijn Tideman, director de productos de Tass International (Steenovenweg, Países Bajos), que fue adquirida el año pasado por Siemens. “Estos modelos generan información de sensores artificiales de alta fidelidad que se puede generar como si viniera de cámaras, radares y LIDAR reales. Cuando alimenta estos datos artificiales a las unidades de procesamiento del automóvil, como el DRS360, puede evaluar el hardware/software del automóvil sin conducir una sola milla”.
Otra clave es asegurarse de que el software de simulación de conducción automatizada se ejecute en clústeres de alto rendimiento (HPC), dijo Tideman.
“Estos clústeres pueden ejecutar muchas simulaciones en paralelo, lo que acelera el proceso de evaluación/validación virtual. Quiere poder conducir un millón de millas virtuales durante el fin de semana.
“Los simuladores de conducción automatizados deben conectarse a una amplia gama de otros módulos de hardware y software, por ejemplo, importadores de mapas, para generar automáticamente redes de carreteras virtuales o herramientas de simulación de dinámica de vehículos para garantizar que el vehículo responda correctamente a las acciones de control”, explicó. . "Las interfaces entre las herramientas de simulación se están estandarizando cada vez más", como con FMI/FMU (interfaz de maqueta funcional/unidad de maqueta funcional), agregó Tideman.
Simulación disruptiva
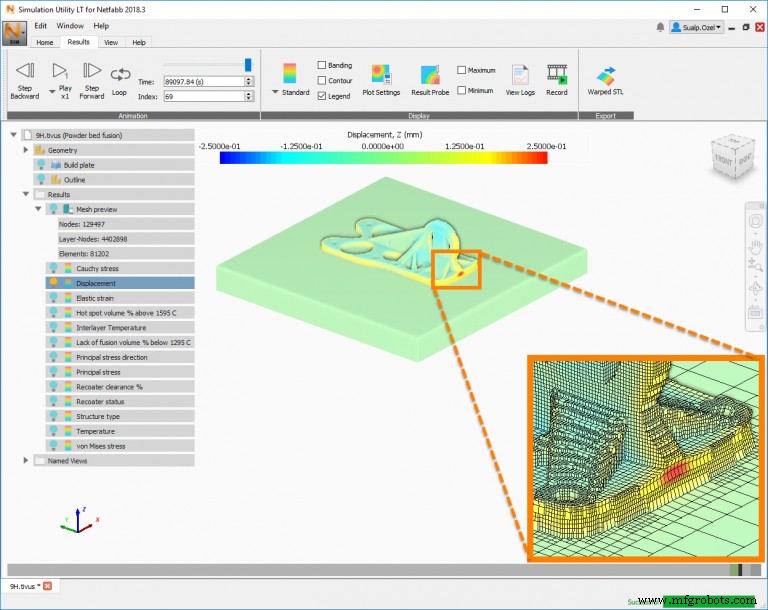
Varias tecnologías habilitadoras clave están afectando la forma en que se aplica la simulación en la fabricación. “Si bien existen numerosos desarrollos técnicos que continúan evolucionando y mejorando, algunos tienen el potencial de alterar fundamentalmente dónde, cómo y quién utiliza las capacidades de simulación”, dijo Seth A. Hindman, gerente sénior de estrategia y gestión de productos, fabricación, construcción y producción en Autodesk Inc. (San Rafael, CA).
“La Ley de Moore ha seguido siendo válida mucho más tiempo de lo que la mayoría hubiera imaginado. Con los continuos avances en la potencia de procesamiento, se puede acceder a un hardware increíblemente potente a un precio muy bajo. Combinado con el desarrollo de extensas redes de fibra óptica, las empresas pueden conectarse a recursos computacionales externos que exceden las velocidades de sus propias intranets”, dijo Hindman. “La capacidad de ráfaga, la computación elástica y la HPC [informática de alto rendimiento] configurable están permitiendo a las empresas cambiar fundamentalmente la forma en que diseñan y fabrican sus productos mediante la ejecución de suficientes análisis para comprender realmente cómo funcionará su producto en numerosas aplicaciones y entornos”.
Los fabricantes también se están alejando del análisis dependiente de la malla, dijo Hindman.
