Flash de moldeo por inyección:9 causas principales y cómo resolverlas
Flash es uno de los defectos más comunes en el moldeo por inyección. Es la fina capa de plástico en la línea de partición o cualquier otra parte donde dos superficies diferentes del molde se encuentran y forman un límite. Tales áreas pueden crear una diferencia en la expansión y otros parámetros, lo que puede contribuir a aumentar las posibilidades de flash.
El manejo del flash de moldeo por inyección es simple, pero exige recursos adicionales y afecta la eficiencia general del proceso. Además, el desbarbado (eliminación de la rebaba de forma manual o automática) también puede afectar negativamente la calidad del producto y dañar potencialmente el molde, lo que genera mayores costos y otras pérdidas. Por eso es tan importante minimizar el defecto flash en los proyectos de moldeo por inyección.
Para resolver el flash de moldeo por inyección, es importante identificarlos primero y luego abordarlos de manera efectiva con un enfoque específico. Hacerlo garantizaría los resultados más rápidos y lo ayudaría a orientarlo en la dirección correcta para optimizar el proceso de moldeo por inyección y eliminar todos los defectos.
¿Qué es Flash en el moldeo por inyección?
La rebaba del moldeo por inyección es un defecto en el que la pieza tiene un exceso de plástico en la línea de partición, un límite o cualquier otra área donde se unen diferentes formas y áreas del molde. En general, el tapajuntas en la moldura de plástico es el más común en la línea de separación. Sin embargo, otras áreas también se ven afectadas. Sus causas y efectos siguen siendo los mismos independientemente de la ubicación.
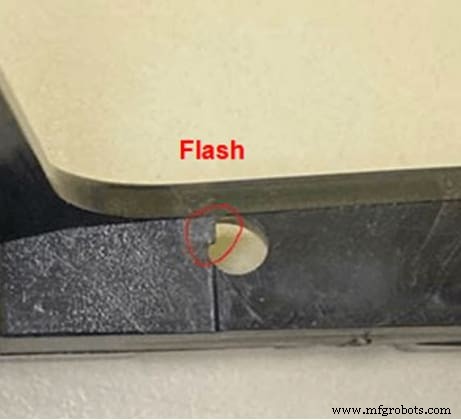
En la industria actual, el rebaba en piezas moldeadas es común y la mayoría de los fabricantes lo reducen significativamente pero no lo eliminan por completo. La razón principal es el costo total del moldeo por inyección. Los moldes sin rebabas son bastante caros, pero la mayoría de las empresas encuentran un compromiso entre costo, calidad y estética.
Las principales causas de las rebabas en el moldeo por inyección
El flash de moldeo por inyección puede ocurrir debido a una serie de razones. A veces, el origen del problema puede ser más de uno. Puede tener un desajuste en la línea de partición junto con un flujo incorrecto, lo que lleva a los mismos resultados:un defecto repentino en las piezas de moldeo por inyección.
Una cosa importante a tener en cuenta sobre el problema del parpadeo en movimiento de inyección es que no está restringido a una sola instancia o un subproceso. El parpadeo tiene múltiples causas y puede ocurrir debido a una gran cantidad de razones, desde problemas en la fase de inyección hasta fallas en el equipo de mantenimiento u otras razones como la viscosidad, la presión o la velocidad.
Estas son las causas más comunes de tapajuntas en molduras de plástico y cuándo ocurren realmente.
Vaso de molde durante la fase de inyección
1:discrepancias en la línea de partición
Una de las principales razones detrás del desajuste de la línea de partición es la presencia de contaminantes ambientales como polvo y escombros, que pueden mantener el molde abierto. Como resultado, el exceso de material se filtra y provoca un defecto relámpago. Además, los defectos en el molde también pueden causar este problema. Principalmente estos defectos se propagan con el tiempo debido al uso. Las herramientas viejas y desgastadas provocan fugas y eso da como resultado tapajuntas debido a la falta de coincidencia de la línea de separación.