“La naturaleza omnipresente de los datos de diseño 3D ha seguido presionando la demanda de herramientas de simulación que ya no dependan de la malla y que puedan beneficiarse de la asociatividad con los datos de diseño nativos. Esto no solo aumenta la productividad en el flujo de trabajo general, sino que amplía la audiencia que puede beneficiarse de las capacidades de simulación. La presión negativa natural es crear soluciones que sean más sólidas, más intuitivas y que rompan con los requisitos CAE tradicionales. El potencial a largo plazo es que esto permite una interacción simplificada con soluciones y la automatización de tareas onerosas”.
La perspectiva de larga data dentro de CAE para llevar la simulación "por adelantado" ahora está siendo reemplazada por la idea del análisis basado en objetivos, agregó Hindman. “Si bien la simulación inicial es poderosa, todavía depende de una convención tradicional de probar lo que ha diseñado frente a impulsar la exploración de diseños que cumplan con los objetivos que ha definido”, dijo. Autodesk actualmente está introduciendo lo que llama diseño generativo en el mercado de la ingeniería, agregó Hindman, que acaba de estar disponible en Autodesk Fusion 360 Ultimate.
“Nuestra tecnología de diseño generativo permite que el sistema cree diseños inspirados en objetivos, lo que facilita la exploración generalizada del espacio de diseño, lo que permite hacer compensaciones basadas en conocimientos”, dijo Hindman. “La tarea principal de los ingenieros históricamente ha sido crear un diseño que funcione. Con el diseño generativo, cada resultado cumple con éxito ese requisito básico, lo que significa que la toma de decisiones y las compensaciones se elevan al nivel de las iniciativas comerciales centrales”.
Simulación de procesos aditivos
Los desarrollos aditivos continúan entusiasmando a la industria manufacturera, y muchos desarrolladores de simulación han lanzado recientemente versiones nuevas o mejoradas específicas de aditivos de su software de simulación.
Por ejemplo, el 19 de abril, el desarrollador de simulación Ansys Inc. (Canonsburg, PA) lanzó sus nuevas soluciones Additive Print y Additive Suite que brindan simulación para procesos de fabricación aditiva de metales. Se dice que las soluciones permiten a los usuarios imprimir piezas metálicas complejas y livianas y analizar las propiedades y el comportamiento de la microestructura. Ansys dijo que esto ayudará a reducir los costos de AM al limitar las restricciones de diseño, reducir el desperdicio y reducir el tiempo de impresión.
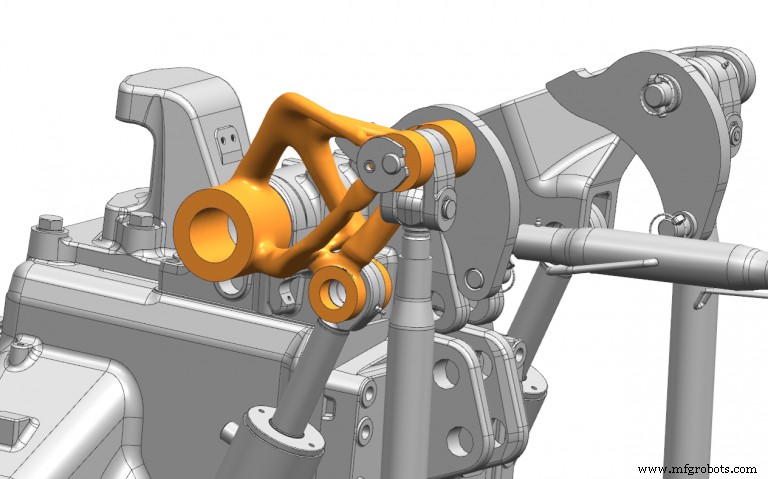
Según la empresa, el flujo de trabajo completo de simulación aditiva de Ansys permite a los clientes probar sus diseños de productos virtualmente antes de imprimir una pieza. El software incorpora simulación previa al proceso de impresión, lo que permite a los ingenieros diseñar, probar y validar el rendimiento de una pieza en la etapa de diseño y reduce en gran medida el alto costo físico de ensayo y error.
AM es un cambio de juego para la fabricación, dijo Brent Stucker, director de fabricación aditiva de Ansys. “Los dispositivos médicos se pueden producir con geometrías específicas del paciente. Los inventarios de piezas de repuesto para muchos componentes serán cosa del pasado, ya que las piezas de repuesto se pueden producir cuando se solicitan”, señaló Stucker. “Los productos que operan en entornos extremos, como en la industria del petróleo y el gas, se pueden producir con nuevas composiciones de materiales híbridos [más duraderos]. La complejidad geométrica que ofrece AM significa que se pueden integrar docenas de componentes en un solo componente que es más liviano y de mayor rendimiento”.
Stucker señaló que en AM, los diseñadores y operadores de máquinas que normalmente no han sido usuarios de simulación de ingeniería ahora deben comprender un proceso de impresión complejo.
“Estamos viendo que los operadores de máquinas quieren algo más que conjeturas informadas cuando se trata de predecir si una pieza se puede construir con éxito”, dijo. “Necesitan comprender rápidamente cómo una configuración de máquina en particular resultará en una distorsión de la pieza antes y después de retirarla de los soportes, y si una distorsión excesiva podría causar que el mecanismo de esparcimiento de polvo golpee la pieza [lo que se conoce como choque de la cuchilla]. La situación es similar con los diseñadores que hacen Diseño para AM [DfAM]. Quieren saber si la pieza que han diseñado se imprimirá correctamente y, si puede, cuáles serán las propiedades de ese componente.
“La simulación pone el poder de comprender el proceso aditivo en manos de diseñadores y operadores”, agregó. "Es por eso que hemos desarrollado Ansys Additive Print para que sea una herramienta de predicción de procesos de impresión independiente, de modo que una persona que no sea ingeniero pueda usar la herramienta en unos pocos días".
Si bien el software de simulación se ha utilizado con éxito para garantizar que una estructura diseñada resistirá las condiciones de servicio durante las operaciones de campo, también se ve constantemente desafiada por cargas, materiales y física complejos, señaló Subham Sett, director de Iniciativas Estratégicas de Simulia, Dassault Systèmes ( París). “El software de simulación ahora tiende a proporcionar soluciones multifísicas y multiescala que brindan predicciones para cada aspecto para acelerar el crecimiento de la industria. Por ejemplo, en la industria automotriz, el software de simulación se utiliza para resolver problemas multifísicos, desde dinámica multicuerpo, ruido y vibración, resistencia a choques hasta flujo inestable, así como problemas multiescala de diseño de materiales, escalado ascendente y descendente de materiales multiescala y subestructuras. ”
Agregar la capacidad de predecir la forma resultante del proceso AM se ubica como uno de los nuevos desarrollos más emocionantes en la simulación de fabricación, dijo Sett. "Teniendo en cuenta la ruta de escaneo, las propiedades del material, la máquina y las propiedades del láser, podemos predecir con precisión la deformación de la pieza debido al calor y la gravedad mientras se imprime la pieza", agregó.
La simulación del proceso aditivo permite a los constructores predecir y controlar el proceso con mayor precisión, lo que evita que se produzcan errores en el proceso de construcción de piezas aditivas capa por capa.
Shankar de Siemens dijo que la simulación en procesos aditivos, que Siemens agregó con su módulo NX Additive el año pasado, permite a los fabricantes predecir los resultados de fabricación.
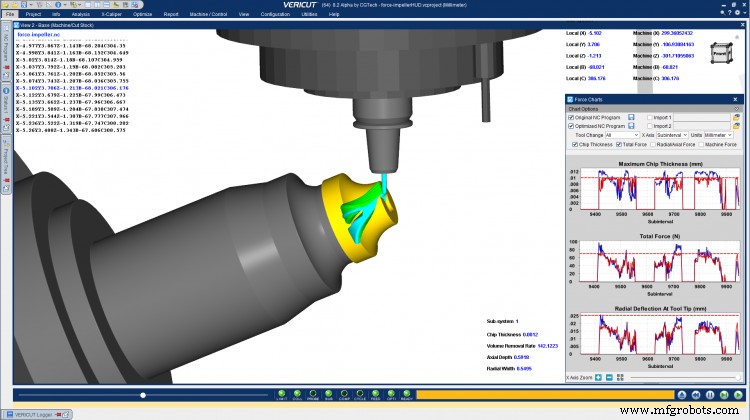
“A medida que crea las capas, debe saber muchas cosas:¿Cuánto tiempo se tarda en enfriar? ¿Cuáles son los vacíos [los espacios vacíos o cajeras] en la pieza? La simulación puede ayudar a abordar los vacíos y también las tensiones residuales en el producto”, dijo. La simulación también ayudará a los fabricantes a saber cómo estandarizar los procesos y comprender cómo funcionará el producto.
Siemens actualmente está trabajando en temas como procesos aditivos con cambios de fase y cómo se enfrían las piezas. En algunos casos, se utiliza HPC, debido a la naturaleza intensiva en computación de esas simulaciones. “Los cálculos a menudo se pueden paralizar. Si está tratando de resolver modelos grandes, [HPC] es atractivo”, dijo Shankar.