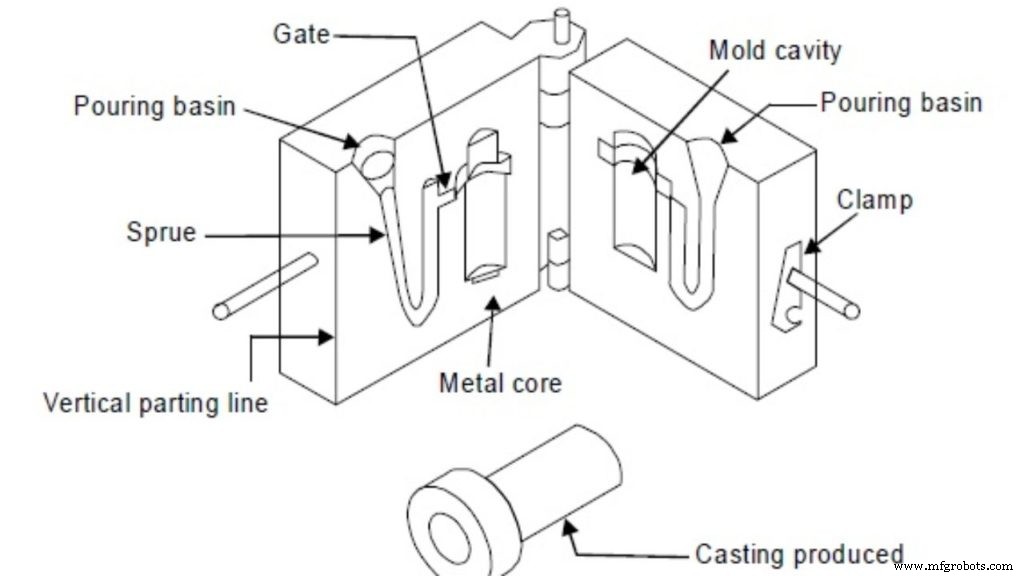
Incluso si tiene el molde perfecto y se asegura de que no haya contaminantes, el flashing puede ocurrir cuando se trata de una presión de sujeción incorrecta o formas extremadamente complejas. Las cavidades y otras características intrincadas pueden aumentar la presión general que soporta su molde y causar fugas y defectos en algunas áreas.
2 - Ventilación inadecuada
El moldeo por inyección es un proceso complejo en el que debe cuidar la temperatura general, la presión, las bolsas de aire y otras características. Por ejemplo, las burbujas de aire atrapadas son un gran defecto en cualquier diseño de moldeo por inyección que puede afectar las capacidades mecánicas y de soporte de carga generales de la pieza. De manera similar, las piezas moldeadas por inyección tienen un rango de temperatura específico para una excelente formación. Los respiraderos son los encargados de garantizar el buen funcionamiento de todos estos componentes. Cualquier problema en eso daría lugar a varios defectos que no se limitan solo al flasheo.
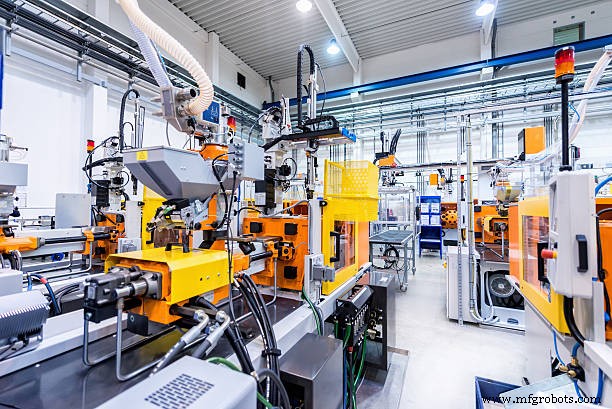
Moho Flash durante el embalaje o almacenamiento
3 – Presión de sujeción baja
El flash puede ocurrir durante el proceso de empaque y almacenamiento. El proceso de empaque tiene en cuenta la contracción del material durante el enfriamiento. La mejor manera es agregar el exceso mientras el proceso de retención mantiene todo el sistema en equilibrio de presión hasta que se enfríe.
En ambos casos, la presión de sujeción debe ser precisa. La fuerza de sujeción incorrecta puede perturbar la línea de separación y permitir que el líquido entrante salga y provoque destellos.
4:Problema con el buje del bebedero
Los casquillos del bebedero son parte del molde y son responsables de transferir los plásticos fundidos a la cavidad. Con el tiempo, pueden perder soporte para sostener la fuerza de la presión de inyección y deteriorar su función. En tales casos, sus piezas moldeadas por inyección tendrán defectos y el más común de ellos es el parpadeo.
Molde Flash durante el proceso debido a las características de flujo
Aparte de la etapa del proceso, hay algunos elementos que pueden causar flash de moldeo por inyección debido a las características del proceso y el flujo. La cantidad de rebaba que tendrá su pieza de plástico debido a las características del proceso depende de las siguientes características del proceso.
5 – Viscosidad
La viscosidad es la propiedad de cualquier líquido para fluir y es central en el proceso de moldeo por inyección. Una viscosidad más baja significa que el líquido fundido fluirá fácilmente fuera de la forma del molde y tendrá distorsiones en forma de destello. Generalmente, esta viscosidad es una función de la temperatura, las propiedades del material, la presión y la velocidad.