Con respecto a los aditivos, Autodesk continúa ampliando su cartera de soluciones, dijo Hindman. “La última incorporación a la cartera de Netfabb es la inclusión de las capacidades de diseño generativo de Autodesk. Como mencioné anteriormente, el diseño generativo permite que el sistema cree diseños inspirados en objetivos para facilitar la exploración generalizada del espacio de diseño. Un ingrediente clave de cómo el sistema puede funcionar como participante activo es que le hemos enseñado a ser consciente del proceso de fabricación aditiva, por lo que generará resultados optimizados para la impresión 3D”.
Con el lanzamiento de Netfabb Ultimate en marzo, Autodesk introdujo capacidades integradas de simulación de procesos además de la oferta independiente existente de Netfabb Local Simulation. Hindman dijo que ambas versiones de Netfabb ahora incluyen:predicciones mejoradas de efectos como polvo atrapado, puntos calientes/quemaduras y falta de fusión; emulación de procesos adicionales como la eliminación de piezas EDM y el impacto del tratamiento térmico; rendimiento mejorado en el servicio de cómputo elástico opcional de Autodesk; introducción de capacidades de análisis de procesos en Netfabb Ultimate; y capacidad optimizada para intercambiar preformas de piezas compensadas impulsadas por simulación por la geometría original.
Autodesk también lanzó soporte para el proceso de deposición directa de energía (DED) en asociación con las carteras Netfabb y PowerMill (PowerMill Ultimate) de la compañía para aprovechar la experiencia en controles robóticos multieje.
“Esto agrega otra capacidad para predecir el potencial de deformaciones y fallas excepcionalmente grandes durante la fabricación de deposición de alta velocidad”, dijo Hindman. “A medida que las empresas adoptan la fabricación aditiva de metal, existen peligros comunes que deben enfrentar y superar”. Agregó que los desafíos más comunes de operar una impresora de fusión de lecho de polvo metálico son:deformación de la pieza, alabeo (la pieza impresa es inaceptable y puede dañar la recubridora); fallas/fracturas inducidas por estrés térmico (parte se rompe durante la impresión y puede dañar la recubridora); fallas de soporte (se acumula tanta tensión en la pieza que rompe la conexión entre la placa de construcción y la pieza, lo que hace que la pieza sea inaceptable y posiblemente permita que el repintado choque con la pieza); y propiedades variables de los materiales (las piezas tienen defectos visibles o no funcionan como se esperaba).
Visualización de procesos NC
Para los procesos de verificación y simulación NC, AM sigue siendo un área de desarrollo clave con desarrolladores de sistemas como el software de simulación NC Vericut de CGTech (Irvine, CA), que recientemente agregó un módulo Vericut Additive. "La fabricación aditiva sigue siendo una de las tendencias más populares en la fabricación, por lo que el software de simulación se esfuerza por mantenerse al día", dijo Gene Granata, gerente de producto de CGTech Vericut.
“Usar un software de simulación capaz de simular los mismos códigos NC que controlarán las máquinas es la mejor manera de proteger el equipo CNC y crear una pieza de calidad la primera vez que sale al taller”.