6 – Temperatura del cilindro y la boquilla
La presión no es el único factor que aumenta la viscosidad y, en consecuencia, la rebaba en la pieza de moldeo por inyección. La temperatura del cañón y de la boquilla también tiene un efecto directo sobre ella. Una temperatura más alta hace que el fluido sea más propenso a las fugas debido a la menor viscosidad y, en consecuencia, aumenta las posibilidades de que el moldeo por inyección se destelle.
7 – Relleno excesivo
Cualquier configuración de moldeo por inyección tendrá restricciones basadas en el tamaño y la geometría. Si el plástico fundido se llena en exceso, la presión de inyección superaría naturalmente la presión de sujeción y provocaría fugas. Esto aumentaría las posibilidades de flash y otros valores predeterminados. Sin embargo, debe tener cuidado al ajustar la configuración de alimentación, ya que el enfriamiento encoge el plástico y no desea una pieza incompleta debido a un tiro corto en el moldeo por inyección.
8 – Alta presión
La presión es una de las características de proceso más comunes que podrían aumentar la probabilidad de relámpago. La física básica dicta que la alta presión conduce a más características de temperatura y flujo en un entorno cerrado. El aumento de la presión y el aumento resultante de la viscosidad pueden causar múltiples valores predeterminados, incluido el flash.
9 – Exceso de embalaje
Las complejidades en el diseño y los caminos intrincados en el molde también pueden crear destellos en las piezas moldeadas por inyección. En campos angostos, una cantidad limitada de líquido fundido puede solidificarse y bloquear el flujo. Creando así una presión localizada dentro del molde. Los defectos resultantes no se detienen solo en el flash. En su lugar, tendrá que lidiar con otros problemas como la deformación, la densidad no uniforme y muchos otros problemas relacionados.
5 formas efectivas de controlar las rebabas en el moldeo por inyección
No hay duda de que prevenir el flasheo es bastante importante porque el flasheo causaría muchos problemas funcionales y estéticos. Sin embargo, es posible eliminar las rebabas del moldeo por inyección.
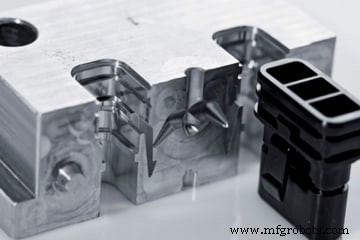
Estas son las 5 formas más efectivas que lo ayudan a controlar las rebabas en sus piezas moldeadas.
Diseño para la fabricación
La forma más eficaz de asegurarse de que su pieza moldeada por inyección esté libre de rebabas es diseñarla para que sea factible de fabricar. Esto significa garantizar las características simples y más efectivas que realizan la función en lugar de centrarse en sistemas intrincados.
Para entender esto mejor desde la perspectiva del proceso de moldeo por inyección, considere la línea de separación. Los expertos en la materia recomiendan utilizar una línea de partición en el borde en lugar de la superficie. Esto tiene beneficios tanto estéticos como funcionales, ya que la línea de partición no será visible en el borde. El diseño también reducirá las posibilidades de rebaba, ya que la costura contrarrestaría cualquier desajuste de la línea de separación.
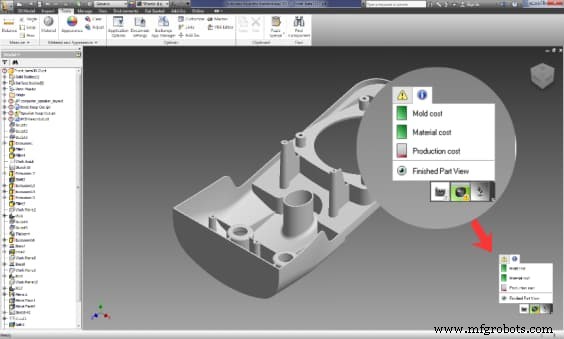
Hoy en día, el uso del análisis DFM es una parte importante de cualquier proyecto de moldeo por inyección industrial. Existen herramientas de software especiales que simulan los resultados de manera efectiva y le muestran las características de flujo y predicen problemas comunes como deformación, flash y flujo de calor en el moldeo por inyección. En RapidDirect, por ejemplo, puede cargar su archivo de diseño de pieza en la plataforma de fabricación en línea y luego obtener un análisis DFM gratuito para sus piezas.