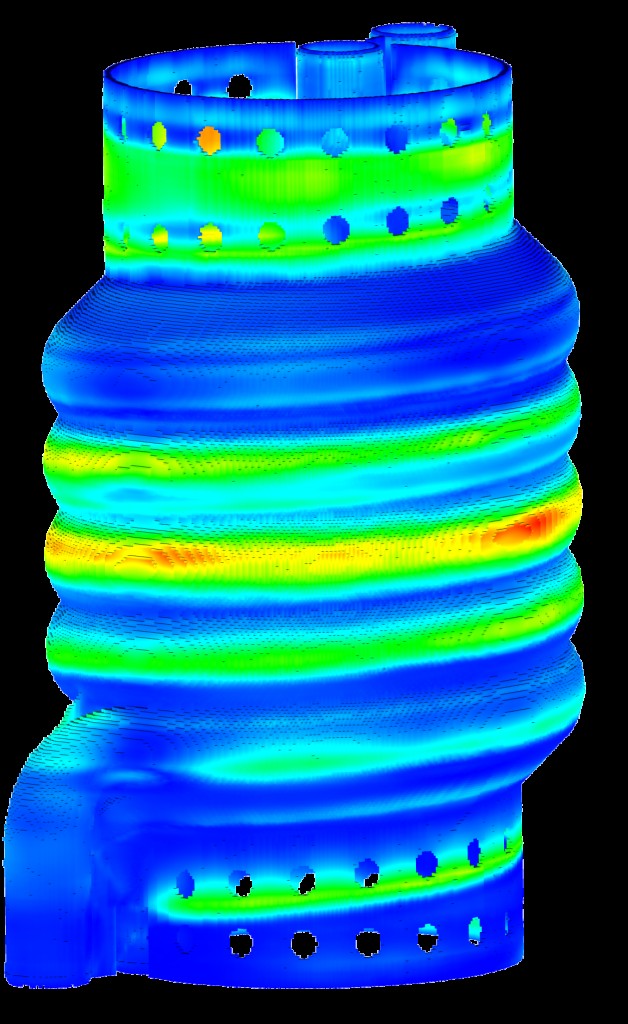
En los compuestos, dos de las últimas tendencias que se destacan son el enfoque en la visualización gráfica y la representación precisa de la pieza de trabajo, señaló Granata. “Aunque mejorar los gráficos puede parecer una mejora cosmética, existen beneficios reales de ingeniería al predecir y visualizar con precisión la forma neta de una pieza compuesta. Los fabricantes están comenzando a confiar más en el software para predecir la forma y la calidad finales de una pieza”, dijo. "Con una pantalla de alta resolución de la pieza de trabajo terminada, los ingenieros pueden comenzar a interrogar las características que más les preocupan con mayor fidelidad".
El software de simulación proporciona importantes herramientas de optimización y evaluación de procesos que mejoran la productividad del taller, agregó. “Nuevas opciones para crear trayectorias de herramienta 'eficientes' parecen aparecer en el mercado regularmente, pero ¿qué tan bien funcionan realmente? El software de simulación, impulsado por trayectorias de herramientas de código G posprocesadas, revela la 'verdad' en los tiempos de ejecución de la máquina”, dijo Granata. "Esto ayuda a los programadores de NC y a los ingenieros de fabricación a evaluar diferentes métodos de mecanizado para que, en última instancia, puedan seleccionar los métodos más eficientes para fabricar sus piezas".
La automatización, la optimización del mecanizado y la flexibilidad de la máquina son áreas clave que Spring Technologies (Cambridge, MA), desarrollador del software NCSimul y Optitool, está impulsando en su desarrollo de software de simulación, dijo Silvere Proisy, gerente general de Spring Technologies.
A medida que el mercado exige más procesos automatizados, NCSimul está desarrollando más automatización, dijo. “A partir de los datos enviados por el software CAM a NCSimul, se verifican automáticamente y el resultado de la simulación se entrega como informe final al programador a través de correos electrónicos. Los usuarios ya no tienen que interactuar con el software; todo puede ejecutarse en un servidor remoto”.
Se mejora la optimización del mecanizado CNC con Optitool, dijo. “Ahora ofrece dos niveles de optimización:uno es la reducción del corte de aire, optimizando todos los movimientos de aproximación y retracción sin cambiar las velocidades de alimentación del material; el segundo nivel es la optimización del modo de aprendizaje que regula los avances de corte del material en función de nueve parámetros de corte, como el grosor de la viruta o el flujo de la viruta, sin comprometer los avances y velocidades originales”.
La flexibilidad de la máquina es el tercer foco de desarrollo con su opción NCSimul 4CAM. “Dar a una empresa de fabricación la capacidad de cambiar un trabajo de una máquina a otra, en unos pocos minutos y sin tener que reprogramar la pieza en un software CAM, es lo que llamamos una revolución”, dijo Proisy. "Lee el código G inicial y vuelve a escribir el código nuevo automáticamente".
Sistema de control de automatización
- Modelado CAD 3D y su relación con la fabricación
- Kollmorgen actualiza su software de red para desarrolladores
- Uso de software de mantenimiento preventivo para la fabricación
- 7 mejores soluciones de software ERP de fabricación de 2022
- Smart Manufacturing:qué es y sus ventajas
- Honda anuncia la reestructuración de su fabricación mundial de automóviles
- Los macrodatos son la cuarta revolución industrial
- Perfil de la empresa:experto en fabricación y tecnología SourceDay
- El auge de las plataformas digitales en la fabricación
- Bright Machines lanza hardware y software de Microfactory
- Siemens presenta el software Camstar Electronics Suite