Disminuya la tasa de inyección
Otra forma excelente de reducir las rebabas del moldeo por inyección es controlar las variables del proceso. La tasa de inyección tiene un efecto directo sobre la viscosidad, la presión y la temperatura que pueden causar flash. Esto es generalmente lo primero que hacen muchos expertos cuando se trata de flash, ya que la mayoría de las variables del proceso están conectadas con la tasa de inyección.
Especifique un molde sin rebabas
Una forma excelente, aunque costosa, de eliminar por completo las rebabas de las piezas moldeadas por inyección es utilizar un molde sin rebabas. Garantiza los mejores resultados, pero tiene un costo enorme que no es viable para muchas empresas y aplicaciones. Para aplicaciones delicadas donde la estética, la funcionalidad y todos los demás elementos son bastante importantes y los costos no son un problema, entonces esta es quizás la mejor manera de garantizar una pieza sin defectos.
Limpieza adecuada del moho
Una de las principales causas del desajuste de la línea de separación es la acumulación de suciedad, residuos y otros contaminantes en el molde. Además, las micropartículas en las cavidades estrechas del molde pueden incluso provocar un sobreembalaje, lo que aumenta aún más los defectos generales de la pieza. Mantener su molde limpio y en buen estado puede ayudar a minimizar las posibilidades de estos problemas y garantizar los mejores resultados.
Mantenimiento adecuado del molde y mejoras en el proceso
Finalmente, el mantenimiento de moldes y las optimizaciones de procesos son algo esencial para obtener resultados consistentes y confiables. El tonelaje de sujeción y la presión a veces pueden dañar el molde y dejar algunas deformaciones que pueden causar múltiples defectos en la pieza.
Un socio capacitado puede ayudarlo con su proyecto de moldeo por inyección
El destello del moldeo por inyección es una realidad inevitable y la mejor manera de reducirlo es a través de la optimización continua del proceso y vigilando todos los signos. Los moldes sin rebabas son una opción, pero tienen el inconveniente de aumentar los costos. En cambio, es más viable abordar las causas más comunes mejorando el diseño, manteniendo los moldes y optimizando el proceso de moldeo por inyección para garantizar los mejores resultados.
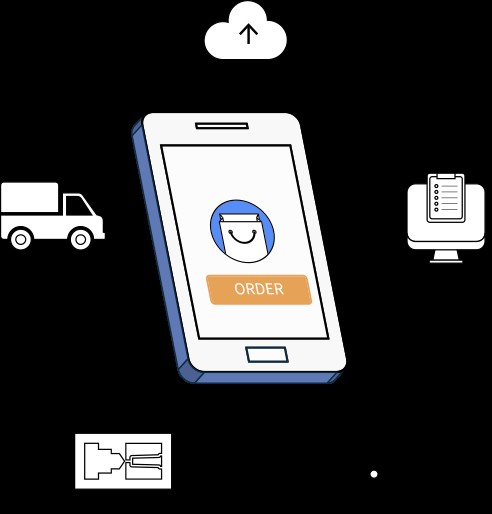
El socio adecuado de servicios de moldeo por inyección como RapidDirect puede ayudarlo a hacer todo eso sin perder tiempo ni recursos. Somos un servicio con certificación ISO que ofrece resultados incomparables gracias a nuestro equipo versátil y estrictos controles de calidad. Desde el diseño más complejo hasta el elemento más simple, nuestro equipo ha trabajado con numerosas entidades nacionales para simplificar cada paso de la fase de diseño y cumplir con todos sus requisitos en el menor tiempo posible.
Lo que distingue a RapidDirect es la plataforma DFM de última generación que ofrecemos. Nuestro portal en línea le permite acceder a nuestras innumerables plantillas de diseño y recibir ayuda de nuestro equipo de expertos para crear el mejor producto. Comenzar con RapidDirect es simple. Simplemente cargue su diseño con las especificaciones y características requeridas para obtener una cotización instantánea y comenzar a experimentar el futuro de la fabricación.
Resina
- Cómo se realiza el moldeo por inyección
- ¿Cómo estimar el costo del moldeo por inyección?
- Moldeo por inyección de plástico frente a mecanizado de plástico:cómo decidir
- PEEK de alta viscosidad para moldeo por inyección y extrusión
- Cómo planificar e implementar la automatización en una planta de moldeo por inyección
- Siete desafíos de entrega de última milla y cómo resolverlos
- 4 causas principales de fallas en los interruptores y cómo evitarlas
- Principales causas de fallas en las máquinas y cómo prevenirlas
- Principales riesgos de seguridad en la construcción y cómo evitarlos
- Principales preocupaciones de seguridad en camiones y cómo evitarlas
- Los 4 principales problemas de las máquinas CNC y cómo solucionarlos